专利名称:制造掺杂石英玻璃的玻璃体的火焰水解方法在EUV石印术(远紫外)中,用于反射镜片和掩模的基材需要在20~30℃范围内没有明显的热膨胀。为了达到此目的,研制了所谓的NZTE材料(近零热膨胀)。满足这些需求的材料是一种掺杂氧化钛的石英玻璃,其由Corning Incorporated公司以ULE商标市售。一种制造ULETM玻璃的方法已经从美国专利5,970,751中知晓。此处的掺杂石英玻璃在多燃烧炉方法中通过火焰水解熔化,其中在燃烧炉中加入氧化硅前体和气态氧化钛前体的气态混合物,其中气态混合物在燃烧炉火焰中生成SiO2粒子和TiO2粒子并沉积于燃烧炉内,它们在炉内熔化并形成固体玻璃体,所述玻璃体的形状由所用坩锅决定。将由此方法制成的直径可能为1m或更大的玻璃体设计成“梨形物”。从该梨形物裁减出成形体,所述成形体用于例如EUV石印术中的反射镜。然而,已经发现由此方法制得的梨形物包含有问题的缺陷,由于该方法,所述缺陷在粗料熔化过程中结合成大块缺陷,并在由此制得的掩模和镜坯的抛光过程中在表面出现。在这点上,它们具有在抛光过程中不能与基材以同一方式移动的危险。因此,隆起就可能会在基体表面出现,或者缺陷区域可能从基体中整体除去,从而在基体表面留下凹陷。这样,由此产生的表面缺陷作为光色散中心,而大大损害了所制产品的质量。特别是,在经抛光的掩模和镜坯的涂覆过程中,出现在它们的部件上的问题会导致在EUV石印术中使用反射元件时的成像性能受到严重损害。另外,对于这些折射率或多或少偏离石英玻璃的元件的掺杂也会导致条痕的产生,这对EUV石印术中材料的应用是有害的。平均厚度为150μm的条痕在制造非球面EUV光学镜时,特别会导致在元件表面出现凹陷。这些凹陷必须随后以较高的费用通过IBF处理(离子光束修整(iron beam figuring))使其变平。根据WO-A-0232622,为了在这种材料中避免条痕缺陷,建议在元件制造过程中以一定的方式处理玻璃,使得内部条痕沿着元件表面的弧度而不突出到表面。然而,这种制造方法很复杂,且不能充分安全地避免上述问题,表面性能仍会被条痕或缺陷损害。虽然已基本知道,无掺杂的石英玻璃可通过火焰水解以相对较高的质量生产(参见WO-A-98/40319或EP-B-0,861,812)。然而,正如可以从美国专利5,154,744看出,这些情况不适用于掺杂石英玻璃的制造。即在制造用氧化钛掺杂的石英玻璃期间,在通过火焰水解制造后,在这些物质被拉制成纤维前,直接在氦/氯气氛下进行加热步骤以得到由此制造的成形体的完整固熔体。
因此,本发明的目的是公开一种改进方法,与现有技术的方法相比,用前者制造的掺杂石英玻璃的玻璃体可产生更高质量的石英玻璃制品。特别是,该玻璃体缺陷较少。附加地或可选择地,与现有技术的方法相比,本发明条痕的厚度也可能会减少。特别是,根据本发明制造的石英玻璃制品,适用于作为在EUV石印术中制造反射光学镜片和掩模的基材。
这个目的可通过一种用火焰水解制造掺杂石英玻璃的玻璃体的方法来解决,其中第一成形体通过单燃烧炉在靶上形成,在炉子内加有用于生成玻璃的燃料和前体。
本发明的目的完全用此方法达到。
通过单燃烧炉制造成形体,它能确保在两个或更多个炉子之间不会出现干扰性相互作用,而所述干扰性相互作用在使用多燃烧炉系统时经常出现。在此方法期间,杆帽周围出现清洁的无干扰流的可能性就大大增加了。
用此方法,制造具有相当少和较小缺陷的掺杂石英玻璃就成为可能。在石英玻璃体内发现的缺陷比用多燃烧炉制造的梨形体中的缺陷少很多。杂质粒子,例如,炉壁材料的分离物,在熔化过程中不能到达成形体帽,因而不包括在该材料中。相反地,它们与燃烧炉的废气一起从炉子内排出。这就使得,与现有技术中掺杂氧化钛的石英玻璃,比如美国专利5,979,751的石英玻璃相比,本方法的石英玻璃具有相当小的缺陷密度。
同时,与美国专利5,979,751的多燃烧炉方法相比,本方法产生的条痕也较小。
本发明的单燃烧炉方法的优点为在熔化区内只产生单一的主流。
根据本发明的优选方案,成形体接着再成形为比第一成形体宽度更大和高度更小的第二成形体。
在本文中,在第一步骤中生成第一成形体,这是一个长而薄的成形体,这个长第一成形体(也称杆)通过凹陷再成形为第二成形体,所述第二成形体的形状和尺寸可能符合待生产元件的所需外形,或者与其相似。
由于再下陷,条痕的厚度通过下陷过程中的流量因素减少了。用此方法,达到厚度≤70μm的条痕是没有任何问题的。而且,厚度≤10μm的条痕也是可能的。如果根据具体应用的必要条件,条痕厚度的进一步减少可以通过进一步的再下陷步骤得到,掺杂物可以优选为TiO2。然而,本发明也可以有利地用于制造掺杂任何掺杂物的石英玻璃的制造,例如,利用包括氟、锗、钒、铬、铝、锆、铁、锌、锡、钽、硼、磷、镍、铅、铪、钼或钨的掺杂物形成玻璃体。本发明的掺杂物导致石英玻璃的折射率有相对较大的偏差。
优选地,掺杂包括至少0.1wt%、优选至少约0.5wt%,通常在大多数掺杂物的百分比范围内。然而,如果用氟作为掺杂物时,此范围下降至少约50重量ppm,通常下降几百个重量ppm。
根据本发明的优选方案,在第一成形体的制造期间,靶要进行旋转驱动。
另外,在本发明中,优选地,在成形体和燃烧炉之间的距离,例如在成形体帽和燃烧炉之间的距离,在制造期间保持基本不变。
这些措施是为了生产尽可能均匀且具有较少缺陷的成形体。
优选地,前体以气态形式装入燃烧炉。
根据本发明的优选方案,利用一个盘作为靶,其可由石英玻璃或其它合适的材料组成。并且,一个凸盘,例如由石英玻璃或优选掺杂石英玻璃组成的凸盘,可以用作靶。
该靶可以基本水平地安装,第一成形体可以在基本垂直的方向上生长。可选择地,也可以基本垂直地安装靶,以使第一成形体基本在靶的水平方向上生长。
正如上述提到的,根据本发明生产的掺杂TiO2石英玻璃特别适用于EUVL基材的制造。
特别是,具有低条痕厚度的积极效果可以在进行进一步的再下陷步骤时达到。
EUVL元件可以由此成形体通过精加工形成所需的形状、尺寸和表面特征而制得。
应理解,上述提到的和下文表述的本发明的特征不仅能以给定的组合使用,而且可以以不同的组合或者其本身单独使用,而不超出本
本发明的其它特征和优势可以参考附图,从下列优选实施方案的描述中理解。图中表示图1本发明的通过火焰水解产生第一成形体的设备的示意图;图2用于生产具有较大直径和较小高度的第二成形体的再下陷方法的示意图;图3a、b在掺杂TiO2的石英玻璃下陷之前和之后的条痕图;图4a由现有技术,即通过美国专利5,979,751的多燃烧炉方法产生的钛掺杂石英玻璃制成的6”掩模坯基体的缺陷图;图4b本发明的钛掺杂石英玻璃制成的6”掩模坯基体的缺陷图。
在图1中,对通过火焰水解用于制造第一成形体24的设备进行了示意性表述,整体设备用数字10表示。
设备10包括第一马弗炉12,在该第一马弗炉12底部设有用于成形体24在其上生长的靶28。靶28可以利用马达32旋转驱动,所述马达32通过驱动轴30安装在马弗炉12的外面。在本发明中,另外提供伺服驱动34,通过该伺服驱动34,靶28可以在如双箭头所示的轴方向上进行调节。燃烧炉14通过马弗炉12顶部的开口突出到马弗炉的空腔中。燃烧炉通过管20连接到合适的燃料供应源,比如H2/O2气体燃料供给系统。另外,用于供应气态前体的管22连接到燃料炉14以生产TiO2掺杂玻璃。举例来说,在掺杂TiO2的情况下,前体可以是例如以气态形式加入到燃料炉火焰中的SiCl4和TiCl4。在燃料炉火焰的高温(>2000℃)下,氯化物分解并生成SiO2和TiO2,从而使TiO2掺杂石英玻璃沉积在靶28上。
对于阳离子掺杂物,例如可以用下列含氯组合物
当掺杂氟时,可用下列气体SiF4、CF4、C2F6和NF3。
所有的元素都可以作为金属-有机化合物分别加入,即烷基、RnE或烷氧基化合物E(OR)n或它们的混合物,比如RnE(OR)m-n可以用作无氯前体。
在火焰水解期间,在第一成形体24和燃烧炉14之间的距离通过移动伺服驱动34保持不变。另外,靶28在火焰水解期间旋转驱动。可能的话,燃烧炉也可以横向驱动。
在生产期间,采用此方法,长而薄的成形体24(也称为杆)在靶28上就渐渐生长了。由于在面向燃烧炉14的端部(称为杆)与燃烧炉14之间的距离保持不变,在整个方法中得到了稳定的条件。由于另外只用了单燃烧炉,没有出现在现有技术的多燃烧炉方法中经常出现的干扰。
根据本发明的单燃烧炉方法,在熔化区域内只产生单一的主流。
优选地,本发明公开的方法使用在外部混合的环形间隙燃烧炉。分布于中心原料喷嘴周围的环形喷嘴的数量取决于所需熔化方法需要的功率。
为了得到优化的熔化方法,在熔化区域(帽)周围无紊流的均质流是必要的。
适当地,为了此目的,可以使用适当的燃烧炉气体设置和适当的系统设计设置。
设计特征包括燃烧炉孔外形和在帽区域内的马弗炉的内部形状。应该选择燃烧炉气体的技术工艺设置,以便通过使用依赖于燃烧炉间隙形状的体积比,使流速从内到外逐渐变小。这就促进了闭合的火焰形态(closed flame picture),并确保出现在中心的产品粒子能够不受气流干扰地到达熔化区域。
另一个参数是所生成帽的形状。它应该是渐近的和近似球形的。应选择燃烧炉设置和移动路线,使得在中心处不会出现过度凹陷。燃烧炉必须优选离粒子生成点有一恒定距离,该距离可以为150至250mm、优选200mm。
炉子内部空腔的结构设计(燃烧炉孔和马弗炉的内部形状)应该优选满足以下条件燃烧炉孔应该设计成近圆锥形,且开口角度从10°渐变为20°,优选13°,以便火焰外沿到马弗炉的耐火材料的距离为约10至20mm。关于马弗炉的内部形状,可以认为帽的距离应该为20至60mm,优选30mm。应选择其形状,以免产生锋利的边缘,并得到与所需帽基本相同的外形。
上述提及的措施可以确保在帽的反应熔化区域顶部有一厚度为1至2mm的稳定粒子薄膜,从而阻止向熔体内引入缺陷(杂质粒子和玻璃烟灰粒子)。
作为靶28,可以采用由适当材料如石英玻璃或掺杂石英玻璃组成的盘。
用此方法产生的第一成形体24优选随后在合适的模子,比如石墨模子38中,在保护气氛下借助于重力再成形,第二成形体的形状大约与所需的最终产品的形状类似(参见图2)。再下陷方法可以用所谓的“压力协助下陷”进行,在此期间第一成形体24加载有重量例如10kg。
如图2所示,再下陷方法可以在现有技术已知的电子加热炉26内,在约1600℃的温度范围内进行。
在再下陷期间发生的材料与石墨模子38的任何接触都可以不予考虑,因为这样的接触只在外部区域中发生。
用此方法生产的任何隐性缺陷决不能与在制造梨形体期间出现的缺陷相比,所述梨形体的制造在现有技术的多燃烧炉方法中,在第一成形体生长时在火焰水解的高温下进行。
在第一成形体24内的任何残留条痕在再下陷过程中都通过流动因素大大减少了。例如,在第一成形体24内厚度为30至50μm的条痕通过再下陷方法使得条痕距离减少为最高10μm,或者甚至比此还小。
图3a和3b表示了掺有约6.8wt%的TiO2的掺杂石英玻璃,其通过再下陷方法使条痕厚度显著降低。
用于再下陷方法的模子38的形状可以类似于所需产品的最终形状,以便最终处理基本上只需要进行研磨和抛光,以例如制造用于EUV石印术的镜子。
图4描述了,在使用由石英玻璃组成的光掩模的常规抛光剂抛光后,通过激光扫描6‘’掩模坯基体所得的缺陷图,所述基体通过由(a)多燃烧炉方法(ULETM)和(b)本发明的单燃烧炉方法制得的钛掺杂玻璃制成。在两种情况下,TiO2的浓度都约为6.8wt%,图3a和3b也分别是这样。
在本文中,缺陷的探测极限为约200nm。因此,由单燃烧炉方法制得的材料与通过多燃烧炉方法熔化的玻璃相比,前者导致的缺陷显著较少。
特别是,在现有技术的ULE掩模基体的情况下,可以看到非常大的缺陷(尺寸为2至11μm),而在本发明的材料中则没有发现这样的缺陷。根据现有技术所产生的这种缺陷,在其用作EUV掩模基体的元件时是不能容忍的。
本发明公开了一种制造掺杂石英玻璃的玻璃体的方法。该方法涉及火焰水解,其中用于形成掺杂玻璃的前体与燃料气体一起加入到单燃烧炉(14)中。第一成形体(24)在靶(28)上形成。用此方法制得的掺杂石英玻璃具有很低的缺陷密度和宽度很小的条痕。优选地,随后将第一成形体成形为比所述第一成形体具有较大宽度和较小长度的第二成形体。从而使得掺杂石英玻璃中的条痕宽度和缺陷密度进一步降低。
制造掺杂石英玻璃的玻璃体的火焰水解方法
- 专利详情
- 全文pdf
- 权力要求
- 说明书
- 法律状态
查看更多专利详情
下载专利文献
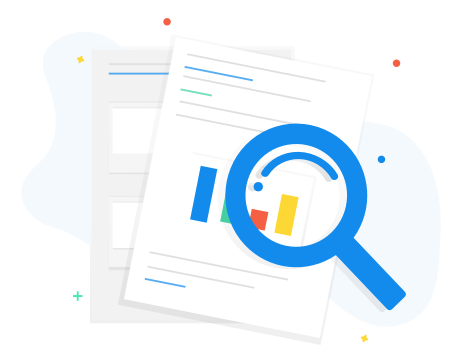
下载专利
同类推荐
-
A.尼科尔, S.威尔逊A.尼科尔, S.威尔逊赵万富, 陈源清丁体英丁体英金凤山王新, 王桂英
您可能感兴趣的专利
-
J·H·阿伦斯J·H·阿伦斯J·H·阿伦斯J·H·阿伦斯罗尔夫·马丁吴润秀何丽萍
专利相关信息
-
严积芳蒂莫·皮沃斯基, 贝恩德·威尔维斯严积芳严积芳丘云灵, 熊玉李宗武吴健, 徐刘彬