一种窄黑边高效多晶硅片的制备方法[0002]目前,多晶硅锭的制备方法主要是利用GTSolar提供的定向凝固系统进行制备,该方法通常包括加热、熔化、长晶、退火和冷却等步骤。在凝固长晶过程中,通过对上端温度控制和侧边保温罩开度进行控制,使得熔融硅液在坩埚底部获得足够的过冷度凝固结晶。但由于在长晶初期,坩埚底部属于各向同性结构,硅液结晶时初始形核不能得到有效控制,形核过程极易形成位错,导致晶向无规律分布、晶界呈现无规则状态,晶粒分布不均匀(晶粒从几十微米到十几厘米),因此通过常规方式获得的多晶硅锭效率不高,越来越难以满足市场对于高效率硅片的需求; [0003]针对常规铸锭方式所生产的多晶硅锭位错密度高、晶界无规则分布,晶粒分布不均匀的问题,国内部分铸锭厂家借鉴了单晶的生长原理,在坩埚底部铺设单晶板材等方法,利用硅料半熔工艺制得了晶粒尺寸较大的类单晶硅片,其中最为知名的如协鑫的鑫单晶,凤凰光伏的类单晶等。虽然利用半熔单晶板材引晶生长技术,可获得类似于单晶的高效多晶硅片,但存在以下缺点:1)类单晶硅片所用的单晶板材加工难度和成本高,导致类单晶硅片生产成本偏高;2)类单晶生长工艺所制备的类单晶硅片单张硅片上虽然绝大部分为单晶,但仍存在少部分的多晶晶粒,所制备的电池片有“花片”现象,组件生产企业难以接受;3)类单晶硅片生产使用的仍为普通的石英坩埚,边缘杂质扩散大,效率难以进一步的提闻。
[0004]本发明所要解决的技术问题是提供一种窄黑边高效多晶硅片的制备方法,该制备方法可制得一种侧边杂质扩散宽度窄、制造成本低且转换效率高的多晶硅片,且操作简单,生产成本低,适于大规模生产。[0005]为解决上述技术问题,本发明的技术方案是:[0006]一种窄黑边高效多晶硅片的制备方法,其制备方法如下:[0007]1)先将粒度为50~150目、纯度> 99.995%的单晶坩埚用高纯石英砂和粒度为200~400目、纯度≥99.99%的多晶坩埚用高纯石英砂以1:1~1:5的重量比混合均匀得石英砂,再将石英砂与粘结剂按1:2~1:4的重量比混合、搅拌均匀后得高纯石英砂浆料,在普通石英坩埚的四壁刷涂或喷涂一层高纯石英砂浆料涂层,并将刷涂或喷涂完高纯石英砂浆料涂层的坩埚在800°C条件下快速烘干lh,再通过喷涂的方式在坩埚内部的高纯石英砂涂层上喷涂一层氮化硅浆料形成氮化硅涂层,所述使用的单晶坩埚用高纯砂与多晶坩埚用高纯砂的金属离子总含量在20ppm以内,所述高纯石英砂衆料涂层厚度大于2mm,所述粘结剂为去离子水和高纯硅溶胶中的一种或两种的组合,其中Fe元素的含量小于5ppm,所述氮化硅浆料由水与α相含量> 90%的氮化硅粉按1:3.5~1:4.5,重量比混合而成,所述氮化硅涂层的厚度为40~70um,喷涂温度为55°C~65°C ;[0008]2)装料,在坩埚底部铺设一层起高效锭诱导生长作用的籽晶层后装入硅料纯度^ 6N的固体硅料,所述的籽晶层为碎的单晶、碎的多晶或原生硅料中的一种或几种,籽晶层厚度≥5mm ;
[0009]3)加热,闭合坩埚保温罩,加热坩埚到1500°C时逐步打开隔热笼,待坩埚温度升高到1540°C时将隔热笼高度控制在6cm,同时,利用石英棒测试籽晶层厚度,当籽晶层厚度在5mm以上时降低温度,进入长晶状态,此时籽晶层上方的固体硅料完全熔化成熔融状态的硅料,籽晶层仅部分熔化;
[0010]4)控制坩埚内部的温度梯度,使得坩埚内部形成由下到上的垂直温度梯度,使得熔融状态的硅料利用底部铺设的籽晶层诱导生长,制得窄黑边高效硅锭,在此过程中,过冷度为-1OK~-35K ;
[0011]5)通过钢线与磨料研磨相配合的方式将步骤(4)中制得的大锭的窄黑边高效硅锭切割为截面尺寸为156_*156_的小方砖后,再利用钢线与磨料研磨相配合的方式将上述小方砖切割为156mm*156mm* (180~200) um的薄片。
[0012]上述一种窄黑边高效多晶硅片的制备方法,其中,所述粘结剂为去离子水和高纯硅溶胶按1:5~1:10的重量比混合制备而成,所述高纯硅溶胶固相含量为10%。
[0013]本发明的有益效果为:
[0014]I)本发明制得的硅片光电转换效率大幅提升,在电池工艺相同的情况下电池光电转换效率相较普通多晶硅片光电转换效率提升0.4 %~0.7 %,平均光电转换效率达到17.6%~17,8% ;
[0015]2)本发明制得的硅锭侧壁晶砖由于杂质扩散所造成的杂质富集层(简称为黑边)宽度由普通晶砖的≥16mm大幅降低到< 6mm ;
[0016]3)本发明的制备方法可制得一种侧边杂质扩散宽度窄、制造成本低且转换效率高的多晶硅片,且操作简单,生产成本低,适于大规模生产,该制备方法制备的窄黑边高效多晶硅片,晶粒细小且分布均匀,对应晶砖少子寿命高且低少子寿命区域少,对应硅片由于坩埚杂质扩散所造成的黑边宽度窄。
[0017]4)如图2所示,本发明所制得的晶砖底部晶粒细小且分布均匀,几乎无枝状晶和孪晶产生;如图3所示,本发明所铸的硅锭边部晶砖红区宽度基本在4mm以内,同时普通坩埚所铸锭边部晶砖侧边红区宽度在16mm以上;如图4所示,本发明所铸锭边部晶砖所切硅片黑边宽度与少子图谱一致基本在4_以内,同时普通坩埚所铸锭边部晶砖所切硅片黑边宽度与少子图谱一致基本在16mm以上,说明利用高纯坩埚所铸锭对于侧边晶砖的杂质扩散较少,同时利用引晶法制备的高效锭内部整体缺陷较少。
[0018]图1为本发明实施例一中的坩埚侧壁高纯涂层、“籽晶层”铺设和装料过程示意图;
[0019]图2为典型窄黑边高效硅锭晶砖底部截面照片;
[0020]图3为典型利用本发明高纯涂层坩埚和非高纯坩埚涂层所铸大锭侧边晶砖少子检测对比图谱;
[0021]图4为典型利用本发明高纯涂层坩埚和非高纯涂层坩埚所铸大锭侧边晶砖所切硅片PL图像对比图。
[0022]以下通过具体实施例对本发明的作进一步详细的说明。
[0023]如图所示图1为坩埚四壁高纯涂层设置和装料的示意图,其中,I为坩埚母体,2为高纯石英砂浆料涂层,3为氮化硅涂层,4籽晶层,5为固体硅料
[0024]实例一
[0025]一种窄黑边高效多晶硅片的制备方法,包括以下步骤:
[0026]I)先将金属杂质浓度低于20ppm、Fe含量低于5ppm的、粒度为50~150目、纯度≥99.995%的单晶坩埚用高纯石英砂250g与金属杂质浓度低于20ppm、Fe含量低于5ppm的、粒度为200~400目、纯度≥99.99%的多晶坩埚用高纯石英砂250g混合均匀得石英砂,再将混合后的石英砂与高纯硅溶胶500g混合搅拌均匀后得高纯石英砂浆料,在普通石英坩埚(I)的四壁刷涂一层高纯石英砂浆料涂层(2),并将刷涂完高纯石英砂浆料涂层的坩埚在800°C条件下快速烘干lh,再通过喷涂的方式在坩埚内部的高纯石英砂涂层2上喷涂一层氮化硅浆料形成氮化硅涂层(3),所述使用的单晶坩埚用高纯砂与多晶坩埚用高纯砂的金属离子总含量在20ppm以内,所述高纯石英砂浆料涂层厚度为4mm,所述粘结剂为去离子水和高纯硅溶胶中的一种或两种,其中Fe元素的含量小于5ppm,所述氮化硅浆料由水与α相含量≥90%的氮化硅粉按1:4,重量比混合而成,所述氮化硅涂层的厚度为60um,喷涂温度为60°C ;
[0027]2)装料,在坩埚底部铺设一层单颗碎片直径< Icm的碎的多晶,平铺于坩埚底部并压实形成起高效锭诱导生长作用的籽晶层,籽晶层的厚度为20mm,在籽晶层上装入500kg的硅料纯度≥6N的固体硅料;
[0028]3)加热,闭合坩埚保温罩,加热坩埚到1500°C时逐步打开隔热笼,待坩埚温度升高到1540°C时将隔热笼高度控制在6cm,同时,利用石英棒测试籽晶层厚度,当籽晶层厚度在IOmm时降低温度,进入长晶状态,此时籽晶层上方的固体硅料完全熔化成熔融状态的硅料,籽晶层仅部分熔化;
[0029]4)控制坩埚内部的温度梯度,使得坩埚内部形成由下到上的垂直温度梯度,逐步打开保温罩,使其抬升到8cm左右,并将温度降低到1420°C,使得坩埚底部温度降低,坩埚底部硅液处于过冷状态,并利用底部“籽晶层”诱导结晶制得窄黑边高效硅锭,在此过程中,过冷度为-25K ;
[0030]5)通过钢线与磨料研磨相配合的方式将步骤(4)中制得的大锭的窄黑边高效硅锭切割为截面尺寸为156_*156_的小方砖后,再利用钢线与磨料研磨相配合的方式将上述小方砖切割为156mm*156mm*200um的薄片。
[0031]实例二
[0032]一种窄黑边高效多晶硅片的制备方法,包括以下步骤:
[0033]I)先将金属杂质浓度低于20ppm、Fe含量低于5ppm的、粒度为50~150目、纯度≥99.995%的单晶?甘祸用高纯石英砂100g与金属杂质浓度低于20ppm、Fe含量低于5ppm的、粒度为200~400目、纯度≥99.99%的多晶坩埚用高纯石英砂400g混合均匀得石英砂,将250g高纯硅溶胶与250g去离子水混合均匀得粘结剂,再将石英砂与粘结剂混合搅拌均匀后得高纯石英砂浆料,在普通石英坩埚(1)的四壁刷涂一层高纯石英砂浆料涂层(2),并将刷涂完高纯石英砂浆料涂层的坩埚在800°C条件下快速烘干lh,再通过喷涂的方式在坩埚内部的高纯石英砂涂层2上喷涂一层氮化硅浆料形成氮化硅涂层(3),所述使用的单晶坩埚用高纯砂与多晶坩埚用高纯砂的金属离子总含量在20ppm以内,所述高纯石英砂浆料涂层厚度为3_,所述粘结剂为去离子水和高纯硅溶胶中的一种或两种,其中Fe元素的含量小于5ppm,所述氮化硅浆料由水与α相含量≥ 90%的氮化硅粉按1:4,重量比混合而成,所述氮化硅涂层的厚度为50um,喷涂温度为65°C ;
[0034]2)装料,在坩埚底部铺设一层单颗碎片直径< 1cm的碎的多晶,平铺于坩埚底部并压实形成起高效锭诱导生长作用的籽晶层,籽晶层的厚度为20mm,在籽晶层上装入500kg的硅料纯度≥6N的固体硅料;
[0035]3)加热,闭合坩埚保温罩,加热坩埚到1500°C时逐步打开隔热笼,待坩埚温度升高到1540°C时将隔热笼高度控制在6cm,同时,利用石英棒测试籽晶层厚度,当籽晶层厚度在IOmm时降低温度,进入长晶状态,此时籽晶层上方的固体硅料完全熔化成熔融状态的硅料,籽晶层仅部分熔化;
[0036]4)控制坩埚内部的温度梯度,使得坩埚内部形成由下到上的垂直温度梯度,逐步打开保温罩,使其抬升到8cm左右,并将温度降低到1420°C,使得坩埚底部温度降低,坩埚底部硅液处于过冷状态,并利用底部“籽晶层”诱导结晶制得窄黑边高效硅锭,在此过程中,过冷度为-20K ;
[0037]5)通过钢线与磨料研磨相配合的方式将步骤(4)中制得的大锭的窄黑边高效硅锭切割为截面尺寸为156_*156_的小方砖后,再利用钢线与磨料研磨相配合的方式将上述小方砖切割为156mm*156mm*200um的薄片。
[0038]实例三
[0039]一种窄黑边高效多晶硅片的制备方法,包括以下步骤:
[0040]1)先将金属杂质浓度低于20ppm、Fe含量低于5ppm的、粒度为200~400目、纯度> 99.99 %的多晶坩埚用高纯石英砂500g与500g去离子水混合均匀得高纯石英砂浆料,在普通石英坩埚(1)的四壁刷涂一层高纯石英砂浆料涂层(2),并将刷涂完高纯石英砂浆料涂层的坩埚在800°C条件下快速烘干lh,再通过喷涂的方式在坩埚内部的高纯石英砂涂层2上喷涂一层氮化硅浆料形成氮化硅涂层(3),所述使用的单晶坩埚用高纯砂与多晶坩埚用高纯砂的金属离子总含量在20ppm以内,所述高纯石英砂浆料涂层厚度为3.5mm,所述粘结剂为去离子水和高纯硅溶胶中的一种或两种,其中Fe元素的含量小于5ppm,所述氮化硅浆料由水与α相含量>90%的氮化硅粉按1:4,重量比混合而成,所述氮化硅涂层的厚度为50um,喷涂温度为60°C ;
[0041]2)装料,在坩埚底部铺设一层单颗碎片直径< Icm的碎的多晶,平铺于坩埚底部并压实形成起高效锭诱导生长作用的籽晶层,籽晶层的厚度为20mm,在籽晶层上装入500kg的硅料纯度≥6N的固体硅料;
[0042]3)加热,闭合坩埚保温罩,加热坩埚到1500°C时逐步打开隔热笼,待坩埚温度升高到1540°C时将隔热笼高度控制在6cm,同时,利用石英棒测试籽晶层厚度,当籽晶层厚度在IOmm时降低温度,进入长晶状态,此时籽晶层上方的固体硅料完全熔化成熔融状态的硅料,籽晶层仅部分熔化;
[0043]4)控制坩埚内部的温度梯度,使得坩埚内部形成由下到上的垂直温度梯度,逐步打开保温罩,使其抬升到8cm左右,并将温度降低到1420°C,使得坩埚底部温度降低,坩埚底部硅液处于过冷状态,并利用底部“籽晶层”诱导结晶制得窄黑边高效硅锭,在此过程中,过冷度为-15K ;
[0044]5)通过钢线与磨料研磨相配合的方式将步骤(4)中制得的大锭的窄黑边高效硅锭切割为截面尺寸为156mm*156mm的小方砖后,再利用钢线与磨料研磨相配合的方式将上述小方砖切割为156mm*156mm*200um的薄片。
[0045]实例四
[0046]—种窄黑边高效多晶硅片的制备方法,包括以下步骤:
[0047]I)先将金属杂质浓度低于20ppm、Fe含量低于5ppm的、粒度为50~150目、纯度≥99.995%的单晶坩埚用高纯石英砂250g与金属杂质浓度低于20ppm、Fe含量低于5ppm的、粒度为200~400目、纯度≥99.99%的多晶坩埚用高纯石英砂250g混合均匀得石英砂,再将石英砂与500g高纯硅溶胶混合搅拌均匀后得高纯石英砂浆料,在普通石英坩埚
(I)的四壁刷涂一层高纯石英砂浆料涂层(2),并将刷涂完高纯石英砂浆料涂层的坩埚在800°C条件下快速烘干lh,再通过喷涂的方式在坩埚内部的高纯石英砂涂层2上喷涂一层氮化硅浆料形成氮化硅涂层(3),所述使用的单晶坩埚用高纯砂与多晶坩埚用高纯砂的金属离子总含量在20ppm以内,所述高纯石英砂浆料涂层厚度为4.5mm,所述粘结剂为去离子水和高纯硅溶胶中的一种或两种,其中Fe元素的含量小于5ppm,所述氮化硅浆料由水与α相含量>90%的氮化硅粉按1:4,重量比混合而成,所述氮化硅涂层的厚度为60um,喷涂温度为60°C ;
[0048]2)装料,在坩埚底部铺设一层单颗碎片直径< Icm的碎的多晶,平铺于坩埚底部并压实形成起高效锭诱导生长作用的籽晶层,籽晶层的厚度为20mm,在籽晶层上装入500kg的硅料纯度≥6N的固体硅料;
[0049]3)加热,闭合坩埚保温罩,加热坩埚到1500°C时逐步打开隔热笼,待坩埚温度升高到1540°C时将隔热笼高度控制在6cm,同时,利用石英棒测试籽晶层厚度,当籽晶层厚度在IOmm时降低温度,进入长晶状态,此时籽晶层上方的固体硅料完全熔化成熔融状态的硅料,籽晶层仅部分熔化;
[0050]4)控制坩埚内部的温度梯度,使得坩埚内部形成由下到上的垂直温度梯度,逐步打开保温罩,使其抬升到8cm左右,并将温度降低到1420°C,使得坩埚底部温度降低,坩埚底部硅液处于过冷状态,并利用底部“籽晶层”诱导结晶制得窄黑边高效硅锭,在此过程中,过冷度为-25K ;
[0051]5)通过钢线与磨料研磨相配合的方式将步骤(4)中制得的大锭的窄黑边高效硅锭切割为截面尺寸为156_*156_的小方砖后,再利用钢线与磨料研磨相配合的方式将上述小方砖切割为156mm*156mm*200um的薄片。
[0052]本发明的有益效果为:
[0053]I)本发明制得的硅片光电转换效率大幅提升,在电池工艺相同的情况下电池光电转换效率相较普通多晶硅片光电转换效率提升0.4 %~0.7 %,平均光电转换效率达到17.6%~17,8% ;
[0054]2)本发明制得的硅锭侧壁晶砖由于杂质扩散所造成的杂质富集层(简称为黑边)宽度由普通晶砖的≥16mm大幅降低到< 6mm ;
[0055]3)本发明的制备方法可制得一种侧边杂质扩散宽度窄、制造成本低且转换效率高的多晶硅片,且操作简单,生产成本低,适于大规模生产。
[0056]4)如图2所示,本发明所制得的晶砖底部晶粒细小且分布均匀,几乎无枝状晶和孪晶产生;如图3所示,本发明所铸的硅锭边部晶砖红区宽度基本在4mm以内,同时普通坩埚所铸锭边部晶砖侧边红区宽度在16mm以上;如图4所示,本发明所铸锭边部晶砖所切硅片黑边宽度与少子图谱一致基本在4_以内,同时普通坩埚所铸锭边部晶砖所切硅片黑边宽度与少子图谱一致基本在16mm以上,说明利用高纯坩埚所铸锭对于侧边晶砖的杂质扩散较少,同时利用引晶法制备的高效锭内部整体缺陷较少。
[0057]将本发明实例一所得硅片,实例二所得硅片,实例三所得硅片,实例四所得硅片与两组普通方法所得硅片(即普通硅片一和普通硅片二)的电池光电转换效率以及杂质富集层(简称为黑边)宽度进行对比,实验结果如下:
[0058]
一种窄黑边高效多晶硅片的制备方法
- 专利详情
- 全文pdf
- 权力要求
- 说明书
- 法律状态
查看更多专利详情
下载专利文献
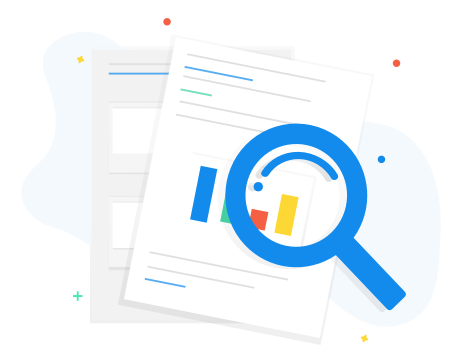
下载专利
同类推荐
-
刘明权倪刚, 李之瑞刘明权刘明权刘明权
您可能感兴趣的专利
-
王胜荣, 戚政权佐藤基树, 佐藤繁师德强杨中平, 彭代春杨中平, 彭代春杨中平, 彭代春
专利相关信息
-
杨中平, 彭代春戴煜