专利名称:脱硫铁水罐防粘渣喷涂料的制作方法 在铁水脱硫过程中,脱硫铁水罐罐嘴、罐沿及罐内渣线部位结渣铁逐渐严重,导致空罐质量增加,重心上移,严重影响到炼铁、炼钢生产组织与生产安全;同时,由于粘渣物非常坚硬且与罐衬结合牢固,去除十分困难,只好提前拆除大修,造成脱硫铁水罐寿命较低,周转紧张、耐材消耗增加。对于粘渣不严重的脱硫铁水罐,粘渣的常用处理方法是采用煤氧枪对粘渣层首先进行切割,然后采用吊具将切割后的小渣块进行钩吊维护,这种粘渣处理方法的不足为导致衬体破损,严重地危害了设备的使用性能与使用寿命;处理时间较长,降低了设备的周转频率。目前,虽然已有在脱硫铁水罐防粘渣喷涂料的报道,“脱硫铁水罐渣线喷涂料的研究《武钢技术》2003(3)”和“攀钢半钢罐防粘技术的开发《四川冶金》2004(4)”报道了在脱硫铁水罐防粘渣喷涂料的研制和实际应用效果,喷涂料主要由高铝熟料、鳞片石墨、土状石墨、碳化硅为主要原料,以无机化学结合剂、微粉、高铝水泥中的一种或多种为结合剂,再添加各种改性添加剂构成,能方便地涂敷在各种材质的脱硫铁水罐罐嘴、罐沿和渣线部位罐衬表面,形成均匀的防粘渣喷涂层,通过喷涂层中石墨与碳化硅材料的不易被浸润的性能,起到隔离粘结物与罐衬的作用,从而大幅度地降低了粘渣物的粘结强度,达到降低清渣难度、缩短清渣时间、减轻清渣过程对罐衬破损的影响,通过实际应用,收到了延长脱硫铁水罐使用寿命、降低维护成本、提高脱硫铁水罐周转率的效果。但是,由于该技术的喷涂层较厚,一般为35mm左右,每次喷涂用料量大,同时,喷涂料原材料价格较高,提升了脱硫铁水罐耐火材料消耗与脱硫成本。
本发明针对现有技术所存在的脱硫铁水罐耐火材料消耗与脱硫成本较高的问题,进而提供一种价格低廉、制备方便、使用简单的脱硫铁水罐防粘渣喷涂料。为了实现上述技术问题,本发明的技术方案是这样实现的所述防粘渣喷涂料由以下重量百分比的原料组成含碳耐火材料废砖70~90%,矾土水泥4~8%,硅酸盐水泥1~3%,硅微粉1~3%,粘土2~13%,土状石墨0~5%,无机短纤维0.5~3%,磷酸盐0.1~0.5%。其中,所述的含碳耐火材料废砖可以是铝碳化硅碳质耐火废砖、铝碳质耐火废砖或者镁碳质耐火废砖。其中,所述的含碳耐火材料废砖分为三种粒度且三种粒度的重量百分比分别是3~1mm的为15~25%、1~0.088mm的为40~50%,<0.088mm的为30~40%。其中,所述磷酸盐是三聚磷酸钠或六偏磷酸钠。其中,所述的土状石墨和粘土为过100目筛的粉料。
其中,所述无机短纤维采用岩棉、矿渣棉、硅酸铝系列纤维棉或废纤维棉;所述无机短纤维的纤维长度为2~8mm。
本发明以含碳耐火材料废砖为喷涂料的主要原材料,取代现有技术中的高铝熟料、鳞片石墨、碳化硅和部分或全部土状石墨,从而,大幅度降低了喷涂料成本;以矾土水泥和硅酸盐水泥为复合结合剂,通过两种水泥的相互作用,达到喷涂层快速凝固的目的;以粘土为部分粉料,利用粘土的粘附性能,降低喷涂料的反弹率,提高喷涂料的利用率;通过无机短纤维增韧作用,提高喷涂料的快速烘烤适应性能;以硅微粉为分散剂,改善喷涂料的搅拌均匀性;以磷酸盐为减水剂,降低喷涂施工用水量。
具体制备工艺是首先进行原材料准备,组分及重量百分比为含碳耐火材料废砖70~90%,矾土水泥4~8%,硅酸盐水泥1~3%,硅微粉1~3%,粘土2~13%,土状石墨0~5%,无机短纤维0.5~3%,磷酸盐0.1~0.5%;其中,主要是对含碳耐火材料废砖进行除渣或除铁处理、破碎、细磨与筛分,筛分后材料粒度分为三种且三种粒度的重量百分比分别是3~1mm的为15~25%、1~0.088mm的为40~50%,<0.088mm的为30~40%;然后,将所有原料加入搅拌器内搅拌均匀,即得到所需的喷涂料,并装袋包装。
本发明脱硫铁水罐防粘渣喷涂料使用方法是采用调和涂抹或直接喷涂的方式,在设备冷态与热态条件下,均可进行防粘渣处理施工,施工完毕后,可立即投入使用。
本发明脱硫铁水罐防粘渣喷涂料具有如下优点1、本发明脱硫铁水罐防粘渣喷涂料制备简单,原材料来源广,成本低,并可做到废旧资源的综合利用。
2、本发明性能优良,可满足不同使用温度条件下脱硫铁水罐的防粘渣要求。
下面结合实施例进一步详述实施例1制备100公斤脱硫铁水罐防粘渣喷涂料其原料组成及重量百分比为将经过除渣或除铁处理的刚玉(铝)碳化硅碳质废砖70.7公斤,其中,粒度为3~1mm、1~0.088mm和<0.088mm分别为14.14公斤、31.82公斤和24.74公斤;过100目筛的粘土粉12公斤,矾土水泥7公斤,硅酸盐水泥1.8公斤,硅微粉3公斤,纤维长度为2~8mm的无机短纤维2公斤,过100目筛的土状石墨粉3公斤,三聚磷酸钠0.5公斤,将上述原料加入搅拌器内搅拌均匀,即得到所需的喷涂料,并装袋包装。
实施例2制备100公斤脱硫铁水罐防粘渣喷涂料其原料组成及重量百分比为将经过除渣或除铁处理的铝碳化硅碳质废砖82公斤,其中,粒度为3~1mm、1~0.088mm和<0.088mm分别为16.4公斤、36.9公斤和28.7公斤,过100目筛的粘土粉7公斤,矾土水泥5公斤,硅酸盐水泥2.8公斤,硅微粉2公斤,纤维长度为2~8mm的无机短纤维1公斤,三聚磷酸钠0.2公斤,将上述原料加入搅拌器内搅拌均匀,即得到所需的喷涂料,并装袋包装。
实施例3制备100公斤脱硫铁水罐防粘渣喷涂料其原料组成及重量百分比为将经过除渣或除铁处理的镁碳化硅碳质废砖86公斤,其中,粒度为3~1mm、1~0.088mm和<0.088mm分别为17.2公斤、38.7公斤和30.1公斤,过100目筛的粘土粉2公斤,矾土水泥4公斤,硅酸盐水泥1公斤,硅微粉1公斤,过100目筛的土状石墨粉4.4公斤,纤维长度为2~8mm的无机短纤维1.5公斤,六偏磷酸钠0.1公斤,将上述原料加入搅拌器内搅拌均匀,即得到所需的喷涂料,并装袋包装。
具体地,在100吨喷吹脱硫用脱硫铁水罐易粘渣的罐嘴、罐沿及罐内渣线部位,采用本发明喷涂料和市售喷涂料进行了工业性对比试验,试验结果表明,本发明喷涂料达到了市售喷涂料同样的效果,即脱硫铁水罐粘渣层不需进行火焰切割便能一次性整体吊脱。
脱硫铁水罐防粘渣喷涂料,它涉及一种防止脱硫铁水罐粘渣的防粘渣喷涂料。为解决现有技术存在的脱硫铁水罐粘渣处理喷涂料价格较贵的不足,本发明采用下述技术方案脱硫铁水罐防粘渣喷涂料,其特征在于原料组成及重量百分比为它由以下重量百分比的原料组成含碳耐火材料废砖70~90%,矾土水泥4~8%,硅酸盐水泥1~3%,硅微粉1~3%,粘土2~13%,土状石墨0~5%,无机短纤维0.5~3%,磷酸盐0.1~0.5%。本发明具有原材料来源广、成本低、废旧资源综合利用和使用效果优良的特点。
脱硫铁水罐防粘渣喷涂料制作方法
- 专利详情
- 全文pdf
- 权力要求
- 说明书
- 法律状态
查看更多专利详情
下载专利文献
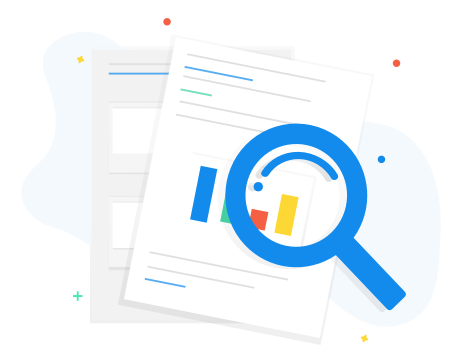
下载专利
同类推荐
-
欧阳德刚倪文龙倪文龙倪文龙倪文龙
您可能感兴趣的专利
-
E.P.伯格, R.斯特拉陈庆洪, 陈东东由伟由伟由伟
专利相关信息
-
由伟由伟李雅松, 焦希英由伟欧阳德刚