专利名称:一种碳酸氢铵发泡法制备多孔氮化硅陶瓷的方法多孔氮化硅陶瓷是一种极具潜力的高温过滤材料和透波材料。作为这两种材料,多孔氮化硅陶瓷必须在具有高孔隙率的同时具有较高的强度。文献“Microstructure and properties of porous Si3N4ceramics with adensesurface.1nt.J.App1.Ceram.Technol.,8 (2011), N0.627 - 636” 公开了一种多孔氣化硅陶瓷的制备方法。在Si3N4粉中加入5%的氧化镥作为烧结助剂,加入5^35%的酚醛树脂作为造孔剂,混合均匀后在IOOMPa的压力下采用冷压工艺成型,最后在0.3MPa的氮气保护下1800°C烧结2小时,制备出孔隙率高、孔连通性好的多孔氮化硅陶瓷。该多孔氮化硅陶瓷的弯曲强度为143MPa 207MPa,孔隙率为46 53%,全部为开气孔。该多孔氮化硅陶瓷满足过滤材料和透波材料的性能要求,但该多孔氮化硅陶瓷采用的冷压成型工艺,只适合制备一些形状简单的构件。若要采用该方法制备形状复杂的构件,必须先烧结出尺寸较大的陶瓷,然后再根据构件的形状进行相应的磨削加工。这样做一方面会造成很大的浪费,另一方面会增加构件的制造成本。文献“Effectof chemical vapor infiltration of Si3N4On themechanical anddielectric properties of porous Si3N4ceramic fabricated by atechniquecombining3_D printing and pressureless sintering.Scripta Mater.,67(2012),N0.380-383”也公开了一种多孔氮化硅陶瓷的制备方法,在氮化硅粉中加入5%的氧化镥作为烧结助剂,加入10%的糊精作为造孔剂,然后根据构件的形状,采用三维打印技术打印出相应形状的坯体,最后在0.3MPa的氮气保护下1800°C烧结0.5^2小时,制备出孔隙率高达68 76%的多孔氮化硅陶瓷。三维打印技术可以成型形状复杂的多孔氮化硅陶瓷构件,但采用该技术制备的多孔氮化硅陶瓷的强度仅有6MPa 13MPa,根本无法使用。为了提高该多孔氮化硅陶瓷的强度,文献中利用了化学气相沉积工艺将该多孔氮化硅陶瓷的强度提高至61MPa 95MPa,此时的多孔氮化硅陶瓷仍具有61飞4%的孔隙率,满足过滤材料和透波材料的性能要求,而且化学气相沉积后的多孔氮化硅陶瓷能够保留其原始形状。但是该多孔氮化硅陶瓷的制备工序复杂,且化学气相沉积工艺昂贵的价格大大增加了多孔氮化硅陶瓷构件的制造成本。
为了克服传统冷压工艺难以制备形状复杂的多孔氮化硅陶瓷构件,以及其它一些工艺制备多孔氮化硅陶瓷构件成本太高的不足,本发明目的在于,提供一种可以制备复杂形状的低成本多孔氮化硅陶瓷的制备方法。该方法将碳酸氢铵加入到氮化硅浆料中,然后把浆料浇铸到模具中,通过调节发泡压力,控制发泡温度,可得到具有复杂形状的陶瓷坯体,最后采用无压烧结工艺将该陶瓷坯体烧结,可制备出具有复杂形状的多孔氮化硅陶瓷构件。为了实现上述任务,本发明采用以下的技术解决方案:—种碳酸氢铵发泡法制备多孔氮化硅陶瓷,其特征在于,包括下述步骤:(a)混合粉料制备将粒径为0.6^2微米的氮化硅粉、糊精和氧化钇粉混合制成混合粉料,其中,以质量百分数计,糊精占混合粉料质量的1(Γ20%,氧化钇占混合粉料质量的5 8%,其余为氮化硅粉;将混合粉体倒入球磨罐中,按每100克混合粉料加入15 25颗直径为8 12毫米的氧化铝球,干球磨1(Γ20小时,干球磨完成后冷却至5 10°C。(b)浆料制备在5 10°C的温度下,按每100克纯净水加入15 20克碳酸氢铵的比例配制出碳酸氢铵溶液;按每100克混合粉料加入8(Γ120毫升碳酸氢铵溶液的比例,将碳酸氢铵溶液倒入前面混好的粉体中,湿球磨5 10分钟,得到浆料。(C)陶瓷坯体发泡成型在5 10°C的温度下,将浆料倒入具有所需形状的氧化铝模具中,然后将模具放入密闭的容器中,并向容器中通入气体加压,利用安装在容器上的恒压阀将容器的压力控制在0.2^0.5MPa ;利用容器中的温度控制器对容器的温度进行调节,先升温至5(T70°C,保温Γ2小时,然后升温至9(T10(TC,保温5 10小时,期间容器的压力保持恒定; (d)陶瓷坯体烧结调节容器的恒压阀,让容器缓慢泄压,为避免在泄压过程中陶瓷坯体内部气体膨胀过快使坯体开裂,泄压速度控制在每分钟0.02MPa^0.05MPa,泄压完毕后将陶瓷坯体取出,放入高温烧结炉中,通入0.2MPa 0.4MPa的氮气,升温至165(Tl700°C烧结2 4小时,即可得到多孔氮化硅陶瓷。本发明采用了边发泡边成型的坯体成型工艺,能够使最终制备的多孔氮化硅陶瓷在具有高孔隙率的同时具有构件所需的形状,因此在多孔氮化硅陶瓷烧成后,只需对其进行少量的修补即可,避免了后期复杂的加工工序,节省了多孔氮化硅陶瓷构件的加工成本。另外,采用该工艺制备的多孔氮化硅陶瓷满足过滤材料和透波材料对孔隙率和强度的要求。
图1是本发明的碳酸氢铵发泡法制备多孔氮化硅陶瓷的流程图;图2是四个实施例制备的多孔氮化硅陶瓷的微结构照片;图3是四个实施例制备的多孔氮化硅陶瓷的孔径分布图。下面结合附图和实施例对本发明作进一步的详细说明。
按质量百分数计,取粒径为I微米的氮化硅粉:75%,糊精:20%,氧化钇粉:5%,混合;然后向每100克混合粉中加入20颗直径8 12毫米的氧化铝球,干球磨10小时。在5 10°C的温度下,按每100克纯净水加入15克碳酸氢铵的比例配制出碳酸氢铵溶液,然后以每100克混合粉体中加入120毫升碳酸氢铵溶液,湿球磨5分钟,制成浆料。将浆料倒入具有所需形状的氧化铝模具中,然后将模具放入密闭容器中并通入气体加压,利用安装在容器上的压力阀控制容器中气体的压力为0.2MPa。利用容器上的温度控制器调节容器中气体的温度,先升温至60°C保温2小时,然后升温至90°C保温10小时,期间容器的压力一直保持在0.2MPa。发泡完毕后,调节容器上的压力阀,让容器以每分钟0.02MPa的速度泄压。泄压完毕后将陶瓷坯体取出,放入高温烧结炉中,通入0.4MPa的氮气,升温至1680°C烧结2小时,制成多孔氮化硅陶瓷(图2 (D)0在室温环境下测试,测试结果参见下表I和图3,该多孔氮化硅陶瓷的孔隙率为66%,密度为1.37 ± 0.02g/cm3、平均孔径为4.0 μ m,抗弯强度为31 土 16MPa、断裂韧性为0.5±0.2MPa.m1/2。实施例2:本实施例的碳酸氢铵发泡法制备多孔氮化硅陶瓷的流程如图1所示:按质量百分数计,取粒径为0.6微米的氮化硅粉:80%,糊精:15%,氧化钇粉:5%,混合,然后按每100克混合粉中加入15颗直径8 12毫米的氧化铝球,干球磨20小时。在5 10°C的温度下,按每100克纯净水加入15克碳酸氢铵的比例配制出碳酸氢铵溶液,然后以每100克混合粉体中加入100毫升碳酸氢铵溶液,湿球磨10分钟,制成浆料。将浆料倒入具有所需形状的氧化铝模具中,然后将模具放入密闭容器中并通入气体加压,利用安装在容器上的压力阀控制容器中气体的压力为0.3MPa。利用容器上的温度控制器调节容器中气体的温度,先升温至50°C保温2小时,然后升温至90°C保温10小时,期间容器的压力一直保持在0. 3MPa。发泡完毕后,调节容器上的压力阀,让容器以每分钟0.03MPa的速度泄压。泄压完毕后将陶瓷坯体取出,放入高温烧结炉中,通入0.2MPa的氮气,升温至1700°C烧结2小时,制成多孔氮化硅陶瓷(图2 (2))。在室温环境下测试,测试结果参见下表I和图3,该多孔氮化硅陶瓷的孔隙率为58%,密度为1.37±0.02g/cm3、平均孔径为3.0 μ m,抗弯强度为116± 15MPa、断裂韧性为
2.1±0.2MPa.m1/2。实施例3:本实施例的碳酸氢铵发泡法制备多孔氮化硅陶瓷的流程如图1所示:按质量百分数计,取粒径为2微米的氮化硅粉:82%,糊精:10%,氧化钇粉:8%,混合,然后按每100克混合粉中加入25颗直径8 12毫米的氧化铝球,干球磨15小时。在5 10°C的温度下,按每100克纯净水加入20克碳酸氢铵的比例配制出碳酸氢铵溶液,然后以每100克混合粉体中加入80毫升碳酸氢铵溶液,湿球磨10分钟,制成浆料。将浆料倒入具有所需形状的氧化铝模具中,然后将模具放入密闭容器中并通入气体加压,利用安装在容器上的压力阀控制容器中气体的压力为0.4MPa。利用容器上的温度控制器调节容器中气体的温度,先升温至70°C保温I小时,然后升温至95°C保温8小时,期间容器的压力一直保持在0.4MPa。发泡完毕后,调节容器上的压力阀,让容器以每分钟
0.04MPa的速度泄压。泄压完毕后将陶瓷坯体取出,放入高温烧结炉中,通入0.3MPa的氮气,升温至1650°C烧结3小时,制成多孔氮化硅陶瓷(图2 (3))。在室温环境下测试,测试结果参见下表I和图3,该多孔氮化硅陶瓷的孔隙率为52%,密度为1.69±0.01g/cm3、平均孔径为2.0 μ m,抗弯强度为116± 15MPa、断裂韧性为
2.1±0.1MPa.m1/2。实施例4:本实施例的碳酸氢铵发泡法制备多孔氮化硅陶瓷的流程如图1所示:按质量百分数计,取粒径为I微米的氮化硅粉:82%,糊精:10%,氧化钇粉:8%,混合,然后按每100克混合粉中加入20颗直径8 12毫米的氧化铝球,干球磨10小时。在5 10°C的温度下,按每100克纯净水加入15克碳酸氢铵的比例配制出碳酸氢铵溶液,然后以每100克混合粉体中加入100毫升碳酸氢铵溶液,湿球磨5分钟,制成浆料。将浆料倒入具有所需形状的氧化铝模具中,然后将模具放入密闭容器中并通入气体加压,利用安装在容器上的压力阀控制容器中气体的压力为0.5MPa。利用容器上的温度控制器调节容器中气体的温度,先升温至60°C保温2小时,然后升温至100°C保温5小时,期间容器的压力一直保持在0.5MPa。发泡完毕后,调节容器上的压力阀,让容器以每分钟
0.02MPa的速度泄压。泄压完毕后将陶瓷坯体取出,放入高温烧结炉中,通入0.3MPa的氮气,升温至1680°C烧结2小时,制成多孔氮化硅陶瓷(图2 (4))。在室温环境下测试,测试结果参见下表I和图3,该多孔氮化硅陶瓷的孔隙率为47%,密度为1.75 + 0.02g/cm3、平均孔径为1.0y m,抗弯强度为178± 13MPa、断裂韧性为
2.9±0.1MPa.m1/2。 表1:
本发明公开了一种碳酸氢铵发泡法制备多孔氮化硅陶瓷的方法,将氮化硅粉、糊精和氧化钇粉按比例混合干球磨,将配制好的碳酸氢铵溶液按比例加入湿球磨,制成陶瓷浆料;然后将陶瓷浆料倒入氧化铝模具中,将氧化铝模具放入密闭容器中,控制容器的压力和温度,使模具中的陶瓷浆料边发泡边成型,制成多孔氮化硅陶瓷坯体;最后将多孔氧化铝陶瓷坯体放入高温烧结炉中进行烧结,制备出具有不同孔隙率的多孔氮化硅陶瓷。该方法能够根据实际需要制备出具有所需形状的多孔氮化硅陶瓷构件,提高了多孔氮化硅陶瓷构件的制备效率,并降低了其制备成本。
一种碳酸氢铵发泡法制备多孔氮化硅陶瓷的方法
- 专利详情
- 全文pdf
- 权力要求
- 说明书
- 法律状态
查看更多专利详情
下载专利文献
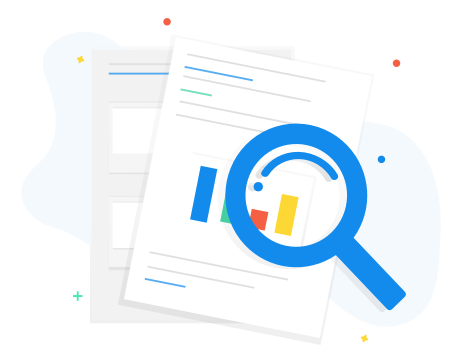
下载专利
同类推荐
-
陈海标, 潘锋陈海标, 潘锋陈海标, 潘锋陈海标, 潘锋
您可能感兴趣的专利
-
陈海标, 潘锋
专利相关信息
-
杨志峰刘建龙田福祯