整体式空心涡轮叶片陶瓷铸型型芯烧结蠕变控制的方法[0002]空心涡轮叶片作为燃气轮机和航空发动机的第一关键部位,其制造质量直接影响发动机的综合性能。传统叶片采用熔模铸造的方法,精度低,生产周期长,制造成本高。而基于光固化成型和凝胶注模技术的型芯型壳一体化的空心涡轮叶片陶瓷铸型的制造方法,克服了上述缺点,具有广泛的应用前景。但通过上述工艺制造铸型的过程中,由于型芯结构细长,质地较脆,容易发生偏移或者断裂等现象。这种现象对于预烧结过程中的U型型芯尤为明显。预烧过程中,陶瓷颗粒相互堆叠,颗粒间几乎没有烧结,铸型强度较低,而U型型芯一端固定,另一端为自由端,刚度偏低,高温保温时蠕变现象明显。所以预烧结过程中U型型芯的蠕变是影响铸型精度的主要因素。采用耐高温合金定位销或陶瓷辅助型芯固定U型型芯底部,增加型芯刚度,可以用来抑制蠕变,但这种方法破坏了叶片铸型内部结构完整性并增加了制造的难度。所以探求一种在不改变叶片铸型内部结构和不增加制造难度的前提下,控制铸型型芯烧结蠕变的方法具有十分重要的意义。
[0003]本发明的目的在于克服上述现有技术的缺点,提供了一种整体式空心涡轮叶片陶瓷铸型型芯烧结蠕变控制的方法,该方法可以在不改变叶片铸型内部结构及制造难度的前提下,控制铸型型芯烧结蠕变。[0004]为达到上述目的,本发明所述的整体式空心涡轮叶片陶瓷铸型型芯烧结蠕变控制的方法包括以下步骤:以涡轮叶片底面作为基准平面绘制初始陶瓷铸型模具,并根据所述初始陶瓷铸型模具制备初始陶瓷铸型,然后将该初始陶瓷铸型在炉膛中的方位作为初始铸型方位,选取所述初始铸型方位下的整套型芯中U型型芯作为优化对象,再以U型型芯的重心及两端面的面心为顶点构成空间三角形,将所述空间三角形所在的空间平面记作重心面。通过改变初始陶瓷铸型相对于水平面的方位,使得重心面垂直于水平面,且在该空间三角形中重心相对于两端面面心的力矩平衡,得二次铸型方位,然后根据二次铸型方位绘制最终陶瓷铸型模具,再根据最终陶瓷铸型模具制备铸型树脂模具,然后给铸型树脂模具内灌注陶瓷浆料,得陶瓷铸型胚体,所述陶瓷铸型胚体再经冷冻干燥、预烧结、脱脂、浸溃强化及烧结,得整体式空心涡轮叶片陶瓷铸型。[0005]根据最终陶瓷铸型模具利用光固化成型技术制备铸型树脂模具。[0006]利用凝胶注模技术给铸型树脂模具内灌注陶瓷浆料。[0007]通过旋转的方法改变初始陶瓷铸型相对于水平面的方位,使得重心面垂直于水平面,且在该空间三角形中重心相对于两端面面心的力矩平衡。
[0008]本发明具有以下有益效果:[0009]本发明所述的整体式空心涡轮叶片陶瓷铸型型芯烧结蠕变控制的方法在制备整体式空心涡轮叶片陶瓷铸型的过程中,以U型型芯的重心及两端面的面心为端点构成空间三角形,将空间三角形所处的平面记作重心面,通过改变初始陶瓷铸型相对于水平面的方位,使得重心面垂直与水平面,且在该空间三角形中重心相对于两端面面心的力矩平衡,得二次铸型方位,然后根据二次铸型方位制备整体式空心涡轮叶片陶瓷铸型。在制备过程中,通过重心面垂直于水平面来抑制U型型芯朝铸型叶盆叶背向的蠕变,通过空间三角形中的重心相对于两端面面心的力矩平衡来抑制U型型芯朝铸型前缘和尾缘向的蠕变,从而在不改变叶片铸型内部结构及制造难度的前提下,控制铸型型芯烧结蠕变,进而提高空心涡轮叶片铸型制造的精度及成品率。
[0010]下面对本发明做进一步详细描述:
[0011]本发明所述的整体式空心涡轮叶片陶瓷铸型型芯烧结蠕变控制的方法包括以下步骤:以涡轮叶片底面作为基准平面绘制初始陶瓷铸型模具,并根据所述初始陶瓷铸型模具制备初始陶瓷铸型,然后将该初始陶瓷铸型在炉膛中相对于水平面的方位作为初始铸型方位,选取所述初始铸型方位下的整套型芯中U型型芯作为优化对象,再以U型型芯的重心及两端面的面心为顶点构成空间三角形,将所述空间三角形所在的平面记作重心面。通过改变初始陶瓷铸型相对于水平面的方位,使得重心面垂直于水平面,且在该三角形中重心相对于两端面面心的力矩平衡,得二次铸型方位,然后根据二次铸型方位绘制最终陶瓷铸型模具,再根据最终陶瓷铸型模具制备铸型树脂模具,然后给铸型树脂模具内灌注陶瓷浆料,得陶瓷铸型胚体,所述陶瓷铸型胚体再经冷冻干燥、预烧结、脱脂、浸溃强化及烧结,得整体式空心涡轮叶片陶瓷铸型。
[0012]需要说明的是,根据最终陶瓷铸型模具利用光固化成型技术制备铸型树脂模具;利用凝胶注模技术给铸型树脂模具内灌注陶瓷浆料;通过旋转的方法改变初始陶瓷铸型相对于水平面的方位,使得重心面垂直于水平面,且在该空间三角形中重心相对于两端面面心的力矩平衡。
[0013]实施例一
[0014]以某型航空发动机叶片铸型为例,初始铸型模具设计完成后,将U型型芯抽取出进行分析,U型型芯长为70mm,平均长径比为25。
[0015]初始优化,以U型型芯两端面的面心和重心为顶点建立空间三角形,空间三角形所在平面称为重心面,重心面的法向量为:el = (0.7863,-0.6173,-0.0283),Z向分量不为0,即重心面不垂直水平面,将此U型型芯以坐标原点为旋转中心,以X轴为旋转轴旋转角度
整体式空心涡轮叶片陶瓷铸型型芯烧结蠕变控制的方法
- 专利详情
- 全文pdf
- 权力要求
- 说明书
- 法律状态
查看更多专利详情
下载专利文献
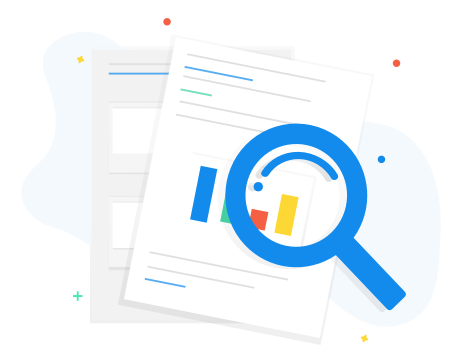
下载专利
同类推荐
-
李涤尘名取荣治刘升逑汤玉斐杨建
您可能感兴趣的专利
-
杨建陈秀丽陈秀丽陈秀丽
专利相关信息
-
王红云王红云周延春