专利名称:光学玻璃镜片的模造成形装置及模造成形方法由于玻璃镜片的透光性极佳而一直都作为光学产品的重要基材,而对于非球面镜玻璃镜片的制造方法,大体可分为研磨方式及模造方式两种,其中模造方式非常适合小尺寸非球面镜的制作。现有的非球面光学玻璃镜片的模造方法,基本上是以一模具或套筒配合成对的上、下模仁以形成模穴,并利用玻璃材料的高温软化特性,在此模穴中借由上模仁或下模仁的加压,将玻璃材料压造成形,使其变形并接近预期中模造成品的表面面形与厚度,随后在玻璃材料冷却收缩且黏滞度升高的过程中再给予模造镜片适当的二次加压成形,上、下模仁的表面面形将因此转写于玻璃材料上,并最终获得所需表面面形的光学玻璃镜片。在现有套筒与模仁搭配的玻璃模造成形装置中,控制镜片厚度的方式主要有利用精密伺服马达控制模造成形中的加压板的下压或上压距离来达成,或以气压缸径行加压由模仁长度搭配筒形模具高度所形成的模具组,利用模具组控制模造镜片的厚度。上述现有技术的实例,有如日本专利特公平7-57697号、特开平7-2535号、特开平11-217227号、特公平6-24992号、特开2002-29763号及特许2909657号等专利公报所揭示的内容。其中,由日本专利特公平7-57697号公开的现有光学玻璃镜片的模造成形装置的基本构造如图1所示,它是利用上模仁91及下模仁92并配合单一套筒模具93来进行光学玻璃镜片94的玻璃模造制程,其中套筒模具93是用来控制模造玻璃镜片的中心厚度,而玻璃镜片的面形精度则借助上、下模仁、套筒模具及玻璃材料的热收缩效应来控制。在选择套筒模具93的制作材料时,若要确保在高温环境下能够耐高温氧化并保持该模具与模仁间的配合精度,则套筒模具的材料的热膨胀系数通常必须与模仁材料相近而无法太高;而若要该套筒模具有足够的冷却收缩量来确保面形转写的精度,则其套筒模具的材料的热膨胀系数又必须要远大于玻璃材料的热膨胀系数,但这种高热膨胀系数材料的高温特性又往往不令人满意。因此,虽然该模造成形装置的构造简易,但由于其模具材料的选用困难而难以推广使用。日本专利特开平7-2535号公开了另一种现有模造成形装置,其基本构造及玻璃镜片的成形过程如图2A至图2C所示,它是利用上模仁81及下模仁82并配合内部套筒模具83及外部套筒模具85,进行光学玻璃镜片的玻璃模造制程。其中,内部套筒模具83与上、下模仁的材质相类似以确保在高温环境下能够耐高温氧化并保持该模具与模仁间的配合精度,而外部套筒模具85的热膨胀系数较大。如图2A所示,上模仁81、下模仁82、内部套筒模具83、外部套筒模具85及导入模穴中的玻璃材料84均处于模造制程的初始状态,其中外部套筒模具85的下端面与下加热成形板86接触。如图2B所示,上加热压板87对软化后的玻璃材料84进行初次加压,而使得该玻璃材料发生初步变形。然后进行适当冷却,之后继续让上加热压板87向下移动,直至外部套筒模具85的上端面与上加热压板完全接触,如图2C所示,以借此控制模造玻璃镜片的中心厚度。而在随后的冷却过程中,再次利用外部套筒模具的较大的热收缩量来夹持内部套筒模具及模仁,以确保玻璃镜片面形转写的精度。但是,由于外部套筒模具85的热膨胀系数较内部套筒模具83的热膨胀系数大,而在冷却过程中,外部套筒模具85的收缩速度亦明显大于内部套筒模具83,这样虽能给玻璃材料84的模造成形带来益处,即可确保玻璃镜片面形转写的精度,但同时也带来了诸多不便。例如在每次的冷却完成后,必须将模具打开以将成品取出并且放入新的玻璃塑材。但由于模具与其套筒间的精密配合及因温度上升所产生的热膨胀干涉量等因素,上或下模仁81或82无法自由的取出,而必须先使用特定的夹具夹住外部套筒模具85,再将上或下模仁81或82连同内部套筒模具83取出;接下来再一次以夹具夹住内部套筒模具83,再将上或下模仁81或82取出,以取出模穴内的玻璃镜片成品;而且在进行下一循环的制程时,也要按照与前述模具组拆解的过程相反的步骤来组合模具组。因此,这种现有的光学玻璃镜片模造成形的方法及其装置的整体模具拆解与组立过程是很复杂及不便的。又如日本专利特许第2909657号所公开的另外一种现有模造成形装置,其基本构造及玻璃镜片的成形过程如图3A至图3D所示,它是利用上模仁71、下模仁72并配合内部套筒模具73及具有较大热膨胀系数的外部套筒模具75,进行光学玻璃镜片的玻璃模造制程。如图3A所示,上模仁71、下模仁72、内部套筒模具73、外部套筒模具75及导入模穴中的玻璃材料74均处于模造制程的初始状态,其中下模仁72的外径凸出部底面可与下加热板(未图示)接触,而内、外部套筒模具的下端面皆与下模仁的外径凸出部的上平面接触,上模仁71的外径凸出部的顶面与上加热压板(未图示)接触。如图3B所示,当制程温度提升至玻璃软化点时,因热膨胀效应的作用,外部套筒模具75的高度将较内部套筒模具73的高度大出许多,此时进行加压成形,直至上模仁71的外径凸出部的底面与外部套筒模具75的上端面相接触,从而获得初步变形状况的玻璃镜片74如图3C所示。在进行适当冷却之后,因外部套筒模具75的收缩量与收缩速度远大于内部套筒模具73、上、下模仁71、72及玻璃镜片74,因此可促使上加热压板再次向下加压,直至内部套筒模具73的上端面与上模仁71的外径凸出部的底面相接触,通过这种方式控制模造玻璃镜片的中心厚度,并确保玻璃镜片面形转写的精度,如图3D所示。同样,由于该种模造成形装置的内、外部套筒模具73、75的配合结构及其与上、下模仁71、72的配合关系均与前述日本专利特开平7-2535号公开的现有模造成形装置相类似,而其弊病也都相同,即也存在有模具拆解与组立机构比较复杂的问题。
需注意的是,在上述现有模造成形装置的使用过程中,随着模仁面的返修或补正加工,模仁的高度将因研磨造成的材料损耗而缩短,最后导致模造镜片的成品厚度增加或超出规格。常见的作法是,对筒形模具进行研磨以调整其高度,借此补偿模仁的高度损失,确保模造镜片成品的厚度。但是,此维修方法复杂且不能及时调整好模具高度,而有改进的必要。
因此,有必要提供一种新的光学玻璃镜片的模造成形装置及模造成形方法,以克服现有技术所存在的所有问题。
本发明的另一目的在于提供一种光学玻璃镜片的模造成形装置,其不但可获得具高精密度的光学玻璃镜片,而且该装置的维修方法简单。
为实现上述发明目的,本发明采用如下技术方案光学玻璃镜片的模造成形装置具备有可借助外力作开启与闭合的运动的主模具及由异质合金材料制成并利用其高度来控制模造镜片的厚度的套筒模具组。其中,主模具包括第一模仁及第二模仁,在第一、第二模仁之间形成模穴以收容模造镜片;套筒模具组是组立于主模具的外围,其包括第一筒形模具及与第一筒形模具的一部分外形结构相配合的第二筒形模具,且该第一、第二筒形模具材料的热膨胀系数不同并均具有阶梯状的构形,其中主模具的第一模仁是与第一筒形模具配合,而主模具的第二模仁则同时与第一筒形模具及第二筒形模具配合,且该套筒模具组的总热膨胀量大于主模具与模造镜片成品的热膨胀量总和。
利用上述模造成形装置进行光学玻璃镜片的模造,其模造过程包括如下步骤首先是将套筒模具组组立于主模具的外围,并将待模造的玻璃材料导入主模具的模穴内;然后提升制程温度至玻璃材料软化点,其中套筒模具组的热膨胀速度会大于主模具与玻璃材料的热膨胀速度;接着对玻璃材料进行第一次模造成形,即主模具将借助外力对玻璃材料进行加压,直至套筒模具组的端面与主模具贴合,从而获得具初步变形状况的玻璃镜片;接着,因套筒模具组的收缩量与收缩速度远大于主模具与玻璃镜片的收缩量与收缩速度,因此可以继续对主模具施加压力,并在温度下降、玻璃黏滞度逐步提升的状况下仍持续提供玻璃材料变形的动力,以稳定、精确地控制光学玻璃模造镜片的中心厚度及主模具的模仁与镜片表面面形转写的过程,并且使模具能在适当的时机进行二次加压的工作,从而获得所需的光学玻璃镜片成品。
在上述模造成形装置中,第一、第二筒形模具之间还配置有一构件,以利用该构件的厚度调节该套筒模具组的总长,其中第一筒形模具具有单一内径及二个呈阶梯状的不同外径,第一筒形模具的内径可同时与第一、第二模仁做精密配合,而第二筒形模具具有单一外径及二个呈阶梯状的不同内径,第二筒形模具的内径可与第二模仁做一般配合,而其较大内径是与第一筒形模具的较小外径相互配合。借此配合关系,可确保在模造成形的冷却过程中,第二筒形模具的内径可以因其高热膨胀量而对第一筒形模具施加适当的压力,而使模仁能对玻璃镜片施加适当的压力;同时,在泠却完成欲取出玻璃镜片成品时,只要用夹具夹住第二筒形模具的外围,再借助第二筒形模具与第一筒形模具之间的阶梯状内、外径干涉作用,即可直接将模仁与第一筒形模具分离,而取出位于模穴中的光学镜片成品;同时相对的,在进行下个制程循环时,其模具的组合步骤也较现有的模具装配方法简便。
相较于现有技术,本发明的光学玻璃镜片的模造成形装置是借由异质合金材料制成的两个具有阶梯状构形的筒形模具组合成单一套筒模具组与玻璃模造用的模仁配合来完成玻璃的模造成形,其拆卸方便具有较好的拆卸便利性,并可借助该套筒模具组与主模具的精确配合及对相互间的热膨胀量的差异控制,从而使得光学玻璃镜片具有较高的精密度。此外,该模造成形装置的维修方法简单,从而提升生产的效率。
图1是现有光学玻璃镜片的模造成形装置的基本构造。
图2A是另一现有光学玻璃镜片的模造成形装置及其模造制程的初始状态的示意图。
图2B是由图2A显示的光学玻璃镜片的模造制程继续进行后,玻璃材料发生了初步变形的示意图。
图2C是由图2B显示的光学玻璃镜片的模造制程的最后阶段并生产出成品的示意图。
图3A是另一现有的光学玻璃镜片的模造成形装置及其模造制程的初始状态的示意图。
图3B是提升制程温度后,由图3A显示的模造成形装置构形变化后的示意图。
图3C是由图3B显示的光学玻璃镜片的模造制程继续进行后,玻璃材料发生了初步变形的示意图。
图3D是图3C显示的光学玻璃镜片的模造制程的冷却阶段完成后,生产出成品的示意图。
图4A是本发明光学玻璃镜片的模造成形装置及光学玻璃镜片的模造成形过程的初始状态的示意图。
图4B是在本发明光学玻璃镜片的模造成形过程中,玻璃材料发生了初步变形的示意图。
图4C是在本发明光学玻璃镜片的模造成形的冷却阶段完成后,生产出成品的示意图。
图5是本发明的光学玻璃镜片与其模造成形装置的尺寸表示示意图。
图6是本发明模造成形装置的另一实施例。
上筒形模具13是呈阶梯状,其具有单一内径及二个呈阶梯状的不同外径,其内径可同时与上、下模仁11、12做精密配合,制作时需要在该上筒形模具13的内缘部以放电加工的方式沿轴向加工数个逃气沟130并使其平均分布在圆周方向,以供模穴内残留气体逸散。这些逃气沟130的长度以可横跨由上、下模仁面所构成的模穴间隙并可通达上、下筒形模具的逃气间隙131为原则,同时其长、宽及深度同样以能达逸气功能为原则。
下筒形模具15也是呈阶梯状,其具有单一外径及二个呈阶梯状的不同内径,其中一较小内径与下模仁12做一般配合,而另一较大内径则与上筒形模具13的其中一较小外径相配合。制作时需在下筒形模具15与逃气间隙131相邻的筒腹上加工数个逃气孔150并将其平均分布在圆周方向,以供模穴内残留气体逃逸,这些逃气孔150贯穿下筒形模具15并用以连通逃气间隙131与外部环境,其孔径大小与形状以能达到逃气功能为原则。
通过对上述结构的描述可以得知,本发明引入了上、下筒形模具对玻璃模造成形装置进行了突破性的改造。上、下筒形模具13、15均具有阶梯状的结构,且两者之间仅有一部分结构相互配合,其配合长度即可确保正常的组立安全性,同时上、下筒形模具13、15间的阶梯状结构又可确保在模具分离的过程中,可让下模仁12能一次性的从筒形模具中取出,并且在取出光学玻璃镜片成品之后,又能快速简便的将下模仁组装回筒形模具中。因此,本发明的模造装置的组立过程简单易行,且该突破性设计将有助于提升玻璃模造制程的稳定度并获得具高精密面形精度的模造镜片。详细制程如下文所述。
如图4A所示是本发明光学玻璃的模造成形的初始状态,其中异质材料套筒模具组13、15与模仁11、12组立并置入玻璃镜片素材14。当制程温度提升至该玻璃材料软化点时,因热膨胀效应的作用,套筒模具组13、15的高度将较模仁与玻璃材料的热膨胀量大,于此时加压成形,即对玻璃材料进行第一次模造成形,直至上模仁11的外径凸出部的底面贴合于套筒模具组的端面上,而获得具初步变形状况的玻璃镜片14,如图4B所示。在成形过程中,模穴内的残留或制程中的衍生气体,将沿着逃气沟130、逃气间隙131及逃气孔150逸散至外部环境中。如图4C所示,在冷却过程中,套筒模具组13、15的收缩量与收缩速度远大于模仁11、12与玻璃镜片14,更进一步讲,是具有阶梯状内径的下筒形模具15的收缩速度快,下筒形模具15将对上筒形模具13产生适当压力,而上筒形模具13将对上、下模仁11、12提供一适当夹持力,以确保该整个模具组在冷却一定时间后,仍继续对模仁施加压力,这样可在温度下降、玻璃黏滞度逐步提升的状况下仍持续提供玻璃材料变形的动力,并且可以使加压设备在适当的时机对玻璃材料进行第二次模造成形,从而使得在玻璃模造制程的末段过程中,完成光学玻璃模造镜片中心厚度稳定且精确的控制,同时达到模仁与镜片表面面形转写的目的。
如图5所示,本发明光学玻璃的模造成形装置,其模造镜片的中心厚度与表面面形的转写精度,除与整个模具组的压缩行程有关外,还取决于上、下模仁11、12与模具组13、15配合的导正部长度(a和c)的热膨胀与收缩量、模造镜片成品的厚度(b)的热膨胀与收缩量、套筒模具组高度(d和e)的热膨胀与收缩量,这些构件的热膨胀与收缩量分别用Δa、Δb、Δc、Δd及Δe表示,且其配置原则为Δa+Δb+Δc<Δd+Δe。
在该光学玻璃的模造成形装置中,借由异质合金材料组合而成的套筒模具组,除形成使玻璃材料在高温成形所需的模穴外,更充分利用热胀冷缩的原理,借由异质模具材料的热膨胀与收缩差异达到可精密控制镜片厚度与表面面形的目的。即本发明采用组合式的上、下筒形模具,可控制镜片的中心厚度以使其具有高度重现性及精确度,同时达成高精密度的面形转写特性。
此外,本发明光学玻璃的模造成形装置还可设置高度控制套环16,该构件16可组立于套筒模具组13、15中,如图6所示,它是组装于上、下筒形模具13、15之间。当模仁高度因磨损而缩短时,仅需以一厚度较低的高度控制套环来取代原来的高度控制套环即可,通过这种方式补偿模仁高度的损失,从而确保模造镜片成品的厚度。该高度控制套环16的材质可以与下筒形模具15的材质相同且可重复使用。
可以理解的是,该高度控制套环16(图中其高度表示为f)当然并不是一定要组装于上、下筒形模具13、15之间,其还可被组装于套筒模具组的上方或下方并提供控制模具组高度的作用。但是,具有高度控制套环16的模造成形装置除了要能保障形成使玻璃材料在高温成形所需的模穴外,还必须遵照热膨胀与收缩量的配置原则Δa+Δb+Δc<Δd+Δe+Δf。
同时,由于上、下筒形模具13、15之间的阶梯状外形的干涉作用,所以在模具组泠却至适当温度时而欲取出镜片成品时,可以用夹具夹住下筒形模具15的外围,再直接将下模仁12由筒形模具中取出,而不会使上筒形模具13一并被取出;而在进行下一制程循环时,该取出的下模仁12也可以很便利的被组装回模具组中。
本发明公开一种光学玻璃镜片的模造成形装置及模造成形方法,该模造成形装置的主模具包括上模仁及下模仁,在上、下模仁之间形成模穴以收容模造镜片,套筒模具组是由异质合金材料制成,其包括有两个具有阶梯状构形的筒形模具及一环状高度控制构件,该套筒模具组的总热膨胀量大于主模具与模造镜片成品的热膨胀量的总和。通过该套筒模具组与主模具的精确配合及对相互之间热膨胀量的差异控制,使该装置的组装、拆卸及维修方便并可稳定、精确地控制光学玻璃模造镜片的中心厚度及镜片表面面形转写特性,从而获得所需要的光学玻璃镜片成品。
光学玻璃镜片的模造成形装置及模造成形方法
- 专利详情
- 全文pdf
- 权力要求
- 说明书
- 法律状态
查看更多专利详情
下载专利文献
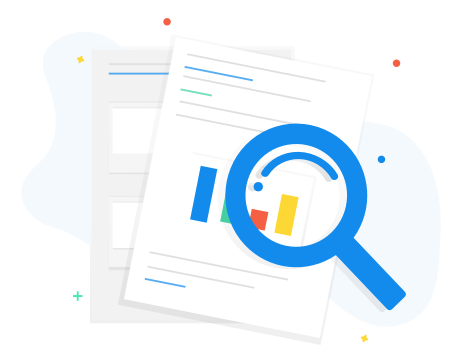
下载专利
同类推荐
-
王坤池, 高伯菘王坤池, 高伯菘吉田雅也徐红萍, 邓建清K-J·胡贝尔-哈格, I·比罗-弗朗斯K-J·胡贝尔-哈格, I·比罗-弗朗斯K-J·胡贝尔-哈格, I·比罗-弗朗斯
您可能感兴趣的专利
-
杉田守男陶武刚, 陈健杉田守男杉田守男杉田守男
专利相关信息
-
R.B.皮尤徐东泌徐东泌