专利名称:陶瓷催化剂体的制备方法 热耐冲击性高的堇青石已广泛地用作现有技术中陶瓷催化剂体的陶瓷载体。通常,在模制成蜂窝状的由堇青石形成的载体的表面上涂布γ-矾土之后,在其上负载贵金属催化剂,从而得到一种陶瓷催化剂体(参见日本已审专利公布(特许)5-50338)。之所以要形成该涂布层是因为堇青石的表面积相对小,因此不能负载所需的足够量的催化剂。当堇青石的表面上涂布有比表面积大的γ-矾土时,可以使该载体的表面积增加。然而,用γ-矾土涂布该载体的表面由于重量增加,而导致热容量增加的问题。为了快速激活废气净化催化剂,近年来已进行了研究以降低载体的孔(cell)壁厚度并降低热容量。涂布层的形成降低了热容量下降的效果。而且,沉积涂布层之后由于蜂窝载体内的开孔面积减少,引起热膨胀系数变大并且压力损失增加的问题。由于热和表面积随时间推移而降低,因此涂布层的细孔易受损。物理吸附到细孔中的催化剂随着表面积减少而陷入内部,并且催化剂量降低,因此净化效率降低。由于上述现有技术的这些问题,本发明旨在提供一种陶瓷催化剂体的制备方法,它能够直接将一催化剂载在陶瓷载体上并且不易遭受热降解。发明概述根据本发明的第一个方面,提供了一种陶瓷催化剂体的制备方法,它将催化剂直接载在一陶瓷载体上,所述陶瓷载体含有由堇青石-W复合体组成的基质相以及由除堇青石-W复合体之外的化合物组成的分散相,该方法包括步骤将催化剂前体溶解在溶剂中并制备一含有催化剂组分的催化剂溶液,所述催化剂组分由得自催化剂前体的负络合离子组成;调整催化剂溶液的pH,使得满足关系E1>E2并且E1>0,其中E1是相对催化剂溶液的pH的陶瓷载体的基质相的表面电位,E2是陶瓷载体的分散相的表面电位;将所述陶瓷载体与所述催化剂溶液接触以在所述陶瓷载体上负载催化剂组分;并施加热处理以使由堇青石-W复合体组成的基质相与催化剂组分结合,从而将所述催化剂直接负载在陶瓷载体上。根据本发明的第二个方面,提供了一种陶瓷催化剂体的制备方法,它将催化剂直接载在陶瓷载体上,所述陶瓷载体含有由堇青石-W复合体组成的基质相以及由除堇青石-W复合体之外的化合物组成的分散相,该方法包括步骤将催化剂前体溶解在溶剂中并制备一含有催化剂组分的催化剂溶液,所述催化剂组分由得自催化剂前体的正络合离子组成;调整催化剂溶液的pH,使得满足关系E1<E2并且E1<0,其中E1是相对催化剂溶液的pH的陶瓷载体的基质相的表面电位,E2是陶瓷载体的分散相的表面电位;将所述陶瓷载体与所述催化剂溶液接触以在所述陶瓷载体上负载催化剂组分;并施加热处理以使由堇青石-W复合体组成的基质相与催化剂组分结合,从而将所述催化剂直接负载在陶瓷载体上。
根据本发明的第三个方面,提供了一种陶瓷催化剂体的制备方法,它将催化剂直接载在一陶瓷载体上,所述陶瓷载体由堇青石-W复合体组成,或者在晶格中有氧缺陷或有晶格缺陷,或者含有细裂纹,该方法包括步骤将催化剂前体溶解在溶剂中并制备一含有催化剂组分的催化剂溶液,所述催化剂组分由得自催化剂前体的负络合离子组成;调整催化剂溶液的pH,使得满足关系E1>0,其中E1是相对催化剂溶液的pH的陶瓷载体的表面电位;将所述陶瓷载体与所述催化剂溶液接触以在所述陶瓷载体上负载催化剂组分;并施加热处理,从而将所述催化剂组分直接载在陶瓷载体上。
根据本发明的第四个方面,提供了一种陶瓷催化剂体的制备方法,它将催化剂直接载在一陶瓷载体上,所述陶瓷载体由堇青石-W复合体组成,或者在晶格中有氧缺陷或有晶格缺陷,或者含有细裂纹,该方法包括步骤将催化剂前体溶解在溶剂中并制备一含有催化剂组分的催化剂溶液,所述催化剂组分由得自所述催化剂前体的正络合离子组成;调整催化剂溶液的pH,使得满足关系E1<0,其中E1是相对催化剂溶液的pH的陶瓷载体的表面电位;将所述陶瓷载体与所述催化剂溶液接触以在所述陶瓷载体上负载催化剂组分;并施加热处理,从而将所述催化剂直接负载在陶瓷载体上。
接下来,将解释本发明的功能和效果。
所述第一个和第二个发明中使用的陶瓷载体含有由堇青石-W复合体组成的基质相以及由除堇青石-W复合体之外的化合物组成的分散相。
在具有这种构造的陶瓷载体中堇青石结构的部分晶格被W所替代,这在后面将有解释。所述材料具有一分散相,其中除堇青石-W复合体之外的组分以岛状聚集(参见后面的附图2)。
当将一催化剂载在陶瓷载体的基质相堇青石-W复合体上时,除了物理吸附之外,还利用了在该复合体中的W与催化剂之间形成的化学键。陶瓷载体的分散相通过物理吸附负载催化剂。
因此,当将催化剂载在陶瓷载体上时,不需要比表面积高的涂布层,而是可以直接负载催化剂。
然而,所述基质相和催化剂之间的结合强度远高于分散相与催化剂之间的结合强度。因此,当在苛刻条件如在高温环境下使用该陶瓷催化剂体时,载在该分散相上的催化剂因热而移动,发生热聚集并脱落。这些是引起陶瓷催化剂体性能降低的主要因素。
因此,在第一个发明中,当催化剂溶液中的催化剂组分由得自所述催化剂前体的负络合离子组成时,调整催化剂溶液的pH,使得满足关系E1>E2并且E1>0,其中E1是相对催化剂溶液的pH的陶瓷载体的基质相的表面电位,E2是陶瓷载体的分散相的表面电位。
换句话说,当基质相11的表面电位E1是正的时(如图4所示),由于催化剂组分13由负络合离子组成,因此在基质相1和催化剂组分13之间呈现电吸引。结果,催化剂组分13粘在催化剂载体的基质相11的表面110上。
当基质相11的表面电位E1大于分散相12的表面电位E2并且E1和E2都是正的时(如图7所示),在由负络合离子组成的催化剂组分13与基质相11之间的吸引作用大于催化剂组分13与分散相12之间的吸引作用。因此,由负络合离子组成的催化剂组分13粘附在基质相11的表面110上并且也粘附在分散相12的表面120上。然而,在分散相12的表面120上的粘附量较小。
调整催化剂溶液的pH,使得满足如上所述的条件时,大部分催化剂负载在结合强度较高的基质相上,而几乎不载在结合强度较低的分散相上。
在第二个发明中,催化剂组分由正络合离子组成,但是由于如上所述的相同原因,可以获得几乎不发生热聚集和催化剂脱落并且耐用性优异的陶瓷催化剂。
换句话说,当基质相和分散相的表面电位都是负的时,如果基质相的表面电位小于分散相的表面电位(根据绝对值,基质相具有更大的表面电位),那么大部分催化剂组分粘附在基质相上。
由于分散相(可能发生热聚集和脱落)上的催化剂量小,因此可以获得不易受到性能下降影响且耐用性优异的陶瓷催化剂。
当通过将催化剂直接载在陶瓷载体上制备陶瓷催化剂体时,第三个和第四个发明中的陶瓷载体由堇青石-W复合体组成,或者在晶格中有氧缺陷或有晶格缺陷并且含有细裂纹。
换句话说,这些发明使用如下的陶瓷载体(1)由堇青石-W复合体组成陶瓷载体;(2)晶格中具有氧缺陷和晶格缺陷中的至少一种的陶瓷载体;和(3)陶瓷载体具有细裂纹。
如第一个和第二个发明所述的,陶瓷载体(1)可以利用复合体的W与催化剂之间存在的化学键以及物理吸附。因此,当催化剂载在陶瓷载体上时,不需要比表面积大的涂布层,并且可以直接负载催化剂。
当在构成陶瓷载体的材料中存在氧缺陷和晶格缺陷时(如(2)所述),在陶瓷载体的表面上形成因氧缺陷和晶格缺陷引起的裂纹和细孔。因氧缺陷和晶格缺陷引起的这些裂纹和细孔特别小并且其大小能够容纳催化剂组分。因此,当将催化剂载在陶瓷载体上时,不需要比表面积大的涂布层并且可以直接负载催化剂。
当在陶瓷载体中存在细裂纹时(如(3)所述),如果催化剂组分具有与细裂纹大小近似的大小,那么催化剂组分可以与(2)中相同的方式容纳在细裂纹中。因此,不需要比表面积大的涂布层并且可以直接负载催化剂。
在第三个发明中,调整催化剂溶液的pH,使得满足关系E1>0,其中E1是相对催化剂溶液的pH的陶瓷载体的基质相的表面电位,并将所述陶瓷载体与所述催化剂溶液接触。
由于陶瓷载体的表面电位E1是正的并且催化剂组分由负络合离子组成,因此它们之间存在电吸引作用,从而催化剂组分被粘附到陶瓷载体的表面上。类似地,在第四个发明中由于陶瓷载体的表面电位E1是负的并且催化剂组分由正络合离子组成,因此它们之间存在电吸引作用,从而催化剂组分被粘附到陶瓷载体的表面上。
当调整催化剂溶液的pH以满足上述条件时,可以使催化剂可靠地粘附到催化剂载体的表面上并进行烤制。
而且,由于是在催化剂组分均匀地粘附到整个陶瓷载体上之后对其进行烧结,因此可以获得一种陶瓷载体,其中不出现局部热弱部分(portions weak to heat),并且它不易受到因热聚集而引起的性能降低的影响,其还具有优异的耐用性。
如上所述,第一个至第四个发明可以提供一种陶瓷催化剂体的制备方法,它可以将一催化剂直接载在陶瓷载体上,不需要在该陶瓷载体上沉积一涂布层并且不易经受热降解。
附图简介
图1显示了如实施方式1的陶瓷催化剂体;图2是显示实施方式1的陶瓷载体的结构的示意图;图3是显示堇青石-W复合体和TiO2的表面电位与pH之间的关系的图;图4是在具有正表面电位的基质相表面与由负络合离子组成的催化剂组分之间的电吸引作用的解释图;图5是在具有正表面电位的基质相表面、具有负表面电位的分散相的表面和由负络合离子组成的催化剂组分之间的电吸引和排斥力作用的解释图;图6是在具有正表面电位的基质相表面、具有0表面电位的分散相的表面和由负络合离子组成的催化剂组分之间的电吸引作用的解释图;图7是在具有正表面电位的基质相表面与由负络合离子组成的催化剂组分之间的电吸引作用的解释图;图8是显示基质相和分散相各自的表面电位与pH之间的关系的图。
优选实施方式的描述在上述第一个发明中,当调整催化剂溶液的pH以满足关系E1>E2、E1>0且E2≤0时,特别是当基质相11的表面电位E1是正的并且分散相12的表面电位E2是0时(如图6所示),吸引力作用于由负络合离子组成的催化剂组分13与基质相11之间,并且由负络合离子组成的大部分催化剂组分13粘附在基质相11的表面110上。尽管电吸引未作用于分散相12的表面120上,但是由于物理吸附,其在一定程度上也吸附催化剂组分13。
特别是如图5所示,当基质相11的表面电位E1是正的并且分散相12的表面电位E2是负的时,在由负络合离子组成的催化剂组分与基质相11之间存在吸引力,而在催化剂组分5与分散相12之间存在排斥力。因此,由负络合离子组成的催化剂组分13大部分粘附到基质相11的表面110上,但是几乎不粘附到分散相12的表面120上。
在第一个发明中,当调整催化剂溶液的pH以满足关系E1>E2、E1>0且E2<0时,并且当基质相11的表面电位E1是正的并且分散相12的表面电位E2是负的时(这种情况下如图5所示),在由负络合离子组成的催化剂组分5与基质相11之间存在吸引力,而在催化剂组分5与分散相12之间存在排斥力。因此,由负络合离子组成的催化剂组分13大部分粘附到基质相11的表面110上,但是几乎不粘附到分散相12的表面120上。
当调整催化剂溶液的pH以满足上述条件时,大部分催化剂负载在结合强度高的基质相上,而几乎不负载在结合强度低的分散相上。
因此,当将该陶瓷催化剂体用于苛刻条件如高温环境下时,可以获得这样一种陶瓷催化剂,它不易受因热聚集导致的性能降低的影响,并且由于分散相所负载的可能发生热聚集和脱落的催化剂的量小,因此耐用性优异。
在第二个发明中,当调整催化剂溶液的pH以满足关系E1<E2、E1<0且E2≥0时,如果基质相的表面电位是负的并且分散相的表面电位是正的或0,那么大部分催化剂组分粘附在基质相上。
在第二个发明中,当调整催化剂溶液的pH以满足关系E1<E2、E1<0且E2>0时,大部分催化剂组分粘附在基质相上。
因此,可以获得一种陶瓷催化剂,它不易受因热聚集所致性能降低的影响,并且由于分散相所负载的可能发生热聚集和脱落的催化剂的量小,因此其耐用性优异。
接下来,将解释第一至第四个发明的堇青石-W复合体。
堇青石以化学式(理论组成)2MgO·2Al2O3·5SiO2表示,并且该复合体具有其中堇青石的Si、Al和Mg被W替换的组成。
电子组态是[Xe]4f145d46s2并在d轨道具有一空轨道。另一方面,W的氧化数是II、IV、V、VI等,其中其中至少存在两种。
因此,W的能级与所负载的作为催化剂的这些元素(特别是贵金属元素)的能级近似,并且可能发生电子交换。由于W具有至少两种氧化态,因此可能与催化剂发生电子交换。通过这种电子交换结合,复合体可以高的结合强度与催化剂结合。
上述复合体可以下面的方式制备。
首先,降低原料中准备用W替换的元素的量,所述原料具备堇青石的理论组成。然后将这些原料捏合、模制并干燥,之后浸泡在含有W化合物的溶液中,干燥并烧结,得到陶瓷载体。
或者,将W化合物加入到这些原料中,所述原料具有堇青石的理论组成并从其中除去准备用W替换的元素。然后将这些原料捏合,模制,干燥并烧结,得到陶瓷载体。
没有进入堇青石晶格的W以及形成堇青石晶格时过量的Al、Mg、Si等转变成氧化物和复合氧化物,并以分散相的形式留在由堇青石-W复合体组成的基质相中。通过对所述陶瓷载体进行X-射线衍射测定可以证实含有堇青石-W复合体的基质相和不含堇青石的分散相的存在。
在上述制备方法中,将W化合物与钛化合物混合使用,可以获得含有较大量W的陶瓷载体。在这种情况下,钛促进W对堇青石内元素的取代。
接下来,将解释第三和第四个发明的陶瓷载体。
由堇青石-W复合体组成的陶瓷载体是具有第一和第二个发明中所示的基质相和分散相的陶瓷载体,但是分散相的量小或者为零。
接下来,将解释在晶格中具有氧缺陷和晶格缺陷之一的陶瓷载体。
氧缺陷是由于形成陶瓷载体的晶格的氧不足所致的,并且催化剂可以载在因氧离去而形成的细孔内。为了承载足以体现陶瓷催化剂的效果的催化剂,晶格的氧量优选低于正常晶格中氧量的47重量%。
晶格缺陷是当所捕获的氧的量大于构成陶瓷载体的晶格的需氧量时形成的缺陷,并且催化剂组分可以载在因晶格变形形成的细孔和金属空格点内。
为了承载足以体现陶瓷催化剂的效果的催化剂,晶格中的含氧量优选大于正常晶格的48重量%,为了获得这种陶瓷载体,优选使用堇青石。
接下来,将解释具有细裂纹的陶瓷载体。
细裂纹必需具有至少约0.1nm的宽度,并且深度为催化剂组分的正和负络合离子的直径的至少1/2,并且通常必需是至少0.05nm。为了提高陶瓷载体的机械强度,这些裂纹优选小。
而且,宽度优选为100nm或更小。更优选,宽度是10nm或更小。
由于催化剂组分进入这些裂纹,因此它粘附到陶瓷载体的表面上。
具有这些细裂纹的陶瓷载体可以通过向普通方法生产的陶瓷载体施加热冲击或者冲击波制得。
可以使用如下两种方法中的任一种来施加热冲击将陶瓷载体加热然后快速冷却的方法,和在陶瓷载体烤制和冷却的加工步骤中将陶瓷载体从预定温度快速冷却的方法。为了通过热冲击产生裂纹,在普通加热温度和快速冷却之间的温差(热冲击温差)可以是至少约80℃。当这些裂纹过大时,不能容易地保持陶瓷载体的形状。因此,热冲击温差优选并通常为900℃或更低。
本发明的裂纹也可以在陶瓷载体内通过施加冲击波形成。换句话说,当陶瓷载体中强度低的部分不能经受冲击波的能量时,就会形成细裂纹。施加冲击波的方法包括使用超声波和振动的方法,并且产生的细裂纹量可以通过冲击波施加的能量的量来控制。
可以使用由堇青石-W复合体组成的陶瓷载体作为上述的陶瓷载体,所述陶瓷载体在晶格内具有氧缺陷或者具有晶格缺陷,并且还具有细裂纹。
也可以使用具有上述两种特征的陶瓷载体。
第一和第二个发明中的符号E1和E2以及第三和第四个发明中的E1是相对溶解催化剂前体的溶剂的堇青石-W复合体的表面电位、催化剂载体的构成材料的表面电位和形成分散相的每一化合物的表面电位,并且分别是在ζ电位下测定的。催化剂溶液的pH是在这些E1和E2的基础上测定的。
下面针对堇青石-W复合体解释pH的测定方法。
首先,测定当溶剂的pH从酸性侧变到碱性侧时堇青石-W复合体的ζ电位。接下来,类似地测定构成分散相的化合物的ζ电位。
接下来,考虑获得图3中所示结果的情形(将在下面描述)以及选择由负络合离子组成的材料作为催化剂前体时的情形。这里,考虑分散相仅由TiO2组成的陶瓷载体。
作为基质相的复合体具有5.5的pH和0的表面电位,并且作为分散相的TiO2的pH是2.1,表面电位是0。在所述复合体和TiO2中表面电位都随pH变大而降低。
因此,当将陶瓷载体浸泡在pH调整至5.5或更低的催化剂溶液中时,载在基质相中的催化剂量将远大于载在分散相中的催化剂量。因此,当其pH低于5.5时,基质相的表面变成正极性,这样正好吸引由负络合离子组成的催化剂组分。当其pH为2.1或更大时,分散相的表面电位变为负极性,此时由负络合离子组成的催化剂组分几乎不粘附到分散相上。
因此,在所述的情形下,通过将pH调整至5.5或以下,可以获得本发明的效果。
为了进一步降低粘附到分散相上的催化剂组分的量,优选将pH调整至2.1或以上以及5.5或以下。在这种情况下,在分散相和催化剂组分之间存在排斥力,或者在它们之间不存在电吸引,如图5和6所示,这样催化剂组分不能容易地粘附到分散相上。
接下来,考虑获得图8所示结果的情形并且催化剂组分选择由正络合离子组成的材料作为催化剂前体。
作为母料的复合体具有m的pH并且表面电位为0,而分散相的pH是n,表面电位是0。在复合体和分散相中随着pH变大,其表面电位者降低。
因此,当将陶瓷载体浸泡在pH调整至大于m的催化剂溶液中时,载在基质相中的催化剂量将远大于载在分散相中的催化剂量。因此,当其pH大于m时,基质相的表面变成负极性,这样正好吸引由正络合离子组成的催化剂组分。当其pH为n或更小时,分散相的表面电位变为正极性,因而由正络合离子组成的催化剂组分几乎不粘附到分散相上。
因此,在所述的情形下,通过将pH调整至m或以上,可以获得本发明的效果。
在第一和第二个发明中,为了进一步降低粘附到分散相上的催化剂组分的量,优选将pH调整至大于m并小于n。在这种情况下,在分散相和催化剂组分之间存在排斥力,或者在它们之间不存在电吸引,这样催化剂组分不能容易地粘附到分散相上。
在第一和第二个发明中,当分散相由许多组分组成时,可以通过上述对在陶瓷载体的表面上形成具有最大占有面积的分散相的组分的观察来确定催化剂溶液的pH。
可以与上述复合体相同的方式确定除堇青石-W复合体以外的其它陶瓷载体的pH。
顺便提一下,在实施例中将描述ζ电位的测定实施例。
在第一至第四个发明中,催化剂溶液是通过将催化剂前体溶解在溶剂中制得的。根据催化剂前体的种类选择溶剂,而催化剂前体则是根据待载的催化剂的种类选择的。催化剂前体形成由催化剂溶液中的负或正络合离子组成的催化剂组分。
当以这种方式调整催化剂溶液的pH以满足第一至第四个发明的条件时,优选使用酸或碱进行滴定。在这种情况下,必需选择那些不腐蚀陶瓷载体并且不容易与催化剂前体、溶剂和作为催化剂组分的负和正络合离子反应的物质作为滴定用酸和碱。
根据催化剂前体的种类,设定所需pH的催化剂溶液可以通过调整溶解在溶剂中的催化剂前体的量来制备。
使用贵金属催化剂如铂、钯或铑作为基料,根据第一至第四个发明的陶瓷催化剂体可以载有三路催化剂(three-way catalyst)、氧化催化剂和脱臭催化剂。
优选使用水作为溶剂和至少一种选自如下的化合物六氯铂酸、硝酸四氨合铂、氯化四氨合钯、六氯铑酸铵、硝酸二硝基二氨合铂、氯化四氨合铂、氯化钯和硝酸钯。
以这种方式,催化剂络合离子可以选择性地吸附到基质相上(在第一和第二个发明中)并且牢固地吸附(在第一至第四个发明中)。
当选择上述催化剂前体和溶剂时,使用硝酸或氨水调整pH。具有所需pH的催化剂溶液可以通过调整催化剂前体的溶解量来制备。
实施例1本实施例给出一种陶瓷催化剂体的制备方法,它将催化剂载在陶瓷载体上,所述陶瓷载体含有由堇青石-W复合体组成的基质相和由除堇青石-W复合体之外的化合物组成的分散相。
换句话说,将催化剂前体溶解在溶剂中以制得含有催化剂组分的催化剂溶液,所述催化剂组分由催化剂前体产生的负络合离子组成。
接下来,调整催化剂溶液的pH以满足关系E1>E2并且E1>0,其中E1是相对催化剂溶液的pH的陶瓷载体的基质相的表面电位,E2是陶瓷载体的分散相的表面电位。然后将所述陶瓷载体与所述催化剂溶液接触。
在催化剂组分载在陶瓷载体上之后,进行热处理以将由堇青石-W复合体组成的基质相与催化剂组分结合,并将所述催化剂载在陶瓷载体上。
接下来,给出详细解释。
本实施例中的陶瓷催化剂体1使用陶瓷载体作为基料并包括载在陶瓷载体表面上的废气净化催化剂,如图1所示。陶瓷催化剂体1被安装到汽车发动机的排气管上,用于净化从汽车发动机放出的废气。
本实施例的陶瓷载体呈蜂窝结构并且具有许多孔腔10,在催化剂使用过程中这些小孔起到废气通道的作用。催化剂主要载在面对气流通道的壁表面上。图1中所示的箭头Z代表催化剂将要处理的废气的流动方向。
本实施例的陶瓷载体包括由堇青石-W复合体组成的基质相和由除堇青石-W复合体之外的化合物组成的分散相。
所述基质相具有将堇青石的Al元素用W代替而制得的组成。分散相不含所述复合体并由氧化钛等组成,如后面的加工方法中所述,这些成分的加入可以促进W的取代。
图2是陶瓷载体的组成示意图。如图所示,分散相12以岛状沉积到基质相11上。
接下来,将解释本实施例中的陶瓷催化剂体的制备方法。
制备滑石、熔融二氧化硅和氢氧化铝为堇青石材料。制备WO3作为W源,并制备TiO2作为促进W取代的材料,从而使W容易进入堇青石。
将适量的粘合剂(甲基纤维素)、润滑剂、湿润剂(多元醇衍生物)和水分加入到这些材料中,并将所述混合物捏合并转变成粘土。
之后将所得粘土状材料成型为蜂窝形状,所述蜂窝形状具有100μm的孔壁厚度,400psi的孔密度和50mm的直径,将其干燥并在1290℃于空气中烧结。当通过X-射线衍射分析该蜂窝结构的陶瓷组分时,发现其中主要有堇青石和TiO2。
对所述堇青石的X-射线衍射结果进行Rietveld分析,证实Al已被W取代。
接下来,将催化剂载在上述的陶瓷载体上。
在本实施例中,将六氯铂(IV)酸作为催化剂前体溶解在作为溶剂的水中,以制备含有作为催化剂组分的负络合离子[PtCl6]2-的催化剂溶液。
顺便提一下,通过流动电位系统测定ζ电位以确定堇青石-W复合体的表面电位和TiO2的表面电位,结果示于图3。
由图3可以清楚地看到,当pH低于5.5时,堇青石-W复合体的表面电位是正的。TiO2的表面电位低于堇青石-W复合体的,与pH无关。
当pH大于2.1时,堇青石-W复合体的表面电位是正的并且TiO2的表面电位是负的,并且当pH变小时堇青石-W复合体的表面电位变大。
当堇青石-W复合体的表面电位变大时,作用于堇青石-W复合体与由负络合离子组成的催化剂组分之间的吸引力也变大。
这里,当制备催化剂溶液时,将所需量的六氯铂酸溶解在水中,然后用硝酸调整以获得pH为2.2的催化剂溶液。室温下将陶瓷载体在这种环境下在催化剂溶液中浸泡5分钟,同时搅拌。之后从催化剂溶液中取出其上粘附有催化剂组分的陶瓷载体,并将其干燥和烧结。
由此获得载有Pt的陶瓷催化剂体。
测得该陶瓷催化剂体上载有的Pt量为1g/l。
当用TEM(透射式电子显微镜)测定通过上述方法制得的陶瓷催化剂体中的铂的负载条件时,可以证实在由堇青石-W复合体组成的基质相的表面上有大量几nm的铂颗粒。然而,在由TiO2组成的分散相的表面上却几乎不存在铂颗粒。
为了对比,将相同的陶瓷载体浸泡在硝酸四氨合铂的水溶液中,干燥并烧结,从而以1g/l的比例将Pt载在该表面上。
硝酸四氨合铂的水溶液的pH是0.6,并且四氨合铂离子是正络合离子。由上述的图3可见,在pH为8.6时TiO2和堇青石-W复合体的表面电位都是负的,并且TiO2的表面电位的绝对值大于复合体的。
当通过TEM(透射式电子显微镜)测定对比实施例的陶瓷催化剂体中的铂的负载条件时,证实在由堇青石-W复合体组成的基质相的表面上有约几nm的铂颗粒,但在由TiO2组成的分散相的表面上有约10nm的铂颗粒。换句话说,更大量的铂颗粒载在分散相上。
因此从上面给出的结果可以发现,采用本实施例的制备方法,通过将铂颗粒选择性地载在基质相上可以制备所述陶瓷催化剂体。
下面将解释本实施例的功能和效果。
本实施例使用含有由堇青石-W复合体组成的基质相和由除堇青石-W复合体之外的TiO2组成的分散相的陶瓷载体。
具有这种组成的陶瓷载体是通过用W替换堇青石中的一部分晶格获得的材料,并且催化剂通过物理吸附以及复合体中的W与催化剂之间的化学结合而牢固地负载在基质相上。
因此,催化剂可以直接载在陶瓷载体上,不用象过去那样单独沉积具有高比表面积的涂布相。
当通过本实施例的制备方法制备陶瓷催化剂体时,催化剂选择性地载在所述陶瓷载体的基质相上。
因此,由于载在分散相(其中易于发生热聚集和脱落)上的催化剂的量小,因此可以获得不易受因热聚集导致的性能降低的影响的陶瓷催化剂,并且所得催化剂耐用性高。
本实施例可提供陶瓷催化剂载体的制备方法,它可以将催化剂直接载在陶瓷载体上,不用在陶瓷载体上沉积涂布层,并且不易发生热降解。
实施例2本实施例对实施例1中所述的本发明的陶瓷催化剂体和对比实施例中通过浸渗法进一步将0.2g/l铑载在陶瓷催化剂体中的催化剂体进行对比测试。
本实施例中所用的陶瓷催化剂体为圆柱体形状,直径为30mm,轴向的长度为50mm(沿图1中的箭头Z的方向)。
为了评价催化剂的净化性能,使用组成与汽车以40kg/hr的恒定速度行驶时排放的废气组成相同的模拟bench气体,测定烃(HC)50%净化温度。对于耐热性条件,将该样品在800℃下的电炉中于空气中静置5小时。
本发明的陶瓷催化剂体的最初50%净化温度是243℃,并在耐热性测试之后仍为243℃。换句话说,在耐热性测试之后50%净化温度没有变化。
在对比实施例中,陶瓷催化剂体的最初50%净化温度是230℃,但是在耐热性测试之后升高到252℃。
换句话说,在耐热性测试之前和之后的温差是22℃。由此可见对比实施例的陶瓷催化剂体在耐热性测试之后发生了退化。
这是由于在本发明的陶瓷催化剂体中催化剂主要载在基质相上,而在对比实施例的陶瓷催化剂体内催化剂主要载在分散相上。在催化剂载在基质相上的本发明中,催化剂和基质相具有高的结合强度。因此,可以防止因耐热性测试导致的催化剂聚集,并且可以抑制因耐热性则试导致的催化剂性能退化。
在对比实施例的陶瓷催化剂体中,催化剂载在分散相上,该分散相仅能通过物理吸附负载催化剂,因此催化剂的保持强度低,在耐热性测试后催化剂发生聚集并且净化性能受损。
本发明提供了一种陶瓷催化剂体的制备方法,它可以将催化剂直接载在一陶瓷载体上,不用在该陶瓷载体上沉积涂布层。在本发明中,制备含有催化剂组分的催化剂溶液,所述催化剂组分由得自催化剂前体的负络合离子组成,并且调整催化剂溶液的pH以满足关系E1>E2并且E1>0,其中E1是由堇青石-W复合体组成的基质相相对催化剂溶液的pH的表面电位,E2是由除堇青石-W复合体之外的化合物组成的分散相的表面电位。在将陶瓷载体与催化剂溶液接触以负载催化剂组分之后,进行热处理以使由堇青石-W复合体组成的基质相与催化剂组分结合,从而将所述催化剂直接负载在陶瓷载体上。
陶瓷催化剂体的制备方法
- 专利详情
- 全文pdf
- 权力要求
- 说明书
- 法律状态
查看更多专利详情
下载专利文献
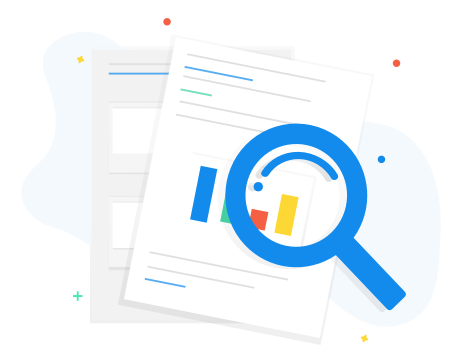
下载专利
同类推荐
-
小池和彦名取荣治汤玉斐杨建杨建
您可能感兴趣的专利
-
陈秀丽陈秀丽陈秀丽王红云王红云
专利相关信息
-
周延春谢建林