专利名称:一种微孔高铬砖及其制备方法高铬砖具有高温条件下强度大,优良的抗酸性煤渣侵蚀性和渗透性,是水煤浆 加压气化炉关键的内衬材料。近十年来随着化肥工业的发展和各种新技术和新工艺的 出现,水煤浆气化炉的使用条件愈加恶劣,如工作温度高达1500°C,炉内气体的压力可达 6. 5MPa,还原性气体强,熔渣的熔点低、粘度小和酸性强;同时随着单投煤量的增加和排渣 量的增大,高速气流的冲刷,以及炉内气压和温度的急剧波动,对高铬砖提出了极为苛刻的 要求。现有高铬砖的制造方法一般是以电熔或烧结氧化铬为骨料,以氧化铬细粉、氧化 铝微粉、氧化铬绿细粉和单斜氧化锆微粉为基质,加入糊精和磷酸盐为结合剂,经配料、混 碾、困料和机压成型,然后于高温窑中经1650°C烧制而成。这种高铬砖在生产过程中不仅 烧成温度高,而且其微孔化率很低,抗煤渣渗透性差。原因是高铬砖在氧化气氛中烧制时, 氧化铬会氧化成高价气态氧化物,蒸发_凝聚传质使颗粒间的颈部被填充,阻止了体积收 缩,很难烧结致密化,且微孔化率低[梁永和,李楠等.低温合成高铬烧结料[J]耐火材 料,2001,35 (4) :199 201]。高铬砖在强还原气氛如埋碳气氛下烧成时,在较低温度下 就可以完全烧结致密化,但是砖内晶粒异常发育长大,材料的抗热震稳定性大大降低(徐 延庆,孙加林等.气氛条件下氧化铬材料的烧结性能研究[J]武汉科技大学学报,2010, 33(2) :170 174)。还原气氛下反应工艺复杂且很难控制,如埋碳气氛下一旦焦炭与高 铬砖直接接触,就会在其表面留下反应层,对制品的性能产生严重影响(梁永和,孙承绪 等.Cr2O3-ZrO2材料的烧结及抗热震性研究.耐火材料,2001,35 (5) 258 260)。
本发明旨在克服现有技术缺陷,目的在于提供一种微孔化率高、抗煤渣渗透性能 好,能延长使用寿命的微孔高铬砖及其制备方法。为了实现上述目的,本发明采用的技术方案是微孔高铬砖的组分及其质量百 分含量为电熔氧化铬颗粒为40 70wt%、电熔氧化铬细粉为10 20wt%、SiC颗粒为 0. 3 5wt%、SiC细粉为0. 3 5wt%、单斜氧化锆微粉为3 15wt%、氧化铝微粉为2 15wt%和氧化铬绿细粉为4 12wt%,外加上述原料0. 5 3衬%的糊精和2 7wt%的磷 酸二氢铝作为结合剂。按所述微孔高铬砖的组分先将其中的电熔氧化铬细粉、SiC细粉、单斜氧化锆微 粉、氧化铝微粉和氧化铬绿细粉按各自的质量百分含量进行混合,预制成混合粉料;再将其 中的电熔氧化铬颗粒和SiC颗粒按各自的质量百分含量干混3 5分钟,然后按糊精和磷 酸二氢铝的外加量将其加入到电熔氧化铬颗粒和SiC颗粒的干混料中,湿混5 7分钟,制 成混合颗粒料;最后将预制成的混合粉料加入到混合颗粒料中,混碾15 30分钟,困料,压制成生坯,干燥,最后在空气中于1350°C 1650°C条件下烧成。其中SiC颗粒的粒径分布为粒度为3 Imm的占0. 1 2wt%,粒度为1 0. 5mm 的占0. 1 2wt%,粒度为0. 5 0. 088mm的占0. 1 lwt%;SiC细粉的粒径分布为粒度 为 < 0. 088mm 的占 0. 1 2wt %,粒度为 < 0. 045mm 的占 0. 1 2wt %,粒度为 < 0. 025mm 的占0. 1 Iwt % ;电熔氧化铬颗粒的粒径分布为粒度为4 2mm的占10 15wt%,粒度 为2 Imm的占15 25wt%,粒度为1 0. 5mm的占5 10wt%,粒度为0. 5 0. 088mm 的占10 20wt% ;电熔氧化铬细粉的粒径分布为粒度为< 0. 088mm的占5 10wt%,S 度为< 0. 045mm的占5 IOwt% ;单斜氧化锆微粉的粒度为< 0. Olmm ;氧化铝微粉的粒度 为< 0. 005mm ;氧化铬绿细粉的粒度为< 0. 045mm。由于采用上述 技术方案,本发明所制备的微孔高铬砖在烧制过程中当温度达到 1200°C时,SiC开始缓慢氧化形成SiO和CO气体,降低了材料内部氧分压,制造了弱还原性 气氛,促进了高铬砖的烧结。同时CO气体在材料内部还原出部分低价氧化物和非计量化合 物,堵塞气孔,提高材料的微孔化率,减少了煤渣通过气孔向微孔高铬砖内部渗透。本发明工艺简单,所制备的微孔高铬砖微孔化率高,其中< Iym的孔容积率大于 30%,抗煤渣渗透性好,延长了高铬砖的使用寿命。对本发明作进一步的描述,并非对保护范围的限制为避免重复,先将本中所涉及到原料的技术参数统一描述如下,实 施例中不再赘述SiC颗粒的粒径分布为粒度为3 Imm的占0. 1 2wt%,粒度为1 0. 5mm的占0. 1 2wt %,粒度为0. 5 0. 088mm的占0. 1 Iwt % ;SiC细粉的粒径分布 为粒度为< 0. 088mm的占0. 1 2wt%,粒度为< 0. 045mm的占0. 1 2wt%,粒度为 < 0. 025mm的占0. 1 Iwt % ;电熔氧化铬颗粒的粒径分布为粒度为4 2mm的占10 15wt%,粒度为2 Imm的占15 25wt%,粒度为1 0. 5mm的占5 IOwt %,粒度为 0. 5 0. 088mm的占10 20wt% ;电熔氧化铬细粉的粒径分布为粒度为< 0. 088mm的占 5 IOwt%,粒度为< 0. 045mm的占5 IOwt%;单斜氧化锆微粉的粒度为< 0. Olmm ;氧化 铝微粉的粒度为< 0. 005mm ;氧化铬绿细粉的粒度为< 0. 045mm。实施例1一种微孔高铬砖及其制备方法,该微孔高铬砖的组分及其质量百分含量为电熔 氧化铬颗粒为40 45wt %、电熔氧化铬细粉为15 20wt %、SiC颗粒为4 5wt %,SiC细 粉为4 5wt%、单斜氧化锆微粉为10 15wt%、氧化铝微粉为5 8衬%和氧化铬绿细粉 为8 12wt%,外加上述混合料1 2衬%的糊精和5 7wt%的磷酸二氢铝作为结合剂。按所述微孔高铬砖的组分先将其中的电熔氧化铬细粉、SiC细粉、单斜氧化锆微 粉、氧化铝微粉和氧化铬绿细粉按各自的质量百分含量进行混合,预制成混合粉料;再将其 中的电熔氧化铬颗粒和SiC颗粒按各自的质量百分含量干混3 5分钟,然后按糊精和磷 酸二氢铝的外加量将其加入到电熔氧化铬颗粒和SiC颗粒的干混料中,湿混5 7分钟,制 成混合颗粒料;最后将预制成的混合粉料加入到混合颗粒料中,混碾15 30分钟,困料,压 制成生坯,干燥,最后在空气中于1350°C 140(TC条件下烧成。本实施例所制备的微孔高铬砖经检测,< Ium的孔容积率为30 38%。实施例2一种微孔高铬砖及其制备方法,该微孔高铬砖的组分及其质量百分含量为电熔 氧化铬颗粒为45 50wt %、电熔氧化铬细粉为10 15wt %、SiC颗粒为2 4wt %,SiC 细粉为2 4wt%、单斜氧化锆微粉为8 10wt%、氧化铝微粉为12 15wt%和氧化铬绿 细粉为4 8wt%,外加上述混合料0. 5 1衬%的糊精和3 5wt%的磷酸二氢铝作为结 合剂。制备工艺除最后在空气中于1400 1450°C条件下烧成外,其余同实施例1。本实施例 所制备的微孔高铬砖经检测,< Ium的孔容积率为31 35%。实施例3一种微孔高铬砖及其制备方法,该微孔高铬砖的组分及其质量百分含量为电熔 氧化铬颗粒为50 55wt %、电熔氧化铬细粉为15 20wt %、SiC颗粒为1 2wt %,SiC细 粉为1 2wt%、单斜氧化锆微粉为5 8wt%、氧化铝微粉为8 12衬%和氧化铬绿细粉 为7 ,外加上述混合料1 3衬%的糊精和2 3wt%的磷酸二氢铝作为结合剂。制备工艺除最后在空气中于1450 1500°C条件下烧成外,其余同实施例1。本实施例所制备的微孔高铬砖经检测,< Ium的孔容积率为35 32%。实施例4一种微孔高铬砖及其制备方法,该微孔高铬砖的组分及其质量百分含量为电熔 氧化铬颗粒为55 60wt%、电熔氧化铬细粉为10 15wt%、SiC颗粒为0. 3 Iwt %,SiC 细粉为4 5wt%、单斜氧化锆微粉为7 1 Iwt %、氧化铝微粉为4 8wt%和氧化铬绿细 粉为5 IOwt%,外加上述混合料1. 5 2. 5wt%的糊精和2 5wt%的磷酸二氢铝作为结 合剂。制备工艺除最后在空气中于1500 1550°C条件下烧成外,其余同实施例1。本实施例所制备的微孔高铬砖经检测,< Ium的孔容积率为33 39%。实施例5一种微孔高铬砖及其制备方法,该微孔高铬砖的组分及其质量百分含量为电熔 氧化铬颗粒为60 65wt %、电熔氧化铬细粉为15 20wt %、SiC颗粒为2 4wt %,SiC 细粉为0. 3 Iwt %、单斜氧化锆微粉为4 6wt%、氧化铝微粉为2 6wt%和氧化铬绿 细粉为4 6wt%,外加上述混合料2 3衬%的糊精和4 7衬%的磷酸二氢铝作为结合 剂。制备工艺除最后在空气中于1550 1600°C条件下烧成外,其余同实施例1。本实施例所制备的微孔高铬砖经检测,< Ium的孔容积率为37 43%。实施例6一种微孔高铬砖及其制备方法,该微孔高铬砖的组分及其质量百分含量为电熔 氧化铬颗粒为65 70wt%、电熔氧化铬细粉为10 15wt%、SiC颗粒为0. 3 lwt%,SiC 细粉为0. 3 、单斜氧化锆微粉为3 5wt%、氧化铝微粉为6 12wt%和氧化铬绿 细粉为4 6wt%,外加上述混合料0. 5 1. 5衬%的糊精和2 5wt%的磷酸二氢铝作为 结合剂。制备工艺除最后在空气中于1600 1650°C条件下烧成外,其余同实施例1。本实施例所制备的微孔高铬砖经检测,< Ium的孔容积率为35 39%。本
所制备的微孔高铬砖在烧制过程中当温度达到1200°C时,SiC开 始缓慢氧化形成SiO和CO气体,降低了材料内部氧分压,制造了弱还原性气氛,促进了高铬 砖的烧结。同时CO气体在材料内部还原出部分低价氧化物和非计量化合物,堵塞气孔,提 高材料的微孔化率,减少了煤渣通过气孔向微孔高铬砖内部渗透。 本
工艺简单,所制备的微孔高铬砖微孔化率高,其中< Iym的孔容 积率大于30 %,抗煤渣渗透性好,延长了高铬砖的使用寿命。
本发明涉及一种微孔高铬砖及其制备方法。其方案是电熔氧化铬颗粒为40~70wt%、电熔氧化铬细粉为10~20wt%、SiC颗粒为0.3~5wt%、SiC细粉为0.3~5wt%、单斜氧化锆微粉为3~15wt%、氧化铝微粉为2~15wt%和氧化铬绿细粉为4~12wt%,外加上述混合料0.5~3wt%的糊精和2~7wt%的磷酸二氢铝作为结合剂。按上述组分先将电熔氧化铬颗粒和SiC颗粒干混3~5分钟,加入磷酸二氢铝湿混5~7分钟,再加入电熔氧化铬细粉、SiC细粉、单斜氧化锆微粉、氧化铝微粉、氧化铬绿细粉和糊精的预制混合粉料,混碾15~30分钟,困料,压制成生坯,干燥,在空气中于1350~1650℃烧成。本发明工艺简单,制备的微孔高铬砖微孔化率高,抗煤渣渗透性好,延长了高铬砖使用寿命。
一种微孔高铬砖及其制备方法
- 专利详情
- 全文pdf
- 权力要求
- 说明书
- 法律状态
查看更多专利详情
下载专利文献
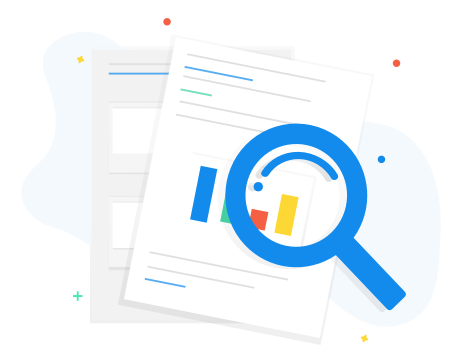
下载专利
同类推荐
-
黄谦章G·B·帕尔默G·B·帕尔默李亚伟
您可能感兴趣的专利
-
于津, 邓存兴张建武张建武张建武
专利相关信息