一种道路路面用普通硅酸盐水泥及生产方法
- 专利详情
- 全文pdf
- 权力要求
- 说明书
- 法律状态
专利名称::一种道路路面用普通硅酸盐水泥及生产方法::本发明涉及一种可适用于各种道路路面混凝土的普通硅酸盐水泥及生产方法。目前,由于交通运输事业的飞速发展,高等级公路的修建任务也越来越繁重,道路沥青也就越来越供不应求,并且价格呈上涨趋势。因此,国家制定了一系列的政策鼓励各地增加一次性投入,修筑使用时间长,维修费用低的水泥混凝土路面。用于道路路面特别是高等级道路路面的水泥,必须具有很高的耐磨性和很小的干缩率,为此国家标准GB13693-92《道路硅酸盐水泥》技术要求中规定水泥熟料中铝酸盐相(C3A)必须小于5.0%,铁相(C4AF)必须大于16.0%,且规定水泥的耐磨性以磨损量表示不得大于3.60Kg/m2,水泥的28天干缩率不得大于0.10%。现有的普通硅酸盐水泥和矿渣硅酸盐水泥的抗折强度、耐磨性能及收缩率等性能不如道路硅酸盐水泥,按国标生产道路硅酸盐水泥将显著增加生产工艺的困难,增高生产成本。所以研究生产耐磨性好、收缩率小,能用于道路工程用的普通硅酸盐水泥势在必行。中国专利CN1050859A提出的《铜矿渣配料烧制硅酸盐水泥熟料的方法》,是采用石灰石、粘土为主要原料,校正原料为高铝土、粉煤灰、沙岩、石煤渣,烧成方法是用全黑生料,暗火操作。其特征在于用铜矿渣代替铁粉(硫酸渣),用发热量3000-4000千卡/Kg低质煤取代优质煤,该方法的目的在于克服了现有生产技术中只能用优质煤的局限性。CN1078220A公开一种“电炉磷矿渣和高炉矿渣配料生产水泥熟料的方法”,它是在生料配料时加入电炉磷渣和高炉矿渣配料全部(或部分)取代粘土,P2O5计控制在0.2-0.6%,高炉矿渣的加入量以生料重量计为5-20%,采用该方法生产的水泥,不能完全符合道路用特种硅酸盐水泥的品质和特性要求。本发明的目的在于提供一种耐磨性高、干缩率小,并能适用于各种道路路面混凝土的普通硅酸盐水泥及简单生产方法。本发明由于采用人工控制硅酸盐水泥熟料铁相组成,在生产配料时,引入3-15%的电炉磷矿渣或电炉磷矿渣与铜矿渣后,有利于改善生料的易烧性,且由于P2O5、F-,Ca离子的矿化作用,不仅使液相提前出现,且显著降低了液相粘度,FeO的配位数、四面体减少而八面体增多,以增加Al2O3在铁相中的固溶量,从而使熟料中的铁相不再象一般水泥熟料中的铁相为C4AF,而是形成了铁铝酸四钙和铁二铝酸六钙的固溶体(C4AF-C6A2F),且两者的摩尔比为1∶1,该固溶体的化学式为C5A1.5F,已被实验和实践所证明,试验表明无论是回转窑和机立窑,当生料中掺入3-15%电炉磷渣或电炉磷矿渣加铜矿渣后,正常煅烧的硅酸盐水泥熟料,其铁相都为C4AF-C6A2F固溶体,从而在不改变其它生产工艺的条件下,可以生产C4AF>16.0%、C3A<5.0%的干缩率小,耐磨性高的硅酸盐水泥熟料,用该水泥熟料磨制的水泥,其干缩率<0.01%,磨损率<3.6%kg/m2,可用于各种道路路面混凝土。对水泥熟料进行水杨酸-甲醇溶液和醋酸液等萃取后残渣(铁相)经化学分析结果,其CaO∶Al2O3∶Fe2O3的摩尔比,基本上为5∶1.5∶1。对熟料样品和残渣进行X-衍射分析以及穆斯堡尔谱试验结果都证明C6A2F的存在正是Fe2O3配位数的四面体减少和八面体增加的结果。本发明采用常规设备就能生产出能用于道路路面的普通硅酸盐水泥,从而解决了专门生产道路水泥较困难的问题,经本发明所生产的水泥具有抗硫酸盐、耐磨性好、干缩率低的特点,是一种较适用的产品。以下对本发明作详细描述。本发明是以常规原料石灰石、粘土为主料,校正原料为砂岩、铁粉、煤为燃料,在生料配制中引入具有矿化离子的电炉磷矿渣或电炉磷矿渣与铜矿渣,其掺入范围在3-15%,若为电炉磷渣与铜矿渣混合配比时,其电炉磷渣与铜矿渣的比为1-2∶1,以增加氧化铝在铁相中的固溶量,从而形成铁铝酸四钙和铁二铝酸六钙固溶体,由于铁相C4AF-C6A2F固溶体的摩尔比为1∶1,因此铁相的表达式可写为铁相C5A1.5F%=3.72F,铝酸盐相C3A%=2.65(A-0.96F),控制铁相后,并采用常规的机械化立窑生产或回转窑生产水泥方法即可生产出用于道路路面的普通硅酸盐水泥。为控制水泥熟料中铁相>16.0%,铝酸盐相<5.0%,硅酸盐水泥熟料成份中的氧化铁Fe2O3应大于4.30%、氧化铝Al2O3应小于6.0%、所制得的普通硅酸盐水泥的耐磨性可达到小于3.60Kg/m2,干缩率小于0.10%。所述的电炉磷矿渣主要化学成份为SiO2和CaO,并含有少量Al2O3、Fe2O3、MgO、P2O5和F-,主要矿物组成为假硅灰石和枪晶石,玻璃体含量为80%以上。所述的的铜矿渣,其主要化学成份为FeO、Fe2O3、CaO、MgO、Al2O3,其矿物组成主要是铁橄榄石和辉石等。实施例1采用回转窑生产道路硅酸盐水泥工业生产试验(1)共作两次工业性试验,工业试验用原材料为石灰石、砂岩、磷矿渣、铜矿渣,其燃料采用烟煤,原燃材料的化学成份和煤灰成份见表1,烟煤的挥发份应大于22%,灰份<28%,发热值在20090KJ/Kg(5000KCal/Kg)以上,原燃材料经破碎或干燥后,按确定的配比计量,送入生料磨,并采用φ2.4×12m棒球磨机研磨,平均细度为0.08mm方孔筛筛余15.00-17.00%,料浆水分为31.00-34.00%;并把配料方案的铁率(P)控制在<0.08%,石灰饱和率(KH)控制在0.94±0.02,硅酸率(n)分别控制在1.9±0.1和1.7±0.1,其配料方案和实际原料配比详见表2、3。生料的化学成份及制备时的技术经济指标及其与同期的比较详见表4。将生料成球后送入回转窑煅烧,采用φ3.5×145M湿法回转窑煅烧,煅烧温度控制在1350-1450℃,熟料化学成份及矿物成份详见表5、6。熟料的一般物理力学性能及耐磨性详见表7,熟料中的C3A<5.0%,C4AF>16.0%,耐磨性<3.6kg/m2,28d干缩率<0.10%。所烧制的水泥熟料送检后的化学组成见表8,熟料的铁相测定是采用水杨酸和甲醇溶液萃取后获得以熔剂矿物为主的残余物,再对残余物进行醋酸水溶液萃取,获得以铁相为主的残余物的化学组成见表9,计算水泥熟料的矿物组成见表10。将道路硅酸水泥熟料与适量石膏和5-10%的粒化高炉矿渣在φ3×9m大型球磨机内共同粉磨,其磨制的道路硅酸盐水泥的比表面积应在300m2Kg以上,以0.08mm方孔筛筛余表示时,细度应<5.0%,磨制的水泥检测结果详见表11。取在昆明水泥厂生产的样品送国家水泥质量监督检验测试中心检测结果见表12。两次工业性试验共生产道路硅酸盐水泥熟料9064吨,磨制道路硅酸盐水泥5546吨,从表1-12中的数据表明,采用本发明方法制得的普通硅酸盐水泥,各项技术指标均达到道路硅酸盐水泥国家标准13693-92的技术要求,其干缩率为0.07%,磨耗率为1.80-1.89kg/m2,完全可作为道路路面使用。结论回转窑水泥企业在原有工艺装备和原料基础上,改变配料方案,增加Fe2O3含量,使水泥熟料中f.CaO<1.0%,C3A<5.0%,C4AF>16.0%,是可以煅烧出道路硅酸盐水泥熟料的。实施例2立窑生产道路用普通硅酸盐水泥工业性试验原料采用石灰石、粘土、铁粉和磷渣,燃料采用无烟煤(原料及煤灰成份见表13)。其生产控制石灰石CaO含量应大于53.00%,MgO含量小于1.0%;粘土硅酸率(n)大于1.80小于3.00;磷矿渣玻璃体含量大于85%,P2O5含量小于3.0%;校铁原料(铁粉)Fe2O3含量大于50.0%;燃料(无烟煤)挥发份小于10.0%,灰份小于25%,热值在24244kj/kg(5800kcal/kg)以上,原燃材料经破碎或干燥后,按确定的配比计量,送入生料磨,采用规格为φ1.5×5.7m的生料磨破碎,出磨生料细度控制在0.08mm方孔筛筛余8-10%,TCaCo3±0.5%,将制备的生料经盘式成球机成球,其料球的成球水份控制在±1.0%,料球粒径φ5-10mm,然后将料球送入机械化立窑内煅烧,煅烧水泥熟料用机械化立窑规格为φ1.7×6.5m,煅烧温度控制在1350-1450℃,并控制熟料石灰饱和率(KH)0.98±0.02;硅酸率(n)1.70±0.1;铝氧率(P)0.85±0.1;C3A小于4.0%;C4AF大于17.0%,将烧好的熟料破碎,送入熟料园库内储存,再掺入3±1%的石膏和6-10%的活性混合材料,共同粉磨至0.08mm筛余4-6%。其水泥熟料的化学成分见表14,水泥熟料的物理力学性能见表15,送检水泥熟料的化学成分及水泥性能见表16、17、18。结论(1)机立窑水泥企业在不改变原燃材料的基础上,采用高饱石灰饱和比率、高铁配料方案,使熟料饱和率控制在0.96-1.00,铁率<0.9,熟料中Fe2O3控制在5.5-6.0%,以磷渣做矿化剂,采用浅暗火煅烧法,注意风、煤、料的合理配合,可以生产出道路硅酸盐水泥熟料。在磨制水泥时适量加入石膏和6-10%的矿渣或磷渣,可以生产425号道路硅酸盐水泥。(2)这种立窑企业生产的道路硅酸盐水泥,除熟料中f.CaO超过GB13693-92规定指标,各项技术要求均符合GB-13693-92标准。水泥的干缩率<0.01%,磨损率<3.6%kg/m2。送中国水泥质量检验中心检验的水泥物理性能见表19、20。安定性良好的立窑企业生产的425号道路硅酸盐水泥,经施工应用表明,能够达到路面混凝土的工艺设计要求。(4)机立窑企业生产道路水泥时,烧成煤耗较生产普通硅酸盐水泥熟料还略有降低,机立窑产量略有提高对生料磨和水泥磨生产能力,基本上没有影响。但水泥中混合材掺量约降低5%,增减因素相抵后,生产成本较生产普通硅酸盐时,仍可以做到基本相当。原燃材料的化学成分(%)表1配料方案的确定表2原料配比(%)表3生料化学成份及生料磨技术经济指标表4<熟料的化学成份和矿物成份表5(1熟料的化学成份和矿物成份表6(2)</tables>熟料一般物理力学性能及耐磨性、干缩性表7熟料的化学组成(%)表8热料萃取残余物化学组成(%)表9熟料矿物组成表10出厂(道路硅酸盐)水泥质量表11送检水泥的物理力学性能表12原燃料的化学成分(%)表13道路硅酸盐水泥熟料的成份表14</tables>道路硅酸盐水泥熟料物理力学性能表1权利要求1.一种道路路面用普通硅酸盐水泥及生产方法,它是以石灰石、粘土、砂岩、铁粉为原料,煤为燃料,其特征在于在生料配制中引入具有矿化离子的电炉磷矿渣或电炉磷矿渣与铜矿渣,其掺入量范围在3-15%,生料配制中引入具有矿化离子的电炉磷渣或电炉磷渣与铜矿渣后,改善了生料的易烧性,使液相提前出现,增加了Al2O3在铁相中的固溶量,从而形成铁铝酸四钙和铁二铝酸六钙固溶体即C4AF-C6A2F,由于铁相C4AF-C6A2F固溶体的摩尔比为1∶1,因此铁相的表达式可写为铁相C5A1.5F%=3.72F,铝酸盐相C3A%=2.65(A-0.96F),控制铁相后,采用常规机械化立窑或回转窑生产水泥即可生产出道路路面用普通硅酸盐水泥。2.按权利要求1所述的一种道路路面用普通硅酸盐水泥及生产方法,其特征在于为控制水泥熟料中铁相>16.0%,铝酸盐相<5.0%,硅酸盐水泥熟料成份中的氧化铁Fe2O3应大于4.30%、氧化铝Al2O3应小于6.0%、所制得的普通硅酸盐水泥的耐磨性可达到小于3.60Kg/m2,干缩率小于0.10%。3.按权利要求1所述的一种道路路面用普通硅酸盐水泥及生产方法,其特征在于所述的电炉磷矿渣主要化学成份为SiO2和CaO,并含有少量Al2O3、Fe2O3、MgO、P2O5和F-,主要矿物组成为假硅灰石和枪晶石,玻璃体含量为80%以上。4.按权利要求1所述的一种道路路面用普通硅酸盐水泥及生产方法,其特征在于所述的铜矿渣,其主要化学成份为FeO、Fe2O3、CaO、MgO、Al2O3,其矿物组成主要是铁橄榄石和辉石等。5.按权利要求1所述的一种道路路面用普通硅酸盐水泥及生产方法,其特征在于所述的电炉磷渣与铜矿渣混合配制时,其电炉磷渣与铜矿渣的比为1-2∶1。全文摘要本发明涉及一种可适用于各种道路路面混凝土的普通硅酸盐水泥。它以常规原料为主料,其特征在于在生料配制中引入具有矿化离子的电炉磷矿渣或电炉磷矿渣与铜矿渣,其掺入量范围在3—15%,以增加氧化铝在铁相中的固溶量,从而形成铁铝酸四钙和铁二铝酸六钙固溶体(C文档编号C04B7/42GK1205311SQ97112689公开日1999年1月20日申请日期1997年7月16日优先权日1997年7月16日发明者张仁寿,张晓玲,曾微,刘振弟,朝良申请人:云南省建筑材料科学研究设计院
查看更多专利详情
下载专利文献
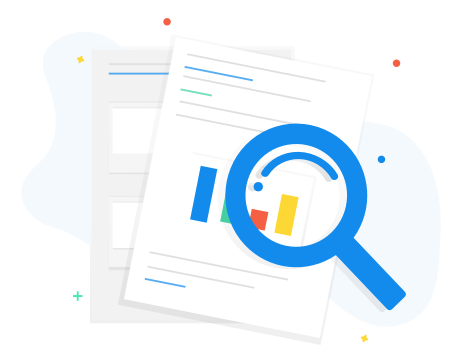
下载专利
同类推荐
-
张声军M·J·德内卡, S·戈麦斯M·J·德内卡, S·戈麦斯王善祝, 王明刘杰, 吕春叶强
您可能感兴趣的专利
-
叶强张雷张雷徐鑫, 刘小康徐鑫, 刘小康
专利相关信息
-
徐鑫, 刘小康徐鑫, 刘小康C·卡斯, C 卡斯C·卡斯, C 卡斯C·卡斯, C 卡斯C·卡斯, C 卡斯C·卡斯, C 卡斯