专利名称:工具式筒模及跟进平台的制作方法 现有的井道模以板面构造分,有铰链井道模和刚性角井道模两种;以收放原理分,有中心操纵杆反正扣收放的,有中心操纵杆伞齿轮收放的两大类。铰链井道模由于构造的缺陷和使用中的不便,当前正逐步为刚性角井道模所取代。但现有的刚性角井道模仍有诸多缺陷主要表现是1、井道模四片墙板靠中心操纵杆连接固定,再由刚性角模定型。在未安装刚性角模前,四片墙模的空间位置实际上并未定型。从结构平面受力分析可以看出,每片与中心操纵杆只是铰接固定,因此它不是一个理想连接形式。2、刚性角模与井道墙模靠闩板连接,无论井道模安装与拆除,都需对闩板螺丝逐一进行二次调整,不利于提高施工工效,而且螺丝容易锈蚀。3、结构造型局限性大,井道断面稍有变化,整个模板必须重新加工,不利于重复利用,不利于批量生产,不利于开展模板租赁。另外,现有与井道模支模匹配的支承平台——跟进平台,也不够完善跟进平台在提升过程中经常碰撞井壁,使提升很不顺利;跟进平台的支腿预留孔在混凝土墙体内的设置至今未形成工具化的程序,仍然靠施工单位在现场临时支设,不仅留置困难(包括躲避竖筋密集的难度),而且预留位置受混凝土浇灌的影响,经常出现位移,直接影响了跟进平台的准确就位。现有跟进平台在高度及水平度的调整装置手段上,至今也很不完善,给筒模的就位、找正工序增添了不必要的麻烦,以至这一技术在80年代问世以来,至今没有形成系统、配套的工具和工序。
本发明的目的在于提供一种工具式筒模及跟进平台,解决井道模安装与拆除都需二次调整、施工工效较低的技术问题;解决井道断面稍有变化,整个模板必须重新加工,不利于重复利用和开展模板租赁的问题;另外,解决跟进平台在提升过程中经常碰撞井壁,其支腿预留孔留置困难、跟进平台就位不易准确、不易调整的问题。本发明的技术方案由筒模和模板支承架连为一整体,其特征在于筒模由四组定型边角组合模架和四块非定型的填充板由背楞拉接成型;每组边角组合模架分别由一个定型的刚性角模和两块呈135°夹角的拐角梁的定型板连接而成;刚性角模的底边与拐角梁滑块在水平方向连接,拐角梁滑块的长边延长线与筒模对角线呈45°夹角;模板支承架由中心收放架与传力架之间由可更换长度的水平拉杆连接,中心收放架及水平拉杆,其平面布局与筒模对角线重合;带拐角梁的定型板与传力架由滑块连接,每副传力架对应一块刚性角模,每副传力架由上、下两对叉形支承腿在竖向连为一体,成为三维传力架;四副传力架在上、下叉形支承腿部位,由对角形的八根水平拉杆与中心收放架连接,中心收放架由中心杆、八根Y形收放杆铰接而成。上述传力架的叉形支承腿脚部各连接一个定型板滑块,定型板滑块镶入固定于定型板的槽形滑轨中。上述定型板滑块由滚珠和箍住滚珠的滑体组成。上述刚性角模在与定型板相接触的缝隙内,上、下分别固定连接两个拐角梁导轨,拐角梁滑块镶入其间,刚性角模与定型板由拐角梁滑块连接。上述拐角梁滑块由滚珠和箍住滚珠的滑体组成。
上述定型板和刚性角模在与滚珠接触的位置设有凹形滚珠滚道。
上述在筒模两侧设有为跟进平台支腿预留孔成型的翻转模盒,其翻转模盒平面及高度位置与跟进平台支腿至结构板顶高度一致。
这种与工具式筒模配套的跟进平台,在平台四角的下方分别连接有支腿,其特征是平台四角的底部分别由轮架连有顶力弹性导向轮,轮架横向连有弹簧,弹簧动端在井道阴角方向顶住顶力弹性导向轮;平台两边的底面连接托梁,托梁上连接并支承四个调平螺杆,托梁的两端连接有支腿靴套,支腿靴套上连接有斜撑支腿。
上述支腿靴套的里侧设有弧形止挡。
上述斜撑支腿对称连有配重,形成人字形支腿。
有益效果1、工具式筒模所有定型部件可提前预制,工厂化生产,筒模断面的变更仅需更换三种非定型部件即可;2、每个传力架连接两块定型板,构成筒模的直角平面和稳定的立体空间;3、筒模的收放功能除中心收放架外,重点体现在两种滑块的构造——由线性传递侧向力;4、在筒模的两侧设有跟进平台支腿预留孔翻转模盒,为跟进平台准确就位提供了保证。
跟进平台四角的下方分别设有轴线与平面成45°弹性顶力弹性导向轮,在弹簧的作用下,顶力弹性导向轮与井道阴角始终处于贴紧状态,使平台在提升过程中能自动找中,提升自如;2、平台两侧下口分别设有在提升过程中能自动入槽的铰接支腿,其特点是(1)、该支腿采用重力平衡原理使支腿提升过程中始终处于外张状态,当平台上升至墙体预留孔时能自动入槽,墙体预留孔由筒模翻转模盒实现。
(2)、铰接支腿与平台的连接由定型支腿靴套实现,该支腿靴套通过螺栓与平台固定。
(3)、在支腿靴套中设有弧形止挡,根据支腿的设计角度及止挡的受力需要确定其空间位置,确保平台支座合理受力和有利于减少加工误差。
3、设有四个调平螺杆,既可整体调高由于筒模与跟进平台之间匹配的不佳而产生的竖向间隙(或竖向尺寸的重叠),又可弥补支腿留洞高低误差的缺陷。
4、以上三项均为定型活动装置,确保该产品重复利用和定型化批量生厂。
跟进平台在现行平衡锤支腿的基础上,对平台底面四角增加顶力弹性顶力弹性导向轮,直接顶紧混凝土井壁的阴角,使平台在提升运行过程中始终保持与混凝土井壁预定间歇和最佳找中状态,消除了塔吊提升过程中的碰撞现向;为确保就位后的平台有可靠的水平度,在平台内设有四个调平螺杆;改进了平衡锤支腿的构造连接;以上三项设置均为定型活动装置,确保该产品重复利用和定型化批量生厂。
井道模安装与拆除迅速,不需要二次调整,施工工效大幅提高,工具式模板大部分是定型标准件,可提前预制,工厂化生产,避免材料浪费,有利于重复利用、开展模板租赁、提高工程质量;跟进平台在提升时不会经常碰撞井壁,支腿预留孔就位准确、高度及水平度容易调整。
图1是实施例一中工具式筒模的平面结构示意图;
图2是图1的A-A剖面图;图3是图1的B-B剖面图;图4是实施例二中工具式筒模的平面结构示意图;图5是工具式筒模平面收放关系示意图;图6是传力架、定型板滑块、定型板连接的平面结构示意图;图7是传力架、定型板滑块、定型板连接的立面结构示意图;图8是刚性角模、拐角梁滑块、定型板连接的平面结构示意图;图9是图8的b-b剖面示意图;图10是定型板滑块连接的结构示意图;图11是拐角梁滑块连接的结构示意图;图12是拐角梁滑块的结构示意图;图13是翻转模盒工作原理示意图;图14是筒模组装程序(1)、(2)、(3)步骤的示意图。
图15是跟进平台的结构示意图;图16是图15的A-A剖面图;图17是图15的B-B剖面图;图18是图17的C-C剖面示意图;图19是支腿靴套的主视图;图20是图19的A-A剖面示意图。
图21是调平螺杆平面位置示意图;图22是图21的节点放大图;图23是图22的b-b剖面示意图;图24是图22的a-a剖面示意图。
图25是跟进平台提升至就位过程示意图。
图26是双筒井道断面的支腿设置位置示意图;图27是单筒双门井道断面的支腿设置位置示意图;图28是单筒井道断面的支腿设置位置示意图。
1-刚性角模、2-定型板、3-传力架、4-定型板滑块、5-拐角梁滑块、6-中心收放架、7-填充板、8-背楞、9-水平拉杆、10-翻转模盒、11-平台、12-托梁、13-顶力弹性导向轮、14-斜撑支腿、15-调平螺杆、16-支腿靴套、17-止挡、18-弹簧、19-横肋、20-盖梁、21-拐角梁导轨、22-槽形滑轨、23-叉形支承腿、24-中心杆、25-Y形收放杆、26-滚珠、27-滑体、28-配重、29-轮架。
实施例一本发明由工具式筒模及与之配套的跟进平台两部分组成。
一、工具式筒模工具式筒模由由筒模和模板支承架连为一整体参见图1、2、3,筒模由四组定型边角组合模架和四块非定型的填充板7由背楞8拉接成型;每组边角组合模架分别由一个定型的刚性角模1和两块呈135°夹角的拐角梁5的定型板2连接而成;刚性角模1的底边与拐角梁滑块5在水平方向连接,其拐角梁滑块的长边延长线与筒模对角线呈45°夹角;模板支承架由中心收放架6与传力架3之间由可更换长度的水平拉杆9连接,中心收放架6及水平拉杆9,其平面布局与筒模对角线重合;带拐角梁的定型板2与传力架3由拐角梁滑块5连接,每副传力架3对应一块刚性角模1,每副传力架由上、下两对叉形支承腿23在竖向连为一体,成为三维传力架;四副传力架3在上、下叉形支承腿23部位,由对角形的八根水平拉杆9与中心收放架6连接,中心收放架6由中心杆24、八根Y形收放杆25铰接而成。
上述传力架3的叉形支承腿脚部各连接一个定型板滑块4,定型板滑块4镶入固定于定型板的槽形滑轨22中。定型板滑块4由滚珠26和箍住滚珠的滑体27组成。刚性角模1在与定型板2相接触的缝隙内,上、下分别固定连接两个拐角梁导轨21,拐角梁滑块5镶入其间,刚性角模1与定型板2由拐角梁滑块5连接。拐角梁滑块5由滚珠26和箍住滚珠的滑体27组成。定型板2和刚性角模1在与滚珠接触的位置可以设有凹形滚珠滚道。
在筒模两侧设有为跟进平台支腿预留孔成型的翻转模盒10,其翻转模盒平面及高度位置与跟进平台支腿至结构板顶高度一致。
二、跟进平台这种与工具式筒模配套的跟进平台,平台11四角的底部分别由轮架29连有顶力弹性导向轮13,轮架横向连有弹簧18,弹簧动端在井道阴角方向顶住顶力弹性导向轮13。
平台两边的底面连接托梁12,托梁上连接并支承四个调平螺杆15,托梁的两端连接有支腿靴套16,支腿靴套上连接有斜撑支腿14。支腿靴套的里侧设有弧形止挡17。
上述斜撑支腿14对称连有配重28,形成人字形支腿。
在实施例一中,传力架3在水平向为等腰梯形。
实施例二传力架3在水平向呈等腰三角形。
本发明的工作过程详细说明一、工具式筒模参见图1-13整个筒体由定型组合体与非定型部件两大块组成,定型组合体由两个组合单元构成,一是边角组合单元,包括如下部件刚性角模1,定型板2,传力架3,定型板滑块4,拐角梁滑块5,平台支腿预留孔内的翻转模盒10共六种定型部件;二是中心收放架6。
非定型部件包括填充板7,背楞8,水平拉杆9等三种部件。非定型部件由井道断面大小确定。
参见图5,筒模的收放功能是通过定型板滑块4实现的,当中心收放架6内收时,在水平拉杆9的带动下,四个传力架将同时沿45°。方向向中心内收,由于定型板滑块4的作用——只能横向传力、纵向滑移,因而当传力架3内收时,与定型板滑块4连接的定型板2也就随之内移,在背楞8的作用下,筒模的四片墙板——定型板2及填充板7也就同时内收,其收放关系是当传力架3沿45°方向内收距离为a时,则墙板的墙板移动距离为1.414a。
参见图6、7,传力架3的两斜边两侧的底部分别设有一个定型板滑块4,两个滑块与筒模平面对角线成45°夹角,在其镶入筒模定型板2后,两块定型板2与传力架3就必然形成一个直角平面空间组合体。当四个组合体按照工程需要的尺寸定位组拼,并镶入填充板7、背楞8后,整个筒体就形成了一个稳定的空间结构,而不需要借助刚性角模的拉接。
参见图8、9,定型板2与刚性角模1相接触的一侧,上下分别设有一组与平面夹角成135°的拐角梁导轨21,并通过拐角梁滑块5与刚性角模1连接,作为悬挂刚性角模1的支承和筒模收放时刚性角模收进或退出的滑轨。
参见图10,刚性角模1与定型板2板面结合处采用高低口搭接,为避免定型板2内收时受刚性角模1接口的阻碍,定型板2在接口处可加工45°坡口,若因设备能力限制,也可留出一个板厚的间隙,在筒模就位后用胶条或腻子嵌平,以免在结构墙面形成水泥楞。
定型板2具有如下两个特征一是在与刚性角模1相接触的一侧上下分别设有一组与平面夹角成135°的拐角梁导轨21,作为悬挂刚性角模1的支承和筒模收放时刚性角模收进或退出的滑轨,二是与刚性角模1相接触的一侧有一凹口,作为与刚性角模1搭接的高低口,以防漏浆。为避免定型板内收时受刚性角模接口的阻碍,定型板在接口处可加工45°坡口,在筒模就位后用胶条或腻子嵌平。
参见图10、11,定型板滑块4及拐角梁滑块5均以滚珠26为媒介,通过滑体27形成挡圈,使之在槽形滑轨22和拐角梁导轨21内定位,形成线性轴承,以确保被连接的部件横向能传递拉力或推力,纵向滑行自如。刚性角模1与定型板2的连接主要靠定型板滑块4来实现,由图10可知,盖梁20通过滚珠26悬挂在拐角梁导轨21上,并通过拐角梁滑块5使之连为一体。刚性角模1与定型板2板面结合处采用高低口搭接;与定型板2高度对应的位置设有横肋19及盖梁20,作为刚性角模1与定型板2连接的悬挂支点和拐角梁滑块5的拐角梁导轨21。
刚性角模在直角三角形底边处设有盖梁20,其断面为倒L形,以滚珠为支承悬挂在拐角梁上,并通过拐角梁滑块将刚性角模在与左右两块定型板紧密连接。与滚珠接触的盖梁及拐角梁在筒模收放过程中将互为滑轨沿梁的轴向滑移。
参见图12,定型板滑块4及拐角梁滑块5的具体构造在被连接部上设有两条里侧为斜坡口或高低口的固定滑道11.1,在两条固定滑道间设有箍住滚珠26的滑体27,滑体27形成条型活动挡圈,滑体27两侧设有与固定滑道里侧相反的坡面或高低口,滑体内与滚珠接触处有一与滚珠直径同一弧度的圆孔,使滚珠26在自由状态下不会脱落,当两块连接部件与滚珠26贴紧后,被连接的部件就能横向传递拉(推)力,纵向滑行自如。为滑动轨迹更加可靠,定型板和刚性角模在与滚珠接触的位置可以设有一条深度≤钢珠半径的纵向凹形滚珠滚道,将有助于提高滑块的耐久性。
参见图13,平台支腿预留孔翻转模盒10的平面位置参见图2,高度位置与跟进平台支腿相适应。平台支腿预留孔内的翻转模盒10的位置及与筒模支承平台支腿至结构板顶高度一致,可在筒模安装就位后翻出,墙体内就能准确留出与支承平台支腿外型相适应的槽穴,从而保证四个支腿能准确入槽。当筒模内收拆除时,应将翻转模盒10提前翻入筒模内,如图10虚线示,以便筒模吊出。
如图14所示整个筒体的组合程序的步骤(1)、根据工程任务确定的井道断面大小将定型板2、传力架3定型滑块4组合拉接定位,(2)、安装填充板7、背楞8及中心收放架6、水平拉杆9使整个筒体连成整体,(3)、安装角模1及拐角梁滑块5,至此整个筒模组装完毕。
二、跟进平台工作过程参见图15-28如图15-20所示,跟进平台由以下五个部分组成平台11,托梁12,顶力弹性导向轮13,斜撑支腿14,调平螺杆15。平台11通过调平螺杆15坐落于托梁12上,并通过调平螺杆15使平台11与托梁12连成一体。斜撑支腿14通过支腿靴套16固定于托梁12的两端,承受整个跟进平台及上部筒模的全部荷载。斜撑支腿14与托梁12通过活动铰连接,斜撑支腿里侧设有配重28,使斜撑支腿14始终处于外张状态,确保平台在提升过程中能自动入槽。斜撑支腿14的外侧设有弧形止挡17,确保斜撑支腿14按设计角度受力。平台底面四角分别设有顶力弹性导向轮13,与平台平面成45°布置,顶力弹性导向轮13的背面的轮架设有弹簧18,使顶力弹性导向轮13始终处于外张状态,始终顶紧已成型的混凝土井壁的四个阴角。在提升时,顶力弹性导向轮在配重28带动下下垂,跟进平台周边与混凝土井壁保持预定间歇,平台提升无阻力,并能自动找中。
参见图21-24,调平螺杆15在每个托梁上各设两个,跟进平台就位后,通过水平尺检查跟进平台的平整度,既可调整井壁留洞高低的误差又可调整平台的整体高低,以保证井道模安装标高及垂直度准确。该装置同时还兼有连接跟进平台11与托梁1 2的功能。
上述所有配件与跟进平台均为工具式连接,当跟进平台平面变更时,所有配件均可拆除重新使用。
如图25所示,当井道模拆除后,塔吊可直接将平台11跟进上提,由于四角顶力弹性导向轮13的推力,跟进平台四周将保持与混凝土井壁均衡的间歇,因此塔吊在提升过程中将不会有什么阻力。待跟进平台提至接近并道上口时,由于斜撑支腿14里侧配重的作用,斜撑支腿14将在混凝土井壁的预留洞穴处自动入槽,塔吊回车下落时平台也就自动完成就位。
如图26、27、28所示不同类型的井道平台支腿的设置形式。
本发明涉及一种工具式筒模及跟进平台,筒模周边由四组定型边角组合模架和四块非定型的填充板通过背楞拉接成型;每组边角组合模架分别由一个定型的刚性角模和两块带拐角梁的定型板组成。刚性角模的底边与拐角梁滑块在水平方向滑动连接;带拐角梁的定型板与传力架由定型板滑块连接成型;中心收放架通过可更换长度的水平拉杆与传力架连接,实现筒模的收放功能。筒模断面的变更,仅需更换填充板,背楞及水平拉杆三种非定型部件即可;跟进平台四角分别设有顶力弹性导向轮,使平台在提升过程中始终保持与混凝土井壁预定间歇和最佳找中状态;为确保就位后的平台有可靠的水平度,在平台内设有四个调平螺杆;确保该产品重复利用和定型化批量生厂。
工具式筒模及跟进平台制作方法
- 专利详情
- 全文pdf
- 权力要求
- 说明书
- 法律状态
查看更多专利详情
下载专利文献
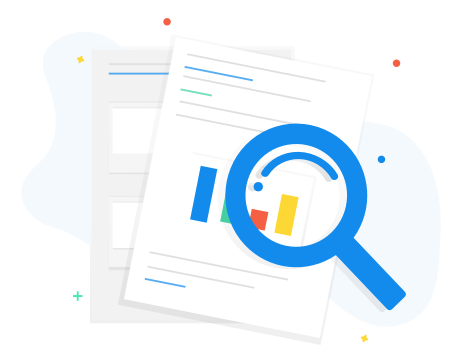
下载专利
同类推荐
-
马永乐马永乐H.J.佩德森, J.A.汉森康斯坦丁诺斯·尼蔻康斯坦丁诺斯·尼蔻吴正新, 吴彦毅安井英明, 丸山刚
您可能感兴趣的专利
-
王小雨吕江, 甘晓东姜国庆姜国庆刘化荣刘化荣
专利相关信息
-
陈晓东吉村贵喜吉村贵喜吉村贵喜吉村贵喜