专利名称:一种高速钢车刀的形变热处理方法本发明属于金属热处理技术。高速钢车刀是车床切削不可缺少的工具,已有数十年的应用历史。其生产工艺也是数十年沿袭不变即首先将胚料轧制成车刀毛胚,之后进行退火,进行粗磨,淬火,三次回火,清洗,精磨,包装出厂。工序多,生产周期长,能耗大,原材料利用率低,产品质量不高。本世纪60年代随形变热处理理论与实用的研究,开始对高速钢的形变热处理进行研究,到目前为止,仅发表研究论文数篇。对于在高速钢淬火温度下的高温形变热处理来说,遇到在轧制时由于形变诱发引起的碳化物析出,使奥氏体中的碳和合金元素贫化,红硬性达不到国家标准的规定,这一问题难以克服。对于在冷奥氏体亚稳定的中温区(500~600℃),所进行的低温形变热处理而论,因高速钢的形变抗力过大,难于进行比较大的变形,因此在生产上也无法采用。结构钢的形变热处理在生产上的应用在国内外均有大量报道,而高速钢的形变热处理尚未见有生产应用的报道。本发明的目的就是将高速钢车刀毛胚的生产(热轧)与淬火两个分离的工序合而为一,实现轧热淬火,同时省去热轧与淬火分离工序间的毛胚退火;在淬火过程中,将车刀的外观尺寸整形、毛胚棱直与低温形变热处理结合起来;为了建成车刀形变热处理生产线的需要,将原来三次回火改为快速回火;热轧和淬火两道分离工序合而为一变为轧热淬火,从而省去退火和淬火两道工序,大大节约了能源;2)将尺寸整形、棱直与低温形变热处理即低温轧制结合起来,提高了车刀毛胚的尺寸精度和表面光洁度,从而可提高原材料的利用率,省去粗磨工序,低温轧制还能进一步改善车刀的内在质量;3)将高速钢原3~4次回火改为1~2次快速回火,有利于组建成为由专用微机控制的高水平的自动流水生产线;4)由新材料新工艺生产出来的车刀具有成本低,性能高的特点,在国内外市场上具有高的竞争能力,为扩大生产出口创汇创造前提。选用现生产用高速钢M2及新型含铝高碳高速纲CW9M03Cr4VAL将高速钢加热至其淬火温度,经5~15分钟保温后自炉中取出予冷5~20秒,然后进行4-7道轧制,不同的轧制参数轧后的奥氏体组将具有动态回复和动态再结晶组织的不同比例。轧制道次少、变形大、轧制速度快,轧完后淬火前的形变奥氏体其再结晶率应在95~98%之间;若再结晶率达不到95%以上时,轧后应进行快速补热,即重新补加热至其淬火温度,经1-10分钟保温以使轧制时因形变诱发析出的碳化物回溶,动态回复奥氏体产生静态再结晶;然后应迅速将轧胚冷却至500~650℃,在此温度下均温后用轧机将车刀毛胚四个棱角(截面图为正方形)轧出来,其变形率为3~10%,避免因高的形变抗力消耗过大的轧制功率,并将热轧和速冷时变形的车刀轧胚棱直和切断。亦可在600-620℃温度下15~30分的短时1-2次回火。本发明提出的轧热淬火工艺方法的特点1)适用于所有的高速钢,只需调整一下工艺参数即可;2)除适用于车刀外,其它用热轧成型的高速钢刀具如钻头、铣刀等均可采用。因而本发明具有通用性。采用本发明后的技术经济效果由于本发明采用了新型含铝超硬型高速钢,将形变热处理理论研究成果应用于车刀生产,将原生产的许多分离工序组合为具有高密度技术的流水生产线,因而必将产生巨大的技术经济效果。本发明工艺与车刀原工艺过程相比,生产工序由原来14道减至8道;生产周期由原1个月减至7天;由于减少留磨量省去粗磨可使高速钢原材料利用率提高5~8%;省去退火和淬火两道加热工序,大大节约能源,以一条原盐炉生产线计算,每年可节电300多万度,与此同时原盐炉生产时的一切物料消耗亦可避除;省去采用盐炉淬火回火后的酸洗、喷砂工序,避免了污染环境。以上各点将对生产厂带来巨大的直接经济效益。此外,采用本发明生产的车刀,内在质量显著提高,切削寿命较普通M2型车刀提高0.5~1倍以上,这无疑对使用单位将带来好处,社会效益显著。实施例选用现生产用高速钢M2及新型含铝高碳高速钢CW9M03Cr4VAL用本发明工艺进行了处理,并生产出少量车刀,切削性能和红硬性对比试验表明在切削HRC29~31调质轴承钢GCr15时,切削规范相同条件下(胚料φ69mm,切削速度V=43.5米/分,吃刀深度2mm,走刀量0.41mm/转),M2形变热处理车刀切削寿命比原工艺产品提高了0.6倍,而CW9M03Cr4VAl则提高了2.1倍。因而只要采用超硬型高速钢,形变热处理工艺合理,至少可比现生产M2钢车刀切削寿命提高1倍以上。
红硬性测定表明,现生产M2钢车刀及形变热处理车刀的红硬性(600℃×4小时)不高为HRC62~63,而超硬型CW9M03Cr4VAl则高达HRC65以上。
本发明的新工艺是将原热轧和淬火两道在冶金厂与工具制造厂的分离工序合并为热轧后直接淬火,从而省去退火和淬火两道主要工序。本发明是在高速钢淬火温度下,通过各热轧工艺参数的合理配合,使轧后的奥氏体具有100%的再结晶组织,保证有足够高的红硬性。由于本发明采用了超硬型含铝高速钢,其切削寿命可比现生产普通高速钢提高1倍以上。本发明还可提供快速回火及微机控制系统,可建成具有80年代水平的车刀流水生产线。
一种高速钢车刀的形变热处理方法
- 专利详情
- 全文pdf
- 权力要求
- 说明书
- 法律状态
查看更多专利详情
下载专利文献
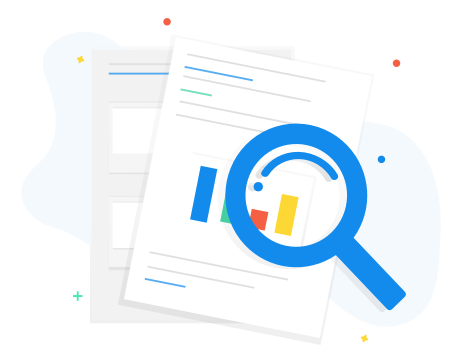
下载专利
同类推荐
-
王占洪张淳崴, 王宽如刘志儒刘志儒刘志儒
您可能感兴趣的专利
专利相关信息