专利名称:浆料密度控制系统的制作方法HOP--------粉料仓,SCR--------螺旋输送器,ROT--------旋转阀,SLU--------浆料罐,SOL--------溶剂,G----------输送泵,LVL--------液位计,DEN--------密度计,Control System---控制系统。控制说明当浆料罐液位偏高时,减少溶剂量,同时相应降低螺旋-旋转阀系统的转速,避免在溶剂量减少时粉料过多造成的密度偏高;当浆料罐液位偏低时,增加溶剂量,同时相应提高螺旋-旋转阀系统转速,避免在溶剂量增加时粉料过少造成的密度偏低。当液位处于正常波动时,因为粉料下料不匀等造成密度波动,通过密度计测量的数据对螺旋-旋转阀系统的转速做相应的调整,达到校正密度的目的。(2)称重罐的方式见附图-HOP--------粉料仓,VAL--------下料阀,WPOT-------称重罐,ROT--------旋转阀,SLU--------浆料罐,SOL--------溶剂,G----------输送泵,WEI--------称重元件,LVL--------液位计,DEN--------密度计,Control System---控制系统。控制说明首先,通过称量元件,按照预先设定的重量,控制下料阀,当称量重量=设定的重量时,关闭下料阀;打开溶剂控制阀,根据溶剂量控制下料量(下料量的速率由旋转阀的转速控制),密度计的测量数据对溶剂和下料量的比率进行校正。上述两种控制系统都存在维护复杂、投资成本高的缺陷。鉴于上述存在的问题,本发明的目的在于提出一种维护方便、投资成本低的浆料密度控制系统。
本浆料密度控制系统见附图-4。
HOP--------粉料仓,VAL--------下料阀,SLU--------浆料罐,SOL--------溶剂,G----------输送泵,LVL--------液位计,DEN--------密度计,Special Control Program---控制系统。
本发明的目的是通过以下措施来实现的该浆料密度控制系统按以下措施进行当系统处于运行状态时,该系统按正常下料时间段、脉冲松动时间段和脉冲快速下料时间段构成一个控制循环在每个控制循环中,在正常下料时间段内,使下料阀处于正常下料阀位;在脉冲松动时间段内,使下料阀处于脉冲松动阀位;在脉冲快速下料时间段内,使下料阀处于脉冲快速下料阀位;在每个控制循环中当密度测量值大于密度设定值与密度增变上下限增量设定值之和,并且密度测量值小于密度设定值与密度联锁上限增量设定值之和,且密度平均值处于上升阶段时,正常下料阀位=上一循环正常下料阀位-密度偏差阀位-液位循环偏差阀位-增变阀位;当密度测量值小于密度设定值与密度增变上下限增量设定值之差,并且密度平均值处于下降阶段时,正常下料阀位=上一循环正常下料阀位-密度偏差阀位-液位循环偏差阀位+增变阀位;
当密度测量值大于密度设定值,并且密度测量值小于密度设定值与密度增变上下限增量设定值之和,且密度平均值处于上升阶段,或者,密度测量值小于密度设定值,并且密度测量值大于密度设定值与密度增变上下限增量设定值之差,且密度平均值处于下降阶段时,正常下料阀位=上一循环正常下料阀位-密度偏差阀位-液位循环偏差阀位;当密度测量值大于密度设定值,并且密度测量值小于密度设定值与密度联锁上限增量设定值之和,且密度平均值处于下降阶段,或者,密度测量值小于密度设定值,并且密度平均值处于上升阶段时,正常下料阀位=上一循环正常下料阀位-液位循环偏差阀位;当液位速率大于液位速率联锁设定值或者密度速率大于密度速率联锁设定值或者密度测量值大于密度设定值与密度联锁上限增量设定值之和时,关闭下料阀,即进行联锁控制;当液位速率小于液位速率恢复设定值并且密度速率小于密度速率恢复设定值并且密度测量值小于密度设定值与密度联锁上限增量设定值之和时,解除联锁,并且使下料阀在联锁后补充加料时间段保持联锁后补充加料阀位,然后下料阀从安全阀位继续运行;其中,在脉冲快速下料时间段或脉冲下料后联锁延迟时间段或联锁后补充加料时间段内,液位速率联锁不起作用,即进行液位速率联锁屏蔽;其中,密度偏差阀位等于本循环周期内的密度平均值与密度设定值之差乘以阀位密度偏差校正系数;液位循环偏差校正阀位等于本次循环的液位平均值与上一次循环的液位平均值之差乘以阀位液位循环偏差校正系数;液位速率为单位时间内液位测量值的变化值;密度速率为单位时间内密度测量值的变化值;其中,系统中浆料罐的溶剂进料量为恒定设定值,浆料罐的出料量为恒定设定值。
上述的正常下料阀位为10至90%的阀位开度。
上述的脉冲松动阀位为0至10%的阀位开度。
上述的脉冲快速下料阀位为90至100%的阀位开度。
上述的联锁后补充加料阀位为10至100%的阀位开度。
上述的正常下料时间段为1至20000秒。
上述的脉冲松动时间段为1至2000秒。
上述的脉冲快速下料时间为1至500秒。
上述的联锁后补充加料时间段为1至500秒。
上述的脉冲下料后联锁延迟时间段为1至300秒。
本发明的名称说明如下NN1正常下料阀位(调节变动),每次循环后按照计算结果给定,一般为10至90%的阀位开度,NN2脉冲快速下料阀位,在脉冲快速下料时间段内下料阀的阀位,一般为90至100%,阀门处于很大的开度,NN3正常下料时间段,一般为1至20000秒,根据浆料罐容积、溶剂进料量、浆料罐出料量等实际工况来确定;NN4脉冲快速下料时间段,一般为1至500秒,根据浆料罐容积、溶剂进料量、浆料罐出料量等实际工况来确定;NN5安全阀位,联锁解除后下料阀的恢复阀位,根据浆料罐容积、溶剂进料量、浆料罐出料量等实际工况来确定;NN6脉冲松动阀位,在脉冲时间段内下料阀的阀位,一般为0至10%,阀门处于很小的开度;NN7脉冲松动时间段,一般为1至2000秒,根据浆料罐容积、溶剂进料量、浆料罐出料量等实际工况来确定;NN9阀位液位循环偏差校正系数,将液位循环偏差转化为校正阀位的系数,根据浆料罐容积、溶剂进料量、浆料罐出料量等实际工况来确定;NN10阀位密度偏差校正系数,将密度偏差转化为校正阀位的系数,根据浆料罐容积、溶剂进料量、浆料罐出料量等实际工况来确定;NN11循环时间,每个循环时间包括正常下料时间段、脉冲松动时间段和脉冲快速下料时间段;NN12密度增变上下限增量设定值,根据浆料罐容积、溶剂进料量、浆料罐出料量等实际工况来确定;NN13密度联锁上限增量设定值,根据浆料罐容积、溶剂进料量、浆料罐出料量等实际工况来确定;NN14增变阀位,根据浆料罐容积、溶剂进料量、浆料罐出料量等实际工况来确定;
NN15液位速率联锁设定值,根据浆料罐容积、溶剂进料量、浆料罐出料量等实际工况来确定;NN16密度速率联锁设定值,根据浆料罐容积、溶剂进料量、浆料罐出料量等实际工况来确定;NN17液位速率恢复设定值,根据浆料罐容积、溶剂进料量、浆料罐出料量等实际工况来确定;NN18密度速率恢复设定值,根据浆料罐容积、溶剂进料量、浆料罐出料量等实际工况来确定;NN19脉冲下料后联锁延迟时间段,脉冲下料后,液位速率瞬间上升幅度很大,按照联锁设计,将发生液位速率联锁,干扰正常的调节,在脉冲快速下料时间段后,延长一段时间,在该时间段内,液位速率联锁不起作用,在脉冲下料后联锁延迟时间段运行结束后,液位联锁起作用。一般为1至300秒,根据浆料罐容积、溶剂进料量、浆料罐出料量等实际工况来确定;NN21联锁后补充加料阀位,在联锁后补充加料时间段内下料阀的阀位,一般为10至90%,根据浆料罐容积、溶剂进料量、浆料罐出料量等实际工况来确定;NN22联锁后补充加料时间段,一般为1至500秒,根据浆料罐容积、溶剂进料量、浆料罐出料量等实际工况来确定;NN34密度偏差阀位,等于本循环周期内的密度平均值与密度设定值之差乘以阀位密度差校正系数;NN36液位速率,单位时间内液位测量值的变化值;NN37密度速率,单位时间内密度测量值的变化值;NN45液位循环偏差校正阀位,等于本次循环的液位平均值与上一次循环的液位平均值之差乘以阀位液位循环偏差校正系数。
本发明的技术特点1、采用脉冲设计,克服固体粉料下料不畅的问题;2、引入分区控制和增变调节的概念,克服滞后,提高精度;3、引入密度速率、液位速率联锁及密度测量值超标联锁的安全模块设计,具有安全联锁的能力;4、使用成本低,适用于不易计量物料量的物料密度调制。
本发明按照安全优先的原则进行如下优先设计(1)优先Ⅰ级当液位速率大于液位速率联锁设定值或者密度速率大于密度速率联锁设定值或者密度测量值大于密度设定值与密度联锁上限增量设定值之和时,关闭下料阀,即进行联锁控制;当液位速率小于液位速率恢复设定值并且密度速率小于密度速率恢复设定值并且密度测量值小于密度设定值与密度联锁上限增量设定值之和时,解除联锁,并且使下料阀在联锁后补充加料时间段保持联锁后补充加料阀位,然后下料阀从安全阀位继续运行。
(2)优先Ⅱ级当Ⅰ级不成立,当本次循环结束时,若密度测量值>密度设定值并且密度平均值处于下降阶段,仅进行液位偏差校正;若密度测量值<密度设定值并且密度平均值处于上升阶段,仅进行液位偏差校正。
(3)优先Ⅲ级当Ⅰ和Ⅱ级均不成立时,若密度测量值与密度设定值之差的绝对值>密度增变上下限增量,进行增变阀位调节。
(4)优先Ⅳ级当Ⅰ和Ⅱ和Ⅲ均不成立时,进行密度偏差调节。
(5)液位循环偏差调节除联锁状态外一直参与的调节。
本发明的设计手段第一手段程序运行时,下料阀以正常下料阀位保持正常下料时间段,然后进入脉冲状态,下料阀以脉冲松动阀位保持脉冲松动时间段,然后,下料阀以脉冲快速下料阀位保持脉冲快速下料时间段,随后进行下一次循环。每个循环如附图-5所示
DENOUT-------下料阀的开度,T-------时间,NN1-------正常下料阀位,NN2-------脉冲快速下料阀位,NN3-------正常下料时间段,NN4-------脉冲快速下料时间段,NN6-------脉冲松动阀位,NN7-------脉冲松动时间段。
脉冲阶段分为两段的目的当下料阀以正常下料阀位保持正常下料时间段以后,由于物料的流动性较差,下料量逐渐减少,直至严重时不下料,这一点和液体或气体介质完全不同,液体或气体介质,只要压差和流通阀位恒定,流量就是恒定的,因此,对于液体或气体的流量控制比较容易,对于粉料,要做到下料量相对偏差较小,就必须采用脉冲的方式来疏通下料线,达到下料量偏差相对较小的目的。一般,粉料下料线上都有松动气线,下料阀以脉冲松动阀位保持脉冲松动时间段时,管线内的松动气使管线内的压力升高,对下料阀以上的粉料起到松动作用,随后,下料阀以脉冲快速下料阀位保持脉冲快速下料时间段,这样,带压的粉料大量快速的进入浆料罐,达到了疏通下料管线的目的,提高了每一循环的再现性,使下料状态尽可能相似,这样,减少了每一循环下料量的偏差。
第二手段在第一手段实施的基础上,需要增加自校正能力,提高调节精度。第一手段实施完成后,调节很机械,对于粉料仓料位、松动状态变化造成的下料变化无自适应调节能力,一段时间后仍需要手动调节正常下料阀位、正常下料时间段、脉冲松动阀位、脉冲松动时间段、脉冲快速下料阀位、脉冲快速下料时间段来平衡密度调节。
设计思路因为密度调节的理想状态应当是波动频率低、波幅小,这就要求密度控制系统具有自修正参数的能力,为此,进行如下计算变动在一个循环周期密度平均值与与密度设定值(根据采用的仪表和量程以及装置要求的对应密度而定)比较,计算出密度平均值与密度设定值的偏差,这个密度偏差再乘以阀位密度偏差校正系数,转化为偏差阀位,作为校正阀位的依据,每一循环后校正正常下料阀位,作为下一轮循环的基础设定值,这样,在下一次的循环时执行新的正常下料阀位。算式如下密度偏差阀位=(本循环周期内的密度平均值-密度设定值)*阀位密度偏差校正系数正常下料阀位=上一循环周期正常下料阀位-密度偏差阀位因此,当平均密度偏高时,减小下料阀位,达到降低平均密度的目的;当平均密度偏低时,增大了下料阀位,达到提高平均密度的目的。
第三手段因为工艺过程的原因,密度测量调节通道长,滞后性很大,采用计算机模拟控制,由于得不到下料量的数据,必须与下料关系最直接的检测量相关联,通过过程分析,配料罐的液位符合条件。当配料罐进溶剂量及配料罐出料量均恒定时,液位的变化与下料量成正比关系,可以在控制系统中引入这一变化。但存在的问题是浆料罐的出料量因下一工序的温度、压力的波动而波动变化,导致配料罐的液位始终处于变化状态,如果采用常规的测量值与设定值的偏差来进行调节的控制是行不通的,为了解决这一问题采用第n次循环的液位平均值与第n-1次循环的液位平均值的偏差,对正常下料阀位进行修正,即液位测量值累加值在一个循环时间周期平均一次,平均值与与上一循环平均值比较,计算出第n次循环的液位平均值与第n-1次循环的液位平均值的偏差,这个液位循环偏差再乘以阀位液位循环偏差校正系数,转化为偏差阀位,作为校正阀位的依据,每一循环后校正正常下料阀位,作为下一轮循环的基础设定值,这样,在下一次的循环时执行新的正常下料阀位。算式如下液位循环偏差阀位=[第n次循环的液位平均值-第n-1次循环的液位平均值]*阀位液位循环偏差校正系数在没有其它异常情况出现的条件下,当平均液位升高时,说明下料量偏多,应当提前减小下料阀位,避免因下料过多造成密度偏高;当平均液位下降时,说明下料量偏少,应当提前增大阀位,避免密度偏低。
这样,在第三手段实施后,减小了因密度滞后带来的震荡,提高了调节精度,因此,下一循环的正常下料阀位修正为正常下料阀位=上一循环正常下料阀位-密度偏差阀位-液位循环偏差阀位第四手段密度调节滞后性较大,当密度表现出升高或降低时,在浆料配制罐中,实际密度已发生振幅较大的变化,而在前三项手段实施后,必须等到一个循环周期运行结束后,正常下料阀位才进行变化,而在一个循环周期内,正常下料阀位是不变的,这样,密度已经表现出持续上升或持续下降的状态,如不及时采取调整措施,密度波动震荡将加大,为此,引入增变调节的概念当密度测量值>密度设定值+密度增变上下限增量设定值,并且,密度平均值处于上升阶段,在本次循环周期内,立刻在下料阀现有的正常下料阀位的基础上,减去增变阀位,减少下料量,达到超前调节的目的;当密度测量值<密度设定值-密度增变上下限增量设定值,并且,密度平均值处于下降阶段,在本次循环周期内,立刻在下料阀现有的正常下料阀位的基础上,加上增变阀位,增大下料量,达到超前调节的目的。在一个循环周期内,一般只进行一次增变调节。
第五手段特殊情况下防止超密度,固体粉料的流动性较差,远不如液体物料和气体物料,为此必须考虑超密度的紧急情况的出现。
浆料配制超密度的表征a.浆料罐的液位速率上升较快;b.密度速率上升较快,特别是浆料罐液位速率上升最为直接,也最敏感;c.密度测量值超标。
针对上述情况,采取以下设计随时计算密度速率、液位速率。
联锁条件液位速率>液位速率联锁设定值或密度速率>密度速率联锁设定值或密度测量值>密度设定值与密度联锁上限增量设定值之和时,下料阀关闭;联锁解除条件液位速率<液位速率恢复设定值并且密度速率(密度速率恢复设定值并且密度测量值<密度设定值与密度联锁上限增量设定值之和时,联锁解除;在联锁时间内,下料阀关闭,这样,浆料罐只进溶剂,不下料,当联锁解除时,浆料罐中的实际密度已经偏小,为克服滞后问题,所以,增加密度补充模块;联锁解除后,先补充下上一部分粉料,再进入安全阀位状态,即下料阀以联锁后补充加料阀位保持联锁后补充加料时间段,然后,下料阀从安全阀位继续运行;与此同时,补充下料时,屏蔽液位速率联锁。
脉冲快速下料时间段和联锁后补充加料时间段一般时间较短,但下料阀开度很大,下料冲击较大,液位速率变化很大,为防止脉冲阶段联锁,在脉冲快速下料时间段或脉冲下料后联锁延迟时间段或联锁后补充加料时间段内,液位速率联锁不起作用,进行液位速率联锁屏蔽。
下面结合实施例及附图对本发明作进一步描述如附图-7所示,某化纤厂对苯二甲酸(PTA)装置精制单元浆料罐的密度控制原设计为自动控制,但因为下料管线较细,且质量流量计无法投用,自95年9月PTA装置投产以来,浆料调制罐的密度控制一直是DCS主操手动控制,每小时手动操作20次左右,多次出现超密度的恶性事故,给装置造成重大损失,同时,密度波动频率高。浆料调制罐的密度控制一直是困扰该装置平稳运行的障碍。
附图-7说明FT2011-----------溶剂流量计,LT2004-----------浆料罐液位计,
DT2021---------密度计,FT2002---------粉料质量流量计,FRC2011--------溶剂流量调节器,LRCA2004-------浆料罐液位调节器,DRC2021--------密度调节器,FRC2002--------粉料流量调节器,FFX2011--------溶剂-粉料流量比例调节器,HS2002---------切换开关(作为密度调节器选择直接控制粉料下料阀或微调FFX2011的选择开关),FCV2002--------粉料下料蝶阀,FCV2011--------溶剂流量阀,F1-1206--------浆料罐。
利用本发明对上述化纤厂对苯二甲酸(PTA)装置精制单元浆料配制系统进行重新设计,满足了该装置的生产需要。
该化纤厂对苯二甲酸(PTA)装置精制单元浆料罐的原浆料配制部分的工艺布置与本发明的实施例(详见附图-4)的系统布置相同,仅在下料管线上有一质量流量计(但无法投用,仅作为下料通道使用)。
利用本发明设计出该化纤厂对苯二甲酸(PTA)装置精制单元浆料罐的浆料密度控制系统,其密度控制达到了以脉冲设计为基础,以分区控制、增变调节为手段,同时具有安全联锁的能力。
按照本发明,该化纤厂对苯二甲酸(PTA)装置精制单元浆料密度控制系统设计完成后,其浆料密度控制示意图(见附图-6)
DEN--------密度测量值,T----------时间,NN12--------密度增变上下限增量设定值,NN13--------密度联锁上限增量设定值。
第一阶段(ab段)密度偏离设定值较小,密度校正及液位校正起作用,正常下料阀位=上一循环正常下料阀位-密度偏差阀位-液位循环偏差阀位第二阶段(bc段)密度偏离较大,增变阀位起作用,迅速减小阀位,加大调节力度,正常下料阀位=上一循环正常下料阀位-密度偏差阀位-液位循环偏差阀位-增变阀位第三阶段(cd段)密度测量值超标联锁,防止超密度的恶性事故出现,下料阀关闭。
当联锁条件解除时,先补充加料,然后恢复至安全阀位,①下料阀以联锁后补充加料阀位,保持联锁后补充加料时间段;②然后,下料阀的阀位=安全阀位正常下料阀位=安全阀位正常下料阀位从安全阀位开始进行校正。
第四阶段(def段)密度已开始回落,按照常规调节,下料阀的阀位应逐渐减小,但密度已开始回落,说明阀位可能已经偏小,再减小下料阀位是不合乎逻辑的,因此应保持现有阀位,让密度缓慢下降,所以在设计上,在这阶段,密度校正及增变阀位不起作用。但不能排除因下料性质变化引起的在下料阀的阀位不变的情况下,下料增多或减少的可能,这种下料性质的变化必然再次引起较大的震荡。因此,在这一阶段,液位循环偏差校正起作用。
正常下料阀位=上一循环正常下料阀位-液位循环偏差阀位第五阶段(fg段)同第一阶段,正常下料阀位=上一循环正常下料阀位-密度偏差阀位-液位循环偏差阀位第六阶段(gh段)增变阀位起作用,迅速增大阀位,减小密度偏差,正常下料阀位=上一循环正常下料阀位-密度偏差阀位-液位循环偏差阀位+增变阀位第七阶段(hij段)类同第四阶段,正常下料阀位=上一循环正常下料阀位-液位循环偏差阀位全过程任何时候,液位速率>液位速率联锁设定值或密度速率>密度速率联锁设定值或密度测量值>联锁密度绝对值,安全模式立刻启动;任何时候,安全恢复时,首先进行密度补充调节。在本实施例中,在下述工况条件下装置负荷8至12吨/小时产品,密度设定值960至995千克/立方米,浆料罐溶剂进料量25至35吨/小时,浆料罐出料量35至45吨/小时,浆料罐容积15立方米;根据上述工况条件,确定的参数范围如下NN1正常下料阀位(调节变动),为15至50%的阀位开度,NN2脉冲快速下料阀位,为95至100%的阀门开度;NN3正常下料时间段,为150至300秒;NN4脉冲快速下料时间段,为10至20秒;NN5安全阀位,为25至40%的阀位开度;NN6脉冲松动阀位,为0至5%的阀位开度;NN7脉冲松动时间段,为10至20秒;NN9阀位液位循环偏差校正系数,为0.30至0.40;NN10阀位密度差校正系数,为0.055至0.070;NN11循环时间,为170至340秒;NN12密度增变上下限增量设定值,为1.5至2.5千克/立方米;NN13密度联锁上限增量设定值,为3.5至4.5千克/立方米;NN14增变阀位,为0.2至0.5%;NN15液位速率联锁设定值,为0.55至0.72%/秒;NN16密度速率联锁设定值,为0.035至0.042千克/立方米.秒;NN17液位速率恢复设定值,为0.030至0.060%/秒;NN18密度速率恢复设定值,为0.00至0.01千克/立方米秒;NN19脉冲下料后联锁延迟时间段,为10至20秒;NN21联锁后补充加料阀位,为95至100%的阀门开度;NN22联锁后补充加料时间段,为10至20秒。
本发明对于硬件环境的要求1、工业控制用集散控制系统(DCS)或工业计算机;2、液位测量信号、密度测量信号均需要引入计算机;3、下料阀最好采用蝶阀或类似的直通阀。
实施例的运行效果见附表-1附表说明DRC2021.SP-------密度设定值(按照装置仪表量程和生产负荷确定),考核下限--------考核时间内,预定的下限值,考核上限--------考核时间内,预定的上限值,最小值----------考核时间内,实际达到的瞬间最小值,最大值----------考核时间内,实际达到的瞬间最大值,合格率-----------密度瞬间值在考核上限和下限之内的比率;从上表数据可以看出,该化纤厂对苯二甲酸(PTA)装置精制单元浆料密度控制系统既不使用旋转阀,又不使用质量流量计,同时具有安全联锁的能力,改变了该化纤厂对苯二甲酸(PTA)装置精制单元浆料密度控制被迫手动操作的状况,实现了程序化控制,避免了超密度的恶性事故再次发生,同时降低了物料密度的波动频率,完全满足了该装置的生产需要,运行至今,未发生过超密度的事故。
综上所述,本发明投资成本较小,维护也非常方便。本系统的特点是不计量具体的物料量,采用脉冲下料、增变调节、分区控制以及全新的安全控制模块相结合的全新控制系统,达到控制浆料密度的目的,特别适用于不易计量物料量的浆料密度的控制。附表-1测试结果统计表
一种浆料密度控制系统,其按以下措施进行:当系统处于运行状态时,接正常下料时间段、脉冲松动时间段和脉冲快速下料时间段构成一个控制循环;使下料阀在正常下料时间段内处于正常下料阀位、在脉冲松动时间段内处于脉冲松动阀位、在脉冲快速下料时间段内处于脉冲快速下料阀位。本发明投资成本较小,维护也非常方便。本发明采用脉冲下料、增变调节、分区控制以及全新的安全控制模块相结合的全新控制系统,达到控制浆料密度的效果,特别适用于不易计量物料量的浆料密度的控制。
浆料密度控制系统制作方法
- 专利详情
- 全文pdf
- 权力要求
- 说明书
- 法律状态
查看更多专利详情
下载专利文献
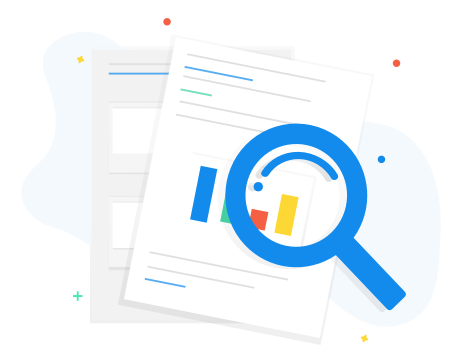
下载专利
同类推荐
-
刘洪杰刘洪杰卢红蓉卢红蓉林景栋
您可能感兴趣的专利
-
M.卡普蒂刘启生尹同远林春强黄清锋刘洪杰
专利相关信息
-
叶佐辉陈寿田丁基哲P.M.杜克, S.S.哈伦P.M.杜克, S.S.哈伦