光纤预制件的制造方法、光纤预制件和光纤的制作方法 [0002] 日本特开2004-307280描述了一种光纤用玻璃预制件的制造方法,其中,制作具 有芯部和包层的一部分的芯棒,在芯棒的外周上沉积成为包层的余部(追加包层)的玻璃 微粒从而制作多孔预制件,并将其透明玻璃化。在该方法中,规定了至少在追加包层的内径 的150%以内的部分中平均0H含有浓度为50ppm以下。追加包层的平均0H含有浓度取决 于追加包层的脱水条件,但是降低平均0H浓度的要求变得越严格,用于脱水处理的处理时 间会增加从而导致成本上升。
[0003] [发明要解决的问题] [0004] 本发明的目的是提供一种可将传输损耗维持在允许范围内、同时能够削减制造成 本的光纤预制件制造方法、光纤预制件和光纤。 [0005] [解决问题的手段]
[0006] 为了达到目的,提供了一种光纤预制件的制造方法,其具有以下步骤:形成芯棒的 步骤,其中所述芯棒由芯部和包围芯部的第一包层部构成,并且第一包层部的外径D相对 于芯部的外径d的比值D/d满足4.8 = D/d = 6.0的关系;使成为第二包层部的玻璃微 粒沉积在芯棒的外周上,从而形成玻璃微粒沉积体的步骤;以及,脱水烧结玻璃微粒沉积体 从而形成光纤预制件的步骤,其中,第二包层部中从第一包层部与第二包层部的界面直到 第一包层部的外径的120%的范围(指定范围)中,平均0H浓度为lOOppm〈平均0H浓度 刍 500ppm。
[0007] 在本发明的光纤预制件的制造方法中,可以是比值D/d满足4.8 = D/d〈5.0的关 系、并且指定范围中平均0H浓度为lOOppm〈平均0H浓度=200ppm,也可以是比值D/d满足 5. 0兰D/d〈5. 2的关系、并且指定范围中平均0H浓度为200ppm〈平均0H浓度兰500ppm。
[0008] 在本发明的光纤预制件的制造方法中,脱水烧结为真空脱水烧结,并且可以为以 下构成:根据目标平均0H浓度来设定在1000?1300°C下加热的时间,从而调节平均0H浓 度,也可以为以下构成:在1000?1300°C下的加热持续0.5小时以上5小时以下。此外, 在本发明的光纤预制件的制造方法中,脱水烧结为常压脱水烧结,并且可以根据目标平均 0H浓度来设定在1000?1300°C下加热的时间,从而调节平均0H浓度,也可以根据目标平 均0H浓度来设定脱水材料的浓度,从而调节平均0H浓度。
[0009] 作为发明的其他实施方式,提供了一种光纤预制件,其由芯棒和第二包层部构成, 所述芯棒由芯部和芯部外周的第一包层部构成,并且第一包层部的外径D相对于芯部的外 径d的比值D/d满足4.8 = D/d = 6.0的关系,第二包层部是通过对沉积在芯棒外周上的 玻璃微粒进行烧结而形成的,其中,第二包层部中从第一包层部与第二包层部的界面直到 第一包层部的外径的120%的范围中,平均OH浓度为lOOppm〈平均OH浓度=500ppm。
[0010] 作为发明的又一个实施方式,提供了一种光纤,其是通过对本发明的光纤预制件 进行拉丝而形成的。
[0011][发明效果]
[0012] 根据本发明,通过调节芯部的外径与第一包层部的外径的比值,并使直到第一包 层部的外径的120%的范围中第二包层部的平均0H浓度的允许值缓和到不影响传输损耗 的程度,从而能够减少用于制作光纤预制件的处理时间,并能够节约光纤预制件的制造成 本。
[0013] 附图简要说明
[0014] 图1是示出了本发明所述光纤的一种形式的截面图。
[0015] 图2是示出了本发明所述光纤的芯部和第一包层部的外径比与传输损耗在允许 范围内的第二包层部的指定范围内的平均0H浓度之间的关系的曲线图。
[0016] 图3是示出了本发明所述光纤的第二包层部的脱水处理时间与第二包层部的指 定范围内的平均0H浓度之间的关系的曲线图。
[0017] 以下,参照附图对本发明所述光纤的实施方式的例子进行说明。图1是将作为本 发明实施方式的光纤1从垂直于光轴的面切断时的截面图。光纤1在中心处具有芯部2,其 外周具有包层5。包层5具有位于芯部2的外周上的第一包层部3、以及位于第一包层部3 的外周上的第二包层部4。
[0018] 芯部2由比包层5的折射率高的物质形成,例如包层5为纯石英时,芯部2为含锗 的石英玻璃。芯部2为纯石英时,包层5由比纯石英的折射率低的物质形成。
[0019] 在包层5中,第一包层部3是靠近芯部2的区域,是对光纤1的光传输特性影响大 的部分。因此,如果第一包层部3中含有一定量以上的0H基等杂质,贝U光纤1的传输损耗 增加,光纤1的光传输特性劣化。因此,必须将第一包层部3的0H浓度抑制到尽可能低的 值。
[0020] 另一方面,在包层5中,第二包层部4是隔着第一包层部与芯部2分隔开的区域, 是对光纤1的光传输特性不会带来那么大影响的部分。因此,与第一包层部3的0H浓度相 t匕,第二包层部4的0H浓度可以为高值。
[0021] 在光纤1中,例如,波长1380nm下基于0H基的传输损耗增加 Λ α 1. 38要求为 0. 020dB/km以下。这是考虑安全性而设定的值,以使得不超出传输损耗α 1. 38的实质允许 值即0. 34dB/km以下。
[0022] 为了在满足上述要求值的同时,削减光纤1的制造成本,本发明人发现:通过调整 芯部2的外径d与第一包层部3的外径D的比值D/d,并且使从第一包层部3和第二包层部 4的界面直到第一包层部3的外径D的120%的范围(以下称为"指定范围")中第二包层 部4的平均0H浓度的允许值缓和到不影响光纤1的传输损耗的程度,可以削减制造光纤时 的处理时间。具体而言,光纤1是这样制造的:在满足4. 8 = D/d = 6. 0的情况下,使指定 范围中平均OH浓度大于lOOppm并且在500ppm以下。这里,规定指定范围内的平均OH浓 度的原因是第二包层部4的0H浓度在该范围内最大,对传输损耗的影响明确已知。
[0023] 关于芯部2与第一包层部3的外径比D/d,规定为4. 8兰D/d兰6. 0。这是因为: D/d小于4. 8的情况下,由于第二包层部4接近芯部2,因此当满足Λ α 1. 38兰0. 020dB/km 时第二包层部4的处理时间和处理成本会大幅增加。此外,D/d大于6. 0的情况下,由于制 造成本比第二包层部4高的第一包层部3所占比例相对变大,因此制造成本变高,不适于实 用化。
[0024] 这里,关于光纤1,在满足4. 8 = D/d〈5. 0的情况下,优选的是,从第一包层部3和 第二包层部4的界面直到第一包层部3的外径D的指定范围中,平均0H浓度为大于lOOppm 并且在200ppm以下。或者,关于光纤1,在满足5. 0 f D/d〈5. 2的情况下,优选的是,从第一 包层部3和第二包层部4的界面直到第一包层部3的外径D的指定范围中,平均0H浓度为 大于200ppm并且在500ppm以下。
[0025] 接下来,对制造光纤1的方法进行说明。需要说明的是,虽然下面以使用了石英玻 璃(其含有锗等提高折射率的物质)的光纤1的制造方法为例进行说明,但并不限于该例 子。芯部2也可以为使用了纯二氧化硅的构造。
[0026] 首先,准备含有光纤1的芯部2和第一包层部3的芯棒。制作芯棒时,在通过(例 如)VAD法添加 Ge的同时制作二氧化硅的玻璃微粒沉积体,在氯气氛中脱水并烧结该玻璃 微粒沉积体并使之透明化,之后拉伸至所需的外径。需要说明的是,也可以通过使芯部2和 石英管塌缩来制造芯棒,对芯棒的制造方法没有特别限定。
[0027] 接下来,在该芯棒的外周上形成成为光纤1的第二包层部4的玻璃。例如,通过 0VD法使纯二氧化硅的玻璃微粒沉积在芯棒的外周上,并使沉积体沿径向生长。真空脱水 烧结时,通过在真空状态的图中未示出的加热炉内加热该沉积体来进行脱水处理。此时,利 用了真空烧结的脱水处理中的温度为1000?1300°C,持续加热0. 5小时以上5小时以下。 详细情况在后面说明,脱水处理时间少于〇. 5小时时,第二包层部4的指定范围内的平均0H 浓度无法满足要求值,多于5小时时降低制造成本的效果变弱。需要说明的是,通过根据目 标平均0H浓度来设定在1000?1300°C下加热的时间,可以调节第二包层部4的指定范围 内的平均0H浓度。
[0028] 之后,将沉积体在氟气体(例如SiF4)气氛中加热并添加氟、同时烧结以透明化。 由此,形成了成为光纤1的第二包层部4的玻璃,从而得到具有成为光纤1的芯部2的部分、 成为第一包层部3的部分和成为第二包层部4的部分的光纤预制件。最后,通过用拉丝装 置对如此制作的光纤预制件进行拉丝,可以得到光纤1。
[0029] 如上所述,根据本实施方式,通过调节芯部2的外径d与第一包层部3的外径D的 比值D/d,并且使直到第一包层部3的外径D的120%的范围中第二包层部4的平均0H浓 度的允许值缓和到不影响光纤1的传输损耗的程度,可以显著地减少用于制作光纤预制件 和光纤1的处理时间,并可以大幅节约制造成本。
[0030] 实施例
[0031] 在Λ α 1. 38兰0. 020dB/km的情况下,研究光纤1的芯部2和第一包层部3的外 径比D/d与第二包层部4的指定范围内的平均0H浓度之间的关系。其结果在图2中示出。 可以看出,随着D/d变大,即使平均0H浓度的值变高也没有问题。
[0032] 接下来,研究真空脱水烧结第二包层部4时的脱水时间与平均0H浓度之间的关 系。其结果在图3中示出。可以看出,随着脱水时间变长,平均0H浓度降低。
[0033] 根据上述关系,准备第一包层部3的外径D相对于芯部2的外径d的比值D/d、从 第一包层部3与第二包层部4的界面直到第一包层部3的外径D的120 %的范围中的平均 0H浓度(ppm)、以及真空烧结时的脱水时间(小时)不同的多个样品,调查各样品在波长 1380nm下的光纤1的传输损耗(dB/km)。其结果在表1中不出。
[0034] 表 1
[0035]
光纤预制件的制造方法、光纤预制件和光纤制作方法
- 专利详情
- 全文pdf
- 权力要求
- 说明书
- 法律状态
查看更多专利详情
下载专利文献
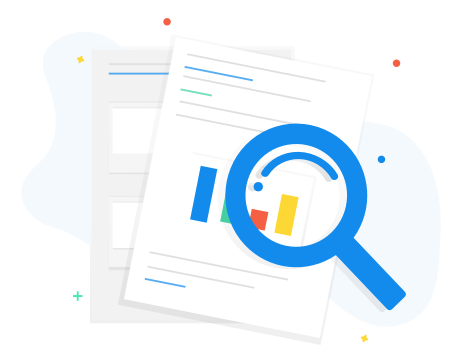
下载专利
同类推荐
-
八木干太, 川崎希一郎平野正晃平野正晃罗文勇
您可能感兴趣的专利
-
王新, 王桂英李诗愈高桥文雄高桥文雄藤原康裕, 邹学禄J·H·阿伦斯
专利相关信息
-
J·H·阿伦斯孙义兴孙义兴吴成国, 金成珍吴成国, 金成珍蒂莫·皮沃斯基, 贝恩德·威尔维斯