专利名称:陶瓷板的烧制方法和制造方法 以前,作为含铅的陶瓷,已知以钛酸铅、钛酸锆酸铅为主要成分的压电陶瓷。另外,该压电陶瓷应用于陶瓷振子、陶瓷滤波器、压电蜂鸣器、压电传感器、压电致动器等各种制品。在用于这些制品的压电陶瓷中,有由压电材料构成的基板(压电陶瓷板)、或近年来积极研究的、交互层叠该基板与内部电极层的层叠体等。这里,简单说明制造压电陶瓷的一般步骤。首先,精制由氧化物、碳酸盐等化合物合成的压电陶瓷粉体,作为出发原料。之后,向该压电陶瓷粉体中加入粘合剂等,进行成形,形成陶瓷板。对形成的陶瓷板实施脱脂(脱粘合剂)处理,并烧制脱脂后的陶瓷板,得到烧结体。研磨得到的烧结体,同时,切断成规定尺寸,从而得到上述压电陶瓷板。另外,压电陶瓷的层叠体通过与在表面涂布由烧制变为内部电极层的电极膏的陶瓷板重叠多块后进行烧制得到。因为压电陶瓷如上所述含有铅,所以在烧制时铅蒸发。尤其是在900度以上的高温下烧制时,铅的蒸发显著。因此,为了抑制铅的蒸发,一般的烧制方法是将脱脂后的陶瓷板装载在载置定位器上,并将该载置定位器设置在密闭的匣钵内进行烧制。另外,作为抑制铅的蒸发的另一方法,已知将氧化铅粉体与载置定位器一起放入匣钵内进行烧制的方法。近年来,随着使用压电陶瓷的制品的小型化,要求压电陶瓷的小型化和薄型化。就压电陶瓷的小型化而言,通过切割等将烧结体切断成规定尺寸,由此可较容易实现。另一方面,在压电陶瓷的薄型化中存在以下问题。即,虽可通过研磨烧结体以达到一定程度的薄度,但在研磨厚的烧结体的情况下,需要大量的手续和时间,并且在研磨薄的烧结体的情况下,仅施加小的压力也会产生断裂。因此,考虑使用薄陶瓷板来求得不必研磨的烧结体,但在烧制薄的陶瓷板的情况下,由于烧制收缩引起的变形,产生翘曲。该翘曲在方形的陶瓷板的边缘部显著。因此,在不研磨来利用压电陶瓷的情况下,必需去除翘曲大的边缘部,导致合格率降低及成本增加。因此,在例如日本专利公开昭62-128973号公报(下面称为专利文献1)、日本专利公开平1-282157号公报(下面称为专利文献2)、日本专利公开平8-91944号公报(下面称为专利文献3)、日本专利公开平10-324574号公报(下面称为专利文献4)中公开了抑制烧结体翘曲的技术。专利文献1中公开的技术是如下方法,即伴随支柱部件的烧制收缩,在烧制过程中,成形体上的载置定位器按压陶瓷板,由此抑制烧制时的翘曲。专利文献2、3和4中示出通过抑制不均匀加热来抑制烧结体翘曲的烧制方法。即,专利文献2中公开的方法是在陶瓷材料中加入有机粘合剂等进行生片(green sheet)的成形后,使生片装载在载置定位器上,在生片整体由与载置定位器相同材质的氧化铝类、莫来石类等陶瓷构成的框包围的状态下放入适当加热炉中,进行生片的粘合剂去除及烧制,降低陶瓷板的翘曲。
专利文献3中公开的技术是由致密氧化镁或致密氧化铝的陶瓷隔板使陶瓷板与其上的载置定位器的间隙变窄,由此抑制烧制引起的陶瓷板的尺寸不均和翘曲量。
在专利文献4记载的烧制方法中,在对面的载置定位器下侧的载置定位器上装载陶瓷板,由具有与陶瓷板相同收缩特性的支柱将上侧载置定位器支撑在下侧载置定位器上,以在陶瓷板与上侧载置定位器之间形成规定间隔的间隙。若在该状态下进行烧制,则支柱也与陶瓷板一起收缩,所以可将陶瓷板与上侧载置定位器之间的间隙保持在规定间隔。
但上,上述现有陶瓷板的烧制方法存在以下问题。
即,在专利文献1公开的技术中,通过载置定位器按压陶瓷板,由于对陶瓷板施加负荷,所以会产生分裂,另外,在支柱部件的烧制速度不均匀的情况下,制作出形状不好的烧结体。
在专利文献2公开的现有技术的方法中,陶瓷板的材质会产生以下问题,所以有时不能消除基板的翘曲或曲折。
即,在进行生片的粘合剂去除处理后,期望完全去除生片材中的粘合剂或溶剂等,但实际上生片材中残留部分粘合剂作为碳素成分。该残留的碳素成分在作为后工序的生片烧制时气化,但有时在此时还原生片材中的氧化物。此时,由于元素而在还原的时刻产生蒸发,所以脱离生片材,结果,基板组成的一部分与期望的不同。这种缺陷在例如生片材中含有ZnO的情况下显著,这构成基板翘曲等的原因。
另外,因为粘合剂去除时产生的气体中在生片背面(载置定位器一侧的面)产生的气体的排出性差,所以当生片薄时,生片从载置定位器抬起,生片错位移动,因此生片从载置定位器脱落,或在生片背面产生瑕疵或变形。
并且,在专利文献2和3公开的烧制方法中,因为不能保持陶瓷板内部及陶瓷板周围的铅气氛气均匀,所以烧结体中产生翘曲。
另外,在专利文献4公开的烧制方法中,因为相对的载置定位器间的陶瓷板的周围部开放,所以陶瓷板与上侧载置定位器之间的气氛气的浓度在烧制中不被均匀保持,陶瓷板的收缩在不同部位变得不均匀,担心在烧制后的陶瓷板中产生翘曲或曲折。陶瓷板的厚度越薄型化,该问题越显著。
另外,随着陶瓷板烧制的进行,支撑载置定位器的多个支柱部件进行烧制收缩,但难以均匀且正确地控制该支柱部件的收缩。尤其是在经支柱部件装载多段载置定位器的情况下,支撑位于下方的载置定位器的支柱部件支撑多个载置定位器,所以收缩的控制变得更困难。
由此,由多个支柱部件支撑的载置定位器倾斜,产生载置定位器与陶瓷板接触的情况。这样,在载置定位器与陶瓷板接触不变地执行烧制的情况下,产生通过陶瓷板烧制得到的烧结体会烧附在载置定位器上等缺陷,这种烧结体在从载置定位器上剥离时会破损,或产生形状不良,所以不适于用于压电陶瓷制品的烧结体。
因此,鉴于上述问题,本发明的目的在于提供①可防止烧制后的陶瓷板中产生翘曲或曲折的陶瓷板烧制方法、②在抑制翘曲等的同时、可防止烧制时载置定位器与陶瓷板接触的情况的陶瓷板烧制方法、和③在确实降低陶瓷板的翘曲等的同时、可防止处理中的陶瓷板相对载置定位器错位移动的陶瓷板的制造方法。
为了实现上述目的①,本发明的陶瓷板的烧制方法是在第一保持部件与第二保持部件之间配置陶瓷板后进行烧制的陶瓷板的烧制方法,其特征在于用由与陶瓷板大致相同组成的陶瓷材料所形成的包围部件包围陶瓷板在第一保持部件与第二保持部件之间的周围部,烧制陶瓷板。
在该陶瓷板的烧制方法中,第一保持部件与第二保持部件之间的陶瓷板的周围部由与陶瓷板大致相同组成的陶瓷材料所形成的包围部件包围,所以配置陶瓷板的气氛气中的浓度在烧制中保持均匀。因此,烧制引起的陶瓷板的收缩被均匀化,可防止烧制后的陶瓷板中产生翘曲或曲折。
另外,所谓陶瓷板除陶瓷片的单板外,也包含层叠多个陶瓷片所构成的板状的层叠体,还包含将陶瓷片作为基板来形成电极等。
另外,根据本发明的陶瓷板的烧制方法在形成陶瓷板的陶瓷材料包含含有铅的化合物的情况下特别有效。虽然钛酸铅、钛酸锆酸铅等含有铅的化合物中的铅通过烧制易蒸发,但因为包围部件由与陶瓷板大致相同组成的陶瓷材料所形成,所以在配置陶瓷板的气氛气中,从包围部件排放含有铅的化合物中的铅。由此,抑制含有铅的化合物中的铅从陶瓷板蒸发,进而配置陶瓷板的气氛气中的铅的浓度在烧制中保持均匀。因此,烧制引起的陶瓷板的收缩被恒定化,可防止烧制后的陶瓷板中产生翘曲或曲折。
另外,优选将陶瓷板装载在第一保持部件上,在陶瓷板与第二保持部件之间设置陶瓷板厚度以下的间隙。这样,若在陶瓷板与第二保持部件之间设置陶瓷板厚度以下的间隙并进行烧制,则促进配置陶瓷板的气氛气的浓度的均匀化,所以可进一步抑制陶瓷板中产生翘曲或曲折。
另外,优选包围部件具有与陶瓷板的厚度大致相同的厚度。若在这种状态下进行烧制,则与上述一样,促进配置陶瓷板后的气氛气的浓度的均匀化,可进一步抑制陶瓷板中产生翘曲或曲折。进而当第二保持部件靠近陶瓷板时,由于包围部件不会成为障碍,所以在将陶瓷板与第二保持部件之间的间隙设定在陶瓷板的厚度以下的情况下特别有效。
另外,优选距陶瓷板规定距离来配置包围部件。通过在陶瓷板与包围部件之间保持规定距离,可调节配置陶瓷板的气氛气的浓度,以对应于陶瓷板的厚度或组成等来抑制该陶瓷板中的翘曲或曲折的产生。
另外,优选在陶瓷板的周围部配置多个保持第一保持部件与第二保持部件的间隙的隔板,在相邻的隔板之间配置包围部件。这样,通过在相邻隔板间配置包围部件,可实现保持部件的小型化,进而实现空间节省化。
另外,优选从陶瓷原料中取出陶瓷板,包围部件由取出陶瓷板后的陶瓷原料的剩余部分形成。例如,当通过冲压等从生片的单板或生片的层叠体等陶瓷原料中取出陶瓷板时,若由陶瓷原料的剩余部分形成包围部件,则可高效形成包含与陶瓷板大致相同组成的陶瓷材料的包围部件。进而,通过利用一般成为废料的陶瓷原料的剩余部分,可实现陶瓷板烧制所需的成本低廉化。
并且,为了实现上述目的②,根据本发明的另一陶瓷板的烧制方法的特征在于具有如下步骤在第一载置定位器上装载陶瓷板、多个支柱部件、和隔板,该隔板在烧制陶瓷板的烧制过程前的高度比该烧制过程前的支柱部件的高度低,并且经过烧制过程后的高度比经过烧制过程后的陶瓷板的高度高;在多个支柱部件上装载覆盖陶瓷板和隔板的第二载置定位器;和烧制夹在第一和第二载置定位器之间的陶瓷板。
在该陶瓷板的烧制方法中,在第一载置定位器与第二载置定位器之间夹入陶瓷板与隔板的状态下进行烧制。另外,经过该烧制过程后的该隔板的高度比经过烧制过程后的陶瓷板的高度高。因此,例如即使在烧制过程中多个支柱部件收缩的情况下,或这些支柱部件不均匀收缩、第二载置定位器倾斜的情况下,通过隔板支撑第二载置定位器的至少一部分,有意抑制第二载置定位器与陶瓷板的接触。另外,陶瓷板中除陶瓷片的单板外,还包含层叠多个陶瓷片所构成的板状的层叠体、或在表面形成有电极等的陶瓷片等。
另外,优选在第一载置定位器上装载多个隔板。此时,可更确实地抑制第二载置定位器与陶瓷板的接触。
另外,优选经过烧制过程后的多个隔板的高度相同。此时,在烧制过程中,即使在支柱部件全部高度比陶瓷板的高度低的情况下,也因为多个隔板以与陶瓷板平行的状态来支撑第二载置定位器,所以可有意抑制第二载置定位器与陶瓷板的接触。
另外,优选将多个隔板配置在夹持陶瓷板的位置上。优选在陶瓷板沿一个方向延伸的情况下,两个隔板沿陶瓷板的长方向排列,以夹持陶瓷。并且,优选陶瓷板含铅。
另外,优选烧制过程前的隔板的高度比烧制过程前的陶瓷板的高度低。此时,可使烧制过程前的第二载置定位器的高度位置靠近至不接触陶瓷板的极限位置,可使第二载置定位器与陶瓷板之间的间隙最小。因此,可实现烧制过程中陶瓷板的周围温度及气氛气的均匀化。
另外,优选在烧制陶瓷板时,在包围部件包围陶瓷板周围的状态下烧制该陶瓷板。此时,可实现烧制过程中陶瓷板的周围温度及气氛气的均匀化。
另外,优选还具有如下步骤,即在位于陶瓷板上的第二载置定位器上还装载陶瓷板、支柱部件和隔板,在该支柱部件上装载新的载置定位器,在重复多次该步骤后,烧制多个陶瓷板。这样,在为了一次烧制多个陶瓷板而重叠多段载置定位器的情况下,因为对位于下方的支柱部件施加较大的负荷,所以这种支柱部件中易产生预定量以上的收缩。因此,虽变为载置定位器易接触陶瓷板的状况,但因为在两个载置定位器之间夹入上述隔板,所以有意抑制陶瓷板与载置定位器的接触。
另外,优选支柱部件由在烧制过程中的收缩特性与陶瓷板的材料大致相同的材料构成。此时,因为支柱部件的收缩动作一定程度跟踪于陶瓷板的收缩动作,所以在一定程度保持陶瓷板与第二载置定位器之间的距离的状态下,可执行陶瓷板的烧制。因此,在烧制过程前,通过使陶瓷板与第二载置定位器一定程序靠近,可有意实现烧制过程中陶瓷板的周围温度及气氛气的均匀化。
另外,优选支柱部件由与陶瓷板的材料相同的材料构成。此时,支柱部件的收缩动作与陶瓷板的收缩动作大致一致。因此,可进一步有意实现烧制过程中陶瓷板的周围温度及气氛气的均匀化。
并且,为了实现上述目的③,根据本发明的陶瓷板的制造方法是烧制陶瓷生片材来制造陶瓷板,其特征在于包含如下工序准备载置定位器,该载置定位器具有形成使在装载有陶瓷生片材的状态下加热陶瓷生片材时产生的物质从陶瓷生片材中排放出的物质排放用凹凸部的装载面;形成含有粘合剂的所述陶瓷生片材;将陶瓷生片材装载在载置定位器的装载面上,去除陶瓷生片材的粘合剂;和在去除陶瓷生片材的粘合剂后,将陶瓷生片材装载在载置定位器的装载面上不动,烧制陶瓷生片材。
这样,通过使用在装载面中形成物质排放用凹凸部的载置定位器,进行陶瓷生片材的粘合剂去除及烧制,在使陶瓷生片材装载在载置定位器的装载面上的状态下,载置定位器与陶瓷生片材的接触面积变小。因此,在陶瓷生片材的粘合剂去除工序中,粘合剂的熔渣易从陶瓷生片材的背面(载置定位器侧的面)排放,所谓的粘合剂去除性好。因此,在粘合剂去除后残留在陶瓷生片材中的碳素成分减少。因此,在陶瓷生片材的烧制工序中,抑制残留碳素气化时还原陶瓷生片材中的氧化物所产生的元素的蒸发。由此,烧制得到的陶瓷板的组成的均匀性变好,所以可确实降低陶瓷板的翘曲等。
另外,因为在陶瓷生片材的粘合剂去除工序中,在陶瓷生片材的背面产生的气体的排出性也因物质排放用凹凸部而变好,所以抑制陶瓷生片材从载置定位器上抬起。并且,在将装载陶瓷生片材的载置定位器容纳在密闭炉内进行陶瓷生片材的烧制的情况下,载置定位器与陶瓷生片材的温度速度差因物质排放用凹凸部而变小,所以防止存在于炉内的气体被卷入陶瓷生片材的背面使得陶瓷生片材从载置定位器上抬起。因此,可防止在陶瓷生片材的粘合剂去除及烧制时,陶瓷生片材相对载置定位器错位移动。
优选将形成物质排放用凹凸部以使装载面的中心线平均粗糙度Ra为1-20微米的载置定位器作为载置定位器。通过在载置定位器的装载面中形成这种物质排放用凹凸部,可使陶瓷生片材中产生的粘合剂的熔渣或气体从载置定位器侧有效排放。另外,可防止陶瓷生片材烧制时,物质排放用凹凸部的模式转录到陶瓷生片材的背面。因此,在制品化烧制得到的陶瓷地,不必对陶瓷板实施研磨等机械加工。
此时,优选还包含如下工序,即不对由陶瓷生片材烧制得到的陶瓷板实施机械加工,在陶瓷板中形成外部电极。这样,当在陶瓷板中形成外部电极时,因为不对陶瓷板进行研磨加工等即可完成,所以可实现陶瓷板的制造处理的简化。
另外,优选使用由具有形成物质排放用凹凸部的凹凸的模具来制作的载置定位器来作为载置定位器。由此,与通过例如喷砂加工或研磨粉的研磨来使载置定位器的装载面变粗糙的情况相比,可容易且廉价制作具有凹凸部的载置定位器。另外,因为不必如喷砂加工那样对载置定位器实施机械加工,所以在保持载置定位器高强度的同时,载置定位器的装载面中不会残留加工屑等。
并且,优选陶瓷生片材由含铅的材料形成,在将承载陶瓷生片材的载置定位器配置在密闭炉内的状态下,烧制陶瓷生片材。由此,可容易得到含铅的压电陶瓷板。另外,通过在密闭炉内烧制陶瓷生片材,可抑制铅的蒸发。
发明效果如上所述,根据本发明的陶瓷板的烧制方法,可防止烧制后的陶瓷板中产生翘曲或曲折,另外,可防止烧制时载置定位器与陶瓷板接触的情况。
并且,根据本发明的陶瓷板的烧制方法,使用具有形成使装载陶瓷生片材的状态下加热陶瓷生片材时产生的物质从陶瓷生片材排放用的物质排放用凹凸部的装载面的载置定位器,进行陶瓷生片材的粘合剂去除及烧制,所以在可确实降低陶瓷板的翘曲或曲折的同时,可防止处理中的陶瓷板(陶瓷生片材)相对载置定位器错位移动。
图1是根据实施方式1的烧制单元的局部截面正面图。
图2是切掉图1所示烧制单元的一部分的平面图。
图3是表示将图1所示烧制单元容纳在密闭匣钵中的状态的局部截面正面图。
图4是根据实施方式2的烧制单元的局部截面正面图。
图5是切掉图4所示烧制单元的一部分的平面图。
图6是表示多段重叠根据实施方式1或2的烧制单元后容纳在密闭匣钵中的状态的局部截面正面图。
图7是表示根据实施方式3的陶瓷板的烧制方法的图。
图8是表示实施方式3中烧制多段层叠载置定位器的状态图。
图9是表示实施方式3中烧制过程中各要素的状态图。
图10是表示实施方式3中不同形态的载置定位器的图。
图11是表示实施方式3中不同形态的载置定位器的图。
图12是表示通过实施方式4进行陶瓷生片材的粘合剂去除时的状态的平面图。
图13是表示通过实施方式4进行陶瓷生片材的粘合剂去除时的状态的侧面图。
图14是图12和图13所示氧化锆载置定位器的表面放大图。
图15是表示通过实施方式4进行陶瓷生片材的烧制时的状态的垂直方向截面图。
图16是表示通过实施方式4进行陶瓷生片材的烧制时的状态的一部分的水平方向截面图。
图17是表示通过实施方式4最终得到的陶瓷板的立体图。
下面,参照附图来详细说明根据本发明的陶瓷板的烧制方法和陶瓷板的制造方法的最佳实施方式。
(实施方式1)首先,参照图1-图3来说明本发明的实施方式1。
如图1和图2所示,在形成为100mm×100mm的正方形状的致密(气孔率为3%以下,更优选气孔率为1%以下)的氧化锆载置定位器(第一保持部件)1上装载陶瓷板2。因为氧化锆载置定位器1在烧制中与陶瓷板2的反应性低且持久性好,所以优选以8mol%-12mol%的氧化钇(Y2O3)完全稳定化。另外,陶瓷板2是由包含钛酸锆酸铅的压电陶瓷(具体而言是PbTiO3-PbZrO3-Pb(Mg1/3Nb2/3)O3-Pb(Zn1/3Nb2/3)O3等4成分类压电陶瓷)形成的单板,如下制作。
即,通过球磨机湿式混合氧化物或碳酸盐形态的材料,混合后以950度下进行中间烧制。用球磨机湿式粉碎该中间烧制后的材料,准备压电陶瓷粉体。接着,向该压电陶瓷粉体中加入粘合剂或溶剂等进行膏剂化,通过压出成形法成形厚度为0.15mm的生片(陶瓷原料)。压切切断该生片,得到[80mm×80mm,厚度0.15mm]的正方形薄板状陶瓷板2。
将这样制作的陶瓷板2配置在氧化锆载置定位器1的中央,在由此形成的氧化锆载置定位器1的空白部的四个角上装载高度为0.30mm的隔板3。并且,在氧化锆载置定位器1的相邻隔板3、3之间装载棒状的包围部件4。此时,使4个包围部件4的每个离开陶瓷板2的4个侧面2a的每个规定距离。这样,通过在相邻隔板3、3之间配置包围部件4,可实现氧化锆载置定位器1的小型化。另外,优选隔板3由与氧化锆载置定位器1相同的材质构成,但也可由氧化铝或氧化镁等材质构成。另外,隔板3的形状不限于方柱状,例如也可以是圆柱状。另外,各包围部件4由在上述陶瓷板2的制作中、切出陶瓷板2后的生片的剩余部分形成。
之后,将与氧化锆载置定位器1相同形状的氧化锆载置定位器(第二保持部件)5相对氧化锆载置定位器1地装载在隔板3上。由此,在陶瓷板2的上面2b与氧化锆载置定位器5的下面5a之间形成间隔0.15mm的间隙S。
将如此构成的烧制单元100如图3所示容纳在密封匣钵7内进行加热。由此,引起陶瓷板2的烧结反应,得到陶瓷板2的烧结体。另外,烧制温度为1100度,稳定时间为2小时。另外,在陶瓷板2的烧制之前,在将陶瓷板1及各包围部件4装载在氧化锆载置定位器1上的上述规定位置上的状态下,在350度下进行加热,进行陶瓷板1和各包围部件4的粘合剂去除。
在根据本实施方式1的陶瓷板的烧制方法中,因为氧化锆载置定位器1、5间的陶瓷板2的周围部(周围空间)由与陶瓷板2大致相同组成的陶瓷材料构成的包围部件4包围,所以钛酸锆酸铅中的铅从各包围部件4放出到陶瓷板2与氧化锆载置定位器5的间隙S中。由此,抑制钛酸锆酸铅中的铅从陶瓷板2蒸发,进而间隙S中的铅的浓度在烧制中保持均匀。因此,均匀化烧制引起的陶瓷板2的收缩,防止烧制后的陶瓷板2中产生翘曲或曲折。
另外,若使间隙S的间隔在陶瓷板2的厚度以下,则可使烧制后的陶瓷板2的翘曲极小,从下示的实验结果可知。作为主要理由,可例如是由于当使间隙S的间隔在陶瓷板2的厚度以下进行烧制时,促进了间隙S中的铅的浓度的均匀化。
首先,如上所述,当设间隙S的间隔为0.15mm(=陶瓷板2的厚度)时,翘曲量为15.7微米,并且当设间隙S的间隔为0.10mm(<陶瓷板2的厚度)时,翘曲量为15.5微米。相反,当设间隙S的间隔为0.30mm(>陶瓷板2的厚度)时,翘曲量为95.5微米。这样,当设间隙S的间隔为陶瓷板2的厚度以下时,可将翘曲量抑制到6分之1的程度。这里,所谓翘曲量是使用激光式非接触3维形状测定装置测定的陶瓷板2的最大高低差,是对100个陶瓷板2的平均值。
另外,当设间隙S的间隔为0.10mm以下时,正方形的陶瓷板2变形为梯形或平行四边形等,确认若干陶瓷板2中产生分裂或缺口的倾向。因此,优选设间隙S的间隔比0.10mm大。另外,在使用多孔质(气孔率约为15%)的氧化锆载置定位器来替换致密的氧化锆载置定位器1、5的情况下,确认若干翘曲量增加的倾向。
另外,在根据本实施方式1的陶瓷板的烧制方法中,因为包围部件4的高度与陶瓷板2的厚度大致相同,所以在调节隔板3的高度来使氧化锆载置定位器5靠近陶瓷板2的情况下,包围部件4不会成为障碍。
另外,因为各包围部件4离开陶瓷板2的侧面2a规定距离,所以可实现陶瓷板2上的间隙S中铅的浓度的均匀化。并且,通过调节陶瓷板2的侧面2a与包围部件4的距离,可调节间隙S中铅的浓度,以对应于陶瓷板2的厚度和组成等抑制该陶瓷板2中的翘曲或曲折的产生。
并且,因为包围部件4是切出陶瓷板2后的生片的剩余部分,所以可高效形成由与陶瓷板2大致相同组成的陶瓷材料构成的包围部件4。并且,因为利用一般为废料的生片的剩余部分,所以可实现陶瓷板2的烧制中所需的成本低廉化和废料的产生量的降低化。
(实施方式2)下面参照图2-图5来说明本发明的实施方式2。
在根据实施方式2的陶瓷板的烧制方法中,使用布图形成电极的陶瓷片的层叠体作为陶瓷板2。该陶瓷板2通过从施压处理后的生片的层叠体(陶瓷原料)中压切来取出10个,形成为[33mm×12mm、厚度0.375mm]的长方形薄板状。另外,陶瓷板2在下示的烧制后实施极化处理等,变为层叠型压电元件。
如图4和图5所示,将从生片的层叠体中切出的10个陶瓷板2装载在氧化锆载置定位器1上,在氧化锆载置定位器1的中央配置成2行5列的矩阵状。另外,将4个棒状包围部件4装载在氧化锆载置定位器1上,以包围陶瓷板2的集合的周围部。并且,在氧化锆载置定位器1上的空白部的四个角装载高度为0.75mm的隔板3。各包围部件4由切出陶瓷板2后的生片的层叠体剩余部分形成。
之后,将与氧化锆载置定位器1相同形状的氧化锆载置定位器5相对氧化锆载置定位器1地装载在隔板3上。由此,在陶瓷板2的上面2b与氧化锆载置定位器5的下面5a之间形成间隔0.375mm的间隙S。
将如此构成的烧制单元100在350度下脱脂后,与上述实施方式1一样,容纳在密封匣钵7内进行加热。由此,引起陶瓷板2的烧结反应,得到陶瓷板2的烧结体。另外,烧制温度为1100度,稳定时间为2小时。
在根据本实施方式2的陶瓷板的烧制方法中,也与上述实施方式1一样,因为氧化锆载置定位器1、5间的各陶瓷板2的周围部由与陶瓷板2大致相同组成的陶瓷材料构成的包围部件4包围,所以均匀化烧制引起的各陶瓷板2的收缩,防止烧制后的陶瓷板2中产生翘曲或曲折。
另外,基于与实施方式1一样的实验的实验结果如下所示。首先,如上所述,当设间隙S的间隔为0.375mm(=陶瓷板2的厚度)时,翘曲量为13.5微米,并且当设间隙S的间隔为0.10mm(<陶瓷板2的厚度)时,翘曲量为13.3微米。相反,当设间隙S的间隔为0.825mm(>陶瓷板2的厚度)时,翘曲量为92.6微米。这样,当设间隙S的间隔为陶瓷板2的厚度以下时,可将翘曲量抑制到7分之1的程度。
本发明不限于上述实施方式1和2。例如,在实施方式1和2中,包围部件由与陶瓷板大致相同组成的陶瓷材料形成即可,可不是取出陶瓷板后的陶瓷原料的剩余部分。另外,即使由相同组成的陶瓷材料形成包围部件与陶瓷板,也可实现与由大致相同组成的陶瓷材料形成的情况相等或之上的效果。另外,在实施方式1和2中,为由多个包围部件包围陶瓷板的周围部的情况,但也可由环状的包围部件包围陶瓷板的周围部。另外,即使包围部件的高度与陶瓷板的厚度基本上不同(例如即使包围部件的高度比陶瓷板的厚度小),但也可防止烧制后的陶瓷板中产生翘曲或曲折。
并且,如图6所示,也可在密闭匣钵中多段(例如10段)重叠容纳根据实施方式1或2的烧制单元,同时执行多个陶瓷板的烧制。
另外,作为载置定位器(第一、第二保持部件)的材料,不限于实施方式1和2中使用的材料,只要是致密性好、烧制中与陶瓷板的反应性低且持久性好的材料即可。
(实施方式3)正面参照图7-图11来说明本发明的实施方式3。
首先,如图7(a)所示,在正方形平板状的载置定位器10的大致中央装载陶瓷板12。载置定位器10由添加了8mol%-12mol%的氧化钇(Y2O3)的完全稳定化氧化锆构成。载置定位器10是致密性的,其气孔率不足3%,但气孔率优选不足1%。陶瓷板12是由包含钛酸锆酸铅的压电陶瓷(具体而言是PbTiO3、PbZrO3、Pb(Mg1/3Nb2/3)O3、和Pb(Zn1/3Nb2/3)O3等4成分类压电陶瓷)形成的长方形薄板状单板,由与实施方式1记载的方法相同的方法制作。
下面,如图7(b)所示,将支柱部件14装载在载置定位器10的4个角上。该支柱部件由与上述陶瓷板12相同的材料构成,从与陶瓷板12一样制作的生片中切出。该支柱部件14任一一个都具有截面正方形的方柱形状,沿载置定位器10的厚度方向延伸。这样,在支柱部件14由与陶瓷板12的材料相同的材料构成的情况下,在后述的陶瓷板12的烧制过程中,支柱部件14的收缩动作与陶瓷板12的收缩动作一致。另外,支柱部件14的材料未必与陶瓷板12的材料相同,例如可从具有与陶瓷板12的收缩特性相同或相等的收缩特性的其它材料中选择。
之后,如图7(c)所示,在载置定位器10上的陶瓷板12的周围装载4个隔板16。具体而言,在作为接近陶瓷板12的各侧面的位置、对应于各侧面的中央部的位置上分别装载1个隔板16。这4个隔板16的高度相同,该高度比支柱部件14的高度低。另外,隔板16的高度比经过后述烧制过程的陶瓷板12的高度高。另外,隔板16由与上述载置定位器10相同的材料构成,任一截面都具有正方形的方柱形状。
之后,在载置定位器10上装载陶瓷板12、支柱部件14和隔板16后,在400度前后加热,进行陶瓷板12和支柱部件14的脱脂。以上示出在载置定位器上按陶瓷板、支柱部件、隔板的顺序装载的步骤,但装载的顺序可适当变更。
在脱脂处理后,如图7(d)所示,在支柱部件14上装载通过与上述一样的步骤准备的、配置了陶瓷板12、支柱部件14和隔板16的载置定位器10。由装载的该载置定位器10来覆盖配置在下载置定位器10上的陶瓷板12和隔板16。并且,重复数次经支柱部件14装载配置了陶瓷板12、支柱部件14和隔板16的载置定位器10的作业,得到图7(e)所示的多段层叠载置定位器20。
之后,将该多段层叠载置定位器20设置在图8所示匣钵22内,实施烧制处理。这里,图8是表示烧制多段层叠载置定位器20的状态的图。匣钵22由上面开口的壳体部22a和盖部22b构成。在壳体部22a中设置多段层叠载置定位器20后,由盖部22b闭盖进行密闭,并从匣钵外部加热,烧制多段层叠载置定位器20。此时的烧制条件可从烧制陶瓷板的公知烧制条件中适当选择。
下面,参照图9来说明烧制过程中的载置定位器10、陶瓷板12、支柱部件14和隔板16的状态。这里,图9是表示烧制过程中各要素的状态图。另外,如图3所示,为了简化说明,不是示出多段层叠载置定位器20整体,而仅示出2个载置定位器10、10和夹在这些载置定位器10、10之间的要素。另外,为了简化说明,将2个载置定位器10、10中上侧的载置定位器称为上载置定位器10A,下侧的载置定位器10称为下载置定位器10B。
首先,在烧制过程前的状态(参照图9(a))中,支撑上载置定位器10A的4个支柱部件14的高度最高。另外,隔板16的高度比陶瓷板12的高度低,陶瓷板12接近上载置定位器10A。这样,在陶瓷板12接近上载置定位器10A、将陶瓷板12与上载置定位器10A之间的距离d设定得小的情况下,烧制过程中的陶瓷板12的周围的温度和从陶瓷板12蒸发的铅的气氛气被有意均匀化,所以可抑制烧制过程中易产生的陶瓷板12的翘曲。
之后,当开始烧制陶瓷板12时,陶瓷板12和支柱部件14伴随烧制开始收缩。另外,因为隔板16如上所述是与载置定位器10相同的原料,所以实质上未收缩。因此,在支柱部件14的收缩以一定程度进行的时刻,支柱部件14与隔板16的高度相同,另外,比陶瓷板12的高度高(参照图9(b))。另外,如上所述,因为支柱部件14与陶瓷板12从相同生片中切出,所以支柱部件14的收缩动作与陶瓷板12的收缩动作一致。因此,可保持陶瓷板12与上载置定位器10A之间的恒定距离d,有意均匀化陶瓷板12的周围温度和从陶瓷板12蒸发的铅的气氛气。
并且当支柱部件14的收缩动作进行时,代替支柱部件14,隔板16支撑上载置定位器10A(参照图9(c))。之后,虽进行陶瓷板12和支柱部件14的烧制收缩,但上载置定位器10A的高度在烧制过程结束之前都不变化。
如上详细说明的那样,在根据本实施方式的陶瓷板12的烧制方法中,在载置定位器10上装载上述隔板16。该隔板16在陶瓷板12的烧制过程途中,代替收缩的支柱部件14来支撑载置定位器10。因此,即使在4个支柱部件14的收缩动作不均匀的情况下,在载置定位器10的支撑从支柱部件14的支撑替代为隔板16的支撑的时刻,可确实平行地保持上载置定位器10A与下载置定位器10B。因此,在烧制过程中,有意抑制了上载置定位器10A相对下载置定位器10B倾斜、上载置定位器10A与陶瓷板12接触的情况。由此,因为降低了陶瓷板12与载置定位器10的煅烧,所以提高通过烧制陶瓷板12得到的压电陶瓷的生产率。
尤其是在层叠多段层叠载置定位器20的情况下,向位于下方的支柱部件14施加较大的负荷。因此,支柱部件14易陷于比预想的还收缩得多的情况,上述隔板进一步有效作用。
另外,在上述实施方式中,在陶瓷板12的周围配置4个隔板16,但即使在适当增减隔板数量的情况下,因为在烧制过程中隔板可支撑上载置定位器的至少一部分,所以不用说,可有意抑制上载置定位器与陶瓷板接触的情况。另外,在上述实施方式中,多个隔板16的高度全部相同,但即使在多个隔板的高度不同的情况下,因为在烧制过程中隔板可支撑上载置定位器的至少一部分,所以有意抑制上载置定位器与陶瓷板的接触。
并且,经过烧制过程的隔板的高度未必比烧制后的支柱部件14的高度高,也可与烧制后的支柱部件14相同或比其低。此时,隔板在陶瓷板12烧制结束之前不支撑上载置定位器,但通过将这种隔板配置在下载置定位器上,即使万一产生引起上载置定位器与陶瓷板接触的情况的原因的情况下,也可抑制这种情况于未然。
另外,在上述实施方式中,是利用实质上未收缩的隔板的方式,但若烧制过程前的高度比烧制过程前的支柱部件的高度低,且经过烧制过程后的高度比经过烧制过程的陶瓷板的高度高,则也可以是在烧制过程中收缩的隔板。
并且,如图10所示,在1个载置定位器10上装载多个陶瓷板12,一次烧制多个陶瓷板12。图10是表示与上述实施方式不同的形态的载置定位器的图。在图10所示形态中,在载置定位器10上以每列2个、将10个陶瓷板12等间隔排列成5列。另外,每列中,夹持2个陶瓷板12地配置3个隔板16。即,3个隔板16沿陶瓷板12的长方向(图中的X方向)排列,在2个陶瓷板12的中间位置配置1个,在经各陶瓷板12与隔板16对峙的位置中各配置1个。另外,沿陶瓷板12的并列方向(图中的Y方向)配置5组3个这种隔板16。
如图10所示,即使在将多个陶瓷板12配置在载置定位器10上的情况下,也可通过在多个陶瓷板12的周围配置隔板16,有意抑制装载在支柱部件14上的载置定位器与陶瓷板12的接触。
另外,如图11所示,在图10所示的载置定位器10上包围陶瓷板12地配置从与陶瓷板12相同的生片中切出的包围部件22。这里,图11是表示与上述实施方式不同的形态的载置定位器的图。即,在该形态中,在相邻两个支柱部件14之间装载4个方柱状包围部件24,10个陶瓷板12全部由从相同生片中切出的支柱部件14和包围部件24包围。在上述陶瓷板12的烧制过程,从支柱部件14和包围部件24中放出钛酸锆酸铅中的铅。由此,抑制铅从由支柱部件14和包围部件24包围的陶瓷板12中蒸发,并且因为陶瓷板12周围的温度和铅气氛气被均匀保持,所以烧制引起的陶瓷板12的收缩在各区域被均匀化,结果,有意抑制烧制后的陶瓷板12中产生翘曲或曲折的情况。
并且,因为包围部件24是切出陶瓷板12后的生片的剩余部分,所以可高效形成由与陶瓷板12大致相同组成的陶瓷材料构成的包围部件4。并且,因为利用一般为废料的生片的剩余部分,所以可实现陶瓷板12的烧制中所需的成本低廉化和废料的产生量的降低化。
下面,说明根据本发明实施方式3的实施例。
在与上述载置定位器10一样的氧化锆载置定位器(100mm×100mm)上,通过图10所示配置来配置陶瓷板、支柱部件和隔板。另外,准备10组与对该载置定位器实施350度脱脂处理后的载置定位器相同的载置定位器,制作10段层叠载置定位器。
这里,用于本实施例中的陶瓷板是以PbTiO3、PbZrO3、Pb(Mg1/3Nb2/3)O3、和Pb(Zn1/3Nb2/3)O3等4成分类压电陶瓷为主要成分的15mm×35mm的单板,从厚度0.35mm的生片中切出。另外,该陶瓷板在后述的烧制过程后,厚度变为0.29mm。
另外,本实施例中所用的隔板与氧化锆载置定位器的材质相同,大小为4mm×4mm(高度为0.32mm)。并且,支柱部件与上述陶瓷板的材质相同,大小为4mm×5mm,高度选择3种高度(0.4mm、0.45mm、0.55mm)。另外,高度为0.4mm、0.45mm、和0.55mm的支柱部件各个情况下的陶瓷板与上载置定位器的距离为50微米、100微米和200微米。
将以上准备的支柱部件厚度不同的3种层叠载置定位器分别容纳在匣钵内,在1100度下烧制。另外,用激光式的非接触3维形状测定装置测定烧制后的各陶瓷板的翘曲。具体而言,将同一基板中的最大高低差作为翘曲量来测定。结果,支柱部件高度为0.4mm时的翘曲量的最大值为25微米,支柱部件高度为0.45mm时的翘曲量的最大值为30微米,支柱部件高度为0.55mm时的翘曲量的最大值为130微米。另外,烧制后的陶瓷板都未产生破损及形状不好。
因此,准备仅在摘除上述隔板这点上与上述10级层叠载置定位器不同的层叠载置定位器,并在与上述一样的条件下烧制。结果,在35%陶瓷板中产生破损及形状不好。这种不好多见于层叠载置定位器的下方陶瓷板中。另外,在采用与图11所示的包围部件22一样的包围部件的情况下,翘曲量的平均值比任一情况都降低10-20%。
向以PbTiO3、PbZrO3、Pb(Mg1/3Nb2/3)O3、和Pb(Zn1/3Nb2/3)O3等4成分类压电陶瓷为主要成分的压电陶瓷粉体中添加粘合剂等,形成膏状,并用刮粉刀形成规定厚度的陶瓷素材。之后,在该陶瓷素材表面的规定区域中丝网印刷Ag与Pb的混合比为7∶3的内部电极膏。并且,层叠8个这样印刷了电极膏的陶瓷素材,并从层叠方向施压,同时,切割成15mm×35mm的大小,制作多个陶瓷素材的层叠体(陶瓷板)。另外,施压后的各层叠体的厚度为0.35mm,后述的烧制过程后的各层叠体的厚度为0.295mm。
另外,在与实施例1一样的氧化锆载置定位器(100mm×100mm)上,通过图10所示配置,配置层叠体、支柱部件和隔板。另外,准备10组与对该载置定位器实施了350度的脱脂处理相同的载置定位器,并制作10级层叠载置定位器。
这里,用于本实施例的隔板与氧化锆载置定位器的材质相同,大小为4mm×4mm(高度为0.32mm)。并且,支柱部件与上述陶瓷板素材的材质相同,大小为4mm×5mm,高度选择3种高度(0.4mm、0.45mm、0.55mm)。另外,高度为0.4mm、0.45mm、和0.55mm的支柱部件各个情况下的层叠体与上载置定位器的距离为50微米、100微米和200微米。
将以上准备的支柱部件厚度不同的3种层叠载置定位器分别容纳在匣钵内,在1100度下烧制。另外,与实施例1一样,用激光式的非接触3维形状测定装置测定烧制后的各层叠体的翘曲。结果,支柱部件高度为0.4mm时的翘曲量的最大值为20微米,支柱部件高度为0.45mm时的翘曲量的最大值为25微米,支柱部件高度为0.55mm时的翘曲量的最大值为120微米。另外,烧制后的层叠体都未产生破损及形状不好。
因此,准备仅在摘除上述隔板这点上与上述10段层叠载置定位器不同的层叠载置定位器,并在与上述一样的条件下烧制。结果,在40%陶瓷板中产生破损及形状不好。这种不好多见于层叠载置定位器的下方陶瓷板中。另外,在采用与图11所示的包围部件22一样的包围部件的情况下,翘曲量的平均值比任一情况都降低10-20%。
(实施方式4)下面,参照图12-17来说明本发明的实施方式4。
本实施方式制造以钛酸铅或钛酸锆酸铅为主要成分的压电陶瓷板。该压电陶瓷板应用于陶瓷振子、陶瓷滤波器、压电蜂鸣器、压电传感器、压电致动器等各种制品。
在制造这种压电陶瓷板的情况下,首先如图12和图13所示,准备装载片状陶瓷生片材31的氧化锆载置定位器32。期望氧化锆载置定位器32具有气孔率不足3%、优选不足1%的致密性。作为氧化锆载置定位器32的材料,期望使用提高持久性的、例如在氧化锆中添加氧化钇(Y2O3)后稳定化的材料。另外,作为稳定化剂,除Y2O3外,还可使用氧化钙(CaO)、氧化镁(MgO)、氧化铈(CeO2)等。
在氧化锆载置定位器32的装载面上,如图14所示,形成使在装载陶瓷生片材31的状态下加热陶瓷生片材31时在陶瓷生片材31中产生的物质从氧化锆载置定位器32排出用的物质排出用凹凸部33。这里所说的物质是在后述的陶瓷生片材31的去除粘合剂时产生的粘合剂的熔渣或后述的陶瓷生片材31的烧制时产生的气体等。
物质排出用凹凸部33构成为氧化锆载置定位器32的装载面的中心线平均粗糙度Ra优选为1-20微米,更优选为2-6微米。另外,所谓中心线平均粗糙度Ra是JIS B0601中规定的表面粗糙度,是从中心线折叠粗糙度曲线,并用长度除以由该粗糙度曲线与中心线得到的面积的值。
具有这种微小物质排出用凹凸部33的氧化锆载置定位器32使用未图示的模具如下形成。即,首先对使用的模具表面实施凹凸加工,以具有上述中心线平均粗糙度Ra。另外,通过由该模具施压加工由Y2O3等添加剂完全稳定化后的氧化锆粉体,在粉体成形体的表面形成微小的凹凸。之后,通过烧制该粉体成形体,得到具有设置了物质排出用凹凸部33的装载面的氧化锆载置定位器32。另外,必要时向氧化锆粉体中加入粘合剂,进行成形,并在烧制前实施粉体成形体的粘合剂去除。
通过如此使用模具来制作氧化锆载置定位器32,与例如通过投射件进行喷砂加工来使载置定位器的装载面粗糙化的情况相比,可容易且廉价地制成具有微小物质排出用凹凸部33的氧化锆载置定位器32。另外,在粉体成形体的烧制后,不对粉体成形体实施研磨或喷砂等机械加工,所以可防止氧化锆载置定位器32的装载面上粘附加工屑等,或在氧化锆载置定位器32中产生变形。
另外,陶瓷生片材31例如由组成为PbTiO3-PbZrO3-Pb(Zn1/3Nb2/3)O3的3成分类压电陶瓷形成。向这种材料构成的压电陶瓷粉体中加入有机粘合剂或有机溶剂等,进行膏剂化或膏化,通过刮粉刀等进行片成形,得到陶瓷生片材31。陶瓷生片材31由例如重叠形成有内部电极图案的多个片之后的层叠体构成。
接着,如图12和图13所示,将这种多个(这里为10个)陶瓷生片材31装载在氧化锆载置定位器32的装载面上,进行去除陶瓷生片材31中含有的粘合剂、所谓的粘合剂去除(脱脂)。成形时使用的粘合剂在后述的烧制时从陶瓷生片材31气化后产生时,混入烧制气氛气中,导致陶瓷生片材31的烧制不好,所以事先在烧制前进行陶瓷生片材31的粘合剂去除。作为该粘合剂去除处理,例如在400度温度下加热陶瓷生片材31,例如稳定10小时。
接着,将陶瓷生片材31装载在氧化锆载置定位器32的装载面上不动,烧制陶瓷生片材31。具体而言,如图15和图16所示,经柱状氧化锆隔板34重叠装载粘合剂去除处理结束后的陶瓷生片材31的多个氧化锆载置定位器32。将氧化锆隔板34装载在氧化锆载置定位器32上的4个角部。另外,在这些氧化锆载置定位器32的一个上,经氧化锆隔板34重叠未装载陶瓷生片材31的氧化锆载置定位器32A。另外,优选氧化锆载置定位器32A的结构与装载陶瓷生片材31的氧化锆载置定位器32相同。此时,通过改变氧化锆隔板34的长度来调整各氧化锆载置定位器32彼此的间隔。另外,期望氧化锆隔板34由与氧化锆载置定位器32、32A相同的材料形成。
之后,将这样多段层载的氧化锆载置定位器32、32A容纳在密闭的烧制炉35内,烧制各陶瓷生片材31。此时,例如在1050度的温度下加热陶瓷生片材31,例如稳定3小时。因为这样将陶瓷生片材31放入烧制炉35内进行烧制,所以可防止包含在陶瓷生片材31中的铅蒸发。另外,为了确实抑制铅的蒸发,优选将氧化铅粉体放入烧制炉35内。通过进行这种烧制,得到压电陶瓷板。
之后,如图17所示,在烧制后的压电陶瓷板36的上面形成外部电极37。这里,形成于氧化锆载置定位器32的装载面中的物质排出用凹凸部33由于是细小的微小凹凸,所以物质排出用凹凸部33的形状基本上不会转录到压电陶瓷板36的下面。因此,可不对压电陶瓷板36实施研磨等机械加工,在压电陶瓷板36中形成外部电极37。不用说,在压电陶瓷板36中形成外部电极37后,不必对压电陶瓷板36进行研磨等。
此时,在压电陶瓷板36的上面涂布Ag膏,并在该状态下在例如700度下煅烧压电陶瓷板36,由此形成外部电极37。另外,作为外部电极37的材料,除Ag外,可使用Au或Cu等。另外,外部电极37的形成方法除煅烧外,也可使用溅射法或无电解镀敷法等。
但是,在陶瓷生片材31的粘合剂去除工序中,当一部分粘合剂不去除地作为碳素成分残留在陶瓷生片材31中时,在作为后工序的陶瓷生片材31的烧制处理时,残留碳素易气化。此时,残留碳素使陶瓷生片材31中的氧化物(ZnO)还原,此时Zn从陶瓷生片材31中蒸发,所以陶瓷生片材31的组成在陶瓷生片材31的表面侧和背面侧不同。由此,在陶瓷生片材31的表面侧和背面侧,陶瓷生片材31的收缩率变化,结果,会产生压电陶瓷板36的翘曲或曲折等。
为了使陶瓷生片材31的粘合剂去除性变好,考虑使用多孔质的载置定位器。但是,在粘合剂去除后使陶瓷生片材装载在相同多孔质载置定位器上进行烧制的情况下,陶瓷生片材31中的铅(Pb)被吸收到多孔质载置定位器中,难以保证陶瓷生片材31的背面侧(载置定位器侧)的均热性和均气氛气性,引起陶瓷生片材31的烧制不均。结果,即使在未产生压电陶瓷板的翘曲等的情况下,也变为未得到期望特性的基板。
另外,考虑在使用多孔质载置定位器来实施粘合剂去除后,将陶瓷生片材31装载在致密性载置定位器中,但因为去除粘合剂后的陶瓷生片材31的保形性低,所以在移动陶瓷生片材31时,会引起陶瓷生片材31的破损。
对此,在本实施方式中,使用具有形成微小物质排出用凹凸部33的装载面的载置定位器作为氧化锆载置定位器32,所以当使陶瓷生片材3 1装载在氧化锆载置定位器32的装载面上时,氧化锆载置定位器32与陶瓷生片材31的接触面积变小。因此,在陶瓷生片材31的粘合剂去除处理时,粘合剂的燃烧气体(碳素)易从陶瓷生片材31的背面(氧化锆载置定位器32侧的面)排出,所以粘合剂去除性变好。因此,在陶瓷生片材31的烧制处理时,残留在陶瓷生片材31中的碳(粘合剂的熔渣)变少。另外,在烧制处理时,当稍稍残留的碳素气化时,该气体也易从陶瓷生片材31的背面排出。由此,通过残留碳素使陶瓷生片材31中的氧化物还原,蒸发的Zn减少,所以可抑制陶瓷生片材31的表面侧与背面侧组成不同。
另外,因为使用难以与铅反应的致密性氧化锆载置定位器32,所以在陶瓷生片材31的烧制处理时,陶瓷生片材31中的铅基本上未被吸收到氧化锆载置定位器32中。另外,在使陶瓷生片材31装载在氧化锆载置定位器32的装载面上的状态下,如上所述,氧化锆载置定位器32与陶瓷生片材31的接触面积变小。由此,陶瓷生片材31的表面侧与背面侧热和气氛气均匀性变好,降低陶瓷生片材31的烧制不均。
如上所述,因为陶瓷生片材31的收缩率作为整体基本上变均匀,所以可确实降低压电陶瓷板36的翘曲或曲折等,可得到具有期望特性的压电陶瓷板36。
并且,通过在氧化锆载置定位器32的装载面上形成微小的物质排出用凹凸部33,当在陶瓷生片材31的粘合剂去除处理时,陶瓷生片材31的背面产生的气体的排放性变好,所以可防止陶瓷生片材31从氧化锆载置定位器32浮起。另外,在陶瓷生片材31的烧制处理时,因为陶瓷生片材31与氧化锆载置定位器32之间的加热速度差变小,所以与原来一样,抑制存在于烧制炉35内的气体卷入陶瓷生片材31的背面。因此,也可防止陶瓷生片材31通过这种气体卷入作用而从氧化锆载置定位器32浮起。
因此,避免了在陶瓷生片材31的粘合剂去除及烧制时,陶瓷生片材31相对氧化锆载置定位器32错位移动。由此,可防止陶瓷生片材31从氧化锆载置定位器32脱落,或瑕疵附着于陶瓷生片材31的背面,或陶瓷生片材31变形。
另外,在制作具有物质排出用凹凸部33的氧化锆载置定位器32时,如上所述,在烧制粉体成形体后,不对粉体成形体实施机械加工,所以在陶瓷生片材31的烧制时,加工屑等异物不会附着于陶瓷生片材31上,或者氧化锆载置定位器32的变形导致氧化锆载置定位器32产生裂开。
本发明的实施方式4涉及含有铅的压电陶瓷板的制造方法,但本发明不用说,也可适用于此外的陶瓷板中。此时,优选使用由氧化铝或氧化镁等形成的载置定位器作为载置定位器。另外,上述实施方式进行层叠体构成的陶瓷生片材的粘合剂去除和烧制,但本发明也可适用于单层的陶瓷生片材。
下面,说明根据实施方式4的实施例和比较例。
(1)载置定位器作为载置定位器,使用在氧化锆中添加8mol%-12mol%的氧化钇(Y2O3)后完全稳定化的致密性氧化锆载置定位器。该氧化锆载置定位器的气孔率不足3%。氧化锆载置定位器的大小为100mm×100mm,氧化锆载置定位器的厚度为1.5mm。在氧化锆载置定位器的表面中形成中心线平均粗糙度Ra优选为2-6微米的物质排出用凹凸部。
(2)陶瓷作为氧化锆载置定位器的材料,使用组成为PbTiO3-PbZrO3-Pb(Zn1/3Nb2/3)O3的3成分类压电陶瓷。通过球磨机湿式混合氧化物或碳酸盐形态的原料,混合后以900度下进行中间烧制后,再次用球磨机进行湿式粉碎,由此微粉化由该材料构成的压电陶瓷粉体。
如下制作陶瓷生片材。即向准备的压电陶瓷粉体中加入粘合剂或溶剂等进行糊剂化,通过刮粉刀片成形为厚度50微米。之后,使用由Ag/Pd=7∶3的金属构成的内部电极膏,通过丝网印刷法在片中形成内部电极图案。之后,重叠片,制作层叠体,使内部电极变为8个,并进行施压处理,形成陶瓷生片材。另外,切断陶瓷生片材,使陶瓷生片材的大小变为15mm×35mm。
(3)粘合剂去除使准备的10个陶瓷生片材装载在氧化锆载置定位器的装载面上(参照图12和图13),在400度温度下稳定10小时,由此进行陶瓷生片材的粘合剂去除。
(4)烧制在粘合剂去除后,重叠10个装载陶瓷生片材的氧化锆载置定位器,并在其上层叠未装载陶瓷生片材的氧化锆载置定位器,形成烧制状态(参照图15和图16)。此时,由氧化锆隔板来调整各氧化锆载置定位器之间的间隙。并且,将如此层叠的10个氧化锆载置定位器配置在密闭的烧制炉内,烧制各陶瓷生片材。此时,在烧制温度为1050度、稳定时间为3小时的条件下进行烧制。
(5)评价通过非接触的激光3维形状测定装置来对烧制得到的100个压电陶瓷板进行翘曲评价。
结果,压电陶瓷板的翘曲最大为20微米以下。另外,就翘曲的产生程度而言,未发现压电陶瓷板局部翘曲。
另外,使用氧气流中燃烧-红外线吸收法来分析粘合剂去除后的10个陶瓷生片材各自的残留碳素量时,为50-150ppm,较少。并且,压电陶瓷板的背面未见到凹入。另外,陶瓷生片材未从氧化锆载置定位器脱落。
比较例中使用的载置定位器是在烧制后实施过研磨的致密性氧化锆载置定位器。即,在该氧化锆载置定位器的装载面中未形成上述实施例那样的物质排出用凹凸部。使用这种氧化锆载置定位器,通过与上述一样的方法来制作压电陶瓷板。
与上述一样,对由此得到的100个压电陶瓷板进行翘曲评价,最大产生100微米的翘曲。另外,就翘曲的产生程度而言,尤其是在基板的四个角局部产生翘曲。
另外,与上述一样分析粘合剂去除后的陶瓷生片材的残留碳素量,残留1000ppm的碳素。并且,有在基板背面产生认为是引起氧化锆载置定位器的研磨屑的凹入的陶瓷生片材。另外,也有从氧化锆载置定位器脱落的陶瓷生片材。
本发明提供陶瓷板的烧制方法和制造方法,在相对的载置定位器之间,在载置定位器上配置陶瓷板,由与陶瓷板大致相同组成的陶瓷材料构成的包围部件包围陶瓷板的周围部,进行烧制;另外,在下载置定位器上,位于陶瓷板周围还装载隔板,隔板在烧制前的高度比烧制前的支柱部件的高度低,经过烧制后的高度比经过烧制过程后的陶瓷板的高度高;此外形成使加热陶瓷生片材时产生的物质从氧化锆载置定位器侧排出的微小物质排出用凹凸部,可防止烧制后陶瓷板产生翘曲或曲折,可防止烧制时载置定位器与陶瓷板接触,且可在降低陶瓷板的翘曲等的同时,防止处理中陶瓷板相对载置定位器错位移动。
陶瓷板的烧制方法和制造方法
- 专利详情
- 全文pdf
- 权力要求
- 说明书
- 法律状态
查看更多专利详情
下载专利文献
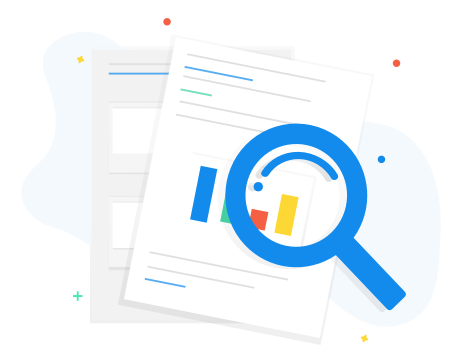
下载专利
同类推荐
-
佐佐木诚志名取荣治汤玉斐杨建杨建
您可能感兴趣的专利
-
杨建陈秀丽陈秀丽陈秀丽陈秀丽
专利相关信息
-
王红云王红云周延春