α型超高强石膏的制备方法【技术领域】,特别涉及一种α型超高强石膏的制备方法。[0002]在用脱硫石膏和化学石膏制备α高强石膏领域,上海建筑材料科学研究院的叶蓓红等(叶蓓红、赵立群,一种短柱状脱硫α高强石膏CN102173621)采用水热法工艺,以脱硫石骨为原料,硫酸续、异丁醇纳和朽1fe酸纳为转晶剂,制得最闻干强度为58.8Mpa的闻强石膏;刘长昕等(刘长昕、李德厚CN102249579)也用脱硫石膏为原料,采用蒸压法工艺,制得2小时抗折4.6Mpa,未提供干压数据,北京朗新明环保科技有限公司的周伟(周伟、徐立、范豫、马翔CN102992375A)等采用常压盐法工艺,以柠檬酸、酒石酸、乙酸钾等为转晶剂制得了干抗度为40Mpa的“超高强石膏”,湖北龙源石膏有限公司的高德武(高德武、余永忠、王兵CN103482892)以天然石膏为原料,采用蒸压法工艺,成功制得了 2小时抗折达6.5Mpa的α筒强石嘗。[0003]综上所述,国内的科研单位和企业在α高强石膏的科研和生产领域都做了不少工作,原料的来源既有天然石膏也有工业副产石膏,生产方法涉及到目前制备α高强石膏全部方法——水热法、蒸压法、常压盐法,然而无论是α高强石膏领域先进制备技术的研发还是α高强石膏生产线关键装备的开发,我国都与国际先进水平有着明显的差距,目前具有国际先进水平的α高强石膏的干强度最高可达90_100Mpa,对照国内众多厂家生产的α高强石膏,采用水热法生产的α高强石膏球磨改性后的二小时抗折一般小于6.5Mpa,或者干抗压强度一般小于 60Mpa,而采用蒸压法工艺生产的α高强石膏的干抗压强度仅在40Mpa左右徘徊。
[0004]针对上述现有技术的不足之处,本发明提供了一种高强度的α型石膏的制备方法。[0005]本发明的技术方案为:[0006]一种α型超高强石膏的制备方法,包括以下步骤:
[0007](I)过筛:用筛子筛除石膏原料中砂子以及碎石等杂质;
[0008](2)制浆:将过筛处理后的石膏原料加入水中,得到石膏悬浮液,控制石膏原料占石膏悬浮液的质量分数为20%~50%;在所述的的石膏悬浮液中加入转晶剂,经过搅拌,制成料浆;其中所述转晶剂包括苹果酸和苹果酸纳中的一种或两种,所述苹果酸和苹果酸钠中的一种或两种占石膏悬浮液中水的质量分数为0.05%~0.2% ;
[0009](3)水热反应:将配制好的料浆置于高压反应釜中进行水热反应,生成短柱状的α石膏晶体;
[0010](4)脱水:将在高压反应釜中转晶生成的短柱状α石膏晶体与水进行固液分离;[0011](5)干燥:将短柱状α石膏晶体在100~300°C环境下干燥,得到α石膏粉体;
[0012](6)球磨改性:将干燥后的α石膏粉体经过粉磨后得到α型超高强石膏。
[0013]进一步,所述的转晶剂还包括钛盐。
[0014]进一步,所述钛盐占石膏悬浮液中水的质量分数为0%~0.2%。
[0015]进一步优选,所述的钛盐为硝酸钛、四氯化钛、硫酸钛中的一种或多种。
[0016]进一步,所述的筛子的孔径为0.08~3mm。
[0017]进一步,所述制浆的过程中控制PH值为6~8之间。
[0018]进一步,所述水热反应中控制反应压力为0.15~0.35Mpa,反应温度为112~140°C,保温时间30~300min。
[0019]进一步,所述石膏原料为工业副产石膏和天然石膏。
[0020]本发明的有益效果为:
[0021](I)按照本发明所公开的方法,在所述石膏悬浮液中加入开发的新型高效转晶剂,解决了 α石膏晶体离开高温(大于100°C)和高压(大于0.1Mpa)环境后在固液分离设备内迅速水化导致固液分离设备无法正常运转的难题,从而提升了所述α型超高强石膏的产品力学性能,从实施例数据表中可表明,采用本发明的方法制备得到的α型超高强石膏的力学性能优异,强度高,球磨改性后两小时抗折强度一般达到6.5Mpa以上,最高可达9Mpa,干抗压强度大于60Mpa,最高可达90Mpa,另外还具有硬度大、轮廓清晰、耐水、防火的特点,将在航空航天、精密铸造、工艺美术等领域有着广阔的应用前景。
[0022](2)大量未能得到资源再生利用的工业副产石膏占用耕地,污染环境;与此同时因技术、设备的落后,大量高品位天然石膏被开采出来后只经过简单的粗放式的加工,不但破坏了石膏矿区的生态,也未能充分发挥优质天然石膏资源应有的价值,因此,对工业副产石膏和天然石膏进行深加工是一项极具社会和经济效益的工作。
[0023]图1为实施例3中短柱状α石膏晶体的X-射线粉末衍射图。
[0024]图2为实施例1制备的短柱状α石膏晶体的形貌。
[0025]下面将通过具体的实施例对本发明作详细的描述,通过各个实施例中的实验数据来说明本发明带来的显著的进步。
[0026]实施例1
[0027]—种α型超高强石膏的制备方法,用筛子筛除石膏原料中砂子以及碎石等杂质,优选筛子孔径为1_,石膏原料为工业副产石膏和天然石膏。
[0028]然后将石膏原料加入水中,得到石膏悬浮液,控制石膏原料占整个石膏悬浮液的质量分数为40% ;在所述的的石膏悬浮液中加入转晶剂,所述转晶剂为苹果酸和硝酸钛,所述苹果酸占石膏悬浮液中水的质量分数为0.05%,硝酸钛占石膏悬浮液中水的质量分数为
0.01%,经过搅拌,制成料浆,在整个制浆过程中通过HCl和NaOH控制PH值为6。
[0029]将配制好的料浆置于高压反应釜中进行水热反应,生成短柱状的α石膏晶体,控制反应压力为0.35Mpa,温度为115°C,保温时间200min,如图2所示为短柱状的α石膏晶体的形貌。
[0030]将在高压反应釜中转晶生成的短柱状α石膏晶体与水进行固液分离,将短柱状α石膏晶体在150°C环境下干燥,得到α石膏粉体。
[0031]将干燥后的α石膏粉体经过粉磨后得到α型超高强石膏。
[0032]实施例2
[0033]一种α型超高强石膏的制备方法,用筛子筛除石膏原料中砂子以及碎石等杂质,优选筛子孔径为1.5_,石膏原料为工业副产石膏和天然石膏。
[0034]然后将石膏原料加入水中,得到石膏悬浮液,控制石膏原料占整个石膏悬浮液的质量分数为50% ;在所述的的石膏悬浮液中加入转晶剂,所述转晶剂为苹果酸纳,所述苹果酸纳占石膏悬浮液中水的质量分数为0.1 %,经过搅拌,制成料浆,在整个制浆过程中通过HCl和NaOH控制PH值为6.2。
[0035]将配制好的料浆置于高压反应釜中进行水热反应,生成短柱状的α石膏晶体,控制反应压力为0.25Mpa,温度为120,保温时间210min。
[0036]将在高压反应釜中转晶生成的短柱状α石膏晶体与水进行固液分离,将短柱状α石膏晶体在120°C环境下干燥,得到α石膏粉体.[0037]将干燥后的α石膏粉体经过粉磨后得到α型超高强石膏。
[0038]实施例3
[0039]一种α型超高强石膏的制备方法,用筛子筛除石膏原料中砂子以及碎石等杂质,优选筛子孔径为1.7_,石膏原料为工业副产石膏和天然石膏。
[0040]然后将石膏原料加入水中,得到石膏悬浮液,控制石膏原料占整个石膏悬浮液的质量分数为40% ;在所述的的石膏悬浮液中加入转晶剂,所述转晶剂为苹果酸和四氯化钛,所述苹果酸占石膏悬浮液中水的质量分数为0.2%,所述四氯化钛占石膏悬浮液中水的质量分数为0.1 %,经过搅拌,制成料浆,在整个制浆过程中通过HCl和NaOH控制PH值为6.5。
[0041]将配制好的料浆置于高压反应釜中进行水热反应,生成短柱状的α石膏晶体,控制反应压力为0.15Mpa,温度为125,保温时间250min。
[0042]将在高压反应釜中转晶生成的短柱状α石膏晶体与水进行固液分离,将短柱状α石膏晶体在170°C环境下干燥,得到α石膏粉体.[0043]将干燥后的α石膏粉体经过粉磨后得到α型超高强石膏。
[0044]图1为本实施例中短柱状α石膏晶体的X-射线粉末衍射图。
[0045]横坐标为2theta角,纵坐标为X射线的衍射强度,通过物相检索表明,本发明所制得的短柱状石膏晶体为高纯度的α相CaSO4.0.5Η20。
[0046]实施例4
[0047]一种α型超高强石膏的制备方法,用筛子筛除石膏原料中砂子以及碎石等杂质,优选筛子孔径为2_,石膏原料为工业副产石膏和天然石膏。
[0048]然后将石 膏原料加入水中,得到石膏悬浮液,控制石膏原料占整个石膏悬浮液的质量分数为30% ;在所述的的石膏悬浮液中加入转晶剂,所述转晶剂为苹果酸,所述苹果酸占石膏悬浮液中水的质量分数为0.1 %,经过搅拌,制成料浆,在整个制浆过程中通过HCl和NaOH控制PH值为6.7。
[0049]将配制好的料浆置于高压反应釜中进行水热反应,生成短柱状的α石膏晶体,控制反应压力为0.35Mpa,温度为130,保温时间lOOmin。
[0050]将在高压反应釜中转晶生成的短柱状α石膏晶体与水进行固液分离,将短柱状α石膏晶体在200°C环境下干燥,得到α石膏粉体.[0051]将干燥后的α石膏粉体经过粉磨后得到α型超高强石膏。
[0052]实施例5
[0053]一种α型超高强石膏的制备方法,用筛子筛除石膏原料中砂子以及碎石等杂质,优选筛子孔径为2.5_,石膏原料为工业副产石膏和天然石膏。
[0054]然后将石膏原料加入水中,得到石膏悬浮液,控制石膏原料占整个石膏悬浮液的质量分数为20% ;在所述的的石膏悬浮液中加入转晶剂,所述转晶剂为苹果酸和苹果酸钠,所述苹果酸占石膏悬浮液中水的质量分数为0.1 %,所述苹果酸钠占石膏悬浮液中水的质量分数为0.05 %,经过搅拌,制成料浆,在整个制浆过程中通过HCl和NaOH控制PH值为7.2。
[0055]将配制好的料浆置于高压反应釜中进行水热反应,生成短柱状的α石膏晶体,控制反应压力为0.25Mpa,温度为135,保温时间150min。
[0056]将在高压反应釜中转晶生成的短柱状α石膏晶体与水进行固液分离,将短柱状α石膏晶体在220°C环境下干燥,得到α石膏粉体.[0057]将干燥后的α石膏粉体经过粉磨后得到α型超高强石膏。
[0058]
[0059]实施例6
[0060]一种α型超高强石膏的制备方法,用筛子筛除石膏原料中砂子以及碎石等杂质,优选筛子孔径为3_,石膏原料为工业副产石膏和天然石膏。
[0061]然后将石膏原料加入水中,得到石膏悬浮液,控制石膏原料占整个石膏悬浮液的质量分数为20% ;在所述的的石膏悬浮液中加入转晶剂,所述转晶剂为苹果酸,所述苹果酸占石膏悬浮液中水的质量分数为0.05%,经过搅拌,制成料浆,在整个制浆过程中通过HCl和NaOH控制PH值为7.5。
[0062]将配制好的料浆置于高压反应釜中进行水热反应,生成短柱状的α石膏晶体,控制反应压力为0.25Mpa,温度为140,保温时间280min。
[0063]将在高压反应釜中转晶生成的短柱状α石膏晶体与水进行固液分离,将短柱状α石膏晶体在250°C环境下干燥,得到α石膏粉体.[0064]将干燥后的α石膏粉体经过粉磨后得到α型超高强石膏。
[0065]表1为以上六个实施例中具体的工艺参数以及每个实施例制备出来的α型超高
强石膏的各项力学性能参数。
[0066]
α型超高强石膏的制备方法
- 专利详情
- 全文pdf
- 权力要求
- 说明书
- 法律状态
查看更多专利详情
下载专利文献
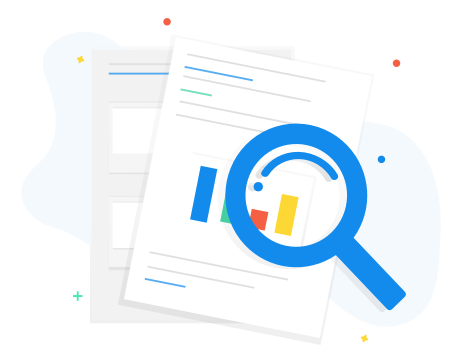
下载专利
同类推荐
-
康德余, 胡盼盼孙红芳, 杨庆兰宋卫, 高品孙红芳, 杨庆兰孙红芳, 杨庆兰
您可能感兴趣的专利
-
武雄飞
专利相关信息