专利名称:生物反应器及其连续生产槐糖脂的方法当发生大面积溢油事故,尤其是海上天气状况恶劣时,使用围油栏、撇油器等物理方法回收溢油十分困难。这种情况下,溢油分散剂可以加速油的自然消散过程,在海浪作用下其更容易将油破碎为小油滴,加速溢油的自然生物降解。溢油分散剂的使用已逐渐为人们所广泛接受,大多数的海岸线国家在应对油泄漏的时候都依赖于分散剂。消油剂可分为化学消油剂和生物消油剂。由于生物消油剂的主要成分生物表面活性剂的生产成本居高不下,阻碍了生物消油剂的大规模应用,目前在应对海上溢油事故时使用的主要是化学消油剂。但化学消油剂本身具有一定的毒性,因此世界各国政府对化学消油剂的应用,都采取慎重的态度。生物消油剂逐步取代化学消油剂是必然的趋势,我国也于2010年7月,在应对大连的原油污染时,首次大规模采用了生物技术处理溢油事故,取得了很好的效果。槐糖脂作为可降解的生物表面活性剂,具有良好的乳化、分散、增溶等特性,且与人体和环境相容性好,以其为主要成分的生物消油剂是化学消油剂的良好替代品。此外,槐糖脂在食品、医药、化妆品、冶金、环境保护、废油回收等领域具有很高的研究和开发价值, 目前已应用于日化、医药、食品工业、石油工业等重要领域。国际上对槐糖脂理论研究及应用开发已开展多年,但我国目前在该领域还处于起步阶段。槐糖脂的应用范围非常广阔,但是其生产成本居高不下,限制着槐糖脂大规模的商业化生产进程,现在我国国内还未有大规模的槐糖脂生产企业,国际范围内也没有纯品槐糖脂的公开销售。制约槐糖脂工业化生产的因素主要包括菌种的生产能力、培养条件、生产方式以及分离提取方式等,其中菌种诱变工作和培养条件优化研究已经非常普遍,也发现了较为优良的菌种,在适宜的培养条件下可达到较高且稳定的产量,但总体来看,现有的工艺与实现工业化生产所要求的低成本还有很大的差距。发明内容本发明要解决的技术问题是提供一种具有降低生产和分离成本,环境友好,操作简单的连续生产槐糖脂的方法。为解决上述技术问题,本发明采用如下技术方案包括罐体,及设置在罐体上的加热套;所述罐体内设置有带梯形孔的筛板,所述筛板将罐体分隔成上面为柱体的主要发酵区域和下面为锥体的产物沉积区域;所述主要发酵区域与产物沉积区域的体积比为 8 1-12 1之间,主要发酵区域的高径比为2 1-3 1之间;所述主要发酵区域的上端设置排气口、冷凝水循环管路、接种口、取样口、补料口、电机和电极,所述主要发酵区域内设置有搅拌器和主要通气管道;所述产物沉积区域内设置有辅助通气管道,下端设置有排液口。进一步地,所述搅拌器为上下双层桨片,包括上层的消泡桨和下层的搅拌桨。进一步地,所述筛板上开设有等腰梯形孔,筛板上表面的的开孔率为3% _6%,下表面的开孔率为75%,等腰梯形孔的上端孔径在2mm-4mm之间,等腰梯形孔的下端孔径在 6mm-20mm之间,等腰梯形孔上端和下端孔径比在1 5_1 3之间,筛板厚度为10mm-15mm。
本发明要解决的另一技术问题是提供一种具有降低生产和分离成本,环境友好, 操作简单的生物反应器
为解决上述技术问题,本发明采用如下技术方案在生物反应器中加入灭菌后的发酵培养基,通过接种口加入培养好的种子液,以50mL/d-80mL/d的速度分批补加菜籽油, 发酵前5证-9他上下罐体同时通氧气,控制转速使溶氧保持在50 %以上,发酵至下端通气停止,3h4h后打开阀门,静滴排出沉降粗产物,同时以40mL/d-100mL/d的速度分批补充发酵液,最终可连续发酵3(Mi-322h,累计回收粗产物4. 75kg-6. 75kg,单位时间单位发酵罐体积的生产效率较单次分批发酵提高3倍以上,有效发酵时间延长了 4倍以上;将发酵废液离心后,取上清液与回收后的粗产物混合,混合后沉降分层池后,将下层产物回收到二次纯化产品收集罐;二次净化后的产品经过灭菌罐进行灭菌后,经70°C烘干至恒重,得到纯品槐糖脂2. 92kg-3. 96kg,
进一步地,发酵为在25-30°C、pH为3. 0-4. 0的条件下进行好氧发酵。
进一步地,培养基组分为葡萄糖130g/L_150g/L、酵母粉3g/L_10g/L和尿素lg/L。
进一步地,培养基组分为葡萄糖150g/L、酵母粉3g/L、蛋白胨0.7g/L、柠檬酸钠 5g/L、MgS04 · 7H20 4g/L、(NH4) 2S042g/L、KH2P041g/L、NaClO. lg/L 和 CaC12 · 2H20 0. lg/L0
进一步地,所述种子液为菌体经种子培养基在30°C培养48小时的菌体富集液,培养条件PH值为6 ;所述种子培养基的成分为葡萄糖100g/L、酵母粉10g/L和尿素lg/L。
本发明的生物反应器及其连续生产槐糖脂的方法,旨在通过把现有的分批发酵生产转变为连续生产,提高槐糖脂的产量;减少分离费用,比如相对于传统的分离过程,本发明完全不使用有机溶剂萃取,环境友好,没有产物的流失;分离操作的同时,可以顺带回收酵母副产品,不需要更多额外的操作及费用;整个流程操作简单,设备控制容易。本发明通过设计一种新的反应器实现了槐糖脂的连续生产,同时以新的分离方法为主线,设计了完整的槐糖脂高效、节能的连续生产、分离以及副产品回收的生产工艺,可以大大节约生产成本,为实现槐糖脂的大规模连续生产提供可能。
图1为本发明生物反应器的示意图2为本发明连续生产槐糖脂的方法的生产工艺流程框图。
本实施例中,参照图1,所述生物反应器,包括罐体,及设置在罐体上的加热套 14 ;所述罐体内设置有带梯形孔的筛板17,所述筛板17将罐体分隔成上面为柱体的主要发酵区域和下面为锥体的产物沉积区域;所述主要发酵区域与产物沉积区域的体积比为 8 1-12 1之间,主要发酵区域的高径比为2 1-3 1之间;所述主要发酵区域的上端设置排气口 10、冷凝水循环管路11、接种口 12、取样口 20、补料口 21、电机22和电极(未图示),所述主要发酵区域内设置有搅拌器和主要通气管道19 ;所述产物沉积区域内设置有辅助通气管道15,下端设置有排液口 16。
其中,所述搅拌器为上下双层桨片,包括上层的消泡桨13和下层的搅拌桨18。所述筛板17上开设有等腰梯形孔,筛板17上表面的的开孔率为3% _6%,下表面的开孔率为 75%,等腰梯形孔的上端孔径在2mm-4mm之间,等腰梯形孔的下端孔径在6mm-20mm之间,等腰梯形孔上端和下端孔径比在1 5-1 3之间,筛板厚度为10mm-15mm。这样的设计是因为,上表面孔径小可以有效阻止生产过程中菌体向下端沉降,下表面孔径大则有利于在通气条件下将沉积的菌体和物料返还上部分的主要发酵区域;产物沉积区域的辅助通气管路 15,可以在生产前期为产物沉积区域提供氧气的同时,起到加速传质的搅拌作用,在发酵后期,停止下端产物沉积区域的通气,使产物沉积区域成为利于产品沉积的相对静止区域;同时,筛板17的存在可以有效减缓产物排放时的涡旋,使罐内流体处于层流状态,静滴回收沉积的产物时,避免产物与发酵液的不必要返混。
如图2所示,连续生产槐糖脂的方法包括以下设备生物反应器1、离心机2、粗产品收集罐3、酵母收集罐4、发酵液上清液收集罐5、二次纯化产品收集罐6、灭菌罐7、烘干设备8和纯品储存罐9。
连续生产槐糖脂的方法为以生物反应器总高为0. km,柱体与锥体部分高度比为3 1,圆柱体罐体直径O.aii,筛板厚度10mm,梯形孔上下孔径比为1 3,上表面孔径为 3mm,有效容积为IOL的反应器为具体实施例,其中,主要通气管道19管内径为1cm,辅助通气管道15管内径为0. 8cm,上下均可分别随时停止或开始通气。生产实例如下
实施例1
以分批发酵时槐糖脂产量为90g/L的菌株1作为生产菌株为例。
将装置中加入6L灭菌后的发酵培养基,培养基组分为葡萄糖130g/L,酵母粉IOg/ L,尿素lg/L。通过接种口加入培养好的种子液,所述种子液为菌体经种子培养基在30°C培养48小时的菌体富集液,培养条件PH值为6 ;所述种子培养基的成分为葡萄糖100g/L、 酵母粉10g/L和尿素lg/L ;再以50mL/d的速度分批补加菜籽油。速度分批补加菜籽油。发酵前上下罐体同时通氧气,控制转速使溶氧保持在50%以上。发酵至下端通气停止,证后打开阀门,静滴排出沉降粗产物,同时以40mL/d的速度分批补充发酵液。最终可连续发酵30他,累计回收粗产物4. 75kg。单位时间单位发酵罐体积的生产效率较单次分批发酵提高3倍以上,有效发酵时间延长了 4倍以上。其中,发酵为在25-30°C、pH为3. 0-4. 0 的条件下进行好氧发酵。
将发酵废液离心后,取上清液与回收后的粗产物混合,混合后沉降分层池后,将下层产物回收到二次纯化产品收集罐;二次净化后的产品经过灭菌罐进行灭菌后,经70°C 烘干至恒重,得到纯品槐糖脂2. 92kg。采用这种分离工艺较传统的有机溶剂萃取分离工艺节省了 6升的乙酸乙酯,并且大大降低了相关的蒸馏能耗和冷凝用水,分离费用仅为传统工艺的1/4左右。同时,得到0. ^kg酵母副产品。
实施例2
以分批发酵时槐糖脂产量为120g/L的菌株2作为生产菌株为例。
将装置中加入6L灭菌后的发酵培养基,培养基组分为葡萄糖150g/L,酵母粉3g/L,蛋白胨 0. 7g/L,柠檬酸钠 5g/L,MgS04 · 7H20 4g/L,(NH4) 2S042g/L, KH2P041g/L, NaCl 0. lg/L,CaC12.2H20 0. lg/L。通过接种口加入培养好的种子液,所述种子液为菌体经种子培养基在30°C培养48小时的菌体富集液,培养条件PH值为6 ;所述种子培养基的成分为 葡萄糖100g/L、酵母粉10g/L和尿素lg/L ;再以80mL/d的速度分批补加菜籽油。发酵前 55h上下罐体同时通氧气,控制转速使溶氧保持在较高水平。发酵至下端通气停止,池后打开阀门,静滴排出沉降粗产物,同时以100mL/d的速度分批补充发酵液。最终可连续发酵32池,累计回收粗产物6. 75kg。单位时间单位发酵罐体积的生产效率较单次分批发酵提高3. 5倍,有效发酵时间延长了 4倍以上。
将发酵废液离心后,取上清液与回收后的粗产物混合,混合后沉降分层池后,将下层产物回收到二次纯化产品收集罐;二次净化后的产品经过灭菌罐进行灭菌后,经70°C 烘干至恒重,得到纯品槐糖脂3. 96kg。采用这种分离工艺较传统的有机溶剂萃取分离工艺节省了 8升的乙酸乙酯,并且大大降低了相关的蒸馏能耗和冷凝用水,分离费用仅为传统工艺的1/4左右。同时,得到0. 35kg酵母副产品。
本发明的生物反应器及其连续生产槐糖脂的方法,优点在于通过设计一种新型的生物反应器把现有的分批发酵的生产方式转变为连续生产方式,大大提高了培养基的利用率、设备的使用效率;通过利用发酵上清液与粗产物重新混合,进一步纯化槐糖脂,由于发酵上清液是槐糖脂的饱和溶液,所以减少了产物的流失,同时相比于使用有机溶剂萃取的传统方法,由于完全不使用有机溶剂萃取,本发明节约能耗,环境友好,成本低廉;分离操作的同时,可以顺带回收酵母副产品,不需要更多额外的操作及费用;整个生产工艺流程完整,操作步骤简单,设备控制容易。
以上已将本发明做一详细说明,以上所述,仅为本发明之较佳实施例而已,当不能限定本发明实施范围,即凡依本申请范围所作均等变化与修饰,皆应仍属本发明涵盖范围内。
本发明的生物反应器及其连续生产槐糖脂的方法,流加补进发酵液的同时排液口静滴回收产品,工艺的主要过程如下发酵废液经过离心机,离心后回收下层沉降的酵母副产品;离心后的上清液与静滴回收的粗产品混合,沉降分层2-5h后,将下层产物回收到二次净化产品收集罐;二次净化后的产品经过灭菌锅进行灭菌后,直接贮藏或者在烘干塔中经55-75℃烘干至恒重后,进行贮藏。
生物反应器及其连续生产槐糖脂的方法
- 专利详情
- 全文pdf
- 权力要求
- 说明书
- 法律状态
查看更多专利详情
下载专利文献
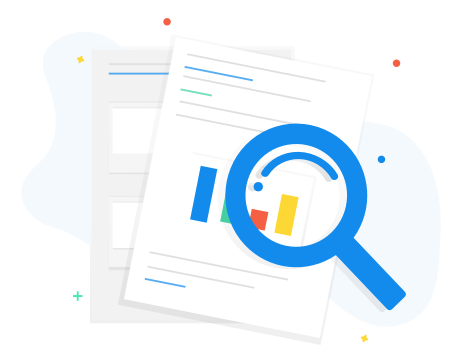
下载专利
同类推荐
-
马丁·哈德, 格哈德·森格山下秀人, 饭岛好隆张亚锋, 胡长坤张亚锋, 胡长坤马欣欣
您可能感兴趣的专利
-
马欣欣彭雅莉, 胡飞彭雅莉, 胡飞中西惠, 棚桥一裕崔正忠, 韩芳吴海燕
专利相关信息
-
周泽良周泽良