专利名称:一种碳复合耐火材料的制备方法及其得到的产品的制作方法碳复合耐火材料是指以氧化物基料和碳素为主要原料,并添加适量结合剂及其他添加剂而制成的材料,常见的碳复合耐火材料有镁碳质、铝碳质和锆碳质耐火材料。碳复合耐火材料不仅耐火度高、高温强度好,而且其抗渣蚀和抗热震的性能良好,广泛适用于高炉、转炉、电炉和连铸系统等钢铁冶金领域。碳复合耐火材料用于炼钢领域时,高温熔钢与碳复合耐火材料表面接触时,碳素在高温下会通过接触面逐渐向熔钢内溶解扩散,导致熔钢的含碳量增加、品质降低。为了提高熔钢的品质,直接的解决方法是降低碳复合材料中的含碳量,以减少碳素在熔钢内的溶解量;但是,单纯的减少含碳量容易导致碳复合耐火材料的抗渣蚀和抗热震性降低,使得材料的使用寿命缩短。为了解决上述问题,有研究人员提出将碳纳米管引入耐火材料中,由于碳纳米管具有强度高和热稳定性强的特性,使其在高温下不易发生溶解扩散,因而既维持了碳复合耐火材料的碳含量,又减少了熔钢内的碳溶解量,同时加入碳纳米管使所制备的碳复合耐火材料具有很高的抗热震性,并且由于碳纳米管与一般碳素材料相比具有较高的比表面积,因而能够进一步提高碳复合耐火材料的抗渣蚀性。目前,向碳复合耐火材料中添加碳纳米管的方法是在制备碳复合耐火材料时,将碳纳米管加入到原料中并进一步混合,但外加碳纳米管一旦搅拌不充分是很难在原料中分散均匀的,因而会影响制备得到的碳复合耐火材料的性能。为了解决这一问题,中国专利文献CN101269980A公开了一种粗大碳纳米管及碳纳米纤维在碳复合耐火材料中的生成方法,将占物料总重量0.5-3%的硝酸镍配制成浓度为10%的水溶液后,与耐火原料刚玉粉或石墨充分混合,并对混合物进行烘干,然后将烘干物与其他剩余原料配合,经混炼、成型、干燥和埋炭煅烧,即可制备得到生成有粗大碳纳米管或碳纳米纤维的碳复合耐火材料;该技术制备得到的碳复合耐火材料,经测试表征可知,粗大的碳纳米管及碳纳米纤维呈丛状交织于碳复合耐火材料内部,长度可达数十微米,附图中表示出粗大碳纳米管的平均直径为2-3微米。上述技术制备出了原位生长有粗大碳纳米管的碳复合耐火材料,解决了外加碳纳米管在碳复合耐火材料中分散不均匀的问题;但是,该技术制备得到的碳复合耐火材料中粗大碳纳米管的平均直径并没有达到纳米级,而是碳微米管,从性能上来讲,碳微米管的强度、热稳定性和比表面积均不及碳纳米管,因而会导致制备的碳复合耐火材料的抗渣蚀性和抗热震性较低的问题。
本发明所要解决的技术问题是现有技术的碳复合耐火材料中原位生长的粗大碳纳米管并没有达到纳米级,而是碳微米管,由于碳微米管的强度、热稳定性和比表面积不及碳纳米管,因而导致碳复合耐火材料的抗渣蚀性和抗热震性较低;进而提供一种制备得到均匀分散有碳纳米管、且具有高抗渣蚀性和高抗热震性的碳复合耐火材料的方法,以及由该方法得到的耐火材料。为解决上述技术问题,本发明提供了一种碳复合耐火材料的制备方法,包括以下步骤,( I)将活性物前驱体配成溶液,向上述溶液中加入氧化物混合,混合物经干燥并分散后,焙烧得到活性物-氧化物复合料;(2)用活化后的活性物-氧化物复合料催化碳源气体、或碳源气体和氢气的混合气体进行裂解反应,得到氧化物-碳纳米管复合料;(3)将氧 化物-碳纳米管复合料浸溃在乙醇溶液中形成预浸体;(4)向基料中依次加入结合剂和步骤(3)中的预浸体进行混合,之后困料、成型、干燥即得到碳复合耐火材料。所述活性物前驱体是摩尔比1: (0.2-5)的硝酸铁和硝酸镍,活性物前驱体溶液的摩尔浓度为0.05-0.5mol/L ;所述氧化物为刚玉、镁砂和氧化锆中的一种或多种,所述氧化物的粒径为2-500 μ m;向所述活性物前驱体溶液中加入所述氧化物的量为l-10g/ml。步骤(I)中,干燥并分散后的活性物前驱体-氧化物复合料的粒径为2-500 μ m,焙烧温度为300-600°C,焙烧时间为30-120min。裂解温度为600-900°C,裂解时间为l_4h ;所述碳源气体为天然气、乙烷和乙烯中的一种或多种,所述碳源气体的流量为100-500L/h ;所述混合气体中,所述碳源气体和氢气的体积比为(1-4):(4-1);所述氧化物-碳纳米管复合料的粒径小于或等于500 μ m。所述乙醇溶液的浓度为20_95v%,所述乙醇溶液为氧化物-碳纳米管复合料的3-15wt%,浸溃时间为0.5-3h ;所述基料、结合剂和氧化物-碳纳米管复合料的质量比为(50-70):(3-10):(20-40);所述基料为电熔白刚玉、电熔致密刚玉、矾土基电熔刚玉、板状刚玉、烧结刚玉、电熔镁砂、烧结镁砂、锆莫来石、锆刚玉和电熔氧化锆中的一种或多种,所述基料的粒径小于或等于8_;所述结合剂为酚醛树脂;步骤(4)中,困料温度为20-35°C,困料时间为12-48h,干燥温度为110-350°C,干燥时间为12_48h。在步骤(4)中,向所述基料中最后加入预混体,再进行混合、困料、成型和干燥;所述预混体为微米级的氧化物微粉;所述基料、结合剂、氧化物-碳纳米管复合料和氧化物微粉的质量比为(50-70): (3-10):(20-40): (4_10);所述氧化物微粉为粒径小于或等于5 μ m的氧化铝。在步骤(4)中,向所述基料中最后加入预混体,再进行混合、困料、成型和干燥;所述预混体为石墨和炭黑中的至少一种、微米级的氧化物微粉和抗氧化剂的混合物;所述石墨和炭黑中的至少一种、基料、结合剂、氧化物-碳纳米管复合料、氧化物微粉和抗氧化剂的质量比为(0.2-3): (50-70):(3-10): (20-40): (4-10): (2-8);所述氧化物微粉为粒径小于或等于5 μ m的氧化铝;所述石墨或炭黑的粒径小于或等于147 μ m ;所述抗氧化剂为碳化物、硼化物、氮化物、金属铝和单质硅中的一种或多种,所述抗氧化剂的粒径小于或等于74 μ m0所述制备方法得到的耐火材料,包括如下组分,基料50_72wt%氧化物-碳纳米管复合料20_41wt%固化的酚醛树脂2.l_10wt%所述氧化物-碳纳米管复合料中,包覆生长在氧化物上的碳纳米管的直径为20_100nm。所述氧化物-碳纳米管复合料中碳纳米管的含量为0.5-3wt% ;所述氧化物-碳纳米管复合料为氧化铝-碳纳米管复合料、氧化镁-碳纳米管复合料和氧化锆-碳纳米管复合料中的一种或多种。还包括氧化物微粉,或者石墨和炭黑中的至少一种、氧化物微粉和抗氧化剂;所述氧化物微粉占所述碳复合耐火材料的4-10wt%,所述石墨和炭黑中的至少一种占所述碳复合耐火材料的0.2-3wt%,所述抗氧化剂占所述碳复合耐火材料的2-8wt% ;所述氧化物微粉为氧化铝,所述抗氧化剂为碳化物、硼化物、氮化物、金属铝和单质硅中的一种或多种。本发明与现有技术方案相比具有以下有益效果:(I)本发明所述碳复合耐火材料的制备方法,包括以下步骤,I)将活性物前驱体配成溶液,向上述溶液中加入氧化物混合,混合物经干燥并分散后,焙烧得到活性物-氧化物复合料;2)用活化后的活性物-氧化物复合料催化碳源气体、或碳源气体和氢气的混合气体进行裂解反应,得到氧化物-碳纳米管复合料;3)将氧化物-碳纳米管复合料浸溃在乙醇溶液中形成预浸体;4)向基料中依次加入结合剂和步骤3)中的预浸体进行混合,之后困料、成型、干燥即得到碳复合耐火材料。本发明先将 干燥后的活性物前驱体-氧化物复合料分散成为小颗粒,再将其焙烧成小颗粒的活性物 -氧化物复合料催化碳源气体进行裂解反应,从而能够得到均匀包覆生长有碳纳米管的氧化物-碳纳米管复合料。混合时,事先将氧化物-碳纳米管复合料浸于乙醇中制备预浸体,先用结合剂先将大颗粒的基料粘合成混合物,而后加入预浸体,能够使小颗粒的复合料均匀分散在混合物中;并且,预浸体中的乙醇能够促进结合剂对复合料的润湿性,从而进一步促进了复合料与基料、结合剂的均匀混合,进一步使碳纳米管均匀分散在耐火材料中,使耐火材料具有优良的抗渣蚀性和抗热震性。现有技术是将活性物前驱体加入到刚玉粉或石墨以及其它耐火材料原料中经烘干和埋炭煅烧,使“粗大碳纳米管”的生成和耐火材料的制备同时完成。现有技术既没有制备出小颗粒的活性物-氧化物复合料,也没有采用其对碳源气体进行催化裂化预先制备出氧化物-碳纳米管复合料,因此没有对碳纳米管的生长进行精细的控制,碳纳米管在生长时容易因生长条件的不适而生长形成碳微米管,即现有技术中的“粗大碳纳米管”;本发明通过精细控制生成条件,能够在氧化物上均匀包覆生长出碳纳米管,并且通过控制混合手段使得碳纳米管能够均匀分散在耐火材料中,避免了现有技术制备得到的碳微米管耐火材料抗渣蚀性和抗热震性不佳的问题。(2)本发明所述碳复合耐火材料的制备方法,所述活性物前驱体是摩尔比1:(0.2-5)的硝酸铁和硝酸镍,活性物前驱体溶液的摩尔浓度为0.05-0.5mol/L ;所述氧化物为刚玉、镁砂和氧化锆中的一种或多种,所述氧化物的粒径为2-500 μ m ;向所述活性物前驱体溶液中加入所述氧化物的量为l-10g/ml。步骤(I)中,干燥并分散后的活性物前驱体-氧化物复合料的粒径为2-500 μ m,焙烧温度为300-600°C,焙烧时间为30_120min。按照上述方法制备的活性物前驱体-氧化物复合料干燥后分散均匀,在300-600°C下焙烧30-120min,除去硝酸根离子的同时氧化生成活性物-氧化物复合料,该复合料上均匀分布有活性物质,并且活性物质的浓度能够使碳纳米管均匀生长在氧化物上。(3)本发明所述碳复合耐火材料的制备方法,裂解温度为600-900°C,裂解时间为l_4h;所述碳源气体为天然气、乙烷和乙烯中的一种或多种,所述碳源气体的流量为100-500L/h ;所述混合气体中,所述碳源气体和氢气的体积比为(1- 4): (4 -1)。使用活性物-氧化物复合料作为催化剂催化碳源气体进行裂解反应,伴随一定浓度的碳源气体加入的氢气可以保证碳纳米管在活性物-氧化物复合料上持续生长,最后得到均匀生长有碳纳米管的氧化物-碳纳米管复合料。(4)本发明所述的碳复合耐火材料,包括如下组分组成:50_70被%的基料,20-40wt%的氧化物-碳纳米管复合料,2.25-8.5wt%的固化酚醛树脂,所述氧化物_碳纳米管复合料中,包覆生长在氧化物上碳纳米管的直径为20-100nm。将氧化物-碳纳米管复合料和基料作为原料,与结合剂酚醛树脂一起制备耐火材料,经干燥后,酚醛树脂发生固化,固化后的酚醛树脂形成交联的网状结构,能够将复合料和基料均匀混合粘结。所制备的耐火材料中碳纳米管均匀包覆生长在氧化物上,因而碳纳米管能够牢固结合并均匀分散在耐火材料中,该耐火材料的抗渣蚀和抗热震性能良好。(5)本发明所述的碳 复合耐火材料,所述氧化物-碳纳米管复合料中碳纳米管为0.5_3wt%。由于碳纳米管具有强度高、热稳定性强和比表面积高的特点,因而耐火材料中含有较少量的碳纳米管,仍然能够具有良好的抗渣蚀性和抗热震性。
为了使本发明的内容更容易被理解,本发明结合附图和
对本发明的内容进行进一步的说明;图1为本发明实施例1中所述氧化铝-碳纳米管复合料的高分辨率透射电镜图;图2为本发明测试例中抗热震性测试的示意图;图3为本发明测试例中抗渣蚀性测试的示意图;其中附图标记为:1-匣钵,2-试样,3-坩埚内孔截面,4-侵蚀后靠近坩埚内孔截面的侵蚀面。
碳复合耐火材料中含有60.6wt%的板状刚玉、4wt%固化的酚醛树脂和35.4wt%的氧化锆-氧化铝-碳纳米管复合料。实施例4(I)向IOmol的硝酸铁和Imol的硝酸镍中加水配置成0.05mol/L的活性物前驱体溶液,向IL的上述溶液中加入2000g、2 μ m的刚玉粉相混合,混合物在60°C下干燥24h后用球磨机分散为2 μ m的颗粒,将上述颗粒在300°C焙烧2h得到活性物-氧化铝复合料;向活性物-氧化铝复合料中通入99.99%氩气并升温至500°C,然后停止通氩气,同时向活性物-氧化铝复合料中通入200L/h的99.99%氢气活化0.5h ;(2)向活化后的活性物-氧化铝复合料中通入100L/h纯度为98v%的天然气进行裂解反应,裂解温度为900°C,裂解时间为lh,得到粒径为10 μ m的氧化铝-碳纳米管复合料,其中碳纳米管的直径为50-100nm,含量为3wt% ;(3)将200g的氧化铝-碳纳米管复合料浸溃在30g、20v%的乙醇溶液中3h形成预浸体; (4)向700g、粒径为小于或等于8mm的电熔白刚玉中依次加入60g的固体粉状酚醛树脂和40g热固型液态树脂、步骤(3)中的预浸体和40g、5 μ m的氧化铝微粉混练5_10min,之后在20°C困料48h,加工成坯体,将坯体在110°C干燥48h即得到碳复合耐火材料。碳复合耐火材料中含有69.3wt%的电熔白刚玉、6.9wt%固化的酚醛树脂、19.8wt%的氧化铝-碳纳米管复合料和4wt%的氧化铝微粉。实施例5(I)向Imol的硝酸铁和5mol的硝酸镍中加水配置成0.5mol/L的活性物前驱体溶液,向IL的上述溶液中加入IOOOgUOO μ m的镁砂相混合,混合物在80°C下干燥36h后用球磨机分散为100 μ m的颗粒,将上述颗粒在600°C焙烧30min得到活性物-氧化镁复合料;向活性物-氧化镁复合料中通入99.99%氩气并升温至600°C,然后停止通氩气,同时向活性物-氧化镁复合料中通入300L/h、99.99%的氢气活化Ih ;(2)向活化后的活性物-氧化镁复合料中通入500L/h纯度为95v%的天然气进行裂解反应,裂解温度为600°C,裂解时间为4h,得到粒径为30 μ m的氧化镁-碳纳米管复合料,其中碳纳米管的直径为20-70nm,含量为lwt% ;(3)将400g的氧化镁-碳纳米管复合料浸溃在12g、95v%的乙醇溶液中0.5h形成预浸体;(4)向500g、粒径为小于或等于5_的电熔镁砂中依次加入30g的热固型液态酚醛树、步骤(3)中的预浸体和100g、3 μ m的氧化铝微粉混练5-10min,之后在35°C困料12h,加工成坯体,将坯体在350°C干燥12h即得到碳复合耐火材料。碳复合耐火材料中含有49wt%的电熔镁砂、2.lwt%固化的酚醛树脂、39wt%的氧化镁-碳纳米管复合料和9.9wt%的氧化铝微粉。实施例6(I)向Imol的硝酸铁和2mol的硝酸镍中加水配置成0.4mol/L的活性物前驱体溶液,向IL的上述溶液中加 入IOOOgUOO μ m的氧化锆相混合,混合物在80°C下干燥36h后用球磨机分散为100 μ m的颗粒,将上述颗粒在400°C焙烧45min得到活性物-氧化锆复合料;向活性物-氧化锆复合料中通入纯氩气并升温至600°C,然后停止通纯氩气,同时向活性物-氧化锆复合料中通入300L/h的高纯氢气活化Ih ;(2)向活化后的活性物-氧化锆复合料中通入200L/h纯度为95v%的乙烯和50L/h的高纯氢气进行裂解反应,裂解温度为700°C,裂解时间为3h,得到粒径为IOym的氧化锆-碳纳米管复合料,其中碳纳米管的直径为70-100nm,含量为4wt% ;(3)将350g的氧化锆-碳纳米管复合料浸溃在12g、95v%的乙醇溶液中0.5h形成预浸体;(4)向600g、粒径为小于或等于3mm的电熔氧化锆中依次加入50g的热固型液态酚醛树、步骤(3)中的预浸体和50g、l μ m的氧化铝粉体混练5-10min,之后在30°C困料24h,加工成坯体,将坯体在250°C干燥12h即得到碳复合耐火材料。碳复合耐火材料中含有57.7wt%的电熔氧化锆、3.9wt%固化的酚醛树脂、33.7wt%的氧化锆-碳纳米管复合料和4.7wt%的氧化铝微粉。实施例7(1)向Imol的硝酸铁和0.2mol的硝酸镍中加水配置成0.05mol/L的活性物前驱体溶液,向IL的上述溶液中加入1000g、6.5 μ m的刚玉粉相混合,混合物在60°C下干燥24h后用球磨机分散为6.5 μ m的颗粒,将上述颗粒在300°C焙烧2h得到活性物-氧化铝复合料;向活性物-氧化铝复合料中通入99.99%氩气并升温至500°C,然后停止通氩气,同时向活性物-氧化铝复合料中通入200L/h的99.99%氢气活化0.5h ;(2)向活化后的活性物-氧化铝复合料中通入100L/h纯度为98v%的天然气和100L/h的氢气进行裂解反应,裂解温度为900°C,裂解时间为lh,得到粒径为43 μ m的氧化铝-碳纳米管复合料,如图1所示,其中碳纳米管的直径为20-40nm,含量为2wt% ;(3)将200g的氧化铝-碳纳米管复合料浸溃在30g、20v%的乙醇溶液中3h形成预浸体;(4)将40g粒径为5 μ m的氧化铝粉体、2g粒径为10 μ m的炭黑和20g粒径为20 μ m的碳化硼混合成预混体;(5)向700g、粒径为小于或等于8mm的电熔白刚玉中依次加入IOOg的液态热固型酚醛树脂、步骤(3)中的预浸体和步骤(4)中的预混体混练5-10min,之后在20°C困料48h,加工成坯体,将坯体在110°C干燥48h即得到碳复合耐火材料。碳复合耐火材料中含有67.5wt%的电熔白刚玉、7.2wt%的固化的酚醛树脂、19.3wt%的氧化招-碳纳米管复合料、3.9wt%的氧化招、1.9wt%的碳化硼和0.2wt%炭黑。实施例8(I)向Imol的硝酸铁和5mol的硝酸镍中加水配置成0.5mol/L的活性物前驱体溶液,向IL的上述溶液中加入1000g、500 μ m的镁砂相混合,混合物在80°C下干燥36h后用球磨机分散为500 μ m的颗粒,将上述颗粒在600°C焙烧30min得到活性物-氧化镁复合料;向活性物-氧化镁复合料中通入纯氩气并升温至600°C,然后停止通纯氩气,同时向活性物-氧化镁复合料中通入300L/h的纯氢气活化Ih ;(2)向活化后的活性物-氧化镁复合料中通入500L/h纯度为95v%的天然气进行裂解反应,裂解温度为600°C,裂解时间为4h,得到粒径为30 μ m的氧化镁-碳纳米管复合料,其中碳纳米管的直径为20-70nm,含量为3wt% ;(3)将400g的氧化镁-碳纳米管复合料浸溃在12g、95v%的乙醇溶液中0.5h形成预浸体;(4)将IOOg粒径为3-5 μ m的氧化铝粉体、30g粒径为13 μ m的石墨和80g粒径为40-60 μ m的碳化硼混合成预混体;(5)向500g、粒径为2mm的电熔镁砂中依次加入30g的热固型液态酚醛树脂、步骤
(3)中的预浸体和步骤(4)中的预混体混练5-10min,之后在35°C困料12h,加工成坯体,将坯体在350°C干燥12h即得到碳复合耐火材料。碳复合耐火材料中含有44.lwt%的电熔镁砂、2.lwt%固化的酚醛树脂、35.3wt%的氧化镁-碳纳米管复合料、2.65wt%的石墨、8.81wt%的氧化铝微粉和7.04wt%的碳化硼。实施例9(I)向Imol的硝酸铁和2mol的硝酸镍中加水配置成0.4mol/L的活性物前驱体溶液,向IL的上述溶液中加入200g、100 μ m的氧化锆相混合,混合物在80°C下干燥36h后用球磨机分散为100 μ m的颗粒,将上述颗粒在400°C焙烧45min得到活性物-氧化锆复合料;向活性物-氧化锆复合料中通入纯氩气并升温至600°C,然后停止通纯氩气,同时向活性物-氧化锆复合料中通入300L/h的高纯氢气活化Ih ;(2)向活化后的活性物-氧化锆复合料中通入200L/h纯度为95v%的乙烯和IOL/h的高纯氢气进行裂解反应,裂解温度为700°C,裂解时间为3h,得到粒径为IOym的氧化锆-碳纳米管复合料,其中碳纳米管的直径为70-100nm,含量为2wt% ;(3)将290g的氧化锆-碳纳米管复合料浸溃在24g、95v%的乙醇溶液中0.5h形成预浸体;(4)将15g粒径为100-125 μ m的石墨、IOg粒径为50-80 μ m的炭黑和15g粒径为40-60 μ m的单质娃和20g粒径为40_60 μ m金属招粉混合成预混体;(5)向600g、粒径为小于或等于3mm的电熔氧化锆中依次加入50g的热固型液态酚醛树脂、步骤(3)中的预浸体和步骤(4)中的预混体混练5-10min,之后在30°C困料24h,加工成坯体,将坯体在300°C干燥24h即得到碳复合耐火材料。碳复合耐火材料中含有60.6wt%的电熔氧化锆、4wt%固化的酚醛树脂、29.2wt%的氧化错-碳纳米管复合料、1.5wt%的石墨,1.0wt%的炭黑,1.5wt%的单质娃粉,2.2wt%的金属招粉。对比例称取5克硝酸镍加入45克蒸馏水配制成浓度为10%的溶液后加入330g的粒度为〈0.043mm的板状刚玉粉中充分混合,将混合物置于干燥箱于110°C下干燥48小时至其中的水分排除,然后将干燥产物置于研磨机中研磨30分钟后与30g a -Al2O3粉、20g金属硅粉混合成备用粉体。将称取好的60g酚醛树脂在80°C的水浴中加热15分钟后,将其一半加入到380g粒度小于1.0mm的板状刚玉中,在混合机中混合5分钟后加入240g鳞片石墨,继续混合5分钟后将剩余的酚醛树脂和备用粉体加入到其中,再继续混合20分钟后将混合物装入塑料袋中困料5-6小时;困好的物料用万能 压力机压制成坯体,将坯体置于180°C的干燥箱中干燥24小时后埋碳加热到1450°C,保温4个小时,自然冷却至室温即得到碳复合耐火材料制品。测试例
(I)显气孔率和体积密度的测定依据国家标准GB/T2997-2000的测试方法对实施例1_9及对比例制备的碳复合耐火材料的显气孔率和体积密度进行测试,测试结果见下表。(2)常温耐压强度的测定依据国家标准GB/T5072.2-2004的测试方法对实施例1_9及对比例制备的碳复合耐火材料的常温耐压强度进行测试,测试结果见下表。(3)高温抗折强度的测定依据国家标准GB/T3002-2004的测试方法对实施例1_9及对比例制备的碳复合耐火材料的高温抗折强度进行测试,试验温度为1100°c,保温时间为lh,测试结果见下表。(4)抗热震性的测定将实施例1-9及对比例的碳复合耐火材料分别制成3个相同的长条形试样,依据国家标准GB/T3002-2004的测试方法用三点弯曲装置测定试样的热震前抗折强度Retl,如图2所示,将3个长条形试样由左至 右依次排列装在填满鳞片石墨的耐热钢制匣钵内密封,将匣钵置入电炉中1100°C保温30min取出,迅速将匣钵置入常温水中冷却,然后调换3个试样的位置,按照上述方式操作一次,之后再次调换3个试样的位置,重复一次上述操作,测定试样的热震后抗折强度Re,Re/Re(l为试样的抗折强度保持率,3个试样抗折强度保持率的平均值为该碳复合耐火材料的抗折强度保持率,结果见下表。调换3个试样的位置进行测试,可以保证每个试样的实验条件相同。(5)抗渣蚀性测定如图3所示,将实施例1-9及对比例的碳复合耐火材料制成外部尺寸为H50X Φ50πιπι、内部尺寸为Η18Χ Φ22πιπι的坩埚。分别向上述坩埚内装填20g钢包渣(成分为 12.18wt% 的 SiO2,2.10wt% 的 Al203、31.01wt% 的 Fe203>41.59wt% 的 CaO,9.30wt% 的 MgO、
0.035wt% 的 K2O,0.05wt% 的 Na2O 和 0.66wt% 的 TiO2,碱度 m(CaO) /m(SiO2) =3.4),然后将坩埚置于埋炭气氛下在1500°C下煅烧3h,冷却后将坩埚沿纵向剖开,观察钢包渣对坩埚的侵蚀情况,坩埚内孔的截面积为Stl,侵蚀后靠近坩埚内孔截面的侵蚀面面积为S,计算侵蚀指数公式为S/XX 100%,结果见下表。
本发明公开了一种碳复合耐火材料的制备方法,包括以下步骤,(1)将活性物前驱体配成溶液,向上述溶液中加入氧化物混合,混合物经干燥并分散后,焙烧得到活性物-氧化物复合料;(2)用活化后的活性物-氧化物复合料催化碳源气体、或碳源气体和氢气的混合气体进行裂解反应,得到氧化物-碳纳米管复合料;(3)将氧化物-碳纳米管复合料浸渍在乙醇溶液中形成预浸体;(4)将氧化物微粉、炭黑与石墨中的至少一种和抗氧化剂混合成预混体;(5)向基料中依次加入结合剂、预浸体和预混体进行混合,之后困料、成型、干燥即得到碳复合耐火材料,所制备耐火材料中碳纳米管的分布均匀,与耐火原料的结合力强,所制备的耐火材料适用于冶金炼钢行业的高温环境。
一种碳复合耐火材料的制备方法及其得到的产品制作方法
- 专利详情
- 全文pdf
- 权力要求
- 说明书
- 法律状态
查看更多专利详情
下载专利文献
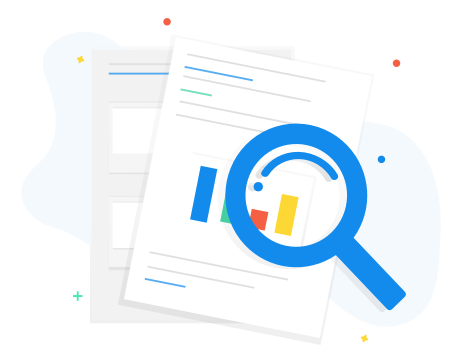
下载专利
同类推荐
-
魏家浩吕志伟吕志伟吕志伟
您可能感兴趣的专利
-
P·莫拉佐尼P·莫拉佐尼李会郎, 李承元芮秀明, 张秉文
专利相关信息
-
芮秀明K·罗杰斯, G·迪泽瑞嘉