高产节能无氨脱硝一体化的水泥熟料煅烧新方法及装置制造方法 [0002] 水泥行业氮氧化物的排放量占全国工业排放总量的15%左右,已是居火力发电、 汽车尾气之后的第三大氮氧化物排放大户。工信部582号文件关于水泥工业节能减排的指 导意见,提出氮氧化物在2009年的基础上降低25%。同时新建或改扩建水泥(熟料)生产线 项目必须配置脱硝装置。且脱硝效率不低于60%。因此,探讨水泥行业最佳可行的脱硝技术 显得尤为迫切。 [0003] 回转窑是新型干法水泥物料烧成的关键技术装备,也是NOx的主要来源。煅烧 水泥熟料时生成一氧化氮N0的途径主要有四种,即第一种热力NOx,它是燃料在水泥窑头 1400°C以上燃烧时会产生大量NOx ;第二种瞬发NOx,它是有碳氢根存在时,于火焰前端瞬 发形成的N0x,一般这种瞬发N0生成量的比例很小;第三种燃料N0,它是由燃料中所含的化 学接合氮所产生的。因为燃料中氮原子的接合能较小,所以在水泥窑系统相对较低温的分 解炉内产生的燃料N〇x较多;第四种生料 N〇x,它是由窑喂料中含氮的化合物分解后而形成 的NOx。在窑废气中N02 -般仅占N0+N02总量的5%以下,N0则占总量的95%以上。国内 运行的干法水泥窑NOx排放浓度大约在600?1400mg/Nm 3左右。
[0004] 本发明的目的在于克服现有技术不足,提供一种新一代高产节能无氨脱硝集成一 体化的高效水泥熟料煅烧方法及装置,使用该装置的工艺煅烧水泥熟料,可大幅降低NOx 排放量,氮氧化物《300ppm,与此同时大幅提高产量、热效率高、煤种适应性广、降低生产成 本。 [0005] 本发明是这样实现的:高产节能无氨脱硝一体化的水泥熟料煅烧新方法及装置由 回转窑主燃烧区1、强力还原区2、三次风管4、再燃烧区5、分解炉6、下料管7、C 4级旋风筒 8、(:5级旋风筒9及缩口环10组成; 其中回转窑1与强力还原区2相连,强力还原区上部与三次风管4连接,形成再燃烧区 5, C4级旋风筒8与下料管7上装有热生料分料阀,热生料分料阀连接上下两根料管,通过对 上下料管分料调节,再燃烧区5与分解炉6相连,在分解炉6内煤粉与风进一步混合、达到 完全燃烧, 当不用分料阀时,设置好(;下料管置燃烧区的高度h,相当于入再燃烧区热生料的平均 高度不同,则再燃烧区温度也不同,最终使生料达到最大的分解,再通过C5级旋风筒9进入 回转窑内煅烧成熟料。
[0006] 使用由回转窑主燃烧区1、强力还原区2、三次风管4、再燃烧区5、分解炉6、下料管 7、C 4级旋风筒8、C5级旋风筒9及缩口环10组成的装置, 且回转窑内的主燃烧区1与再燃烧区5用煤比例在20:80-40:60,煤由强力还原区2全 部喷入主燃烧区产生的980°C?1KKTC烟气中,形成强力还原区2,煤在此区内分解出大量 的CO、CHi、H2、HCN和固定碳等还原剂,将窑内产生的NOx还原成队气; 煤在强力还原区中同时还被预热,并与三次风热空气混合后快速着火燃烧,调节分料 阀(或无调节阀时需调整好C4下料点高度h)将温度控制为850°C?1100°C,着火的煤粉、 空气与生料通过一缩口环10,进入分解炉,而后进入C 5旋风筒9经分离后物料入窑。
[0007] 所述的强力还原区2是由CaC03分解用煤全部从三次风管与窑尾烟室缩口之间的 位置喂入而形成。
[0008] 所述的四级筒下料管为单管时:对分解炉下料点位于三次风管之上,高于三次风 管0.5米以上。
[0009] 所述的四级筒下料管为上下两管时,上管位置可在缩口环10之上或之下。
[0010] 本发明具有以下效果: (1)在不增加成本,增强水泥煅烧性能的前提下,N0X排放浓度大幅度降低,大大减少了 对空气的污染,有利于环境保护。
[0011] (2)分解炉燃尽率高、热效率高,在降低N0X排放的同时大幅降低煤耗及电耗; (3) 因为实现了煤的强化燃烧,可使窑产量大幅提高(20%以上); (4) 由于燃烧效率的有效提高,使得分解炉对煤种的适应性得到很大的增强,特别是可 以使用低劣煤及挥发很低的煤种,因而可降低水泥熟料的生产成本。
[0012] 下面结合附图及
[0013] 图1是脱硝技术原理图。
[0014] 图2是回转窑头与窑尾温差示意图。
[0015] 图3是本发明装置(不带分料阀)的原理图。
[0016] 图4是本发明装置(带分料阀)的原理图。
[0017] 图5是回转窑热平衡示意图。
[0018] 图6为图4装置(带分料阀)的结构示意图。
[0019] 图7为图5装置(不带分料阀)的结构示意图。
[0020] 图8为本发明装置(带分料阀)的结构示意图。
【具体实施方式】
[0021] 本发明装置由回转窑主燃烧区1、强力还原区2、三次风管4、再燃烧区5、分解炉6、 下料管7、C 4级旋风筒8、C5级旋风筒9及缩口环10组成; 其中回转窑1与强力还原区2相连,强力还原区上部与三次风管4连接,形成再燃烧区 5, C4级旋风筒8与下料管7上装有热生料分料阀,热生料分料阀连接上下两根料管,通过对 上下料管分料调节,可控制再燃烧区5的温度,再燃烧区5与分解炉6通过缩口环10相连, 在分解炉6内煤粉与风进一步混合、达到完全燃烧。
[0022] 当不用分料阀时,设置好(;下料管置燃烧区的高度h,使入再燃烧区热生料的平均 高度不同,其温度也不同,达到控制温度的目的,最终使生料达到最大的分解,再通过分解 炉6及C5级旋风筒9进入回转窑内煅烧成熟料。
[0023] 本发明的无氨脱硝的水泥熟料煅烧方法,使用由回转窑主燃烧区1、强力还原区 2、三次风管4、再燃烧区5、分解炉6、下料管7、C4级旋风筒8、C5级旋风筒9及缩口环10组 成的装置, 且回转窑内的主燃烧区1与再燃烧区5用煤比例在20:80-40:60,煤在强力还原区2全 部喷入由主燃烧区产生的980°C?1KKTC烟气中,形成强力还原区2,煤在此区内分解出大 量的C0、CHi、H2、HCN和固定碳还原剂,将窑内产生的NOx还原成队气; 煤在强力还原区中同时还被预热,并与三次风热空气混合后快速着火燃烧,调节分料 阀或无调节阀时需调整好C4下料点高度h将温度控制为850°C?1000°C,着火的煤粉、空 气与生料通过一缩口环10,进入分解炉而后进入C 5旋风筒9经分离后物料入窑。
[0024] 所述的强力还原区2是由分解炉用煤全部从三次风管与窑尾烟室缩口之间的位 置喂入而形成。
[0025] 所述的四级筒下料管为单管时:对分解炉下料点位于三次风管之上,高于三次风 管0.5米以上。
[0026] 所述的四级筒下料管为上下两管,上管位置可在缩口环10之上或之下。
[0027] 图3和图4中,这种氮氧化物高效阻控的高产、节能的水泥熟料煅烧工艺及装置, 由回转窑主燃烧区1、强力还原区2、再燃烧区5、下料管7 (及C4级旋风筒8)及分解炉6等 组成。回转窑1与强力还原区2相连,强力还原区上部与三次风管4连接,形成再燃烧区5, 再燃烧区的温度是可控的,控制由c4级旋风筒下料管构成,C 4级旋风筒8下料管7上装有 热生料分料阀(也可简化不用分料阀),热生料分料阀连接上下两根料管,通过对上下料管 分料调节(当不用分料阀时,可设置好C 4下料管入再燃烧区的高度h),相当于入再燃烧区热 生料的平均高度不同,由于生料受热分解将吸收大量的热,热生料平均高度不同,意味着再 燃烧区的温度将随之而变化,达到温度可控的目的。再燃烧区与分解炉6相连,在分解炉内 煤粉与风进一步混合、达到完全燃烧,最终使生料达到最大的分解,再通过C 5级旋风筒9进 入回转窑内煅烧成熟料。
[0028] 本发明新一代氮氧化物高效阻控性的高产、节能的水泥熟料煅烧工艺,主燃烧区1 (回转窑内)与再燃烧区5用煤比例在20:80-40:60,煤在强力还原区2全部(但可多点喷)喷 入由主燃烧区产生的980°C?1100°C烟气中,形成强力还原区2,煤在此区内分解出大量的 C0、CHi、H2、HCN和固定碳等还原剂,将窑内产生的NOx还原成队气。煤在强力还原区中同 时还被预热,并与三次风热空气混合后快速着火燃烧,因而具有了强制着火与燃烧的作用。 通过调节分料阀(或无调节阀时需调整好C 4下料点高度)将温度控制为850°C?1000°C,以 有利于燃烧区及分解炉的煅烧安全性以及防止NOx的二次形成。着火的煤粉、空气与生料 通过一缩口环10使他们进一步混合均匀并有利于更充分的燃烧与传热,进入分解炉后生 料分解完成,而后进入C 5旋风筒9经分离后物料入窑。
[0029] 本发明所提供一种新一代高产、节能及无氨脱硝集成一体化的高效水泥熟料煅烧 工艺及装置,使用该装置的工艺煅烧水泥熟料,可大幅降低NOx排放量,氮氧化物《300ppm, 与此同时大幅提高产量、热效率高、煤种适应性广、降低生产成本。
[0030] 在我国,现行水泥窑脱硝工艺中,新型干法水泥回转窑上常用的NOx控制技术主 要有以下几种:SNCR (非选择性催化还原)、SCR (选择性催化还原)、分级燃烧技术、空气分 级燃烧+SCR以及低氮燃烧器技术。
[0031] 低NOx燃烧器 目前在国内已经有广泛应用,但其效果受窑工况影响较大,一般NOx的排放量不能达 到预期效果或效果不明显。
[0032] SCR 法 SCR法采用选择性催化还原法,具有脱氮效率高的优势,在电厂锅炉脱氮被广泛应用。
[0033] 技术原理如图1。理想状态下,脱硝率达90% ;实际上由于受技术条件的限制,国内 采用该技术的水泥企业,脱硝率在50%左右。但由于SCR操作300°C?400°C温度和含尘量 的特殊要求,在国内外水泥生产线上极少使用,主要原因为:(1)出窑的烟气通常用于余热 发电,出余热发电系统的烟气温度无法满足SCR的温度要求;(2)窑尾框架周边基本上没 有布置SCR催化剂框架的空间;(3)出窑的烟气中高浓度粉尘及其Na 20、K20、CaO、S02等有 害元素易造成催化剂破损和失效;(4) 一次性投资大;烟气通过催化剂的阻力增大了窑系 统的阻力;(5)催化剂每三年需要更换,运行成本高。
[0034] 分级燃烧技术 分级燃烧脱氮的基本原理是在分解炉内建立还原燃烧区,将原分解炉用煤的一部分均 布到该区域内,使其缺氧燃烧(第一级燃烧区域内空气过剩系数小于1)以便产生CO、CH4、 H2、HCN和固定碳等还原剂。这些还原剂与窑尾烟气中的NOx发生反应,将NOx还原成N2 等无污染的惰性气体。此外,煤粉在缺氧条件下燃烧也抑制了自身燃料型NOx产生,从而实 现水泥生产过程中的NOx减排。主要化学反应如下: 2C0 +2 N0 - N2+ 2C02 NH+NH - N2+H2 2H2+2N0 - N2+2H20 优点:无运行成本,对水泥正常生产无不利影响;无二次污染,不额外产生固体或液体 的污染物或副产物生成; 不足:对水泥生产及产量有影响。NOx脱除率低,为20?30%。
[0035] 脱硝技术 SNCR (选择性非催化还原)技术在旋窑水泥窑脱硝系统上广泛的运用。该法将氨水(质 量浓度20%?25%)或尿素溶液(质量浓度309T50%)通过雾化喷射系统直接喷入分解炉合 适温度区域(850?1050°〇,雾化后的氨与NOx (N0、N02等混合物)进行选择性非催化还原 反应,将NOx转化成无污染的队。当反应区温度过低时,反应效率会降低;当反应区温度过 高时,氨会直接被氧化成队和N0。化学反应方程式如下: 4N0+4NH3+02 - 4N2+6H20 2N02+4NH3+02 - 3N2+6H20 SNCR法的脱硝效率为50%?70%,低于选择性催化还原法(SCR)的脱硝效率(80%? 90%),但SNCR法的费用(包括设备费用和操作费用)只有SCR法的1/5左右。实际上由于 上述三个条件不能同时满足,脱硝效率低于40%。
[0036] SNCR法需要氨水或者尿素作为还原剂,氨水属于毒性化学易燃易爆危险品,其毒 性可致人死亡,氨水贮罐成为水泥厂内一大安全隐患。而且运行成本高,使水泥成本提高 3-6元/吨。
[0037] 发明人经过长期的研究发现,制约普通新型干法窑产量进一步提高的主要原因是 回转窑窑尾存在一传热瓶颈。即:一方面,窑尾温度在850°C-110(TC度的范围内(仅占窑 长1/5)物料需热量约为余下的大部分回转窑(1100°C -1450°C温度内,占窑长4/5)物料总 吸热量的10倍。另一方面,窑尾传热效率极低(窑尾气固温差较低),因而严重影响窑产量。 如图2所示。
[0038] 设想若将回转窑低温区(< 1000°C区域)在具有悬浮状态下的分解炉内完成,使入 窑物料分解率和温度皆有所提高,则回转窑内所需传热量将大幅减少,窑头用煤与窑尾分 解炉用煤比例将发生较大变化,因而有效地克服了回转窑传热瓶颈。从以下热平衡图5可 见,新型干法水泥产量及各项经济技术指标将发生大幅度变化。
[0039] 假定原预分解回转窑窑内烧煤量不变,以原来的产量为基准,令m为原窑产量的 倍数,则可建立如下回转窑的热平衡: 热收入: 1入窑物料带入的热:Q物入=m ? Cm ? 1000°C =1090 ? m kj/kg熟料 2窑头二次风带入的热:Q二次风=577. 33 kj/kg熟料 3窑内烧成带熟料温度从1450°C下降到1300°C所提供的热: Q冷却带=1. 091 X 150°C?m=163. 6?m kj/kg熟料4煤燃烧的放热:Q煤=3200 X 0? 4=1380 kj/kg熟料 热支出: 1 烟气带走热: Q烟气=1150°C XL 9X0. 483=1055. 36 (kj/kg熟料 2 熟料带走热: Q熟料=1300X 1. 091?m=1418. 3?m kj/kg熟料 3物料在窑内化学反应及升温吸热:Q反应=153. 1 kj/kg熟料 4窑筒体表面散热:Q散热=150 kj/kg熟料故:1091m+577. 33+163. 65m+1280=10 55.36+1418. 3m+153. lm+150 解此方程后得:m=2. 06 这意味着,若分解炉入窑物料已完全分解,且温度提高到l〇〇〇°C时,理论计算窑的产量 可较普通预分解窑提高一倍左右。
[0040] 这一情况与预热器窑(SP)和预分解窑(NSP)的进化关系十分类似。预分解窑因在 窑尾加了"第二把火"将CaC0 3大部分分解,同直径的窑产量提高一倍多。现在我们将在窑 尾加入"第三把火"使物料进一步分解和预热,计算得出同直径的窑产量也可提高一倍。
[0041] 其次NOx排放将大幅减少。原因就在于窑头高温燃煤量大幅度减少,从而减少了 NOx的生成。
[0042] 从预分解窑总体结构来看,水泥熟料烧成用煤已被分为两部分,一部分是高温煅 烧用煤(窑头),一部分是低温CaC03*解用煤,约860°C -950°C (窑尾分解炉内)。现行的 分级燃烧(可以称为局部分级燃烧)的特点是,将分解炉的用煤(或用风)进一步分级,其效 果十分有限。然而从整体的角度来看,水泥熟料煅烧系统本身已经构成了一个系统整体的 分级燃烧,即由窑头高温煅烧用煤构成主燃烧,形成NOx,窑尾分解用煤构成再燃烧,可消除 NOx。也就是说由窑头高温煅烧形成的NOx可以用窑尾煤在合适的温度及气氛下有效还原。 从这一思路来看,窑头用煤量越少,窑尾用煤量越多,则越有利于NOx还原和脱除。
[0043] 再其次,本技术可大幅节煤,且能适应煤质变化,可解决低劣及高硫煤资源在新型 干法水泥工业中的应用问题。这是因为本技术运用了强化煅烧方法,能在操作运行中灵活 调节和控制燃烧状态,燃烧效率高,结皮堵塞几率很低。
高产节能无氨脱硝一体化的水泥熟料煅烧新方法及装置制造方法
- 专利详情
- 全文pdf
- 权力要求
- 说明书
- 法律状态
查看更多专利详情
下载专利文献
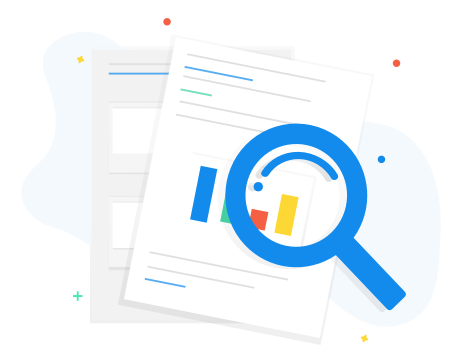
下载专利
同类推荐
-
张声军张声军王善祝, 王明刘杰, 吕春叶强叶强
您可能感兴趣的专利
-
裴满景张雷谭纪林秦健, 姜青平秦健, 姜青平
专利相关信息
-
阿布都艾则孜·阿布来提, 艾力江·如苏力阿布都艾则孜·阿布来提, 艾力江·如苏力阿布都艾则孜·阿布来提, 艾力江·如苏力徐鑫, 刘小康徐鑫, 刘小康徐鑫, 刘小康徐鑫, 刘小康