专利名称:玻璃板的制造方法及玻璃板制造装置的制作方法以往,液晶显示器等平板显示器的显示部使用玻璃板。玻璃板是通过将熔融玻璃成型为片状的片材玻璃而制作得到的。片材玻璃是通过如下方式而成型的:在熔解槽中将所调配的原料熔解而得到熔融玻璃,使熔融玻璃通过用于去除气泡的澄清槽、用于使组成分布均匀的搅拌槽等而流入成型装置,从而成型为片材玻璃。通常,使熔解槽中所熔解的熔融玻璃流动的装置或配管使用由钼或钼合金制造的装置或配管。其原因在于:防止熔融玻璃因构成装置或配管的材料熔融而受到污染,且通过向装置或配管本身通电而调整在内部流动的熔融玻璃的温度。此处,例如在平板显示器用的玻璃板的制造工序中,熔融玻璃的温度约为1000°C 1700°C的高温,因此就用于输送熔融玻璃的配管或装置而言,需要考虑热膨胀。例如在专利文献1(日本专利第449830号公报)中,为了抑制作业时的钼或钼合金制配管的由热膨胀所导致的破损,在流动有熔融玻璃的配管的外壁及内壁上,在圆周部以螺旋状形成有在直径方向上凸出的凸出部。然而,如专利文献I (日本专利第4498390号公报)所公开的那样,输送熔融玻璃的配管大多情况下分割为2段以上。其原因在于:若不将配管分割为2段以上,则难以吸收由配管或装置提升至作业时的温度时产生的热膨胀所导致的伸长。即,原因在于:无法吸收由热膨胀所导致的伸长,因此配管或装置有可能变形或破损。因此,在专利文献I中,在使配管或装置升温至特定温度的状态下(高温状态下),利用焊接等来连接分割为2段以上的配管或装置,由此减少连 接后的配管或装置的由膨胀所导致的伸长量,抑制配管或装置的变形。另外,输送熔融玻璃的配管、装置及它们的周边部件需要在作业前升温至作业时的温度的附近。其原因在于:若配管或装置的温度不足够高,则有可能流动在配管或装置中的熔融玻璃的温度下降,使熔融玻璃在配管或装置中凝固而无法流动。另外,认为其原因在于:若使高温的熔融玻璃流入常温状态的配管或装置中,则在这些配管、装置或它们的周边部件中产生与温度差对应的热膨胀。即,认为在这种情况下,在输送熔融玻璃的配管、装置及它们的周边部件中产生热膨胀/热应变。并且,认为其原因在于:产生由该热膨胀/热应变所导致的变形或破损。
发明要解决的问题但是,在升温至特定温度的状态下(即在高温状态下)对2段以上的配管进行焊接等而形成作业时的状态,这对于作业人员而言是较为困难的作业。因此,有时存在无法高精度地进行焊接等而使熔融玻璃自焊接部位泄漏出来的问题。另外,与未焊接的区域的强度相比较,进行了焊接的区域的强度必然下降。另外,虽然预先使配管升温,但是若考虑到进行焊接等的作业人员的作业性等,则实际上难以升温至作业时的温度。因此,即便为了抑制由热膨胀所导致的变形或破损而预先将配管升温至特定温度,有时也会在连接该配管而形成作业时的状态后,进一步升温至作业时的温度。因此,担心仍会产生配管的热膨胀而产生配管的变形或破损。另外,近年来,伴随着平板显示器的大型化,其使用的玻璃板也倾向于大型化。随着所制造的玻璃板变大而使成型装置也大型化,因此为保持生产性而需要增加一天内流入成型装置中的熔融玻璃的量。需要说明的是,若使一天内流入成型装置中的熔融玻璃的量增加,则流动有熔融玻璃的配管或装置倾向于大型化。此处,若配管或装置大型化,则存在升温时的膨胀量增加而使配管的破损或变形显著的问题。另外,近年来,对于平板显示器等电子设备等所使用的玻璃板内的由气泡所导致的缺陷的要求变得严格,需要使用澄清剂来减少玻璃板内的气泡数。进而,近年来由于环境负荷的问题,作为澄清剂,要求使用氧化锡或氧化铁等金属氧化物而并非可获得高澄清效果但毒性高的As203。此处,为了使氧化锡或氧化铁等作为澄清剂而发挥作用,与As2O3相比,需要进一步提升熔融玻璃的温度。更详细而言,氧化锡作为澄清剂而开始发挥作用的温度高于As203。即,在含有氧化锡等作为澄清剂的玻璃板的制造中,澄清槽或其周边的配管的温度也需要高于含有As2O3作为澄清剂的情况。因此,存在澄清槽或其周边的配管的膨胀量增加而使配管的破损或变形显著的问题。如上所述,近年来,由钼或钼合金制造的配管或装置的膨胀量倾向于增加,因此利用上述专利文献I所记载的方法难以充分抑制上述配管的破损或变形。因此,本发明的课题在于提供一种玻璃板的制造方法及玻璃板制造装置,其中,可通过更简便的作业来抑制流动有熔融玻璃的配管的变形或破损。用于解决问题的手段本发明的玻璃板的制造方法具备熔解工序、输送工序、供给工序、成型工序、及切割工序。在熔解工序中,将玻璃原料熔解而形成熔融玻璃。在输送工序中,使熔融玻璃流入由钼族元素或钼族元素合金制造的配管内而进行输送。在供给工序中,将熔融玻璃供给至成型装置。在成型工序中,将供给工序中所供给的熔融玻璃成型为片材玻璃。在切割工序中,对片材玻璃进行切割而形成玻璃板。在输送工序中用于输送熔融玻璃的配管具有:第I管及第2管、和覆盖部件。第I管及第2管是相隔而配置的,在其间形成有容许作业时的热膨胀的热膨胀容许空间。覆盖部件用于覆盖第I管及第2管的端部及热膨胀容许空间,且相对于第I管及第2管而能够在轴方向自由移动。输送工序包括粘度提升工序。在粘度提升工序中,在自第I管经由热膨胀容许空间向第2管输送熔融玻璃时,使自所述熔融玻璃向所述覆盖部件的外部的热转移量大于自所述熔融玻璃向所述第I管及所述第2管的外部转移的热的热转移量,由此提升所述熔融玻璃的粘度。此处,例如覆盖部件并不限于覆盖第I管及第2管的全周。此处,可通过简便的作业而使流动有熔融玻璃的配管为作业时的状态。 另外,优选的是,在粘度提升工序中,提升第I管的第2管侧的端部与覆盖部件之间的熔融玻璃的一部分的粘度,提升第2管的第I管侧的端部与覆盖部件之间的熔融玻璃的一部分的粘度。另外,优选的是,在粘度提升工序中,使第I管的第2管侧的端部与覆盖部件之间的熔融玻璃的粘度Π为log η =4 13,使第2管的第I管侧的端部与覆盖部件之间的熔融玻璃的粘度Η为log η =4 13。另外,输送工序中的覆盖部件优选具有覆盖部、及至少I个凸缘部。覆盖部用于覆盖第I管、第2管及热膨胀容许空间。凸缘部自覆盖部向外侧延伸。另外,优选的是,覆盖部形成有至少I个开口部,凸缘部自形成有开口部的开口部形成部向外侧延伸,且通过凸缘部形成有凸缘部间空间,在粘度提升工序中,凸缘部间空间中的熔融玻璃的粘度为log η =6以上。另外,玻璃板优选为在熔解工序中熔解的玻璃原料中实质上不含As2O3的液晶显不器用玻璃板。关于所述玻璃板的制造中所使用的所述熔融玻璃的粘度η,优选成为log η=2.5时的温度为1500°C 1750°C。所述玻璃板的制造中所使用的玻璃的应变点优选为655°C以上。所述玻璃原料优选含有氧化锡作为澄清剂。优选的是,所述玻璃板含有SiO2和Al2O3,且所述玻璃板的所述SiO2与所述Al2O3的总含有率为70质量%以上,所述玻璃板的碱金属氧化物的含有率为2质量%以下。所述玻璃板优选为实质上不含有碱金属氧化物的无碱玻璃。 所述玻璃板优选含有50质量% 70质量%的Si02、0质量% 15质量%的B203、5质量% 25质量%的A1203、0质量% 10质量%的Mg0、0质量% 20质量%的Ca0、0质量% 20质量%的SrO、O质量% 10质量%的BaO、5质量% 20质量%的RO (其中,R是选自Mg、Ca、Sr及Ba中的至少I种的所述玻璃板所含有的成分)。另外,在供给工序中,优选每天对所述成型装置供给6t以上的所述熔融玻璃。本发明的玻璃板制造装置具备熔解槽、成型装置及配管。熔解槽中,将玻璃原料熔解而形成熔融玻璃。成型装置中,将熔融玻璃成型为片材玻璃。配管配置在熔解槽与成型装置之间,在其内部流动有熔融玻璃,其由钼族元素或钼族元素合金制造。配管具有相隔而设置的第I管及第2管、及相对于第I管及第2管而能够在轴方向自由移动的覆盖部件。在第I管与第2管之间形成有容许作业时的热膨胀的热膨胀容许空间。覆盖部件覆盖第I管及第2管的端部及热膨胀容许空间,且相对于第I管及第2管而能够在轴方向自由移动。进一步,配管中,在自第I管经由热膨胀容许空间向第2管输送熔融玻璃时,使自熔融玻璃向覆盖部件的外部的热转移量大于自熔融玻璃向第I管及第2管的外部转移的热转移量,由此提升熔融玻璃的粘度。需要说明的是,配管例如只要配置在熔解槽与成型装置之间即可,也可不与熔解槽及成型装置直接连接。此处,可利用简便的作业使流动有熔融玻璃的配管为作业时的状态。发明效果在本发明中,可利用更简便的作业来抑制流动有熔融玻璃的配管的变形或破损。
图1是用于说明本实施方式的玻璃板的制造方法的流程图。图2是玻璃板制造装置的模式图。图3是第I配管的示意性分解立体图。图4是覆盖部件及按压部件的示意性立体图。图5是表示第I部件及第2部件正常安装在第I管及第2管上的状态、即第I配管的图。图6是通过第I空间在第I方向的垂直方向上对图5所示的第I配管进行切割时的剖面图。图7是变形例IA的第I配管的示意性立体图。图8是变形例IC的第I配管的示意性立体图。
熔解槽101是用于熔解玻璃原料的槽。熔解槽101由砖等耐火物所构成,且在下部具有液槽。例如,利用配置在壁面上的燃烧器而适当地对熔解槽101进行加热。并且,通过使用燃烧器加热壁面而产生辐射热,利用该辐射热加热玻璃原料而使其熔解。在液槽中,设置有电加热装置,其用于通过对玻璃原料进行通电而使玻璃原料自身产生焦耳热。在液槽的壁面上,按照与玻璃原料接触的方式设置有电加热装置的电极。在熔解槽101中,进行熔解工序STl。需要说明的是,在上述中,举出了具有燃烧器和电极的单元作为示例对玻璃原料的加热单元进行说明,但并不限于此,只要具有任一者即可。另外,玻璃原料的熔解方法并不特别限定于此,也可使用其他加热单元来熔解玻璃原料。
澄清槽102是用于从熔解槽101所熔解的熔融玻璃中去除气泡的槽。通过在澄清槽102中进一步对自熔解槽101送入的熔融玻璃进行加热,从而促进熔融玻璃中的气泡的脱泡。在澄清槽102中,进行澄清工序ST2。更详细而言,澄清槽102中的熔融玻璃的温度升温至澄清剂释放气体成分(例如,若为氧化锡则为氧)的温度以上、即上述气体成分在熔融玻璃中的原有的气泡中扩散而使原有的气泡的泡径扩大的温度。另外,熔融玻璃的温度升温至实现熔融玻璃中的气泡具有充分的浮起速度的粘度(200泊 800泊)的温度以上。由此,使熔融玻璃中的气泡自熔融玻璃内释放至外部。其后,使熔融玻璃降温,残存在熔融玻璃中的气泡被吸收至澄清剂。由此,可使熔融玻璃中的气泡消失而进行澄清。需要说明的是,气泡的消失也可在澄清槽102、第I配管105及搅拌槽103中进行。搅拌槽103具有搅拌装置,该搅拌装置包括收容熔融玻璃的容器、旋转轴、安装在该旋转轴上的搅拌桨。作为容器、旋转轴及搅拌桨,例如可使用由钼等钼族元素或钼族元素的合金制造的部件,但并不限定于此。通过利用发动机等驱动部(未图示)的驱动使旋转轴旋转,从而使安装在旋转轴上的搅拌桨搅拌熔融玻璃。在搅拌槽103中,进行均质化工序ST3。需要说明的是,此处,将在熔解槽101中投入玻璃原料然后进行熔解工序ST1、澄清工序ST2、及均质化工序ST3的过程(即,熔融玻璃流入熔解槽101、澄清槽102、第I配管105、搅拌槽103、及第2配管106的内部的过程)称为输送工序。成型装置104具备在上部形成有沟槽且纵向的剖面呈楔形形状的成型体。沟槽是沿着成型体的长度方向而形成的。成型体为耐火物。另外,成型装置104还具备:使自成型体溢出并在成型体的下端合流的熔融玻璃向下方延伸的辊、使玻璃缓缓冷却的冷却装置等。在成型装置104中,进行成型工序ST5。需要说明的是,在供给工序ST4中,每天将6t以上的熔融玻璃供给至成型装置104。第I配管105、及第2配管106是由钼族元素(钼、铱、锇、鈀、铑、钌等)或钼族元素合金制造的配管。第I配管105是连接澄清槽102与搅拌槽103的配管。第2配管106是连接搅拌槽103与成型装置104的配管。需要说明的是,对于由钼族元素或钼族元素合金构成的澄清槽102、第I配管105、搅拌槽103、第2配管106而言,优选通过直接对该钼族元素或钼族元素合金通电来对其进行加热。通过直接对钼族元素或钼族元素合金通电而进行加热,可高效地使熔融玻璃升温。因此,即便在使用氧化锡作为澄清剂的情况下,也可容易地将熔融玻璃升温至氧化锡作为澄清剂而有效地发挥作用的温度(例如1620°C以上)。需要说明的是,澄清槽102、第I配管105、搅拌槽103、第2配管106的加热方法并不限定于上述方法,例如,也可在澄清槽102、第I配管105、搅拌槽103、第2配管106的周围设置电热器等加热装置,利用该加热装置来进行加热。(3)第I配管105的详细构成图3是第I配管105的示意性分解立体图。如图3所示,第I配管105具有第I管111、第2管112、及覆盖部件113。第I管111是由钼族元素或钼族元素合金制造的中空管,其与澄清槽102连接。第I管111自澄清槽102向熔融玻璃流入搅拌槽103中的第I方向突出。第2管112是由钼族元素或钼族元素合金制造的中空管,其与搅拌槽103连接。第2管112自搅拌槽103向与第I方向相反的方向、即第2方向突出。第I管111及第2管112例如使用直径为IOmm 1000mm(优选为70mm 200mm)的管。需要说明的是,第I管111及第2管112的直径并不限定于此。在第I管111与第2管112之间存在第I空间SI (相当于热膨胀容许空间)。即,第I管111与第2管112是相隔而设置。此处,在本实施方式中,基于熔融玻璃的散热量(基于玻璃的温度的下降量、流量、比热、及散热条件而进行计算)来决定相隔状态下的第I管111及第2管112的互不相对侧的端面(即,第I管111的第2方向侧的端面与第2管112的第I方向侧的端面)间的长度。在第I管111及第2管112的互不相对侧的端部(即,第I管111的第2方向侧的端部、及第2管112的第I方 向侧的端部),配置有2层以上的隔热材料。覆盖部件113覆盖第I管111的第2管112侧的端部及第2管112的第I管111侧的端部(即,第I管111的第I方向侧的端部与第2管112的第2方向侧的端部)、以及第I空间SI。即,覆盖部件113具有连接相隔状态下的第I管111与第2管112的作用。由此,可使在第I管111的内部流动的熔融玻璃流入第2管112的内部。另外,覆盖部件113相对于第I管111及第2管112而能够在其轴方向(第I方向及第2方向)自由移动。覆盖部件113具有第I部件113a、及第2部件113b。第I部件113a由钼族元素或钼族元素合金制造,其覆盖第I管111及第2管112的上部。另外,第I部件113a自上方覆盖第I空间SI。第I部件113a具有覆盖部213a、及凸缘部213b、213c。覆盖部213a是覆盖第I管111、第2管112、及第I空间SI的部分。覆盖部213a为了能够覆盖第I管111及第2管112而使垂直于其长度方向的面进行切割而成的剖面形状呈现大致半圆的圆弧。凸缘部213b、213c自覆盖部213a的两端部分别向直径方向外侧(具体而言,与在第I方向上水平的水平面正交的方向)在水平方向上延伸。需要说明的是,此处,凸缘部213b、213c自覆盖部213a在水平方向上延伸,但并不限于在水平方向上延伸。凸缘部213b、213c的各自的宽度Wl(参照图4)例如优选为20mm以下(但是,为除O以外的自然数)。需要说明的是,凸缘部213b、213c的宽度Wl优选为20mm以下的原因在于:首先该凸缘部213b、213c具有作为冷却片的作用。S卩,若凸缘部213b、213c的宽度Wl过大(例如,若大于下述第I按压部件114a的第I下表面414的宽度),则会不必要地降低第I管111及第2管112的温度,进而降低在第I管111及第2管112的内部流动的熔融玻璃的温度,因此为了避免该状况而使上述宽度Wl优选为20mm以下。接着,覆盖部件113是由与其他金属相比相对昂贵的钼族元素或钼族元素合金制造得到的,因此为了实现成本的降低而使上述宽度Wl优选为20mm以下。第2部件113b由钼族元素或钼族元素合金制造,其覆盖第I管111及第2管112的下部。另外,第2部件113b自下方覆盖第I空间SI。在本实施方式中,第2部件113b具有以第I部件113a的纵向为轴而对称的形状,并具有覆盖部214a及凸缘部214b、214c。需要说明的是,覆盖部214a及凸缘部214b、214c具有与第I部件113a的覆盖部213a及凸缘部213b、213c相同的构成,故省略说明。需要说明的是,第I部件113a及第2部件113b并不限定于以这些部件的纵向为轴而对称的形状。通过下述第I按压部件114a来支持第I部件113a。通过下述的第2按压部件114b并利用未图示的支持部件(例如千斤顶等)来支持第2部件113b。此处,在第I管111及第2管112、与第I部件113a及第2部件113b之间,在其圆周方向存在间隙S2、S3(参照图5)。S卩,第I部件113a及第2部件113b的内径分别大于第I管111及第2管112的外径。此处,由于存在间隙S2及间隙S3而使覆盖部件113容易在第I管111及第2管112的轴方向上移动。第I部件113a及第2部件113b的内径与第I管111及第2管112的外径的差优选为5mm以下(但是,为除O以外的自然数)。其原因在于,可抑制熔融玻璃泄漏至外部。在第I部件113a的凸缘部213b、213c与第2部件113b的凸缘部214b、214c之间,分别形成有凸缘部间空间S4(参照图5)。S卩,第I部件113a及第2部件113b是以如下方式配置的:在第I部件113a的两端部与第2部件113b的两端部之间,分别形成有可使在第I管111及第2管112中流动的熔融玻璃流入凸缘部间空间S4中的开口部313 (参照图5或图6,在图5中仅示出了纸面近前侧的开口部)。由此,覆盖 部213a、214a的两端部可作为形成开口部313的开口部形成部而发挥作用。凸缘部间空间S4的垂直方向的高度(具体而言,凸缘部213b、213c的下表面与凸缘部214b、214c的上表面的距离)优选为5mm以下(但是,为除O以外的自然数)。其原因在于,可抑制熔融玻璃泄漏至外部。第I部件113a及第2部件113b是通过按压部件114而被按压的。以下,对按压部件114进行说明。(4)按压部件114的详细构成图4是覆盖部件113及按压部件114的示意性立体图。如图4所示,按压部件114具有自上方按压第I部件113a的第I按压部件114a、及自下方按压第2部件113b的第2按压部件114b。第I部件113a及第2部件113b分别通过第I按压部件114a及第2按压部件114b而按压在互相接近的方向上。第I按压部件114a及第2按压部件114b是耐火性和耐热性优异的块状部件,例如砖等。第I按压部件114a及第2按压部件114b使用了与上述配置在第I管111及第2管112的互不相对侧的端部的隔热材料相比热导率更高的部件(优选为1.2 20W/m -K)。第I按压部件114a及第2按压部件114b分别在其厚度方向的一端部形成有沿长度方向以大致半圆状开放的空间S5、S6。第I按压部件114a及第2按压部件114b的内径与覆盖部件113的外径相同。由此,在将第I按压部件114a安装在第I部件113a的状态(作业时的状态)下,第I按压部件114a的形成空间S5的圆弧部314的内周与第I部件113a的覆盖部213a的外周接触。另外,在将第2按压部件114b安装在第2部件113b的状态(作业时的状态)下,第2按压部件114b的形成空间S6的圆弧部315的内周与第2部件113b的覆盖部214a的外周接触。另外,在将第I按压部件114a安装在第I部件113a的状态(作业时的状态)下,第I按压部件114a的除圆弧部314以外的第I下表面414与第I部件113a的凸缘部213b、213c的上表面接触。另外,第2按压部件114b的除圆弧部315以外的第2下表面415与第2部件113b的凸缘部214b、214c的下表面接触。此处,第I按压部件114a及第2按压部件114b的第I下表面414及第2下表面415的宽度优选为分别与第I部件113a的凸缘部213b、213c、第2部件113b的凸缘部214b,214c的宽度相同。第I按压部件114a是通过未图示的支持部件(例如螺丝等)而支持固定的。第2按压部件114b是通过未图示的支持部件(例如千斤顶等)而支持固定的。
第I按压部件114a及第2按压部件114b例如通过砖的榫眼(Mortice)加工或者浇铸而成型。(5)第I配管105及按压部件114的安装方法以下,对第I配管105及按压部件114的安装方法进行说明。首先,如图3所示,以覆盖与澄清槽102连接的第I管111的第I方向侧的端部、与搅拌槽103连接的第2管112的第2方向侧的端部、及第I管111与第2管112之间的第I空间SI的方式,安装第I部件113a及第2部件113b。具体而言,自第I管111及第2管112的上方安装第I部件113a,自第I管及第2管112的下方安装第2部件113b。需要说明的是,在图5中表示将第I部件113a及第2部件113b正常安装在第I管111及第2管112的状态。接着,如图4所示,在覆盖部件113上安装按压部件114。此时,以第I按压部件114a的内周与第I部件113a的外周接触且第2按压部件114b的内周与第2部件113b的外周接触的方式进行安装。需要说明的是,此后,对于澄清槽102、搅拌槽103、成型装置104、第I配管105、第2配管106等,利用配置在附近的温度调节装置而升温至特定温度(例如,作为作业时的温度的1500°C)。其后,开始进行作业。需要说明的是,在作业时的状态下,将玻璃原料在熔解槽101中熔解,使熔融玻璃流入第I配管105中而流向成型装置104(即,使熔融玻璃在第I管111及第2管112的内部流动)。需要说明的是,在将熔融玻璃自第I管111经由第I空间SI向第2管112输送时,使熔融玻璃的一部分的粘度局部提升(粘度提升工序)。在较澄清槽102更下游侧(自熔解槽101向成型装置104流动的熔融玻璃的流体的较澄清槽102更下游侧)使熔融玻璃的温度缓慢降低,因此熔融玻璃的粘度随着流向下游而缓慢提升。本实施方式中所谓的粘度提升工序并非是指上述的缓慢降低熔融玻璃温度的工序,而是指在间隙S2和间隙S3、以及在第I空间SI中局部且急速地提升玻璃粘度使其为log η =4以上的工序。在该工序中,使自熔融玻璃向覆盖部件113的外部转移的热转移量大于熔融玻璃的利用第I管111及第2管112进行输送时向外部释放的热转移量,从而急剧提升熔融玻璃的粘度。所谓热的转移量,是沿熔融玻璃的流动方向每单位长度的向外部转移的热的转移量。具体而言,在粘度提升工序中,在间隙S2及间隙S3中,在第I管111的第2管112侧的端部与覆盖部件113之间所形成的空间内,使熔融玻璃的一部分的粘度提升。此时,熔融玻璃的粘度Π为log η =4 13。另外,在粘度提升工序中,在间隙S2及间隙S3中,在第2管112的第I管111侧的端部与覆盖部件113之间所形成的空间内,使熔融玻璃的一部分的粘度提升。此时,熔融玻璃的粘度Η为log η =4 13。另外,在粘度提升工序中,凸缘部213b、213c、214b、214c的附近的熔融玻璃(具体而言,为进入凸缘部间空间S4的熔融玻璃)的粘度并非容易泄漏至外部那样柔和,而是为产生粘性流动的程度的粘度。需要说明的是,作为测定熔融玻璃的粘度的方法,可适用已知的方法。例如可根据熔融玻璃的粘度而适当使用球提拉法(球引t上(f法)、贯入法、弯曲梁法等。(6)利用本发明而制造的玻璃板的示例以下,对使用本发明而制造的玻璃板的示例进行说明。需要说明的是,并不限于下述方式。对于玻璃板的厚度并无特别限定,可为0.1mm 1.lmm、0.2mm 0.7mm、0.2mm
0.5mmο另外,对于玻璃板的尺寸并无特别限定,例如可为宽度方向的长度为500mm 3500mm、长度方向的长度为500mm 3500mm。需要说明的是,若玻璃板大型化,则为了保持生产性而需要增加熔融玻璃的量(以下,称为MG量)。即,存在玻璃板越大型化则配管(第I配管105或第2配管106)或装置(熔解槽101、澄清槽102、搅拌槽103、及成型装置104)的尺寸越大的倾向。因此,这些配管或装置的热膨胀量增加,配管或装置的破损的问题明显。
由此,在玻璃的宽度方向的长度为2000mm以上的情况时,本发明的效果尤为显著。另外,玻璃的宽度方向的长度越为2500mm以上、进一步3000mm以上,本发明的效果越显著。另外,对于玻璃板的种类并无特别限定,可为硼硅酸盐玻璃、铝硅酸盐玻璃、铝硼硅酸盐玻璃、钠钙玻璃、碱硅酸盐玻璃、碱铝硅酸盐玻璃、碱铝锗酸盐玻璃。另外,对于玻璃板的用途并无特别限定,可用于平板显示器(液晶显示器或等离子体显示器等)用玻璃板、太阳能电池用面板、覆盖玻璃。需要说明的是,所谓覆盖玻璃例如是指为了保护AV设备(移动终端等)的显示画面或壳体而对玻璃板进行化学或物理强化的强化玻璃。另外,作为平板显示器(液晶显示器或等离子体显示器等)用玻璃板,可以举出以质量%表示含有以下成分的玻璃板。下述括弧内的表示为各成分的优选的含有率,且越靠后越为优选。SiO2:50% 70% (55% 65%、57% 64%、58% 62%)、Al2O3:5% 25% (10% 20%、12% 18%、15% 18%)、B2O3: 0% 15% (5% 15%、6% 13%、7% 12%)。此时,作为任意成分,可含有下述组成。MgO:0% 10%(下限为0.01%、下限为0.5% ;上限为5%、上限为4%、上限为2%)、CaO:0% 20%(下限为1%、下限为3%、下限为4% ;上限为9%、上限为8%、上限为7%、上限为6%)、SrO:0 ~ 20%(下限为0.5%、下限为3% ;上限为9%、上限为8%、上限为7%、上限为6%)、BaO:0% 10%(上限为8%、上限为3%、上限为1%、上限为0.2%)、ZrO2:0% 10% (0% 5%、0% 4%、0% 1%、0% 0.1%)。另外,尤其是,玻璃板优选以质量%表示含有下述组成:SiO2:50% 70%、B2O3:5% 18%、Al2O3:10% 25%、Mg0:0% 10%、Ca0:0% 20%、Sr0:0% 20%、Ba0:0% 10%、RO:5% 20% (其中,R为选自Mg、Ca、Sr及Ba中的至少I种)。进一步,优选含有R’20:超过0.2%且为2.0%以下(其中,R’是选自L1、Na及K中的至少I种的玻璃板所含有的成分)。将此时的玻璃组成的玻璃称为含有微量碱的玻璃,将该玻璃组成的玻璃板称为含有微量碱的玻璃板。含有微量碱的玻璃的R’20的含有率只要超过0%且为2.0%以下即可。在本实施方式中,可使用R’ 20的含有率超过0%且为2.0%以下的含有微量碱的玻璃,但优选为超过0.2%且为2.0%以下。另外,R’20也可实际上为0.0%。将此时的玻璃组成的玻璃称为无碱玻璃,将该玻璃组成的玻璃板称为无碱玻璃板。另外,优选合计含有0.05% 1.5%的澄清剂,且实质上不含As2O3及PbO。另外,玻璃中的氧化铁的含量进一步优选为0.01% 0.2%。’另外,玻璃板优选以质量%表示含有下述组成:SiO2:50% 70%、B203:0% 15%、Al2O3:5% 25%、Mg0:0% 10%、Ca0:0% 20%、Sr0:0% 20%、 Ba0:0% 10%、RO:5% 20%(其中,R是选自Mg、Ca、Sr及Ba中的至少I种的所述玻璃板所含有的成分)。进而,在所制造的玻璃板为用于使用了 TFT(ThinFilmTransistor)的平板显示器(液晶显示器或有机EL显示器等)中的玻璃板的情况下,从抑制TFT的破坏的观点出发,本实施方式中所制造的玻璃板优选为无碱玻璃板。另一方面,为了使玻璃的熔解性与无碱玻璃相比有所提升,本实施方式中所制造的玻璃板也可为含有微量碱成分的含有微量碱的玻璃板。在碱金属氧化物自玻璃板中溶出的情况下,有可能破坏TFT,因此无碱玻璃板或含有微量碱的玻璃板可优选地用于使用TFT的平板显示器用途。
在为含有微量碱的玻璃板的情况下,优选为以质量%表示含有超过0.05%且为
2.0%以下的碱金属氧化物R’20,更优选优选为含有超过0.1%且为1.0%以下的R’20(其中,R’是选自L1、Na及K中的至少I种的玻璃板所含有的成分)。另外,优选合计含有0.05%
1.5%的澄清剂(以质量%表示),且实质上不含As2O3及PbO。另外,以质量%表示,玻璃组成中的氧化铁的含量进一步优选为0.01% 0.2%。需要说明的是,由于近年来对于平板显示器要求轻量化,因此在为平板显示器用玻璃板的情况下,SrO+BaO以质量%表示优选为0% 10%。另外,除轻量化的观点以外,若考虑到环境负荷,则BaO以质量%表示进一步优选为0% 2%。此处,关于平板显示器用玻璃板,如上所述可优选地使用:如上所述那样的SiO2或Al2O3的含量多且碱金属氧化物(Li20、Na2O, K2O)的含量少的含有微量碱的玻璃板、或者无碱玻璃板。但是,该含有微量碱的玻璃板或无碱玻璃板的熔解性低。具体而言,熔融玻璃的粘度η为logn=2.5时的温度为1500°C 1750°c,该温度高于含碱玻璃。关于具有这种粘度的熔融玻璃,需要使澄清槽102或其周边的配管的温度高于制造使用含碱玻璃的玻璃板的情况。因此,存在澄清槽102或其周边的配管的膨胀量增加而使配管的破损或变形显著的问题。更具体而言,在澄清工序中,熔融玻璃中的气泡浮起的速度受熔融玻璃的粘度的影响,熔融玻璃的粘度越低气泡的浮起速度越提升。因此,为进行无碱玻璃或含有微量碱的玻璃的澄清而使熔融玻璃的粘度为适合澄清的粘度、即200泊 800泊。如上所述,含有微量碱的玻璃板或无碱玻璃板的熔解性较低,因此在为无碱玻璃或含有微量碱的玻璃的情况下,与含碱玻璃相比需要使熔融玻璃的温度进一步提升。更详细而言,在无碱玻璃板或含有微量碱的玻璃板的制造中,在澄清工序中,需要使熔融玻璃的温度与氧化锡作为澄清剂开始发挥作用的温度相比为更高的温度(例如为1620°C以上,更优选为1650°C以上,进一步优选为1680°C以上) 。即,将设置在熔解槽101的下游侧的澄清槽102的温度提升至例如1640°C以上,由此将熔融玻璃加热至例如1620°C以上、更优选优选为1650°C、进一步更优选优选为1680°C以上。另外,在熔解槽101中熔解玻璃原料而成的熔融玻璃需要自澄清槽102流出之后保持在较高的温度(例如,1200°C 1600°C )直至供给至形装置104为止。因此,在无碱玻璃板或含有微量碱的玻璃板的制造中,可以设想流动有高温的熔融玻璃的装置(具体而言为熔解槽、澄清槽、搅拌槽、及成型装置)或配管(具体而言为第I配管或第2配管)的膨胀量变大。因此,容易产生这些装置或配管的破损。因此,在制造SiO2或Al2O3的含量多且碱金属氧化物(Li20、Na20、K2O)的含量少或完全不含有碱金属氧化物的平板显示器用玻璃板时,本发明的效果显著。例如,本发明适合于Si02+Al203的含量为70质量%以上(例如70质量% 95质量%)并且碱金属氧化物(Li20、Na20、K20)的含量为2质量%以下(例如O质量% 2质量%以下)的玻璃板。另外,本发明更适合于Si02+Al203的含量为70质量%以上(例如70质量% 95质量%)并且碱金属氧化物(Li20、Na20、K20)的含量为I质量%以下(例如O质量% I质量%)的玻璃板。另外,本发明更适合于Si02+Al203的含量为75质量%以上(例如75质量% 95质量%)并且碱金属氧化物(Li20、Na2O, K2O)的含量为0.5质量%以下(O质量% 0.5质量%)的玻璃板。需要说明的是,如上所述,为了使粘度为log η =2.5时的温度为1500°C 1750°C的熔融玻璃在澄清槽102中获得充分的气泡的浮起速度,例如需要使熔融玻璃的温度例如为1620°C以上。因此,与以往的含碱玻璃相比,上述熔融玻璃使构成澄清槽102的钼族元素或钼族元素合金的膨胀量增加。即,成为log η =2.5的温度为1500°C 1750°C的熔融玻璃容易使钼族元素或钼族元素合金的膨胀变大。因此,上述熔融玻璃适合于本实施方式的制造方法。关于玻璃的粘度,优选为成为log η =2.5时的温度为1530°C 1750°C,更优选为1550°C 1750°C,进一步优选为 1570°C 1750°C。另外,作为适用于覆盖玻璃或太阳能电池用玻璃板的玻璃板,例如可以举出以质量%表示含有以下成分的玻璃板。下述括弧内的表示为各成分的优选的含有率。SiO2:50% 70% (55% 65%、57% 64%、57% 62%)、Al2O3:5% 20% (9% 18%、12% 17%)、 Na2O:6% 30% (7% 20%、8% 18%、10% 15%)。此时,作为任意成分,可含有下述组成。Li2O:0% 8% (0% 6%、0% 2%、0% 0.6%、0% 0.4%、0% 0.2%)、B2O3:0% 5% (0% 2%、0% 1%、0% 0.8%)、K2O:0% 10%(下限为1%、下限为2% ;上限为6%、上限为5%、上限为4%)、MgO:0% 10%(下 限为1%、下限为2%、下限为3%、下限为4% ;上限为9%、上限为8%、上限为7%)、CaO:0% 20%(下限为0.1%、下限为1%、下限为2% ;上限为10%、上限为5%、上限为
4%、上限为3%)、ZrO2:0% 10% (0% 5%、0% 4%、0% 1%、0% 0.1%)。尤其是作为经化学强化的覆盖玻璃或太阳能电池用玻璃板,优选以质量%表示含有:
0160] SiO2:50% 70%、 0161] Al2O3:5%, 20%、 0162] Na2O:6% ~ -30%、 0163] K2O:0%10%、 0164] MgO:0%10%、 0165] CaO:0%20%。
在玻璃板的玻璃中,可添加澄清剂作为使玻璃中的气泡脱泡的成分。作为澄清剂,只要为环境负荷小且玻璃的澄清性优异的物质即可,无特别限制,可以举出例如选自氧化锡、氧化铁、氧化铈、氧化铽、氧化钥及氧化钨等金属氧化物中的至少I种。需要说明的是,As203、Sb2O3及PbO是具有在熔融玻璃中产生伴随价态变动的反应而使玻璃澄清的效果的物质,但As2O3及PbO为环境负荷大的物质,因此在本实施方式的玻璃板中,在玻璃中实质上不含As2O3及PbO。需要说明的是,在本实施方式中,所谓实质上不含As2O3及PbO意味着含量小于0.01%质量且除杂质以外并非故意含有的情况。此处,例如为使氧化锡、氧化铁等金属氧化物作为澄清剂而发挥作用,与As2O3相比需要进一步提升熔融玻璃的温度。由此,也需要提高澄清槽102或其周边配管的温度,因此与适用As2O3作为澄清剂的情况相比,澄清槽或其周边配管的膨胀量增加,配管的破损或变形的问题显著。因此,在不使用As2O3及PbO而使用氧化锡、氧化铁、氧化铈、氧化铽、氧化钥及氧化钨等金属氧化物作为澄清剂的情况下,本发明的效果更加显著。此处,在将玻璃板用于平板显示器用玻璃基板的情况时,对于气泡缺陷的要求特别严格。因此,作为澄清剂,优选至少含有氧化锡、氧化铁、氧化铈、氧化铽、氧化钥及氧化钨等金属氧化物中澄清效果特别高的氧化锡。在使用氧化锡进行澄清的情况下,在澄清槽102中例如需要使熔融玻璃为1600°C以上(例如1620°C以上)。其原因在于:若不使其为1600°C以上(例如1620°C以上),则氧化锡不会剧烈地释放氧气。为将熔融玻璃加热至1600°C以上(例如1620°C以上)而直接对构成设置在熔解槽101的下游侧的配管或澄清槽102的钼族元素或钼族元素合金进行通电。由此,将配管或澄清槽102的温度提升至1600°C以上(例如1620°C以上),将配管或澄清槽102中的熔融玻璃加热至适合澄清的温度。即,与使用As2O3作为澄清剂的玻璃板的制造相比,在使用氧化锡作为澄清剂的玻璃板的制造中,澄清槽102或其周边的配管的温度变高。因此,存在澄清槽102或其周边的配管的膨胀量增加而使配管的破损或变形显著的问题。因此,本发明的效果在使用氧化锡进行澄清的情况下更加显著。需要说明的是,如本实施方式,尤其是在将需要提升温度的澄清槽102与搅拌槽103连接的第I配管105中适用本发明的情况下,上述破损抑制的效果显著。进一步,近年来,为实现平板显示器的进一步高精细化,要求使用P-Si (低温多晶硅).TFT或氧化物半导体的显示器元件而并非使用α -Si (非晶硅).TFT的显示器元件。此处,在P-Si (低温多晶硅).TFT或氧化物半导体的形成工序中,进行与α -Si.TFT的形成工序相比温度更高的热处理。因此,对于形成有P-Si (低温多晶硅)*TFT或氧化物半导体的玻璃板,要求热收缩率小。为减小热收缩率,优选提高玻璃的应变点,但应变点高的玻璃倾向于高温时的粘度(高温粘性)变高。因此,在澄清槽102中,为使熔融玻璃为适合澄清的粘性而需要进一步提升熔融玻璃的温度。即,从提高熔融玻璃的温度观点出发,与以往相比,本发明的制造方法更适合于使用P-Si.TFT的平板显示器用玻璃板的制造。因相同的原因,本发明适合于使用氧化物半导体的平板显示器用玻璃板的制造。例如,本发明适 合于使用应变点为655°C以上且粘度η为logn=2时的温度为1600 V以上的熔融玻璃的玻璃板的制造。尤其是,本发明适合对于P-Si (低温多晶硅)*TFT或氧化物半导体的形成更适合的应变点为675°C以上的玻璃板的制造,进一步适合于应变点为680°C以上的玻璃板的制造,更进一步适合于应变点为690°C以上的玻璃板的制造。需要说明的是,作为应变点为675°C以上的玻璃板的组成,可以举出例如玻璃板以质量%表示含有以下成分的玻璃板。—种玻璃板,其包含:SiO2:52% 78%、Al2O3:3% 25%、B2O3:3% 15%、RO (其中,RO为Mg0、Ca0、Sr0、及BaO中所含有的成分的总量):3% 20%,且质量比(Si02+Al203) /B2O3 为 7 20 的范围。进而,为进一步提升应变点,质量比(Si02+Al203)/B203优选为7.5以上。进而,为提升应变点,优选使β -OH值为0.1mm 0.3mm。另一方面,为了在熔解时使电流通过熔融玻璃而不通过熔解槽102,优选含有0.01质量% 0.8质量%的R2O (其中,R2O为Li20、Na2O及K2O中所含有的成分的总量)以降低熔融玻璃的电阻率。或者,为降低熔融玻璃的电阻率而优选含有0.01质量% 1.0质量%的Fe203。进而,为实现高应变点并且防止失透温度的提升,优选使0&0/1 0为0.65以上。通过使失透温度为1250°C以下,可适用溢流下拉法。另外,在适用于移动通讯终端之类的移动设备等的情况下,从轻量化的观点出发,优选为SrO及BaO的总含量为O质量% 小于2质量%。(7)特征(7-1)以往,液晶显示器等平板显示器的显示部使用玻璃板。玻璃板是通过对片状的片材玻璃进行加工而成型得到的。片材玻璃是通过如下方式而成型的:在熔解槽中将所调配的原料熔解而形成熔融玻璃,使熔融玻璃通过用于去除气泡的澄清槽、用于使组成分布均匀的搅拌槽等而流入成型装置,从而成型为片材玻璃。流动有所熔解的熔融玻璃的装置或配管通常使用由钼或钼合金制造的装置或配管。其目的在于:防止熔融玻璃因构成装置或配管的材料熔融而受到污染、或通过向装置或配管本身通电而调整在内部流动的熔融玻璃的温度等。此处,在作业时流动在配管等中的熔融玻璃约为1000°C 1700°C的高温。另外,关于此时的熔融玻璃的粘度Π,为log Π =5以下。尤其是,关于在连接澄清槽与搅拌槽的配管中流动的熔融玻璃的粘度Π,为log Π =4以下。因此,在设备的设置时与作业时产生温度差。因此,可认为输送熔融玻璃的配管或装置产生热膨胀。但是,由于熔解玻璃原料的熔解槽或使片材玻璃成型的成型装置的位置是预先决定的,因此难以根据由钼或钼合金制造的装置或配管的热膨胀来移动熔解槽或成型装置。因此,若无法顺利地释放由钼或钼合金制造的装置或配管的热膨胀,则它们或成型装置等有可能变形而无法充分 发挥特定的性能。若考虑到更糟糕的状况,则也担心这些装置或配管部分破损。因此,由钼或钼合金制造的装置或配管的热膨胀是重要的课题。因此,例如在专利文献I (日本专利第4498390号公报)中,为了抑制作业时的钼或钼合金制配管的由热膨胀所导致的破损,在流动有熔融玻璃的配管的外壁及内壁上,在圆周部以螺旋状形成有在直径方向上凸出的凸出部。然而,如专利文献1(日本专利第4498390号公报)所公开的那样,输送熔融玻璃的配管大多情况下被分割为2段以上。其原因在于:若不将配管分割为2段以上,则难以吸收由配管或装置提升至作业时的温度时产生的热膨胀所导致的伸长。即,其原因在于:无法吸收由热膨胀所导致的伸长,因此配管或装置有可能变形或破损。另外,输送熔融玻璃的配管、装置、及它们的周边部件需要在作业前升温至作业时的温度的附近。其原因在于:若配管或装置的温度不足够高,则有可能在配管或装置中流动的熔融玻璃的温度下降,使熔融玻璃在配管或装置中凝固而无法流动。另外,认为其原因在于:若使高温的熔融玻璃在常温状态的配管或装置中流动,则在这些配管、装置或周边部件中产生与温度的差对应的热膨胀。即,认为在这种情况时,在输送熔融玻璃的配管、装置、及它们的周边部件中产生热膨胀/热应变,且认为由于该热膨胀/热应变而产生变形或破损。在专利文献I (日本专利第4498390号公报)所公开的发明中,认为利用焊接等将输送熔融玻璃的各配管连接而形成作业时的状态前,将其升温至特定温度。但是,在高温状态下对分割为2段以上的配管进行焊接等而形成作业时的状态,这对于作业人员而言是较为困难的作业。具体而言,首先,通常认为配置有该配管的空间在大多情况下较狭窄。因此,可认为对作业者而言难以在高温并且狭窄的空间内进行2段以上的配管的焊接作业。因此,有可能导致焊接作业的效率或精度降低。接着,如上所述,配管是在进行连接而形成作业时的状态前预先升温至特定温度的。但是,虽然预先使配管升温,但若考虑作业者的作业性等,则其上限温度为1000°C 1200°C,难以升温至作业时的温度(例如1500°C )。因此,即便为了抑制由热膨胀所导致的变形或破损而预先将配管升温至特定温度,也会在使配管为作业时的状态后,进一步升温至作业时的温度。因此,担心仍会产生配管的热膨胀,进而产生配管的变形或破损。更详细而言,认为由于应力集中于连接2段以上的配管的焊接区域、或温度高且强度弱的部位而产生配管的变形或破损。近年来,随著平板显示器的大型化,其使用的玻璃板也倾向于大型化。另外,随着所制造的玻璃板变大而使成型装置也大型化,因此为保持生产性而需要增加一天内流入成型装置中的MG量。需要说明的是,若使一天内流入成型装置中的MG量增加,则流动有熔融玻璃的配管或装置倾向于大型化。此处,若配管或装置大型化,则存在升温时的膨胀量增加而使配管的破损或变形显著的问题。进而,近年来由于环境负荷的问题,因此作为澄清剂,要求使用氧化锡或氧化铁等金属氧化物而并非毒性较高的As2O3。此处,为使氧化锡或氧化铁等作为澄清剂而发挥作用,与As2O3相比较,需要进 一步提升熔融玻璃的温度。即,需要提高澄清槽或其周边的配管的温度,因此存在澄清槽或其周边的配管的膨胀量增加而使配管的破损或变形显著的问题。如此,近年来存在由钼或钼合金制造的配管或装置的膨胀量增加的倾向,因此在上述专利文献I所记载的方法中,难以充分抑制上述配管的破损或变形。因此,在本实施方式中,即便流动有熔融玻璃的配管为进行了分割的状态、S卩如第I管111及第2管112那样配管彼此相隔的状态下,也可通过利用覆盖部件113覆盖该管
111、112及这两个管的管111、112之间的第I空间SI而将第I管111与第2管112连接。即,可通过简便的作业而将流动有熔融玻璃的配管、即第I配管105为作业时的状态。另外,在本实施方式中,对于第I管111及第2管112而言,两者均为一端固定而另一端未固定的状态。另外,覆盖部件113使用与第I管111及第2管112相同的部件。由此,考虑到配管的热膨胀,也可在预先将配管升温至特定温度后,不使其为作业时的状态。即,可在常温下使第I配管105为作业时的状态,因此作业效率提高、作业精度也提高。另外,通常认为多个部件等的焊接部分的强度容易降低,但在本实施方式中,可通过利用覆盖部件113覆盖管111、112及这两个管的管111、112之间的第I空间SI而间接地连接第I管111与第2管112。由此,从强度的观点出发也可以说是优选的。进而,在专利文献I (日本专利第4498390号)中,配管的一端与搅拌装置连接,另一端与其他配管连接。即,配管的两端为固定的状态。因此,若高温的熔融玻璃在内部流动,则会产生热膨胀,因此即便在配管的外壁及内壁上于周部以螺旋状形成有在直径方向上凸出的凸出部,也仍会担心在长度方向上产生压缩应力。另一方面,在本实施方式中,如上所述,对于第I管111及第2管112而言,两者均为一端固定而另一端未固定的状态。另外,在第I管111及第2管112之间存在第I空间SI。因此,在作业状态下,即便高温的熔融玻璃在第I配管105的内部流动而使第I管111及第2管112在互相接近的方向上产生热膨胀,也难以产生其长度方向的压缩应力。即,第I管111及第2管112的一端处于自由的状态,因此即便因作业时的温度的变更而产生收缩或膨胀,也可减少第I管111及第2管112自身的破损的可能性。换而言之,第I空间SI作为容许作业时的第I管111及第2管112的热膨胀的热膨胀容许空间而发挥作用。因此,可抑制流动有熔融玻璃的第I配管105的变形或破损。需要说明的是,本发明人使用本实施方式中所记载的玻璃板的制造方法及玻璃板制造装置100制造得到了长度方向为1870mm、宽度方向为2200mm、厚度为0.7mm的玻璃板。需要说明的是,此时的熔融玻璃中所含的各成分的含有率(质量%)如下所示。SiO2:60%Al2O3:19.5%B2O3:10%CaO: 5%SrO: 5%SnO2:0.5%
此时,即便连续进行玻璃板的制造,也不会在包含第I配管105的玻璃板制造装置100中产生变形或破损。由此,证明了本发明在抑制玻璃板制造装置100的变形或破损的方面是有用的。(7-2)在本实施方式中,覆盖第I管111及第2管112的端部、及第I管111与第2管112之间的第I空间SI的覆盖部件113具有2个以上的部件、即第I部件113a、及第2部件113b。由此,使覆盖部件113在第I管111及第2管112上的安装作业变得容易。(7-3)在本实施方式中,第I部件113a及第2部件113b分别具有覆盖部213a、214a、及凸缘部213b、213c、214b、214c。并且,在本实施方式中,通过第I部件113a的凸缘部213b与第2部件113b的凸缘部213b而形成了凸缘部间空间S4,并且通过第I部件113a的凸缘部213c与第2部件113b的凸缘部214c而形成了凸缘部间空间S4。例如,即便自第I管111经由第I空间SI向第2管112流动的熔融玻璃漏出至第I管111及第2管112的外部而向覆盖部件113侧泄漏,该熔融玻璃也可通过凸缘部间空间S4而提升粘度。即,凸缘部213b、213c、214b、214c是按照容易提升自间隙S2或间隙S3漏出的熔融玻璃的粘度的方式而设置的。另外,粘度经提升的熔融玻璃可发挥抑制在第I管111及第2管112的内部流动的熔融玻璃漏出至第I管111及第2管112的外侧的作用。另外,粘度经提升的熔融玻璃也可发挥使第I部件113a与第2部件113b接合的作用。由此,容易使第I部件113a与第2部件113b接合。利用熔融玻璃的粘度提升而使熔融玻璃具有接合剂的功能,由此也可不对第I部件113a与第2部件113b进行焊接。由此,作业效率得以提闻。此处,凸缘部间空间S4中的熔融玻璃的粘度易在提升的原因在于:凸缘部间空间S4是未由隔热材料覆盖而容易受外部气体影响的空间。即,由于与第I管111及第2管112的内部相比,温度不易上升。另外,源自在第I管111及第2管112的内部流动的熔融玻璃的转移热量也较少,因此与间隙S2或间隙S3相比,温度不易上升。换而言之,本实施方式的第I配管105是成为如下构成:该构成是可在凸缘部间空间S4中以熔融玻璃的温度与在第I管111及第2管112的内部流动的熔融玻璃及间隙S2、S3中的熔融玻璃的温度相比较低的方式调整热量。因此,进入该凸缘部间空间S4的熔融玻璃是未柔软至易在漏出至外部的程度,另一方面成为产生粘性流动的程度的粘度。(7-4)在本实施方式中,在熔融玻璃于第I管111及第2管112中流动的作业状态下,在覆盖部件113与第I管111及第2管112之间存在有间隙S2、S3。间隙S2、S3是未由隔热材料覆盖而容易受外部气体影响的空间,因此与第I管111及第2管112的内部相比,温度不易上升。换而言之,本实施方式的第I配管105采取如下构成:可在间隙S2、S3中以熔融玻璃的温度低于在第I管111及第2管112的内部流动的熔融玻璃的温度的方式来调整热量。即,在将熔融玻璃自第I管111经由第I空间SI向第2管112输送的输送工序中,提升该熔融玻璃的粘度(粘度提升工序)。由此,进入间隙S2、S3的熔融玻璃(即,进入第I管111的第2管112侧的端部与覆盖部件113之间的熔融玻璃、及进入第2管112的第I管111侧的端部与覆盖部件113之间的熔融玻璃)的一部分并非容易泄漏至外部那样柔和,而是为产生粘性流动的程度的粘度(具体而言,log η =4 13)。因此,例如即便在作业中改变包括第I管111及第2管112的各种部件等的温度而使第I管111及第2管112膨胀/收缩(S卩,即便产生应力),覆盖部件113也由于上述原因而在第I管111及第2管112的轴方向上自由移动,因此进入间隙S2、S3的熔融玻璃可吸收该应力。需要说明的是,从可抑制熔融玻璃自第I管111及第2管112漏出至外部的观点出发,进入间隙S2、间隙S3的熔融玻璃的粘度Π优选为log η =6 13、log η =8 13。需要说明的是,在本实施方式中,覆盖部件113具有凸缘部213b、213c、214b、214c,因此粘度也可低于上述粘度。例如,进入间隙S2、S3的熔融玻璃的粘度η也可为logn=2 10、1gn =3 8、log η=3 5。在该情况下,可抑制过度降低第I管111及第2管112的内部的熔融玻璃的温度而在熔融玻璃中析出晶体。因此,可进一步维持玻璃板的品质。(7-5)在本实施方式中,覆盖部件113是通过按压部件114而被按压的。具体而言,第I部件113a及第2部件113b分别通过第I按压部件114a及第2按压部件114b而按压在互相接近的方向上。此处,利用按压部件114按压覆盖部件113,由此能够以简便的方法固定第I部件113a及第2部件113b。由此,作业效率得以提高。(7-6)通常优选为自澄 清槽至搅拌槽为止使熔融玻璃的温度降低。并且,大多情况下在连接澄清槽与搅拌槽的配管的附近,使用用于间接地调整熔融玻璃的温度的温度调整装置。另一方面,在本实施方式中,按压部件114使用热导率高于配置在第I管111与第
2管112的互不相对侧的端部的隔热材料的部件。按压部件114与外部气体接触,因此与上述隔热材料相比容易散热。由此,按压部件114不仅具有按压覆盖部件113的作用,也具有隔着覆盖部件113而对熔融玻璃进行冷却的作用。由此,也可不使用温度调整装置,因此可抑制成本或能量,或者即便使用温度调节装置,按压部件114也具有温度调整装置的功能,因此可有助于节省温度调整装置的成本及能量。需要说明 的是,MG量越多该效果越显著。其原因在于:MG量越多熔融玻璃的保有热量越多,难以使第I配管105中的熔融玻璃的温度降低。(7-7)图6是通过第I空间SI且在第I方向的垂直方向上对图5所示的第I配管105进行切割时的剖面图。需要说明的是,在图6中,关于存在于第I配管105的内部的熔融玻璃,省略图不。以往,为使熔融玻璃不泄漏至配管的外部,主要是将流动有熔融玻璃的配管密封。由此,产生基于由热膨胀所导致的变形而产生的应力的问题、高温下的焊接作业的困难性等上述所说明的问题。另一方面,在本实施方式中,通过在相隔的状态下利用覆盖部件113来覆盖第I管111及第2管112,从而可使其作为输送熔融玻璃的第I配管105而发挥作用,因此如上所述,可减少上述问题。另外,在本实施方式中,利用向外部泄漏的熔融玻璃的固化,如图6中所示那样抑制在第I管111及第2管112的内部流动的熔融玻璃漏出至覆盖部件113的外侧。S卩,构成为即便熔融玻璃泄漏至第I管111及第2管112的外部,也可对其进行充分利用。(7-8)在平板显示器用玻璃板中,从抑制TFT的破坏的观点出发,可使用含有微量碱的玻璃或无碱玻璃,并且从减少环境负荷的观点出发,可使用氧化锡。因此,在玻璃板制造的至少澄清工序中,为高效地进行熔融玻璃的澄清而调整熔融玻璃的温度使其与以往相比较高。并且,从为了达成高精细的平板显示器而期望减小热收缩率的玻璃板的观点出发,可使用应变点高的玻璃组成。此时,对于应变点较高的玻璃组成而言,高温时的粘度(高温粘性)变高。因此,即便在减小热收缩率的情况下,也可调整澄清工序中的熔融玻璃的温度使其与以往相比较高。如此,从高效地制造玻璃板的观点出发,可相对于澄清工序中所要求的熔融玻璃的高温化而抑制流动有熔融玻璃的澄清槽102的周围的配管的变形或破损的本发明的制造方法是有效的。(8)变形例以上,基于附图对本发明的实施方式进行了说明,但具体的构成并不限于上述实施方式,可在不脱离发明的主旨的范围内进行变更。(8-1)变形例 IA在上述实施方式中,虽限定于第I配管105进行了说明,但并不限定于此,也可适用于使用钼族元素或钼族元素合金制配管的部位、例如第2配管106等。S卩,只要具有如第I管111及第2管112那样的相隔的多个配管(不限于2个,也可为3个以上的配管),就能够利用具有与覆盖部件113或按压部件114相同的构成/功能的部件将多个配管间接地连接。由此,也可形成比第I配管105长的配管。例如,在图7中示出了使用覆盖部件413将各自相隔的3个管310、320、330间接地连接的情况。覆盖部件413具有与覆盖部件113相同的构成/功能。(8-2)变形例 IB在上述 实施方式中,对第I部件113a及第2部件113b分别具有2个凸缘部213b、213c,214b,214c的情况进行了说明,但个数并不限于2个,只要具有至少I个凸缘部即可。另外,在上述实施方式中,对凸缘部213b、213c、214b、214c分别自覆盖部213a、214a的两端部在水平方向上向各自的外侧延伸进行了说明。但是,对于设置凸缘部213b、213c,214b,214c的位置并无特别限定,只要设置为相对于第I管111及第2管112向外侧延伸即可。(8-3)变形例 IC在上述实施方式中,对第I部件113a及第2部件113b分别具有凸缘部213b、213c、214b,214c的情况进行了说明,但凸缘部213b、213c、214b、214c也可不为必需的构成。例如,代替设置凸缘部213b、213c、214b、214c,可选择热导率高且易于冷却的材质作为按压部件114的材质、或者也可对第I按压部件114a与第2按压部件114b的接合部分进行冷却。另外,在上述实施方式中,对凸缘部213b、213c的宽度Wl优选为20mm以下的情况进行了说明。另外,对第I按压部件114a及第2按压部件114b的第I下表面414及第2下表面415的宽度优选为分别与第I部件113a的凸缘部213b、213c及第2部件113b的凸缘部214b、214c的宽度相同的情况进行了说明。但并不限定于此。例如,若考虑到各种状况,则可使凸缘部213b、213c的宽度Wl及凸缘部214b、214c的宽度大于上述实施方式、或也可使其分别大于第I下表面414、第2下表面415的宽度。具体而言,例如在为减少第I配管105中的熔融玻璃的冷却量而在第I按压部件114a及第2按压部件114b中使用隔热性相对较高的材料的情况下,有时第I部件113a的凸缘部213b、213c及第2部件113b的凸缘部214b、214c的温度过度上升。总而言之,可依据想要利用凸缘部213b、213c、214b、214c释放多少热量而改变它们的宽度、或按压部件114的材料及尺寸等。(8-4)变形例 ID在 上述实施方式中,对第I部件113a与第2部件113b之间存在凸缘部间空间S4的情况进行了说明,但并不限定于此,也可使第I部件113a与第2部件113b接触。S卩,也可不形成凸缘部间空间S4。在图8中示出了该情况下的一个示例。在该情况下,例如只要较长地形成第I部件113a的覆盖部213a和/或第2部件113b的覆盖部214a的圆弧部分就能够形成间隙S2及间隙S3并且不形成凸缘部间空间S4。若采用这种构成,则第I部件113a的凸缘部213b、213c与第2部件113b的凸缘部214b、214c接触。此处,例如在第I按压部件114a的自身重量大于第I配管105内的压力的情况下,也可不使用按压部件来支持配置在第I管111及第2管112的上方的第I部件113a或第I按压部件114a。在该情况下,可更加有助于节省成本或提高作业效率。需要说明的是,也可利用焊接等将第I部件113a与第2部件113b连接。例如,通过利用焊接等将第I部件113a的凸缘部213b、213c与第2部件113b的凸缘部214b、214c连接,可提高第I配管105的强度。此处,第I部件113a与第2部件113b的焊接等可在提升第I配管105的温度之前进行,因此也可提高作业效率或作业精度。另外,即便在该情况下,自第I管111及第2管112流向外部的熔融玻璃的粘度也容易在凸缘部213b、213c、214b、214c的附近提升。
另外,在上述实施方式中,对覆盖部件113与第I管111及第2管112之间分别存在间隙S2、S3的情况进行了说明,但并不限定于此。例如也可仅形成间隙S3,或也可形成间隙S2、S3中的任一个。前者的情况下,第I部件113a的内径与第I管111及第2管112的外径相同。在该情况下,第I部件113a是以覆盖部213a的内周与第I管111及第2管112的外周接触的方式安装在第I管111及第2管112上的,因此可进一步抑制熔融玻璃向第I管111及第2管112的外侧漏出。后者的情况下,第I部件113a及第2部件113b的内周与第I管111及第2管112的外周接触。虽然需要提高第I部件113a及第2部件113b的制作精度、及各部件的设置精度,但在第I管111及第2管112内流动的熔融玻璃的温度高,另一方面在欲将该部分中的冷却抑制为最小限度的情况下是有效的。
玻璃板的制造方法及玻璃板制造装置制作方法
- 专利详情
- 全文pdf
- 权力要求
- 说明书
- 法律状态
查看更多专利详情
下载专利文献
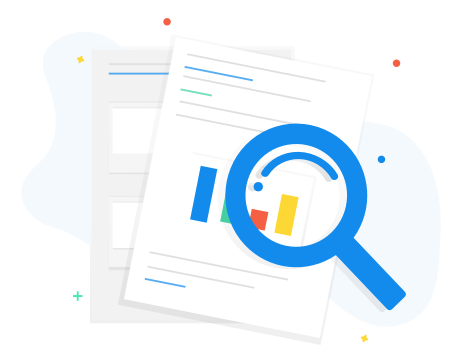
下载专利
同类推荐
-
吉田雅也徐红萍, 邓建清K-J·胡贝尔-哈格, I·比罗-弗朗斯苅谷浩幸, 前田伸广苅谷浩幸, 前田伸广
您可能感兴趣的专利
-
苅谷浩幸, 前田伸广苅谷浩幸, 前田伸广杉田守男陶武刚, 陈健杉田守男杉田守男杉田守男
专利相关信息
-
徐东泌徐东泌徐东泌