专利名称:结晶取向陶瓷及其制造方法 压电材料是具有压电效果的材料,其形态分为单晶、陶瓷、薄膜、高分子及复合材料(composite)。在这些压电材料中,特别是压电陶瓷由于其具有高性能,形状的自由度大,材料设计比较容易,因此在电子学或机电一体化领域已广泛应用。压电陶瓷是对强介电体陶瓷外加电场,使强介电体的分域方向全部为一定方向,即实施了所谓极化处理的陶瓷。在压电陶瓷中,为了通过极化处理使自发极化全部为一定方向,自发极化的方向可在三维空间取的各向同性钙钛矿型的结晶结构是有利的。因此,已实用化的压电陶瓷的大部分为各向同性钙钛矿型强介电体陶瓷。作为各向同性钙钛矿型强介电体陶瓷,已知的包括例如,Pb(Zr-Ti)O3(以下,将其称为“PZT”)、相对于PZT添加了铅系复合钙钛矿作为第三成分的PZT3成分系、BaTiO3、Bi0.5Na0.5TiO3(以下,将其称为“BNT”)等。其中,以PZT为代表的铅系压电陶瓷比其他压电陶瓷具有更高的压电特性,因此占据了现已实用化的压电陶瓷的大部分。但是,由于含有蒸气压高的氧化铅(PbO),因此存在对环境压力大的问题。因此,需要低铅或者无铅、且与PZT具有同等压电特性的压电陶瓷。另一方面,BaTiO3陶瓷在不含铅的压电材料中具有较高的压电特性,因此已用于声纳等。此外,已知在BaTiO3和其他非铅系钙钛矿化合物(例如,BNT等)的固溶体中,也显示出较高的压电特性。但是,这些无铅压电陶瓷与PZT相比,具有压电特性低的问题。因此,为了解决该问题,到目前为止提出了各种提案。例如,特开平11-180769号公报公开了具有(1-x)BNT-BaTiO3(其中,x=0.06~0.12)的基本组成,且含有0.5~1.5重量%稀土类元素的氧化物(例如,La2O3、Y2O3、Yb2O3等)的压电陶瓷材料。此外,特开2000-272962号公报公开了以通式{Bi0.5(Na1-xKx)0.5}TiO3(其中,0.2<x≤0.3)所示的压电瓷器组合物,及使其含有2重量%以下添加物(例如,Fe2O3、Cr2O3、MnO2、NiO、Nb2O5等)的压电瓷器组合物。此外,特开2000-281443号公报公开了以通式xNaNbO3-yBaNb2O6-zBiNb3O9(其中,x+y+z=1,(x,y,z)位于三成分组成图上的所定范围内)所示的钨酸碱金属盐型复合氧化物为主成分,且在全重量中以金属换算计含有3~6重量%比例的Bi的压电瓷器组合物。
此外,本申请的申请人在特开2000-313664号公报中公开了在以通式K1-xNaxNbO3(其中,x=0~0.8)所示的固溶体中添加了含有从Cu、Li、Ta中选取的1种或2种以上元素的化合物的碱金属含有铌酸物系压电瓷器组合物。
此外,特开2002-137966号公报公开了以组成式(1-x)NaNbO3+xMnTiO3(其中,0.014≤x≤0.08)所示的压电瓷器,以及相对于该组成式所示化合物还含有0.5~10摩尔%的KNbO3或NaNbO3作为副成分的压电瓷器。
此外,特开2001-240471号公报公开了含有NaxNbO3(0.95≤x≤1)所示的主成分、组成式AyBOf(A为K、Na及Li内的至少1种和Bi,B为Li、Ti、Nb、Ta及Sb内的至少1种,0.2≤y≤1.5,f为任意)所示的副成分、以及用以氧化物换算计为0.01~3重量%原子序号21的Sc到原子序号30的Zn的第1过渡金属元素的至少1种的压电瓷器组合物,其中副成分的含有量为8摩尔%以下。
此外,特开2001-291908号公报公开了由作为层状钙钛矿型化合物的一种的Na0.5Bi4.5Ti4O15构成,c轴沿一方向取向,且沿与c轴取向方向正交的方向极化的压电体陶瓷。在同一文献中还记载在含有初始原料的胚片(green sheet)表面形成平行排列的线状电极,将胚片积层使电极沿积层方向相互重合,边在胚片的积层方向加压力边烧成,进而在片材面上通过在相对的电极间外加直流电场,从而得到在片材的面内方向上彼此沿反方向极化的压电体陶瓷。
此外,特开2001-039766号公报公开了由作为层状钙钛矿型化合物的一种的CaBi4Ti4O15构成,c轴沿一方向取向,沿与c轴取向方向正交的方向极化,而且在与c轴的取向方向及极化方向平行的面上形成部分电极的压电元件。在同一文献中还记载通过对原料粉末进行煅烧、粗粉碎及成型而得到圆柱状前处理试样,在600℃下对其进行热处理,边对热处理的前处理试样沿厚度方向进行单轴加压边烧成,按加压方向为宽度方向由烧成试样切出矩形试样,通过使矩形材料沿长度方向极化,得到沿与c轴的取向方向正交的方向极化的压电陶瓷。
此外,特开2002-193663号公报公开了由通式ABO3(其中,A为2价金属元素,B为4价金属元素)所示的结晶取向钙钛矿型化合物。在同一文献中还记载将含有Ba6Ti17O40板状粉末、BaTiO3粉末及BaCO3粉末的原料成型为片状,将其积层压合,进而在所定温度下对该积层体烧成,从而得到(111)面取向的钛酸钡烧结体。
此外,本申请的申请人在特开平11-60333号公报中公开了由含有菱面体晶为端相的钙钛矿型陶瓷(例如,相对于BNT使Bi0.5K0.5TiO3、BaTiO3、NaNbO3等固溶的钙钛矿型陶瓷)构成,且拟立方{100}面的Lotgering法测定的取向度为30%以上的压电陶瓷。此外,在同一文献中还公开了将具有板状形状且由层状钙钛矿型化合物构成的主材料A(Bi4Ti3O12)、具有各向同性钙钛矿型结构的副材料B或能够生成副材料B的原料Q(Bi0.5(Na0.85K0.15)0.5TiO3的等轴形状粉末)、用于将主材料A转换为各向同性钙钛矿型化合物的副材料C(Bi2O3粉末、Na2CO3粉末、K2CO3粉末及TiO2粉末)混合,将它们成型从而使主材料A取向,然后进行加热烧结的压电陶瓷的制造方法。
由BaTiO3、BNT、K1-yNayNbO3(0≤y≤1)等各向同性钙钛矿型化合物构成的非铅系强介电体的压电、焦电、介电、热电、电子导电、离子导电等特性(以下,将它们称为“压电特性等“)一般比PZT为代表的铅系强介电体差。另一方面,如专利文献1~6中记载的那样,已知如果相对于非铅系的强介电体添加各种添加剂,烧结性或压电特性等提高。
但是,如果用通常的陶瓷制造工艺,即使用含有成分元素的单纯化合物作为初始原料进行煅烧、成型及烧结的制造工艺来制造各向同性钙钛矿型化合物,得到的烧结体的各晶粒无规取向。因此,即使是实际上具有高压电特性等的组成,得到的烧结体的压电特性等也不足。
对此,已知各向同性钙钛矿型化合物的压电特性等一般是因结晶轴方向的不同而不同的。因此,如果使压电特性等高的结晶轴沿一定的方向取向,则可以最大限度地利用压电特性等的各向异性,可以期待压电陶瓷的高特性化。实际上,已知在由非铅系强介电体材料构成的单晶中存在显示出优异压电特性等的物质。
但是,单晶存在制造成本高的问题。此外,具有复杂组成的固溶体的单晶在制造时容易产生组成的变形,不适宜作为实用材料。此外,由于单晶的破坏韧性差,因此在高应力下使用困难,存在使用范围受到限制的问题。
此外,如上述特开2001-291908号公报及特开2001-039766号公报中记载的那样,如果烧结时进行单轴加压,则也有可能使特定的结晶面取向。但是,该方法只适用于如层状钙钛矿型化合物那样本质上各向异性大的结晶系及结晶面,存在对于如各向同性钙钛矿型化合物那样各向异性小的结晶系及结晶面不适用的问题。
另一方面,如上述特开2002-193663号公报及特开平11-60333号公报中记载的那样,使用具有所定组成的板状粉末作为反应性模板使特定的结晶面取向的方法,即使是各向异性小的结晶系及结晶面,也可以容易且价廉地制造特定的结晶面以高取向度取向的结晶取向陶瓷。
但是,如果是使用Ba6Ti17O40、Bi4Ti4O12等构成的板状粉末作为反应性模板的方法,制得的结晶取向陶瓷中肯定残留有板状粉末中所含有的A位置元素(Ba或Bi)及B位置元素(Ti)。因此,在将该方法适用于在非铅系中也显示出相对的高压电特性的各向同性钙钛矿型铌酸钾钠(K1-yNayNbO3)或其固溶体时,有时不能实现最希望的组成,由于不可避免地含有A位置元素及/或B位置元素,因此担心压电特性受到损害。
本发明要解决的课题在于提供以各向同性钙钛矿型铌酸钾钠为基本组成,且显示出优异压电特性等的结晶取向陶瓷及其制造方法。此外,本发明要解决的其他课题还在于提供以各向同性钙钛矿型铌酸钾钠为基本组成,且特定的结晶面以高取向度取向的结晶取向陶瓷及其制造方法。
为了解决上述课题,本发明的要旨在于本发明的结晶取向陶瓷由通式在ABO3中,A位置元素为K、Na及/或Li,B位置元素为Nb、Sb及/或Ta,{Lix(K1-yNay)1-x}{Nb1-z-wTazSbw}O3(1)(其中,x、y、z、w分别为0≤x≤0.2、0≤y≤1、0≤z≤0.4、0≤w≤0.2、x+z+w>0)所示各向同性钙钛矿型化合物的多晶体构成,且构成该多晶体的各晶粒的特定的结晶面取向。
在各向同性钙钛矿型铌酸钾钠中,如果将A位置元素的一部分用所定量的Li置换,及/或B位置元素的一部分用所定量的Ta及/或Sb置换,则与不含有它们的组成相比,压电特性提高。
此外,如果使特定的结晶面取向,与具有同一组成的无取向烧结体相比,压电d31常数、压电g31常数及机电耦合系数kp提高。
此外,本发明的要旨在于本发明的结晶取向陶瓷的制造方法包括将其生长面(发展面)与权利要求1记载的各向同性钙钛矿型化合物的特定结晶面具有晶格匹配性的第1各向异性形状粉末、与该第1各向异性形状粉末反应至少生成前述各向同性钙钛矿型化合物的第1反应原料混合的混合工序;成型在该混合工序中得到的混合物从而使前述第1各向异性形状粉末取向的成型工序;加热在该成型工序中制得的成型体,使前述第1各向异性形状粉末与前述第1反应原料反应的热处理工序。
使满足所定条件的第1各向异性形状粉末和具有所定组成的第1反应原料反应,便生成继承了第1各向异性形状粉末的取向方向的由权利要求1记载的各向同性钙钛矿型化合物构成的各向异性形状结晶。因此,如果使第1各向异性形状粉末在成型体中取向,将成型体加热到所定温度,便得到由权利要求1记载的各向同性钙钛矿型化合物构成,且以特定结晶面作为生长面的结晶粒沿特定方向取向的结晶取向陶瓷。
图1为实施例1中得到的结晶取向陶瓷的X射线衍射图形。
图2为实施例3中得到的结晶取向陶瓷的X射线衍射图形。
图3(a)及图3(b)分别为实施例8中得到的结晶取向陶瓷及比较例3中得到的无取向烧结体的X射线衍射图形。
图4表示实施例2中得到的结晶取向陶瓷及比较例1中得到的无取向烧结体的压电d31常数的温度依赖性。
图5表示实施例7中得到的结晶取向陶瓷及比较例3中得到的无取向烧结体的压电d31常数的温度依赖性。
图6表示实施例9中得到的结晶取向陶瓷及比较例6中得到的无取向烧结体的压电d31常数的温度依赖性。
图7表示室温下压电d31常数的组成依赖性。
图8表示实施例9中得到的结晶取向陶瓷及比较例6中得到的无取向烧结体的动态变形量D33large的温度依赖性。
图9表示实施例9中得到的结晶取向陶瓷及比较例6中得到的无取向烧结体的动态介电常数E33large的温度依赖性。
图10表示实施例9中得到的结晶取向陶瓷及比较例6中得到的无取向烧结体的D33large/(E33largge)1/2的温度依赖性。
图11表示实施例9中得到的结晶取向陶瓷及比较例6中得到的无取向烧结体的D33large/E33large的温度依赖性。
图12表示实施例22中得到的结晶取向陶瓷的动态变形量D33large的温度依赖性。
图13表示实施例23中得到的结晶取向陶瓷的动态变形量D33large的温度依赖性。
图14表示实施例23中得到的结晶取向陶瓷的室温基准位移比率的温度依赖性。
图15表示实施例23中得到的结晶取向陶瓷在不同注入能量下位移的温度依赖性。
图16表示实施例23中得到的结晶取向陶瓷在不同注入能量下电场的温度依赖性。
图17表示实施例23中得到的结晶取向陶瓷在不同注入电荷下位移的温度依赖性。
图18表示实施例23中得到的结晶取向陶瓷在不同注入电荷下电场的温度依赖性。
以下,对本发明的一实施方案进行详细地说明。本发明的结晶取向陶瓷的特征在于其由示于以下化1式的通式所示的各向同性钙钛矿型化合物的多晶体构成,且构成该多晶体的各晶粒的特定的结晶面取向。
{Lix(K1-yNay)1-x}{Nb1-z-wTazSbw}O3(1)(其中,0≤x≤0.2、0≤y≤1、0≤z≤0.4、0≤w≤0.2、x+z+w>0)本发明的结晶取向陶瓷以作为各向同性钙钛矿型化合物的一种的铌酸钾钠(K1-yNayNbO3)为基本组成,由A位置元素(K、Na)的一部分被所定量的Li置换(取代),及/或B位置元素(Nb)的一部分被所定量的Ta及/或Sb置换。在化1式中,“x+z+w>0”表示可以含有Li、Ta及Sb内的至少一个作为置换元素。
此外,在上述式(1)中,“y”表示结晶取向陶瓷中所含K和Na的比。本发明的结晶取向陶瓷可以含有K或Na的至少一方作为A位置元素。即,K和Na的比y并无特别限定,可以取0以上、1以下的任意值。为了获得高压电特性等,y的值优选0.05以上0.75以下,更优选0.20以上、0.70以下,进一步优选0.35以上、0.65以下,进一步优选0.40以上、0.60以下,最优选0.42以上、0.60以下。
“x”表示将作为A位置元素的K及/或Na置换的Li的置换量。如果用Li将K及/或Na的一部分置换,获得的效果是压电特性等提高、居里温度上升、及/或促进致密化。具体地,x值优选0以上、0.2以下。如果x值超过0.2,由于压电特性(压电d31常数、机电耦合系数kp、压电g31常数等)降低,因此不可取。x值优选为0以上、0.15以下,更优选0以上、0.10以下。
“z”表示将作为B位置元素的Nb置换的Ta的置换量。用Ta将Nb的一部分置换,则得到压电特性等提高的效果。具体地,z的值优选0以上、0.4以下。如果z值超过0.4,则居里温度降低,难于用作家电或汽车用的压电材料。z值优选0以上、0.35以下,更优选0以上、0.30以下。
此外,“w”表示将作为B位置元素的Nb置换的Sb的置换量。用Sb将Nb的一部分置换,则得到压电特性等提高的效果。具体地,w的值优选0以上、0.2以下。如果w值超过0.2,则压电特性、及/或居里温度降低,因此不可取。w值优选0以上、0.15以下,更优选0以上、0.10以下。
此外,期望本发明的结晶取向陶瓷只由示于化1式的通式所示的各向同性钙钛矿型化合物(以下,将其称为“第1KNN系化合物”)构成,但只要能够维持各向同性钙钛矿型的结晶结构,且对烧结特性、压电特性等诸特性不产生不良影响,也可以含有其他元素或其他相。
作为所述的“其他元素”,具体地说,作为一例可以例举将第1KNN系化合物的A位置元素置换的其他1价阳离子元素(例如,Ag+、Cs+等)、将第1KNN系化合物的B位置元素置换的其他五价阳离子元素(例如V5+、Re5+等)等。
此外,将A位置元素及B位置元素置换的“其他元素”可以为它们的价数之和为6价的组合。具体地说,作为一例可以例举Ba2+和Ti4+的组合、Sr2+和Ti4+的组合、Ca2+和Ti4+的组合等。此外,作为将B位置元素置换的“其他元素”,也可以只含有6价的金属元素(例如,W6+、Mo6+等)。在这种情况下,为了使阳离子元素全体的价数为6价,则A位置上形成缺陷(空缺)。
此外,作为“其他相”,具体地说,其一例可以是源自于后述的制造方法或使用的初始原料的添加物、烧结助剂、副生成物、杂质等(例如,Bi2O3、CuO、MnO2、NiO等)。由于担心对压电特性等产生不良影响,因此其他元素或其他相的含有量越少越好。
所谓“特定的结晶面取向”是指,各晶粒配列以使第1KNN系化合物的特定结晶面相互平行(以下,将该状态称为“面取向”),或各晶粒配列以使特定的结晶面相对于贯通成型体的1个轴平行(以下,将该状态称为“轴取向”)。
取向的结晶面的种类并无特别限制,根据第1KNN系化合物的自发极化的方向、结晶取向陶瓷的用途、要求特性等进行选择。即,与目的相适应,取向的结晶面选择拟立方{100}面、拟立方{110}面、拟立方{111}面。
一般地,各向同性钙钛矿型化合物具有比正方晶、斜方晶、三方晶略有变形的结构,但由于其变形很小,因此所谓“拟立方{HKL}”,是指将其看作立方晶而用密勒指数表示。
此外,特定的结晶面面取向时,面取向的程度可以用下数式(数学式1)表示的Lotgering法测定的平均取向度F(HKL)表示。
F(HKL)=Σ′I(HKL)ΣI(hkl)-Σ′IO(HKL)ΣIO(hkl)1-Σ′IO(HKL)ΣIO(hkl)×100(%)]]>在该数学式1中,∑I(hkl)为对于结晶取向陶瓷测定的所有结晶面(hkl)的X射线衍射强度的总和,∑I0(hkl)为对于与结晶取向陶瓷具有同一组成的无取向陶瓷测定的所有结晶面(hkl)的X射线衍射强度的总和。此外,∑’I(HKL)为对于结晶取向陶瓷测定的结晶学上等价的特定结晶面(HKL)的X射线衍射强度的总和,∑’I0(HKL)为对于与结晶取向陶瓷具有同一组成的无取向陶瓷测定的结晶学上等价的特定结晶面(HKL)的X射线衍射强度的总和。
因此,当构成多晶体的各晶粒为无取向时,平均取向度F(HKL)为0%。此外,当构成多结晶体的所有结晶粒的(HKL)面相对于测定面平行取向时,平均取向度F(HKL)为100%。
一般地,取向的结晶粒的比例增高,则获得高特性。例如,当使特定的结晶面面取向时,为了获得高压电特性等,优选下述的数学式1所示的Lotgering法测定的平均取向度F(HKL)为30%以上,更优选50%以上。此外,使其取向的特定的结晶面优选垂直于极化轴的面。例如,当该钙钛矿型化合物的结晶系为正方晶时,使其取向的特定的结晶面优选{100}面。
此外,使特定的结晶面轴取向时,其取向程度不能用与面取向同样的取向度(数学式1)定义。但是,对于垂直于取向轴的面进行X射线衍射时,可以用与(NKL)衍射相关的Lotgering法测定平均取向度(以下,将其称为“轴取向度”)表示轴取向的程度。此外,特定的结晶面大致完全轴取向的成型体的轴取向度与对于特定的结晶面大致完全面取向的成型体测定的轴取向度为相同程度。
由于本发明的结晶取向陶瓷由以第1KNN系化合物为主相的多晶体构成,因此即使在非铅系的压电陶瓷中也显示出高压电特性。此外,由于本发明的结晶取向陶瓷,其构成多晶体的各晶粒的特定的结晶面沿一方向取向,因此与具有同一组成的无取向烧结体相比,显示出高压电特性等。
具体地说,通过使构成其主相的第1KNN系化合物的组成、取向度、制造条件等最适化,制得的结晶取向陶瓷其室温下压电d31常数为具有同一组成的无取向烧结体的至少1.1倍以上。此外,如果使这些条件最适化,制得的结晶取向陶瓷其室温下压电d31常数为具有同一组成的无取向烧结体的1.2倍以上,如果进一步最适化,为1.3倍以上。
同样地,通过使构成其主相的第1KNN系化合物的组成、取向度、制造条件等最适化,制得的结晶取向陶瓷其室温下机电耦合系数kp为具有同一组成的无取向烧结体的至少1.1倍以上。此外,如果使这些条件最适化,制得的结晶取向陶瓷其室温下机电耦合系数kp为具有同一组成的无取向烧结体的1.2倍以上,如果进一步最适化,为1.3倍以上。
此外,通过使构成其主相的第1KNN系化合物的组成、取向度、制造条件等最适化,制得的结晶取向陶瓷其室温下压电g31常数为具有同一组成的无取向烧结体的至少1.1倍以上。此外,如果使这些条件最适化,制得的结晶取向陶瓷其室温下压电g31常数为具有同一组成的无取向烧结体的1.2倍以上,如果进一步最适化,为1.4倍以上。
此外,对于驱动器用材料,在电场强度100V/mm以上的大电场下,利用与外加电压方向平行方向产生的位移。通过使构成其主相的第1KNN系化合物的组成、取向度、制造条件等最适化,得到的结晶取向陶瓷其在同一温度、同一电场强度的条件的大电场下产生的位移是具有同一组成的无取向烧结体的至少1.1倍以上。此外,如果使这些条件最适化,制得的结晶取向陶瓷为具有同一组成的无取向烧结体的1.2倍以上,如果再进一步最适化,为1.3倍以上。此外,在驱动器用材料中,希望在大电场下产生的位移的温度依赖性小。如果是无取向烧结体,产生位移的温度依赖性大,不适于驱动器用途。但是,通过使构成其主相的第1KNN系化合物的组成、取向度、制造条件等最适化,得到的结晶取向陶瓷具有优异的温度特性,其在大电场下产生的位移的最大值和最小值相对于平均值的变动幅度在任意的100℃以上的整个温度范围中至少为±20%以内。进一步使这些条件最适化,得到的结晶取向陶瓷在任意的100℃以上的温度范围中最大位移和最小位移相对于平均值的变动幅度至少在±10%以内,如果再进一步最适化,为±7%以内,如果进一步最适化,为±5%以内。此外,为了使位移量增大,优选驱动时的电场强度为500V/mm以上,更优选为1000V/mm以上。
此外,对大电场下产生的位移进行控制的方式可以分为①以电压作为参数进行控制的电压控制法、②以注入能量作为参数对位移进行控制的能量控制法、以及③以注入电荷为参数对位移进行控制的电荷控制法。在①电压控制法的情况下,希望在一定电压下产生位移的温度依赖性小,在②能量控制法的情况下,希望在一定注入能量下产生位移的温度依赖性小,在③电荷控制法的情况下,希望在一定注入电荷下产生位移的温度依赖性小。
此外,在能量控制和电荷控制的情况下,由于大电场下静电容量的温度依赖性,负荷于驱动器及驱动回路的端子电压变动,因此必须用端子电压变动幅度的上限设计回路。由于静电容量的温度依赖性,有时需要高耐压、高价格的回路元件,因此希望静电容量的温度特性小。以上所述可以通过A3式及A4式很容易地理解。
W=1/2×C×V2A3Q=C×V A4这里,W能量[J]、C静电容量[F]、V外加电压[V]及Q电荷[C]。
此外,由于驱动器的位移(电场诱导位移量ΔL)与外加电压存在比例关系,因此定电场驱动(EF一定)中的位移如A5式所示,与D33large成比例。
ΔL=D33large×EFmax×L A5这里,D33large动态变形量[m/V]、EFmax最大电场强度[V/m]及L外加电压前原本的长度[m],D33large是在一定的振幅下外加电场强度0~2000V/mm的高电压进行驱动的情况下,根据式A6求得的与外加电压的平行方向上产生的位移,作为动态变形量。
D33large=Smax/EFmax=(ΔL/L)/(V/L) A6这里,Smax最大变形量。
此外,定能量驱动(W一定)中的位移(ΔL)如A7式及A8式所示,与D33large/(E33large)1/2成比例。
ΔL=D33large×(2×W/C)1/2A7C=E33large×ε0×A/LA8这里,ΔL电场诱导位移量[m]、E33large动态介电常数、A电极面积[m2]及ε0真空中的介电常数[F/m]。
此外,E33large是在以一定的振幅外加电场强度0~2000V/mm的高电压进行驱动的情况下,根据式A9测定由极化量-电滞回线得到的极化量,以此为基础算出高电场下驱动的注入电荷量,作为介电常数(动态介电常数)。
E33large=Pmax/(EFmax×ε0)=(Qmax/A)/((V/L)×ε0) A9这里,Pmax最大电荷密度[C/m2]及Qmax最大电荷[C]。
此外,定电荷驱动(Q一定)中位移(电场诱导位移量ΔL)如A10式及A8式所示,与D33large/E33large成比例。
ΔL=D33large×Q/C A10
对于无取向烧结体,D33large和E33large的温度依赖性大,D33large/(E33large)1/2及D33large/E33large的温度依赖性也大,因此不适于驱动器用途。但是,通过使构成其主相的第1KNN系化合物的组成、取向度、制造条件等最适化,得到的结晶取向陶瓷具有优异的温度特性,其在大电场下产生的D33large/(E33large)1/2、D33large/E33large及E33large的最大值和最小值相对于平均值的变动幅度中,任一个以上在任意的100℃以上的整个温度范围中至少为±20%以内。如果进一步使这些条件最适化,得到的结晶取向陶瓷其在D33large/(E33large)1/2、D33large/E33large及E33large的任一个以上中,在任意的100℃以上的温度范围中最大位移和最小位移相对于平均值的变动幅度为±15%以内,如果进一步最适化,则为±10%以内,如果再进一步最适化,则为±8%以内,如果再进一步最适化,则为±5%以内。
以下,对本发明的用于制造结晶取向陶瓷的第1各向异性形状粉末进行说明。具有第1KNN系化合物这样复杂组成的陶瓷通常用下述方法制造混合使含有成分元素的单纯化合物达到化学计量比,将该混合物成型、煅烧后进行破碎,然后将破碎粉再成型、烧结。但是,使用该方法,要得到各晶粒的特定结晶面沿特定方向取向的取向烧结体是极其困难的。
为了解决该问题,本发明的特征在于使满足特定条件的第1各向异性形状粉末在成型体中取向,用该第1各向异性形状粉末作为模板或反应性模板进行第1KNN系化合物的合成及其烧结,从而使构成多晶体的各晶粒的特定结晶面沿一方向取向。在本发明中,在第1各向异性形状粉末中使用满足以下条件的物质。
第1,用于第1各向异性形状粉末的物质,其在成型时具有容易使其沿一定方向取向的形状。为此,第1各向异性形状粉末的平均长宽比(=第1各向异性形状粉末的最大尺寸/最小尺寸的平均值)(aspect ratio)要求为3以上。如果平均长宽比不足3,则成型时使第1各向异性形状粉末沿一方向取向困难,因此不可取。为了得到高取向度的结晶取向陶瓷,第1各向异性形状粉末的平均长宽比优选为5以上,更优选为10以上。
一般地,第1各向异性形状粉末的平均长宽比越大,成型时第1各向异性形状粉末越容易取向。但是,如果平均长宽比过大,有时在后述的混合工序中第1各向异性形状粉末被破碎,不能得到第1各向异性形状粉末取向的成型体。因此,第1各向异性形状粉末的平均长宽比优选为100以下。
此外,第1各向异性形状粉末的平均粒径(长度方向尺寸的平均值)优选0.05μm以上。如果第1各向异性形状粉末的平均粒径不足0.05μm,则通过成型时作用的剪切应力使第1各向异性形状粉末沿一定方向取向变得困难。此外,由于界面能的益处减小,因此在用作制作结晶取向陶瓷时的反应性模板时,不易产生向模板粒子的外延生长。
另一方面,第1各向异性形状粉末的平均粒径优选为20μm以下。如果第1各向异性形状粉末的平均粒径超过20μm,则烧结性降低,得不到烧结体密度高的结晶取向陶瓷。第1各向异性形状粉末的平均粒径更优选为0.1μm以上、10μm以上。
第2,用于第1各向异性形状粉末的物质,其生长面(占有最大面积的面)与第1KNN系化合物的特定结晶面具有晶格匹配性。即使是具有所定形状的各向异性形状粉末,当其生长面与第1KNN系化合物的特定结晶面不具有晶格匹配性时,有时作为用于制造本发明的结晶取向陶瓷的反应性模板不能发挥作用,因此不可取。
晶格匹配性好否可以用第1各向异性形状粉末的生长面的晶格尺寸除以第1各向异性形状粉末的生长面的晶格尺寸和第1KNN系化合物的特定的结晶面的晶格尺寸的差的绝对值所得到的值(以下,将该值称为“晶格匹配率”)表示。该晶格匹配率有时由于所取晶格方向的不同而略有不同。一般地,平均晶格匹配率(对于各方向算出的晶格匹配率的平均值)越小,该第1各向异性形状粉末越能作为良好的模板发挥作用。为了得到高取向度的结晶取向陶瓷,第1各向异性形状粉末的平均晶格匹配率优选20%以下,更优选10%以下。
第3,第1各向异性形状粉末未必是与第1KNN系化合物具有同一组成的物质,可以为与后述第1反应原料反应,生成具有成为目的组成的第1KNN系化合物的物质。因此,第1各向异性形状粉末从化合物或固溶体中选取,所述化合物或固溶体含有要制作的第1KNN系化合物所含有的阳离子元素内的任何一种以上的元素。
此外,所谓“各向异性形状”,是指长度方向的尺寸比宽度方向或厚度方向的尺寸大。具体地说,作为适合的一例可以例举板状、柱状、鳞片状等。此外,构成生长面的结晶面的种类并无特别限定,根据目的从各种结晶面中选取。
如果为满足以上条件的第1各向异性形状粉末,均可以起到用于制造本发明的结晶取向陶瓷的模板或反应性模板的作用。作为满足这种条件的材料,具体如下所述。
适合作为第1各向异性形状粉末的材料的第1具体例,为作为各向同性钙钛矿型化合物的一种的NaNbO3(以下,将其称为“NN”)、KNbO3(以下,将其称为“KN”)、或K1-yNayNbO3、或Li、Ta及/或Sb置换、固溶于这些物质中的物质,示于下式的通式所示的物质(以下,将它们总称为“第2KNN系化合物”)。
{Lix(K1-yNay)1-x}{Nb1-z-wTazSbw}O3(2)(其中,x、y、z分别为0≤x≤1、0≤y≤1、0≤z≤1、0≤w≤1)第2KNN系化合物当然与第1KNN系化合物具有良好的晶格匹配性。因此,由第2KNN系化合物构成、且以特定的结晶面作为生长面的第1各向异性形状粉末(以下,特别将其称为“各向异性形状粉末A”)可以起到用于制作本发明的结晶取向陶瓷的反应性模板的功能。此外,各向异性形状粉末A由于实质上由第1KNN系化合物所含有的阳离子元素构成,因此可以制造不纯物元素极少的结晶取向陶瓷。在这些物质中,由以拟立方{100}面作为生长面的第2KNN系化合物构成的板状粉末,适宜作为用于制造本发明的结晶取向陶瓷的反应性模板,以拟立方{100}面作为生长面的NN或KN板状粉末特别适合。
适合作为第1各向异性形状粉末的材料的第2具体例,为由层状钙钛矿型化合物构成、且表面能小的结晶面与第1KNN系化合物的特定结晶面具有晶格匹配性的物质。由于层状钙钛矿型化合物的结晶晶格的各向异性大,因此能够比较容易地合成以表面能小的结晶面作为生长面的各向异性形状粉末(以下,将其特称为“第2各向异性形状粉末”)。
适宜作为第2各向异性形状粉末的材料的层状钙钛矿型化合物的第1具体例,为示于下式的通式所示的铋层状钙钛矿型化合物。
(Bi2O2)2+(Bi0.5AMm-1NbmO3m+1)2-(3)(其中,m为2以上的整数,AM为从Li、K及Na中选取的至少一个碱金属元素)该式(3)所示的化合物,由于{001}面的表面能比其他结晶面的表面能小,因此能够容易合成以{001}面作为生长面的第2各向异性形状粉末。这里,所谓{001}面是指与化3式所示的铋层状钙钛矿型化合物的(Bi2O2)2+层平行的面。并且,式(3)所示的化合物的{001}面与第1KNN系化合物的拟立方{100}面之间具有极好的晶格匹配性。
因此,由式(3)所示的化合物构成、且以{001}面作为生长面的第2各向异性形状粉末适宜作为用于制作以拟立方{100}面作为生长面的结晶取向陶瓷的反应性模板。此外,如果使用化2式所示的化合物,通过使后述的第1反应原料的组成最适化,即使是以实质上不含有Bi作为A位置元素的第1KNN系化合物作为主相的结晶取向陶瓷,也可以制造。
适宜作为第2各向异性形状粉末的材料的层状钙钛矿型化合物的第2具体例为Sr2Nb2O7。Sr2Nb2O7的{010}面,其表面能比其他结晶面的表面能小,且与第1KNN系化合物的拟立方{110}面之间具有极好的晶格匹配性。因此,由Sr2Nb2O7构成、且以{010}作为生长面的各向异性形状粉末适宜作为用于制作以{110}面为生长面的结晶取向陶瓷的反应性模板。
作为第2各向异性形状粉末的材料适宜的层状钙钛矿型化合物的第3具体例为Na1.5Bi2.5Nb3O12、Na2.5Bi2.5Nb4O15、Bi3TiNbO9、Bi3TiTaO9、K0.5Bi2.5Nb2O9、CaBi2Nb2O9、SrBi2Nb2O9、BaBi2Nb2O9、BaBi3Ti2NbO12、CaBi2Ta2O9、SrBi2Ta2O9、BaBi2Ta2O9、Na0.5Bi2.5Ta2O9、Bi7Ti4NbO21、Bi5Nb3O15等。这些化合物的{001}面与第1KNN系化合物的拟立方{100}面具有良好的晶格匹配性。因此,由这些化合物构成、且以{001}面作为生长面的各向异性形状粉末适宜作为用于制造以拟立方{100}面作为生长面的结晶取向陶瓷的反应性模板。
作为第2各向异性形状粉末适宜的层状钙钛矿型化合物的第4具体例为Ca2Nb2O7、Sr2Ta2O7等。这些化合物的{010}面与第1KNN系化合物的拟立方{110}面具有良好的晶格匹配性。因此,由这些化合物构成、且以{010}面作为生长面的各向异性形状粉末适宜作为用于制造以拟立方{110}面作为生长面的结晶取向陶瓷的反应性模板。
以下,对第1各向异性形状粉末的制造方法进行说明。由具有所定组成、平均粒径及/或长宽比的层状钙钛矿型化合物构成的第1各向异性形状粉末(即,第2各向异性形状粉末)通过与液体或通过加热成为液体的物质一同加热,可以很容易地制造含有第2各向异性形状粉末的成分元素的氧化物、碳酸盐、硝酸盐等原料(以下,将其称为“各向异性形状粉末生成原料”)。
如果在原子扩散容易的液相中对各向异性形状粉末生成原料进行加热,可以很容易地合成表面能小的面(例如,当为式(3)所示物质时,{001}面)优先发展的第2各向异性形状粉末。在这种情况下,第2各向异性形状粉末的平均长宽比及平均粒径可以通过适当选择合成条件进行控制。
作为第2各向异性形状粉末的制造方法,具体地说,作为适宜的一例可以例举在各向异性形状粉末生成原料中添加适当的助熔剂(例如,NaCl、KCl、NaCl和KCl的混合、BaCl2、KF等)并在所定温度下进行加热的方法(助熔剂法)、将与要制作的第2各向异性形状粉末具有同一组成的无定形粉末和碱性水溶液一起在高压釜中加热的方法(水热合成法)。
另一方面,由于第2KNN系化合物的结晶晶格的各向异性极小,因此直接合成由第2KNN系固溶体构成、且以特定的结晶面作为生长面的第1各向异性形状粉末(即,各向异性形状粉末A)困难。但是,各向异性形状粉末A可以使用上述第2各向异性形状作为反应性模板,通过将其与满足所定条件的第2反应原料在助熔剂中加热而制造。
此外,使用第2各向异性形状粉末作为反应性模板合成各向异性形状粉末A时,如果使反应条件最适化,则只引起结晶结构的变化,而几乎没有发生粉末形状的变化。此外,第2各向异性形状粉末的平均粒径及/或长宽比通常在反应前后维持不变,但如果使反应条件最适化,也可以使制得的各向异性形状粉末A的平均粒径及/或长宽比增减。
但是,为了容易地合成成型时使其沿一方向取向容易的各向异性形状粉末A,希望用于其合成的第2各向异性形状粉末也具有成型时使其沿一方向取向容易的形状。
即,使用第2各向异性形状粉末作为反应性模板合成各向异性形状粉末A时,第2各向异性形状粉末的平均长宽比也优选至少3以上,更优选5以上,进一步优选10以上。此外,为了抑制在后续工序中的粉碎,平均长宽比优选100以下。此外,第2各向异性形状粉末的平均粒径优选0.05μm以上、20μm以下,更优选0.1μm以上、10μm以下。
所谓“第2反应原料”,是指与上述第2各向异性形状粉末反应,生成至少由第2KNN系化合物构成的各向异性形状粉末A的物质。在这种情况下,第2反应原料可以通过与第2各向异性形状粉末反应,只生成第2KNN系化合物,或也可以生成第2KNN系化合物和剩余成分两者。这里,所谓剩余成分,是指成为目的的第2KNN系化合物以外的物质。此外,由第2各向异性形状粉末与第2反应原料生成剩余成分时,希望剩余成分由容易通过热或化学方法除去的物质构成。
第2反应原料的形态并无特别限定,可以使用氧化物粉末、复合氧化物粉末、碳酸盐、硝酸盐、草酸盐等盐,烷氧基金属等。此外,第2反应原料的组成由要制作的第2KNN系化合物的组成及第2各向异性形状粉末的组成决定。
例如,使用作为式(3)所示铋层状钙钛矿型化合物的1种的Bi2.5Na0.5Nb2O9(以下,将其称为“BINN2”)构成的第2各向异性形状粉末,合成作为第2KNN系化合物的一种的NN构成的各向异性形状粉末A时,作为第2反应原料,可以使用含有Na的化合物(氧化物、氢氧化物、碳酸盐、硝酸盐等)。在这种情况下,相对于1摩尔的BINN2,可以添加相当于Na原子1.5摩尔的Na含有化合物作为第2反应原料。
相对于具有这样组成的第2各向异性形状粉末及第2反应原料,添加1重量%~500重量%适当的助熔剂(例如,NaCl、KCl、NaCl和KCl的混合、BaCl2、KF等),加热到共晶点-熔点,生成NN和以Bi2O3为主成分的剩余成分。由于Bi2O3熔点低、不耐酸,因此通过水洗等从制得的反应物中将助熔剂去除后,用高温对其加热,或如果进行酸洗,得到由以{100}面为生长面的NN构成的各向异性形状粉末A。
此外,例如,使用BINN2构成的第2各向异性形状粉末合成由作为第2KNN系固溶体的一种的K0.5Na0.5NbO3(以下,将其称为“KNN”)构成的各向异性形状粉末A时,作为第2反应原料,可以使用含有Na的化合物(氧化物、氢氧化物、碳酸盐、硝酸盐等)及含有K的化合物(氧化物、氢氧化物、碳酸盐、硝酸盐等)、或含有Na及K两者的化合物。在这种情况下,相对于1摩尔的BINN2,可以添加相当于0.5摩尔Na原子的Na含有化合物、及相当于1摩尔K原子的K含有化合物作为第2反应原料。
相对于具有这样组成的第2各向异性形状粉末及第2反应原料,添加1重量%~500重量%适当的助熔剂,加热到共晶点-熔点,生成KNN和以Bi2O3为主成分的剩余成分,因此如果从得到的反应物中除去助熔剂及Bi2O3,便得到由以{100}面为生长面的KNN构成的各向异性形状粉末A。
与通过第2各向异性形状粉末与第2反应原料反应而只生成第2KNN系化合物的情况相同,可以在适当的助熔剂中对具有所定组成的第2各向异性形状粉末和具有所定组成的第2反应原料进行加热。这样便在助熔剂中生成具有成为目的组成的第2KNN系化合物。此外,如果从制得的反应物中除去助熔剂,便得到由第2KNN系化合物构成、且以特定的结晶面作为生长面的各向异性形状粉末A。
由于第2KNN系化合物的结晶晶格的各向异性小,因此直接合成各向异性形状粉末A困难。此外,直接合成以任意的结晶面作为生长面的各向异性形状粉末A也困难。
与此相比,由于层状钙钛矿型化合物的结晶晶格的各向异性大,因此直接合成各向异性形状粉末容易。此外,由层状钙钛矿型化合物构成的各向异性形状粉末的生长面与第2KNN系化合物的特定结晶面之间多具有晶格匹配性。此外,第2KNN系化合物与层状钙钛矿型化合物相比,具有热力学稳定性。因此,使由层状钙钛矿型化合物构成、且其生长面与第2KNN系化合物的特定结晶面具有晶格匹配性的第2各向异性形状粉末和第2反应原料在适当的助熔剂中反应,可以容易地合成第2各向异性形状粉末起到反应性模板的功能,由继承了第2各向异性形状粉末取向方向的第2KNN系化合物构成的各向异性形状粉末A。
此外,如果使第2各向异性形状粉末及第2反应原料的组成最适化,第2各向异性形状粉末所含有的A位置元素(以下,将其称为“剩余A位置元素”)作为剩余成分排出,且生成由不含剩余A位置元素的第2KNN系化合物构成的各向异性形状粉末A。
特别当第2各向异性形状粉末由化3式所示的铋层状钙钛矿型化合物构成时,Bi作为剩余A位置元素被排出,生成以Bi2O3为主成分剩余成分。因此,如果通过热或化学方法将该剩余成分除去,便得到实质上不含Bi,由第2KNN系化合物构成、且以特定的结晶面作为生长面的各向异性形状粉末A。
以下,对本发明的结晶取向陶瓷的制造方法进行说明。本发明的结晶取向陶瓷的制造方法包括混合工序、成型工序、热处理工序。
首先,对混合工序进行说明。混合工序是将第1各向异性形状粉末和第1反应原料混合的工序。这里,所谓“第1各向异性形状粉末”,是指其生长面与第1KNN系化合物的特定结晶面具有晶格匹配性的物质。作为第1各向异性形状粉末,具体地说,可以使用上述的各向异性形状粉末A、第2各向异性形状粉末等。
此外,所谓“第1反应原料”,是指与第1各向异性形状粉末反应,至少生成第1KNN系化合物的物质。在这种情况下,第1反应原料由于与第1各向异性形状粉末反应,可以只生成第1KNN系化合物,或也可以生成第1KNN系化合物和剩余成分两者。此外,由第1各向异性形状粉末与第1反应原料生成剩余成分时,希望剩余成分为容易通过热或化学方法除去的物质。
第1反应原料的组成由第1各向异性形状粉末的组成、及要制作的第1KNN系化合物的组成确定。此外,第1反应原料的形态并无特别限定,可以使用氧化物粉末、复合氧化物粉末、氢氧化物粉末、碳酸盐、硝酸盐、草酸盐等盐,烷氧基金属等。
例如,使用具有KNN组成或NN组成的各向异性形状粉末A作为第1各向异性形状粉末,制作由第1KNN系化合物构成的结晶取向陶瓷时,作为第1反应原料,使用含有Li、K、Na、Nb、Ta及Sb的至少一个元素的化合物的混合物,可以将它们按化学计量组成进行配合从而由各向异性形状粉末A和第1反应原料生成具有目的组成的第1KNN系化合物。
此外,例如,使用具有化3式所示组成的第2各向异性形状粉末作为第1各向异性形状粉末,制作第1KNN系化合物构成的结晶取向陶瓷时,作为反应原料使用含有Li、K、Na、Nb、Ta及Sb的至少一个元素的化合物的混合物,可以将它们按化学计量组成进行配合从而由第2各向异性形状粉末和第1反应原料生成具有目的组成的第1KNN系化合物及Bi2O3。制作具有其他组成的结晶取向陶瓷时也同样。
此外,在混合工序中,对于以所定比率配合的第1各向异性形状粉末及第1反应原料,可以添加具有与通过它们的反应而得到的第1KNN系化合物同一组成的化合物构成的无定形的微粉(以下,将其称为“化合物粉末”)及/或烧结助剂(例如,CuO等)。对于第1各向异性形状粉末及第1反应原料进一步添加化合物微粉或烧结助剂,具有更容易使烧结体致密化的优点。
此外,在配合化合物微粉时,如果化合物微粉的配合比率过大,则必然使第1各向异性形状粉末占原料全体的配合比率减小,担心特定的结晶面的取向度降低。因此,化合物微粉的配合比率优选根据要求的烧结体密度及取向度选择最适的配合比率。
第1各向异性形状粉末的配合比率由第1各向异性形状粉末中一个到多个成分元素构成,优选使ABO3所示第1KNN系化合物的A位置占有的比率为0.01~70原子%,更优选为0.1~50原子%。此外,进一步优选为1~10原子%。
此外,第1各向异性形状粉末及第1反应原料,以及根据需要配合的化合物微粉及烧结助剂的混合可以为干式混合,或添加水、醇等适当的分散介质进行湿式混合。此外,此时根据需要也可以加入粘合剂及/或增塑剂。
以下,对成型工序进行说明。成型工序是将混合工序中得到的混合物成型从而使第1各向异性形状粉末取向的工序。此时,可以成型以使第1各向异性形状粉末面取向,或也可以成型使第1各向异性形状粉末轴取向。
对于成型方法,可以为能够使第1各向异性形状粉末取向的方法,并无特别限定。作为使第1各向异性形状粉末面取向的成型方法,作为适宜的一例具体可以例举刮片法、压制成型法、压延法等。此外,作为使第1各向异性形状粉末轴取向的成型方法,作为适宜的一例具体可以例举挤出成型法、离心成型法等。
此外,为了使第1各向异性形状粉末面取向的成型体(以下,将其称为“面取向成型体”)的厚度增加,或提高取向度,可以对面取向成型体进一步进行积层压合、压制、压延等处理(以下,将其称为“面取向处理”)。在这种情况下,可以对于面取向成型体进行任何一种面取向处理,或也可以进行2种以上的面取向处理。此外,对于面取向成型体可以反复多次进行1种面取向处理,或也可以分别反复多次进行2种以上的取向处理。
以下,对热处理工序进行说明。热处理工序是对在成型工序中制得的成型体加热,使第1各向异性形状粉末和第1反应原料反应的工序。如果将含有第1各向异性形状粉末和第1反应原料的成型体加热到所定温度,由于它们的反应使第1KNN系化合物生成,与此同时,生成的第1KNN系化合物的烧结进行。此外,由于第1各向异性形状粉末及/或第1反应原料的组成的不同,剩余成分也同时生成。
为了使反应及/或烧结有效地进行,且生成具有目的组成的反应物,加热温度可以根据使用的第1各向异性形状粉末、第1反应原料、要制作的结晶取向陶瓷的组成等选择适当的温度。
例如,当使用具有KNN组成的各向异性形状粉末A制造由第1KNN系化合物构成的结晶取向陶瓷时,加热一般在900℃以上、1300℃以下进行。最适的加热温度根据第1KNN系化合物的组成的不同而不同。此外,加热可以在大气中、氧中、减压下或真空下的任何气氛下进行。此外,为了得到所定的烧结体密度,加热时间可以根据加热温度选择最适的时间。
此外,当由于第1各向异性形状粉末和第1反应原料反应而生成剩余成分时,可以使剩余成分作为副相残留在烧结体中,或也可以从烧结体中将剩余成分除去。当除去剩余成分时,其方法包括加热除去的方法和化学除去的方法。
加热除去的方法是将第1KNN系化合物及剩余成分生成的烧结体(以下,将其称为“中间烧结体”)加热到所定温度从而使剩余成分挥发的方法。具体地说,作为适宜的一例可以例举减压下或真空下以剩余成分挥发产生的温度加热中间烧结体的方法、在大气中或氧中以剩余成分挥发产生的温度长时间加热中间烧结体的方法等。
为了剩余成分的挥发有效地进行,且副生成物的生成得以抑制,用热将剩余成分除去时的加热温度可以根据第1KNN系化合物及/或剩余成分的组成选择最适的温度。例如,当剩余成分为氧化铋单相时,加热温度优选800℃以上、1300℃以下,更优选1000℃以上、1200℃以下。
将剩余成分化学除去的方法是将中间烧结体浸渍于具有只使剩余成分浸蚀性质的处理液中,将剩余成分抽出的方法。使用的处理液可以根据第1KNN系化合物及/或剩余成分的组成选择最适的处理液。例如,当剩余成分为氧化铋单相时,处理液优选使用硝酸、盐酸等酸。硝酸特别适合作为将以氧化铋为主成分的剩余成分化学抽出的处理液。
第1各向异性形状粉末和第1反应原料的反应及剩余成分的除去可以同时、逐次或个别的任一时间方式进行。例如,可以在减压下或真空下对成型体直接加热,直至第1各向异性形状粉末和第1反应原料的反应及剩余成分的挥发两者有效进行的温度,在反应的同时进行剩余成分的除去。
此外,例如,可以在大气中或氧中、在第1各向异性形状粉末和第1反应原料的反应有效进行的温度下对成型体进行加热,使中间烧结体生成后,紧接着在减压下或真空下、在剩余成分的挥发有效进行的温度下对中间烧结体进行加热,从而将剩余成分除去。或者,可以在使中间烧结体生成后,紧接着在大气中或氧中、在剩余成分的挥发有效进行的温度下对中间烧结体进行长时间加热,从而将剩余成分除去。此外,例如,可以在使中间烧结体生成、将中间烧结体冷却到室温后,将中间烧结体浸渍于处理液中,将剩余成分化学除去。或者,可以在使中间烧结体生成、冷却到室温后,在所定气氛下再次将中间烧结体加热到所定温度,用热将剩余成分除去。
此外,含有粘合剂的成型体的情况下,可以在热处理工序前进行以脱脂为主目的的热处理。在这种情况下,脱脂的温度可以是足以至少使粘合剂热分解的温度。但是,当原料中含有易挥发物(例如,Na化合物)时,脱脂优选在500℃以下进行。
此外,如果进行取向成型体的脱脂,则取向成型体中第1各向异性形状粉末的取向度降低,或者有时在取向成型体上产生体积膨胀。在这种情况下,优选在进行了脱脂后、进行热处理前,还要对取向成型体进行静水压(CIP)处理。如果对脱脂后的成型体进一步进行静水压处理,具有能够抑制伴随脱脂而产生的取向度降低或取向成型体体积膨胀而引起的烧结体密度降低的优点。
此外,由于第1各向异性形状粉末和第1反应原料反应而生成剩余成分时,在进行剩余成分的除去时,可以进而对除去了剩余成分的中间烧结体进行静水压处理、将其再烧成。此外,为了进一步提高烧结体密度及取向度,有效的方法是进一步对热处理后的烧结体进行热压。此外,可以组合使用添加化合物微粉、CIP处理、热压等方法。
以下,对本发明的结晶取向陶瓷的制造方法的作用进行说明。将第1各向异性形状粉末及第1反应原料混合,使用对第1各向异性形状粉末从一方向作用力的成型方法将其成型,由于作用于第1各向异性形状粉末的剪切应力使第1各向异性形状粉末在成型体中取向。如果在所定温度下加热该成型体,则第1各向异性形状粉末和第1反应原料反应,生成第1KNN系化合物。
此时,由于第1各向异性形状粉末的生长面和第1KNN系化合物的特定结晶面之间具有晶格匹配性,因此第1各向异性形状粉末的生长面作为生成的第1KNN系化合物的特定结晶面被继承下来。因此,在特定的结晶面沿一方向取向的状态下,在烧结体中生成了第1KNN系化合物的各向异性形状结晶。
用由层状钙钛矿型化合物构成的各向异性形状粉末作为反应性模板,只使各向同性钙钛矿型化合物生成的以往的方法,只可以制造结晶取向陶瓷或各向异性形状粉末,所述结晶取向陶瓷或各向异性形状粉末由含有各向异性形状粉末及其他原料所含有的全部A位置元素及B位置元素的各向同性钙钛矿型化合物构成。
另一方面,用作反应性模板的各向异性形状粉末的材质须为结晶晶格的各向异性大,且与各向同性钙钛矿型化合物之间具有晶格匹配性的材质,但由于要制作的各向同性钙钛矿型化合物的组成的原因,因此不存在满足这样的条件的材料,或者有时对其研究伴随着显著的困难。因此,在以往的方法中,在制得的结晶取向陶瓷或各向异性形状粉末的组成控制,特别是A位置元素的组成控制上存在限度。
与此相比,首先使用由各向异性形状粉末合成容易的层状钙钛矿型化合物构成的第2各向异性形状粉末作为反应性模板,合成由第2KNN系化合物构成的各向异性形状粉末A,然后使用该各向异性形状粉末A作为反应模板制造结晶取向陶瓷的第1方法,根据该方法,即使是结晶晶格的各向异性小的第1KNN系化合物,也可以容易且价廉地制造任意结晶面取向的结晶取向陶瓷。
并且,如果使第2各向异性形状粉末及第2反应原料的组成最适化,即使是不含有剩余A位置元素的各向异性形状粉末A也可以合成。因此,与以往的方法相比,A位置元素的组成控制更容易,即使是以具有以往方法中无法制得的组成的第1KNN系化合物作为主相的结晶取向陶瓷,也可以制造。
此外,使用由层状钙钛矿型化合物构成的第2各向异性形状粉末作为第1各向异性形状粉末的第2方法,根据该方法,可以在烧结的同时合成第1KNN系化合物。此外,如果使成型体中使之取向的第2各向异性形状粉末及使与其反应的第1反应原料的组成最适化,在合成第1KNN系化合物的同时,可以将剩余A位置元素作为剩余成分从第2各向异性形状粉末中排出。
此外,当使用生成容易热或化学除去的剩余成分的第2各向异性形状粉末作为第1各向异性形状粉末时,制得实质上不含有剩余A位置元素,由第1KNN系化合物构成,且特定的结晶面取向的结晶取向陶瓷。
此外,用本发明的方法得到的结晶取向陶瓷由于由含有所定量的Li、Ta及/或Sb的第1KNN系化合物构成,因此与由不含有这些的各向同性钙钛矿型化合物构成的烧结体相比,显示出高压电d31常数及机电耦合系数kp。此外,这样得到的结晶取向陶瓷由于特定的结晶面以高取向度取向,因此与具有同一组成的无取向烧结体相比,显示出高压电d31常数、机电耦合系数kp及压电g31常数。
(实施例1)(1)NN板状粉末的合成按化学计量比为Bi2.5Na3.5Nb5O18(以下,将其称为“BINN5”)组成,称量Bi2O3粉末、Na2CO3粉末及Nb2O5粉末,对其进行湿式混合。然后,向该原料中添加50重量%NaCl作为助熔剂(flux),进行1小时干式混合。
然后,将制得的混合物放入铂坩埚中,在850℃×1小时的条件下进行加热,在使助熔剂完全溶解后,进一步在1100℃×2小时的条件下加热,合成BINN5。此外,升温速度为200℃/小时,降温为炉内冷却。冷却后,通过热水洗从反应物中去除助熔剂,得到BINN5粉末。得到的BINN5粉末是以{001}面为生长面的板状粉末。
然后,在该BINN5板状粉末中添加NN合成所需量的Na2CO3粉末并混合,以NaCl作为助熔剂,在铂坩埚中进行950℃×8小时的热处理。
由于在得到的反应物中除了NN粉末,还含有Bi2O3,从反应物中去除助熔剂后,将其放入HNO3(1N)中,使作为剩余成分生成的Bi2O3溶解。进而,将该溶液过滤、分离NN粉末,用80℃的离子交换水洗涤。得到的NN粉末是以拟立方{100}面为生长面、粒径为10~20μm且长宽比为10~20左右的板状粉末。
(2)具有{Li0.02(K0.5Na0.5)0.98}{Nb0.94Sb0.06}O3组成的结晶取向陶瓷的制作按目标组成称量(1)中制作的NN板状、以及非板状的NN粉末、KN粉末、KT(KTaO3)粉末、LS(LiSbO3)粉末及NS(NaSbO3)粉末,进行20小时的湿式混合。
向浆料和从初始原料合成的1mol的{Li002(K0.5Na0.5)098}{Nb0.94Sb0.06}O3中分别加入10.35g粘合剂(积水化学(株)制造、エスレツク(注册商标)BH-3)及10.35g增塑剂(邻苯二甲酸二丁酯),其后再混合2小时。
此外,NN板状粉末的配合量使从初始原料合成的第1KNN系固溶体(ABO3)的A位置元素的5原子%为从NN板状粉末供给的量。此外,非板状的NN粉末、KN粉末、KT粉末、LS粉末及NS粉末是通过将含有所定量的K2CO3粉末、Na2CO3粉末、Nb2O5粉末、Ta2O5粉末及/或Sb2O5粉末的混合物在750℃下加热5小时,用球磨机将反应物粉碎的固相法制作的。
然后,使用刮板装置,将混合的浆料成型为厚度100μm的带(tape)状。然后,通过将该带状物积层、压合及压延,制得厚度为1.5mm的板状成型体。然后,在大气中、加热温度600℃、加热时间2小时、升温速度50℃/小时、冷却速度为炉内冷却的条件下对制得的板状成型体进行脱脂。进而,在压力300MPa下对脱脂后的板状成型体实施CIP处理,其后在氧中、烧成温度1100℃、加热时间1小时、升降温速度200℃/小时的条件下进行常压烧结。
对于制得的烧结体,测定烧结体密度、及对与带状面平行的面用Lotgering法测定{100}面的平均取向度F(100)、以及作为压电特性的压电变形常数(d31)、机电耦合系数(kp)及压电电压传感器g系数(g31)。
此外,用数学式1算出平均取向度F(100)。此外,压电特性是通过研削、研磨、加工从制得的烧结体制作其上下面与带状面平行且厚度为0.7mm、直径11mm的圆盘状试样,通过对其上下面进行溅射涂布Au电极,在沿圆盘状试样的上下方向实施极化处理后,在室温下、电场强度为1V/mm的条件下用共振反共振法测定的。此外,根据需要对0℃~200℃的温度范围中压电d31常数的温度依赖性及居里温度进行评价。
本实施例中制得的结晶取向陶瓷的相对密度为95%以上。此外,拟立方{100}面相对于带状面平行取向,Lotgering法测定的拟立方{100}面的平均取向度达到82%。此外,对室温下压电特性的评价结果d31为85.9pm/V、kp为0.532及g31为15.6×10-3Vm/N,与后述的同一组成的无取向烧结体(比较例1)相比,分别提高1.29倍、1.22倍及1.69倍。此外,该结晶取向陶瓷与后述没有添加Li、Ta及Sb的KNN结晶取向陶瓷(比较例5)相比,具有约2倍的d31。
(实施例2)除了使脱脂后的板状成型体的烧成温度为1125℃外,按照与实施例1相同的步骤,制作具有{Li0.02(K0.5Na0.5)0.98}{Nb0.94Sb0.06}O3组成的结晶取向陶瓷。对于制得的结晶取向陶瓷,在与实施例1相同的条件下,对烧结体密度、平均取向度及压电特性进行评价。
本实施例中制得的结晶取向陶瓷的相对密度为95%以上。此外,拟立方{100}面相对于带状面平行取向,Lotgering法测定的拟立方{100}面的平均取向度达到82%。此外,对室温下压电特性的评价结果d31为93.2pm/V、kp为0.588及g31为16.5×10-3Vm/N,与后述的同一组成的无取向烧结体(比较例1)相比,分别提高1.40倍、1.35倍及1.79倍。此外,对d31的温度依赖性的评价结果为0~200℃的范围中d31的最大值达到146.7pm/V,与比较例1相比,提高了1.17倍。此外,居里温度为311℃。
(实施例3)除了按{Li0.02(K0.5Na0.5)0.98}{Nb0.88Ta0.10Sb0.02}O3组成配合初始原料,使脱脂后的板状成型体的烧成温度为1125℃外,按照与实施例1相同的步骤,制作具有{Li0.02(K0.5Na0.5)0.98}{Nb0.88Ta0.10Sb0.02}O3组成的结晶取向陶瓷。对于制得的结晶取向陶瓷,在与实施例1相同的条件下,对烧结体密度、平均取向度及压电特性进行评价。
本实施例中制得的结晶取向陶瓷的相对密度为95%以上。此外,拟立方{100}面相对于带状而平行取向,Lotgering法测定的拟立方{100}面的平均取向度达到81%。此外,对室温下压电特性的评价结果d31为79.9pm/V、kp为0.537及g31为16.0×10-3Vm/N,与后述的同一组成的无取向烧结体(比较例2)相比,分别提高了1.20倍、1.20倍及1.67倍。
(实施例4)除了A位置元素的2原子%由NN板状粉末供给,且按{Li0.02(K0.5Na0.5)0.98}{Nb0.81Ta0.14Sb0.05}O3组成配合初始原料,使脱脂后的板状成型体的烧成温度为1150℃以外,按照与实施例1相同的步骤,制作具有{Li0.02(K0.5Na0.5)0.98}{Nb0.81Ta0.14Sb0.05}O3组成的结晶取向陶瓷。对于制得的结晶取向陶瓷,在与实施例1相同的条件下,对烧结体密度、平均取向度及压电特性进行评价。
本实施例中制得的结晶取向陶瓷的相对密度为95%以上。此外,拟立方{100}面相对于带状面平行取向,Lotgering法测定的拟立方{100}面的平均取向度达到75%。此外,对室温下压电特性的评价结果d31为123.0pm/V、kp为0.588及g31为11.8×10-3Vm/N,与后述的同一组成的无取向烧结体(比较例3)相比,分别提高了1.54倍、1.45倍及1.63倍。
(实施例5)除了按{Li0.02(K0.5Na0.5)0.98}{Nb0.81Ta0.14Sb0.05}O3组成配合初始
结晶取向陶瓷及其制造方法
- 专利详情
- 全文pdf
- 权力要求
- 说明书
- 法律状态
查看更多专利详情
下载专利文献
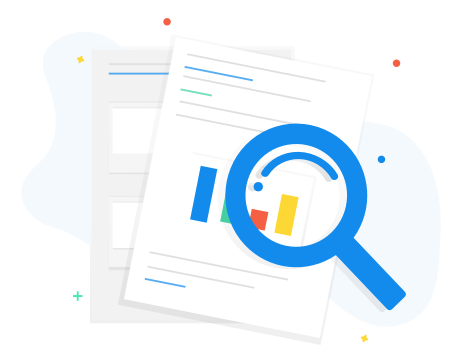
下载专利
同类推荐
-
名取荣治汤玉斐杨建杨建
您可能感兴趣的专利
-
杨建I·韦希特尔-施特勒陈秀丽陈秀丽陈秀丽陈秀丽
专利相关信息
-
王红云王红云