专利名称:新型下流流化催化裂化设备的制作方法本发明涉及在催化剂存在下将烃原料催化转化成低分子量烃产品的设备和方法。USP3,215,505已公开了烃的连续热裂解设备,其中上流再生器在细长的气力提升管中将传热颗粒如砂再生,分离后同蒸汽一起送入热裂解反应器。载热体的入口通道与热解反应器顶部连通,反应器内装有挡板结构,用以克服气泡在上流方向推动传热颗粒的问题。USP2,458,162报道了另一种在固态物料(可用催化剂)存在下转化液态烃的设备。其中的图2举例说明了下流反应器,操作中调节好送入转化区的催化剂量之后,让密相床层下来的固体颗粒与大约从转化塔中部送入的液态进料接触。调节下流催化剂量为的是在反应器底部适当地建立起相当致密的催化剂床层。待生催化剂于再生器中转化成新鲜催化剂后用传送器送入转化器上方的密相催化剂储斗。USP2,420,632和2,411,603说明的是螺旋形流道反应段的应用,这是由中间的挡板段造成的。USP4,514,285也公开了下流催化裂化反应器与上流再生器连通的方案。反应产物和催化剂混合物从反应段向下直接排入弹道分离段的上部,分离段无挡板且其横截面积为反应段的20-30倍。尽管这种催化剂靠重力向下流的反应历程可减少生焦量,但仍会大量生焦。物流这样从下流反应器底部排入无挡板区,由于延长了催化剂与烃的接触时间,所以会引起严重的“后续裂化”。USP3,835,029公开的是下流顺流催化裂化方法,其中让各种烃原料在下流过程中与沸石催化剂与蒸汽接触0.2-5秒,这种方法据说可提高产率。其中的常规汽提器和分离器接收催化剂-烃混合物流,而且还要求-立式旋风分离器以有效地将蒸汽与固体颗粒分开。本发明涉及成套烃催化裂化设备和方法,其中采用至少3台相连的容器,包括(1)上流提升管再生器,(2)下流烃转化反应器以及(3)连接上流提升管再生器底部(入口)和下流反应器低部(出口)的卧式旋风分离器。再生器顶部(出口)和反应器顶部(入口)用新鲜再生催化剂的增压管路密封床层连接以确保烃催化转化过程在相当低的压降(与提升管再生器相比)下进行。为了有效地操作本发明成套催化转化设备,催化剂实际上是借助蒸汽的速度向下“吹送”的,同时与烃反应物流,必要时还有蒸气稀释剂形成分散体。本发明设备的重要优点之一是转化相同量烃物料所需催化剂装料量减少了5-10倍。本发明涉及将烃原料转化成低分子量烃产品的成套烃催化裂化设备,其中包括a)细长的下流催化反应器,在其顶部和低部包括与其顶部并列的烃原料入口和再生催化剂入口以及与其底部并列的产品和待生催化剂出口;b)细长的上流提升管催化剂再生器,用以再生从反应器送来的待生催化剂,在其顶部和低部包括与其底部并列的待生催化剂入口和含氧再生气的入口装置以及与其顶部并列的再生催化剂和蒸汽相出口,蒸气是用含氧再生气氧化待生催化剂上的焦炭而产生的,该出口包括适于将再生催化剂和蒸气分开的装置;c)将待生催化剂和烃产品分开的卧式旋风分离装置,该装置与反应器底部和再生器底部连通;
d)与再生器顶部和反应器顶部连通用以将来自再生器的再生催化剂和废氧化气分开的连接管分离装置,该装置可在再生器顶部和反应器顶部之间形成催化剂密相;
e)减压装置,用以确保紧靠反应器上游的密相内的压力高于反应器顶部的压力。
卧式分离装置包括ⅰ)细长的卧式壳体容器,其中包括顶部,第一无孔壁,底部以及让烃产品出口管穿过的第二有孔壁,容器顶部与下流裂化反应器相连,连接点在偏离由卧式壳体直径的垂直面所限定的容器顶部中心线的位置足以使待生催化剂和烃产品混合物向下流进细长的容器;
ⅱ)细长的立式下导管,用以向下传送少量的待生催化剂,该管在容器与反应器连接点的另一端的端部与容器连通;
ⅲ)烃产品排出管,用以连续排出从待生催化剂中二次分离出的烃产品,该管在反应器与容器连接点一侧并于连接点以下装在容器的第二侧壁上;
ⅳ)固体槽排放装置,该装置在至少与反应器和容器顶部连接点隔开90°的位置与容器底部相连,角度是沿容器圆周测量的,整圆周为360°排放装置接收待生催化剂和烃产品初次质量流向分离后的待生催化剂,初次质量流向分离是在卧式容器内围绕上述至少90°的角度对待生催化剂进行离心加速来完成的,其中待生催化剂对着卧式容器圆周加速而进行初次质量分离并借此将大部分待生催化剂经固体槽排放装置送入垂直下导管;
ⅴ)其中烃产品排出管,卧式容器及反应器的结构应确保排出管的直径小于卧式容器的直径,操作过程中烃产品和待生催化剂的混合物偏心流入后的旋流比大于0.2,旋流比是用烃产品流过反应器横截面的切线速度除以流过排出管横截面的边界轴向速度来定义的,这样使烃产品连同夹带的少量待生催化剂一起作螺旋流动,旋流轨迹从与烃产品排出管相对一端的无孔壁延伸出来,从而达到二次离心分离,促使夹带的少量待生催化剂与旋流烃产品脱开并将脱开的少量待生催化剂送至容器与垂直下导管的连接位置以通过下导管送入汽提区;
ⅵ)汽提区,该区与垂直下导管和再生器底部连通,其中包括待生催化剂密相床层,操作过程中该床层接收1)初次质量流向分离后经槽型排放装置送来的待生催化剂和2)二次离心分离后经垂直下导管送来的待生催化剂,操作中的汽提气用汽提气输入装置送入汽提区,而且从第一端壁至排出管的烃产品旋流道迹可阻止至少一部分汽提气经垂直下流管向上流入卧式容器。
如后续详述的图1,2和3所示,催化剂密相床层在反应器顶部位置的停留时间非常短。短停留时间的催化剂密相床层可有效地进行管路密封以确保反应器顶部以上的压力高于其内部压力。反应器和管路密相密封床层的这种布置方案要求特殊的压差装置以确保烃原料与沿反应器下流的催化剂组成适用的分散体。可满足此要求的各家阀门销售商和供货商包括Kubota American Corporation,Chapman Engineers,Inc.或Tapco International,Inc.。这些压差阀可使催化剂量符合要求并确保在下流反应器中达到令人满意的烃转化率。也可用其它装置如节流管达到适当的压差。
反应器顶部压差装置之上的管路密封催化剂床层借助卧式旋风分离器维持,该分离器连接再生器出口和反应器入口,其结构与下述连接反应器和再生器低部的卧式旋风分离器类似。
作为本发明实施特例,可在反应器顶部压差装置之上的料管密封催化剂床层里进行部分再生,确切地说肯定能进行部分再生。
反应器中的工艺参数包括近乎零的低压降,4-5巴的压力(当然压力可为1-50巴),0.2-5秒的停留时间以及260-649℃的温度。反应器内压力与管路密封层(建立在反应器之上)的压力之差大于34.5毫巴。这有助于蒸汽,烃原料和催化剂等物料以均匀分散相并以近乎零的压降向下流动。
裂化反应器和提升管再生器在高速流化态下操作。当蒸汽的携带速度超过大部分催化剂的终点速度时就可达到流化态。携带速度可为单个颗粒终点速度的3-300倍,因为密相催化剂是成串即射流形式流动的。蒸汽携带速度超过大部分催化剂的终点速度时的速度即为达到高速流化态的最小速度,在典型密度状态下为大约1m/s。
经高速流化系统的压降随速度头(1/2 Ps Vs-)增加,而经流化床的压降相对速度或流速来说是相对恒定的。
高速流化系统中的少量混合由于会引起湍流而非常有效,但其中的大量反混却比流化床中少得多。在提升管再生器中可用比流化床中少的空气将催化剂上的积炭烧至较低水平。事实上,流化床反应程度仅为理论燃烧程度的大约10%,而提升管可达到近100%。这种高效率正是提升管再升器进行成功操作所要求的。
下流反应器也是高速流化的,只是按下流布置。蒸汽速度(量值)超过催化剂终点速度。蒸汽携带固体沿反应器向下流,而不是让固体自由下落。反应器底部阻挡性必须为最小以便快速将已反应蒸气分出并防止固体反向上流。将其直接排进下述的独特卧式旋风分离器即实现了这一目的。以典型蒸气速度操作时,催化剂在下流反应器里的停留时间约为在提升管反应器里的停留时间的一半,这主要是由高速流化(湍流夹带)造成的。而接触时间仅为其三分之一至一半长,所以本设备中的后续再生操作更为容易。
可将烃原料在与再生催化剂和蒸汽混合物流通过上述压差装置的方向并行的某一点加入到下流反应器,烃原料沸点一般为93-427℃,可以部分蒸汽部分液体状态送入反应器上部或注入其上的催化剂密相中。适宜转化为低分子量烃产品的烃原料一般来自天然原油和合成原油,其具体例子可为真空瓦斯油沸程馏分,常压蒸馏下部馏分,煤油沸程烃馏分或石脑油。还应看到,沥青也可用作烃原料,当然由于其中氢含量低,裂化结果就不一定相同。
由于本发明中观察到优选催化剂会迅速失活(详见下述),实际上就要求催化剂和烃原料的接触时间短,为此可沿下流反应器采用多级原料入口以尽量延长或缩短催化剂与烃原料的实际接触时间。催化剂会很快失去活性,一旦出现这种情况,催化剂和烃原料之间就只是非生产性接触。本工艺的低分子量烃产品优选为内燃机用汽油或其它燃料油如飞机燃料油,柴油机燃料油以及日用燃料油。
下流反应器和上流再生器是底部对底部和顶部对顶部相连的,这种连接采用的是高速分离装置,特别是在底部对底部的连接上。顶部对顶部连接中的高速分离装置可包括卧式旋风分离器,立式旋风分离器,回流分离器或弯管分离分离器,该分离器的入口管尺寸小于反应段直径的4倍或横截面积的6倍。在本发明反应器底部下游独特的卧式旋风分离器中,待生催化剂分离时间仅为0.2-2.0秒,这与USP4,514,285所述的无挡板分离时间8-60秒形成鲜明的对比。因此,本发明底部连接的高速分离装置必须包括至少一台卧式旋风分离器且优选为本申请所述的等效分离器。
卧式旋风分离器优选的是与反应器的最底部(出口)和再生器的最低部(入口)相连,其顶部有输入待生催化剂和烃产品的偏心入口,其输入角加速度远远大于重力加速度,这样可迫使待生催化剂流向分离器壁并因而以角加速度和离心力的作用对催化剂进行初次质量分离。
卧式旋风分离器装有旋流稳定器,用以从其一端至产品出口端形成螺旋形蒸气流道。这种旋流作为二次分离手段将夹带的待生催化剂从烃产品中分离出来。该分离器还装有特定固体槽排放装置,该装置与分离器底部相连并与待生催化剂和烃产品(气相)的入口和连接分离器的另一端的下导管并行,这样可将待生催化剂迅速从烃产品中分离出来,因而可消除或至少是可减轻后续裂化或过量生焦。本发明的卧式旋风分离器与下流反应器和提升管再生器协同操作可使工艺方法更具灵活性且生焦处理起来也比现有技术特别是USP4,514,285所述更容易。然而,最好是分离器和再生器底部用一汽提区相连,其中的汽提介质优选为蒸汽或烟道气,用其与沉积了0.1-5.0%(重量碳)的催化剂紧密接触以从待生催化剂中排除吸附的和孔间的烃产品。汽提器可作常见的立式设计,其底部容钠密相催化剂;或作卧式设计,其中将下倾管集中起来的催化剂送入装料室,该室几乎全部由密相催化剂和未填充空间构成。不管其结构如何,汽提器一般都维持在反应器的相同温度下,通常为454-566℃。常用蒸汽或氮气等做汽提气,一般以0.7-2.4巴的压力送入,其用量足以基本上完全彻底地从待生催化剂中抽提出挥发性组分。汽提区的下游区与连通再生器的移动阀相连。
再生器可将待生催化剂再生达到几乎新鲜催化剂的水平,其构型是各种多样的。对再生器的主要设想是让其在整个高度范围内以密相高速流化态操作。为在再生器底部引发焦炭燃烧,就必须提高汽提后送入其底部的待生催化剂的温度。这可有多种方式,其中包括向其底部回送实际燃烧(即焦炭氧化成CO)的热量,所采取的措施包括建立密相催化剂床,循环再生催化剂,让传热介质对流以及采用扩大的反混段,如可将密相催化剂床层置于接近再生器底部的位置但应尽量减小该床以减少催化剂装料量。减少装料量带来的优点是可节省投资,缓和催化剂失活速度并降低催化剂的磨损。在回送并反混催化剂的情况下,再生器底部温度将提高到起燃温度即烧炭程度受传质而不是氧化动力学影响的温度附近。这一升高温度可比汽提后送入的待生催化剂原有温度高55.6-166.7℃。这一反混段可称为密相循环区,这对提高上述温度是不可少的。
在本发明的一个实施方案中,提升管再生器中包括其底部的待生和正在再生的密相催化剂床层(第一密相床)以及其上部进入第二分离器且优选为卧式旋风分离器的催化剂稀释相。将来自汽提区的汽提后待生催化剂送入再生器底部,可建立起用以达到烧炭温度的密相催化剂床层,但与常见提升管再生器比较,其催化剂密相床的装料量应尽量降低。必要时可加装带或不带旋风分离器的循环装置以从再生器内部或外部将再生催化剂回送到其底部,从而达到烧炭温度。催化剂循环量最好随再生器密相内的温度变化而进行调节。本发明中还可在催化剂循环回路中加装流化装置以流化再生后的循环催化剂。循环催化剂流化程度随再生系统温度而进行调节,以能够更好地调节再生器底部催化剂密相温度为准。
再生器底部密相催化剂用流化气流化,该气体还用于将待生催化剂上的沉积焦炭氧化成一氧化碳,随后氧化成二氧化碳,最后这两种气体从工艺流程中分离出去或在再生器下游的能源回收系统中产生能源。最为优选的流化气为空气,其用量最好稍为多于进行焦炭氧化所必须的化学计量用量(以氧为准)。过量氧可为上述化学计量用量的0.1-25%,从而可经再生得到活性最高的催化剂。
FCC装置中的温度控制很严格,因此必须对再生器温度进行严格监控。再生器的主要障碍是入口温度低且停留时间短。为了缓解这些困难,炼油商都采用下述并不相互排斥的方案之一。第一,让传热颗粒经提升管下落以回送热量,延长催化剂停留时间或尽量提高传热效率。如需再循环传热颗粒,可用适当的气力提升装置让颗粒在提升管底部和顶部之间循环。第二,让再生后的催化剂再循环返回至提升管底部以回送热量。第三,在提生管低部设置扩大段以将热量回送入再生器进料区。
提升管内再生后的催化剂再于密相催化剂床中几乎完全得到再生。再生器中建立(如火炬油的初始燃烧要求的话)并加以维持的反应条件为温度621-768℃,压力0.35-3.5巴。必要时可在密相催化剂床下游位置添加二次含氧气体。如再生器底部已有氧化气体源,则优选的是在紧靠密相催化剂床上方加入此二次氧化气体。还可加进助燃剂以更密切地调节温度并尽可能降低催化剂上的焦炭量。USP4,341,623和4,341,660对可采用的再生助燃剂进行了说明,其公开内容仅作参考。
在提升管再生器底部保持有催化剂密相床的实施方案中,再生催化剂离开密相床,然后进入温度保持在649~815℃的稀释相区。需再次指出,必须找出再生区温度的关系,这对向反应段提供热再生催化剂以尽量减少整个工艺中的热消耗是必要的。要认识到,与标准的上流提升管反应器相比,催化剂的装料量大大降低,因此可以找到并且维持下流反应器和上流再生器中更精确的温度平衡。进一步的构思还有,提升管再生器可有一催化剂稀释相进入隔离室,其中底部保持有再生器的第二催化剂密相床,用于积累并且使其通过再生催化剂循环装置,达到提升管再生器底部的催化剂密相床。
本发明的构思还包括,选用的已知固体颗粒传热材料,如金属球、相变材料、热交换颗粒或其它低碳固体,应分散在催化剂之中。在这一较好的实施方案中,受热颗粒被用来维持再生器提升管底部的高温,这些颗粒对催化剂的实际功能以及烃类反应材料的理想转化一般来讲是惰性的。尽管存在这些传热材料,再生催化剂表面的沉积碳仍要低于0.5%(重量),最好低于0.02%(重量)的炭。
本发明所采用的催化剂含有催化活性晶体硅铝酸盐,这些晶体硅铝酸盐在烃转化过程中初始活性高,在较好的催化剂中沸石分散于氧化铝基质中。也可以采用二氧化硅-氧化铝组合物。其它耐火金属氧化物,如镁或锆的氧化物也是可用的,但其有效性不如二氧化硅-氧化铝催化剂。还可以采用适宜的分子筛,分子筛可与氧化铝基质掺合,也可不与其掺合,氧化铝基质的实例有八面沸石、菱沸石、X型和Y型硅铝酸盐材料和超稳定大孔晶体硅铝酸盐材料,如Z SM-5或Z SM-8催化剂。使用前,这些材料的金属离子应用铵或氢交换。如果存在碱金属或碱土金属,其存在量只能是很少的。
就本发明方法的整体来说,提升管再生器要比下流催化反应器长。这种结构尺寸的不同其原因在于下流反应器中催化剂活性的快速下降。下流催化反应器的长度最好不超过提升管再生器长度的一半。
本发明还涉及在下流裂化反应器中将烃原料连续裂化为低分子量烃产品的方法,该方法包括在催化裂化组合物存在下,使烃原料进入细长的下流反应器顶部,并在操作温度大约为260~815℃,压力为大约1~50巴,压降接近0的条件下将所述原料的分子裂化为较小的分子,所述烃原料下流至反应器出口,在反应器中的停留时间约为0.2~5秒;经过上述停留时间后,从所述反应器的出口排出烃产品和表面带有积炭的待生催化剂;将所述烃产品与所述待生催化剂分离并将烃产品从流程中排出;将所述表面带有积炭的待生催化剂送入提升管上流再生器并加入含有含氧气体的再生气中;用升温装置将所述再生器底部的温度升至烧炭程度并在上流提升管再生器的几乎整个长度内保持密相高速流化催化剂床,温度为593~982℃,压力为1~50(大气压),其中所述催化剂在所述上流再生器中停留时间约为30~300秒;将再生催化剂和在含氧气体存在下氧化所述积炭所形成的蒸气相送入水平安置的旋风分离器;在所述的卧式旋风分离器中将再生催化剂与所述蒸气相分离并将该气相排出所述工艺;将分离后的再生催化剂从所述卧式旋风分离器送至催化剂密相床,催化剂密相床温度保持在大约538~982℃,压力在大约1~50巴,催化剂在所述密相床的停留时间大约为1~600秒;使再生催化剂从所述密相床进入所述下流反应器的顶部并使其与进入所述反应器顶部的烃原料接触,其中催化剂密相床的压力比所述下流反应器内的压力要高34.5毫巴以上。
图1 是本发明的总体图。
图2 是与提升管再生器和下流反应器相联的卧式旋风分离器的详细图。
图3 是关于颗粒催化剂回收的本发明较好实施方案的流程图。
图1展示了下流反应器1经卧式旋风分离器2与再生器3相连。烃原料经管线5和控制阀6被加入到下流反应器1的顶部或顶部附近。进料最好经多支管系统(未示出)输入,以使原料在下流反应器的顶部完全分散并在再生过的催化剂的存在下向下移动。进料位置最好在压差装置2米以下,此处表示为一阀门,以使催化剂加速和分散。通过压差阀7将再生催化剂加入到下流反应器1,确保下流反应器上方(数字8所示)的压力高于下流反应器内(数字10所示)的压力。这种压差最好大于34.5毫巴以使催化剂在较短的停留时间里在整个下流反应器中具有有效的分散能力。
下流反应器内的温度条件最好为427~815℃,压力为4~5巴。下流反应器应在温度高于提升管平均温度下操作以降低分散蒸汽量,近而使催化剂与油之比增高。本发明突出的优点之一是整个下流催化反应器中的压降接近于0。如有必要,可在与进料物流并列的点加入蒸汽,最好是经管线9和阀11将蒸汽加到第二催化剂密相床12。第二催化剂密相床12对于确保下流反应器中适当的压差是必需的。催化剂在该第二密相床内停留的时间只需要能确保在上述两部分之间形成适当的管路密封即可。催化剂在下倾管路中的停留时间一般不超过5分,最好少于30秒。
下流反应器1通过卧式旋风分离器2和汽提区14与提升管再生器3相通。待生催化剂和烃产品由下流反应器1底部卸出,在旋风分离器卧式容器偏心点处进入卧式旋风分离器2。流入的不同固体和流体相受角加速力(通常270°)作用而进行初次质量流向分离。固体颗粒经固体槽排放装置16(侧视图中不能看到)直接进入下导管15,该装置由固紧装置17支撑。少量固体待生催化剂将夹带在烃类流体产品中。卧式旋风分离二器2的具体结构应使得通过容器的流体的切线速度(Ui)除以通过产品排出管线18的流体的轴向速度(Vi)应大于0.2,如下所定义旋流比= (Ui)/(Vi) = (Re)/(Ri) × 1/(F)其中Re=下流反应器1的半径;
Ri=排出管18的半径;
F=管状反应器的横截面积除以流体排出管横截面积。
满足上述关系式,在水平轴向19处形成流体的螺旋流道,始自任选的旋流稳定器20,延至烃产品出口18。这样可分离出少量夹带的待生固体催化剂,固体催化剂经下导管15进入汽提器14。
汽提器14具有第三个(待生)催化剂密相床21,经汽提气体输入管线22和控制阀23导入的汽提剂,最好是空气或蒸汽,立即与该密相催化剂接触。催化剂在汽提器14内的停留时间应足以使部分吸附的烃从催化剂表面脱离,最好为10~100秒,汽提后的待生催化剂经连接导管25和流量控制装置26进入第一催化剂密相床层24。第三催化剂密相床21温度通常为26~537℃。
第一催化剂密相床24保持在一特定规格的筛板(未示出)上,以使蒸气通过筛板上流,待生催化剂从催化剂密相中下流。适宜的流化气体是含氧气体,也用来将催化剂表面的积炭氧化成一氧化碳和二氧化碳。含氧气体经管线29和气体分布支管束31提供。本发明的范围还包括,再生器3的流化气体的加入量可以根据燃烧区的温度、第一催化剂密相床24中催化剂的数量或高度调节。如果需要,可以提供一再生过的催化剂循环装置27,经管路27和控制阀28从提升管再生器3的稀释相的上部使催化剂循环,这也可根据再生区稀释相的温度来调节。图中所示的催化剂循环线在提升管再生器的外部,以可以装在再生器的内部以保证循环的催化剂在达到催化剂密相床24的过程中不致过度冷却。还可以考虑使管路27与管路25相交,将再生的催化剂与待生催化剂的混合物经管路25同时加到第一催化剂密相层24。
再生催化剂和氧化积炭所形成的蒸气馏出物穿过催化剂稀释相33至分离装置,最好是卧式旋风分离器,其它类似分离器如立式旋风分离也是可使用的。再次指出,可以使用1台以上的旋风分离器,组成串联的或并联的分离流程。上流的催化剂与蒸气分离。进入管线41的蒸气通常含有少于1000ppm的CO,经管路43,蒸气可从工艺中排出,或经管路41进入能源回收器45或一氧化碳锅炉装置(未示出)。旋风分离器连通管路47用以使催化剂与任何不需要的气体脱离并保证再生催化剂进入第二密相层12,密相层12在下流反应器的上方形成管路密封层。
图2更详细地展示了卧式旋风分离器2,该分离器用以将下流反应器卸出的待生催化剂和烃产品分离,将催化剂送至汽提器,最终送至上流提升管再生器的第一催化剂密相层。
图3展示了本发明更为完善的设备和工艺流程。下流反应器101通过上方的卧式旋风分离器102与提升管再生器103相连。提升管再生器103的底部经管路105和支管束107供应含氧气体。选用的多孔板109用来支撑催化剂流化床的底部。催化剂密相层很小,即直径为2.44米时,多孔板不是必需的。催化剂密相111保持在适宜的再生条件下,即温度为649~815℃,以将催化剂表面的积炭降低至0.05%(重量)或更低。在再生器103经过再生的催化剂进入稀释相113,其下部可经管路115和/或二次空气供应线117加入助燃剂。通常要调节空气量以使氧气含量按化学计量足以将积炭烧成一氧化碳,近而将其部分或全部转化成二氧化碳。再生过的催化剂被夹带向上穿过保持在上述条件下的稀释相,进入卧式旋风分离器102或通过循环线121和控制阀123被循环至再生催化剂密相111。需再指出,图中所示循环物流在再生器的外面,但也可装在里面并且含有各种工艺流程控制装置,如流量指示器或温感和温控装置,以将温度做为稀释相113内条件的调节参数。燃烧产品,通常主要为二氧化碳、氮和水,通过旋流排放管131离开卧式旋风分离器102。旋流排出导管使催化剂135沿旋风分离器以基本上垂直于提升管再生器103的方向成螺旋流动。这种螺旋流体最好全部绕过折流锥体装置137,使颗粒催化剂向下流动至密相管路密封层139。连接管141可以是卧式旋风分离器的延伸管,也可以是旋风分离器的催化剂输送导管。进料由压差阀147下面的导管145供给。如有必要,可经管线149和/或管线151加入蒸汽。压差阀147的存在是为了保证烃类不会倒流进入催化剂密封段。这样,下移的蒸气将催化剂颗粒吹下,使催化剂一烃反应物流分散良好。这三种物体沿反应器101向下流形成目的烃类产品。在本实施方案中,下流反应器101的底部装有第二台卧式旋风分离器。蒸气可由下导管的任一边离开,在本实施方案中,蒸气通过连接于常规立式旋风分离器157的旋流排出导管167排出。在所述的立式旋风分离器中,气体经导管159离开流程,而所提取的固体催化剂经下倾管161送到蒸汽汽提区165中的另一催化剂密相163。旋流排出导管167也使待生催化剂169产生螺旋流动,经旋流稳定器171进入汽提器密相床163。催化剂密相163可装一下倾管173,为汽提塔底部的另一催化剂密相床供应催化剂。后一个催化剂密相床有两个蒸汽源,即由管线177和179供给。汽提后的待生催化剂经管线181从汽提器165底部排出并经过滑阀183进入提升管再生器103的密相床111。
热蒸气流用管线131从卧式旋风分离器102导出后进入常规立式旋风分离器201,该分离器配有蒸气排出装置203和催化剂下流管205,回收的再生催化剂沿下流管回到密相111。立式分离器201将尾气送入与旋风分离器102结构相似的第三个旋风分离器207。再生催化剂从热气体中回收后经管线209循环至催化剂密相床111。管线211中的尾气基本上不含固体材料。从旋风分离器207排出的尾气进入装有涡轮机215的发电装置,由发电机221发出电力。这些电力可用来运转炼油厂的其它部分或通过并网售给公众。尾气发电后进入压缩机213。
本发明公开在近乎零的压降下将烃原料转化成低分子量烃产品的成套烃转化设备和方法,其中包括下流反应器,上流提升管再生器和卧式旋风分离器并于下流反应器上方设置管路密封层。
新型下流流化催化裂化设备制作方法
- 专利详情
- 全文pdf
- 权力要求
- 说明书
- 法律状态
查看更多专利详情
下载专利文献
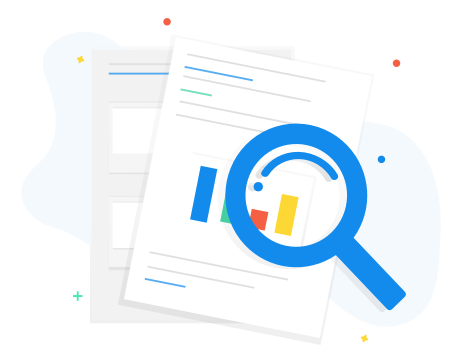
下载专利
同类推荐
-
汤马斯·西安·德维茨汤马斯·西安·德维茨汤马斯·西安·德维茨汤马斯·西安·德维茨汤马斯·西安·德维茨张军
您可能感兴趣的专利
-
张军张军张军张军张军张军
专利相关信息
-
张军孙颖莹, 申 谢孙颖莹, 申 谢孙颖莹, 申 谢孙颖莹, 申 谢孙颖莹, 申 谢孙颖莹, 申 谢