专利名称:耐水耐火材料及其制造方法本申请是1993年10月28日提出的,序列号为08/141,965的部分继续申请。本发明涉及耐水耐火材料及其制造方法。本发明还涉及用来赋予众多纤维素材料以耐水耐火性能的组合物,这些纤维素材料包括各种木质纤维和粉粒,各种纤维素薄片,各种木条,和各种有机废弃物。天然木材,木质粉粒,纤维,和木片具有许多良好的性能,因而广泛用于木质复合结构材料中。然而,这些结构材料存在一些缺点或不足之处。具体来讲,木基制品不但天生易燃,而且暴露于湿气中易膨胀。这种膨胀导致粘接力和结构强度下降,从而限制这种结构材料的使用范围。另外,由于用以制造胶合板的胶合板级木材的供应源显著减少,此类胶合板的成本大幅度提高。这就使得利用“废弃”副产品如软木和硬木粉粒、木屑、薄片和纤维生产结构材料(如,面板、地板、墙板、木材替代物、天花板、屋顶护板和门)有经济上的必要性。制造工艺的改进使得由废木质纤维和有机副产物材料制成的产品在强度和尺寸稳定性上有所提高,这些材料现已广泛用于制作结构产品和工业产品。例如,这些产品包括,取向木条板(OSB),中密度纤维板(MDF)、刨花板、纤维基板、层压板、石膏纤维板、纤维板和水泥纤维板。尽管在全球范围内使用上述材料制作大量建筑及工业制品,但此类制品的市场和应用还将继续扩大,假如这些有机和木质副产物在使用时的两大特点即缺乏耐火性和潮湿环境下的不良膨胀能得以克服的话。直到本发明之前,提高材料如OSB的耐火性和阻燃性仅局限于在最终OSB板表面涂覆涂料,其效果是很有限的。以前对诸如OSB薄板或板材等用传统的阻燃化合物象磷酸盐、铝酸盐和其它酸的盐进行预处理或加压浸渍的种种尝试(如耐火处理的层压板)均被认为是很不成功的。而且经这些化合物处理的OSB板要么以破坏模量测得的强度大幅度下降要么因膨胀而使尺寸稳定性下降。另外,上述建筑和工业制品的抗白蚁性一般都很差。因而,为了克服上述缺点,本发明的一个目的是制造出可燃性和膨胀性均显著降低的有机和木质副产物结构材料,如板材,例如使之不易燃烧和在潮湿环境如湿气中耐膨胀。另外,本发明的一个目的是制得抗白蚁性能优异的有机和木质副产物结构材料。
本发明的另一个目的是提供可以将这些优异性能及其他性能赋予有机及木质副产物材料的方法。
本发明的还一个目的是开发一种组合物,使用该组合物可使有机及木质副产物材料具有上述种种优异性能。
至于本发明的其它目的和优点,有一部分将在以下的说明中阐明,而另一部分可很容易由该说明了解清楚或者通过本发明的实施而进一步了解。本发明的目的和优点可通过所附的权利要求书中具体指明的要点及其组合来认识和实现。
发明概要为了实现本文所概括的本发明的目的,本发明涉及一种组合物,该组合物包含一种细碎的材料如纤维素材料和一定量含有能有效地赋予上述材料以耐水性和耐火性的氯氧化镁和/或含氧硫酸镁的胶乳。
另外,本发明涉及制造耐水和耐火制品的方法。一个实施方案包括以下步骤将含有氯氧化镁和/或含氧硫酸镁和胶乳的组合物加到细碎的材料如纤维素材料或木质纤维素材料(如,木质纤维、木质细条、木质薄片、木质颗粒和纤维素纤维)、矿物纤维、有机废弃物或无机废弃物中,并混合这些组分使组合物涂覆于细碎的材料表面。此方法的一个可选择步骤是调节被涂覆材料的含水量。然后,本方法的下一步是将热固性树脂或冷固化树脂与已涂覆的材料混合。完成了这一步后,制成基板并随即经加热和/或加压形成耐水耐火制品。
在另一实施方案中,耐水耐火制品可通过这样的方法制作,即边混合边把含有氯化镁和/或硫酸镁和胶乳混合物的液态组分施于(例如通过喷涂)细碎的材料如纤维素材料或木质纤维素材料(例如,木质纤维、木质细条、木质薄片、木质颗粒和纤维素纤维)、矿物纤维、有机废弃物、或无机废弃物。然后,在这一初步喷涂后,混入氧化镁粉末以便使该粉末涂覆于细碎材料的湿表面。完成之后,将剩余的液态组分喷涂在粉末涂覆的纤维素材料上。氯化镁或硫酸镁与氧化镁就地反应生成氯氧化镁或含氧硫酸镁。然后,可选择地,调节材料的含水量。随后,在被涂覆材料的表面施以热固性树脂或冷固化树脂。施加完树脂涂层后将材料制成基板并经加热和/或加压形成耐水耐火制品。
需要明确的是上述一般性描述和以下的具体描述都仅为举例说明而不是限定本发明的权利要求范围。
本发明的详细说明本发明的一个方面是一种组合物,该组合物含有氯氧化镁和含氧硫酸镁和胶乳溶液。
该组合物还可包含其它组分如铝酸钙水泥、二氧化硅、二氧化钛、ZnCl2溶液、消泡剂和表面活性剂。
美国专利5039454和4572862(在此引作参考)公布了由起始原料氯化镁和氧化镁制造氯氧化镁的方法,并且还公布了以硫酸镁和氧化镁为原料制造含氧硫酸镁的方法,有关术语曾在这些专利中使用。另外,这些专利指明了这些起始原料的可靠商业来源。
详细而言,基本粘结组分,一种“水泥”,由一种高度煅烧(热活化的)氧化镁(MgO)组成,当它与MgCl2水溶液和/或MgSO4盐溶液混合时,结晶形成互相连接的晶体网络(以及其它离子键合体系),从而通过连接体系中所含的纤维素材料而使该体系具有强度。高氧化铝铝酸钙水泥和胶态二氧化硅可以添加进去作为配伍的共粘结剂。
“活化剂”水溶液(叫作调节液)是氯化镁(MgCl2)或硫酸镁(MgSO4)的盐溶液,或者它们的组合。这两种盐都是易溶于水的水合盐(分别是6H2O和7H2O)。实践表明,对MgO的固化有效的溶液必须是高浓度(40%到60%),通常表示为比重,以比重值标识或以玻美度标识(比重1.22到1.26,或26°到32°玻美)。这些盐最好以反应所需要的化学计量比率加入,这样不会使某种盐过量,过量的盐会使表面风化或在水中或在潮湿条件下会渗出;或与空气中的CO2反应生成化合物,这些化合物因其体积大于其原先在初期固化水泥中所占据的体积而引起结构破坏。在本发明中,使用该盐溶液作为MgO水泥和铝酸钙水泥(如果使用的话)的普通水合剂。利用该溶液使铝酸钙水合不必使盐和MgO的比率保持在特定的化学计量比例。
氧化镁,和任选的组分一氧化铝铝酸钙水泥,和二氧化钛都是粉末并且最好都是研磨得十分细的固体粉末。每种原料最好先在200°F的热空气炉中予以干燥。将干燥的材料混合或掺和在一起,如通过碾磨有效地掺混。
各液体组份,MgCl2和/或MgSO4,和胶乳,以及如果使用的话还有消泡剂、ZnCl2溶液、二氧化硅胶体和表面活性剂,以类似的方式制备。如果使用某种表面活性剂的话最好是将其逐滴加入MgCl2和/或MgSO4溶液中,而二氧化硅胶体(如果使用的话)最好是缓慢地加到上述溶液中。这样会使透明溶液变成乳白色但不会产生沉淀。反应是强放热的。随后液态组分即可进行掺混。溶液的粘度将显著上升,放置后则又会下降。
然后最好是在恒连机械搅拌下将混好的粉末慢慢加到液体相中,使每个粒子被液体充分浸湿。得到均匀的油漆状粘稠悬浮液。适用期通常较短-20至30分钟,溶液逐渐稠化直至变成软凝胶。在头1到1.5小时内凝胶渐渐硬化,放置2到4小时完全固化。适用期和固化时间可通过改变固液比例来调节-通过增减液相数量的方式更为方便。将固化温度升高到100°-400°F,涂料的完全固化时间将大幅度缩短。在本发明的配方中,涂料的完全固化即硬度及其他表面特性对液固比的变化较不敏感。
各种类型的MgO(氧化镁)均可使用。不过,各种可用的MgO的反应活性因来源不同和热处理方式不同而有所不同。尽管美国专利4572862指出各种MgO均可使用,但最好的MgO是Baymag30和/或Baymag40(Baymag Products,Inc.,Calgary,Alberta)。
’862专利指出了可接受的MgCl2和/或MgSO4溶液的来源。比重为1.26-1.3的优选MgCl2来自MacKenzie & Feimann Ltd.,Vancouver,B.C.。
20℃时MgCl2·6H2O的溶解量可达155克/100毫升蒸馏水。60°F时基于MgCl2的28%溶液的玻美度为30°。实际使用时,1000毫升自来水溶解1500克六水合镁盐,得到1800毫升比重为1.26(30°玻美)的溶液,其PH为6.0。建议在使用之前让溶液“熟化”24小时;并且在密闭容器中,配妥的溶液将长期保持稳定。
1升水溶解500克MgSO4·7H2O(或1美制加仑溶解4.169磅盐)获得比重为1.25或26°玻美的溶液。该溶液盐的净含量为41%。用自来水配制的溶液PH为5.3。
如前所述,MgCl2和MgSO4可按1∶1、2∶1、或3∶1的比例混用。
涂料组合物中的胶乳可以是任意一种能提高氯氧化镁和/或含氧硫酸镁对细碎材料的粘结力和附着力的胶乳,这些细碎材料有纤维素纤维如木质纤维、木质薄片、木质颗粒,或细碎的无机或有机废弃物,矿物纤维等,这将在下文介绍。在本发明涂料组合物的制备中,通常是将胶乳加入调节溶液或液态组分中(即MgCl2和/或MgSO4)中。
在制成板材前,胶乳可足量直接混入氯氧化镁和/或含氧硫酸镁中以提高细碎材料(如纤维素材料)同氯氧化镁和/或含氧硫酸镁之间的粘结力并赋予该材料(如纤维素材料)以耐水耐火性能。胶乳的实例包括苯乙烯-丁二烯共聚物乳液,丙烯酸酯树脂乳液和聚乙酸乙烯酯。此外,胶乳可包含一种以上上述乳液。
胶乳优选为苯乙烯-丁二烯(65/35)共聚物乳液。优选的苯乙烯-丁二烯共聚物乳液是Emchem Sales,Ld.(North Vancouver,B.C.)出品的Union Latex Amisco 4040和4040 Latex型乳液。
可以将胶乳加入初始原料,即氯化镁和/或硫酸镁中,形成液体混合物,然后将其加到氧化镁中形成涂料组合物。通常,各组分用量如下胶乳对氯化镁和/或硫酸镁的体积比率从约1∶3至约1∶15,优选为约1∶8到约1∶12。
对于任选组分-铝酸钙水泥,’862专利还指明了它的可接受的来源和用量。优选使用Secar80(Lafarge Canada,Inc.,Richmond Hill,Ontario)和CA-25(ALCOA)。
本发明中,铝酸钙(如果使用的话)水合化所需的“水”由氯化镁(或硫酸镁)溶液提供。
’862专利介绍了使用任选组分,表面活性剂,胶体或无定形二氧化硅和二氧化钛的好处以及它们的可接受的来源和用量。优选的表面活性剂是Lonza Company(Fair Lawn,New Jersey)出品的Amphoterge KJ2。优选的二氧化硅是来自L.V.Lomas,NewWestminster B.C.的Illinois无定形二氧化硅,而优选的TiO2是来自Van Waters & Rogers,Richmond,B.C.的产品。
此外,本发明的涂覆溶液中还可使用消泡剂。优选的消泡剂是Henckel Canada,Inc.(Mississauga,Ontario)出品的FoamasterNXZ。组成涂覆溶液的另一任选组分是氯化锌溶液,优选VanWaters & Rogers,Richmond,B.C.的产品。
本发明组合物中任选组分的用量无决定性影响,而且本技术领域熟练技术人员通过常规实验可以总结出最有效用量。在以下讨论的优化配方中给出它们的最佳用量。
添加水基或油基矿物颜料如Hoechst Corporation“Colanyl”浆料(如,黄、棕、绿)可对涂料进行着色或染色;本发明的最终产品可通过丝网印刷法或其它印刷方法来罩印以获得装饰图案。
在实施例中系用的涂料组合物优化配方如下粉末组分液态组分MgO(30级)45kgMgCl2溶液(比重1.26)145L(Baymag 30/Baymag Products Inc.)(Mackenzie & Feimann Ltd.)MgO(40级)45kg消泡剂 0.72L(Baymag 40/Baymag Products Inc.)(Formaster NXZ,HenckelCanada Inc.)铝酸钙(200目)22.7kg 表面活性剂 1.45L(Secar 80,Lafarge Canada Inc.) (Amphoterge KJZ,Lonza co.)Illinois无定形二氧化硅22.7kgZnCl2溶液1.45kg(L.V.Lomas) (Van Waters & Rogers)TiO22.25kg胶乳(固含量50%) 11.6L(Van Waters & rogers) (4040胶乳,Emchem Sales,Ltd.)采用的优选比例是每1毫升液态组分对应1克粉末组分。
将胶乳混入氯氧化镁和/或含氧硫酸镁可采用任意一种混合两个组分的普通已知方法,例如使用本技术领域熟练技术人员所熟知的市售掺和机或混合器。胶乳与氯化镁和/或硫酸镁的混合也一样。
为制得耐水耐火产品,将上述组合物涂覆在细碎材料如纤维素或木质纤维素材料等表面。这些材料优选为木质纤维、木质细条、木质薄片、木质颗粒、纤维素纤维,以及类似材料。适用于本发明的其他细碎材料包括矿物纤维、有机废料、无机废料、以及类似材料。具体的例子包括诸如硬木或软木的木质细条和薄片(例如山杨类和南部的黄松木)、稻壳、干草和纸张包括报纸。例如,纤维素材料可以是3-48英寸长、1/4-2英寸宽、0.020~0.125英寸厚的木条。这样的纤维素材料可从本技术领域熟练技术人员所熟知的各种渠道大量获取。
在用于本发明方法之前,这些细碎的材料(例如,纤维素材料),可以是水含量为5-100%(重量)的“原生料”,或可以是经过干燥至材料的水含量约为5-8%(重量)的材料。有一种干燥方法是使用炉式干燥机。
下面将描述由上述起始组分制造耐水耐火制品的优选方法。
制造耐水耐火制品的一种方法包括下列步骤。
首先,在一个已装有细碎材料如纤维素材料(例如,木质纤维、木质薄片、木质颗粒和纤维素纤维)、有机或无机废料、或矿物纤维的筒式掺和机中,加入至少会有氯氧化镁和/或含氧硫酸镁和胶乳的上述组合物。在把组合物加入掺和机中后,材料与组合物一起被掺混搅和,使组合物均匀地涂覆在材料(如纤维素材料)表面。一种优选的筒式掺和机是Coil Industries,Inc.(Vancouver,B.C.)制造的,该设备采用高速旋转的盘式雾化器。另外,可以在掺混机掺和材料的同时,通过喷射棒、常规无空气喷雾器或带空气辅助喷雾设备的无空气喷雾器将本发明的组合物施加到材料(如,纤维素材料)上。
材料(如纤维素材料)经组合物均匀涂覆后,其水含量可任意调节,例如借助空气驱动的干燥容器进行干燥。已涂覆材料(如已涂覆的纤维素材料)的总含水量可控制在已涂覆纤维素材料总重量的大约5-25%(重量),优选为约9-11%(重量)。干燥过程是利用抽气泵使20°-100℃的空气通过已涂覆纤维素材料来实现的。通常将含水量降至这一优选范围内以免在下述的加热和/或加压步骤中可能出现水蒸气爆发。
尽管干燥是更可取的,但干燥步骤是可有可无的,并且含水量高于大约25%的材料如纤维素材料也能使用。
然后,再将已涂覆材料(如,纤维素材料)装入掺和机并用热固性树脂或冷固化树脂涂覆。具体而言,本发明使用的冷固化树脂,又叫冷固化粘合剂,是添加硬化剂或不添加硬化剂时能在正常室温(如20℃)下固化的合成或天然树脂。其实例包括,但不局限于,动物皮胶。鉴于本发明可包括冷压作业(一种胶接作业,其中组件在不加热情况下经加压处理),因此,冷固化树脂的另一种定义是无需加热可以胶接的树脂。
热固性树脂,又称热固性合成树脂粘合剂,包括各种树脂酚醛树脂、脲醛树脂、三聚氰胺-甲醛树脂以及其他缩聚材料如呋喃树脂和聚氨酯树脂。热固性树脂或粘合剂的特征是在热或催化剂作用下会转变成不溶不熔材料。含有苯酚-、间苯二酚-、脲-、三聚氰胺-甲醛、苯酚糠醛,及类似成份的粘合剂组合物已用于粘接木材、织物和纸张,因而也将适合于本发明。换句话说,热固性树脂或粘合剂是一种塑料,它在经加压首次受热时固化而且不破坏其固有性能就不能再熔化或再成型。另外的例子是环氧树脂、三聚氰胺树脂、酚醛塑料和尿素塑料。
适用于本发明的树脂的其它具体例子包括Ashland Chemicals出品的各种ISOSET?木材粘接用粘合剂树脂。ISOSET WD3-A322树脂是可交联型水乳液聚合物,它与ISOSET CX交联剂(硬化剂)(如,ISOSET CX-47交联剂)并用。ISOSET树脂体系是乳液聚合物异氰酸酯(EPI)粘合剂,以双组分体系的形式使用。树脂部分(ISOSET WD)由水基聚合物乳液组成。硬化剂部分(ISOSET CX交联剂)是基于聚二苯基甲烷二异氰酸酯(MDI)的被保护的异氰酸酯。当二个组分混合在一起时就形成了适用期达数小时的高性能粘合剂体系。将该粘合剂施用于基质如本发明中已涂覆的细碎的材料时,发生室温化学反应形成交联的聚合物粘接层。
鉴于ISOSET树脂可进行室温固化粘接,在本发明中它们可视为冷固化树脂。
本发明所使用树脂的优选例子包括二苯基甲烷二异氰酸酯(MDI)树脂(来自Miles)、亚甲基二乙基二异氰酸酯树脂、异氰脲酸酯树脂、脲甲醛树脂、酚醛树脂、ISOSET树脂、酚醛胶和动物皮胶。最优选树脂是ICI United′States(Wilmington,DE)出品的MDI,该树脂销售的商品名为Rubinate?1840(曾定名为Rubinate MF-184)(ICI Polyurethanes Group,West Deptford,N.J.)。
树脂完全混合并涂覆在前述的已涂覆材料(如,纤维素材料)上面之后,可以任选地测定含水量以确保含水量仍处在优选的范围内。如果有必要的话可对已涂覆的材料再进行另一次干燥。
然后,将已涂覆材料(如纤维素材料)制成基板。基板的形成可使用任意一种方式如机械成型、缠绕成型,或用Sunds Debrator提供的分级成型机(Classiformer)成型。基板可由单层或多层涂覆材料(如纤维素材料)形成。此外,基板的形成例如可以使木质细条层以与矩形纤维基板最长尺寸方向相平行或垂直的方向取向。完成此步骤之后,在热和/或压力任用下如经热压处理使用基板成型为板材。例如,一个木质细条基板可压制成厚度从3/8英寸到1.5英寸的平板。另外,木质细条基板还可压制成波长为2英寸到24英寸、板高为0.5英寸到4英寸而板面厚为3/8英寸到1英寸的波纹板。通常施加足够的压力以形成板材。优选的压力是大约300psi到大约600psi,最优选的压力为450psi。例如,最终厚度为7/16英寸的板材是在大约300°F到大约375°F温度的压模板上压制大约3到大约8分钟,优选为大约180秒。模压后将所得材料即板材堆放好并冷却。
在基板成型时,作业所采用的许多设备都可形成二个面层和一个芯层,它们分别构成模压板材的外层和内层。在测定表面火焰蔓延性能及其它表面性能的特定情形中,可以仅对二个面层的材料如(纤维素材料)涂以氯氧化镁/胶乳(或含氧硫酸镁/胶乳)。这样既可以获得合符要求的板材表面特性又可降低板材成品的总成本。
涂料组合物可以大范围的比率与材料(如纤维素材料)混合。优选地,涂料组合物的加入量为该材料(如纤维素材料)(经烘干)重量的约10-200%(重量),优选为该材料(如纤维素材料)(经烘干)重量的约30-60%(重量)。涂料组合物的最佳用量可根据待制材料或板材的物理及耐火性能要求来确定。
热固性树脂或冷固化树脂的加入量通常是涂料组合物与材料(如纤维素材料)(经烘干)重量的2~10%(重量),优选为2~5%(重量)。
以下介绍制作耐水耐火材料的另一种方法。
这种方法充分利用这样的事实,即如前文及美国专利4572862所述,氯化镁或硫酸镁是一种水溶液,而氧化镁是一种粉末。具体而言,是将胶乳与氯化镁或硫酸镁水溶液混合形成液态组分。假如使用消泡剂、ZnCl2溶液和/或表面活性剂,那么这些组分也将成为液态组分的一部分。胶乳的用量可与前文所述的相同。
优选地,将大约25%(体积)的液态组分喷到细碎的材料(如纤维素材料)上。液态组分的喷涂可借助任意一种方法(如使用喷枪或喷射棒)而完成。在喷涂约25%(体积)的液态组分的同时,掺和机对材料(如纤维素材料)进行混合。初期喷涂后,在掺和机继续运行的情况下,将全部氧化镁粉末(如果使用的话还将包括铝酸钙、无定形二氧化硅及二氧化钛)加入掺和机进行混合使其涂覆在材料(如纤维素材料)的湿表面上。涂覆时可采用空气驱动方法以使粉末在材料(如纤维素材料)表面达到均匀分布。当粉末在材料(如纤维素材料)表面充分分散后,按前述相同的方式将剩余的液态组分喷涂到已被粉末涂覆的材料(如纤维素材料)上。氯化镁和/或硫酸镁分别与氧化镁就地反应生成氯氧化镁和/或含氧硫酸镁。同样,如前一种方法,第二次喷涂后可选择地将材料的含水量调整到约5-25%(重量),优选为约9-11%(以已涂覆材料总重量为准)。如前所述,调节含水量的一种方法是使用空气干燥机。然后,与前一种方法相同,将已涂覆材料(如纤维素材料)放入同一掺和机或第二台掺和机中,加入热固性树脂或冷固化树脂。同样,还可以检测含水量以确保含水量处于合适的范围。随后,可将具有适宜含水量的材料制成基板,进而加热和/或加压(如经热压)将基板制成板材和板。与前法相同,施加足够压力以形成板材。优选压力为大约400psi到大约500psi,最优选压力为450psi。优选地,将基板于大约375°F热压大约180秒形成7/16英寸厚的板材。
对于制作本发明耐水耐火制品,施用热固性树脂或冷固化树脂的步骤并非必不可少。更详细地说,可以用相对于已烘干材料(如纤维素材料)重量约为10-500%(重量)的涂料组合物通过前述方式对材料(如纤维素材料)进行涂覆。然后,将已涂覆材料(如纤维素材料)制成基板并进行加热和/或加压处理,例如在不添加粘合剂或树脂的情况下置于热压机中于大约150°F温度下施压约12小时。本发明的发明人已发现,对于那些用作非结构板材如防火门的芯层等的应用,热压时间延长可免除对添加树脂的需求。
上述任一方法可以包括一步添加防水剂的步骤。比如可加入硅氧烷作为涂料组合物的成份。通常,防水剂的加入量约为氯化镁和/或硫酸镁及胶乳(即液态组分)重量的1~10%(重量),优选为2%。
此外,在板材成型之后,可选择地以本发明的涂料组合物对其实施单面或多面喷涂。最佳喷涂厚度为大约1密耳。
值得注意的是,本发明的耐水耐火制品在本发明的材料中不需加蜡,而蜡是以往的板及板材结构材料中所常加的组分。加蜡通常是为了减少水和湿气的不良影响并促进树脂向材料(如纤维素材料)的扩散。然而,在本发明中,使用蜡所产生的有益作用可由本发明的组合物、具体地说是氯氧化镁/胶乳或含氧硫酸镁/胶乳组分所产生。
本发明可通过以下实施例做进一步的阐述,这些实施例仅仅是作为本发明的举例说明。
通过以下某些实施例表明,与现有的结构材料制品(如,OSB,MDF,刨花板)相比,本发明的材料具有以下优点耐火性、不可燃性、耐水及耐潮湿性;改善的内在粘结强度、改善的破坏模量、改善的弹性模量、改善的尺寸稳定性、改善的抗弯强度、减低的蠕变、降低了因燃烧而产生的烟雾等气态物质的毒性、降低了在水环境及湿环境中的膨胀敏感性,免除了蜡的使用、抗白蚁和昆虫、抗磨性、提高的防霉性,并且该材料更易于涂漆或用其它涂料涂覆。
实施例1
用以下方式制得了三块本发明的板材。使用了山杨类商品木条(0.03英寸厚、0.5-2英寸宽和大约4英寸长),这些木条经烘干后的含水量(MC)为7~8%并除去小于4.8mm的碎末。采用前述配方的组合物,即按2.77kg粉末组分对2.77kg液态组分的比例掺和而成的混合物,将该组合物(为待将其加入的烘干木条或配料的30%(重量))经转盘施于商品木条上,其中粉末组分与液态组分在经转盘施加之前已混在一起。转盘设定为12000rpm(每分钟12000转),而施加过程中组合物的温度保持在20℃。经转盘施加后,在一个筒式间歇掺和机(直径2.44m×深1.22m)中将商品木条和组合物掺混直至组合物均匀地包覆了木条,其中掺和机的转速设定为25.5rpm。本批处理量为18.47kg。
各种材料混合之后,水850克/分钟的流速经同一转盘施涂器施加2.3%重量(以组合物及木条重量为准)的树脂MDI MF-184(ICI提供)。
然后,在上述筒式间歇式掺和机中让树脂和材料混合30秒。混合结束后,将物料用手工制成基板。基板构造是100%无规取向、单层,且其长度为865mm、宽度为865mm。基板的第一块板材重量为5.35kg,而第二和第三块板材重量为6.17kg。基板成型所使用的抛光板(caul)是密闭的罩板,具有固定的钢制上抛光板和下抛光板。脱模剂610ACI用来辅助基板成型后的脱模。压制前各基板的含水量为13.5%(重量)。
成型后的基板以及实施例2-11的基板在450psi压力、190℃板温下模压170秒以形成板材。另外,锅炉温度为210℃。模压结束时板材含水量为5.4和4.9%。将板材修整为700mm长、700mm宽和11.1mm厚。板材的内在粘接强度列于表I,强度的测试按CAN3-0437-85标准进行,每个试验材料的厚度为11.0mm,在65%RH、20℃下测定。
实施例2重复实施例1,但不同的是使用5.77kg粉末组分和5.77kg液态组分混合而成的组合物,通过转盘施涂器将组合物加到经烘干、含水量为7~8%(重量)的商品木条中。该组合物为木条(已烘干)的50%(重量)。使用同一筒式间歇掺和机将物料掺混325秒,本批处理量为23.08kg。以750克/分钟的流速经转盘施涂器施加5.0%(重量)的与实施例1相同的树脂。
同样,因同一筒式间歇式掺和机将物料掺混60秒,本批处理量为15.54kg。实施例2与实施例1的显著不同在于,将组合物施加于木条并掺混后,通过抽吸干燥的方法除去物料中过多的水份。因而,在模压之前基板的含水量为8.1%。采用实施例1的相同方法制成重量为6.17kg和7.35kg的两块基板。另外,基板成型后按实施例1的相同方法将其压制成板材并进行整修。其中一块板材的内在粘结强度列于表I。
实施例3采用与实施例1相同的木条,其烘干后的含水量为7-8%(重量),采用由5.77kg粉末组分和5.77kg液态组分组成的组合物(其为所用烘干木条的50%(重量)),先将四分之一(体积)的液体喷涂于木条上,然后将全部粉末吹于其上,最后喷涂其余的四分之三(体积)液体。为完成这一步骤,使用空气雾化喷嘴。按该方式施涂时,使用如前所述的筒式间歇式掺和机将物料掺混615秒,其中处理量为23.08kg。然后将物料干燥使其含水量为12.7%(重量)。在混合和干燥之后,以560克/分钟的流速通过转盘施涂器施加5%(重量)实施例1所使用的树脂。施加完树脂后,用同一筒式间歇式掺和机将物料搅和75秒且处理量为13.6kg。本方法制备的二块基板以与实施例1相同的方式用手工制作,每块基板的重量为6.17kg。模压前每块基板的含水量为12.7%(重量)。随后,按实施例1将基板压制成板材。模压后在其中一块板材上将340克组合物无空气喷涂在它的上表面。然后按实施例1对各板材进行修整。这二块板材的内在粘结强度列于表I。
实施例4使用与前述实施例相同的商品木条,其烘干后的含水量为7-8%(重量),所用组合物为11.55kg粉末组分和11.55kg液态组分的混合物(其为烘干木条的100%(重量)),用实施例1所述的转盘施涂器施加组合物,流速为2.92千克/分钟。施加后,用实施例1所述的相同掺和机将物料掺混475秒,其中处理量为23.10kg。本次的板材不施加树脂。施加完组合物后按实施例1所述方法将材料制法成基板,该基板重量为7.35kg而含水量为23.6%(重量)。然后按实施例1所述相同方法将基板压制成板材并进行整修。模压后板材的含水量为9%。其内在粘结强度列于表I。
实施例5所用商品木条与前述实施例相同,其烘干后的含水量为7-8%(重量),用实施例1的转盘式施涂器施加由11.55kg粉末组分和11.55kg液态组分混合的混合物,流速为2.92千克/分钟,其中混合物用量为(烘干)木条的100%(重量)。然后用实施例1的掺和机将物料搅和475秒,其中处理量为23.10kg。施加了混合物并掺混后将材料抽吸干燥使其含水量为10.1%(重量)。然后,用相同的转盘施涂器施加5%(重量)实施例1所用的树脂,流速为690克/分钟。
随后用同一掺和机将材料搅和100秒,其中处理量为22.7kg。
第二次掺混后,按与实施例1相同的方法制成三块基板,它们的重量分别为6.17kg、7.35kg和7.35kg。每块基板的含水量均为10.1%(重量)。然后按实施例1所述方法将基板压制成板材并进行整修,板材的含水量分别为3.8%(重量)、3.6%(重量)和3.3%(重量)。各板材的内在粘结强度列于表I。
实施例6所用商品木条同实施例1,使用11.5kg粉末组分和11.5kg液态组分,它们的用量为(烘干)木条的50%(重量)并以下方式施涂。将四分之一体积的液体喷涂于木条上,然后将全部粉末吹于其上,再如同实施例3将剩余的液态组分喷涂于木条上。随后将物料掺混1275秒,其中处理量为46.0kg。混合相同重量的另一批物料。然后将二批物料抽吸干燥使含水量为10.4%(重量)。
然后,用实施例1的转盘施涂器施加5.0%(重量)与实施例1相同的树脂,流速为735克/分钟。然后将物料分四批依次掺混95秒,每批处理量为22.5kg。
制得三块基板。制作基板时使用的成型设备是一个管状OSB成型机,基板的构造是60%平行面和40%垂直芯,其中板长2745mm、板宽1475mm。各板重量为34.02kg、含水量为10.4%(重量)。所使用的脱模剂以及抛光板种类与实施例1相同。基板成型后按与实施例1相同的方法压制法成板材。板材的实际含水量为5.5%、6.5%和6.8%(重量)。然后将每块板材整修成1220mm宽、2440mm长、11.1mm厚。其中一块板材在模压、整修后立即在其上表面上无空气喷涂1360g组合物。
其中一块板材(上表面未用组合物喷涂)的内在粘结强度的测定结果列于表I。
实施例7所使用的商品木条同实施例1,按以下方式施加7.04kg粉末组分和7.04kg液态组分。如同实施例3,将四分之一体积的液态组分喷涂于木条上,然后将全部粉末吹于其上,然后将其余的液态组分喷涂于其上。随后分二批将物料掺混770秒,每批处理量为46.9kg。然后将已涂覆的木条抽吸干燥使其含水量为10.1%(重量)。
然后,用实施例1的转盘施涂器施加5%(重量)的树脂(同实施例1),流速为685克/分钟。随后将物料分五批再掺混100秒,每批处理量为22.4kg。
然后如同实施例6将物料制施成二块基板,各基板重量为34.02kg、含水量为10.1%(重量)。制成基板后如同实施例1将物料压制施成板材并予以整修。板材的实测含水量为5.3%和5.6%(重量)。其中一块板材的内在粘结强度列于表I。
实施例8所用商品木条同实施例1,按以下方式使用11.6kg粉末组分和11.5升液态组分,它们的用量为(烘干)木条的50%(重量)。如同实施例3,将四分之一体积的液态组分喷涂于木条上,然后将全部粉末吹于其上,再将其余的液态组分喷涂于其上。然后将物料掺混880秒,该批处理量为46.5kg。随后将物料抽吸干燥以达到10.1%(重量)的含水量。然后,用实施例1的转盘施涂器施加5.0%(重量)实施例1的树脂,流速为625克/分钟。然后将物料分二批再掺和128秒,每批重量为26.7kg。按实施例6的相同方法制成含水量为10.1%(重量)、重量为34.02kg的基板。接着如同实施例1将基板压制施成板材并整修。板材的含水量为5.2%(重量)。
实施例9所用商品木条同实施例1,将11.8kg粉末组分与11.8升液态组分混合,将此混合物(相当于干燥木条的100%(重量))经实施例1的转盘施涂器施加于木条上,流速为4200克/分钟。然后将物料分二批搅和385秒,每批重量为23.7kg。干燥物料,使其含水量为10.9%(重量)。第二天用相同转盘施涂器以666克/分钟的流速施加5.0%(重量)实施例1的树脂。然后将物料分二批掺和160秒,每批重量为35.8kg。按实施例6的相同方法制成38.56kg重的基板,其含水量为10.9%(重量)。然后如同实施例1将基板压制成板材并进行整修。板材的实测含水量为6.8%(重量)。
实施例10所用商品木条同实施例1,将7.8kg粉末组分与7.8升液态组分混成的混合物(其用量为干燥木条的150%(重量))经实施例1的转盘施涂器施加于木条上,流速为5400克/分钟。然后将物料分二批掺混445秒,每批重量为23.7kg。然后,将物料抽吸干燥使其含水量为11.1%(重量)。随后,用相同转盘施涂器以685克/分钟的流速施加5%(重量)实施例1的树脂。然后将物料分二批掺和205秒,每批重量为47.0kg。
如同前一实施例,树脂是在物料存放过夜后施加。基板按实施例6的相同方法制作,其重量为43.09kg、含水量为11.1%(重量)。按实施例1的相同方法将基板压制成板材并进行整修。板材含水量为5.8%(重量)。
以上实施例的结果汇总于下面的表中
表1-第一页涂覆溶液 IB(psi)涂覆溶液 树脂含量中液体(升)初始木含量(基于(基于木条 与粉末(千 涂覆溶液 模压前基刚模压 贮存板材 实施 条的MC木条的%)加涂覆溶克)之比 施加方法 板的MC 成型 14天后尺寸 例号(%) 液的%)1 7-8 30 2.30.8/1.0 转盘113.5 31.5 33.61 7-8 30 2.30.8/1.0 转盘113.5 - 50.41 7-8 30 2.30.8/1.0 转盘113.5 43.8 38.72 7-8 50 5.00.8/1.0 转盘18.193.1 100.33 7-8 50 5.00.8/1.0 液体+ 12.7 129.4 112.8粉末+液体22’×2’ 3 7-8 50 5.00.8/1.0 液体+ 12.7 - 113.4(表面7/16”粉末+液体2喷涂)4 7-8 50 5.00.8/1.0 转盘123.6 - 20.95 7-8 100 5.00.8-1.0 转盘110.1 93.3 72.05 7-8 100 5.00.8/1.0 转盘110.1 106.3 93.75 7-8 100 5.00.8/1.0 转盘110.1 - 91.3
表1-第二页涂覆溶液 IB(psi)初始木 涂覆溶液含树脂含量中液体(升)与板材实施条的MC 量(基于木条 (基于木条加 粉末(千克)涂覆溶液 模压前基刚模压贮存14尺寸例号 (%) 的%) 涂覆溶液的%) 之比 施加方法 板的MC 成型 天后67 505.00.8/1.0液体+ <11 -105.1粉末+液体267 505.00.8/1.0液体+ <11 --粉末+液体267 505.00.8/1.0液体+ <11 --(表面粉末+液体2喷涂)4’×8’ 77 305.00.8/1.0液体+ <11 -137.17/16”粉末+液体277 305.00.8/1.0液体+ <11 --粉末+液体287 505.01.0/1.0液体+ <11 --粉末+液体297 100 5.01.0/1.0转盘1<11 132.63-10 7 150 5.01.0/1.0转盘1<11 132.63-1.在转盘施涂之前将涂覆溶液混合。2.经喷嘴先施加四分之一液体组分,再吹入全部粉末组分,最后施加剩余的液态组分。3.实施例9和10不在65%相对湿度及20℃条件下测定。
表2最小CSA 0437 OSB板材OSB0-2级实施例6 实施例7要求平行 4200psi 4590psi 6350psiMOR垂直 1800psi 3450psi 3560psi平行 800,000psi 741,000psi 905,000psiMOE垂直 225,000psi 428,000psi 435,000psiIB 50psi104psi 121psi煮沸 平行 2100psi 2040psi 2750psi2小时后的 垂直 900psi 1540psi 1640psiMOR煮沸2小时后厚19.2% 24%度膨胀 无要求浸泡24小时后 25% 11.5% 12.6%厚度膨胀密度 43.1lb/ft345.4lb/ft3无要求表2汇总了本发明两种板材的质量性能,并与OSB板材的加拿大标准对照。可以看出,每一块本发明板材的性能都大大超过取向纤维板的性能指标。
按ASTM试验方法E84之规定,检测了本发明板材的表面燃烧特性。具体做法是,将上述实施例9和10的二样品送往Weyerhauser Fire Technology Laboratary,其中每个样品均为根据本发明的厚度为7/16”的4’×8’板材。将样品置于70°F、50%RH的条件调节室内。定期称重样品以测定吸水速度并确定它们是否达到平衡含水量。调理期结束后,将样品分割成二个21”×96”的样条。将一个样条切成21”宽、长度一定的小块,当把各小块头尾相接码放在管道中时,其总长为24’。按美国材料与试验学会(ASTM)试验方法E84-89a规定的步骤进行测试。
测试结果材料类别火焰蔓延指数烟生成指数实施例9 20 -1实施例10 15 30红橡木板 91 100水泥板 001.未知,原因是烟检测系统出现故障。根据目测读数可能低于50。
将上述样条测试30分钟以确定它们能否视为大型建筑法典所规定的“防火处理的木板”。大型建筑法典将“防火处理的木材”定义为在制造过程中以加压或其它方法用化学物质浸渍的任何木制品,并且,按U.B.C.标准42-1号(或ASTM E84)测试30分钟时,火焰蔓延指数不超过25且无进一步燃烧迹象。此外,在整个测试期间火焰前端不超出燃烧器中心线的10.5英尺。
二个样条的火焰前端教师都未超出10.5英尺,因此二样条均可视作“防火处理的木材”。实施例8的火焰前端扩展至10.5英尺,而实施例9的火焰前端扩展至9英尺。
其他数据样品的固定常规,边缘支撑。
样品重量实施例9-29.90磅(lbs.)实施例9-29.20lbs.
实施例10-32.80lbs.
实施例10-32.05lbs.
燃烧特性实施例9的样品55秒后引燃,8分钟后火焰前端扩展至10.5英尺。火焰前端在此距离处维持数分钟后退回到8英尺以内直至试验结束。实施例10的样品48秒后引燃,15分钟后火焰前端扩展至9英尺,然后缓慢退回到7英尺。二者燃烧时均为黄色火焰且低烟。
实施例12使用制造中密度纤维板(MDF)所常用的木纤维,用与100%干燥纤维等重的混合物喷涂木纤维。混合物中粉末组分与液态组分的比率为1g粉末组分对应1ml液体组分。用无空气喷枪将混合物喷涂于木纤维上,用叶轮掺和机掺混。混合物全部加入掺和机中的MDF配料后,加入5.5%(以配料干重为准)ICI提供的MDI树脂。然后将已用混合物和树脂浸渍了物料转移到研磨机中机械研磨60秒。然后用压缩空气将已浸渍的纤维从研磨机输入计量箱。经计量箱将已浸渍物料用压缩空气输入真空成型机。在模压前让低密度物料在刮台下面通过以适当调高密度。物料达到适宜密度后,在已浸渍纤维的上面和底部装上抛光板。将二块钢制抛光板间夹持的物料置于热压机中于280°F压制180秒,压制压力为每平方英寸90磅。
以这种方式生产MDF材料并将其压成板材,一周后测定板材的以下物理性能和燃烧特性表III厚度(英寸) 0.682破坏模量(MOR)(psi) 2577弹性模量(MOE)(1000psi) 377内聚强度(IB)(psi) 113(模压后的)含水量(MC)% 6.9螺旋拉力面(磅) 260螺旋拉力边(磅) 255吸水率% 32.0厚度膨胀% 9.7密度(lbs/ft3) 51.2MOH-硬度 1300密度梯度仪测定的表面密度 63.1(表面30密耳的平均密度,磅/立方呎)
密度梯度仪测定的芯层密度45.8燃烧面积6.04燃烧面对参照面的% 96灰份% 23.98含砂量%6.16线性膨胀% 0.4050%相对湿度时厚度膨胀平衡含水量5.9%90%相对湿度时厚度膨胀平衡含水量31.9%实施例13按以下方法制法得二块本发明的板材。使用山杨类商品木条(厚0.03”、宽0.5-2”、长约4”),其烘干含水量(MC)为7~8%并除去小于4.8mm的细末。前述配方的组合物是比例为21.7kg粉末组分对26.6kg液体组分的掺混物,以4200克/分钟的流速用类似于实施例3的空气雾化喷嘴将上述组合物涂于商品木条上(组合物用量为待加入它的烘干木条或配料重量的100%);其中粉末和液体组分在经空气雾化喷嘴施加之前已混合好。组合物施加温度维持在20℃。经空气雾化喷嘴施加后,用筒式间歇掺和机(直径2.44m×深1.22m)掺混商品木条及组合物直至组合物均匀地涂覆在木条上(约690秒),其中掺和机设定在每分钟15转。处理批量为47.6kg。
将物料混匀后,用类似于实施例1的转盘施涂器以800克/分钟的流速施加5%(重量)(以组合物及木条重量为准)的MDI MF-184树脂(由ICI提供)。转盘设定为每分钟12000转。
然后,用上述筒式间歇掺和机将树脂与物料掺和80秒。本批树脂涂覆物料的处理量为12.9kg。掺和后用手工将物料制成基板。基板构造是,100%无规取向,单层,长865mm、宽865mm。制作基板所使用的抛光板是密闭的罩板,它具有固定的钢制上抛光板和锡制底板。以610ACI为脱模剂以使基板成型后易于下料。压制前二块基板的含水量各为24.6%和25.8%(重量)。
基板成型后于大约450psi压力、190℃板温下热压185秒制成板材。热压后板材含水量为15.8%和17.7%。将板材整修成712mm长、712mm宽、11.1mm厚。按CAN3-0437-85方法测得板材内在粘结强度为98和80psi,测定时每块试验材料的厚度为11.0mm,测定条件为相对湿度65%、20℃。经修整后,第二块板材的平均内聚强度为116.3psi。第二块板材的平均MOR为1730psi,平均密度为45.8磅/立方英尺。
至于本发明的其他实施方案,本技术领域熟练技术人员通过对本文所公开的本发明的说明书及实施进行思考后是很容易弄清的。需要强调的是,本说明书和实施例仅是作为举例说明,而本发明的真正范围和精髓将在下列权利要求中阐述。
公开了包含细碎的材料如纤维素材料和一定量含能有效地赋予该材料以耐水耐火性的氯氧化镁和/或含氧硫酸镁的胶乳的组合物。还公开了制造该耐火耐水产品的方法。
耐水耐火材料及其制造方法
- 专利详情
- 全文pdf
- 权力要求
- 说明书
- 法律状态
查看更多专利详情
下载专利文献
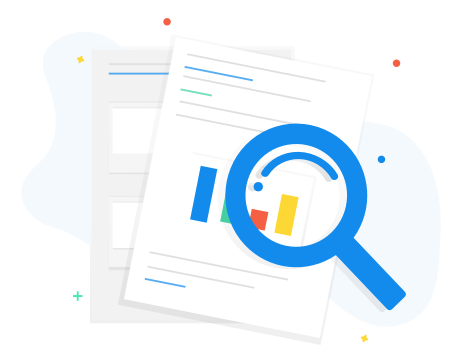
下载专利
同类推荐
-
李楠赵风清付伟峰, 窦涛付伟峰, 窦涛付伟峰, 窦涛
您可能感兴趣的专利
-
王新, 王桂英J·H·阿伦斯J·H·阿伦斯J·H·阿伦斯J·H·阿伦斯
专利相关信息
-
蒂莫·皮沃斯基, 贝恩德·威尔维斯克里斯托斯.阿内齐里斯克里斯托斯.阿内齐里斯丘云灵, 熊玉李宗武马克·K·邦卡特, 陈兆男吴健, 徐刘彬