专利名称:一种定向增强抗冲击结构陶瓷素坯的成型方法素坯成型,是陶瓷制备工艺中的一个关键环节,直接影响着陶瓷制备的质量。目前,陶瓷素坯较成熟的成型工艺主要有干压法、注浆法以及挤出成型等。干压法,是将碳源与陶瓷粉料混合后采用机械压制,成为具有一定形状和强度的坯体。该方法的主要缺点是压制的粉料一般须经过造粒过程获得,由于粉料团聚等原因很难混合均勻,造成素坯密度不均勻,强度较低,无法实现粉料与纤维的均勻混合,因而烧制的陶瓷制品强度不高。注浆法,是将碳源与陶瓷粉体制成浆料,注入到多孔模具中;然后,靠多孔模的毛细管力将排除水分,干燥后即为具有一定形状和强度的坯体。该方法的主要缺点是生产周期长,在制备形状复杂的样品时尤为明显;在排除水分的过程中,容易产生颗粒的定向排列,导致素坯结构不均勻,强度低。挤出成型,是利用压力将具有塑性的泥料通过模具挤出,获得与模具内腔横截面形状一致的坯体。这种成型方法不能制备形状复杂的样品;未经干燥的生坯强度低,坯体收缩大,容易出现缩孔、裂纹等缺陷。基于以上问题,近几年出现了凝胶注模成型、直接凝固注模成型等方法。这类工艺可以使浆料不经脱水,而在无孔模具内实现原位凝固,其得到的素坯微观结构较为均勻,且适宜于形状复杂及大尺寸陶瓷部件的成型。但其仍具有如下局限性凝胶注模成型,虽然可以生产出强度较高的素坯,但其必须使用大量的、具有毒性的聚合单体,污染环境,危害人体健康。该工艺只能尽量减少毒性,但并不能从根本上解决毒性问题。直接凝固注模成型,虽然污染较低,但其脱模时间长,生产周期长,且得到的素坯强度较低。专利号为200710017364. 0的发明专利,公开了一种碳/碳-碳化硅陶瓷基复合材料的制备方法。该方法是采用纤维结构形式进行加工直接制备出成品陶瓷,具体采用了化学气相浸渗法。其首先在碳纤维预制体表面先沉积一层热解碳界面层,然后交替沉积热解碳和SiC,形成(PyC/SiC)n多层基体,得到C/C-SiC复合材料。由于该方法的整个生产过程都是在高温环境中进行,因此,能耗大、成本高,且耗时长、工艺复杂,尤其是无法进行批量生产。综上,干压法、注浆法、挤出成型以及后续出现的凝胶注模成型、直接凝固注模成型等均无法实现定向增强抗冲击结构陶瓷用的素坯。
本发明提供的定向增强抗冲击结构陶瓷素坯的成型方法,主要解决了现有成型方法工艺复杂、成本高,且制备出的陶瓷定向抗冲击性能差或无法实现大规模批量生产的技术问题。本发明的具体技术解决方案如下该定向增强抗冲击结构陶瓷素坯的成型方法,包括以下步骤(1)制混合浆料(1.1)选取主料:(1.1.1)选取主料 I:按任意比例取碳化硅晶须、纳米碳纤维、短切碳纤维中的一种或任意二至多种;(1.1. 2)选取主料 II:取烧结陶瓷用超细粉料,其中,烧结陶瓷用超细粉料为碳化硅超细微粉或碳化硼超细微粉之任一种或其二者以任意比例的混合,烧结陶瓷用超细粉料的粒径小于等于 5μπ ,以粒径小于Ιμ 为佳;(1.2)选取辅料取烧结助剂、素坯成型粘合剂、微粉分散剂和悬浮剂,其中,烧结助剂、素坯成型粘合剂、微粉分散剂与悬浮剂的配比为注浆成型工艺中已公知的配比;(1.3)混合浆料将主料I、主料II和辅料与混合用液体混合均勻,得到混合浆料;其中混合用液体为水、任意浓度的甲醇、任意浓度的乙醇或任意浓度的丙酮之任一种或任意二至多种以任意比例的混合,以水、乙醇或水与乙醇的混合液为佳;混合浆料中除混合液体外的主料和辅料所占比例主料I所占质量百分比为0 10%,主料II所占质量百分比为80% 95%,辅料所占质量百分比为2 10% ;主料和辅料与混合用液体的质量比为1 0.5 3,其中以主料和辅料与混合用液体的质量比1 1 1.5为佳;(2)按照所成型素坯形状及增强的方向制成碳纤维层状物或编织物;(3)碳纤维层状物或编织物的铺设及加压排液将混合浆料与碳纤维层状物或编织物交替注入或铺设入模具,加压,使模具腔体逐渐缩小,至混合浆料中的液体排出模具,得到粗素坯。以上所述步骤(3)中的将混合浆料与碳纤维层状物或编织物交替注入或铺设入模具,加压,具体是先将部分混合浆料注入模具,然后铺设碳纤维层状物或编织物,再注入部分混合浆料,再铺设碳纤维层状物或编织物,如此交替进行,直至混合浆料和碳纤维层状物或编织物注入和铺设完毕,之后再加压;铺设的层数根据碳纤维层状物或编织物的厚度以及陶瓷的强度要求而定;碳纤维层状物或编织物与混合浆料的比例为1 0. 8 2. 5。以上所述的加压排液中,具体是采用抽式排液或挤式排液;其中,抽式排液的压力为负压,压力范围为-0. 09 -0. 02Mpa ;挤式排液的压力为正压,压力范围为0. 2 2Mpa。以上所述的加压排液中,混合浆料中的液体具体是通过模具壁上的透孔或模具内壁上的排液槽排出模具;模具壁上的透孔为超细微孔或大孔;超细微孔的孔径介于水分子直径与选取物最小颗粒直径之间。以上所述模具壁上的透孔为大孔时模具壁内侧有过滤层,过滤层采用带有超细微孔的过滤材料或分子筛加工制成的过滤材料,过滤层上的微孔孔径介于水分子直径与选取物最小颗粒直径之间。本发明的优点在于1、本发明提供的定向增强抗冲击结构陶瓷素坯的成型方法工艺简单,生产周期短,定向增强效果明显,可实现大规模批量生产;节能;无毒性;环保。上述所有特点还使得本发明的定向抗冲击结构陶瓷生产成本大幅度降低。2、采用本发明制备出的陶瓷素坯,具有如下优良特性素坯密度均勻,坯体收缩小,强度高,能进行机械加工;用该素坯烧制的陶瓷定向抗冲击强度大;抗氧化性好;抗热震;热稳定性佳;耐磨损;耐化学腐蚀。6浆料和碳纤维层状物或编织物注入和铺设完毕,之后再加压。铺设的层数根据碳纤维层状物或编织物的厚度以及陶瓷的强度要求而定。碳纤维层状物或编织物与混合浆料的比例为1 0. 8 2. 5。混合浆料中的液体具体是通过模具壁上的透孔或模具内壁上的排液槽排出模具。 模具壁上的透孔为超细微孔或大孔;超细微孔的孔径介于水分子直径与选取物最小颗粒直径之间;模具壁上的透孔为大孔时模具壁内侧有过滤层,过滤层采用带有超细微孔的过滤材料或分子筛加工制成的过滤材料,过滤层上的微孔孔径介于水分子直径与选取物最小颗粒直径之间。加压的目的是使模具腔体逐渐缩小,至混合浆料中的液体排出模具,得到粗素坯;加压可以采用抽式排液或挤式排液;其中,抽式排液的压力为负压,压力范围为-0. 09 -0. 02Mpa ;挤式排液的压力为正压,压力范围为0. 2 2Mpa。实施例1(1)制混合浆料(1. 1)选取主料(1. 1. 1)选取主料 I 取短切碳纤维,纤维长度为1 10mm,对短切碳纤维进行热沉积碳处理;(1.1. 2)选取主料 II:选取烧结陶瓷用超细粉料烧结陶瓷用超细粉料是粒径为小于1 μ m的碳化硅超细微粉;(1.2)选取辅料辅料包括烧结助剂、素坯成型粘合剂、微粉分散剂和悬浮剂;将上述选取物置于水中进行超声分散、搅拌混合均勻,得到混合浆料;选取物中除水外的各部分所占质量百分比分别为,短切碳硅纤维5 %,碳化硅超细微粉90 %,辅料5 % ; 选取物与水之间的质量比为1 1,水比例过大时会导致悬浮困难,水比例过小时会导致混合不均勻;(2)按照所成型素坯形状及增强的方向制成碳纤维层状物或编织物,碳纤维可以进行热沉积碳处理;(3)碳纤维层状物或编织物的铺设及加压排液先将1/10的混合浆料注入矩形模具,然后铺设碳纤维层状物或编织物,再注入 1/10混合浆料,再铺设碳纤维层状物或编织物,如此交替进行,直至将最后剩余的1/10混合浆料注入;碳纤维层状物或编织物与混合浆料的比例为1 1.2,加压,使模具腔体逐渐缩小,至混合浆料中的液体排出模具;模具底部设置有超细微孔便于液体迅速排出,超细微孔的孔径大于水分子直径,小于选取物直径;水排尽后,模压成型素坯,成型后将素坯脱模, 得到九层碳纤维编织物的定向增强抗冲击结构陶瓷的素坯。素坯制备完成后,采用公知技术对素坯进行烧制,得到定向增强抗冲击结构陶瓷, 经试验检测,该抗冲击结构陶瓷断裂功大于11. 32KJ · m_2,拉伸强度大于350. SMPa0利用该种制得的定向增强抗冲击结构陶瓷素坯的方法适合于制造矩形或圆形板状陶瓷素坯、长方体陶瓷素坯和圆柱体或圆锥体陶瓷素坯。实施例2(1)制混合浆料(1. 1)选取主料(1. 1. 1)选取主料 I 选取5 %碳化硅晶须和95 %的1 3mm短切碳纤维;(1.1. 2)选取主料 II:选取烧结陶瓷用超细粉料烧结陶瓷用超细粉料是粒径为小于0. 5 μ m的碳化硼超细微粉;(1.2)选取辅料辅料包括烧结助剂、素坯成型粘合剂、微粉分散剂和悬浮剂;选取物中除水外的各部分所占质量百分比分别为,碳化硅晶须和短切碳纤维5%, 碳化硼超细微粉90 %,辅料5 % ;将碳化硅晶须、短切碳纤维、烧结陶瓷用超细粉料、辅料置于水中进行超声分散、 搅拌混合均勻,得到混合浆料;选取物与水之间的质量比为1 1.5,水比例过大时会导致悬浮困难,水比例过小时会导致混合不均勻;(2)按照所成型素坯形状及增强的方向制成碳纤维层状物或编织物,碳纤维可以进行热沉积碳处理;(3)碳纤维层状物或编织物的铺设及加压排液先将1/5的混合浆料注入圆形模具(成型管状碳化硅陶瓷),然后铺设碳纤维层状物,再注入1/5混合浆料,再铺设碳纤维层状物,交替进行直至浆料和碳纤维层状物注入和铺设完毕。碳纤维层状物或编织物与混合浆料的比例为1 1.5,模具底部设置有超细微孔便于液体迅速排出,超细微孔的孔径大于水分子直径,小于选取物直径;采取负压为-0. 09Mpa的压力将液体抽出;水排尽后,模压成型素坯,成型后将素坯脱模,得到四层碳纤维编织物的定向增强抗冲击结构陶瓷的素坯。素坯制备完成后,采用公知技术对素坯进行烧制,得到定向增强抗冲击结构陶瓷, 经试验检测,该抗冲击结构陶瓷断裂功大于13. 32KJ · m_2,拉伸强度大于323. 2MPa。这种制造定向增强抗冲击结构陶瓷素坯的方法适用于制造环状或管状陶瓷素坯。
本发明提供的定向增强抗冲击结构陶瓷素坯的成型方法,主要解决了现有成型方法工艺复杂、成本高,且制备出的陶瓷定向抗冲击性能差或无法实现大规模批量生产的技术问题。该定向增强抗冲击结构陶瓷素坯的成型方法,包括以下步骤(1)制混合浆料(1.1)选取主料,(1.2)选择辅料,(1.3)混合浆料;(2)按照所成型素坯形状及增强的方向制成碳纤维层状物或编织物;(3)混合浆料与碳纤维层状物或编织物的交替注入和铺设及加压排液,液体排出后脱模得到烧结定向增强抗冲击结构陶瓷用的素坯。
一种定向增强抗冲击结构陶瓷素坯的成型方法
- 专利详情
- 全文pdf
- 权力要求
- 说明书
- 法律状态
查看更多专利详情
下载专利文献
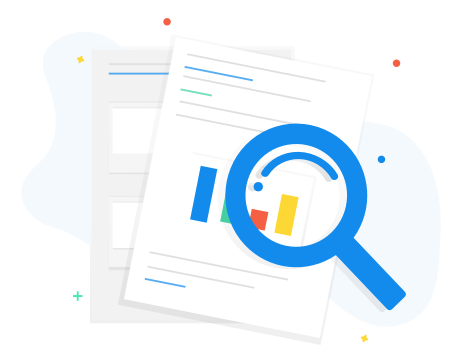
下载专利
同类推荐
-
朱胜利名取荣治名取荣治汤玉斐杨建
您可能感兴趣的专利
-
杨建杨建郑木莲, 李欣杨雪平陈秀丽陈秀丽
专利相关信息
-
陈秀丽王红云王红云