晶须补强氮化硅复合材料制造方法
- 专利详情
- 全文pdf
- 权力要求
- 说明书
- 法律状态
专利名称:晶须补强氮化硅复合材料制造方法本发明属于一种碳化硅晶须补强氮化硅复合材料的制造方法,是用Si
查看更多专利详情
下载专利文献
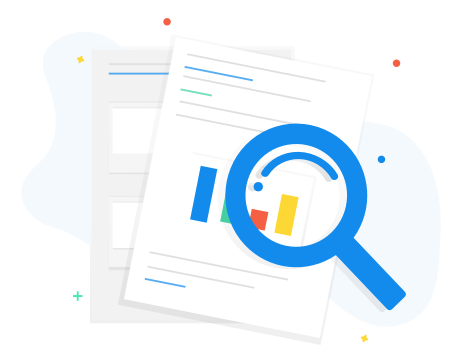
下载专利
同类推荐
-
柳光祖, 宁慎泰柳光祖, 宁慎泰李贺军李贺军
您可能感兴趣的专利
-
王刚C·J·黄, A·J·皮兹克刘友举
专利相关信息
-
付伟峰, 窦涛王新, 王桂英D·J·默克莱伊J·H·阿伦斯J·H·阿伦斯J·H·阿伦斯