专利名称::一种新型气雾染色机的制作方法:目前我国染色行业所普遍使用的染色设备主要是液流染色机。它的主要原理是将液体染料助剂及水的混合物通过喷嘴喷洒在织物上,使织物在被染色的同时获得循环运动的动力。它必须要提供足够循环泵带动织物运行的水,需要的浴比非常高,同时带来能耗高、排污大、布速低和企业经济效益差等缺陷。而且由于织物的运动主要靠染液与织物之间的摩擦将动能传递给织物,液流的密度较大,在与织物连续摩擦的过程中,对织物产生很大冲击力,容易造成纤维的磨损,影响织物的外观,甚至会造成经纱的位移而破坏织物的结构。
本发明所要解决的技术问题是提供一种不损坏织物、浴比低、节能环保的新型气雾染色机,为此,本发明采用以下技术方案它包括主缸体、高压鼓风机和喷嘴雾化系统,所述高压鼓风机的一端出口与喷嘴雾化系统中的高压进气口相通;喷嘴雾化系统的两端即织物进口和织物出口,该织物进口和织物出口分别与主缸体相通;喷嘴雾化系统内设有染液切割喷嘴、能量转换喷嘴与提布辊。所述染液切割喷嘴为环状狭缝形,所述能量转换喷嘴的轴向截面由直管段、锥度段和渐扩段三段组成;所述高压鼓风机的另一端进口与设于主缸体内部的空气过滤网相通。通过以上技术方案,本发明特殊的喷嘴雾化系统能很好的对染液进行雾化,采用气雾流染色,取消了对织物的循环染液牵引而由气流牵引织物运行,从而使浴比大为降低,节约能源、减少污染,促进环保。图l为本发明的原理示意图。图2为从侧面角度看本发明的整体结构示意图。图3为从正面角度看本发明的整体结构示意图。图4为从俯视角度看本发明的整体结构示意图。图5为本发明喷嘴雾化系统的结构示意图。图6为图5从俯视角度的结构示意图。图7为本发明喷嘴雾化系统的内部结构示意图。图8为本发明喷嘴雾化系统中的导布轮装置剖视图。图9为本发明喷嘴雾化系统包括导布轮电机的结构示意图。图10为图9的B-B剖视图,也即本发明喷嘴雾化系统中的染液切割喷嘴的布置示意图。图11为本发明喷嘴雾化系统中的染液切割喷嘴的结构剖视图。图12为本发明喷嘴雾化系统中的染液切割喷嘴的另一个结构剖视图。图13为浴比对一次成功率及重现性影响图。图14为气流染色机和传统溢流染色机的效益比较直方图。具体实施例方式参照附图1、2、3、4、5、6、7、8。本发明包括主缸体1、高压鼓风机3和喷嘴雾化系统2,所述高压鼓风机3的一端出口33与喷嘴雾化系统中的高压进气口35相通;喷嘴雾化系统2的两端即织物进口21和织物出口22,该织物进口21和织物出口22分别与主缸体1相通;喷嘴雾化系统2内设有染液切割喷嘴96,能量转换喷嘴8与提布辊7。所述喷嘴雾化系统上还设有染液进口23。参照附图10所述染液切割喷嘴96为环状狭缝形,参照附图7该能量转换喷嘴8的轴向截面由直管段81、锥度段82和渐扩段83三段组成,独特的喷嘴设计使气液两相进入喷嘴后都能混合成雾化状,织物与雾化状染液接触后,有利于染液向纤维的边界层扩散、渗透、固着进行染色。所述高压鼓风机的另一端进口34与设于主缸体1内的空气过滤网相通。所述喷嘴雾化系统织物出口22下方设有摆布器4,该摆布器4的下方设有储布槽5,储布槽5另一端与喷嘴雾化系统中的织物进口21相通,喷嘴雾化系统2、摆布器4和储布槽5形成可供织物在内循环移动的循环回路。能量转换喷嘴8的独特设计使得在喷嘴的锥度段与喷嘴雾化系统中的织物出口之间形成低压区,使得部分染液迅速汽化成雾状,雾状的染料分子动能增加,渗透力增强,此时雾状染料分子的微粒小于液状染料分子体积,染料分子单位时间内的泳移增加进一步提高织物的染色匀染性,缩短了织物的上染时间,提高生产效率。本发明使用的时候,首先高压鼓风机3运行,通过能量转换喷嘴8产生足够强的负压,将织物10吸入到喷嘴雾化系统2中,接着经过喷嘴雾化系统中的独立控制的导布轮装置6的辅助作用下到达能量转换喷嘴8、摆布器4和储布槽5中。从图8和图9可以看出,导布轮装置6包括导布轮61、导布轮电机62、机械密封63和导布轮轴64。高压鼓风机产生的高速气流从高压进气口21注入喷嘴雾化系统中的能量转换喷嘴8,同时通过管路84和染液注入口85向喷嘴雾化系统中注入染液,染液由循环泵16提供强大动力、经染液切割喷嘴96将染液切割成毫米级液滴,毫米级液滴与高速气流在喷嘴雾化系统中空间相遇并混合、击碎、再经能量转换喷嘴8中相遇并混合形成雾状微细液滴喷向织物。大量的气流与织物之间有足够摩擦力推动促使织物进行运动,同时促使染料加速渗透到纤维内部,达到高效率、低耗能、低浴比、低污染的环保型染色目的。织物与染液的交换方式对染色的均匀性以及染色的时间均有较大影响。从染色理论上讲,织物与染液相对运动越强烈,交换的频率越高,对织物的匀染性越有利。在本发明中,织物与染液的交换主要是在喷嘴系统中完成的,染液通过循环泵产生足够大的动力,经过特殊设计的喷嘴切割形成较小的液滴,再借助于气流进一步击碎产生雾化喷射到织物表面上,染液除了自身循环频率以外,还以极细的水雾与抖动的织物快速接触,完成染液的吸附过程。本发明主要依靠气流牵引织物作循环运动,染液仅仅作为溶解的染料,通过在喷嘴中周而复始的与被染织物接触,完成上染过程。织物一方面受到喷嘴气流的牵引,另一方面在高速气流的带动下不停快速激烈振动、抖动、扩展,加速了染料在动力边界层与扩散边界层的运动,染液与织物接触时间很短,依靠这种快速变换动态平衡,有效提高了织物匀染性,缩短了织物的匀染时间,提高了生产效率。本发明因在织物与染液或者处理液的更换频率非常高,并且具有激烈的相互揉搓作用,所以更有利于功能湿加工如天丝,纤维的原纤处理,酶处理,碱减量处理,和织物的柔软处理等,显著提高织物的性能。织物在气流喷嘴中运行时,还有一个扩展的过程,气流可以使织物不断的改变绳状位置,减少织物经向与纬向永久性折痕的形成。织物进入喷嘴之前是绳状的,进入喷嘴与导布管以后,在气流场作用下,纬向得到扩展,有利于充分的与雾状染液接触,当织物离开喷嘴与导布辊以后,气流动力突然释放,织物速度减慢,又以新的松式的绳状有规律落入储布槽;在整个染色过程中,织物在储布槽中自始至终没有浸在染液中。因气流密度较小,即使在高速下也比较柔和,还容易使织物达到特殊风格及柔软整理功能。本发明将传统液流喷射染色机中带动织物运行的水以高速气流等代替,并同时完成染料对织物的上染过程。因此,本发明又称气流染色机。在整个染色过程中,水仅仅使作为染料的溶剂和织物的浸湿剂。因此所需的浴比非常低,浴比的降低意味着蒸汽消耗、水消耗,染料与助剂消耗及排污都显著降低。因此本发明符合生态环保经济染色四要素水、能源、助剂染料、时间的最少消耗。在本发明中,能量转换喷嘴8中的直管段81的管壁86为特氟龙材料,以及在织物与染液分离的储布槽5也大量使用了特氟龙材料,减少了织物摩擦,特别是在高速条件下的摩擦,为快速染色及保证织物的外观品质创造了条件。本发明还包括设置在喷嘴雾化系统中的织物出口22通路上的摆布器4,由设置在摆布槽上轴的驱动连杆41、驱动电机齿轮箱42和摆布电机43组成,使摆布槽在缸体内作横向的往复运动,使掉至储布槽内的织物均能获得预期排放摆放效果。本发明除了织物的本身循环外,还有两道循环系统,一是空气动力循环系统,二是染液循环系统。空气动力循环系统由储布槽5、多孔网板和空气过滤网、高压鼓风机3、阀门和喷嘴8以及气流管道51组成。多孔网板和空气过滤网设于储布槽5上方。高压鼓风机的一端出口与喷嘴雾化系统相通,另一端进口与该空气过滤网相通。高速气流是牵引织物循环的动力源,同时还兼有织物对染料加速均勾吸附的作用。储布槽上方的摆布器将织物有规律的折叠,落到储布槽,在摆布的过程中,便推动织物所有气体均能迅速经多孔网板的孔口通路排出迅速到空气过滤网进入气体有效循环状态。染液循环系统由集液槽13和染液过滤网、循环泵16、热交换器17、染液管路84、阀门组成。主缸体1内设有圆柱形特氟龙过滤层,染液过滤网和集液槽13设于该圆柱形特氟龙过滤层下方,集液槽13和循环泵16、热交换器17相连,热交换器17和染液喷嘴8相连。织物到了储布槽5后,由圆柱形特氟龙过滤层将染液与织物分离,使染液快速经由多根圆形特氟龙间隙流入染液槽13和染液过滤网,进入染液循环状态。储布槽能有效将织物与染液有效快速分离,为提供染料直接性创造有利条件,因为任何一物体要使其它媒介渗入其内部,该物需提供相对的对流环境及空间方可顺利实现,换言之,染液中的染料分子一旦被织物纤维吸收后,其携带染料进入织物纤维内部的液体分子必须随即分离,只有这样,其他带有染料的液体才能获得再次进入纤维内部的机会。除此之外,本发明还设有加料系统9,加料系统9包括加料泵91和加料桶92,它还设有流量计93、比列阀和液位控制装置、阀门。本发明还设有出布辊94和人可以站在上面的操作平台95。本发明有如下优点-1、高效气流染色在低浴比情况下,织物与染液的交换频率很高,只要适当控制上染速率最快温度段的升温速率,其余升温阶段可实现快速升温縮短升温时间。如果按织物与交换频率来计算,那么相对于速度较慢的液流喷射染色机来说气流染色可縮短染色总体时间,提高单缸产量。2、节能降耗实现低浴比染色,一直是液流喷射染色工艺和设备所追求的目标,但是液流喷射染色机牵引织物运行的是染液,太少了织物无法正常循环,因此浴比的降低是有限的或者行不通的。气雾染色取消了循环染液牵引而由气流牵引织物运行,从而使浴比大为降低,染色过程中使用的水少了,升温,保温所消耗蒸汽量也相对减少,传统染色机的浴比在l:8~1:10,气流缸浴比l:3~1:4.5.节7jC,节气是显而易见的。在这种低浴比的情况下,如果可用活性染料染色,提高活性染料的直接性,减少对盐的依存性,同时染料的固色率也会相应提高减少碱消耗,盐和碱的用量减少,排放物中COD含量大幅度降低减少污水处理的成本以及染料在使用中水解量有大幅度降低节约染料。3、环保8污染是当今印染行业所面临的最大问题,其生产过程排放废液,为达到真正的排放要求,必须花费很高的成本进行处理。为此必须减少污水的排放量与降低污水中COD含量,气雾染色工艺正是迎合这个要求,它是一种低污染工艺,可以有效节约助剂30%以上染料、10~15%用水、40%排污,蒸汽节约40%,对环保意义重大。本发明采用雾化气流染色的最大优势,是除适合液流染色所能加工的织物品种外,更适合高档织物布料如天丝、天丝混纺织物,针织棉、超细纤维等需低张力,产生特殊风格的各种机织物与针织物的加工。本发明在最大载布量450Kg(两管)的情况下,布速可以达到600m/min,浴比可达到l:3~1:4.5(棉织物及一些吸湿性大的纤维所织成织物偏大),本发明适合克重100-600克/米的机织物与针织物。经过多次实验,本发明在喷嘴压力(气流)0.12Kg(液流)3Kg4Kg,喷嘴直径eilOmm的时候能够取得最佳效果。现将本发明与传统的溢流喷射染色机的各项技术指标进行跟踪对比,并将对比结果绘制成下面三张图表,足以说明浴比减低带来明显优势。从图表中可以明显看出,加工同样的织物,本发明与传统溢流喷射染色机相比节省助剂(盐、碱)60%。耗水量节省50%以上,节省蒸汽46%52%,且染色时间縮短了14%16%。表1加工棉织物耗盐量比较表如果某公司每天生产12T棉布<table>tableseeoriginaldocumentpage9</column></row><table><table>tableseeoriginaldocumentpage10</column></row><table>表2浴比与盐浓度的关系表:<table>tableseeoriginaldocumentpage10</column></row><table>表3:两种染色机的效率能耗对比表<table>tableseeoriginaldocumentpage10</column></row><table>权利要求1、一种新型气雾染色机,其特征在于它包括主缸体、高压鼓风机和喷嘴雾化系统,所述高压鼓风机的一端出口与喷嘴雾化系统中的高压进气口相通;喷嘴雾化系统的两端即织物进口和织物出口,该织物进口和织物出口分别与主缸体相通;喷嘴雾化系统内设有染液切割喷嘴、能量转换喷嘴与提布辊。所述染液切割喷嘴为环状狭缝形,所述能量转换喷嘴的轴向截面由直管段、锥度段和渐扩段三段组成;所述高压鼓风机的另一端进口与设于主缸体内部的空气过滤网相通。2、如权利要求1所述的一种新型气雾染色机,其特征在于所述能量转换喷嘴的进口段为特氟龙材料制作。3、如权利要求1所述的一种新型气雾染色机,其特征在于所述喷嘴雾化系统织物出口下方设有摆布器,该摆布器的下方设有储布槽,储布槽另一端与喷嘴雾化系统中的织物进口相通,所述喷嘴雾化系统、摆布器和储布槽形成可供织物在内循环移动的循环回路。4、如权利要求1所述的一种新型气雾染色机,其特征在于所述储布槽上方设有多孔网板和空气过滤网。5、如权利要求1所述的一种新型气雾染色机,其特征在于所述主缸体内设有特氟龙过滤层,所述特氟龙过滤层下方设有染液过滤网和集液槽,所述集液槽与循环泵相连,所述循环泵通过热交换器和染液管路与染液雾化喷嘴相连。6、如权利要求1所述的一种新型气雾染色机,其特征在于它还设有加料系统,所述加料系统包括加料泵和加料桶,它还设有流量计,比列阀和液位控制装置、阀门。全文摘要本发明提供一种新型气雾染色机,它包括主缸体、高压鼓风机和喷嘴雾化系统,所述高压鼓风机的一端出口与喷嘴雾化系统中的高压进气口相通;喷嘴雾化系统的两端即织物进口和织物出口,该织物进口和织物出口分别与主缸体相通;喷嘴雾化系统内设有染液切割喷嘴、能量转换喷嘴与提布辊。所述染液切割喷嘴为环状狭缝形,所述能量转换喷嘴的轴向截面由直管段、锥度段和渐扩段三段组成;所述高压鼓风机的另一端进口与设于主缸体内部的空气过滤网相通。本发明特殊的喷嘴雾化系统能很好的对染液进行雾化,采用气雾流染色,取消了对织物的循环染液牵引而由气流牵引织物运行,从而使浴比大为降低,节约能源、减少污染,促进环保。文档编号D06B23/00GK101591845SQ200910096838公开日2009年12月2日申请日期2009年3月17日优先权日2009年3月17日发明者王旭东申请人:浙江卓信机械有限公司
一种新型气雾染色机制作方法
- 专利详情
- 全文pdf
- 权力要求
- 说明书
- 法律状态
查看更多专利详情
下载专利文献
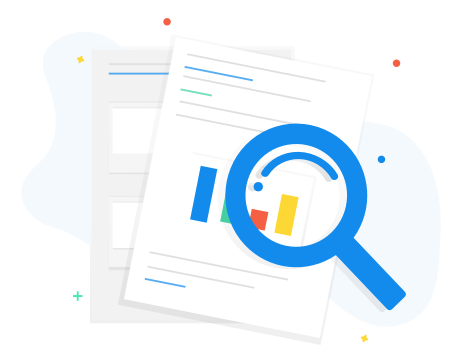
下载专利
同类推荐
-
吴大发吴大发吴大发
您可能感兴趣的专利
-
吴大发吴大发吴大发吴大发吴大发
专利相关信息
-
E·扎姆贝里E·扎姆贝里张军张军张军张军张军