专利名称:光纤陶瓷套筒的制作方法 陶瓷套筒在光纤中是一个非常重要的部件,该套筒的精度如何直接关系到光纤中两根光纤的对接质量。目前对于陶瓷套筒的加工一般是采用数控机床进行加工,这种加工方式虽然可以保证加工的精度,但是,这种加工方法存在着成本高、设备投资大的缺点。
本发明采用模压烧结以及普通机床进行加工的方法,完成了陶瓷套筒的制作,使陶瓷套筒的加工成本降低,设备投资小和便于普及。本发明的技术方案如下一种光纤陶瓷套筒的制作方法,包括毛坯制作成型和半成品加工两个过程,其中毛坯制作成型过程包括如下步骤A.模具组装将外模与模芯按要求组装成型;B.毛坯模压成型将陶瓷套筒原料通过震料器注入模具中,盖上模盖,在压力机上对该模具内的原料进行施压处理;C.毛坯烧结把毛坯从B步骤结束后的模具中取出,按要求摆放于烧结炉中,进行高温烧结处理;D.毛坯的后期处理对烧结后的毛坯进行包括热处理的后期处理;陶瓷套筒半成品的加工过程包括如下步骤E.磨套筒半成品的内孔将套筒半成品夹在扩孔研磨机的夹具上,夹具上套筒半成品从扩孔研磨机的一端开始向另一端进行磨削,粗磨与精磨工序之间还包括有磨同心度工序,该工序以粗磨后的内孔为基准在上导板无心磨床上磨削陶瓷套筒的外圆,然后进行同心度检测;内孔全部被磨削并且达到要求时,该内孔磨削步骤结束; F.磨套筒半成品的外圆将经过E步骤加工后的套筒半成品夹于外圆下导板无心磨床的夹具上,进行半成品外圆的磨削处理,直至该套筒的外圆达到要求时,F步骤结束;G.磨套筒半成品的端面将经过F步骤加工后的套筒半成品夹于平面磨床的夹具上,首先磨削该套筒半成品的一个端面,该端面的平面度和相对于中心线的垂直度达到要求后,将套筒半成品翻过来,对该套筒半成品的另一端面进行磨削处理,当两个端面的平面度和垂直度均达到要求后,该步骤结束;H.套筒半成品切口及表面处理将经过G步骤加工后的套筒半成品夹于切口机的夹具上,在该套筒半成品的一端切制切口,在切口尺寸和崩口达到要求后,进行该套筒最后的表面处理。所述步骤B的施压处理过程中,所采用的是等静压成型方法,等静压压力为150~250兆帕/平方厘米(Mpa/cm2)。所述步骤E和F包括粗磨和精磨两个过程,步骤E中的精磨工序中磨具需要分别由两端开始进行磨削,而且每端至少需要反复磨两次,精磨分至少两道精磨工序。步骤B中的模压成型、步骤E前的裁断工序、步骤E和F中的内外圆磨削和步骤H中的表面处理过程完成后,需要对套筒进行清洗。套筒半成品双面刷棱内外倒角将经过上述加工步骤的套筒在抛刷机床上进行双面倒角,并且达到要求时倒角结束。套筒半成品的抛光将经过上述加工步骤的套筒在抛光机上进行套筒表面抛光处理,并且达到要求时抛光结束。
本发明由于采用上述技术方案,在达到使用要求的同时,降低了陶瓷套筒的加工成本,同时减少了投资,中小型企业也可以生产高质量的陶瓷套筒。
图1是本发明加工制作工序的流程图。
结合上面的
本发明的最优实施例。
由图1中可知,本发明的光纤陶瓷套筒的制作方法包括毛坯制作成型和半成品加工两个过程,其中毛坯制作成型过程包括如下步骤A.模具组装将外模与模芯按要求组装成型;B.毛坯模压成型将陶瓷套筒原料通过震料器注入模具中,盖上模盖,在压力机上对该模具内的原料进行施压处理;C.毛坯烧结把毛坯从B步骤结束后的模具中取出,按要求摆放于烧结炉中,进行高温烧结处理;D.毛坯的后期处理对烧结后的毛坯进行包括热处理的后期处理;陶瓷套筒半成品的加工过程包括如下步骤E.磨套筒半成品的内孔将套筒半成品夹在扩孔研磨机的夹具上,夹具上套筒半成品从扩孔研磨机的一端开始向另一端进行磨削,粗磨与精磨工序之间还包括有磨同心度工序,该工序以粗磨后的内孔为基准在上导板无心磨床上磨削陶瓷套筒的外圆,然后进行同心度检测;内孔全部被磨削并且达到要求时,该内孔磨削步骤结束;F.磨套筒半成品的外圆将经过E步骤加工后的套筒半成品夹于外圆下导板无心磨床的夹具上,进行半成品外圆的磨削处理,直至该套筒的外圆达到要求时,F步骤结束;G.磨套筒半成品的端面将经过F步骤加工后的套筒半成品夹于平面磨床的夹具上,首先磨削该套筒半成品的一个端面,该端面的平面度和相对于中心线的垂直度达到要求后,将套筒半成品翻过来,对该套筒半成品的另一端面进行磨削处理,当两个端面的平面度和垂直度均达到要求后,该步骤结束;
H.套筒半成品切口及表面处理将经过G步骤加工后的套筒半成品夹于切口机的夹具上,在该套筒半成品的一端切制切口,在切口尺寸和崩口达到要求后,进行该套筒最后的表面处理。所述步骤B的施压处理过程中,所采用的是等静压成型方法,等静压压力为150~250Mpa/cm2。
所述步骤E和F包括粗磨和精磨两个过程,步骤E中的精磨工序中磨具需要分别由两端开始进行磨削,而且每端至少需要反复磨两次,精磨分至少两道精磨工序。步骤B中的模压成型、步骤E前的裁断工序、步骤E和F中的内外圆磨削和步骤H中的表面处理过程完成后,需要对套筒进行清洗。
本方法采用模压烧结的方式使套筒成型,保证了陶瓷套筒的强度、表面硬度和耐磨性,再辅之热处理工序,消除套筒的内部应力,最后采用多道粗、精加工程序,消除套筒在机械加工过程中的应力变化所造成的变形,所以保证套筒始终不变形,精度完全达到使用要求。
所述步骤B的施压处理过程中,所采用的是等静压成型方法,等静压压力为150~250Mpa/cm2,其中以200Mpa/cm2为最佳,等静压成型方法的优点在于压力比较稳定,部件内部的应力变化不大,部件本身的密实度比较均匀。
为了使比较的密实度更加均匀,所述步骤B中,施压前和/或施压中进行震料处理。在施压处理前,将模具放在振动器上或者将振动器放在模压平台上进行振动,使陶瓷颗粒之间的距离均匀,缝隙更小,密实度更高。
所述步骤C的烧结温度为1200~1600℃,升温时间20~35小时,保温时间1~4小时,最佳方案是温度1450℃,升温时间24~30小时,保温时间2小时,所述步骤D的热处理处理过程包括在完成步骤C后进行炉内自然降温,炉内温度低于250℃时打开炉门,炉内温度低于150℃时取出套筒毛坯,在环境温度下自然降温,其中最佳方案是温度低于200℃时打开炉门,炉内温度低于100℃时取出套筒毛坯,这样可以有效地降低套筒内部的应力,保证套筒在以后的制作过程中不会变形或破损。
所述步骤D的后期处理过程中包括对套筒毛坯密度的检测,采用排水法检测;由于套筒毛坯在烧结后呈黑灰色,所以后期处理过程中还需要对套筒进行颜色处理,该工序是将毛坯放入加热炉中,在1.5~7小时内升温至800~1300℃,保温0.5~1.5小时,炉内自然降温至250℃下时打开炉门,炉内温度低于150℃时取出毛坯,在自然环境中降温,其中优选方案是温度为1000℃,升温时间2~5小时,保温1小时,炉内自然降温至200℃下时打开炉门,炉内温度低于100℃时取出毛坯,经过如此处理后的套筒毛坯呈灰白色。
一般情况下,烧结处理套筒毛坯的长度较长,因此在所述步骤E前还有裁断工序,即将毛坯按产品的规格裁成合适的长度。
为了提高加工精度,所述步骤E和F包括粗磨和精磨两个过程,所述步骤E中精磨工序中磨具需要分别由两端开始进行磨削,而且每端至少需要反复磨两次。
所述步骤E中的磨具可以采用砂轮或钎子。所述钎子的一端腐蚀成锥体状,锥度为0.003~0.007,其中以锥度0.005为最佳,该钎子表面有螺旋状的沟槽,类似于钻头的形状,便于磨削下来的磨屑排出,所述步骤E选用钎子磨削过程中,钎子上涂研磨膏。
所述步骤H中的表面处理是将套筒两端的内外圆口处修成倒角,倒角主要是便于该套筒在连接器中的安装,同时,也可以提高安装精度。套筒半成品双面刷棱内外倒角将经过上述加工步骤的套筒在抛刷机床上进行双面倒角,并且达到要求时倒角结束。
套筒半成品的抛光将经过上述加工步骤的套筒在抛光机上进行套筒表面抛光处理,并且达到要求时抛光结束。
为了保证陶瓷套筒在加工过程中的清洁以及防止磨屑的存在对陶瓷套筒所产生的副作用,所述步骤B中的模压成型、步骤E前的裁断工序、步骤E和F中的内外圆磨削和步骤H中的表面处理过程完成后,需要对套筒进行清洗。所述步骤B中模压成型后的清洗过程中,使用的清洗液是煤油和油污清洗剂。所述步骤E前的裁断工序、步骤E和F中的内外圆磨削和步骤H中的表面处理后清洗工序,用热碱或强力清洗剂通过至少一次8~15分钟(10分钟/每次为最佳)的超声波清洗,至少一次去离子水3~8分钟(5分钟/每次为最佳)的超声波清洗以及至少一次无水乙醇的超声波清洗(10分钟/每次为最佳),其中优选方案是;所述步骤E中的精磨和步骤H中的表面处理两个工序后的清洗完成后,套筒还有经过烘干处理。
一种光纤陶瓷套筒的制作方法,包括毛坯制作成型和半成品加工两个过程,其中毛坯制作成型过程包括模具组装、毛坯模压成型、毛坯烧结、毛坯的后期处理等工序。而加工过程包括磨套筒半成品的内孔、磨套筒半成品的外圆、磨套筒半成品的同心度、磨套筒半成品的端面和套筒半成品切口及表面处理等工序。本方法采用模压烧结的方式成型,再辅之热处理工序以及多道粗、精加工程序,保证了陶瓷套筒的强度、表面硬度和耐磨性,消除套筒的内部应力,保证套筒始终不变形,精度完全达到使用要求。本发明在达到使用要求的同时,降低了陶瓷套筒的加工成本,同时减少了投资,使中小型企业也可以生产高质量的陶瓷套筒。
光纤陶瓷套筒制作方法
- 专利详情
- 全文pdf
- 权力要求
- 说明书
- 法律状态
查看更多专利详情
下载专利文献
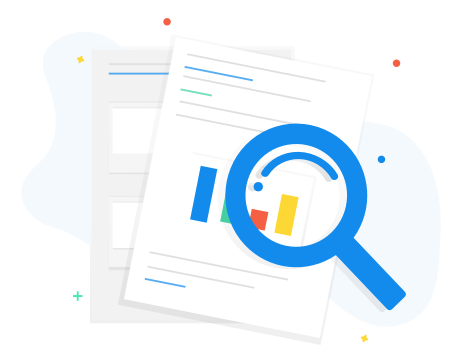
下载专利
同类推荐
-
王毅名取荣治汤玉斐杨建杨建
您可能感兴趣的专利
-
陈秀丽平野正晃平野正晃平野正晃王红云
专利相关信息
-
王红云周延春