专利名称:可直接送粉的高效微纳复合粉体湿法球磨制备方法近年来,一种构建介观(微纳米级)新物质的技术---微纳米颗粒复合技术,引起了国内外专家学者的重视。微纳米颗粒复合技术,是将纳米颗粒包覆于微米颗粒表面或使其弥散分布在微米颗粒中制备具有微纳协同多功能效应微纳复合粉体的技术。微纳复合粉体的制备方法可分为机械法、气相法、液相法和固相法等四大类。其中,机械法尤其是湿法球磨法具有处理时间短、反应过程易控制、可连续批量生产且所需设备简单、通用、价廉等优点,在生产实践中得到了广泛应用。2007年,王宏宇等公开了一种纳米陶瓷/微米金属复合粉体的机械制备方法(ZL 200710024996. X),其核心思想是“以纳米·悬浮液作为球磨介质引入纳米粉体,基于湿法球磨制备微纳复合粉体”,较好地解决了纳米粉体易团聚造成微纳复合粉体中纳米颗粒的分散性差进而引起微纳复合粉体实际使用效果不好的问题。但是,在采用该方法制备微纳复合粉体时存在两方面的问题。其一,未充分考虑已市场化原粉形貌的多样性如市购微米原粉一般为多边形、股骨形或虽为球形但其表面粘附有大量的小颗粒等。如果直接使用这些市购微米原粉进行球磨复合,球磨复合过程中在球磨作用下从微米原粉上会脱落大量的细微颗粒,纳米悬浮液中的纳米颗粒优先与脱落的细微颗粒复合,导致主体微米粉表面实际复合的纳米颗粒较少;另一方面,存在诸如球磨复合过程中微米粉易沉降而造成微米粉参与复合几率较低,进而导致纳米悬浮液中的纳米颗粒不能充分与微米粉接触等问题。正是由于上述两方面的原因,采用该方法所制备的微纳复合粉体不能兼顾复合效果和直接送粉两方面的要求。若为了保证引入的纳米颗粒增强作用,所制备的微纳复合粉体中由于存在大量的细微颗粒在送粉过程中易堵塞粉管,难以满足热喷涂、激光熔覆等技术直接送粉的要求,只能采用如粘结铺粉或模压预置等方法,其工程实用性较差且所制备涂层品质不够理想;若为了满足热喷涂、激光熔覆等技术直接送粉的要求,将细微颗粒筛除后再使用,则由于其主体微米粉表面实际复合的纳米颗粒较少,造成引入的纳米颗粒增强作用又显不足。2012年5月,王宏宇等又提出了一种带有搅拌功能的制备微纳复合粉体用球磨罐(申请号201210131290. 4),解决了球磨过程微米粉易沉降造成微米粉参与复合几率较低的问题,但并未涉及由于微米原粉形貌多样性带来的问题。与此同时,大量实验表明,球磨复合过程中附加搅拌,减少了微米粉易沉降的现象,提高了微米粉参与复合的几率;但是,这种情况下所附加的搅拌,进一步地促使纳米悬浮液中纳米颗粒与从微米原粉上脱落的细微颗粒的复合,进而造成主体微米粉表面上包覆的纳米颗粒没有增加反而呈现减少趋势。所以,所制备的微纳复合粉体不能兼顾复合效果和直接送粉两方面要求的问题仍未得到解决。因此,到目前为止,尚未有一种可直接送粉的高复合效果微纳复合粉体(简称为高效微纳复合粉体,下同)湿法球磨制备方法可供使用,极大地制约了微纳复合粉体在表面工程等领域中的广泛应用。
本发明的目的是针对现有微纳复合粉体湿法球磨制备方法的不足,发明一种可直接送粉的高效微纳复合粉体湿法球磨制备方法,使所制备的微纳复合粉体能够兼顾复合效果和直接送粉两方面的要求,从而推动微纳复合粉体在表面工程等领域中的广泛应用。本发明的技术方案是 一种可直接送粉的高效微纳复合粉体湿法球磨制备方法,其特征是 首先,对微米原粉进行球磨预处理,以便消除微米原粉形貌的多样性对复合效果的影响,将球磨预处理后的微米原粉过筛,滤除从微米原粉上磨下的细微颗粒,获得预处理后的微米粉,所述的细微颗粒的粒径不大于微米原粉平均粒径的85% ; 其次,将纳米粉在乙醇或乙醇与去离子水的混合溶液中进行分散,制备分散稳定的纳米悬浮液; 再次,将按照所需配比称量好的预处理后的微米粉和分散稳定的纳米悬浮液置于球磨罐中混合并加入磨球,使球磨液体介质没过微米粉的表面后开始球磨复合,在球磨复合过程中对球磨罐中粉体进行连续搅拌或间歇搅拌; 最后,将球磨复合制备好的微纳复合粉体从球磨罐中取出,置于干燥箱中进行干燥,即可获得可直接送粉的高效微纳复合粉体。所述球磨预处理为将市购微米原粉置于球磨罐中,用乙醇作为球磨介质,磨球的直径相同或不同,不同直径的磨球比例不限,设置球磨转速200-400转/分钟、球料质量比5:1-10: I、球磨时间0. 5-8小时进行球磨,球磨后在干燥箱中对粉体进行干燥。所述过筛为将球磨预处理后的微米原粉置于分样筛中进行筛选,留在筛中的粉体即为预处理后的微米粉,所用分样筛筛孔的直径不大于所选微米原粉颗粒平均粒径的85%。所述分散稳定的纳米悬浮液为静置沉降I小时后无沉淀现象的纳米悬浮液。所述球磨复合所采用的球磨工艺参数为球磨转速200-400转/分钟、球料质量比10:1-20: I、球磨时间0. 5-1. 5小时,磨球的直径相同或不同,不同直径的磨球比例不限。所述球磨复合过程中的连续搅拌为采用带有搅拌功能的球磨罐,在球磨复合过程中对球磨罐内粉体进行搅拌。所述球磨复合过程中的间歇搅拌为采用通用球磨罐即无搅拌功能球磨罐,球磨3-9分钟后停机打开球磨罐手动搅拌至无明显固液分界后再继续球磨,如此反复,直至球磨累积时间等于设定球磨时间。所述微米原粉最好为金属粉体,所述纳米粉最好为陶瓷粉体或稀土氧化物粉体。本发明未涉及部分均与现有技术相同或可采用现有技术加以实现。本发明的有益效果
(I)本发明方法创造性地提出了对微米粉进行球磨预处理,消除了微米原粉形貌的多样性对复合效果的影响(市购微米原粉一般呈现多边形、股骨形或虽为球形但其表面粘附有细微小颗粒等,采用这些微米原粉制备微纳复合粉体时,将会在球磨复合过程中产生大量细微颗粒,使得纳米悬浮液中纳米颗粒优先与这些细微颗粒复合,进而造成主体微米粉上复合的纳米颗粒较少),大幅提高了纳米悬浮液中纳米颗粒与主体微米粉的复合效果,从而使所制备的微纳复合粉体兼顾复合效果和直接送粉两方面要求成为可能。(2)本发明方法采取了对微米原粉进行球磨预处理和球磨复合过程中附加搅拌两种增效措施,不仅改善了微纳复合粉体的复合效果,使所制备的微纳复合粉体中微米粉表面包覆的纳米粉占纳米粉原始添加量的90%以上;而且,微纳复合粉体表面上纳米颗粒分布的均匀性很好,同时其上纳米微团聚体无论数量还是尺寸均很小,能充分发挥纳米颗粒的增强作用,大幅提高了微纳复合粉体的实际使用效果。(3)本发明方法所制备的微纳复合粉体,在保证复合效果的前提下,其平均粒径仅略小于所选微米原粉且几乎不含细微颗粒,具有很好地粉体输送性能,能满足现有热喷涂、激光熔覆等技术直接送粉的要求,很好地拓展了微纳复合粉体的使用范围,进而推动了热喷涂、激光熔覆等表面工程技术的发展。 (4)本发明方法经过大量的实验获得了合适的微米原粉球磨预处理工艺参数和球磨复合工艺参数,不仅保证了市购微米原粉的利用率不低于75%,而且经过球磨预处理后的微米粉在球磨复合过程中几乎不再产生新的细微颗粒,有力地保证了所制备微纳复合粉体的复合效果和粉体输送性。换言之,只有采用本发明方法所述工艺参数,才能达到本发明所述目的。(5)本发明方法所需设备简单、通用、价廉,对原始微米粉和纳米粉的品质要求不高,是一种简单、易行、经济的微纳复合粉体制备方法,具有很强的工程价值和应用前景。
图I是本发明所述高效微纳复合粉体球磨制备方法过程框图。图2是本发明实施例I、实施例2、对比例I和对比例2所述微米原粉SEM形貌图。图3是本发明实施例I、实施例2和对比例2所述预处理后的微米粉SEM形貌图。图4是本发明所述可采用的带有搅拌功能的球磨罐结构示意图。图4中,I-环形橡胶垫、2-底部外壳、3-圆形橡胶垫、4-小型电动机、5-环形蓄电池、6-可控电源开关、7-紧固螺钉、8-密封套、9-L形密封环、10-0形密封圈、11-搅拌叶轮、12-锁紧螺钉、13-叶轮防护罩、14-球磨罐端盖、15-密封垫、16-球磨罐壳体、17-紧固螺钉、18-电源充电接口、19-球磨罐夹紧装置、20-球磨罐安装底座。图5是本发明实施例I所述微纳复合粉体高倍SEM形貌图。图6是本发明实施例I所述微纳复合粉体低倍SEM形貌图。图7是本发明对比例I所述微纳复合粉体高倍SEM形貌图。图8是本发明对比例I所述微纳复合粉体低倍SEM形貌图。图9是本发明对比例2所述微纳复合粉体高倍SEM形貌图。图10是本发明实施例4所述微米原粉SEM形貌图。
一种可直接送粉的高效微纳复合粉体湿法球磨制备方法。首先,对微米原粉进行球磨预处理,以便消除微米原粉形貌的多样性对复合效果的影响(市购微米原粉一般呈现多边形、股骨形或虽为球形但其表面粘附有细微小颗粒等,如图2所示,采用这些微米原粉制备微纳复合粉体时,将会在球磨复合过程中产生大量细微颗粒,使得纳米悬浮液中纳米颗粒优先与这些细微颗粒复合,进而造成主体微米粉上复合的纳米颗粒较少),将球磨预处理后的微米原粉过筛,滤除从微米原粉上磨下的细微颗粒,将粒径小于85%的微米原粉平均粒径的细微粉体筛除,获得预处理后的微米粉(图3);其次,将纳米粉在乙醇或乙醇与去离子水的混合溶液中进行分散, 制备分散稳定的纳米悬浮液,分散方法可采用如中国专利ZL200710133580. I的方法;再次,将按照所需配比称量好的预处理后的微米粉和分散稳定的纳米悬浮液置于球磨罐中混合并加入磨球,配比时所述的纳米粉体的重量一般不超过微米粉体质量的10%,球磨时液体介质的表面应高出微米粉体的表面,然后开始球磨复合,在球磨复合过程中对球磨罐中粉体采用图4所示的装置进行连续搅拌或采用常规的搅拌方法如手动搅拌进行间歇搅拌;最后,将球磨制备好的微纳复合粉体从球磨罐中取出,置于干燥箱中进行干燥,即可获得可直接送粉的高效微纳复合粉体。所述球磨预处理为将市购微米原粉置于球磨罐中,用乙醇作为球磨介质,设置球磨转速为200-400转/分钟、球料质量比5:1-10: I、球磨时间为0. 5-8小时进行球磨,球磨所用的球径可在4、6、10毫米三种规格中选取,可选一种、二种或三种球径的磨球,配比不限,试验研究发现,球磨时球径的选择对预处理效果影响不大,因此可任意选取。球磨后在干燥箱中进行干燥。所述过筛为将球磨预处理后的微米原粉置于分样筛中进行筛选,留在筛中的粉体即为预处理后的微米粉,所用分样筛的筛孔直径以不大于所购微米粉体平均粒径的85%为宜,常用的过滤筛的规格为200-500目(对应74-25微米)。所述分散稳定的纳米悬浮液是指静置沉降I小时后无沉淀现象的悬浮液。所述球磨复合所采用的球磨工艺参数为球磨转速为200-400转/分钟、球料质量比10:1-20: I、球磨时间为0. 5-1. 5小时,球磨复合所用的球径可在4、6、10毫米三种规格中选取,可选一种、二种或三种球径的磨球,配比不限,试验研究发现,球磨时球径的选择对球磨复合处理效果的影响也不大,因此可任意选取。所述球磨复合过程中的连续搅拌采用带有搅拌功能的球磨罐(图4),在球磨复合过程中利用搅拌叶轮11对球磨罐内粉体进行搅拌,搅拌叶轮11电机4驱动,电机由蓄电池5供电。所述球磨复合过程中的间歇搅拌其特征是,采用通用球磨罐即无搅拌功能球磨罐(一般为一中空圆筒),球磨3-9分钟后停机打开球磨罐手动搅拌至无明显固液分界后再继续球磨,如此反复,直至球磨累积时间等于设定球磨时间。具体实施时根据具体情况,所述微米原粉最好采用金属粉体,所述纳米粉最好采用陶瓷粉体或稀土氧化物粉体。以下是采用本发明方法所制备微纳复合粉体的实例,但不仅仅限于这些实例,对于不同规格(成分、种类、粒径等)的微、纳米粉体,只要采用本发明所述方法均可达到本发明的目的。实施例I :微米粉为平均粒径为75 ii m的NiCoCrAH合金粉,原粉呈球状但表面粘附有大量的小颗粒(图2),纳米粉为平均粒径为20nm的氧化铈粉体。首先,以乙醇为球磨介质对微米原粉进行球磨预处理,球磨预处理的工艺参数为球磨转速200转/分钟、球料比5: I、球磨时间2小时,将球磨预处理后的微米原粉用250目(对应61微米)分样筛过筛,获得表面光滑无粘附的预处理后微米粉(图3),称量预处理后的微米粉,其质量是预处理前的80% ;其次,将纳米粉在乙醇与去离子水混合溶液(乙醇与去离子水的比例为1:1)中进行分散,制备分散稳定的纳米悬浮液;再次,将按照所需配比称量好的预处理后的微米粉和分散稳定的纳米悬浮液置于球磨罐中混合并加入磨球,球磨时液体介质的表面应高出微米粉体的表面,然后开始球磨复合,所采用的球磨工艺参数为球磨转速250转/分钟、球料比15:1、球磨时间0. 5小时,在球磨复合过程中每球磨3分钟停机对球磨罐中粉体进行间歇搅拌;最后,将球磨制备好的微纳复合粉体从球磨罐中取出,置于干燥箱中进行干燥,即可获得可直接送粉的高效微纳复合粉体(图5)。从图5中可以看出,纳米粉在微米粉表面均匀分布且微团聚体无论尺寸还是数量都很小,与此同时,纳米粉几乎与微米粉完全复合,且微纳复合粉体中小颗粒含量极少,如图6所示,使用SPH-2/h型火焰喷涂枪送粉,所制备的微纳复合粉体输送顺畅无堵塞现象。对比例I :微米粉为平均粒径为75 ii m的NiCoCrAH合金粉,原粉呈球状但表面粘附有大量的小颗粒(图2),纳米粉为平均粒径为20nm的氧化铈粉体。首先,将纳米粉在乙醇与去离子水混合溶液(乙醇与去离子水的比例为1:1)中进行分散,制备分散稳定的纳米悬浮液;其次,将按照所需配比称量好的微米原粉和分散稳定的纳米悬浮液置于球磨罐中混合并加入磨球,球磨时液体介质的表面应高出微米粉体的表面,然后开始球磨复合,所采用的球磨工艺参数为球磨转速250转/分钟、球料比15: I、球磨时间0. 5小时,在球磨复合过程中每球磨3分钟停机对球磨罐中粉体进行间歇搅拌;最后,将球磨制备好的微纳复·合粉体从球磨罐中取出,置于干燥箱中进行干燥,即可获得微纳复合粉体(图7)。从图7中可以看出,微米粉表面上分布的纳米粉数量相对于实施例I所制备的微纳复合粉体要少得多,主要原因在于纳米悬浮液的纳米粉多数与球磨过程中脱落的小颗粒复合在一起,使用SPH-2/h型火焰喷涂枪送粉,所制备的微纳复合粉体由于存在大量的小颗粒(图8) —送即堵根本无法实现输送。对比例2 :微米粉为平均粒径为75 ii m的NiCoCrAH合金粉,原粉呈球状但表面粘附有大量的小颗粒(图2),纳米粉为平均粒径为20nm的氧化铈粉体。首先,以乙醇为球磨介质对微米原粉进行球磨预处理,球磨预处理的工艺参数为球磨转速200转/分钟、球料比5: I、球磨时间2小时,将球磨预处理后的微米原粉用250目(对应61微米)分样筛过筛,获得表面光滑无粘附的预处理后微米粉(图3);其次,将纳米粉在乙醇与去离子水混合溶液(乙醇与去离子水的比例为1:1)中进行分散,制备分散稳定的纳米悬浮液;再次,将按照所需配比称量好的预处理后的微米粉和分散稳定的纳米悬浮液置于球磨罐中混合并加入磨球,球磨时液体介质的表面应高出微米粉体的表面,然后开始球磨复合,所采用的球磨工艺参数为球磨转速250转/分钟、球料比15: I、球磨时间为0. 5小时,在球磨复合过程中不进行搅拌;最后,将球磨制备好的微纳复合粉体从球磨罐中取出,置于干燥箱中进行干燥,即可获得可直接送粉的微纳复合粉体(图9)。从图9中可以看出,微米粉表面上分布的纳米粉数量少于实施例I所制备的微纳复合粉体但多于对比例I所制备的微纳复合粉体,而且纳米粉的分布均匀性较差,与此同时微米粉表面上微团聚体尺寸有所增多增大,使用SPH-2/h型火焰喷涂枪送粉,所制备的微纳复合粉体输送较为顺畅,偶尔会发生堵塞现象。实施例2 :微米粉为平均粒径为75 ii m的NiCoCrAH合金粉,原粉呈球状但表面粘附有大量的小颗粒(图2),纳米粉为平均粒径为20nm的氧化铈粉体。首先,以乙醇为球磨介质对微米原粉进行球磨预处理,球磨预处理的工艺参数为球磨转速200转/分钟、球料比5:1、球磨时间2小时,将球磨预处理后的微米原粉用250目(对应61微米)分样筛过筛,获得表面光滑无粘附的预处理后微米粉(图3);其次,将纳米粉在乙醇与去离子水混合溶液(乙醇与去离子水的比例为1:1)中进行分散,制备分散稳定的纳米悬浮液;再次,将按照所需配比称量好的预处理后的微米粉和分散稳定的纳米悬浮液置于带有搅拌功能的球磨罐(图
4)中混合并加入磨球,球磨时液体介质的表面应高出微米粉体的表面,然后开始球磨复合,所采用的球磨工艺参数为球磨转速250转/分钟、球料比15: I、球磨时间0. 5小时,在球磨复合过程中对球磨罐中粉体进行连续搅拌;最后,将球磨制备好的微纳复合粉体从球磨罐中取出,置于干燥箱中进行干燥,即可获得可直接送粉的高效微纳复合粉体,所制备微纳复合粉体达到本发明所述目的。实施例3 :微米粉为平均粒径为75 ii m的NiCoCrAH合金粉,原粉呈股骨形且表面粘附有大量的小颗粒,纳米粉为平均粒径为20nm的氧化铈粉体。首先,以乙醇为球磨介质对微米原粉进行球磨预处理,球磨预处理的工艺参数为球磨转速400转/分钟、球料比10: I、球磨时间6小时,将球磨预处理后的微米原粉用325目(对应47微米)分样筛过筛,获得表面光滑无粘附且呈球形化趋势的预处理后微米粉,称量预处理后的微米粉,其质量是预处理前的90%;其次,将纳米粉在乙醇与去离子水混合溶液(乙醇与去离子水的比例为I: I)中进行分散,制备分散稳定的纳米悬浮液;再次,将按照所需配比称量好的预处理后的微米粉和分散稳定的纳米悬浮液置于球磨罐中混合并加入磨球,球磨时液体介质的表面应高出微米粉体的表面,然后开始球磨复合,所采用的球磨工艺参数为球磨转速350转/分钟、球料比10: I、球磨时间I小时,在球磨复合过程中每球磨6分钟停机对球磨罐中粉体进行间歇搅拌;最后,将球磨制备好的微纳复合粉体从球磨罐中取出,置于干燥箱中进行干燥,即可获得可直接送粉的高效微纳复合粉体,所制备微纳复合粉体达到本发明所述目的。实施例4 :微米粉为平均粒径为50 Pm的Al-Si合金粉,原粉呈类球形状、大颗粒和中等颗粒粘连在一起、表面粘附有大量的小颗粒(图10),纳米粉为平均粒径为20nm的Al2O3陶瓷粉。首先,以乙醇为球磨介质对微米原粉进行球磨预处理,球磨预处理的工艺参数为球磨转速300转/分钟、球料比8: I、球磨时间4小时,将球磨预处理后的微米原粉用425目(对应33微米)分样筛过筛,获得表面光滑无粘附的预处理后微米粉,称量预处理后的微米粉,其质量是预处理前的85%;其次,将纳米粉在乙醇中进行分散,制备分散稳定的纳米悬浮液;再次,将按照所需配比称量好的预处理后的微米粉和分散稳定的纳米悬浮液置于球磨罐中混合并加入磨球,球磨时液体介质的表面应高出微米粉体的表面,然后开始球磨复合,所采用的球磨工艺参数为球磨转速为300转/分钟、球料比20: I、球磨时间为I. 5小时,在球磨复合过程中每球磨9分钟停机对球磨罐中粉体进行间歇搅拌;最后,将球磨制备 好的微纳复合粉体从球磨罐中取出,置于干燥箱中进行干燥,即可获得可直接送粉的高效微纳复合粉体,所制备微纳复合粉体达到本发明所述目的。本发明未涉及部分均与现有技术相同或可采用现有技术加以实现。
本发明公开了一种可直接送粉的高效微纳复合粉体湿法球磨制备方法,其特征是首先,对微米原粉进行球磨预处理,将球磨预处理后的微米原粉过筛,获得预处理后的微米粉;其次,将纳米粉在乙醇或乙醇与去离子水混合溶液中进行分散,制备分散稳定的纳米悬浮液;再次,将预处理后的微米粉和分散稳定的纳米悬浮液置于球磨罐中混合并加入磨球,在球磨复合过程中对球磨罐中粉体进行连续搅拌或间歇搅拌;最后,将球磨制备好的微纳复合粉体从球磨罐中取出,置于干燥箱中进行干燥,即可获得可直接送粉的高效微纳复合粉体。采用本发明方法所制备的微纳复合粉体能够兼顾微纳复合粉体复合效果和满足热喷涂、激光熔覆直接送粉要求,具有很强的工程价值和应用前景。
可直接送粉的高效微纳复合粉体湿法球磨制备方法
- 专利详情
- 全文pdf
- 权力要求
- 说明书
- 法律状态
查看更多专利详情
下载专利文献
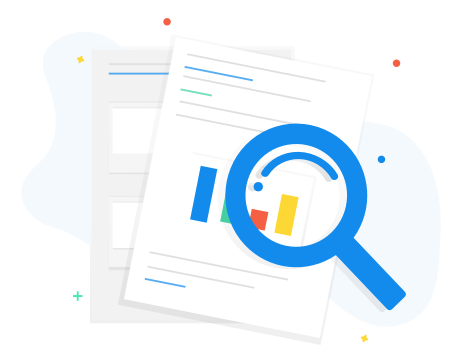
下载专利
同类推荐
-
吴志奎魏家浩吕志伟吕志伟
您可能感兴趣的专利
-
吕志伟P·莫拉佐尼P·莫拉佐尼李会郎, 李承元芮秀明, 张秉文
专利相关信息
-
芮秀明K·罗杰斯, G·迪泽瑞嘉