专利名称:一种食用植物油脱胶工艺及其应用的制作方法所有食用植物油的生产都是要通过毛油脱胶、脱杂、脱酸、脱溶、干燥、脱色、脱臭及冬化脱蜡等精炼工序加工而来的,由于毛油种类及成品油等级要求的不同,加工过程的工序工艺可能略有不同,然而无论毛油的种类指标及成品油等级要求有何不同,其中脱胶工段在各个工艺中都是必不可少的。当前行业内存在的脱胶工艺包括水脱胶,特殊脱胶及酶法脱胶。其中,水脱胶的缺陷在于无法脱除非水化磷脂;特殊脱胶的缺陷在于磷脂脱除不彻底,含磷量大于20ppm ;酶法脱胶的脱除效果好,但缺陷在于酶的价格偏高,相对生产成本高。脱胶工艺效果的好坏会直接或间接的影响其它工段的工艺效果。油脂精炼生产线如果其单纯脱胶工段的效果不理想,就必须通过中和脱酸或者通过脱色多加活性白土的辅助脱胶效果来达到较为完全的脱胶效果,然而这种不得已的辅助脱胶加工势必降低产品得率,增加原辅料及中性油的消耗,而且还会增加废水排污的可能性。目前食用植物油物理精炼工艺仅仅是用在含胶量低的棕榈油的加工上。对于菜籽油大豆油等含磷量高尤其是非水化磷脂含量高的籽油,由于没有经济可靠的脱胶工艺,大型工业化生产为了达到必须的脱胶效果而基本上都要采用化学精炼工序。
本发明的目的就是克服现有技术中的缺陷,提供一种食用植物油的脱胶工艺及其应用。本发明首先公开了一种食用植物油的脱胶工艺,为先将毛油与酸反应将毛油中的非水化磷脂转化为水化磷脂,而后经水化凝聚胶团,再经离心分离获得脱胶油。具体的,所述脱胶工艺包括下列步骤1)转化将温度为50--70°C的毛油与占毛油重量0.05-0. 5%的柠檬酸、磷酸、苹果酸或草酸混合后,在酸反应罐中搅拌反应15-30分钟,完成非水化磷脂转化为水化磷脂的反应,得到转化混合物;2)水化将转化混合物与20-50°C重量为毛油中磷脂重量的1. 5-2. 5倍的软水混合后,调温至20-45°C,在水化反应罐中搅拌反应45-150分钟,完成水化反应,得到水化混合物;3)离心分离将水化混合物加热至75_90°C后经离心机离心分离,分离得到的轻相分离物经真空脱溶干燥后获得脱胶油。更具体的步骤1)中,所述毛油可以为任意食用植物油的毛油,包括但不限于毛菜籽油、毛豆油、葵花籽毛油、玉米胚芽毛油,毛米糠油(也称毛稻米油)。较佳的,所述毛油的含磷量为100-700ppm(mg/kg),含杂量< 0. 2wt%。毛油可采用板式或列管换热器或加热器加热至50--70°C。所用的酸可选自柠檬酸,磷酸,苹果酸,草酸。较佳的,柠檬酸、磷酸、苹果酸或草酸占毛油重量0. 15-0. 5%o如本发明实施例所列举的,酸可先配置酸的水溶液后,按比例加入。例如加入 50wt%的柠檬酸水溶液。所述酸反应罐中搅拌反应的搅拌速度一般控制为45-60转/分钟。经步骤1),毛油中,非水化磷脂转化为水化磷脂的反应率> 99. 5%。步骤2)中,所述软水为低于10度(德国度)的软水。所述转化混合物与所述软水混合后,可采用板式换热器冷却调温。所述水化反应罐中搅拌反应的搅拌速度一般控制为35-75转/分钟,水化反应停留时间可为45-150分钟,一般控制为45-120分钟。水化反应的搅拌速度及反应时间可调, 可根据毛油种类含磷量及反应温度调整。一般而言,毛油含磷量高或者反应温度高,可适当搅拌快些,反应温度低反应时间长些。步骤3)中,所述经水化的混合物可经板式或列管换热器或加热器加热至75-90°C。较佳的,经水化的混合物先通过板式换热器与进水化反应罐的混合物换热,再通过板式或列管换热器加热至75-90°C,此设计可进一步节能。所述轻相分离物可为经离心机一次离心分离获得的第一轻相分离物或经离心机两次离心分离获得的第二轻相分离物。所述经离心机两次离心分离的方法具体为将水化混合物加热至75_90°C后经第一离心机离心分离获得第一轻相分离物,将所述第一轻相分离物与75-90°C的占所述第一轻相分离物重量2. 5-5%的软水混合,油水混合物进入水洗停留罐水洗10-30分钟后,再经第二离心机离心分离,获得第二轻相分离物。在毛油含杂量大,毛油磷脂含量相对较高,对脱胶油含磷量要求相对不高及单台离心机分离能力不足情况下,可采用两次离心分离。在仅生产四级脱胶油及壹台离心机分离能力充足的情况下,只需一次离心分离。所述两次离心分离中,油水混合物进入水洗停留罐水洗时,可同时伴随搅拌,搅拌速度可快可慢,一般可控制为0-60转/分钟。所述软水为低于10度(德国度)的软水。离心分离所用的离心机可采用碟片离心机。较佳的,为了免除离心分离后重相分离物(即废水)的处理,可将经第二离心机离心分离的重相分离物作为步骤2)中的软水来源。此步骤不仅可节约用水,也可减少废水的处理与排放。进一步的,轻相分离物真空脱溶干燥前,加热至75_120°C,较佳为85_115°C。此步骤可采用板式或列管换热器或加热器加热。如果未经加热,轻相分离物已经达到温度要求 (75°C以上),则此步骤可省略。较佳的,所述真空脱溶干燥时的残压为25-lOOmpa。可干燥至水分含量 < 0. Iwt%。脱溶至残溶降至< 30ppm。真空脱溶干燥可采用真空干燥器进行,如喷雾干燥型或挡板溢流型真空干燥器。本发明的脱胶方法通过酸反应转换非水化磷脂,再水化凝聚胶团,通过离心机分离(转化-水化-离心分离),获得的脱胶油含磷量即可达到国标280°C加热实验合格,脱胶油的含磷量指标< lOppm,不必经过化学精炼的中和工段而直接进入脱色脱臭工段,可完全采用物理精炼的工艺路线生产一级油。本发明的食用植物油的脱胶工艺可用于食用植物油的精炼。本发明还进一步公开了一种食用植物油精炼工艺,包括下列步骤a.将毛油先采用本发明所述脱胶工艺脱胶获得脱胶油;b.脱胶油不经中和脱酸直接脱色获得脱色清油;c.脱色清油经脱酸脱臭后,经冷却及精滤获得成品RBD油(精炼脱色脱臭油)。具体的,步骤a)中,所述脱胶油含磷量< lOppm,水分含量< 0. Iwt %。若脱胶油水分含量> 0. lwt%,则步骤a)增加干燥步骤,使得脱胶油水分含量 < 0. lwt%。步骤b)中,所述脱色可以采用一次脱色工艺,为降低白土消耗也可以采用二次脱色工艺(也称预脱复脱工艺)。较佳的,所述脱色获得脱色清油的方法具体为将所述脱胶油加热至105-120°C, 在50-150mbar绝对压力下加入占所述脱胶油重量0. 5-2. 0%的活性白土,经25-45分钟的脱色反应后,依次经过滤和精滤获得脱色清油。脱胶油可采用板式或列管换热器或加热器加热至105-120°C。过滤可采用过滤机,精滤可采用保险过滤器。步骤c)中,较佳的,脱酸脱臭时,汽提气添加重量为脱色清油重量的0. 3-1. 5 %,更佳为 0. 3-1. 0%。具体的,所述脱色清油脱酸脱臭的方法可以选自以下任一I、将脱色清油加热至240-260°C后,经脱酸脱臭塔脱酸脱臭;II、将脱色清油加热至240-260°C后,先经脱酸塔脱酸,再经脱臭塔脱臭;III、将脱色清油加热至240-260°C后,先经脱臭塔脱臭,再经脱酸塔脱酸;较佳的,方法I)中,所述脱酸脱臭塔的脱酸部分采用规整填料塔结构,脱臭部分采用板式塔结构。所述脱酸脱臭塔的填料塔可在先、在后或者在中间。较佳的,进塔脱酸脱臭前,脱色清油FFA (游离脂肪酸)含量为0. 05wt % -4wt %, 脱酸和脱臭时的绝对压力< 2. 5mbar,脱酸脱臭总时间为45min—120min (其中,脱酸时间较短,一般不超过5min)。较佳的,脱色清油的加热方法为将脱色清油首先与经脱酸脱臭出塔的高温油换热,再经过高压蒸汽或其它热源加热至240-260°C。此措施,可进一步节能。本发明的食用植物油精炼工艺依次经脱胶、脱色、脱酸脱臭(蒸馏法去酸)获得 RBD成品油,整个过程无单独碱炼中和脱酸步骤,为物理精炼。CN 102533441 A本发明的有益效果本发明的食用植物油脱胶工艺适用于任何植物油的脱胶,特别对于含磷量高尤其是非水化磷脂含量高的籽油,脱胶效果优良的特点更加突出,这不单是在油脂脱胶方面的创新,而且该种脱胶工艺的进步带动了产生新型的油脂加工物理精炼技术。本发明的食用植物油精炼工艺摒弃化学精炼而采用物理精炼的优势在于1)可以提高成品油的得率约(菜籽油提高得率0.8% -1 %、大豆油提高得率 0. 6% —0. 8% );2)没有了中和水洗水废水的排放(通常化学精炼水洗污水排量占量的6%左右);3)采用物理精炼没有了含磷皂脚的处理费用,提高了高价值副产品脱臭脂肪酸的产量与质量(脂肪酸产量提高约菜籽油1%,豆油0.8%,脂肪酸的FFA由50%含量提高至 75% ),其它白土等辅料使用与化学精炼相当。检测脱胶油含磷量6ppm,280°C加热实验无析出,脱胶油残溶22ppm,脱胶油FFA 含量0. 45%。实施例5原料加拿大卡诺拉毛菜籽油,酸价1. 8mgK0H/g,含磷量650ppm,含杂0. 1 %。采用下列精炼工艺精炼采用实施例1的脱胶工序制备脱胶油(水分< 0. ),采用板式或列管换热器调整温度至110°c,在IOOmbar绝对压力下加入占脱胶油重量活性白土,经过35min的脱色反应,进入过滤机过滤,出来的清油再经过保险过滤器精滤,脱色清油进入脱酸脱臭工段(汽提气添加量,油重的0. 8% ),脱色清油首先与脱臭塔出来成品油换热,再经过高压蒸汽或其它热源加热至258°C,进入脱酸脱臭塔,进入脱酸脱臭塔的脱色清油FFA含量在 1. 2wt%,脱酸脱臭的绝对压力2. 2mbar,脱臭时间在90min,出来的脱酸脱臭油与进塔的脱色清油节能换热,再经过最后换热器冷却及精滤器即得到成品RBD油(最终脱色脱臭成品油)。检测采用相关国标标准检测(酸值检验按GB/T 5530执行检测,加热试验按 GB/T 5531执行,水分及挥发物检验按GB/T 55 执行)色泽检验按GB/T 5525-1985中的第2章执行,烟点检验按GB/T 177561999附录B执行),成品油FFA含量为0. 035%,成品油色泽Rl. 1Y12,成品油烟点218°C,以成品油得率=成品油质量/毛油质量计算成品油得率为95. 1% ο实施例6原料加拿大卡诺拉浸出毛菜籽油(非水化磷脂含量为植物油中之最),酸价 1. 8mgK0H/g,含磷量 650ppm。采用下列精炼工艺精炼采用实施例1的脱胶工序制备脱胶油(水分< 0. 1% ),采用板式或列管换热器调整温度至105°C,在50mbar绝对压力下加入占脱胶油重量2. 0%活性白土,经过45min 的脱色反应,进入过滤机过滤,出来的清油再经过保险过滤器精滤,脱色清油进入脱酸脱臭工段(汽提气添加量,油重的0. 3 % ),脱色清油首先与脱臭塔出来成品油换热,再经过高压蒸汽或其它热源加热至240°C,进入脱酸脱臭塔,进入脱酸脱臭塔的脱色清油FFA含量在 1. 2wt%,脱酸脱臭的绝对压力< 2. 5mbar,脱臭时间在45min,出来的脱酸脱臭油与进塔的脱色清油节能换热,再经过最后换热器冷却及精滤器即得到成品RBD油(最终脱色脱臭成品油)。检测成品油FFA含量为0. 045%,成品油色泽Y10R0. 8,成品油烟点216°C,成品油得率为95. 45%。实施例7原料加拿大卡诺拉毛菜籽油(非水化磷脂含量为植物油中之最),酸价 1. 8mgK0H/g,含磷量 650ppm。采用下列精炼工艺精炼采用实施例1的脱胶工序制备脱胶油(水分< 0. ),采用板式或列管换热器调整温度至120°c ),在150mbar绝对压力下加入占脱胶油重量0. 5%活性白土,经过25min 的脱色反应,进入过滤机过滤,出来的清油再经过保险过滤器精滤,脱色清油进入脱酸脱臭工段(汽提气添加量,油重的1 % ),脱色清油首先与脱臭塔出来成品油换热,再经过高压蒸汽或其它热源加热至260°C,进入脱酸脱臭塔,进入脱酸脱臭塔的脱色清油FFA含量在 0. 05% --#t%,脱酸脱臭的绝对压力< 2. 5mbar,脱臭时间在120min,出来的脱酸脱臭油与进塔的脱色清油节能换热,再经过最后换热器冷却及精滤器即得到成品RBD油(最终脱色脱臭成品油)。 检测成品油FFA含量为0. 03%,成品油色泽Y12R1. 2,成品油烟点218°C,成品油得率为95.8%。
本发明涉及一种食用植物油脱胶工艺及其应用。本发明的食用植物油的脱胶工艺,为先将毛油与酸反应,将毛油中的非水化磷脂转化为水化磷脂,而后经水化凝聚胶团,再经离心分离获得脱胶油。本发明的食用植物油的脱胶工艺可用于食用植物油的精炼。本发明还进一步公开了一种食用植物油精炼工艺,依次经本发明的脱胶工艺、脱色及脱酸脱臭获得RBD成品油。本发明的食用植物油脱胶工艺适用于任何植物油的脱胶,特别对于含磷量高尤其是非水化磷脂含量高的籽油,脱胶效果优良,这不单是在油脂脱胶方面的创新,而且脱胶工艺的进步带动了产生新型的油脂加工物理精炼技术。
一种食用植物油脱胶工艺及其应用制作方法
- 专利详情
- 全文pdf
- 权力要求
- 说明书
- 法律状态
查看更多专利详情
下载专利文献
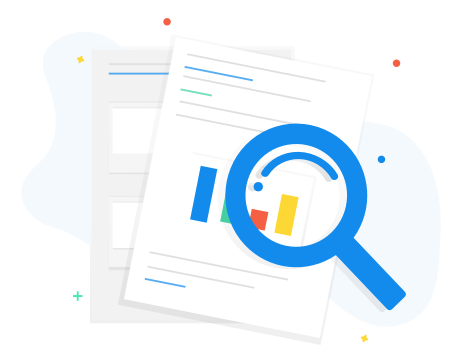
下载专利
同类推荐
-
颉二旺, 张维程继红, 王文平佘志清
您可能感兴趣的专利
-
颜钢锋颜钢锋颜钢锋颜钢锋
专利相关信息
-
颜钢锋颜钢锋颜钢锋颜钢锋颜钢锋颜钢锋颜钢锋