具有复杂型面的高强度复合材料骨软骨支架的制备方法[0002]关节疾病正影响着全球约4亿患者的生活,中国骨关节病患者约占30%,由于退变、创伤、炎症等因素破坏关节软骨和其下方的软骨下骨板的结构与功能,导致关节功能减退或丧失。虽然临床上已有对小面积的骨软骨缺损的治疗方法,但是大段骨软骨缺损的修复治疗仍然是医学界的一个国际性难题。[0003]已有的高强度水凝胶、生物陶瓷、高分子复合材料具有较高的力学性能和良好的生物学性能。因此,将高强度水凝胶与陶瓷等材料复合制造的骨软骨组织工程支架为上述问题的解决提供了新的思路。但是具有复杂型面的支架的复合制备过程中存在着软材料复杂型面成型难,外观形貌难控制的问题。是因为现有的方法是先完成水凝胶块制备,然后通过后期加工成所需要的形状,而水凝胶的高含水性导致其后期的复杂形貌加工成型困难,即便是通过模具完成了水凝胶复杂型面的成型,其与陶瓷等硬材料的稳定地结合仍然是个难题。
[0004]本发明的目的在于克服上述现有技术的缺点,提供了一种具有复杂型面的高强度复合材料骨软骨支架的制备方法,该方法在制备具有复杂型面的高强度复合材料骨软骨支架的过程中复杂型面成型容易。[0005]为达到上述目的,本发明所述的具有复杂型面的高强度复合材料骨软骨支架的制备方法,其特征在于:包括以下步骤:[0006]1)绘制骨的三维立体模型,并绘制软骨的第一三维立体模型,再根据软骨的第一三维立体模型绘制软骨的第二三维立体模型,其中,软骨的第一三维立体模型的厚度大于软骨的第二三维立体模型的厚度,然后再根据软骨的第一三维立体模型制备第一模具,并根据软骨的第二三维立体模型制备第二模具;[0007]2)在骨的三维立体模型中绘制发散式贯通管道模型,再根据所述骨的三维立体模型及发散式贯通管道模型通过生物陶瓷材料制备陶瓷骨支架,然后将连接介质穿过陶瓷骨支架中的发散式贯通管道并伸出到所述发散式贯通管道外,再将粘结介质溶液注入到所述发散式贯通管道中,当粘结介质溶液凝固后,连接介质与陶瓷骨支架相连接,得复合材料骨支架; [0008]3)将复合材料骨支架的下端面放入到第二模具中,固定后,将第一种水凝胶溶液注入到第二模具中,固化后,成型为第一层水凝胶,再将带有第一层水凝胶的复合材料骨支架放置到第一模具中,固定后,注入第二种水凝胶溶液,浸泡后固化成型,得具有复杂型面的高强度复合材料骨软骨支架。[0009]步骤I)中第一三维立体模型的厚度为第二三维立体模型的厚度的3-5倍。
[0010]步骤2)中连接介质的下端伸出到发散式贯通管道外I~2mm。
[0011]步骤3)中浸泡的时间为24~26h。
[0012]步骤3)中复合材料骨支架与第二模具及第一模具分别通过第一螺栓及第二螺栓固定。
[0013]所述第一螺栓及第二螺栓的长均为55-60mm,直径均为3_4mm。
[0014]所述第一模具及第二模具均为开合结构,第一模具的上端及第二模具的上端均设有浇冒口,开合结构的侧面均设有四个通孔,所述通孔的直径为3-4_,开合结构的开合面上设有密封结构,所述密封结构由第一凸起及沟槽构成,密封结构位于通孔与软骨的成型面之间,其中,所述三角形结构为等边三角形结构,三角形结构的边长为2-3mm。
[0015]所述发散式贯通管道包括上部结构及下部结构,上部结构包括圆柱型结构及设于圆柱型结构下端的半球体结构,下部结构由中心管道及若干组管道组成,任意一组管道中各管道的轴线与半球体结构表面的交点均匀分布于圆上,各组管道对应圆的圆心均位于圆柱型结构的轴线上,且相邻两个圆的圆心距为固定值,各管道的轴线相交于半球体结构的球心处,中心管道的轴线与圆柱型结构的轴线相重合。
[0016]所述下部结构包括7-9组管道,半球体结构的直径为9_13mm,各组管道中管道的数目为2-26个,每个管道的直径为l_3mm。 [0017]所述复合材料骨支架的侧面设有第二凸起。
[0018]本发明具有以下有益效果:
[0019]本发明提供的具有复杂型面的高强度复合材料骨软骨支架的制备方法在制备具有复杂型面的高强度复合材料骨软骨支架的过程中,先得到骨的三维立体模型及软骨的第一三维立体模型,再根据软骨的第一三维立体模型绘制软骨的第二三维立体模型,然后再根据软骨的第一三维立体模型及软骨的第二三维立体模型制备第一模具及第二模具,同时在骨的三维立体模型内绘制发散式贯通管道模具,再根据骨的三维立体模型及发散式贯通管道模具得陶瓷骨支架,并将连接介质穿过陶瓷骨支架上的发散式贯通管道,再通过粘结介质将连接介质与陶瓷骨支架相连接,然后再根据第一模具、第二模具及陶瓷骨支架通过第一种水凝胶溶液及第二种水凝胶溶液通过逐层成型的方法得到具有复杂型面的高强度复合材料骨软骨支架,操作简单、方便,易于成型,并且成型精度高,表面形貌好,且制备的具有复杂型面的高强度复合材料骨软骨支的强度好,解决了复杂型面软骨支架成型难及与任意曲面的陶瓷支架结合困难的问题。
[0020]图1为本发明中陶瓷骨支架的结构示意图;
[0021]图2为本发明制备过程中的结构示意图。
[0022]其中,I为第二模具、2为连接介质、3为第二凸起、4为陶瓷骨支架、5为第一层水凝胶、6为圆柱型结构、7为半球体结构、8为发散式贯通管道、9为通孔。
[0023]下面结合附图对本发明做进一步详细描述:[0024]参考图1及图2,具有复杂型面的高强度复合材料骨软骨支架的制备方法包括以下步骤:
[0025]I)绘制骨的三维立体模型,并绘制软骨的第一三维立体模型,再根据软骨的第一三维立体模型绘制软骨的第二三维立体模型,其中,软骨的第一三维立体模型的厚度大于软骨的第二三维立体模型的厚度,然后再根据软骨的第一三维立体模型制备第一模具,并根据软骨的第二三维立体模型制备第二模具I ;
[0026]2)在骨的三维立体模型中绘制发散式贯通管道8模型,再根据所述骨的三维立体模型及发散式贯通管道8模型通过生物陶瓷材料制备陶瓷骨支架4,然后将连接介质2穿过陶瓷骨支架4中的发散式贯通管道8并伸出到所述发散式贯通管道8外,再将粘结介质溶液注入到所述发散式贯通管道8中,当粘结介质溶液凝固后,连接介质2与陶瓷骨支架4相连接,得复合材料骨支架;
[0027]3)将复合材料骨支架的下端面放入到第二模具I中,固定后,将第一种水凝胶溶液注入到第二模具I中,固化后,成型为第一层水凝胶5,再将带有第一层水凝胶5的复合材料骨支架放置到第一模具中,固定后,注入第二种水凝胶溶液,浸泡后固化成型,得具有复杂型面的高强度复合材料骨软骨支架。优选的,通过使用紫外光第一种水凝胶溶液及第二种水凝胶溶液固化。
[0028]步骤I)中第一三维立体模型的厚度为第二三维立体模型的厚度的3-5倍。
[0029]步骤2)中连接介质2的下端伸出到发散式贯通管道8外I~2mm。
[0030]步骤3)中浸泡的时间为24~26h。 [0031]步骤3)中复合材料骨支架与第二模具I通过第一螺栓固定,复合材料骨支架与第一模具通过第二螺栓固定,所述第一螺栓及第二螺栓的长均为55-60_,直径均为3-4_。
[0032]需要说明的是,第一模具及第二模具I均为开合结构,第一模具的上端及第二模具I的上端均设有浇冒口,所述开合结构的侧面开设有四个通孔9,所述通孔9的直径为3-4_,开合结构的开合面上设有密封结构,所述密封结构由第一凸起及沟槽组成,密封结构位于通孔9与软骨的成型面之间,其中,所述三角形结构为等边三角形结构,三角形结构的边长为2_3mm。
[0033]所述发散式贯通管道8包括上部结构及下部结构,上部结构包括圆柱型结构6及设于圆柱型结构6下端的半球体结构7,下部结构由中心管道及若干组管道组成,任意一组管道中各管道的轴线与半球体结构7表面的交点均匀分布于圆上,各组管道对应圆的圆心均位于圆柱型结构6的轴线上,且相邻两个圆的圆心距为固定值,各管道的轴线相交于半球体结构7的球心处,中心管道的轴线与圆柱型结构的轴线相重合。所述下部结构包括7-9组管道,半球体结构7的直径为9-13_,各组管道中管道的数目为2-26个,每个管道的直径为1-3_,复合材料骨支架的侧面设有第二凸起3,所述第二凸起3的长为5-7_,宽为3-4_,高位2-4_,在使用过程中,通过第二凸起3确定第一模具、第二模具I及陶瓷骨支架4的相对位置。
[0034]另外,所述第一模具及第二模具I均采用透明材料的钢化玻璃制作成型而成。连接介质2为聚乳酸纤维,粘结介质采用左旋聚乳酸(PLA)用氯仿溶解配制而成的质量浓度为10%的溶液制备完成后第一层水凝胶5及第二层水凝胶组成了双网络水凝胶,所述双网络水凝胶的含水量为85~90%,缩弹性模量为0.4~0.9MPa。
具有复杂型面的高强度复合材料骨软骨支架的制备方法
- 专利详情
- 全文pdf
- 权力要求
- 说明书
- 法律状态
查看更多专利详情
下载专利文献
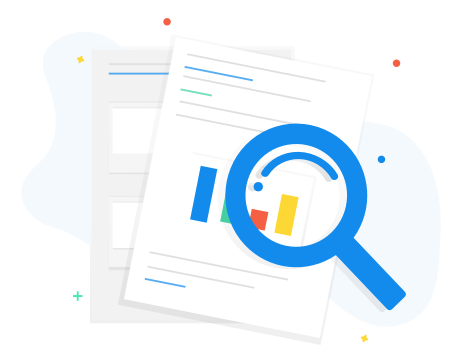
下载专利
同类推荐
-
连芩李贺军李坤
您可能感兴趣的专利
-
刘友举D·J·默克莱伊王圣茂C·汉松廖寄乔
专利相关信息
-
陈发荣, 赵正杨袁远, 杨群吕强, 罗峥伊凡·W·翁, 杰拉尔德·W·瓦尔克何唯平, 杰 张何唯平, 杰 张