专利名称:用于表征手术针中孔的形状和尺寸的x射线显微方法手术针和缝合线组合是外科手术领域所熟知的。手术针和缝合线是外科手术和创伤修复的基本支柱。手术缝合线传统上由天然或合成聚合物材料织造或编织而成,所述材料包括丝绸、聚酯、聚对二氧环己酮、聚交酯等等。缝合线还可由单丝构成。缝合线可为生物可吸收或不可吸收。手术缝合线通常安置到传统手术针上以形成针和缝合线组合,以便于外科医生用来缝合组织等。传统手术针通常为细长、弯曲的结构,具有远侧穿刺顶端和近侧缝合线安装部。可选地,针可具有刀刃以帮助组织穿透。近侧缝合线安装部可具有用于接纳缝合线末端的传统盲深孔或槽。手术缝合线的一端或两端可装在所述槽或深孔中并以传统方式固定于其中,所述传统方式包括将手术针的缝合线安装末端局部压缩的传统机械型锻以及粘合齐U、粘固剂等。手术针传统上由生物相容性材料制成,特别是金属和金属合金,例如外科手术级不锈钢。在手术针发展的早期,使用槽来将缝合线附装在针上。这对于带针眼的针而言是一种改进,其中在手术现场将手术缝合线穿过所述针眼。然而,槽在闭合(即,被型锻)时 (或多或少)会在槽的远侧部分中形成隆起块。这样的隆起块可能对于外科医生以及其他医疗专业人员而言是不可取的,因为隆起块会妨碍针穿过组织时的平滑通过。带槽针的这一特性已通过引入机械钻削的深孔以用于缝合线安装而得以消除,然而机械钻削仅可用于低强度合金和大直径孔。较近期激光打孔的使用是本领域的一个重要进步并解决了这一问题,因为其允许在小直径线材(尤其是由高强度合金制成的线材)中打出小直径深孔,目前大部分高强度合金由于技术局限而无法机械钻削。钻出的深孔在手术针中尤为理想,因为针主体的轮廓不会像在针的近侧缝合线安装端中冲压槽时那样改变。平滑轮廓是外科医生所希望的,因为据认为这样可减轻组织创伤并通过显著降低阻力而减小拉引针穿过组织所需的力。手术针中的钻出深孔可以多种传统方式形成。如前所述,用于钻孔的两种传统方法包括机械钻削和激光打孔。机械钻削的深孔和激光打的深孔之间存在明显不同。机械钻削的深孔的形状和轮廓通常均勻且精确,因为它们呈现钻头的形状。机械钻削的手术针可利用传统塞规(即, 具有恒定直径,或者可选地从近侧向远侧渐缩的机加工的圆柱件)来容易地检查。尽管机械钻削通常将生成具有较精确尺寸和精确构型的深孔,但是仍存在可能与机械钻削相关的若干缺点。这些缺点包括自动化高速制造系统中慢的深孔深度;钻头磨损和寿命;难以对细线径的针制造工业生产级钻头;成本增加;以及无法在小线径的高强度合金中钻小直径孔。尽管激光打孔克服了这些问题,但另一方面,激光打孔带来了若干其他独特问题,这些问题尚待解决,虽然其无疑是可以解决的。激光打孔的针往往会具有与使用激光打孔相关的若干问题。例如,在激光熔融材料以形成孔的情况下,有可能在孔内部形成重铸物, 此类重铸物可能影响缝合线附接。其他问题可能包括深孔轮廓的一致性和深孔的光滑度、 以及爆裂的可能性。已经开发出在手术针中深孔的激光打孔工艺。此类工艺的例子包括在下列美国专利和专利申请(这些专利和专利申请以引用方式并入本文)中US6018860、US 5776268、US 5701656、US 5661893、US 5644834、US 5630268、US 5539973、US6252195 和 US20050109741。此类激光打孔工艺具有许多优点,包括对高速制造工艺的适应能力、效率和成本、在小线径的基本上任何材料中钻小孔的能力、以及维护量减少。尽管激光打孔工艺具有所有这些优点,但如前所述,激光打孔通常不具有与机械钻孔相同的精确尺寸构型。激光打孔利用传统激光器,所述激光器所发射的激光束的形状通常为锥形或高斯形。这意味着通过激光束钻成的深孔通常随其深度加大而渐缩。设计用于钻孔的激光束的参数,例如能级、脉冲、波形等,以形成具有所需构型和特性的深孔,包括深孔深度、长度、横截面以及关于针的纵向轴线和关于针线材主体的中心的取向,使得激光打的深孔能够充分且有效地接纳手术缝合线的末端以安装和附接。这是由激光打孔的本性导致的,其中当光束被定向时,高能量脉冲激光束基本上使位于针近侧的缝合线安装端的目标金属液化或汽化。在一些激光打孔中,熔化的材料将在孔内不一致地重塑;这种重塑的材料常常称作重铸物,如前所述。重铸物可引起不均勻的孔状态,这会影响缝合线插入和附接。为了将手术缝合线的末端有效附连或安置在手术针中的激光打的深孔中,尽管如上所述成锥形,深孔应该类似于机械钻孔的针中所形成的深孔具有基本上均勻的直径。类似地,深孔的长度必须具有最大和最小尺寸。该长度过长会削弱针的强度,而过短会导致针 /缝合线分离。并且,深孔须相对于缝合线针的近端的纵向轴线较为对中。关于测量激光打的深孔的尺寸,当前技术水平是如机械钻削的深孔的传统标准那样使用传统机械针规。针规的使用通常为人工过程,其中从许多已钻孔针中选择统计意义上显著数量的针,然后由检查员将针规手工插入深孔中。记录所得数据。存在与使用机械针规相关的若干缺点。虽然针规非常理想地适用于机械钻孔的针,但其不是特别适用于激光打孔的针的制造,其原因有几个。首先,针规不适合用于高速的制造工序。另外,用于测量甚小直径的深孔的针规昂贵且难以制造,且用于更细直径的容易损坏。另外,使用针规无法提供有关重铸物存在的信息。针规可容易地测量机械钻削的深孔,因为其本质上是圆柱形的并具有规则轮廓,但手术针中的激光打的深孔的轮廓通常不是圆柱形的,并且可能包含重铸物,沿着深孔的长度直径可能变化。因此,针规仅近似于激光打的深孔的小直径测量值,而无法提供有关其他重要参数的其他信息,例如渐缩、长度、居中程度、不规则性、倾斜程度等。重铸物的存在会导致无法正确表示激光所深孔的真实小直径。另外,如上所述,针规测量无法应对深孔轮廓的可能变型。使用针规无法指示大直径或表示深孔轮廓的变化。 因此,针规仅能提供指示深孔的最小可能直径的测量值,而无法就直径变化、轮廓、倾斜程度以及其他关键参数给出值或加以确定。与使用针规相关的另一缺点在于,针规不提供实时数据,所述实时数据可用于立即调节生产工艺参数。一批已钻孔针的统计采样可能指示深孔不合格,从而需要销毁整个不合格批次的针。其他缺点包括针规磨损;相对于所需深孔测量值针规为负公差还是正公差;以及认可了满足针规标准的针孔,但仍具有未检测到的阻碍或阻止后续缝合线附接的内部几何形状。针规测量是手动工序,因此,不是能够跟上高速手术针制造工艺的速度的工序,所述工艺是现代针制造工艺中所需的且通常与激光打孔相关。激光打孔的针的统计采样可能令人难以接受(尽管如果愿意接受伴随的任何缺点,则也是可能的),不可能实时检查统计相关样本。因此,通常有必要使用减小的样本大小,这可能导致假阳性,从而可能导致销毁激光打孔的针,而如果按照合格水平检查,将不会导致这样的损失和与一生产批次的针的损失相关的相当花费。针规检查方法的另一缺点包括有可能认可满足针规标准的深孔,但仍具有未检测到的阻碍或阻止后续有效缝合线插入和附接的缺陷内部几何形状或构型,从而可能在现场导致故障。如上所述,传统深孔测量手段(即,塞规测定)由于伴随的许多缺点而不适用于激光所深孔。考虑到激光孔的不一致轮廓,塞规测定仅可向用户提供不一致轮廓的小直径的指示,而无法提供大直径和/或孔轮廓的测量。这是严重的缺点,因为孔轮廓的变化以及孔的小直径和大直径之间的差异直接影响将缝合线固定到针的能力。在机械所深孔中这不是问题,因为孔是钻头几何形状的反映。另一缺点在于针规测定极其耗时,且仅具有与针规被制造和维护一样的精度。不幸的是,除了物理破坏(具体地讲,机械地横截针并检查深孔的形状)之外没有其他选择,这对统计上显著的样本大小而言是困难、费力、耗时且性价比不高的,并且无法提供可用于控制生产工艺的实时信息。因此,本技术领域需要一些新方法,用以在高速制造环境下表征深孔并使用这样的表征来调节和控制激光打孔和后续制造工艺。其显著效果在于提高产率与产品性能,并改善产品的一致性。
因此,本发明公开了一种表征手术针中的钻孔的新型方法。在此方法中,将X射线束从X射线发生器定向到手术针(优选地,包含深孔的手术针的近端)。被X射线束照射的传感器数字地产生针近端的图像。至少针的近端位108于X射线发生器和所述传感器之间。所述图像包括激光打的深孔。处理所述数字图像以确定相对于所述深孔的标准尺寸规格的偏差。尤其优选用激光打孔。本发明的另一方面是一种在深孔工序期间控制激光打孔设备的方法。在此方法中,设置将激光束发射到手术针的近端的激光器,以在针中深孔。将X射线束从X射线发生器定向到手术针(优选地,定向到包含激光打的深孔的手术针的近端)。被X射线束照射的传感器数字地产生针近端的图像。至少针的近端位于X射线发生器和所述传感器之间。所述图像包括激光打的深孔。处理所述数字图像以确定相对于所述深孔的标准尺寸规格的偏差。然后提供算法以确定对激光束参数的适当校正,以便于得到在所述规格范围内的手术针中打出的深孔。本发明的另一方面是一种表征手术针中的激光打的深孔的方法。在此方法中,将 X射线束从X射线发生器定向到手术针(优选地,定向到包含激光打的深孔的手术针的近端)。被X射线束照射的传感器数字地产生针近端的图像至少针的近端位于X射线发生器和所述传感器之间。所述图像包括激光打的深孔。处理所述数字图像以确定相对于所述深孔的标准尺寸规格的偏差并确定所述深孔的测量值。用包含所述图像的所述测量值的代码标记针或装载所述针的载带,每个针被给予数字标识符。可选地,下游工艺步骤可利用此信息,改变诸如压力、时间和保压之类的压缩变量以抵消通过X射线分析确定的深孔轮廓的细微变化,由此控制缝合线在深孔中的附接。这极大地提高缝合线/针对接或附接的一致性和功效,并对该元件的性能有直接贡献。本发明的这些方面和其他方面以及优点将通过下列和附图变得更为显而易见。图1是本发明的激光打孔工艺的流程图。图2是示出机械钻头的几何特征和参数的示意图。图3是插入激光打孔的手术针的深孔中的针规的示意图;所述针以横截面示出。图4是示出被安装并型锻在手术针近端的激光加工深孔内的手术缝合线的远端的示意图。图5是被型锻在手术针近端的机械钻削的深孔内的手术缝合线的远端的示意图。图6是被装线并剖切的激光打孔手术针的照片,其示出了深孔。图7是被装线并剖切的手术针的照片,其示出了激光打的深孔存在重铸物。图8是激光打孔手术针的近端的装线的横截面照片。可以看到所钻深孔已爆裂。图9是激光打孔的针的近端的装线的横截面照片,其中沿着深孔长度可容易地看到孔径的不一致或变化。图10是机械钻削手术针的透视X射线图像。图11是激光打孔手术针的透视X射线图像。图12是砧型锻的激光打孔针的X射线图像。图13是激光打孔手术针的近端的X射线图像,其中可看到潜在的爆裂缺陷。图14是已被型锻的激光打孔手术针的远端的透视X射线图像,其中可见由型锻工艺所导致的内部开裂。
图8是激光打孔手术针的近端的装线的横截面照片。可以看到深孔已爆裂,其中激光束导致围绕深孔的针侧面向外部开口,从而在针中形成通向深孔腔的侧向孔或开口。 这是不可取的,因为其形成外观瑕疵,会削弱壁,导致破损的可能,并且可能形成会割伤使用者或在不需要的部位切割组织的锋利面。现在参照图9,可以看到激光打孔的针的近端的横截面照片。沿着深孔的长度可容易地看出深孔径的不一致性;还可以看到较大的和较小的直径。图10、图11和图12的图像示出被X射线照射的针的实例。图10示出机械钻孔的针的远端。不难观察到深孔的均勻性并且可见到规则的形状,这与激光打的深孔形成对照。图11是激光打孔的针的近端的X射线图像。可清楚地看出深孔的锥形。显然,由于此锥形,不是深孔的整个长度均可使用,而在机械钻孔的针中,孔的整个长度均可利用(即用来接纳缝合线的远端)。图12是砧型锻针激光打孔的针的X射线图像。该图像示出X射线图像能够呈现附接工艺的结果,而其无法通过非破坏性的任何其他手段做到。X射线成像还非常适合于制造。可检查多个图像并且可获得实时信息和评价,因为仅需要几毫秒就可拍摄照片并进行尺寸和轮廓评价;这取决于X射线孔径和计算机速度。一种特殊的可能性是将照片评价与激光器控制相结合,并利用检查结果来对激光器进行微调或控制,以优化一致性并将变化降至最低。X射线检查的一个尤其显著的前景在于其能够检查细微到甚小直径的线材/孔径。这是针规测量所无法实现的,尤其是在高速率下更是如此。X射线系统一次可检查多个针,而针规测量一次仅可检查一个针。针规测量还易受针规公差、其磨损程度、其同心度(不因使用而弯曲)和检查员技能的影响。通过X 射线检查所有这些特性均得以消除。还无法以任何有效的速率对针进行针规测量。X射线系统还可通过一次扫描多个针来以任何所需速率进行检查。X射线系统还将提供测量结果的即时电子归档,从而可消除将数据从测量值转移至纪录单时的纸面处理差错与耗时。图13是示出潜在爆裂状态的X射线图像。该照片示出了激光打的深孔偏离中心的针,所得轮廓显示深孔处于几乎贯穿侧壁的薄壁状态。该状态会导致针的过早失效以及可能因削弱区域的部位而造成破损。图14是具有深孔的针的X射线图像,其中针的材料已断裂并局部分离。这在如下情况下值得关注断裂蔓延至表面从而导致削弱区域,所述削弱区域有可能导致破损,或者断裂可能影响装上的缝合线,使得缝合线被切断,从而与针过早分离。本发明的新型X射线表征方法提供了一种在自动化针制造工艺中表征深孔的方法。该方法可用于利用机械钻削的工艺或利用激光打孔的工艺。本发明的表征方法尤其被优选用于激光打孔工艺。本发明的方法中可利用的X射线装置或X射线机将具有如下特性。 X射线装置能在X射线单元内在X射线发射源和传感器之间传送并适当定位单个或多个已钻孔针。所述单元还能将针暴露于发射源所发射的X射线,获得所得X射线图像并将其数字化。所述单元还能将数字化图像与数字模板或一系列具体深孔尺寸要求进行比较,提供并产生有关深孔合格性的指令性处置信号。另外,所述单元具有处理能力以有效处理所述指令性信号,从而分类或以其他方式识别各个针的合格性或具体深孔尺寸、和/或调节激光参数以制作规定要求范围内的深孔。所述X射线单元将为可针对本发明的方法进行修改的传统市售单元,例如,由Envision Product Design (Anchorage, Alaska)制造的X射线单兀。可用于实施本发明的方法的X射线装置提供用来与标准尺寸进行比较的已钻深孔图像的数字化输出。该比较可以包括下列方式在内的若干方式进行。将由X射线单元拍摄并生成的图像像素化。评价这些像素的光密度。将此密度与已同样像素化的模板进行比较。由于像素的尺寸为已知量值,所以系统对在模板所确定的光密度范围内的像素进行计数,并将此计数转换为长度单位。如果所得值在公差范围之内或在公差范围之外,则传输适当指示。另外,可跟踪这些测量值,持续作出统计结论以进行轨迹与趋势判断或统计控制。 另外,该信息可选地通过墨水、激光蚀刻或其它已知手段记录在针和/或其载体上,以用作下游信息。这样,通过对每个针提供数字标识,然后在计算机数据库中存储与数字标识对应的图像,数字化地存储每个针的每一表征。可用于本发明的实践的优选X射线系统是集成检查系统,其包括屏蔽机柜、设置在机柜顶部的130kV X射线源、设置在X射线源下方的高度可调式平台上的4" X4" CMOS 成像面板、用于将样本定位于X射线源下方的四轴操纵器以及带有软件的计算机工作站。 为了对针成像,所述方法以如下步骤开始将成像面板设置成与X射线源相隔所需距离,将待检查的样品针附装在操纵器的检查板上,然后基于所需取向和几何放大率将该样品移动到位。如果还没有开发出先前的成像技术,则下一步骤将涉及校准和各种试拍,以确定最佳光子能量(电压kV)和光子通量(发生器电流mA)。最佳kV和mA参数对于针材料、厚度和拍摄几何尺寸是唯一的,并被选择以提供图像灰度值是最大可能范围,以达到最高的可能图像对比度。如果还没有开发出先前的成像技术,则成像可以所需的小调整开始,以将针定向到可观察关注区域(AOI)。通常,拍摄总是要涉及到由针偏离成像面板平面设置并朝着X 射线源移动所导致的几何放大率。随着针移动更靠近X射线源而远离成像面板,面板上所得的图像将变得更大,从而形成针的放大视图。根据AOI的尺寸,最高放大率可达15X。为了采集X射线图像,启动X射线源,用投射到X射线面板上的X射线光子束照射针。处于光束中间的针在面板上形成与针的密度对应的阴影,针的密度基于材料和几何形状或厚度而变化。面板将部分衰减的X射线束强度转换为与饱和X射线能量和不可测X射线能量之间的范围对应的电信号。此信号被数字化为视觉上由0至4096范围内的灰度值表示的12比特范围,并呈现在IXD显示器上。然后对图像应用调窗工具以选择包含有关数据的较窄灰度值范围,调节所述工具以使所关注的值范围内的图像对比度最大化。在已采集并调节了图像以获得最佳观察之后,可完成分析和判读并基于检查要求来评价图像。典型评价可包括利用已针对X射线校准的工具对特征进行尺寸分析。本发明的用于表征手术针中的钻孔的新型方法示意性地示出于图1中。从图1可以看出,在其近端12中具有激光打的深孔30的手术针10被装在将针生产工位之间移动的输送带40上。首先使装上的针10向激光打孔工位50移动,在激光打孔工位使用传统激光器,所述激光器的激光束具有足以能够在手术针10的近端20中钻出深孔30的所需波形和参数。此类参数包括常规参数,例如焦点、脉冲和功率。然后,针10和输送带40向X射线表征工位70移动。在工位70,用X射线照射每一单独的针10,获得在远端12包括深孔30 的针的数字表征。在工位70给予每个针数字识别号,将X射线表征发送给控制器/处理器 90。控制器/处理器90是传统的计算机或数据处理器。每个针10的表征由控制器/处理器90存储在存储单元100中,并被分析以确定深孔的尺寸特性,包括纵向取向、中心、最大直径和最小直径、最大长度和最小长度以及深孔周围的最大和最小壁厚。将所述尺寸特性与标准模板进行比较,并记录偏差。可选地,利用每个针的特性以及相对于标准的偏差来产生信号92,该信号被发送回激光打孔工位50给控制激光打孔工位的计算机,以便调节激光打孔光束的特性,包括诸如波形、脉冲、能量、功率、焦点、脉冲和时间之类的参数,为得到距约相对于规定尺寸最小偏差的深孔创造条件。另外,可选地,可利用与深孔尺寸有关的信息产生信号95,该信号被发送给缝合线附接系统110(例如,机械型锻系统)的控制器/处理器,以便于计算和控制附接压力和保压,以优化缝合线/针对接的产率和性能。这样,每个已钻孔针能够具有一组根据该针中深孔的特性定制的附接参数。可选地,用唯一的标识符标记每个针,这可用常规方式完成,包括例如激光蚀刻或喷墨印刷。除了标识符(例如条形码)之外,可选地,可在每个针上标记每个针的得自X射线表征步骤的数据(包括特性以及相对于标准的偏差)。可利用本发明的新型方法处理的手术针包括具有缝合线安装末端(优选具有近侧深孔)传统手术针。所述手术针可由传统生物相容性材料及其等同物制成,包括(但不限于)马氏体不锈钢(例如,UNS 42000)、奥氏体不锈钢(例如,UNS 30200)、马氏体时效不锈钢(例如,UNS S45500.UNS 46910和ETHALL0Y牌不锈钢)和耐热合金系(例如钨铼合金) 以及聚合材料和陶瓷材料和复合材料。针可具有1. 0密耳至70密耳,优选约6. 0密耳至约 12密耳范围内的线径,并将具有多种常规长度。本发明的新型X射线和激光打孔工艺具有许多优点和意义,包括如下所述。可在高速制造工序中按照激光打孔速度执行X射线成像。 该成像不是破坏性的,使得被测试针可被用作成品。所述方法取消了成本高且可能不精确的塞规测量。计算机可对照轮廓和/或预定的测量值对X射线图像进行数字化、放大和查询,其可形成实际测量值并允许对制造的每个针作出有根据的处置。X射线成像系统和工序可向后连接到激光打孔工位,由此将深孔的测量值反馈回给激光器以进行调节以微调和 /调节激光束的参数,从而通过调节诸如焦点、时间、能量、脉冲或位置之类的参数来控制深孔形状和纵横比(深度与直径测量值之比)。还可通过稍后在制造工序中连同唯一的数字标识一起对每个针或与针相邻的针载体以代码或实际数字标记“通过”/ “未过”或实际测量值,进一步增强本发明的方法以改善质量处置。通过调节将针附接到缝合线时的压力、保压和闭合力,所述数据还可用来控制将所述缝合线附接至针(例如,通过传统型锻工艺)的过程。通过确保针/缝合线附接的完整性,这将导致优化的产率和进一步改善的成品质量。虽然本发明已通过其详细实施例得到了显示和描述,但本领域的技术人员将会理解,在不脱离受权利要求书保护的本发明的精神和范围的前提下,可以对本发明进行形式上和细节上的各种更改。
本发明公开了一种表征激光打的深孔的新型方法。所述方法使用X射线显微方法来进行尺寸表征。在包括激光打孔系统和型锻设备的自动化生产系统中,对X射线输出进行处理以控制制造设备。
用于表征手术针中孔的形状和尺寸的x射线显微方法
- 专利详情
- 全文pdf
- 权力要求
- 说明书
- 法律状态
查看更多专利详情
下载专利文献
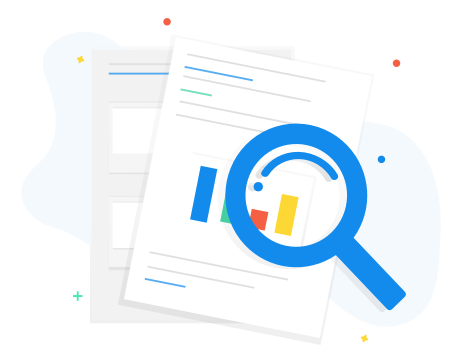
下载专利
同类推荐
-
斯科特·T·拉特雷尔斯科特·T·拉特雷尔伍晓明
您可能感兴趣的专利
-
余光远, 乔治·哈齐利亚朴淳五朴淳五梁智韦, 解燕喜石运香, 付存玉徐金根, 胡庆华徐金根, 胡庆华
专利相关信息
-
徐金根, 胡庆华苏同江苏同江苏同江