一种快速制备超高强α半水石膏的方法及反应釜的制作方法 [0002]石膏材料具有悠久的使用历史,至今仍为重要的胶凝材料。半水石膏是制备石膏基制品的原材料,有α半水石膏和β半水石膏两种。其中,β半水石膏产量大,但其制备的制品强度很低,而α半水石膏可以具有规则的外形,标准稠度需水量较β半水石膏要低很多,制品结构致密,孔隙率,强度高,因此具有越来越广泛的应用,特别在模型、精密铸造等领域具有不可替代的作用。目前,α半水石膏主要存在三个问题:一个是基本都关注于晶体形貌的控制,即制备短柱状的晶体,但是,根据研究,α半水石膏的性能不仅与颗粒形貌有关,还与晶体的粒度大小及级配密切相关;二是,现有的工艺和装备制备的α半水石膏虽然形貌理想,但是颗粒粗大,这就使得制备的石膏制品强度并不太高,只有30Mpa左右并且用其制备的石膏制品细腻度不够;三,在加入转晶剂以调控形貌的同时,使得转化开始温度提升了近30°C,这就导致能耗增大,对反应器要求提高,同时升温时间大幅度增加,延长了生产周期,成本大。因此,现有α半水石膏的制备工艺,一方面通过控制α半水石膏形貌,使其具有规则外形,减少标准稠度需水量;另一方面为了降低粒度大小,优化粒度级配,在α半水石膏制备之后还要进行粉磨又破坏了部分晶体的规则形貌使得标准稠度需水量又有增加的趋势,强度受到限制。为了降低转化温度,采用大浓度的盐溶液如NaCl溶液,浓度高达20%以上,一方面生产成本增加,另外制得的α半水石膏还需要进行清洗,工艺繁杂,产品质量也难以保证。
[0003]本发明的目的在于克服现有技术的缺点与不足,提供一种快速制备超高强α半水石膏的方法。 [0004]本发明的目的还在于提供一种实现上述方法的反应釜。 [0005]本发明的目的通过下述技术方案实现:
[0006]一种快速制备超高强α半水石膏的方法,包括如下步骤:
[0007](I)水、转晶剂和易溶钙盐或易溶硫酸盐按照一定组成配制成0.5-5% (质量百分比)盐溶液,其中,转晶剂浓度0.2-1% (质量百分比)。
[0008](2)配制的盐溶液与粉状二水石膏按照1:0.5-2 (质量比)比例配制成料浆并加热到 90-100。。。
[0009](3)将热的料浆加到内部设有挡板的反应釜中,于110-150°C、100-800转/分钟的转速下保温0.2-1.0小时。浆体在100-800转/分钟高速旋转下保持悬浮,并与反应釜中的挡板碰撞。
[0010](4)反应后的半水石膏晶浆通过脱水、烘干即得高强α半水石膏成品。
[0011]步骤(1)中所述的转晶剂优选为丁二酸、柠檬酸、柠檬酸钠等中的至少一种。
[0012]步骤(1)中所述的易溶钙盐优选为氯化钙、硝酸钙等中的至少一种;所述的易溶硫酸盐优选为硫酸钠、硫酸钾等中的至少一种。
[0013]一种实现上述方法的反应釜,主要由釜体、夹套加热装置、搅拌装置和测控装置组成;釜体内部设有挡板,挡板垂直面与浆体旋转方向垂直,使得高速旋转的浆体与挡板碰撞,产生大量晶屑作为晶种能够大幅度增加晶体的数量,从而使得晶体细度降低。挡板的高度、数量可以根据需要进行调整。
[0014]更优选的,所述的反应釜主要由釜体、夹套加热装置、搅拌装置和测控装置组成。釜体的顶端设有加料口,釜体内部设有钢制挡板,釜体的底部设有出料口。夹套加热装置包裹着釜体底部和四周,夹套加热装置底部有进入口、上方有排出口,导热油或高温蒸汽由进入口进入通过排出口排出对釜体快速加热。搅拌装置包括搅拌头、搅拌轴、搅拌桨,通过高速搅拌使浆体保持悬浮旋转与与挡板碰撞。测控装置包括测温装置和取样装置,均从釜体顶端伸入到釜体内部,测温装置可以测得釜体内部温度并反馈给夹套加热装置进行调节温度,取样装置在反应进程中进行取样分析。
[0015]使用上述反应釜快速制备超高强α半水石膏的方法,包括如下步骤:
[0016](I)将配制好的90-100°C的料浆通过反应釜加料口加入到釜体内。
[0017](2)料浆在搅拌装置的作用下以100-800转/分钟高速旋转并保持悬浮,并在夹套加热装置作用下加热升到110-150°C并保温0.2-1.0小时。浆体在100-800转/分钟高速旋转下保持悬浮,并与釜体的挡板碰撞。
[0018](3)通过取样装置取出浆液,分析反应程度;当二水石膏完全反应后,反应获得的半水石膏晶浆通过反应釜出料口排出。
[0019](4)半水石膏晶浆通过脱水、烘干即得高强α半水石膏成品。
[0020]步骤(1)中料浆加入到釜体的填充度优选为50-90%。
[0021]本发明主要针对现有α半水石膏生产工艺的不足,从两个方面进行创新性改进:
[0022]一、采用低浓度(质量百分比小于5% )的易溶钙盐(如氯化钙、硝酸钙)或者易溶硫酸盐(如硫酸钠、硫酸钾等)溶液,降低二水石膏和半水石膏的转化温度。硫酸钙是一种微溶物质,其一定条件下,溶度积为一常数。即使低浓度的钙盐或硫酸盐溶液也会使得硫酸钙的平衡溶解度就会大幅度降低,这样半水石膏的过饱和度大幅度增加,进而就会降低α半水石膏的转化温度(不加时在为140°C左右,盐溶液浓度为1.2%时为125°C )。不仅降低了生产能耗,也减少高温、高压对设备的要求,另外就是可以增大晶体的生长速率,使得反应周期变短(从4个小时左右降低到I个小时以内)。
[0023]二、对反应釜进改造,在内部引入了挡板,增加了半水石膏的二次成核速率,降低了细度。根据对溶液介质二水石膏制备α半水石膏的研究,半水石膏成核方式主要是二次成核。二次成核速率主要决定于晶体与搅拌桨、晶体与器壁、晶体与晶体之间的碰撞几率及能量。在晶浆浓度一定的条件下,现有生产工艺为了提升二次成核速率唯一的方法就是提高搅拌速率。但是,搅拌速率的提高是有一定限度的,并且,搅拌速率提高到一定程度后其对二次成核速率的影响变化不大。本发明在反应釜中引入了多个挡板,挡板垂直于釜壁的一面也垂直于浆体旋转的方向。这样,在浆体快速旋转的时候,其与挡板垂直碰撞后速率变为零,碰撞能量远远大于传统反应釜中任何形式的碰撞,这样能够更多的碎屑并作为晶种生长为新的晶体,进而大幅度降低半水石膏细度,优化其粒度分布,可以使得2小时干抗压强度从30Mpa提升到50Mpa以上。
[0024]图1是本发明快速制备超高强α半水石膏的反应釜的结构图;其中,1:釜体,1-1:加料口,1-2:挡板,1-3:出料口,2:夹套加热装置,2-1:进入口,2-2:排出口,3:搅拌装置,3-1:搅拌头,3-2:搅拌轴,3-3:搅拌桨,4:测控装置,4-1:测温装置,4_2:取样装置。
[0025]图2是实施例1-5制备的超高强α半水石膏的粒度分布图。
[0026]下面结合具体实施例对本发明做进一步详细的描述,但本发明的实施方式不限于此。
[0027]—种快速制备超高强α半水石膏的反应釜的结构图如图1所示,主要由釜体1、夹套加热装置2、搅拌装置3和测控装置4组成。釜体I的顶端设有加料口 1-1,釜体I内部设有钢制挡板1_2(挡板1-2垂直面与浆体旋转方向垂直,使得高速旋转的浆体与挡板
1-2碰撞,产生大量晶屑作为晶种能够大幅度增加晶体的数量,从而使得晶体细度降低;挡板1-2的高度、数量可以根据需要进行调整。),釜体I的底部设有出料口 1-3。夹套加热装置2包裹着釜体I底部和四周,夹套加热装置2底部有进入口 2-1、上方有排出口 2-2,导热油或高温蒸汽由进入口 2-1进入通过排出口 2-2排出对釜体I快速加热。搅拌装置3包括搅拌头3-1、搅拌轴3-2、搅拌桨3-3,通过高速搅拌使浆体保持悬浮旋转与与挡板1-2碰撞。测控装置4包括测温装置 4-1和取样装置4-2,均从釜体I顶端伸入到釜体I内部,测温装置4-1可以测得釜体内部温度并反馈给夹套加热装置2进行调节温度,取样装置4-2在反应进程中进行取样分析。
[0028]使用上述反应釜快速制备超高强α半水石膏的方法,包括如下步骤:
[0029](I)将配制好的90_100°C的料浆通过反应釜加料口 1-1加入到釜体I内并使得填充度为50-90%。
[0030](2)料浆在搅拌装置3的作用下以100-800转/分钟高速旋转并保持悬浮,并在夹套加热装置2作用下(导热油或高温蒸汽由进入口 4进入通过排出口 5排出对釜体I快速加热)加热升到110-150°C并保温0.2-1.0小时。浆体在100-800转/分钟高速旋转下保持悬浮,并与釜体I的挡板1-2碰撞。
[0031](3)在达到预定时间后通过取样装置4-2取出浆液,通过快速分离干燥并进行形貌观察分析反应程度。当二水石膏完全反应后,反应获得的半水石膏晶浆通过反应釜出料口 1-3排入到装料桶。
[0032](4)装料桶温度控制在95°C以上;晶浆通过装料桶下部排料管不断排入到高速离心机内进行快速脱水,离心机内的温度保持在100 V左右。
[0033](5)快速脱水后的湿粉料通过干燥设备快速干燥后即获得成品。离心分离的液体作为配制二水石膏料浆的盐溶液进行循环使用。
[0034]下述实施例均为使用上述装置和方法制备超高强α半水石膏。
[0035]实施例1
[0036]盐溶液中为0.55% (质量百分比)0&(:12、转晶剂为0.2% (质量百分比)丁二酸,盐溶液与二水天然石膏按照1:1 (质量比)配制成料浆并加热到95°c。料浆在反应釜中的填充度为60%,搅拌速率为400转/分钟,反应温度130°C,反应时间为0.8小时。反应结束后,浆体通过脱水、烘干即得超高强α半水石膏成品。超高强α半水石膏d0.5为26.5 μ m,D [4,3]为31.3 μ m (粒度分布见图2),标准稠度需水量为29.5 %,2小时干抗压强度 50.1Mpa0
[0037]实施例2
[0038]盐溶液中为Ca(NO3)2浓度为1.6% (质量百分比)、转晶剂为0.5%柠檬酸(质量百分比),盐溶液与二水天然石膏按照1:1(质量比)配制成料浆并加热到90-100°C。料浆在反应釜中的填充度为80%,搅拌速率为200转/分钟,反应温度145°C,反应时间为I小时。反应结束后,浆体通过脱水、烘干即得超高强α半水石膏成品。超高强α半水石膏d0.5为34.0 μ m,D[4,3]为36.9 μ m(粒度分布见图2),标准稠度需水量为29.5%,2小时干抗压强度51.0Mpa。
[0039]实施例3
[0040]盐溶液中为Na2SO4浓度为L 6% (质量百分比)、转晶剂为0.5%柠檬酸(质量百分比),盐溶液与二水脱硫石膏按照1: 1.5 (质量比)配制成料浆并加热到95°C。料浆在反应釜中的填充度为80%,搅拌速率为500转/分钟,反应温度125°C,反应时间为0.5小时。反应结束后,浆体通过脱水、烘干即得超高强α半水石膏成品。超高强α半水石膏d0.5为24.3μπι,D[4, 3]为26.5 μ m(粒度分布见图2),标准稠度需水量为28.5%,2小时干抗压强度53.3Mpa。
[0041]实施例4
[0042]盐溶液中为K2SO4浓度为3.5% (质量百分比)、转晶剂为0.9%柠檬酸钠(质量百分比),盐溶液与二水脱硫石膏按照1: 1.5 (质量比)配制成料浆并加热到95°C。料浆在反应釜中的填充度为80%,搅拌速率为800转/分钟,反应温度115°C,反应时间为0.4小时。反应结束后,浆体通过脱水、烘干即得超高强α半水石膏成品。超高强α半水石膏d0.5为24.1 μ m, D[4,3]为25.9 μ m(粒度分布见图2),标准稠度需水量为28.5%,2小时干抗压强度56.8Mpa。
[0043]实施例5
[0044]盐溶液中为CaCl2浓度为1.1 % (质量百分比)、转晶剂为0.1 %丁二酸(质量百分比)和0.3%柠檬酸(质量百分比),盐溶液与二水脱硫石膏按照1:2(质量比)配制成料浆并加热到95°C。料浆在反应釜中的填充度为80%,搅拌速率为400转/分钟,反应温度1351:,反应时间为0.3小时。反应结束后,浆体通过脱水、烘干即得超高强α半水石膏成品。超高强α半水石膏d0.5为20.6 μ m(粒度分布见图2),D[4,3]为23.2 μ m,标准稠度需水量为29.0%,2小时干抗压强度61.6Mpa。
[0045]上述实施例为本发明较佳的实施方式,但本发明的实施方式并不受上述实施例的限制,其他的任何未背离本发明的精神实质与原理下所作的改变、修饰、替代、组合、简化,均应为等效的置换方式,都包含在本发明的保护范围之内。
一种快速制备超高强α半水石膏的方法及反应釜制作方法
- 专利详情
- 全文pdf
- 权力要求
- 说明书
- 法律状态
查看更多专利详情
下载专利文献
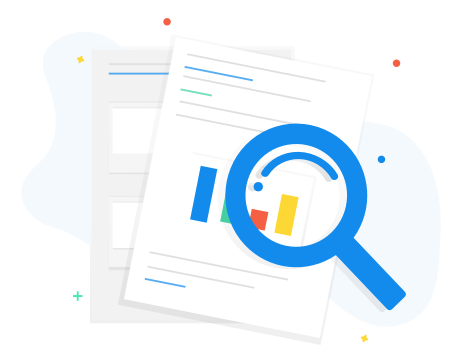
下载专利
同类推荐
您可能感兴趣的专利
-
康德余, 胡盼盼康德余, 胡盼盼孙红芳, 杨庆兰宋卫, 高品孙红芳, 杨庆兰
专利相关信息
-
唐明亮陈凯, 陈树德李明照