专利名称:人造石材的制造方法 以往,作为模仿大理石等石材的人造石材,已知有用白水泥凝固大理石粒并对其表面进行研磨的水磨石,以及将大理石或花网板等的石粒混入树脂中凝固后得到的人造石材。又,专利文献1(日本专利第2551858号公报)公开了这样一种人造大理石的制造方法,所述人造大理石的制造方法包括在底部为平面状的玻璃座型箱的内侧涂敷脱模剂的第1工序;在型箱内的玻璃座上涂敷透明树脂,在所述透明树脂半干的状态下,放置花纹纸,边抽出空气,边使透明树脂和花纹纸密接粘合的第2工序;在花纹纸上涂敷石粒和树脂的混合物的背衬材料的第3工序;在所述背衬材料上放入木制芯体材料,再在其上及周围用所述背衬材料被覆的第4工序;以及在放置适当时间后,将形成的人造大理石从型箱中卸下的第5工序。然而,用以往方法制造的、在全体中含有石粒的人造石材存在有比重大、重量重、施工费事的问题。又,所述人造石材也存在虽具有优异的耐压强度,但耐曲折强度差的问题。其次,专利文献1所述发明的人造大理石,由于其中加入木制芯体材料,因此能够制造比重轻、具有优异的耐压缩及耐曲折强度的人造大理石,但在需对该人造大理石的角进行磨圆处理的场合,若进行研磨或切削则花纹纸的端部露出,故使得加工困难。另外,上述大理石存在的问题还有,只能形成由花纹纸形成的同一图案,比起天然大理石或缟玛瑙石(条纹大理石),其花纹深度不大,即,缺乏立体感,呈平面化。
本发明系鉴于上述问题而作,本发明的目的在于提供一种人造石材的制造方法,所述人造石材重量轻而具有优异的耐压、耐弯曲强度,如同天然大理石或缟玛瑙石(条纹大理石)具有图案深度。按照所述目的,本发明技术方案1所述的人造石材的制造方法包括下述(1)~(5)的工序。(1)在预先准备的、由具有一定厚度的浮法玻璃或不锈钢制平板构成的模制台上,在由使用浮法玻璃或硬质合成树脂材料的壁材构架形成的型箱的内侧底面和内侧垂直面上涂敷表面涂层用不饱和聚酯树脂的工序;(2)在上述表面涂层用不饱和聚酯树脂固化后,将由树脂材料组成的配炼胶料(basecompound)放入所述型箱,形成规定厚度的基底层的工序,所述树脂材料是相对100重量份的不饱和聚酯树脂,配入低收缩剂10~40重量份、无机质填充料的微粉200~400重量份、固化剂0.4~3.5重量份及适当的着色颜料,进行搅拌及脱泡处理而得;(3)还将可留有间隙地装入上述型箱内、且与制品厚度相应厚度的层压板载于上述基底层上的工序;(4)在上述层压板的周围及上面,浇注上述树脂材料直至型箱上表面的工序;(5)上述树脂材料在常温下固化后,从所述型箱脱模,得到比重为1.0~1.1的轻量、不易开裂的模制品的工序。按照上述目的,本发明技术方案2所述的人造石材的制造方法包括下述(1)~(5)的工序。
(1)在预先准备的、由具有一定厚度的浮法玻璃或不锈钢制平板构成的模制台上,在由使用浮法玻璃或硬质合成树脂材料的壁材构架形成的型箱的内侧底面和内侧垂直面上涂敷表面涂层用不饱和聚酯树脂的工序;(2)在上述表面涂层用不饱和聚酯树脂固化后,将配炼胶料放入所述型箱内,形成规定厚度的基底层的工序,所述配炼胶料是将(a)相对不饱和聚酯树脂100重量份,配入低收缩剂10~40重量份、无机质填充料的微粉200~400重量份、固化剂0.4~3.5重量份及适当的着色颜料,进行搅拌及脱泡处理而得到的树脂材料,和(b)相对不饱和聚酯树脂100重量份,配入低收缩剂10~40重量份、无机质填充料的微粉200~400重量份、固化剂0.4~3.5重量份及适量的与上述着色颜料不同颜色的着色颜料,进行搅拌及脱泡处理而得到的花纹显露材料,混合至颜色不融合的程度而形成;(3)再将可留有间隙地装入上述型箱内、且与制品厚度相应厚度的层压板载于上述基底层上的工序;(4)在上述层压板的周围及上面,浇注上述树脂材料或上述配炼胶料直至型箱上表面的工序;(5)上述树脂材料在常温下固化后,从所述型箱脱模,得到比重为1.0~1.1的轻量、不易开裂的模制品的工序。
按照上述目的,本发明技术方案3所述的人造石材的制造方法包括下述(1)~(5)的工序。
(1)在预先准备的、由具有一定厚度的浮法玻璃或不锈钢制平板构成的模制台上,在由使用浮法玻璃或硬质合成树脂材料的壁材构架形成的型箱的内侧底面和内侧垂直面上涂敷表面涂层用不饱和聚酯树脂的工序;(2)在上述表面涂层用不饱和聚酯树脂固化后,将(a)相对不饱和聚酯树脂100重量份,配入低收缩剂10~40重量份、无机质填充料的微粉200~400重量份、固化剂0.4~3.5重量份及适当的着色颜料,进行搅拌及脱泡处理而得到的树脂材料,和(b)相对不饱和聚酯树脂100重量份,配入低收缩剂10~40重量份、无机质填充料的微粉200~400重量份、固化剂0.4~3.5重量份及适量的与上述着色颜料不同颜色的着色颜料,进行搅拌及脱泡处理而得到的花纹显露材料,无间隙地装入型箱内,从上述型箱的内侧底面起到规定厚度形成基底层的工序;(3)再有,将可留有间隙地装入上述型箱内、且具有与制品厚度相应厚度的层压板载于上述基底层上的工序;(4)在上述层压板的周围及上面,浇注上述树脂材料或花纹显露材料直至型箱上表面的工序;(5)上述树脂材料在常温下固化后,从所述型箱脱模,得到比重为1.0~1.1的轻量、不易开裂的模制品的工序。
在上述技术方案1~3所述的人造石材的制造方法中,模制台由具有厚度为例如8~10mm左右的浮法玻璃或不锈钢制平板形成,型箱是在模制台上,由使用例如厚度为2.5~6mm(例如3mm左右)的浮法玻璃或硬质合成树脂材料(例如,聚氯乙烯或聚乙烯树脂等)的壁材构架形成。型箱可形成俯视为三角形、四边形以上的多边形、圆形、椭圆形及其他任意形状的一种,也可形成这些形状的组合形状。
使用硬质合成树脂材料的壁材,例如,包括在由薄的胶合板等形成的侧壁内侧贴合硬质合成树脂材料的场合。又,表面涂层用不饱和聚酯树脂可以使用透明(也可是多少带有一些其内部可透视程度的色彩)的树脂,其厚度涂敷至约0.5mm(也可是0.3~1mm)。另外,较好的是,预先在型箱的内侧底面和内侧垂直面上涂敷脱模剂,以便于脱模。
相对不饱和聚酯树脂100重量份,配入低收缩剂10~40重量份、无机质填充料的微粉200~400重量份、固化剂0.4~3.5重量份及适当的着色颜料,例如边用搅拌机进行搅拌、混合,边进行由例如真空脱泡处理,制得具有适度流动性的树脂材料。利用脱泡的进行,可防止在树脂材料上形成针孔状空穴。
对不饱和聚酯树脂添加固化剂进行充分混合,则在不饱和聚酯树脂中产生聚合反应,不饱和聚酯树脂渐渐固化,成为固化状态。藉由配合的无机质填充材料微粉及着色材料,可以人工调节得到各种石材的色彩及质感。又,将不饱和聚酯树脂与固化剂,较好的是,与固化促进剂共同混合,使之固化,由此,可制得任意形状、及尺寸的人造石材(模制品)。
作为不饱和聚酯树脂,可以制得1)选自如马来酸、马来酸肝、富马酸、衣康酸、柠康酸、氯代马来酸、乌头酸及二氢化粘康酸的一种或二种以上的不饱和二元酸(包括其酸酐),和2)选自如乙二醇、二乙二醇、丙二醇、二丙二醇、T二醇、新戊二醇、1,3-丁二醇、1,6-己二醇及加氢双酚A的一种或二种以上的多元醇的缩聚物,3)再加入如乙烯单体及苯乙烯单体的一种或二种组成的交联剂制成。
又,不饱和聚酯树脂较好的是使用粘度为例如250~500mPa·s(帕斯卡秒)。如不饱和聚酯树脂的粘度不到250mPa·s,则粘度低,涩爽,难以使用;而如果不饱和聚酯树脂的粘度超过500mPa·s,则过硬,且容易导入气泡。由于不饱和聚酯树脂是透光性的,因此,可以透视看见内部结构,得到具有进深感的人造石材。
低收缩剂用于降低固化体积收缩率约为6~10%的不饱和聚酯树脂的收缩,减少模制品的翘曲(凹凸)及扭转。作为低收缩剂,可以使用一般的不饱和聚酯树脂用的低收缩剂。相对不饱和聚酯树脂100重量份,配入10~40重量份,较好的是,配入20~30重量份。低收缩剂的配合量相对不饱和聚酯树脂100重量份,如不到10重量份,则容易发生模制品的翘曲及扭转;超过40重量份,则反应钝化,有难以固化的可能。
作为低收缩剂,可以举出有1)丙烯酸或甲基丙烯酸的低级烷基酯(例如,选自甲基丙烯酸甲酯、甲基丙烯酸乙酯、甲基丙烯酸丁酯、丙烯酸甲酯以及丙烯酸乙酯的一种或两种以上),2)苯乙烯、氯乙烯及酯酸乙烯的任一种的单独聚合物或其两种以上的共聚物类。再有,作为上述低收缩剂,也可以是上述乙烯单体中的至少一种,和含有甲基丙烯酸月桂酯、甲基丙烯酸异乙烯酯、丙烯酰胺、甲基丙烯酰胺、丙烯酸羟基烷基酯或甲基丙烯酸酯、丙烯腈、甲基丙烯腈、丙烯酸、甲基丙烯酸、及甲基丙烯酸鲸蜡硬脂酸酯的任一种的单体的至少一种的共聚物。又,作为上述低收缩剂,例如,由乙酸纤维素(酯)、乙酸丙酸纤维素、聚乙烯、聚丙烯及饱和聚酯的任一种组成。
无机质填充材料微粉用于缓和不饱和聚酯树脂固化时的收缩及提高人造石材的质感。作为无机质填充材料,可以使用例如,氢氧化铝、碳酸钙、滑石、及含水石粉的一种或二种以上、粒径为50~100μm的细微粉末。无机质填充材料可以在相对不饱和聚酯树脂100重量份为200~400重量份的范围内添加。如无机质填充材料相对不饱和聚酯树脂100重量份的添加量不到200重量份,则不饱和聚酯树脂固化时的收缩缓和效果不佳,如无机质填充材料相对不饱和聚酯树脂100重量份的添加量超过400重量份,则人造石材的强度低下。
作为固化剂,有由市售的二烯丙基过氧化物类、过氧化酯类、过氧化氢类、二烷基过氧化物类、酮过氧化物类、过氧化物酮缩醇类、烷基过酯类、及过碳酸酯类的任一种组成的固化剂,例如,可以使用作为酮过氧化物类(有机过氧化物类)的55%浓度的过氧化甲乙酮。另外,在低温固化不饱和聚酯树脂的场合,为促进固化,较好的是,并用选自钴系、钒系、或锰系等的金属碱类、叔胺类、季胺盐、及硫醇类的至少一种组成的固化促进剂。例如,可以使用1%浓度的萘酸钴。
固化剂的配合量,可以是相对不饱和聚酯树脂100重量份,配入固化剂0.4~3.5重量份,较好的是,0.5~3.0重量份。如固化剂相对不饱和聚酯树脂100重量份的配入量不到0.4重量份,则难以发生固化,而其配入量超过3.5重量份,则有时虽发生急剧胶体化,但有时仍会发生未固化,不饱和聚酯树脂发生变色。又,在使用固化促进剂时,相对不饱和聚酯树脂100重量份,可配入固化促进剂0.4~1.3重量份,较好的是,0.4~1.0重量份。如固化促进剂相对不饱和聚酯树脂100重量份的配入量不到0.4重量份,则固化末得到促进,而其配入量超过1.3重量份,则虽发生急剧胶体化,但有时发生未固化的现象,不饱和聚酯树脂发生变色。藉由固化促进剂的添加,可在夏天及冬天的全部,确保使用时间,使不饱和聚酯树脂固化。
作为着色颜料,可以使用市售的聚酯用颜料,可以藉此赋予人造石材以各种颜色。着色颜料可以适量,但较好的是,相对不饱和聚酯树脂100重量份的配入量为0.04~5.0重量份的范围。
在技术方案2及3的人造石材的制造方法中,作为花纹显露材料,可以使用不同于上述树脂材料的着色颜料进行制造。又,用于花纹显露材料的不饱和聚酯树脂,其浓度最好高于使用于树脂材料的不饱和聚酯树脂的粘度,以不使花纹显露材料的颜色和树脂材料的颜色混合。藉由花纹显露材料的使用,可以使人造石材着以多种色彩,获得更具立体感的缟玛瑙石(条纹大理石)花纹。又,在载持层压板时,藉由例如振动器使层压板振动,使花纹显露材料和树脂材料自然融合,现出深度。
又,在技术方案2所述的人造石材的制造方法中,所谓“混合至色彩不融合的程度”是指,混合至颜色不致混合变成其他颜色的程度。
在技术方案1~3所述的人造石材的制造方法中制造树脂材料的工序中,还有在技术方案2、3所述的人造石材的制造方法中制造花纹显露材料的制造工序中,也可在搅拌不饱和聚酯树脂、低收缩剂、无机质填充材料粉末、固化剂及着色材料之时配入消泡剂,由此,可在搅拌上述材料的同时有效地在短时间内去除带入的空气。消泡剂可以使用市售的聚酯用消泡剂。
又,基底层的厚度较好的是形成在6~15mm。如基底层的厚度不到6mm,则可以看见其中的层压板,或者,会发生翘曲或扭转。另外,如基底层的厚度大于15mm,则树脂材料的使用量增加,成本增高,同时,基底层的固化时间缩短,发热量增大,容易发生翘曲或开裂等,导致人造石材品质下降。
再有,较好的是,基底层上的层压板使用胶合板,且作成可以一定间隙(使型箱内侧面与其对应的层压板的面之间隔为,例如,8~15mm)装入型箱内的大小,其厚度作成从成品厚度减去12~30mm的数值。另外,在成品厚度较薄的场合,也可将装入的层压板的厚度作成成品厚度的约一半。
藉由层压板的使用,可以在减轻人造石材的收缩及翘曲、增加强度的同时,减轻重量。且,在将人造石材用于桌子等场合,可将木螺钉直接螺合于人造石材上,而无须承木。
较好的是,将锤载于层压板上使其重量压合基底层和层压板。如在载持锤的状态下,在常温(例如,15~30度),放置20~60分钟,使不饱和聚酯树脂聚合,基底层固化,同时,使基底层和层压板粘合。再有,在层压板周围及上面,在浇注树脂材料直至型箱上表面之后,再进行例如,4~15小时左右、常温下的固化,从型箱脱模,得到模制品。
在技术方案1~3所述的人造石材的制造方法中,形成基底层的树脂材料和注入层压板周围及其上的树脂材料的成分可以相同,其成分只要是在本发明的要点内的范围,即使有所变化,也可适用本发明。再在技术方案2所述的配炼胶料及技术方案3所述的花纹显露材料中,注入基底层和层压板周围及其上的树脂材料的成分只要是在本发明的要点内的范围,即使有所变化也适用本发明。
技术方案4所述的人造石材的制造方法,系在技术方案3所述的人造石材的制造方法中,根据上述形成基底层的工序,上述花纹显露材料用浇注器具(即,注入容器)进行浇注。在技术方案4所述的人造石材的制造方法中,作为浇注容器,有,例如,储存花纹显露材料的容器和设置于容器上的喷嘴、带有如同注射器般的活塞式的汽缸、泵等排出花纹显露材料的器具。藉由注射器具的花纹显露材料的排出口的口径、及花纹显露材料的浇注速度(排出速度)等的变化,可获得多种多样的花纹。又,也可使用浇注器具浇注配炼胶料及树脂材料。
技术方案5所述的人造石材的制造方法,系在技术方案2~4所述的人造石材的制造方法中,根据上述形成基底层的工序,混合上述树脂材料和上述花纹显露材料,使其边界颜色不融合。在技术方案5所述的人造石材的制造方法中,颜色边界的搅拌可以用例如圆头刮刀等器具进行,由此,可在人造石材上形成旋涡状的花纹。
技术方案6所述的人造石材的制造方法,系在技术方案2~5所述的人造石材的制造方法中,具有多种上述花纹显露材料,且分别用不同的着色颜料附以色彩。
技术方案7所述的人造石材的制造方法,系在技术方案1~6所述的人造石材的制造方法中,用加热炉对上述模制品施以二次固化处理。在技术方案7所述的人造石材的制造方法中,二次固化在例如,温度30~50℃、较好的是40~50℃,加热处理3~4小时。加热炉可以使用通风式。二次固化较好的是在车间的氛围温度在30℃不到的条件下进行,车间的氛围温度在30~40℃的场合,特别是在夏季,可省略二次固化。在二次固化工序中,其加热温度如不到30℃,则模制品不能完全固化,超过50℃,则层压板和具有不饱和聚酯树脂及无机质填充材料的树脂材料的热膨胀系数不同,导致翘曲或扭转的发生。
技术方案8所述的人造石材的制造方法,系在技术方案1~7所述的材料的制造方法中,所述模制品被加工成对所述层压板留有一定的厚度,再在其表面涂敷表面涂层用不饱和聚酯树脂。在技术方案8所述的人造石材的制造方法中,残留厚度,即层压板周围的厚度,较好的是,作成例如,6~15mm。如上述厚度不到6mm,则可以看见其中的层压板,或者发生翘曲、扭转。
本发明技术方案1及其从属技术方案7及8所述的人造石材的制造方法包括(1)在型箱的内侧底面和内侧垂直面上涂敷表面涂层用不饱和聚酯树脂的工序,(2)在上述表面涂层用不饱和聚酯树脂固化后,将由树脂材料组成的配炼胶料放入所述型箱,形成自型箱的内侧底面起具有一定厚度的基底层的工序,(3)再将层压板载于上述基底层上的工序,(4)在上述层压板的周围及上面,浇注上述树脂材料直至型箱上表面的工序,和(5)上述树脂材料在常温下固化后,从所述型箱脱模,得到比重为1.0~1.1的轻量、不易开裂的模制品的工序。由此,可以获得重量轻、具有优异的耐压缩、耐弯曲强度、具有如同天然大理石或条纹大理石(缟玛瑙石)的深度的单色人造石材。
本发明技术方案2及其从属技术方案5~8所述的人造石材的制造方法包括(1)在型箱的内侧底面和内侧垂直面上涂敷表面涂层用不饱和聚酯树脂的工序,(2)在上述表面涂层用不饱和聚酯树脂固化后,将树脂材料和花纹显露材料混合至颜色不融合的程度,将混合的配炼胶料放入所述型箱,形成自型箱的内侧底面起具有一定厚度的基底层的工序,(3)再将层压板载于上述基底层上的工序,(4)在上述层压板的周围及上面,浇注上述配炼胶料直至型箱上表面的工序,和(5)上述树脂材料在常温下固化后,从所述型箱脱模,得到比重为1.0~1.1的轻量、不易开裂的模制品的工序。由此,可以获得重量轻、具有优异的耐压缩、耐弯曲强度、具有如同天然大理石或条纹大理石(缟玛瑙石)的自然花纹和深度的多色人造石材。
本发明技术方案3及其从属技术方案4~8所述的人造石材的制造方法包括(1)在型箱的内侧底面和内侧垂直面上涂敷表面涂层用不饱和聚酯树脂的工序,(2)在上述表面涂层用不饱和聚酯树脂固化后,将树脂材料和花纹显露材料无间隙地放入型箱,使之形成从上述型箱的内侧底面起达一定厚度的基底层的工序,(3)将层压板载于上述基底层上的工序,(4)在上述层压板的周围及上面,浇注树脂材料或花纹显露材料直至型箱上表面的工序,和(5)上述树脂材料在常温下固化后,从所述型箱脱模,得到比重为1.0~1.1的轻量、不易开裂的模制品的工序。由此,可以获得重量轻、具有优异的耐压缩、耐弯曲强度、可自由加工成具有如同天然大理石或条纹大理石(缟玛瑙石)的自然花纹、具有深度的多色人造石材。
技术方案4所述的人造石材的制造方法由于是在形成基底层的工序中,用浇注器具浇注花纹显露材料,因此,可藉由注射口口径或浇注速度的变化,形成各种各样的图案花纹。
技术方案5所述的人造石材的制造方法由于是在形成基底层的工序中,对树脂材料和花纹显露材料之间的边界进行颜色不融合程度的混合,因此,可以形成旋涡状的图纹。
技术方案6所述的人造石材的制造方法由于具有多种花纹显露材料,可分别由各不同的着色颜料进行着色,由此,可以获得更接近于天然大理石或条纹大理石(缟玛瑙石)的风格。
技术方案7所述的人造石材的制造方法由于其模制品是在加热炉中进行二次固化,因此,可以使模制品完全固化。
技术方案8所述的人造石材的制造方法由于其模制品的加工是对于层压板加工为一定厚度,因此,可以加工得到具有各种形状的模制品。另外,加工表面涂敷表面涂层用不饱和聚酯树脂,因此,可以在模制品表面打出光泽。
图1为本发明第1实施例的人造石材的制造方法的说明图。
图2为上述制造方法中对层压板的基底层进行加压的加压方法的说明图。
图3为用上述制造方法制造的模制品的说明图。
图4为对用上述制造方法制造的模制品进行加工后的桌台的说明图。
图5为本发明第2实施例的人造石材的制造方法的说明图。
图6为用该制造方法制造的模制品的说明图。
图7为本发明第3实施例的人造石材的制造方法的说明图。
图8为该制造方法中的用花纹显露材料的注射模具进行浇注的说明图。
以下,参照附图,就本发明的
作一说明,以供对本发明的理解。
这里,图1为本发明第1实施例的人造石材的制造方法的说明图,图2为上述制造方法中对层压板的基底层进行加压的加压方法的说明图,图3为利用上述制造方法制造的模制品的说明图,图4为对利用上述制造方法制造的模制品进行加工后的桌台的说明图,图5为本发明第2实施例的人造石材的制造方法的说明图,图6为利用该制造方法制造的模制品的说明图,图7为本发明第3实施例的人造石材的制造方法的说明图,图8为利用该制造方法的花纹显露材料的注射模具进行浇注的说明图。
首先,参照附图1~3,就本发明第1实施例的人造石材的制造方法进行说明。
(第1工序)在由具有约为8~10mm左右厚度的浮法玻璃构成的模制台10上,在型箱12的内侧底面13和内侧垂直面14上预先涂敷使模制品15的脱模变得容易的未图示的脱模剂,上述型箱以厚度约3mm的作为硬质合成树脂材料一例的氯乙烯的壁材11构架形成。然后,将透明的表面涂层用不饱和聚酯树脂涂敷至厚度约为0.5mm。这里,所谓透明,包括内部可透视看见这种程度、多少带有色彩的情况。
又,型箱12形成为,使其内侧尺寸与制造的模制品15(成品)的大小(纵向600mm,横向1000mm,厚30mm)的尺寸相同。又,模制台10的尺寸形成可构架壁材11的程度,例如,纵向620mm,横向1200mm。另外,为增加型箱12的强度,将补强材料16(例如,热塑性粘结剂)填充于壁材11的外侧下部。
(第2工序)在表面涂层用不饱和聚酯树脂固化,形成表面涂层17之后,相对不饱和聚酯树脂100重量份,配入低收缩剂10~40重量份、无机质填充料的微粉200~400重量份、固化剂0.4~3.5重量份及适当的着色颜料,制作由经过搅拌处理及真空脱泡处理而得到的树脂材料a组成的配炼胶料(base compound)。这里,作为不饱和聚酯树脂,使用马来酸和乙二醇的缩聚物,加入苯乙烯单体,使用粘度为250~500mPa·s(帕斯卡秒),例如,400mPa·s的树脂。低收缩剂使用甲基丙烯酸甲酯。无机质填充材料微粉使用将平均粒径在65μm、白色度在90以上的氢氧化铝和平均粒径在300μm、白色度在90以上的碳酸钙以同重量比混合的混合物。
固化剂使用如酮过氧化物的55%浓度的过氧化甲乙酮,还配入作为固化促进剂一例的1%浓度的萘酸钴。着色颜料使用市售白色的聚酯用颜料,相对不饱和聚酯树脂100重量份,配入0.04~5.0重量份。如配合使用市售的聚酯用消泡剂,则可短时间内有效消除搅拌时带入的空气,优选使用。
这里,作为对其进行搅拌的装置,可以使用作为混合机一例的回转型混合机,进行约为10分钟的搅拌和脱泡,制得树脂a。若使用具有自动翻转功能的回转型混合机,则由于可在短时间内完全混合,因此优选使用,混合机的回转速度以60rpm左右为宜。通过脱泡处理可防止在树脂材料a上形成针孔。对不饱和聚酯树脂添加固化剂,进行充分混合,则在不饱和聚酯树脂中引起聚合反应,慢慢固化,成为硬质状态。
用不锈钢制的薄勺捞取适量的配炼胶料,翻转薄勺,将配炼胶料置于型箱12内,反复该操作,无间隙地填埋型箱12的内侧底面13,再用玻璃制或不锈钢制板状拉规(尺)对配炼胶料上表面进行平滑化处理,最终自型箱12的底面起形成规定厚度为6~15mm、例如7mm的基底层18。另外,也可是,配炼胶料用浇注器具浇注,用拉规对其上表面进行平滑化处理,形成基底层18。
(第3工序)将可留有间隙地装入型箱12内、且具有与成品厚度对应的板厚的层压板(例如,胶木板)19载于基底层18上。层压板19使用如厚度为16mm、长570mm、宽970mm的层压板,以使各面分别位于与模制品15的外侧对应的面的8~15mm内侧。
如图2所示,为将层压板19压接于基底层18上,以跨接型箱12对向而置的壁材11的形态,以一定间隔配置多根,例如10根不锈钢制方管20。又,为了将从模制品15的上表面至层压板19上表面的距离设为7mm,在层压板19上载置厚度7mm的不锈钢制压紧材料21,例如,将重量10~15kg的铁制重锤22载置于方管20上面加压。由此,可将层压板19水平放置,并与型箱12上端具有一定距离的间隙。在常温下(例如,15~30℃)放置20~90分钟,随着不饱和聚酯树脂固化的同时,层压板19被压着于基底层18上。其后,除去方管20、按压材料21、及重锤22。
(第4工序)在上述层压板19的周围及上面,浇注树脂材料a,直至型箱12的上表面。
(第5工序)在常温下固化约4~15小时,形成树脂层23后,从型箱12对模制品15进行脱模(参照图3)。由于在型箱12的内侧底面13和内侧垂直面14上预先涂敷有脱模剂,因此模制品15的脱模容易。
模制品15因其中装入有层压板,其比重为1.0~1.1的轻量,可减轻模制品15的收缩和翘曲,并且能增加模制品15的强度,使其不易开裂。进一步,模制品15在加热炉(例如,空气浴装置)内,进行30~50℃、3~4小时加热处理的二次固化,使不饱和聚酯树脂完全固化。配置于型箱12内的模制品15中,此时处于下部的由表面涂层17形成的面成为模制品的上表面(表面)。
以下,参照图4,对利用本发明一实施形态的人造石材的制造方法制造的模制品15进行加工后的桌子25,进行说明。
首先,对模制品15的角进行倒角加工,使得从层压板19留有所定厚度,例如6~15mm,即在层压板19的周围,确保6~15mm的树脂层,再在除去表面涂层17后的加工表面上涂敷表面涂层用不饱和聚酯树脂,形成台面26。还有,在台面26的下部,介以载持台面26的板状的固定部28,设置有用于支承台面26的多个台脚、例如2根台脚27。另外,从固定部28的下部向层压板19螺合多根木螺钉29,固定台面26,制得桌子25。
以下,参照图5及图6,就本发明第2实施例的人造石材的制造方法作一说明。有关与第1实施例相同的人造石材的结构要件赋以相同符号,省略其详细说明(以下的实施例也同样)。
(第1工序)在模制台10上构架壁材11形成型箱12,在其内侧底面13和内侧垂直面14上涂敷脱模剂之后,将透明的表面涂层用不饱和聚酯树脂涂敷至厚为约0.5mm。还有,为增强壁材11的强度,将补强材料16装入壁材11的外侧下部。
(第2工序)在表面涂层用不饱和聚酯树脂固化而形成表面涂层17之后,制作树脂材料a,以及与树脂材料a组成材料相同、而使用仅仅是着色颜料不同的色彩的、例如茶色的花纹显露材料b。又,使用于花纹显露材料b的不饱和聚酯树脂最好是,其粘度高于使用于树脂材料a的不饱和聚酯树脂的粘度,使得花纹显露材料b的颜色不与树脂材料a的颜色混在一起。
将树脂材料a和花纹显露材料b进行混合,混合至使其二者颜色不融合的程度,即,颜色不混合至成为其他颜色的程度;将混合的配炼胶料装入型箱12,用薄勺无间隙地填埋于型箱12的内侧底面13,再用拉规对配炼胶料上表面进行平滑化处理,最终形成例如厚7mm的基底层30。又,在形成基底层30的工序中,也可以混合树脂材料a和花纹显露材料b的边界至颜色不融合的程度,形成旋涡状花纹。也可在制造树脂材料a和花纹显露材料b时,添加消泡剂。
(第3工序)将可留有间隙地装入型箱12内、且具有与成品厚度对应的板厚的层压板19载于基底层30上。如同实施例1,将层压板19压合于基底层30上。在对层压板19进行加压时,如使用振动器使层压板19振动,则树脂材料a和花纹显露材料b可自然融合,露出深度,因此优选使用。
(第4工序)在上述层压板19的周围及上面,将配炼胶料(树脂材料a与花纹显露材料b的混合物)浇注,直至型箱12的上表面。另外,也可取代配炼胶料,浇注树脂材料a。
(第5工序)在常温下固化约4~15小时,形成树脂层32后,从型箱12脱模模制品31(参照图6)。
由于在型箱12的内侧底面13和内侧垂直面14涂敷有脱模剂,模制品31的脱模容易。模制品31的比重为1.0~1.1的轻量,不易开裂。进一步,模制品31在加热炉内,进行30~50℃、3~4小时加热处理的二次固化,使不饱和聚酯树脂完全固化。型箱12内配置的模制品31中,此时处于下部的由表面涂层17形成的面成为模制品的上表面(表面)。
以下,参照图7及图8,就本发明第3实施例的人造石材的制造方法作一说明。
(第1工序)对在模制台10上构架壁材11而形成的型箱12的内侧底面13和内侧垂直面14涂敷脱模剂之后,将透明的表面涂层用不饱和聚酯树脂涂敷至厚为约0.5mm。为增强壁材11的强度,将补强材料16装入壁材11的外侧下部。
(第2工序)在表面涂层用不饱和聚酯树脂固化,形成表面涂层17之后,制作树脂材料a,及花纹显露材料b。如图8所示,用具有储存花纹显露材料b的容器34和容器34上设置的喷嘴35的浇铸器具36,将花纹显露材料b注入型箱12的内侧底面上。通过改变浇注器具36的喷嘴35的排出口37的口径,或使花纹显露材料b的浇注速度(排出速度)变化,可以制得各种花纹图案。
其次,将树脂材料a装入型箱12,用薄勺无间隙地填埋型箱12的内侧底面,再用拉规对配炼胶料上表面进行平滑化处理,最终形成例如厚7mm的基底层38。又,在形成基底层38的工序中,也可以薄勺等搅拌树脂材料a和花纹显露材料b的边界,形成旋涡状花纹。也可在制造树脂材料a和花纹显露材料b时,添加消泡剂。
(第3工序)将层压板19载于基底层38上。如同实施例1,将层压板19压合于基底层38上。在对层压板19进行加压时,如使用振动器使层压板19振动,则树脂材料a和花纹显露材料b可自然融合,露出深度,因此优选使用。
(第4工序)在上述层压板19的周围及上面,浇注树脂材料a,直至型箱12的上表面。另外,可取代树脂材料a,如同基底层38,分别加入树脂材料a与花纹显露材料b。
(第5工序)在常温下固化约4~15小时,形成树脂层32a后,从型箱12脱模模制品39。由于在型箱12的内侧底面13和内侧垂直面14上涂敷有脱模剂,模制品39的脱模容易。模制品39的比重为1.0~1.1的轻量,不易开裂。另外,模制品39在加热炉内,进行30~50℃、3~4小时加热处理的二次固化,使不饱和聚酯树脂完全固化。型箱12内配置的模制品39中,此时处于下部的由表面涂层17形成的面成为模制品上表面(表面)。
本发明并不限于上述实施形态,在不脱离本发明的要点的范围内可有所变更。例如,组合上述各个实施例及变化例的一部分或全部,以构成本发明的人造石材的制造方法的场合,也包含于本发明的权利要求范围内。
例如,在上述实施例的人造石材的制造方法中,是以具有厚度的浮法玻璃形成模制台的,但也可适用不锈钢制平板。又,在模制台上,是将使用了硬质合成树脂材料一例的聚氯乙烯的壁材构架形成型箱的,但也可使用聚乙烯树脂等的高湿合成树脂材料及浮法玻璃形成壁材。另外,型箱形成俯视为矩形的形状,但也可形成为正方形、三角形、五边形以上的多边形、圆形、椭圆形中的任意一种,还可作成这些形状的组合。使用硬质合成树脂材料形成壁材的场合,也可是,其外侧由薄板的胶合板形成,其内侧可贴合硬质合成树脂材料。
不饱和聚酯树脂、低收缩剂、无机质填充料、固化剂及着色颜料,分别可以使用除上述说明以外的物质。花纹显露材料是仅由一种颜色形成了一种,但也可使用不同的着色颜料,作成彩色的多种花纹显露材料,使用上述材料形成人造石材,作成更接近于天然大理石及缟玛瑙石(条纹大理石)的风格。另外,以上是对形成板状的模制品角部进行倒角处理,使对于层压板留有一定厚度进行加工,再在加工表面涂敷表面涂层用不饱和聚酯树脂的,但也可不必涂敷这些树脂,对于层压板留有一定厚度进行加工。
10模制台,11壁材,12型箱,13内侧底面,14内侧垂直面,15模制品,16补强材料,17表面涂层,18基底层,19层压板,20方管,21压紧材料,22重锤,23树脂层,25桌子,26台面,27台脚,28固定部,29木螺钉,30基底层,31模制品,32、32a树脂层,34容器,35喷嘴,36浇注器具,37排出口,38基底层,39模制品。
一种重量轻、耐压耐曲折强度高、具有如大理石、缟玛瑙石般色泽深度的人造石材的制造方法。包括在型箱(12)内侧底面(13)和内侧垂直面(14)上涂敷表面涂层用不饱和聚酯树脂的工序;在表面涂层用不饱和聚酯树脂固化后,将由定量配合不饱和聚酯树脂、低收缩剂、无机质填充粉料、固化剂及着色颜料进行搅拌及脱泡处理而得的树脂材料组成的配炼胶料注入型箱(12),形成规定厚度的基底层(18)的工序;将可留有间隙地装入上述型箱(12)内且与制品厚度相应厚度的层压板(19)载于基底层(18)上的工序;在上述层压板(19)的周围及上面,浇注上述树脂材料直至型箱(12)上表面的工序;在常温下固化后从型箱(12)脱模得到模制品(15)的工序。
人造石材的制造方法
- 专利详情
- 全文pdf
- 权力要求
- 说明书
- 法律状态
查看更多专利详情
下载专利文献
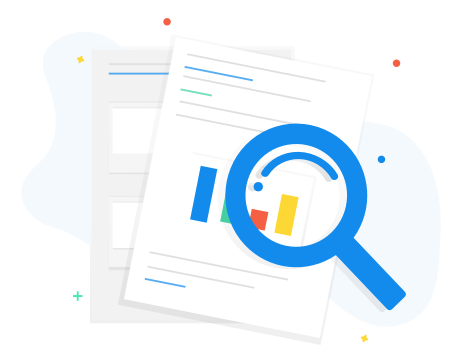
下载专利
同类推荐
-
裵正洙, 李震皓裵正洙, 李震皓裵正洙, 李震皓裵正洙, 李震皓葛怀友王新, 王桂英
您可能感兴趣的专利
-
吴贞义吴贞义吴贞义吴贞义魏从业J·H·阿伦斯J·H·阿伦斯
专利相关信息
-
J·H·阿伦斯J·H·阿伦斯J·H·阿伦斯蒂莫·皮沃斯基, 贝恩德·威尔维斯蒂莫·皮沃斯基, 贝恩德·威尔维斯蒂莫·皮沃斯基, 贝恩德·威尔维斯丘云灵, 熊玉