一种热结构复合材料部件的制作方法[0001]本申请是申请日为2009年7月20日,名称为“一种制造热结构复合材料部件的方法以及由此获得的部件”的中国专利申请N0.200910151636.5的分案申请。[0003]热结构复合材料由于其机械性能和在高温下保持这些机械性能的能力而显著。[0004]众所周知的热结构复合材料为包含由碳基体致密化的碳纤维增强件的碳/碳(C/C)复合材料,以及包含由陶瓷基体或由基本上为陶瓷的基体致密化的耐火纤维(碳或陶瓷纤维)组成的纤维增强件的陶瓷基体复合(CMC)材料。[0005]在CMC材料中,公知介于纤维增强件的纤维和基体之间的防脆(embrittlement-relief)界面的存在大大减少了材料对裂化的敏感度并增加了材料经受冲击的能力。所述界面由能够解除裂缝底部的应力(所述应力穿过基体传递至界面),并由此能够避免或延迟裂缝穿过纤维的传递的材料组成。裂纹穿过纤维的这种传递导致纤维破裂,从而妨碍其使得CMC材料较不脆性。构成所述界面的材料可由例如通过化学气相渗透(CVI)沉积至纤维增强件的纤维上的热解碳(PyC)或氮化硼(BN)构成,特别如文献US4752503所描述。另一适用于防脆界面的材料为掺硼碳(BC)。[0006]在C/C材料中,纤维增强件的纤维与碳基体之间的界面(所述界面为除了碳之外的材料)的存在也能特别用于改进氧化行为,例如若使用含硼界面,如BN或BC。[0007]此外,为了制造形状复杂的热结构复合材料部件,公知由制造纤维预成型体开始,所述纤维预成型体通过将纤维结构成形并通过固结(consolidation)使其保持在所需的形状而构成部件的纤维增强件。固结包括利用固结基体相将纤维预成型体部分致密化,充分、且优选仅刚刚充分地进行所述部分致密化以保证能处理所述预成型体并同时保持其形状而无须支撑工具的协助。这使得固结的预成型体的致密化能够继续而无需工具,这特别有利,特别是当致密化通过在烘箱中的CVI继续时,否则工具将占据烘箱的可用体积的主要部分。[0008]所述纤维预成型体可通过CVI固结。然后所述预成型体在通过工具保持所需形状时被置于烘箱,在其中有可能接连形成涂布在纤维上的界面并通过部分致密化将它们固结。然而,这回到占据烘箱的可用空间的工具的上述缺点。此外,众所周知地,CVI法即使对于仅仅部分的致密化而言也是漫长的。[0009]因此通过液体技术进行固结是有利的,所述液体技术涉及从纤维结构成形纤维预成型体,所述纤维结构已用含有树脂的液体固结组合物浸溃,所述树脂为碳或陶瓷固结基体相的前体,随后将树脂通过热解转化为固体碳或陶瓷残留物。然而,为了实现防脆功能,显示足够厚度的界面涂层在纤维结构的纤维上的在先形成对纤维结构的变形能力具有有害的影响,且这能使得不可能将纤维预成型体成为所需形状,特别是当待制部件具有相对复杂的形状时。
[0010]为了解决这个困难,文献US5486379提出在纤维预成型体通过液体技术固结之后并在继续致密化之前放入界面。然而,由于固结相的存在,不可能保证界面将在纤维预成型体的纤维上连续形成,特别是当热解固结树脂的固体残留物牢固粘附于纤维时,正如例如热解在SiC纤维上的为碳化硅(SiC)前体的树脂的残留物所发生的那样。
[0011]本发明的目的是提供一种能够通过使用液体技术成形和固结纤维预成型体并同时确保连续界面存在于纤维和基体之间而制造形状复杂的热结构复合材料部件的方法。
[0012]该目的通过包含如下连续步骤的方法实现:
[0013].使用化学气相渗透以在由耐火纤维组成的纤维结构的纤维上形成第一连续界面层,所述第一界面层具有不多于100纳米的厚度;
[0014]?通过将具有所述第一界面层并用包括碳或陶瓷前体树脂的固结组合物浸溃的纤维结构成形来形成固结的纤维预成型体;
[0015].通过热解将所述树脂转化为由碳或陶瓷颗粒形成的不连续固体残留物;
[0016]?然后使用化学 气相渗透以形成覆盖所述第一界面层和所述固体热解残留物颗粒的第二连续界面层;以及
[0017].然后用耐火基体将所述预成型体致密化。
[0018]这保证了连续且足够的界面存在于纤维和基体之间,而同时确保制造预成型体的纤维结构保持其变形的能力。
[0019]优选地,所述第一界面层由选自热解碳、氮化硼或掺硼碳的材料组成。相同的可应用于所述第二界面层,且第一和第二界面层的材料不必需相同。在一个变体中,所述第二界面层可通过使例如PyC、BN或BC的防脆层与例如SiC的陶瓷层交替而顺序形成。连续界面的制造特别描述于文献US5738951中。
[0020]有利地,所述第一界面层具有不多于50纳米的厚度。
[0021]优选地,所述第一界面层具有至少10纳米的厚度。
[0022]所述第二界面层的厚度优选不少于100纳米。
[0023]在该方法的一个特别的实施方案中,通过热解将树脂转化为碳或陶瓷的固体残留物的操作,以及形成第二界面层的操作在相同的烘箱内连续进行。
[0024]本发明也提供一种能由上述方法获得的热结构复合材料部件。
[0025]根据本发明,包含通过化学气相渗透获得的由耐火基体致密化的耐火纤维的纤维增强件,并具有介于纤维增强件的纤维和基体之间的界面的这种部件具有包含涂布纤维增强件的纤维并具有不多于100纳米的厚度的第一连续界面层以及第二连续界面层的界面,所述第二界面层覆盖第一界面层和由热解树脂得到的固体碳或陶瓷残留物的不连续颗粒,所述颗粒介于第一和第二界面层之间。
[0026]优选地,所述第一界面层由选自热解碳(PyC)、氮化硼(BN),或掺硼碳(BC)的材料组成。所述第二界面层也可由选自PyC、BN或BC的材料组成,两个界面层的材料不必需相同。在一个变体中,所述第二界面可为通过在例如PyC、BN或BC的防脆材料与例如SiC的陶瓷材料交替的连续层制得的顺序界面。
[0027]所述第一界面层可具有不多于50纳米的厚度,且优选具有至少10纳米的厚度,而所述第二界面层具有优选不小于100纳米的厚度。
[0028]所述复合材料部件可特别为CMC材料部件,其中热解的固体残留物颗粒和基体由陶瓷组成。
[0029]本发明能通过阅读非限制性的表示并参照附图的如下描述更好地理解,其中:
[0030]图1显示本发明的方法的一个实施方案中的连续步骤;
[0031]图2为显示界面和基体在根据本发明获得的复合材料部件中的纤维上的形成的闻度图不;以及
[0032]图3绘制了显示根据本发明和根据现有技术获得的复合材料的样品的伸长行为的曲线。
[0033]所述方法的第一步(10)包括提供制造纤维预成型体的纤维结构,该纤维结构适于制造具有给定形状的复合材料。所述纤维结构可具有多种形式,如:
[0034]?二维(2D)织物;
[0035].通过3D编织或多层编织获得的三维(3D)织物;
[0036].织带;
[0037].针织;
[0038].毛毡;和
[0039]?纱或纤维束的单向(UD)片,或者通过在不同方向上重叠多个UD片并例如通过缝合、通过化学粘结剂或通过针刺将所述UD片粘结在一起而获得的多向(nD)片。
[0040]也可能使用由多个重叠的织物、织带、针织、毛毡、片等的层组成的纤维结构,所述层例如通过缝合、通过植入纱或刚性元件,或通过针刺粘结在一起。
[0041]构成纤维结构的纤维为耐火纤维,即由陶瓷组成的纤维,例如由碳化硅(SiC)、碳纤维,或耐火氧化物的真正纤维(例如氧化铝(A1203))组成的纤维。
[0042]在步骤12中,小厚度的第一界面层在纤维结构的纤维上形成。为了保持纤维结构的可变形性,选择所述第一界面层的厚度为不多于100纳米(nm),且优选不多于50nm。为了保持如下详述的第一界面层的功能,其厚度优选不小于10nm。
[0043]所述第一界面层的材料有利地选自热解碳(PyC)、氮化硼(BN),或掺硼碳(BC)。该第一界面层通过化学气相渗透(CVI)形成。用于形成PyC、BN或BC的沉积物的CVI法是已知的。对于沉积PyC或BN,可参考上述文献US4752503。对于BC,即包含约5%至20%的B (其余为C)的体系的CVI沉积,有可能使用含有如下组分的混合物的反应气体:B的前体三氯化硼(BC13)、C的前体丙烷(C3H8),和形成还原剂和稀释气体的氢气(H2),特别如文献US6068930 所描述。
[0044] 在第一界面层形成之后,将纤维结构用含有为碳或陶瓷前体的固结树脂的液体组合物浸溃(步骤14)。为了该目的,将纤维结构浸入含有树脂和通常所用的溶剂的浴中。在排干之后,在炉中进行干燥。所述干燥可伴随树脂的预固化或部分固化。由于这种预固化提供另外的刚性,因此若完全进行预固化,则该预固化需要保持有限的从而保持其上已形成第一界面层的纤维结构的足够的可变形性。
[0045]能使用其他已知的浸溃技术,如通过将纤维结构穿过连续浸溃机来制备预浸溃的还料、灌注浸溃(infusion impregnation),或通过树脂传递模塑(RTM)的真正浸溃。
[0046]选择固结树脂以确保在热解之后该树脂留下足以固结随后制得的纤维预成型体的碳或陶瓷的残留物。
[0047]碳前体树脂可选自酚醛树脂和环氧树脂。
[0048]陶瓷前体树脂可例如为:碳化硅(SiC)的前体聚碳硅烷树脂;或SiCO的前体聚硅氧烧;或SiCNB的前体聚硼碳娃氮烧(polyborocarbosilazane)树脂。
[0049]在浸溃之后,构成待制部件的纤维增强件并具有其形状基本上对应于所述部件形状的纤维预成型体通过在支撑工具的协助下将纤维结构成形(步骤16)而获得。
[0050]纤维结构的成形可包括覆盖(draping)纤维结构或者覆盖从纤维结构上切割的层片或板的操作。可制造切断(cuts)或切口(incisions)以促进需要相对大量的变形的覆盖。
[0051 ] 纤维结构的成形也可包括折叠纤维结构的部分的操作,所述纤维结构的部分例如位于在制造纤维结构时形成的未粘结区域的任一侧的部分,或者在整个纤维结构制造的切断的任一侧的部分。
[0052]支撑工具可由刚性模具和模具盖构成,在刚性模具和模具盖之间将纤维预成型体成形。
[0053]所述支撑工具也可由芯模或成形器和可能的挠性外套构成,在应用外套之前纤维结构或纤维结构层片通过被覆盖在芯模上而被成形。
[0054]若需要,纤维预成型体的成形可伴随纤维结构的压缩以获得纤维在待制造的部件的复合材料中相对较高体积分数。
[0055]在将预成型体成形之后,树脂被固化,或者若树脂已被预固化,则树脂固化完成(步骤18),所述预成型体保持于支撑工具中。
[0056]之后,进行热处理以热解树脂(步骤20)。
[0057]热解在例如约900°C至1000°C的温度下进行。有利地,在将通过固化的树脂被固结的预成型体从支撑工具取出之后,在温度上升(该温度上升实际上先于形成所述第二界面层)过程中在烘箱中进行热解,该烘箱当所述层通过CVI (如下所述)获得时用于形成第
二界面层。
[0058]在步骤22中,第二界面层在固结的纤维预成型体上形成,所述第二界面层覆盖第一界面层和由热解树脂得到的碳或陶瓷颗粒的不连续固体残留物。
[0059]为了进行所需的功能,所述第二界面层具有优选不小于100纳米的厚度。
[0060]所述第二界面层的材料可选自PyC、BN或BC,应理解第二界面层的材料可不同于第一界面层的材料。在一个变体中,可通过如PyC、BN或BC的防脆层的单个层的交替沉积以及如SiC的陶瓷材料的单个层的沉积形成顺序的第二界面层,每一单个层具有非常小的厚度,例如小于10纳米,如上述文献US5738951所述。所述第二界面层通过CVI形成。
[0061]在形成第二界面层之后,继续用基体将纤维预成型体致密化(步骤24)。[0062]致密化有利地通过CVI进行,优选自形成第二界面层继续进行,CVI法的参数和反应气体的性质适应于待形成的基体的性质。因此有可能使用相同的烘箱顺序进行热解固结树脂、形成第二界面层和致密化的操作。
[0063]在一个变体中,致密化能使用液体技术进行,即用含有待形成的基体的前体(通常为陶瓷或碳前体树脂)的液体组合物浸溃预成型体。浸溃接着是固化树脂和热解以获得所需的碳或陶瓷残留物,可能重复几次浸溃、固化和热解循环。
[0064]通过CVI形成的基体可为例如SiC基体的陶瓷基体,或者其可为如硅-硼-碳(S1-B-C)基体或碳化硼(B4C)基体的至少部分自愈合的基体,或者实际为具有交替的非愈合陶瓷和愈合陶瓷的基体相的顺序基体。可特别参考如下文献:FR2401888、US5246736、US5965266、US6068930 和 US6291058。
[0065]通过CVI形成的基体可为碳基体,通过CVI制造碳基体是公知的。
[0066]如图2非常图解式地所示,复合材料部件由此获得,其中每个纤维30被连续涂布于具有相对较小厚度的第一连续界面层32中,由热解固结树脂的固体残留物构成的形成不连续固结相34的碳或陶瓷颗粒介于所述第一界面层32和所述第二连续界面层36之间。通过CVI获得的基体38覆盖所述第二界面层。
[0067]当纤维10和固结相34由陶瓷组成时,由于这能够使复合材料脆化(特别是固结相和纤维由SiC组成),所述第一界面层32起到避免固结相过于牢固粘附于纤维的作用。
[0068]当纤维10为碳纤维且固结相34由陶瓷或碳组成时,所述第一界面层32促进了固结相固定在纤维上。
[0069]第二界面层36的厚度不小于100纳米,但在100纳米以上时该厚度可取决于基体38的性质较大或较小。
[0070]因此,具有陶瓷纤维,特别是SiC纤维,和非愈合(例如SiC)或愈合的陶瓷基体的厚度为100纳米至几百纳米的第二界面层可足以确保所需的防脆功能。
[0071]具有由碳组成的纤维和非愈合或愈合的陶瓷基体的第二界面层36的厚度可达到或甚至超过I微米(μ m),所需的功能同样为防脆功能。
[0072]对于具有碳基体的碳纤维,第二界面层36的厚度可达到或超过I μ m。第二界面层的功能可为改进复合材料的氧化行为,在此情况下所述第二界面层优选由BN或BC组成,或者为重复BN/SiC或BC/SiC顺序η次(其中η不小于2)的顺序形式。
[0073]实施例1 (根据本发明)
[0074]复合材料部件如下制造:
[0075].由日本供应商Nippon Carbon提供的名为“Nicalon”的SiC纤维制造织造的多
层纤维结构;
[0076].使用CVI形成厚度为约50纳米的PyC的第一界面层;
[0077]?用在甲基-乙基-甲酮中的聚硅氧烷树脂溶液浸溃所述纤维结构;
[0078]?干燥(无预固化);
[0079].通过在支撑上 覆盖多个浸溃的纤维结构的层片并在真空袋中覆盖制造纤维预成型体;
[0080].在由支撑和真空袋形成的工具内在真空中固化树脂以获得固结的预成型体;以及[0081]?从工具中移出所述固结的预成型体,并在约1000°C下热解树脂,热解在CVI致密化烘箱中进行,其中顺序进行如下步骤:
[0082].使用CVI由BC形成厚度等于约200纳米的第二界面层;以及
[0083].使用CVI用S1-B-C型自愈合陶瓷基体致密化。
[0084]实施例2 (用于比较)
[0085]程序与实施例1相同,但不制备第二界面层。
[0086]实施例3 (用于比较)
[0087]程序与实施例1相同,但使用厚度约为150纳米的第一界面层且不形成第二界面层。
[0088]在实施例1中,发现浸溃的纤维结构显示良好的变形能力,即使未使用该能力以与实施例3进行比较。
[0089]对根据实施例1、2和3获得的复合材料部件的样品进行牵引试验。
[0090]图3中的曲线1、II和III显示了施用的应力σ和测量至断裂的相对伸长ε之间的关系。
[0091 ] 可发现实施例1和III的材料具有基本上相同的机械行为,而实施例11的材料特别脆性。
[0092] 因此,在保持制造用于形状复杂的复合材料部件的纤维预成型体的可能性的同时,通过使用利用液体技术的固结,本发明的方法使得保持材料的非脆行为成为可能。
一种热结构复合材料部件制作方法
- 专利详情
- 全文pdf
- 权力要求
- 说明书
- 法律状态
查看更多专利详情
下载专利文献
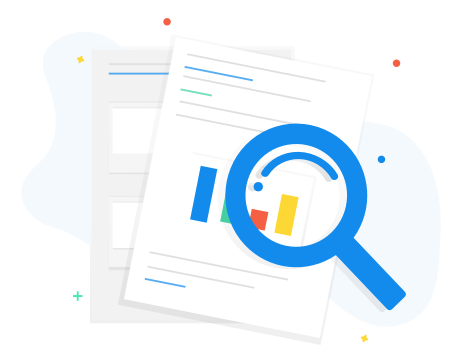
下载专利
同类推荐
-
E·菲利普, E·布永E·菲利普, E·布永E·菲利普, E·布永杨雪平李小成, 周超李贺军
您可能感兴趣的专利
-
方宗哲, 林宰演刘友举D·J·默克莱伊D·J·默克莱伊O·米尔盖, R·L·M·戈斯米尼O·米尔盖, R·L·M·戈斯米尼
专利相关信息
-
C·汉松廖寄乔王春燕袁远, 杨群伊凡·W·翁, 杰拉尔德·W·瓦尔克