专利名称:建筑物桁架整体提升方法及其设备的制作方法 由于钢材的强度比钢筋混凝土高,重量比钢筋混凝土要轻,在高层建筑特别是在一些大型的场馆建筑中被广泛采用。在建筑面积过万平方米的一些大型场馆中大多都是采用钢结构,但是钢结构技术复杂,施工难度大,施工成本高,而且施工质量,施工速度,施工成本上都不能满足要求。例如一个占地面积为12多万平方米的体育馆,其建筑面积超过4万平方米,其半椭球型钢结构屋盖的展开面积近4.4万平方米(+0.2米标高处投影椭圆长轴328米,短轴224米),其屋盖中心最大高度约54米,其详细结构可参见图1。覆盖整个场馆空间的屋盖主体钢结构为纵向两榀300多米跨的大跨度空间主桁架、近30榀最大跨度200多米的纬向次桁架和环向桁架钢性联接形成,整个屋盖由钢柱支撑。在这样的一个巨型建筑物中两榀纵向主桁架的安装为施工的关键工序,也是安装难度最大的一个工序,其中主桁架的断面图可以参见图2。而通常所采用的这样桁架的安装方法为分段吊装拼接法即先根据起吊设备的能力在地面将主桁架按安装顺序一段一段拼接成若干个吊装分段单元,然后分点搭设支撑拼接胎架,用大型吊车将分段单元吊装至支撑拼接胎架上按安装位置摆放好并与下一个相连分段单元拼装焊接,完成整个主桁架的安装工作,可以详见图3所示。但是常规方案存在以下问题支撑拼接胎架用料大,且胎架材料重复利用率很低;需大吨位的大型吊机且费用很高;高空作业施工效率低、安全性差;高空拼焊施工难度大,质量不易控制;施工时间长受环境因素影响大(如大风,降水等)构件高空拼接需采取专门措施防止构件倾覆;拼装操作平台搭设工作量大,耗费人工。
本发明的目的是提供一种节省胎架用料,不需使用巨型吊机,减少高空作业量,提高质量,减少工作量节省人工的整体提升方法。本发明的目的是提供一种在整体提升过程中为实现同步提升的监测控制方法,以及桁架落地端滑移的处理方法。本发明的目的提供一种桁架整体提升方法中所使用的设备。本发明的目的是提供一种在整体提升中实现落地端水平移动和提升端垂直移动同步进行的传感控制系统。
本发明的目的是提供一种在整体提升中落地端滑移装置。根据本发明的一方面提供一种建筑物桁架整体提升的方法,其特征在于将主桁架在地面拼装为多个单元;制作并安装相应的提升架;在提升架上设置缆风系统,在相应位置安装液压提升设备;安装桁架落地端滑移装置;以主控计算机控制液压同步提升,并确保落地端的水平移动与提升端的垂直移动同步进行;空中对接口就位后拆除落地端滑移装置,提升并固定落地端;对空中对接口实施拼接。
更可取的是,其中主桁架以中间为界,在地面将其拼装为两个单元。
更可取的是,由计算机控制液压同步提升系统对桁架进行同步提升,该计算机控制液压同步提升系统包括钢绞线;作为承重部件的提升油缸集群;作为驱动部件的液压泵站;监测传感器;作为控制部件的计算机;液压系统采用比例同步法,传感器将监测提升油缸的位置、载荷,提升中桁架的空中姿态及应力应变情况,并将这些监测到的信息传给计算机,由主机来确定下一步的动作。
更可取的是,其中由电气控制使其同步的卷扬机组成的滑移牵引装置在提升过程中对落地端滑移装置实施牵引,设置落地端滑移导向装置,设置防止桁架外移的牵引装置,使得提升动作和滑移动作协调进行。
更可取的是,其中桁架提升过程中提升钢绞线的偏斜度不大于8°。
根据本发明的另一方面提供一种建筑物桁架整体提升的设备,该设备可以实现前一方面中所述的提升方法,并包括提升架,提升架缆风系统,液压提升装置,落地端滑移装置,传感监测系统,主控计算机,提升架上设置提升架缆风系统及液压提升装置,以便将在地面拼装成的桁架单元的一端提升至预定高度,桁架单元的另一端在落地端滑移装置上并在提升过程中平移,传感器监测系统检测整个的提升过程,并将检测结果实时传递至主控计算机中,主控计算机对整个的提升过程进行控制。
更可取的是,其中液压提升装置采用比例同步技术,提升吊点中油缸可以并联使用。
更可取的是,其中落地端滑移装置包括落地端滑移导向装置,滑移牵引装置和防止桁架外移的牵引装置,滑移导向装置由涂有硅脂滑移导轨和滑移小车组成,滑移小车由钢板焊接而成,将主桁架支点放置在滑移小车上。
更可取的是,其中传感监测系统包括使用经纬仪跟踪钢绞线的水平偏移量,并设置边界值不大于8°,在吊点下面设置激光测距仪,随时测量主桁架提升高度,并传送给主控计算机依照一定的控制算法,来决定相应比例阀的控制量,实现跟随提升吊点和主令提升吊点的位置同步。
更可取的是,其中设置有应力应变监测系统,采用大型有限元结构分析程序ANSYS软件进行计算分析,对桁架主要受力杆件和提升架在提升过程中的应力应变进行实时监控。
先将主桁架在地面拼装成两个吊装分段单元(例如,两个分段单元加上相连的中间次桁架重量约2800吨),然后采用在提升架上放置液压提升装置,将两个吊装分段单元同步整体起吊,进行空中合拢对口,从而完成主桁架安装工作。两种方案的对比和整体提升安装方案的优点由于拼装高度下降(指胎架高度),整体吊装方案与常规方法相比,胎架材料节省75%(胎架平均高度由20米降为5米),即可节约钢材,胎架的制作费用相应降低60%以上。吊机吊装能力从500吨降至250吨,从而机械费降低40%以上。最主要的是提高了工效(工效提高50%以上)、施工质量得到保障及大大降低了施工中的不安全性。
图1所示为屋盖系统平面图;图2所示为桁架的断面图;图3所示为常规采用的分段吊装拼接方案的示意图;
图4所示为整体提升方案示意图;图5所示为整体液压提升安装方案的工艺流程图;图6所示为整体提升同步控制的方框图;图7所示为落地端滑移装置的示意图;图8所示为落地端支点的加固示意
采用主桁架1地面拼装后整体提升就位的方法。整体提升安装方案是先将主桁架1在地面拼装成两个吊装分段单元(两个分段单元加上相连的中间次桁架2重量约2800吨),然后采用在提升架6上放置液压提升装置(由于液压提升装置为施工领域的常用装置,为使附图清楚附图4中就没有一一给出),再将两个吊装分段单元7和8同步整体起吊,进行空中合拢对口,从而完成主桁架1的安装工作,参见附图4所示。
主桁架1的两个吊装分段单元7和8使用多个胎架9支撑并在地面完成拼装,由于拼装高度由42米降到了11米(指胎架高度),整体吊装方案与常规方法相比,胎架材料节省75%(胎架平均高度由20米降为5米),即可节约钢材600吨,胎架的制作费用相应降低60%以上。吊机吊装能力从500吨降至250吨,从而机械费降低40%以上。最主要的是提高了工效(工效提高50%以上)、施工质量得到保障及大大降低了施工中的不安全性。
主桁架1以及相连中间次桁架2拼装完后,重量约为2800吨,提升所用提升井架6根据提升就位需要,提升井架6的高度应在65米左右,由于安装现场各种环境、气候及天气的因素的考虑,因此,风载是必须加大考虑的。还有,由于提升井架6承受载荷大,还必须考虑提升井架6因基础的不均匀沉降对其影响。另外根据现场情况,充分利用工程原有材料,以提高材料的重复利用率,降低成本,提升井架6设计如图6所示。
主桁架1为拱形结构,两端落地,吊点选择在中间,可以降低拼装高度,减小提升架横梁的悬臂长度,保证提升井架6的承载均衡,缆风系统对称受力。由于在主桁架1提升的过程中在不断地向前移动和转动,而提升井架6不能倾斜摆杆,这就要求选择的吊点位置在主桁架1的提升过程中不能有较大的水平位移,即在提升过程中尽量保持提升钢绞线的垂直。如果按钢铰线垂直度不大于8°(最好是小于2°),当小于2°时来计算,在主桁架1提升至最高处时,吊点水平位移不能超过220mm,经过对提升井架6位置及主桁架1结构特点进行深入考虑,决定将吊点位置设在主桁架上弦杆上的中间两个节点处,对此在此就不再详述。
由于两榀主桁架中间用次桁架联接,在主桁架的提升过程中,如果两榀主桁架不同步,构件在吊装过程中将产生变形,这是不允许的,为保证构件在吊装过程中不产生变形,这就要求提升机构具备同步功能,因此,在本方案中采用计算机控制液压同步提升系统对主桁架进行提升。
计算机控制液压同步提升系统可以保证桁架在提升过程中的不正常变形,该系统是由钢绞线、提升油缸集群(承重部件)、液压泵站(驱动部件)和传感检测及计算机(控制部件)等几个部分组成,参见图7。
钢绞线及提升油缸是系统的承重部件,用来承受提升主桁架1的重量。可以根据提升重量(提升载荷)的大小来配置提升油缸的数量,每个提升吊点中油缸可以并联使用。在此采用的提升油缸为4台350吨、4台200吨,均为穿芯式结构。钢绞线采用高强度低松弛预应力钢绞线,公称直径为15.24mm,截面积为140mm,抗拉强度为1860N/mm,破断拉力为260.7KN,伸长率在1%时的最小载荷221.5KN。液压泵站是提升系统的动力驱动部分,它的性能及可靠性对整个提升系统稳定可靠工作影响最大。在液压系统中,采用比例同步技术,这样可以有效地提高整个系统的同步调节性能。传感检测主要用来获得提升油缸的位置信息、载荷信息和提升时整个主桁架空中姿态信息,并将这些信息通过现场实时网络传输给主控计算机。这样主控计算机可以根据当前网络传来的油缸位置信息决定提升油缸的下一步动作,同时,主控计算机也可以根据网络传来的提升载荷信息和主桁架姿态信息决定整个系统的同步调节量。
主控计算机除了控制所有提升油缸的统一动作之外,还必须保证各个提升吊点的位置同步,只有这样才能保证各吊点受力均衡。在提升体系中,设定主令提升吊点,其它提升吊点均以主令吊点的位置作为参考来进行调节,因而,都是跟随提升吊点。主令提升吊点决定整个提升系统的提升速度,可以通过泵站的流量分配和其它因素来设定提升速度。根据本次提升系统的设计,最大提升速度控制在5米/小时左右。主令提升速度的设定是通过比例液压系统中的比例阀来实现的。
在提升系统中,每个提升吊点下面均布置一台激光测距仪,这样,在提升过程中这些激光测距仪可以随时测量当前的主桁架高度,并通过现场实时网络传送给主控计算机。每个跟随提升吊点与主令提升吊点的跟随情况可以用激光测距仪测量的高度差反映出来。主控计算机可以根据跟随提升吊点当前的高度差,依照一定的控制算法,来决定相应比例阀的控制量大小,从而,实现每一跟随提升吊点与主令提升吊点的位置同步。
为了提高提升系统的安全性,在每个提升吊点都布置了油压传感器,主控计算机可以通过现场实时网络监测每个提升吊点的载荷变化情况。如果提升吊点的载荷有异常的突变,则计算机会自动停机,并报警示意。
由于主桁架1在提升过程中,其落地端10随之在不断地进行水平移动,因此需要对主桁架落地端10进行滑移处理,以保证主桁架1提升的顺利进行。主桁架1在提升过程中落地端随之处于水平滑移状态,由于提升锚具要求提升钢绞线偏斜角度不大于3°,同时钢绞线偏斜角度过大产生的水平力对提升井架6以及缆风系统受力不利。因此需在主桁架1提升的同时对落地端进行水平牵引滑移,滑移的平稳、轨迹的正确性以及滑动摩擦力将直接影响到整个提升过程的安全性以及主桁架定位的准确性。主桁架落地端10每个支点载荷约为200吨,共8个支点,如果采用传统滚杠作滚动滑移,根据计算,每榀主桁架单侧水平拉力约60吨,而且要求滚杠摆放精度高,否则主桁架落地端10滑移将会偏离正确位置,给主桁架1在Y轴方向定位造成极大困难。为改善上述不足,采用新型滑移材料聚四氟乙烯板来代替滚杠。
参见图8,滑移装置主要包括落地端滑移导向装置、滑移牵引装置及防止两榀主桁架外移的牵引装置等。滑移导向装置包括滑移导轨和滑移小车12,滑移导轨主要是20mm钢板14和1mm厚材质为1Cr18Ni9Ti的不锈钢板13铺成,不锈钢板13面上涂上滑移润滑用的硅脂;滑移小车由钢板14焊接而成,将主桁架支点11放置在滑移小车12上。此时单榀主桁架单侧水平拉力为12吨,由于采用聚四氟乙烯滑移板作滑移材料,使得牵引力大大减小,且导向也容易实现,即在增设导向装置后,导向问题就获得了解决。滑移过程中为保证提升和滑移的同步协调进行,滑移牵引装置,我们采用规格为H32*4D的32吨滑轮组及由电气控制其同步的卷扬机组成,共4组。
主桁架提升就位过程中,需要设置合理安全的吊点、支点及顶点。其吊点结构为主桁架在提升过程中吊点处存在转动,因此将吊点设置为铰支连接,吊点如图十所示。在吊点处,经计算,吊耳下方腹杆应力较大达280MPa,需作加强处理。加强方案是在腹杆处增加4条筋板。此时应力值为220MPa。吊点周围其他杆件受力也均符合安全应力要求,吊耳强度验算略,以上说明吊耳设置可行。
在大型钢结构的传统拼装过程中,尤其对长形构件最终合拢对口时一般设中间嵌补段,用以调节构件分段拼接过程中的尺寸偏差,最终保证构件的整体尺寸。本工程项目中桁架跨距有320米左右,整体造型奇特为空间三向弯扭,总重量约2800吨,整体结构弹性大,给主桁架最终空中合拢对口,保证主桁架整体尺寸带来了很大难度。采用中间嵌补段可以很好的控制调整主桁架整体拼装尺寸,保证质量,但同时也带来了需要另外的大型吊机、空中对口工作量增加一倍、安全性能降低等诸多不利。我们权衡利弊,决定取消中间嵌补段。为此,在主桁架地面拼装过程中我们应用了激光全站仪,对主桁架分段的拼装进行精确的定位。根据设计院的设计模型,将主桁架的空中状态调整到地面拼装状态,对关键节点的三维坐标进行量取,取得设计的理论值,然后据此应用全站仪对实际拼装尺寸进行测量和精确的调整,从而保证了主桁架分段以至整体的定位尺寸,达到了质量控制标准。
参照图5来详细说明主桁架整体起吊采用液压提升方法及其工艺流程。首先,在地面将主桁架完成拼接,制作安装提升架,设置提升架缆风系统,安装液压提升设备,安装应力应变检测系统,安装桁架落端滑移装置并进行应力应变监测和过程数据统计分析,然后是加载提升和超提,拆除滑移装置固定落地端,空中对口拼接,最后是拆除提升架,完成桁架的整体提升安装任务。
主桁架在提升过程中吊点处存在转动,因此将吊点设置为铰支连接,吊点如图十所示。在吊点处,经计算,吊耳下方腹杆应力较大达280MPa,需作加强处理。加强方案是在腹杆处增加4条筋板。此时应力值为220MPa。吊点周围其他杆件受力也均符合安全应力要求,吊耳强度验算略。以上说明吊耳设置可行。
主桁架在提升时落地端存在集中载荷,为此需对主桁架落地端支点及支点上部杆件进行加固,落地端支点加固。支点上方腹杆需要加固,未加固时应力为260MPa,加固后应力降为210MPa,满足结构安全应力值。腹杆加固方法与吊点下方腹杆加固相同。
主桁架提升到位后,需要拆除主桁架落地端的滑移小车及滑道等,安装落地端支座,此时需要用千斤顶顶起主桁架落地端才能进行。因此,需要在主桁架落地端千斤顶顶升处设置顶点,顶点位置应设在主桁架节点上,且受集中载荷下而不发生失稳及变形,顶点构造如图十二所示。这样保证主桁架落地端在拆除滑移小车顶升时,不会对主桁架的结构造成破坏,从而保证主桁架是安全的。
主桁架在提升过程中,主桁架落地端一直处于滑移状态,因此提升钢绞线的垂直度保证显得非常重要,体现在以下两个方面其一、锚具对钢绞线的垂直度要求,这对吊装安全起重要作用;其二、提升架以及缆风系统对钢绞线垂直度的要求,如果钢绞线垂直偏移较大,将对提升架以及缆风系统产生较大的水平分力,对整个提升系统不利。
在主桁架提升的过程中,用经纬仪全程跟踪钢绞线的水平偏移量,设置边界值;列出主桁架提升高度与落地端滑移距离的对照表,在滑移导向轨道上画出距离标记,用全站仪测量主桁架的提升高度;滑移端设置导向装置。
主桁架提升脱离胎架后,经过计算,因拱变形影响,单侧主桁架伸长110mm(对非拱形构件无此影响),且在中部的下挠度达360mm,为消去主桁架弹性变形对主桁架合拢拼接定位及对后期次桁架安装定位的影响,需要采取一些措施,才能保证主桁架拼装定位精度,措施如下1、主桁架地面分段拼装时,两个拼装单元中间需留出300mm间隙,同时提升时采用错位提升的方法,以便在提升时,不会因主桁架伸长而发生干涉。
2、因主桁架变形影响,主桁架提升到设计标高时落地端支座并未到达设计水平位置,解决此问题的方法是对主桁架进行超提,落地端支点到位后,拆除滑移装置及定位导向装置,安装落地端支座,然后再下降主桁架至设计标高。
3、为消去主桁架变形(主要是伸长和下挠度)对空中合拢对接及对后期次桁架安装定位精度的影响,其方法是将主桁架单侧中部增设一组临时支撑和主桁架八个支撑钢柱一同支撑主桁架,此时主桁架最大下挠度降为8mm,伸长量基本消除,从而基本上消去了主桁架变形对其安装定位精度及对次桁架安装定位精度的影响。
为保证主桁架整体提升过程的安全性和可靠性,对其结构和提升架在提升过程的受力、变形采用大型通用有限元结构分析程序ANSYS软件进行充分计算分析。在此前提下,对主桁架各主要受力杆件和提升架在提升过程中的应力应变进行实时监控,为提升过程提供有力的科学保证。
应力应变监测系统采用ZX系列智能记忆弦式数码应变计进行现场应力测试。该应变计采用振弦理论设计制造,具有高灵敏度、高精度、高稳定的优点,适用于长期观测,并可进行实时监控。应变片的测试数据通过YJ-31静态电阻应变仪采集。应力观测点选择原则主桁架、提升架中经计算在提升过程中应力应变较大的杆件;主桁架在拼装完成后受力较大的杆件;测点数量40个。
在主桁架的安装过程中,对主桁架上的监测点应变数值进行测量。在主桁架提升的过程中,按每提升1-2米及在计算书中强度验算所选取的高度下记录应变数据。最后对整个提升阶段的应变数据进行整理并选取典型测点做应力随主桁架安装过程变化曲线。
为保证主桁架提升过程的科学性和安全性,除应力应变的监测外,我们还对整个提升过程中64个监控点进行全程实时监控。保证提升的每一个指令都是在切实的实际测量状态和一定的理论计算保证的前提下发出的。我们的实时监控的项目主要包括主桁架提升高度、提升井架的沉降、不均匀沉降及垂直度、缆风系统拉力及其滑轮组的工作状态、四个落地端滑移距离、与滑移导向装置间隙及其滑轮组工作状态、提升装置各组钢绞线垂直偏角、提升油缸油压、各提升点相对高差等。在提升的准备工作中,我们进行了大量的计算工作,把每一个监控点理论的状态进行了量化,同时把允许的上下浮动的偏差状态(边界值)一一进行了量化,制作成了主桁架提升过程监控数据库模式,同时将理论状态、边界值状态各数据生成曲线图。在实施中,每一个提升分段点通过多台对讲机报数,实时将实际获取的数据生成的曲线同上述三条曲线进行比较,分析与理论曲线的差异大小是否在允许的范围内,确定是否需要调整,为下一步提升动作提供充分的监控数据,为下一个指令的发出提供有力、科学、有效的依据。
该方案通过本次项目的实际运用,完全达到了预期的目的,安全、可靠、经济、快捷地完成了主桁架的提升就位工作,整个提升过程完全在我们预计控制范围内,提升系统(含提升架)载荷及主桁架应力应变情况也与理论计算基本相符。本次液压提升技术通过大胆创新及综合运用多项先进科学技术,成功完成了超大跨度的大型拱形钢结构的吊装工作,为大型构件的整体提升技术开创了一个新的应用领域,也是建设部十大推广运用新技术的成功范例,这将为建筑安装领域带来一个新的发展,为北京2008年奥运工程项目提供借鉴。
上列的详细说明是针对本发明的一可行实施例具体说明,惟该实施例并非用以限制本发明的专利范围,凡未脱离本发明技艺精神所为的等效实施例或变更,例如,等变化的等效性实施例,均应包含于本案的专利范围内。
一种建筑物桁架整体提升方法,其特征在于将主桁架在地面拼装为2个单元;制作并安装相应的提升架;在提升架上设置缆风系统,在相应位置安装液压提升设备;安装桁架落地端滑移装置;以主控计算机控制液压同步提升,并确保落地端的水平移动与提升端的垂直移动同步进行;空中对接口就位后拆除落地端滑移装置,提升并固定落地端;对空中对接口实施拼接。
建筑物桁架整体提升方法及其设备制作方法
- 专利详情
- 全文pdf
- 权力要求
- 说明书
- 法律状态
查看更多专利详情
下载专利文献
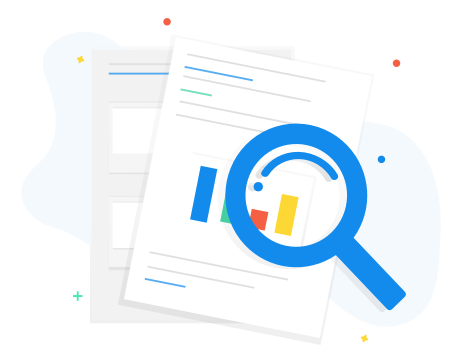
下载专利
同类推荐
-
刘国光, 武志玮刘升逑许发明, 小林敏庆曹广斌
您可能感兴趣的专利
-
姜雯雯, 闫佳莹姜雯雯, 闫佳莹姜雯雯, 闫佳莹姜雯雯, 闫佳莹姜雯雯, 闫佳莹张英丽
专利相关信息
-
沈晓明沈进焕, 杜春梅沈进焕, 杜春梅立石洁