一种硅锆硬质釉及硅锆硬质釉下喷色装饰瓷的制备方法[0002]陶瓷在我国有已有5000余年的历史。瓷器是我国的伟大发明之一,精美的中国陶瓷曾经享誉世界。我国是世界第一大日用陶瓷生产国和出口国。[0003]长期以来,日用瓷在装饰工艺技术方面缺乏创新,工艺水平多年未有明显提升,制品装饰仍多采用贴花、转移印花工艺方法,釉上贴花产品,耐磨性能差,难以满足西餐具对釉面硬度的要求,花面缺乏自然、发璞归真的气息,而釉上贴花,容易出现重金属离子的溶出问题。限制了彩瓷的出口,严重影响了企业的经济效益,急需研制一种新的装饰工艺,满足西餐具对釉面硬度的要求,全面提升产品质量,提高企业经济效益。
[0004]本发明的目的在于提供一种硅锆硬质釉及硅锆硬质釉下喷色装饰瓷的制备方法,以解决上述技术中存在的问题和缺陷。[0005]为达到上述目的,本发明采用以下技术方案: 一种硅锆硬质釉,包 括重量百分比为A配方料55~70%、B配方料30~45%、水分40~45%、釉料添加剂0.3^1.2%、颜料5~10% ;其中,A配方料包括重量百分比:钾长石20-25%、氧化铝8~15%、龙岩颗粒38~48%、石英20~25%、膨润土 0~2% ;Β配方料包括重量百分比:钾长石34~39%、方解石9~15%、氧化锌4~9%、高岭土 5~10%、石英25~30%、锂辉石0~5%、滑石0~2%、硼熔块0~2%。[0006]所述釉料添加剂为糖稀、甘油或蔗糖。
[0007]本发明还提供一种硅锆硬质釉下喷色装饰瓷的制备方法,其方法步骤为:
51:取A配方原料,球磨18-22小时,细度为325目筛筛余≤0.3%,过筛180-200目,备
用;
52:取B配方原料,球磨20-26小时,细度为325目筛筛余< 0.1%,过筛250目,备用;
53:取SI得到的A配方55~70%、S2得到的B配方30~45%、水份40~45%、釉料添加剂
0.3^1.2%、颜料5~10%混合均匀,得到制备好的色釉;
S4:将制备好的色釉用喷枪在陶瓷坯体或低温素烧坯体上喷色,调整喷枪和压缩空气的压力,喷色的压缩空气压力为0.4-0.45MPa,喷好色的坯体烘干后,浸釉,釉坯烘干后,入窑氧化烧成1280-1320°C,保温20-30min,自然冷却到室温。
[0008]与现有技术相比,本发明具有以下有益效果:
1.釉料添加剂采用保湿类的添加剂,如糖稀、甘油、蔗糖等有机无毒的安全原料,调整色釉的物理性能,调节色釉、面釉、坯体之间的相互匹配问题,提高色料层与面釉的浸润性,在喷色后,施釉时不会造成制品的缩釉缺陷,同时这类添加剂还有粘结作用,提高色料层的附着能力,施面釉操作时,避免造成颜色浑浊,解决了面釉操作中的起泡、爆釉、缩釉等缺陷;
2.由于发色层在釉面之下,降低了铅镉溶出和重金属离子的溶出风险,色料层在烧成过程中,不会因为釉层的流动而流动,极大方便了装饰的要求。
[0009]下面结合对本发明作进一步的说明。
[0010]实施例1
本实施例公开了一种娃错硬质釉,包括重量百分比为A配方料65%、B配方料35%、水分40%、糖稀1%、黄色料8% ;其中,A配方料包括重量百分比:钾长石20%、氧化铝8%、龙岩颗粒38%、石英22%、膨润土 1% ;B配方料包括重量百分比:钾长石34%、方解石10%、氧化锌4%、高岭土 6%、石英26%、锂辉石2%、滑石1.5%、硼熔块0.5%。
[0011]取A配方原料,球磨18小时,细度为325目筛筛余0.3%,过筛180目,备用;取B配方原料,球磨22小时,细度为325目筛筛余0.05%,过筛250目,备用;取上述得到的A配方65%、B配方35%、水份40%、糖稀1%、黄色料8%混合均匀,得到制备好的色釉;将制备好的色釉用喷枪在陶瓷坯体或低温素烧坯体上喷色,调整喷枪和压缩空气的压力,喷色的压缩空气压力为0.4MPa,喷枪空气开关正常调节,从制品边缘向内喷色,做到颜色渐变的效果,喷好色的坯体烘干后 ,浸釉,釉坯烘干后,入窑氧化烧成1280°C,保温25min,自然冷却到室温。
[0012]本实施例制备的产品抗热冲击性达到180_20°C水热交换一次不裂,釉面光亮,色料呈色饱满,装饰效果良好,古朴、典雅、美观。
[0013]实施例2
本实施例公开了一种硅锆硬质釉,包括重量百分比为A配方料70%、B配方料30%、水份42%、甘油0.3%、棕色料9% ;其中,A配方料包括重量百分比:钾长石22%、氧化铝10%、龙岩颗粒45%、石英20%、膨润土 0.5% ;B配方料包括重量百分比:钾长石38%、方解石12%、氧化锌5%、闻岭土 8%、石央28%、裡辉石5%、滑石2%、砸溶块1%。
[0014]取A配方原料,球磨20小时,细度为325目筛筛余0.2%,过筛200目,备用;取8配方原料,球磨26小时,细度为325目筛筛余0.1%,过筛250目,备用;取上述得到的A配方70%、B配方30%、水份42%、甘油0.3%、棕色料9%混合均匀,得到制备好的色釉;将制备好的色釉用喷枪在陶瓷坯体或低温素烧坯体上喷色,调整喷枪和压缩空气的压力,喷色的压缩空气压力为0.4MPa,喷枪空气开关正常调节,从制品边缘向内喷色,做到颜色渐变的效果,喷好色的坯体烘干后,浸釉,釉坯烘干后,入窑氧化烧成1280°C,保温20min,自然冷却到室温。
[0015]本实施例制备的产品抗热冲击性达到180_20°C水热交换一次不裂,生产一次烧成合格率85%,满足搬运操作等工序的工艺要求。
[0016]实施例3
本实施例公开了一种硅锆硬质釉,包括重量百分比为A配方料70%、B配方料30%、水份45%、蔗糖1.2%、混合色料9% ;其中,A配方料包括重量百分比:钾长石25%、氧化铝9%、龙岩颗粒48%、石英24%、膨润土 2% ;B配方料包括重量百分比:钾长石39%、方解石14%、氧化锌7%、高岭土 5%、石英27%、锂辉石2%、滑石1%、硼熔块1.5%。[0017]取A配方原料,球磨22小时,细度为325目筛筛余0.1%,过筛200目,备用;取8配方原料,球磨24小时,细度为325目筛筛余0.08%,过筛250目,备用;取上述得到的A配方70%、B配方30%、水份45%、蔗糖1.2%、混合色料9%混合均匀,得到制备好的色釉;将制备好的色釉用喷枪在陶瓷坯体或低温素烧坯体上喷色,调整喷枪和压缩空气的压力,喷色的压缩空气压力为0.45MPa,喷好色的坯体烘干后,浸釉,釉坯烘干后,入窑氧化烧成1320°C,保温30min,自然冷却到室温。
[0018]本实施例制备的产品抗热冲击性达到180_20°C水热交换一次不裂,满足对釉面硬度的要求,解决了 面釉操作中的起泡、爆釉、缩釉等缺陷。
一种硅锆硬质釉及硅锆硬质釉下喷色装饰瓷的制备方法
- 专利详情
- 全文pdf
- 权力要求
- 说明书
- 法律状态
查看更多专利详情
下载专利文献
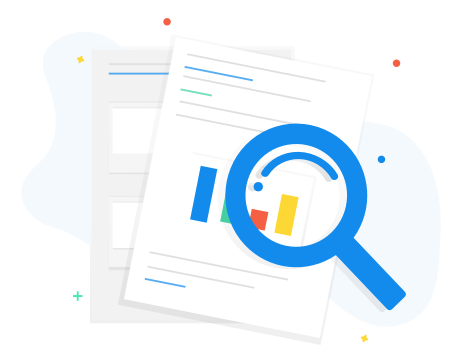
下载专利
同类推荐
-
赵景飞赵景飞
您可能感兴趣的专利
-
A·布尔奎恩, J·C·普罗布斯特
专利相关信息