专利名称:一种复合材料电力线杆及其制备方法传统复合材料电力杆塔的缺点:1、使用单向布和玻璃纤维采用螺旋(90度)缠绕和搭接工艺生产,无法保证纵向拉伸和压缩强度,纵向拉伸和压缩强度较低;2、产品厚度较大,因此成本较高;3、采用单一树脂生产,生产成本和产品品质不能同时保证;4、产品重量大,运输不方便。
有鉴于此,有必要提供一种结构强度较佳的复合材料电力线杆及其制备方法。本发明是这样实现的,一种复合材料电力线杆,定义平行于该复合材料电力线杆的轴线方向为轴向,而垂直于该复合材料电力线杆的轴线方向为纵向,该复合材料电力线杆由内而外包括以下结构:第一柱体结构,其采用树脂沿轴向方向环向缠绕;第二柱体结构,其采用树脂沿轴向方向倾斜缠绕,该缠绕方向与该轴向之间的锐角夹角不大于10度;第三柱体结构,其采用树脂沿轴向方向倾斜缠绕,该缠绕方向与该轴向之间的锐角夹角为45度;第四柱体结构,其采用树脂沿平行于轴向方向缠绕;第五柱体结构,其采用树脂缠绕,且缠绕方向同第三柱体结构的缠绕方向;第六柱体结构,其采用树脂缠绕,且缠绕方向同第二柱体结构的缠绕方向;第七柱体结构,其采用树脂缠绕,且缠绕方向同第一柱体结构的缠绕方向;第八柱体结构,其采用复合毡不带树脂且零搭接沿平行于轴向方向缠绕;第九柱体结构,其采用方格布零搭接沿平行于轴向方向缠绕;第十柱体结构,其采用短切毡零搭接沿平行于轴向方向缠绕;第十一柱体结构,其采用聚酯薄膜50%搭接沿平行于轴向方向缠绕。作为上述方案的进一步改进,该第一柱体结构、该第六柱体结构以及该第七柱体结构的厚度均为0.7~0.8mm。作为上述方案的进一步改进,该第二柱体结构的厚度为1.5~1.6mm。作为上述方案的进一步改进,该第三柱体结构、该第五柱体结构的厚度均为0.8mmο作为上述方案的进一步改进,该第四柱体结构的厚度为2.3~2.5mm。作为上述方案的进一步改进,该第一柱体结构至该第七柱体结构的总厚度为7.2 .4mm。作为上述方案的进一步改进,该复合材料电力线杆的总厚度为扩9.3mm。本发明还提供一种上述复合材料电力线杆的制备方法,其特征在于:其包括以下步骤:一、导丝头平行于模具轴向,进行90度环向缠绕,厚度为0.7 0.8mm形成该第一柱体结构;二、导丝头与模具轴向成10度或小于10度夹角进行缠绕,厚度为1.5^1.6mm形成该第二柱体结构;三、导丝头与模具轴向成45度夹角缠绕,厚度为0.8mm形成该第三柱体结构;四、导丝头与模具轴向成90度夹角进行O度缠绕,厚度为2.3^2.5mm形成该第四柱体结构;五、导丝头与模具轴向成45度缠绕,厚度为0.8mm形成该第五柱体结构;六、导丝头与模具轴向成10度或小于10度缠绕,厚度为0.7-0.8mm形成该第六柱体结构;七、导丝头平行于模具轴向,90度缠绕,厚度为0.7-0.8mm形成该第七柱体结构;八、缠绕上一层复合毡不带树脂,并等待凝胶即半成品上的树脂不再流动为止;凝胶后,将模具上纱梳与模具之间用刀具切开,将纱梳清理干净,并将模具两端的半成品切割平整;九、准备表面层树脂,将乙烯基树脂、抗紫外线剂、阻燃剂、色浆按照100:2:15:0.5的比例搅拌均匀;按照混合树脂中乙烯基数量的量加入f 2.5%的固化剂,搅拌均匀;将切割成的短切毡和复合毡以及方格布准备好,进行以下作业;十、在半成品上淋 上树脂,用胶辊辊涂均匀,使用复合毡进行缠绕并淋上树脂零搭接,其厚度为0.5mm,形成该第八柱体结构;十一、使用方格布进行缠绕并淋上树脂零搭接,其厚度为0.6mm,形成该第九柱体结构;十二、采用短切毡进行缠绕并淋上树脂零搭接,其厚度为0.5mm,形成该第十柱体结构;十三、使用聚酯薄膜将半成品完全覆盖50%搭接,形成该第十一柱体结构,待其完全固化后进行脱模;十四、进行固化,固化炉温度设定为80-100摄氏度,固化45-60分钟形成该复合材料电力线杆。作为上述方案的进一步改进,该第一柱体结构至该第七柱体结构的总厚度为7.2^7.4mm ;该复合材料电力线杆的总厚度为扩9.3_。作为上述方案的进一步改进,在第八柱体结构至第十柱体结构的制作过程中,每层相交处尽量错开以保证整体强度,每层应完全浸胶并用压辊压实才能进行下一层作业。与现有技术相比,本发明的复合材料电力线杆具有加强的结构强度:1、大量采用玻璃纤维通过O角度以及各种角度缠绕生产,仅在树脂转换层采用少量的方格布和短切毡,因此能保证产品的纵向和各方向的强度,同时也能保证不同种类树脂的连接强度;2、产品厚度较低,生产成本较低;3、采用多种树脂复合生产,在报这个结构稳定的前提下,同时也保证了产品的表面电性能和稳定性能;4、产品重量较低,运输方便,产品表面强度大,耐候以及稳定性高。
图1为本发明较佳实施方式提供的复合材料电力线杆的局部示意图,其为了便于介绍对层次逐一由外而内剥开展示。
2.3^2.5mm。在制备时,导丝头与模具轴向成90度夹角进行O度缠绕,厚度为2.3^2.5mm形成该第四柱体结构4。第五柱体结构5,其采用树脂缠绕,且缠绕方向同第三柱体结构3的缠绕方向;该第五柱体结构5的厚度可为0.8mm。在制备时,导丝头与模具轴向成45度缠绕,厚度为0.8mm形成该第五柱体结构5。第六柱体结构6,其采用树脂缠绕,且缠绕方向同第二柱体结构2的缠绕方向;该第六柱体结构6的厚度可为0.7 0.8mmο在制备时,导丝头与模具轴向成10度或小于10度缠绕,厚度为0.7-0.8mm形成该第六柱体结构6。第七柱体结构7,其采用树脂缠绕,且缠绕方向同第一柱体结构I的缠绕方向;该第七柱体结构7的厚度可为0.7 0.8mm。在制备时,导丝头平行于模具轴向,90度缠绕,厚度为0.7-0.8mm形成该第七柱体结构7。第八柱体结构8,其 采用复合毡不带树脂且零搭接沿平行于轴向方向缠绕;其厚度可为0.5mm。第九柱体结构9,其采用方格布零搭接沿平行于轴向方向缠绕;其厚度可为
0.6mmο
第十柱体结构10,其采用短切毡零搭接沿平行于轴向方向缠绕;其厚度可为
0.5mmο第十一柱体结构11,其采用聚酯薄膜50%搭接沿平行于轴向方向缠绕。在制备时,在制备第八柱体结构8至第十一柱体结构11之前,需要缠绕上一层复合毡不带树月旨,并等待凝胶即半成品上的树脂不再流动为止;凝胶后,将模具上纱梳与模具之间用刀具切开,将纱梳清理干净,并将模具两端的半成品切割平整;准备表面层树脂,将乙烯基树脂、抗紫外线剂、阻燃剂、色浆按照100:2:15:0.5的比例搅拌均匀;按照混合树脂中乙烯基数量的量加入广2.5%的固化剂,搅拌均匀;将切割成的短切毡和复合毡以及方格布准备好,最后进行制备第八柱体结构8至第^ 柱体结构11的相关作业。而且,在第八柱体结构8至第十柱体结构10的制作过程中,每层相交处尽量错开以保证整体强度,每层应完全浸胶并用压辊压实才能进行下一层作业。在制备第八柱体结构8时,在半成品上淋上树脂,用胶辊辊涂均匀,使用复合毡进行缠绕并淋上树脂零搭接,其厚度为0.5mm,形成该第八柱体结构8。在制备第九柱体结构9时,使用方格布进行缠绕并淋上树脂零搭接,其厚度为
0.6mm,形成该第九柱体结构9。在制备第十柱体结构10时,采用短切毡进行缠绕并淋上树脂零搭接,其厚度为
0.5mm,形成该第十柱体结构10。在制备第十一柱体结构11时,使用聚酯薄膜将半成品完全覆盖50%搭接,形成该第十一柱体结构11,待其 完全固化后进行脱模。然后进行固化,固化炉温度设定为80-100摄氏度,固化45-60分钟形成该复合材料电力线杆。其中,该第一柱体结构至该第七柱体结构的总厚度可为7.2^7.4mm,该复合材料电力线杆的总厚度可为9 9.3_。接下去对该复合材料电力线杆制备过程做更详细的举例说明。一.材料准备需要使用的材料为以下各项:1.FL-819型间苯型不饱和聚酯树脂、FL-822邻苯型不饱和聚酯树脂、FL-856柔性间苯型不饱和聚酯树脂或与上述树脂性能相同或相近的不饱和聚酯树脂。2.FC-854标准通用性乙烯基树脂、FC-892化学阻燃性乙烯基树脂或与上述树脂具有相同或相近性能的乙烯基树脂。3.以上1、2项可以使用双组份聚氨酯树脂替代,聚氨酯树脂具有优良的防腐、阻燃、高强度以及优良的电气性能。4.色浆(乙烯基树脂基型),根据不同颜色需求5.阻燃剂三氧化二铝微粉(100目)或三氧化二锑微粉100目6.抗紫外线剂UV-320或相近性能产品,可适用于乙烯基树脂;7.石英细沙(25-50目),减少树脂用量,增加产品强度和硬度;8.无碱玻璃纤维缠绕纱(2400Tex),国产巨石玻纤或重庆玻纤;9.玻璃纤维复合毡750型,无碱型; 10.04无碱玻璃纤维方格布400# (400克/平方米)11.短切毡300# (300克/平方米),无碱型;12.固化剂KP100或性能相类似的MEKP类过氧化物;
13.促进剂异辛酸钴(不能与固化剂一起堆放,两者存储距离不少于20米);14.聚酯薄膜(用于产品生产完成后封膜固化以及玻璃钢模具生产前的表面处理)15.为保证脱模,需要12#蜡脱模剂以及少量水性脱模剂,适用于模具处理,方便产品脱模;二.设备1.专用型变锥度复合材料缠绕机,导丝头上置;2.产品修整机;3.脱模机;4.固化炉;5.旋转机(用于手糊部分);6.吊车(5 吨);7.模具(根据不同型号产品采用钢制或玻璃钢制备);在模具两端安装低于模具两端15mm的钢制纱梳,纱梳与模具之间有15-20cm的间距;8.打磨机、切割机、铝制压辊、钢制压辊、滚刷等小型工具。三.产品生产工艺和流程1.模具准备钢制模具需要在表面涂上12#蜡脱模剂并涂抹均匀,玻璃钢模具则需要缠绕一层聚酯薄膜(10%搭接)。2.材料准备A.玻璃纤维缠绕纱放置于纱架并完成穿纱和导丝头的穿纱等工作,清理浸胶槽并将玻璃纤维纱布置好;B.将不饱和树脂、阻燃剂、石英细沙按照100:5:15的比例搅拌均匀备用(需不停搅拌);C.在搅拌好的不饱和树脂混合液中,以不饱和树脂的量为基准加入1-2. 5%的固化剂(不同温度情况下需要调整固化剂用量,一般以30-45分钟凝胶为标准);D.挂纱在I旲具大端(或小端)的纱梳上准备生广;一般以大端开始以大端结束;3.生产流程A.纱片宽度为44根纱(200mm宽),两层。纱片平行于模具轴向;B.启动缠绕机并输入相应参数(模具长度、模具大端直径、模具小端直径、纱片宽度、需要缠绕层数);C.开始自动缠绕;4.需要完成的相应缠绕数量(按缠绕次序)A.导丝头平行于模具轴向,进行90度环向缠绕I层(2层纱),厚度为O. 7—O. 8mmB.导丝头与模具轴向成10度或小于10度夹角进行缠绕2层(4层纱),厚度为1.5-1. 6mmC.导丝头与模具轴向成45度夹角缠绕I层(2层纱),厚度为O. 8mmD.导丝头与模具轴向成90度夹角进行O度缠绕3层(6层纱),厚度为2. 3-2. 5mmE.导丝头与模具轴向成45度缠绕I层(2层纱),厚度为0.8mmF.导丝头与模具轴向成10度或小于10度缠绕I层(2层纱)厚度为O. 7-0. 8mm
G.导丝头平行于模具轴向,90度缠绕I层(2层纱),厚度为O. 7-0. 8mm缠绕完成后总厚度为7. 2-7. 4mm。在缠绕机上世纪生产时间约为40_50分钟;5.将缠绕完成的产品吊运至旋转机上继续旋转,并立即缠绕上一层复合毡(不带树脂)并等待凝胶(产品上的树脂不再流动)为止;6.产品上的树脂不再流动(凝胶后),将模具上纱梳与模具之间用刀具切开,将纱梳清理干净,并将模具两端的产品切割平整。7.准备第二次作业,将进行表面层作业,生产工艺如下A.准备表面层树脂,将乙烯基树脂、抗紫外线剂、阻燃剂、色浆按照100:2:15:0. 5的比例搅拌均匀;B.按照混合树脂中乙烯基数量的量加入1-2. 5%的固化剂,搅拌均匀;C.进行手糊作业,将切割成300mm宽度的短切毡和复合毡以及方格布准备好,进行以下作业;8.表面层手糊作业流程A.首先在产品上淋上树脂,用胶辊辊涂均匀;B.使用复合毡进行缠绕并淋上树脂(O搭接);0. 5mmC.使用方格布进行缠绕并淋上树脂(O搭接);0. 6mmD.采用短切毡进行缠绕并淋上树脂(O搭接);0. 5_E.每层相交处尽量错开以保证整体强度,每层应完全浸胶并用压辊压实才能进行下一层作业;F.使用聚酯薄膜将产品完全覆盖(50%搭接),待其完全固化后进行脱模,聚酯薄膜可不撕去,到现场安装使用前应完全撕去;在旋转机上生产时间,分批进行约为30— 45分钟。生产过程同时进行约为20分钟。G.将产品放入固化炉中进行固化,固化炉温度设定为80-100摄氏度,固化45-60分钟。H.固化完成后将产品吊出,防止脱模机上脱模,脱模后的产品运出车间在堆放场地上堆放以备运输。1.广品完成后总厚度为9-9. 3mm。四.重点注意事项1.导丝头是可以按照角度旋转的,每次旋转应注意导丝头的旋转角度;导丝头的旋转受缠绕程序控制,导丝头可旋转以及可按不同角度定位是设备专利的一部分;2.由于不饱和聚酯树脂和乙烯基树脂均含有苯乙烯溶剂,在生产时将释放一定量的苯乙烯气体挥发,因此在车间内是完全禁止明火以及电焊、切割等动火作业;苯乙烯对人体无毒害,车间保持良好的通风,并且苯乙烯密度比空气重,比较容易在地面沉积。3.凝胶后未固化的产品比较容易处理,因此在缠绕机缠绕完成后,对于模具两端的处理要及时,等到产品固化后模具两端和纱梳之间的废弃物极难处理,将影响模具的流转和产品的生产。4.树脂使用应根据需要量配置,未加入固化剂的树脂如果不使用应密封保存,即使混合树脂也可以保存并使用,保存过的树脂使用前应搅拌均匀后方能使用;5.已经加入固化剂的树脂应在凝胶时间内使用完毕;不能使用的树脂(已加入固化剂)应倒入废树脂桶中并在表面放水,以防止树脂因积聚产生大量热量导致自燃,引起火灾。6.每天生产前应进行凝胶试验并记录,以保证产品生产的周期和时间,并可依据长时间的数据积累制定不同温度、湿度情况下的树脂和固化剂的用量表格。7.促进剂的使用是在比较极端的情况下(低温)促进树脂的固化,在一般情况下使用量不大或可以不使用,也可以要求树脂供应方提供预促进的树脂使用。但预促进的树脂的保存期较短。8.产品可以直接在现场打孔安装扶梯等附属装备,但建议尽量采用怀抱式扶梯为佳,在实际情况下为保证复合材料电力线杆的强度,尽量不要破坏复合材料的完整性。9.外层(表面层)可以根据需要定制颜色、夜光等,也可以根据需要喷涂防水防火的涂料和油漆,推荐以喷涂IOOum的氟碳漆为佳,具有更佳的耐候性和耐水耐腐和更好的电性能。如果需要喷涂油漆,需要采用表面修整机将产品表面进行磨砂磨平后进行喷漆处理。10.由于产品两端直径不同,在进行O度玻璃纤维纱缠绕时小端会有多层堆积,因此小端的复合材料产品的厚度会大于大端的厚度l_2mm。11.生产中如果发生断纱状况,可以在过程中直接穿纱或接纱,不需要停止生产。12.在产品生产中为了减少树脂的使用,需要将多余的树脂从产品上用胶板刮下,刮下的树脂可以直接重复使用,以降低生产成本,但凝胶结块后的树脂不能再使用。五.产品指标数据
本发明公开了一种复合材料电力线杆及其制备方法,复合材料电力线杆由内而外包括第一至十一柱体结构。第一柱体结构沿轴向方向环向缠绕;第二柱体结构沿轴向方向倾斜缠绕且倾斜度不大于10度;第三柱体结构沿轴向方向倾斜缠绕且倾斜度为45度;第四柱体结构沿平行于轴向方向缠绕;第五、六、七柱体结构的缠绕方式分别与第三、二、一柱体结构的缠绕方式相同。第八柱体结构采用复合毡不带树脂且零搭接沿平行于轴向方向缠绕;第九柱体结构采用方格布零搭接沿平行于轴向方向缠绕;第十柱体结构采用短切毡零搭接沿平行于轴向方向缠绕;第十一柱体结构采用聚酯薄膜50%搭接沿平行于轴向方向缠绕。本发明还涉及该复合材料电力线杆的制备方法。
一种复合材料电力线杆及其制备方法
- 专利详情
- 全文pdf
- 权力要求
- 说明书
- 法律状态
查看更多专利详情
下载专利文献
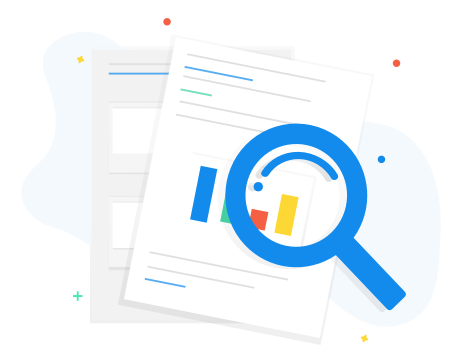
下载专利
同类推荐
-
李光海李光海李贺军刘友举D·J·默克莱伊
您可能感兴趣的专利
-
C·汉松廖寄乔袁远, 杨群伊凡·W·翁, 杰拉尔德·W·瓦尔克何唯平, 杰 张
专利相关信息
-
何唯平, 杰 张杨洪