专利名称:镍基超耐热合金的制品及制造方法本发明介绍γ′强化的镍基超耐热合金锻坯和锻件的制造法,其开始用料为铸锭。镍基超耐热合金广泛用于燃气轮发动机。它的一种用途是用于蜗轮盘。随着发动机性能普遍的进展,对蜗轮盘材料的性能要求也已提高。早期发动机的蜗轮盘材料多半采用锻钢和由钢派生出的合金锻件。但这些材料很快被第一代的镍基超耐热合金取代,例如瓦斯帕洛伊镍基超耐热合金,即使这些合金的锻造往往有某些困难,但是它们是能够锻造的。γ′相能大大地增加镍基超耐热合金的强度。因而镍基超耐热合金的发展方向是增加可提高强度的γ′体积百分率。用于早期发动机蜗轮盘的瓦斯帕洛伊(Waspaloy)合金大约含25%体积的γ′相,而新近研制的蜗轮盘合金大约含40-70%的γ′相。然而增加γ′相的体积百分率会降低可锻性。可以用铸锭原料锻造瓦斯帕洛伊合金材料,但是新近研制的较高强度的盘材不能可靠地通过锻造,并且要求采用较昂贵的粉末冶金技术来生产一种蜗轮盘预制坯,它可以被锻造而且还可以经济地机械加工成成品尺寸。美国专利号3,529,503和4,081295所介绍的方法是一种已获得基本成功的生产发动机蜗轮盘的粉末冶金法。该方法业已证明采用粉末冶金原料是十分成功的,但采用铸造原料不太成功。涉及蜗轮盘材料锻造的其他专利有美国专利号3,802,983、3,975,219、4,110,131、4,574,015和4,579,602。本发明在某些方面是美国专利号4,574,015方法的发展。总之,向高强度盘材发展的方向引起一些加工困难,这些困难只得求助于昂贵的粉末冶金技术来解决。本发明的一个目的是介绍一种很容易锻造高强度超耐热合金铸材的方法。本发明的另一个目的是提出一种用铸造的超耐热合金材料生产锻坏的方法,这种铸造的超耐热合金含有超过大约40%体积的γ′相,并且在其他情况下必定是不可锻造的。本发明的又一个目的是揭示一种结合有热处理、挤压和锻造的组合方法,该组合法将生产出无孔隙的完全再结晶的,具有均匀细晶粒显微组织的超耐热合金制品。本发明的再一个目的是提供一种完全可锻造的镍基超耐热合金锭料,该锭料具有过时效的γ′形态和完全再结晶的显微组织,γ′的平均大小约超过2微米。γ′微粒在γ基体中的分布大大地提高镍基超耐热合金的强度。γ′相是以Ni3Al化合物为基础的,其中例如Ti和Nb的各种合金元素可部分地代替Al。而象No、W、Ta和Nb一类的难熔元素则可强化γ基体相,并且Cr和Co的添加剂通常是和次要元素C、B和Zr一起存在的。
表Ⅰ列出了各种热加工成形的超耐热合金的一般成分,可按常规用铸造原料锻造瓦斯帕洛伊合金。其余合金通常是用粉末成型,或采用直接的等静压热压压实,或者由锻造压实粉末预制坯;虽然有时不用粉末冶金技术可锻造超耐热镍合金,但是由于有高的γ′含量,因此锻造这些合金成分的铸锭料是不现实的。
表Ⅰ合金,以及似乎可用本发明处理的其他合金的成分范围为(重量百分数);5-25%Co、8-20%Cr、1-6%Al、1-5%Ti、0-6%Mo、0-7%W、0-5%Ta、0-5%Re、0-2%Hf、0-2%V、0-5Nb、其余部分主要是与常量的次要元素C、B和Zr在一起的Ni。Al和Ti含量的总和通常为4-10%,Mo+W+Ta+Nb含量的总和为2.5-12%。本发明可广泛地用于γ′含量范围最高达大约75%体积的镍基超耐热合金,而且对于含40%以上和最好超过50% γ′相体积的,并且因此在其他情况下用传统(非粉末冶金)技术不可锻造的合金特别有效。
就铸造的镍基超耐热合金而言,有两种形式的γ′相共晶的和非共晶的。在凝固过程中产生共晶的γ′,而在凝固以后的冷却过程中由于沉淀而产生非共晶的γ′。发现共晶的γ′相主要在晶粒边界处,并且通常具有大的颗粒大小,大概最大可达100微米。在晶粒内发现提供合金大部分强化的非共晶的γ′相,并且其典型大小为0.3-0.5微米。
通过把合金材料加热到高温,可将γ′相溶解或固溶到固溶体中。某一种相进入固溶体的温度是该相的溶线温度。在某一个温度范围内加热(或冷却)时非共晶的γ′发生固溶(或沉淀)。在本文所公开的内容中,溶线开始的术语将用来描述可观察到的固溶开始的温度(它被定义为一种光学金相的测定温度,在此温度时,缓慢冷却到室温时出现的大约5%体积的γ′相固溶到固溶体中),溶线终止的术语表示固溶基本完成的温度(再次用光学金相测定)。查阅溶线温度时,对于没有附加以开始/终止的溶线温度可理解为溶线的终止温度。
共晶和非共晶型的γ′产生不同的形状,具有不同的成分和溶线温度。非共晶γ′的溶线开始和终止的温度低于共晶γ′的溶线温度,一般约在28℃-83℃(50°-150°F)。在MERL76合金成分中,非共晶γ′的溶线开始温度为1121℃(2050°F),溶线终止温度为1196℃(2185°F)。共晶γ′的溶线开始温度为1176℃(2170°F)和该γ′溶线终止温度为1218℃(2225°F)[因为开始熔化温度为1196℃(2185°F),所以如果没有部分熔化,该共晶的γ′就不能够完全溶解]。
本发明最广泛的形式包括把材料挤压成细而完全再结晶的组织,把该再结晶材料锻造成需要的形状,然后等静压热压该热加工材料。通常该材料在挤压前将给予过时效热处理。
图1是表示本发明处理工序流程图,它包括另一种可供选择的处理工序,通过对图1的研究可以正确地评估本发明的方法。根据图1的流程图,原料是细晶粒的铸锭,可对该铸锭施加任选的等静压热压预处理以闭合气孔,并进行某些均匀化处理或预先热处理。为了产生粗的γ′颗粒度,最好按照美国专利号4,574,015的方法对该材料进行过时效热处理。为了把表面裂纹减少到最低限度,最好用护套或罐把热处理过的铸锭首先密封好,然后热挤压该热处理过的铸锭。于是在最佳的本发明方法中,对该材料进行等静压热压而产生一种以后可以锻造成成品型材的锻坯。在另一种可供选择的处理工序中,在等静压热压之前先锻造挤压过的材料。在下面的讨论中,将提到各种处理工序的说明。
从该说明书、
权利要求
1.产生一种镍基超耐热合金锻坯的方法,其特征在于包括如下工序a.提供一种细晶粒的铸锭,b.对铸锭进行热处理以产生一种过时效的非共晶的γ′显微组织,c.以足以产生一种完全再结晶的细晶粒显微组织的一种面积减缩率挤压热处理过的铸锭,d.在足以防止晶粒明显长大的低温度下,对挤压过的材料进行等静压热压,以闭合所有的孔隙和气孔,由此所得到的制品将具有细的晶粒度和粗的γ′大小,并且将适合于以后的锻造工序。
2.用γ′相体积含量约大于40%的细晶粒铸锭生产一种镍基超耐热合金锻件的方法包括下如工序a,对铸锭进行热处理以产生一种过时效的非共晶γ′颗粒的显微组织,b,以足以产生一种完全再结晶的细晶粒显微组织的一种面积减缩率挤压处理过的铸锭,c,在足以防止晶粒明显长大的低温度下,对挤压过的材料进行等静压热压以闭合孔隙和气孔,d,采用加热的模具锻造该挤压过的材料,
3.用γ′相体积含量约大于40%的细晶粒铸锭生产一种镍基超耐热合金锻件的方法包括如下工序a,对铸锭进行热处理以产生一种过时效的非共晶γ′颗粒显微组织,b,以足以产生一种完全再结晶的细晶粒显微组织的一种面积减缩率挤压热处理过的铸锭,c,采用加热的模具锻造该挤压过的材料,d,在足以防止晶粒明显长大的低温度下,对锻造过的材料进行等静压热压以闭合孔隙和气孔。
4.产生一种镍基超耐热合金锻坯的方法包括如下工序a,提供一种细晶粒的铸锭,b,用约大于4∶1的减缩比挤压热处理过的铸锭以产生完全再结晶的细晶粒显微组织,c,在足以防止晶粒明显长大的低温度下,对挤压过的材料进行等静压热压以闭合全部孔隙和气孔,由此所得到的制品具有细的晶粒度和粗的γ′大小,并且将适合于以后的锻造工序。
5.用γ′相体积含量约大于40%的细晶粒铸锭生产一种镍基超耐热合金锻件的方法包括如下工序a,用约大于4∶1的减缩比挤压热处理过的铸锭以产生完全再结晶的细晶粒显微组织,b,在足以防止晶粒明显长大的低温度下,对挤压过的材料进行等静压热压以闭合孔隙和气孔,c,采用热的模具锻造该材料。
6.用γ′相体积含量约大于40%的细晶粒铸锭生产镍基超耐热合金锻件的方法包括如下工序a,用约大于4∶1的减缩比挤压热处理过的铸锭以产生完全再结晶的细晶粒显微组织,b,采用加热的模具锻造挤压过的材料,c,在足于防止晶粒明显长大的低温度下,对锻造过的材料进行等静压热压以闭合孔隙和气孔。
7.根据权利要求
1-6中的任何1项所述的方法,其特征在于铸锭的成分为(重量百分)5-25%Co、8-20%Cr、1-6%Al、1-5%Ti、0-6%Mo、0-7%W、0-5%Nb、0-5%Ta、0-5%Re、0-2%Hf、0-2%V、0-0.5%C、0-0.15%B、0-0.15%Zr,其余基本为镍。
8.根据权利要求
1-6中的任何1项所述的方法,其特征在于原始晶粒度(在铸锭表面上的)不大于约3,17毫米(1/8英寸)。
9.根据权利要求
1-3中的任何1项所述的方法,其特征在于该热处理工序包括以小于大约8.3℃/小时(15°F/小时)的速度,把该材料从至少有40%(体积)的非共晶γ′相溶于基体的温度冷却到该非共晶γ′溶线开始温度以下的温度,从而大大地粗化该γ′颗粒。
10.根据权利要求
1-3中的任何1项所述的方法,其特征在于,在挤压前罐装该材料。
11.根据权利要求
1-3中的任何1项所述的方法,其特征在于,用大于约2.5∶1的面积减缩率挤压该材料。
12.根据权利要求
1-3中的任何1项所述的方法,其特征在于,再结晶的晶粒度为美国材料试验协会标准ASTM8-10级或更细。
13.根据权利要求
1-3中的任何1项所述的方法,其特征在于,用大于约3.5∶1的面积减缩率挤压该材料。
14.根据权利要求
1-3中的任何1项所述的方法,其特征在于,热处理后γ′的颗粒度约大于1.5微米。
15.根据权利要求
1-3中的任何1项所述的方法,其特征在于热处理后γ′的颗粒度约大于4微米。
本文介绍一种由细晶粒超耐热合金的铸件转换为一种锻件的方法,该锻件具有相当于那些用粉末冶金处理所得制品的机械性能。对铸造材料进行挤压和锻造。使用等静压热压来闭合气孔。
镍基超耐热合金的制品及制造方法
- 专利详情
- 全文pdf
- 权力要求
- 说明书
- 法律状态
查看更多专利详情
下载专利文献
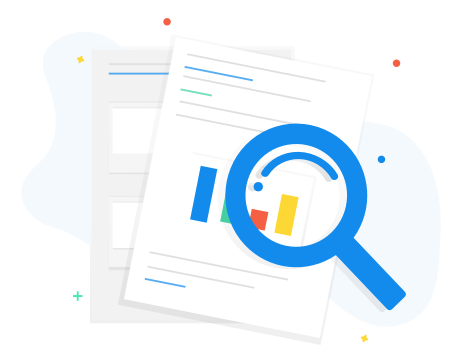
下载专利
同类推荐
-
保罗·达米安·吉纳鲁克斯, 丹尼尔·弗朗西斯·保隆尼斯保罗·达米安·吉纳鲁克斯, 丹尼尔·弗朗西斯·保隆尼斯保罗·达米安·吉纳鲁克斯, 丹尼尔·弗朗西斯·保隆尼斯保罗·达米安·吉纳鲁克斯, 丹尼尔·弗朗西斯·保隆尼斯王新, 王桂英J·H·阿伦斯J·H·阿伦斯
您可能感兴趣的专利
-
S·W·卡森李峤玲G·M·里克尔, R·J·赛勒R·J·赛勒, W·C·安卡洛三世E·W·小利法特克里斯·埃夫斯塔西奥斯·豪斯曼克雷德斯, 卡尔-路德维格·吉布斯
专利相关信息
-
克里斯·埃夫斯塔西奥斯·豪斯曼克雷德斯, 卡尔-路德维格·吉布斯蒂莫·皮沃斯基, 贝恩德·威尔维斯蒂莫·皮沃斯基, 贝恩德·威尔维斯丘云灵, 熊玉李宗武吴健, 徐刘彬阿德里亚那·布里西奥, 阿德里亚那 布里西奥