专利名称:双面双色印染布制造方法及该印染布在服装上应用的制作方法 双面具有不同色泽的纺织面料可用作服装、室内装饰用品和其它工业用品,其价格可以高出一般单色织物许多倍,具有较高的附加值。早期,人们采用不同色泽的几种纱线,织成双层组织结构的双面多色织物,或将两块不同色泽的织物通过粘合剂粘合在一起制成复合织物,使两面具有不同的色调。这种双层组织结构的双面双色或多色织物仅限于厚织物,并且制作过程麻烦。后来,人们曾尝试采用双面双色染料染色或印花方法,虽使用了各种方法防止一面的染料渗透到另一面上,使染料仅固着在一面,但该方法极其困难。关于目前提供的双面多色纺织物可列举出以下一些缺点(1)双层组织结构的双面多色织物,仅限于厚织物。(2)粘合结构的双面多色织物,也仅限于厚织物。(3)在(1)、(2)两种情况下,都需要应用分开的工艺染出的纤维。(4)这种将织物两面分开染色的技术,时常不能完全防止施加在织物一面的染料渗透到织物的背面去。
本发明的目的之一在于提供一种能有效地控制制备双面双色印染布时所出现的双色串色问题,从而避免产生色花和串色病疵。本发明的目的之二是采用本方法制造的双面双色印染布制成的服装,经处理后具有柔软的质感、独特的仿旧和双色复合风格,赋予服装穿着舒适性和美观的视觉效果,以迎合服装休闲和个性的需要。本发明所提出的技术解决方案是这样的一种双面双色印染布制造方法,首先采用组成织物纤维的适用染料染色,再用涂料满地印花制得,其制备工艺流程包括(1)前处理,采用冷轧堆前处理或连续煮漂前处理; (2)染底色,采用还原染料或活性染料染底色;(3)涂料满地印花。对于厚织物,采用冷轧堆前处理,其工艺步骤包括(1)制备冷轧堆前处理液冷轧堆前处理的主要药剂及其用量100%浓度NaOH 60-70g/L,100%浓度H2O215-20g/L,HLD-1 7-8g/L,HLD-2 7-8g/L,络合分散剂 1-2g/L,其余水;按上述配比拌匀制得冷轧堆前处理液,在35±3℃温度下冷轧堆置18-20小时;(2)洗水冷轧堆前处理后用净洗剂3.5-4.5g/L溶液进行水洗;半成品的毛效控制在7-8cm/30min,半成品的PH值控制在6.5-7.5,布面均匀一致。对于薄织物,采用连续煮漂前处理,其工艺步骤包括(1)制备连续煮漂前处理药液煮练液主要组分及其用量100%浓度NaOH 40-50g/L,透芯油 5-6g/L,络合分散剂 1-2g/L,其余 水;漂白液组份及其用量100%浓度H2O23-3.5g/L,稳定剂 4-4.5g/L,透芯油 5-6g/L,络合分散剂 1-2g/L,其余 水;按上述配比拌匀,分别制得煮练液和漂白液;
(2)连续煮漂前处理工艺流程及条件平幅进布,在90-95℃热水浸轧,之后在60-65℃温度及0.08mpa压力下轧煮练液,然后在100-105℃温度下进入R-BOX箱汽蒸堆置50-70min,之后在90-95℃温度下进行三格高效平洗,轧一格冷流水,在室温及0.08mpa压力下轧氧漂液,然后在100-105℃温度下进入R-BOX箱汽蒸堆置50-70min,再在85-90℃温度下进行三格高效平洗,最后烘干落布。
采用还原染料染底色,其工艺步骤包括(1)制备染液、还原液和氧化液染液主要药剂及其用量还原染料X 0.01-120g/L,防泳移剂PA8-12g/L,渗透剂NOR 1-3g/L;其余 水;还原液主要药剂及其用量100%纯度保险粉 23-28g/L,100%浓度NaOH 28-32g/L,其余 水;氧化液主要药剂及其用量100%浓度H2O21-2g/L,Na2CO35-7g/L,其余 水;按上述配比分别制得染液、还原液和氧化液;(2)染底色工艺流程及条件浸轨染液,然后烘干,再浸轧还原液,在101-102℃温度下汽蒸50-60S,冷洗水,在氧化液内氧化,经透风,在95-100℃温度下且加入3.5-4.5g/L净洗剂的皂液中皂煮,然后热水洗,最后烘干。
采用活性染料染底色,其工艺步骤包括(1)制备染液和固色液染液主要药剂及其用量活性染料Y 0.1-90g/L,
防泳移剂PA 6-10g/L,渗透剂NOR3-7g/L,防染盐S 2-4g/L,其余 水;固色液主要药剂及其用量Na2CO320-40g/L,100%浓度NaOH5-7g/L,NaCl 150-220g/L,其余 水;按上述配比分别制得染液和固色液;(2)染底色工艺流程及条件浸轧染液,然后烘干,再浸轧固色液,在100-102℃温度汽蒸40-60s,洗水,在含醋酸1.8-2.2g/L的酸液中酸洗,在95-100℃温度下且加入3.5-4.5g/L净洗剂的皂液中皂煮,然后,热水洗,最后烘干。
所述涂料满地印花工艺步骤包括(1)制备涂料满地印花色浆涂料满地印花色浆主要药剂及其用量涂料W 0.01-100g/L,粘合剂 5-50g/L,增稠剂一路得素HIT 1.5-2.5g/L,其余 水;粘度控制在40-50dpas按上述配比制得涂料满地印花色浆;(2)涂料满地印花工艺流程及条件对涂料满地印花药剂调浆,其粘度控制在40-50dpas,进行印花,在130-140℃温度下焙烘4-5min,进入后整理。
所述粘合剂为聚丙烯酸酯类或聚氨酯类。
所述涂料满地印花色浆中加入乳化剂,该乳化剂选择聚乙二醇醚衍生物,用量为1-5g/L。
用上述方法制得的双面双色印染布制成服装进行酵素水洗,在下列工艺条件下均匀脱色处理酵素6000L 0.5-3%浓度,浴比 18-10,PH值 4.5-5.5,温度 40-50℃,时间 30-60min。
织物经染料染色后,再将其一面用其他色调的染料满地印花时,染料有渗透到织物背面的倾向。正如大家在工艺中所熟知的,如果织物结构紧密,渗透就困难;如果织物结构较稀松,渗透就容易。另外,着色材料毛细管效应也会影响染料的渗透,毛细管效应强,渗透容易;毛细管效应弱,渗透难。根据纤维的密度和种类不同,可能会不同程度地引起双面双色印染布的串色,由于渗透是局部的,因此造成布面颜色不均匀,这些是染整行业中所说的色花和串色病疵。
本发明的关键技术是应用涂料对颜色具有较好遮盖性,对染色织物进行涂料满地印花制备双面双色印染布,并对涂料满地印花渗透影响因素,通过前处理、染色和印花工艺加以控制,保证本发明顺利实施。
若厚重织物采取连续煮漂时,汽蒸堆置时间不宜过长,宜控制在12分钟内,否则易形成堆置折痕,后道工序难以消除。对布面要求较高的灯心绒,本发明优选采取冷轧堆前处理。对较厚重织物,宜采用二煮一漂前处理工艺,以确保退浆干净,煮练透彻(灯心绒不用丝光)。
涂料满地印花产品对布面光洁度要求高,前处理烧毛要干净。如采用气体烧毛机,要注意火口清洁,不能有杂质堵塞火口;火焰要均匀,防止烧毛条花或烧毛不净。烧毛次数二正二反或二正一反。本发明优选接触式烧毛机、铜板或磁棒烧毛机,布面光洁度好。对府绸类薄织物如133×72、130×70等,由于布面纱节多,可优选加一道磨毛工序,以解决印后水洗露浅色点的现象。
前处理半成品的毛效不宜过高。毛效过高,涂料色浆渗透过快,布面均匀性欠佳,易形成布面花,会导致色浆透底,影响织物印制风格。因此,本发明选择前处理半成品的毛效为7-8cm/30min。
前处理半成品的PH值过高,则耐气候牢度差的颜色在存放过程中容易发生变色现象PH值过低,则织物在后工序的焙烘时,会发生脆损,使织物强力下降。本发明半成品的PH值优选在6.5-7.5,布面色泽均匀一致。
在涂料满地印花之前先染底色,再通过涂料满地印花,可得到双面双色效果的印花布。印花底色宜采用浅色,本发明底色选用还原染料或活性染料染色。
一般情况下,还原染料或活性染料与纤维的亲和力比较小,容易造成初开机时色浅,染色过程中还原液或固色液轧槽里染料浓度越来越大,造成前浅后深。为避免此现象,根据颜色的深浅,在还原液或固色液中加入0.1-150g/L的染液,最好加入50-100%g/L的染液。
活性染料做浅色时,汽蒸时颜色因受还原气体作用,易变色,不稳定,为避免此种现象发生,需加入0.1-10g/L防染盐S到染液中,本发明优选2-4g/L。
染色后水洗要彻底,以避免织物上的残留杂质对涂料满地印花质量的影响。
印前对布面平整度要求高,本发明优选轧水、滚筒烘燥、打卷工序。
涂料满地印花工艺对粘合剂的选择很重要,一般可选择的粘合剂有聚丙烯酸酯类和聚氨酯类粘合剂。在保证干、湿摩擦牢度基础上,力求选择手感软的粘合剂,同时要求粘合剂具有一定的耐电解质,避免满地色上易产生色花和不规则的条花。洗脱色产品,粘合剂的用量特别重要。粘合剂用量过高,牢度太好,洗水不掉色,失去仿旧风格;用量过少,牢度太差,洗水就会掉色太多。本发明优选粘合剂用量5-50g/L,结合汽蒸处理,可以得到脱色20-70%效果。
涂料满地印花色浆对耐电解质要求特别高,应尽量选择耐电解质好的增稠剂。为此,本发明优选路得素HIT,也可以同时加入乳化剂,例如聚乙二醇醚衍生物,以提高色浆体系耐电解质性能。
对地色较深的织物,为了避免对涂料的串色或降低涂料的鲜艳度,可考虑适当添加些消光剂或遮光剂,例如钛白粉。
焙烘温度不能太高,以免交联过度,不利于后道脱色,所以本发明优选为130-140℃,焙烘4-5min。
为了改善涂料满地印花织物的的手感,可在涂料色浆中加入少量柔软剂,例如优选阴离子或非离子型有机硅类。
与现有技术相比,本发明具有如下显著效果(1)本发明是采用适用染料染色,再用涂料满地印花的方法制备双面双色印染布,通过对前处理、染底色和涂料满地印花工艺的控制,有效地克服了在制备双面双色印染布时可能会出现的色花和双色串色的问题。
(2)本发明双面双色印染布制造方法具有简单、易控制和织物适应性广等优点。
(3)用本发明方法制备的双面双色印染布制成的服装,通过酵素水洗、均匀脱色处理后,具有柔软的质感,同时具有独特的仿旧和双色复合风格,赋予了服装穿着舒适性和美观的视觉效果,迎合了服装休闲和个性的需要。
通过下面实施例对本发明作进一步详细阐述。
实施例1(1)冷轧堆前处理冷轧堆前处理药剂及其用量(g/L)NaOH(100%) 60,H2O2(100%) 15,HLD-1 7,HLD-2 7,络合分散剂 1,其余水;工艺流程及条件工艺流程及条件坯检→拼缝→冷轧堆置(18-20小时,35±3℃)→洗水(净洗剂3.5-4.5g/L)。半成品的毛效宜控制在7-8cm/30min,半成品的PH值宜控制在6.5-7.5,布面均匀一致。
(2)采用还原染料染底色(悬浮体轧染)染液药剂及其用量(g/L)还原染料X60,
防泳移剂PA10,渗透剂2,其余 水;还原液药剂及其用量(g/L)保险粉(100%) 25,NaOH(100%) 30,其余 水;氧化液药剂及其用量(g/L)H2O2(100%)1,Na2CO35,其余 水;按上述配比分别制得染液、还原液和氧化液。
工艺流程及条件浸轧染液→烘干→浸轧还原液→汽蒸(101-102℃,50-60s)→冷洗水→浸轧氧化液→透风-皂煮(95℃-100℃,净洗剂3.5-4.5g/L)→热水洗→烘干。
(3)涂料满地印花色浆药剂及其用量(g/L)涂料W 30,粘合剂NF-2 5,路得素HIT(增稠剂) 1.5,其余 水;涂料满地印花工艺流程及条件调浆(粘度控制在40-50dPas)→印花→焙烘(130℃-140℃,4-5min)→后整理。
实施例2(1)冷轧堆前处理冷轧堆前处理药剂及其用量(g/L)NaOH(100%) 65,H2O2(100%) 18,HLD-17.5,HLD-27.5,络合分散剂 1.5,其余 水;工艺流程及条件与例1相同(2)采用还原染料染底色(悬浮体轧染)染液药剂及其用量(g/L)还原染料X120,防泳移剂PA 12,渗透剂 3,其余 水;还原液药剂及其用量(g/L)保险粉(100%)28,NaOH(100%) 32,其余 水;工艺流程及条件与例1相同(3)涂料满地印花色浆药剂及其用量(g/L)涂料W0.01,粘合剂NF-2 30,路得素HIT(增稠剂)2,其余 水;涂料满地印花工艺流程及条件与例1相同实施例3(1)冷轧堆前处理冷轧堆前处理药剂及其用量(g/L)NaOH(100%) 70,H2O2(100%)20,HLD-1 8,HLD-2 8,络合分散剂2,其余 水;工艺流程及条件与例1相同(2)采用还原染料染底色(悬浮体轧染)染液药剂及其用量(g/L)还原染料X 0.01,防泳移剂PA8,渗透剂1,其余 水;还原液药剂及其用量(g/L)保险粉(100%) 23,NaOH(100%) 28,其余 水;工艺流程及条件与例1相同(3)涂料满地印花色浆药剂及其用量(g/L)涂料W 100,粘合剂NF-250,路得素HIT(增稠剂) 2.5,
其余 水;涂料满地印花工艺流程及条件与例1相同实施例4薄织物(例如府绸)双面双色印染布的制造方法(1)连续煮漂前处理,前处理药剂及其用量(g/L)煮炼液药液及其用量(g/L)NaOH(100%)40,透芯油 5,络合分散剂 1,其余 水;漂白液组份及其用量(g/L)H2O2(100%) 3.0,稳定剂 4.0,透芯油 5,络合分散剂 1,其余 水;工艺流程及条件平幅进布,→浸轧热水(90-95℃)→轧煮练液(60-65℃,0压力0.08mpa)R-BOX箱汽蒸堆置(100-105℃,50-70min)→三格高效平洗(90-95℃)→轧一格冷流水→轧氧漂液(室温,压力0.08mpa)R-BOX箱汽蒸堆置(100-105℃,50-70min)→三格高效平洗(85-90℃)→烘干落布。
织物丝光按常规丝光工艺进行,前处理半成品毛效宜控制在7-8cm/30min,半成品的PH值宜控制在6.5-7.5,布面均匀一致。
(2)采用活性染料染底色,染液药剂及其用量(g/L)活性染料Y0.1,防泳移剂PA 6,渗透剂NOR3,
防染盐S2,其余 水;固色液药剂及其用量(g/L)Na2CO320,NaOH(100%)5,NaCl 150,其余 水工艺流程及条件浸轧染液→烘干→浸轧固色液→汽蒸(00-102℃,40-60s)→洗水→酸洗(醋酸1.8-2.2g/L)→皂煮(95-100℃,净洗剂3.5-4.5g/L)→热水洗→烘干。
(4)涂料满地印花所述涂料满地印花工艺步骤包括色浆药剂及其用量(g/L)涂料W 0.01,粘合剂NF-2 5,增稠剂-路得素HIT 1.5,其余 水;涂料满地印花工艺及条件同实施例1。
实施例5薄织物(例如府绸)双面双色印染布的制造方法(1)连续煮漂前处理,前处理药剂及其用量(g/L)煮炼液药液及其用量(g/L)NaOH(100%) 45,透芯油 5.5,络合分散剂 1.5,其余水;漂白液组份及其用量(g/L)H2O2(100%) 3.2,稳定剂 4.3,
透芯油 5.5,络合分散剂 1.5,其余 水;工艺流程及条件与实施例4相同。
(2)采用活性染料染底色,染液药剂及其用量(g/L)活性染料Y 40,防泳移剂PA 8,渗透剂NOR 5,防染盐S 3,其余水;固色液药剂及其用量(g/L)Na2CO330,NaOH(100%) 6,NaCl200,其余水;工艺流程及条件与实施例4相同。
(4)涂料满地印花所述涂料满地印花工艺步骤包括色浆药剂及其用量(g/L)涂料W 20,粘合剂NF-2 25,增稠剂-路得素HIT2,其余水;涂料满地印花工艺及条件同实施例1。
实施例6薄织物(例如府绸)双面双色印染布的制造方法(1)连续煮漂前处理,前处理药剂及其用量(g/L)
煮炼液药液及其用量(g/L)NaOH(100%) 50,透芯油 6,络合分散剂 2,其余水;漂白液组份及其用量(g/L)H2O2(100%) 3.5,稳定剂 4.5,透芯油 6,络合分散剂 2,其余水;工艺流程及条件与实施例4相同。
(2)采用活性染料染底色,染液药剂及其用量(g/L)活性染料Y 90,防泳移剂PA 10,渗透剂NOR 7,防染盐S 4,其余水;固色液药剂及其用量(g/L)Na2CO340,NaOH(100%) 7,NaCl220,其余水;工艺流程及条件与实施例4相同。
(4)涂料满地印花所述涂料满地印花工艺步骤包括色浆药剂及其用量(g/L)涂料W 100,
粘合剂NF-2 50,增稠剂-路得素HIT 2.5,其余 水;涂料满地印花工艺及条件同实施例1。
实施例7将实施例1至6的方法制得的双面双色印染布制成的服装,进行酵素水洗,其工艺及条件酵素6000L0.5%浓度,浴比1∶8,PH值4.5,温度40℃,时间30min。经酵素水洗、均匀脱色处理后,服装具有柔软的质感,同时具有独特的仿旧和双色复合风格,赋予服装穿着舒适性和美观的视觉效果,迎合服装休闲和个性的需要。
实施例8将例1至6的方法制得的双面双色印染布制成的服装,进行酵素水洗,其工艺及条件酵素6000L1.5%浓度,浴比1∶9,PH值5,温度45℃,时间45min。处理工艺及效果与例7相同。
实施例9将例1至6的方法制得的双面双色印染布制成的服装,进行酵素水洗,其工艺及条件酵素6000L 3%浓度,浴比1∶10,PH值5.5,温度50℃,时间60min。处理工艺及效果与例7相同。
本发明公开了一种双面双色印染布制造方法及该印染布在服装上应用,它要解决的技术问题在于能有效地控制制备双面双色印染布时所出现的双色串色问题,从而避免产生色花和串色病疵;以及采用本方法制造的双面双色印染布制成的服装,经处理后具有柔软的质感、独特的仿旧和双色复合风格,赋予服装穿着舒适性和美观的视觉效果。为此,该双面双色印染布制造方法是先采用组成织物纤维的适用染料染色,再用涂料满地印花制得,其工艺流程为前处理,采用冷轧堆前处理或连续煮漂前处理;染底色,采用还原染料或活性染料染底色;涂料满地印花。用该产品制成的服装,需经酵素水洗、均匀脱色处理。
双面双色印染布制造方法及该印染布在服装上应用制作方法
- 专利详情
- 全文pdf
- 权力要求
- 说明书
- 法律状态
查看更多专利详情
下载专利文献
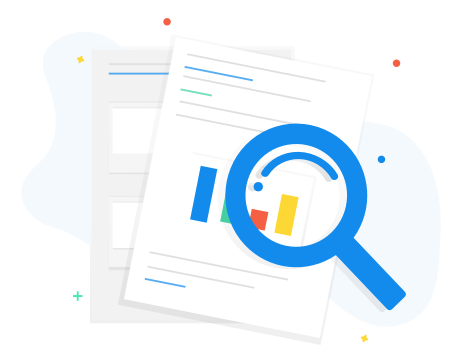
下载专利
同类推荐
-
钱平陈慰来陈慰来王新, 王桂英王英奎
您可能感兴趣的专利
-
王英奎王英奎J·H·阿伦斯J·H·阿伦斯J·H·阿伦斯蒂莫·皮沃斯基, 贝恩德·威尔维斯蒂莫·皮沃斯基, 贝恩德·威尔维斯
专利相关信息
-
蒂莫·皮沃斯基, 贝恩德·威尔维斯丘云灵, 熊玉李宗武吴健, 徐刘彬阿德里亚那·布里西奥, 阿德里亚那 布里西奥卢兰达·马尔舒埃塔·埃雷乌, 恩里克·莫伊斯·瓦尔斯卢兰达·马尔舒埃塔·埃雷乌, 恩里克·莫伊斯·瓦尔斯