专利名称:合成非晶态二氧化硅粉末及其制造方法以往,半导体用途的单晶制造中使用的坩埚或夹具类是将通过粉碎天然石英或硅砂后精制而得到的石英粉作为原料来制造的。但是,天然石英或硅砂含有各种金属杂质,即使进行上述精制处理,也不能完全去除金属杂质,因此在纯度方面不能充分满足。此外,随着半导体的闻集成化的发展,对可成为材料的单晶的品质要求提闻,对该单晶的制造中使用的坩埚或夹具类也期望高纯度产品。因此,将高纯度的合成非晶态二氧化硅粉末作为原料以代替天然石英或硅砂的合成二氧化硅玻璃产品受到关注。作为制造该高纯度的合成非晶态二氧化硅粉末的方法,公开了使高纯度的四氯化硅在水中水解,对生成的二氧化硅凝胶进行干燥、整粒、烧结而得到合成非晶态二氧化硅粉末的方法(例如,参见专利文献I。)。此外,公开了使硅酸酯等烷氧基硅烷在酸和碱的存在下水解而凝胶化,对得到的凝胶进行干燥、粉碎后,进行烧结,由此得到合成非晶态二氧化硅粉末的方法(例如,参见专利文献 2、3。)。利用上述专利文献I 3所记载的方法制造的合成非晶态二氧化硅粉末与天然石英或硅砂相比为高纯度,使从将这些作为原料制造的坩埚或夹具类等合成二氧化硅玻璃产品混入的杂质的降低或者高性能化变得可能。专利文献1:日本特公平4-75848号公报(权利要求1)专利文献2:日本特开昭62-176929号公报(权利要求1)专利文献3:日本特开平3-275527号公报(第2页左下栏第7行 第3页左上栏第6行)但是,将利用上述专利文献I 3所记载的方法制造的合成非晶态二氧化硅粉末作为原料制造的合成二氧化硅玻璃产品在合成二氧化硅玻璃产品的使用的环境为高温和减压的环境下的情况下,存在气泡产生或膨胀,使该合成二氧化硅玻璃产品的性能显著地降低的缺点。例如,单晶硅提拉用坩埚存在如下问题:在15000C附近和7000Pa附近的高温和减压的环境下使用,因上述气泡的产生或膨胀导致的坩埚性能的显著降低会影响提拉的单晶的品质。对于在这样的上述高温和 减压的环境下的使用中产生的问题,可以考虑如下对策:对通过四氯化硅的水解得到的合成非晶态二氧化硅粉末实施热处理,分别减少合成非晶态二氧化硅粉末中的羟基和氯的浓度,或者对通过烷氧基硅烷的溶胶-凝胶法得到的合成非晶态二氧化硅粉末实施热处理,分别减少合成非晶态二氧化硅粉末中的羟基和碳的浓度,由此使合成非晶态二氧化硅粉末中可成为气体成分的杂质浓度降低。但是,即使利用上述对策,也不能充分地抑制在高温和减压的环境下所使用的合成二氧化硅玻璃产品的气泡的产生或膨胀。
本发明的目的在于,提供克服这样的上述以往的课题,即使在高温和减压的环境下的使用中,也适合作为气泡的产生或膨胀少的合成二氧化硅玻璃产品的原料的合成非晶态二氧化硅粉末及其制造方法。本发明的第I方案,其特征在于,是对造粒的二氧化硅粉末实施球化处理后,清洗并干燥而得到的平均粒径D5tl为10 2000 μ m的合成非晶态二氧化硅粉末,BET比表面积除以由平均粒径D5tl计算出的理论比表面积得到的值超过1.35且1.75以下,真密度为2.10 2.20g/cm3,粒子内孔隙率为O 0.05,圆形度为0.50以上且0.75以下以及未熔解率大于0.25且0.60以下。本发明的第2方案为基于第I方案的发明,其特征在于,而且,是在实施球化处理之前对造粒的二氧化硅粉末进行烧结的合成非晶态二氧化硅粉末时,满足碳浓度小于2ppm或氯浓度小于2ppm中的任意一者或该两者。本发明的第3方案为基于第2方案的发明,其特征在于,而且,造粒的二氧化硅粉末是通过使四氯化硅水解而生成二氧化硅质的凝胶,干燥该二氧化硅质的凝胶而成为干燥粉,粉碎该干燥粉后,进行分级而得到的二氧化硅粉末,碳浓度小于2ppm。本发明的第4方案为基于第2方案的发明,其特征在于,而且,造粒的二氧化硅粉末是通过使有机系硅化合物水解而生成二氧化硅质的凝胶,干燥该二氧化硅质的凝胶而成为干燥粉,粉碎该干燥粉后,进行分级而得到的二氧化硅粉末,氯浓度小于2ppm。本发明的第5方案为基于第2方案的发明,其特征在于,而且,造粒的二氧化硅粉末是通过使用气相二氧化硅生成二氧化硅质的凝胶,干燥该二氧化硅质的凝胶而成为干燥粉,粉碎该干燥粉后,进行分级而得到的二氧化硅粉末,碳浓度小于2ppm小于,氯浓度小于2ppm0本发明的第6方案为一种合成非晶态二氧化硅粉末的制造方法,其特征在于,按顺序包括:造粒工序,生成二氧化硅质的凝胶,干燥该二氧化硅质的凝胶而成为干燥粉,粉碎该干燥粉后,进行分级,由此得到平均粒径D5tl为10 3000 μ m的二氧化硅粉末;利用热等离子体的球化工序,在以预定的流量导入氩气并以预定的高频输出功率产生等离子体的等离子体炬内,以预定的供给速度投入上述造粒工序中所得到的二氧化硅粉末,在从2000°C至二氧化硅的沸点的温度加热并熔融;清洗工序,去除附着于上述球化工序后的球化二氧化硅粉末表面上的微粉;和干燥工序,干燥上述清洗工序后的二氧化硅粉末,将上述球化工序中的氩气的流量调整50L/min以上且在高频输出功率(W)设为A、二氧化硅粉末的供给速度(kg/hr)设为B时,以A/B(ff.hr/kg)的值为3.0XlO3以上且小于1.0X104的方式调整后进行,得到平均粒径D5tl为10 2000 μ m、BET比表面积除以由平均粒径D5tl计算出的理论比表面积得到的值超过1.35且1.75以下、真密度为2.10 2.20g/cm3、粒子内孔隙率为O 0.05、圆形度为0.50以上0.75以下以及未熔解率大于0.25且0.60以下的合成非晶态二氧化硅粉末。 本发明的第7方案为基于第6方案的发明,其特征在于,而且,造粒工序为使四氯化硅水解而生成二氧化硅质的凝胶,干燥该二氧化硅质的凝胶而成为干燥粉,粉碎该干燥粉后,进行分级,由此得到平均粒径D5tl为10 3000 u m的二氧化硅粉末的工序。本发明的第8方案为合成非晶态二氧化硅粉末的制造方法,为基于第6方案的发明,其特征在于,而且,造粒工序为使有机系硅化合物水解而生成二氧化硅质的凝胶,干燥二氧化硅质的凝胶而成为干燥粉,粉碎该干燥粉后,进行分级,由此得到平均粒径D5tl为10 3000 u m的二氧化硅粉末的工序。本发明的第9方案为合成非晶态二氧化硅粉末的制造方法,为基于第6方案的发明,其特征在于,而且,造粒工序为使用气相二氧化硅生成二氧化硅质的凝胶,干燥该二氧化硅质的凝胶而成为干燥粉,粉碎该干燥粉后,进行分级,由此得到平均粒径D5tl为10 3000 u m的二氧化硅粉末的工序。本发明的第10方案为一种合成非晶态二氧化硅粉末的制造方法,其特征在于,按顺序包括:造粒工序,生成二氧化硅质的凝胶,干燥该二氧化硅质的凝胶而成为干燥粉,粉碎该干燥粉后,进行分级,由此得到平均粒径D5tl为10 3000 u m的二氧化硅粉末;烧结工序,对上述造粒工序中所得到的二氧化硅粉末在800 1450°C的温度进行烧结;利用热等离子体的球化工序,在以预定的流量导入氩气并以预定的高频输出功率产生等离子体的等离子体炬内,以预定的供给速度投入上述烧结工序中所得到的二氧化硅粉末,在从2000°C至二氧化硅的沸点的温度加热并熔融;清洗工序,去除附着于上述球化工序后的球化二氧化硅粉末表面上的微粉;和干燥工序,干燥上述清洗工序后的二氧化硅粉末,将上述球化工序中的氩气的流量调整为50L/min以上且在高频输出功率(W)设为A、二氧化硅粉末的供给速度(kg/hr)设为B时,以A/B(W hr/kg)的值为3.0XlO3以上且小于1.0X104的方式调整后进行,得到平均粒径D5tl为10 2000 ynuBET比表面积除以由平均粒径D5tl计算出的理论比表面积得到的值超过1.35且1.75以下、真密度为2.10 2.20g/cm3、粒子内孔隙率为0 0.05、圆形度为0.50以上0.75以下以及未熔解率大于0.25且0.60以下,满足碳浓度小于2ppm或氯浓度小于2ppm中的任意一者或该两者的合成非晶态二氧化硅粉末。本发明的第11方案为基于第10方案的发明,其特征在于,而且,造粒工序为使四氯化硅水解而生成二氧化硅 质的凝胶,干燥该二氧化硅质的凝胶而成为干燥粉,粉碎该干燥粉后,进行分级,由此得到平均粒径D5tl为10 3000 u m的二氧化硅粉末的工序时,得到的合成非晶态二氧化硅粉末的碳浓度小于2ppm。本发明的第12方案为基于第10方案的发明,其特征在于,而且,造粒工序为使有机硅化合物水解而生成二氧化硅质的凝胶,干燥该二氧化硅质的凝胶而成为干燥粉,粉碎该干燥粉后,进行分级,由此得到平均粒径D5tl为10 3000 u m的二氧化硅粉末的工序时,得到的合成非晶态二氧化硅粉末的氯浓度小于2ppm。本发明的第13方案为基于第11方案的发明,其特征在于,而且,造粒工序为使用气相二氧化硅生成二氧化硅质的凝胶,干燥该二氧化硅质的凝胶而成为干燥粉,粉碎该干燥粉后,进行分级,由此得到平均粒径D5tl为10 3000 u m的二氧化硅粉末的工序是,得到的合成非晶态二氧化硅粉末的碳浓度小于2ppm,氯浓度小于2ppm。本发明的第I方案的合成非晶态二氧化硅粉末,是对造粒的二氧化硅粉末实施球化处理后,清洗并干燥而得到的平均粒径D5tl为10 2000 u m的合成非晶态二氧化硅粉末,BET比表面积除以由平均粒径D5tl计算出的理论比表面积得到的值超过1.35且1.75以下,真密度为2.10 2.20g/cm3,粒子内孔隙率为0 0.05,圆形度为0.50以上0.75以下以及未熔解率大于0.25且0.60以下。因此,使用该合成非晶态二氧化硅粉末制造合成二氧化娃玻璃产品时,原料粉末的表面所吸附的气体成分变少,并且粉末内部的气体成分变少,因此可以降低气泡的产生或膨胀。本发明的第2方案的合成非晶态二氧化硅粉末,是对造粒的二氧化硅粉末进行烧结后,实施球化处理的合成非晶态二氧化硅粉末,满足碳浓度小于2ppm或氯浓度小于2ppm中的任意一者或该两者。因此,使用该合成非晶态二氧化硅粉末制造合成二氧化硅玻璃产品时,原料粉末的表面所吸附的气体成分变少,并且粉末内部的气体成分变少,因此可以降低气泡的产生或膨胀。特别是,在该合成非晶态二氧化硅粉末中,在实施球化处理之前进行烧结,由此表面所吸附的气体成分、粉末内部的气体成分极少,可以更加提高上述合成二氧化硅玻璃产品中的气泡的产生或膨胀的降低效果。本发明的第3方案的合成非晶态二氧化硅粉末的造粒的二氧化硅粉末是通过使四氯化硅水解而生成二氧化硅质的凝胶,干燥该二氧化硅质的凝胶而成为干燥粉,粉碎该干燥粉后,进行分级而得到的二氧化硅粉末,实现碳浓度小于2ppm。在该合成非晶态二氧化硅粉末中,对于作为原料粉末的二氧化硅粉末,通过使用使四氯化硅在液体中反应而得到的物质,可以抑制碳浓度,因此可以提高上述合成二氧化硅玻璃产品中的气泡的产生或膨胀的降低效果。本发明的第4方案的合成非晶态二氧化硅粉末的造粒的二氧化硅粉末是通过使有机系硅化合物水解而生成二氧化硅质的凝胶,干燥该二氧化硅质的凝胶而成为干燥粉,粉碎该干燥粉后,进行分级而得到的二氧化硅粉末,实现氯浓度小于2ppm。在该合成非晶态二氧化硅粉末中,对于作为原料粉末的二氧化硅粉末,通过使用由四甲氧基硅烷等有机系硅化合物得到的物质,可以抑制氯浓度,因此可以提高上述合成二氧化硅玻璃产品中的气泡的产生或膨胀的降低效果。本发明的第5方案的合成非晶态二氧化硅粉末的造粒的二氧化硅粉末是通过使用气相二氧化硅生成二氧化硅质的凝胶,干燥该二氧化硅质的凝胶而成为干燥粉,粉碎该干燥粉后,进行分级而得到的二氧化硅粉末,实现碳浓度小于2ppm、氯浓度小于2ppm。与将使氯系硅化合物在液体中反应而得到的物质或由四甲氧基硅烷等有机系硅化合物得到的物质用作原料粉末的情况相比,在该合成非晶态二氧化硅粉末中,对于作为原料粉末的二氧化硅粉末,通过使用气相二氧化硅,可以进一步抑制碳浓度和氯浓度这两者,因此可以进一步提高上述合成二氧化硅玻璃产品中的气泡的产生或膨胀的降低效果。本发明的第6 第9方案的合成非晶态二氧化硅粉末的制造方法,其特征在于,按顺序包括;造粒工序,例如使四氯化硅水解而生成二氧化硅质的凝胶,或者使四甲氧基硅烷等有机系硅化合物水解而生成二氧化硅质的凝胶,或者使用气相二氧化硅生成二氧化硅质的凝胶,然后干燥该二氧化硅质的凝胶而成为干燥粉,粉碎该干燥粉后,进行分级,由此得到所期望平均粒径的二氧化硅粉末;利用热等离子体的球化工序,在以预定的流量导入氩气并以预定的高频输出功率产生等离子体的等离子体炬内,以预定的供给速度投入上述造粒工序中所得到的二氧化硅粉末,在从2000°C至二氧化硅的沸点的温度加热并熔融;清洗工序,去除附着于上述球化工序后的球化二氧化硅粉末表面上的微粉;和干燥工序,干燥上述清洗工序后的二氧化硅粉末,将上述球化工序中的氩气的流量调整为50L/min以上且在高频输出功率(W) 设为A、二氧化硅粉末的供给速度(kg/hr)设为B时,以A/B (W.hr/kg)的值为3.0X IO3以上且小于1.0X IO4的方式调整后进行,得到平均粒径D5tl为10 2000 u m、BET比表面积除以由平均粒径D5tl计算出的理论比表面积得到的值超过1.35且1.75以下、真密度为2.10 2.20g/cm3、粒子内孔隙率为0 0.05、圆形度为0.50以上0.75以下以及未熔解率大于0.25且0.60以下的合成非晶态二氧化硅粉末。通过上述工序,可以简便地制造不可避免的气体吸附量少且粉末内部的气体成分少、从而作为合成二氧化硅玻璃产品的原料适合的合成非晶态二氧化硅粉末。本发明的第10 第13方案的合成非晶态二氧化硅粉末的制造方法,例如使四氯化硅水解而生成二氧化硅质的凝胶、或使四甲氧基硅烷等有机硅化合物水解而生成二氧化硅质的凝胶、或者使用气相二氧化硅生成二氧化硅质的凝胶。于是,其特征在于,按顺序包括:造粒工序,例如使四氯化硅水解而生成二氧化硅质的凝胶,或者使四甲氧基硅烷等有机硅化合物水解而生成二氧化硅质的凝胶,或者使用气相二氧化硅生成二氧化硅质的凝胶,然后干燥该二氧化硅质的凝胶而成为干燥粉,粉碎该干燥粉后,进行分级,由此得到所期望平均粒径的二氧化硅粉末;烧结工序,对上述造粒工序中所得到的二氧化硅粉末在800 1450°C的温度进行烧结;利用热等离子体的球化工序,在以预定的流量导入氩气并以预定的高频输出功率产生等离子体的等离子体炬内,以预定的供给速度投入上述烧结工序得到的二氧化硅粉末,在从2000°C至二氧化硅的沸点的温度加热并熔融;清洗工序,去除附着于上述球化工序后的球化二氧化硅粉末表面上的微粉;和干燥工序,干燥上述清洗工序后的二氧化硅粉末,将上述球化工序中的氩气的流量调整为50L/min以上且在高频输出功率(W)设为A、二氧化硅粉末的供给速度(kg/hr)设为B时,以A/B(W -hr/kg)的值为3.0X IO3以上且小于1.0X IO4的方式调整后进行,得到平均粒径D5tl为10 2000 u m、BET比表面积除以由平均粒径D5tl计算出的理论比表面积得到的值超过1.35且1.75以下、真密度为2.10 2.20g/cm3、粒子内孔隙率为0 0.05、圆形度为0.50以上0.75以下以及未熔解率大于0.25且0.60以下、满足碳浓度小于2ppm或氯浓度小于2ppm中的任意一者或该两者的合成非晶态二氧化硅粉末。通过上述工序,可以简便地制造不可避免的气体吸附量少且粉末内部的气体成分少而适合作为合成二氧化硅玻璃产品的原料的合成非晶态二氧化硅粉末。特别是,在该制造方法中,在球化处理工序之前设置利用预定的条件的烧结工序,由此可以使表面所吸附的气体成分、粉末内部的气体成分极少,可以制造上述合成二氧化硅玻璃产品中的气泡的产生或膨胀的降低效果更加好的合成非晶态二氧化硅粉末。图1为表示本发明第I实施方式的合成非晶态二氧化硅粉末的代表性粉末粒子的照片。图2为表示本发明第2实施方式的合成非晶态二氧化硅粉末的代表性粉末粒子的照片。
图3为表示本发明第I实施方式的合成非晶态二氧化硅粉末的制造工序的工艺流程图。图4为表示本发明第2实施方式的合成非晶态二氧化硅粉末的制造工序的工艺流程图。图5为利用热等离子体的球化装置的概要截面图。
图6为粒度、形状分布测定器的概要图。图7为表示未实施球化处理的代表性二氧化硅粉末粒子的照片。图8为表示带棱角的二氧化硅粉末粒子的一例的照片。
,基于附图进行说明。本发明第I实施方式的合成非晶态二氧化硅粉末是通过对造粒的二氧化硅粉末实施球化处理后,清洗并干燥而得到的。并且,其特征在于,BET比表面积除以由平均粒径D50计算出的理论比表面积得到的值超过1.35且1.75以下,真密度为2.10 2.20g/cm3,粒子内孔隙率为O 0.05,圆形度为0.50以上0.75以下以及未熔解率大于0.25且0.60以下。此外,本发明第2实施方式的合成非晶态二氧化硅粉末是对造粒的二氧化硅粉末进行烧结后,实施球化处理的合成非晶态二氧化硅粉末。从而,满足碳浓度小于2ppm或氯浓度小于2ppm的任意一者或其两者。作为在高温和减压下单晶硅提拉用坩埚等合成二氧化硅玻璃产品中气泡的产生或膨胀的主要原因,可以认为是产品的制造中使用的原料粉末的表面所吸附的气体。即,制造合成二氧化硅玻璃产品之际,在作为其一工序的熔融时,原料粉末的表面所吸附的气体成分会解吸。并且,该气体成分残留在合成二氧化硅玻璃产品中,这会成为气泡的产生或膨胀的原因。成为合成二氧化硅玻璃产品的原料的二氧化硅粉末,通常通过粉碎工序,因此如图7所示较多含有不定形(粉碎粉末形状)的粒子。因此,可以认为比表面积变大,不可避免的气体吸附量变大。为此,本发明的合成非晶态二氧化硅粉末是通过对粉末实施球化处理,使BET比表面积除以由平均粒径D5tl计算出的理论比表面积得到的值成为上述范围。BET比表面积是指通过BET三点法测定的值。此外,粒子的理论比表面积是在假设粒子为圆球体、表面为平滑的情况下,由下式(I)计算出的。另外,式(1)中,D表示粒子的直径,P表示真密度。理论比表面积=6/(DX P) (1)本说明书中,粉末的理论比表面积是在上述式(I)中,由将D设为粉末的平均粒径D5tl、将P假设为真密度2.20g/cm3的理论真密度计算出的值。即,粉末的理论比表面积是由下式(2)计算出的。粉末的理论比表面积=2.73/D5Q (2)BET比表面积除以由平均粒径D5tl计算出的理论比表面积得到的值变大时,比表面积变大,不可避免的气体吸附量变大。该值为1.35以下时,石英坩埚等合成二氧化硅玻璃产品的成型性会降低。另一方面,超过1.75时,气泡的产生或膨胀的降低效果小。其中,BET比表面积除以由平均粒径D5tl计算出的理论比表面积得到的值,优选为1.40 1.60的范围。此外,合成非晶态二氧化硅粉末的圆形度为0.50以上0.75以下。圆形度意味着越接近1.00,粉末粒子越接近圆球,由下式(3)计算出。圆形度=4jiS/L2(3)
式(3)中,S表示拍摄的粒子投影图的面积,L表示粒子投影图的周长。本说明书中,粉末的圆形度是由上述式(3)计算出的200个粉末粒子的平均值。粉末的圆形度小于0.50时,气泡的产生或膨胀的降低效果小。此外,粉末的圆形度超过0.75时,石英坩埚等合成二氧化硅玻璃产品的成型性会降低。其中,粉末的圆形度,优选为0.60 0.70的范围。此外,合成非晶态二氧化硅粉末的未熔解率大于0.25且0.60以下。粉末的未熔解率是表示在上述200个粉末粒子的粒子投影图中,带棱角的粉末粒子含有比例。未熔解率为0.25以下时,石英坩埚等合成二氧化硅玻璃产品的成型性会降低。另一方面,未熔解率大于0.60时,气泡的产生或膨胀的降低效果小。其中,粉末的未熔解率,优选为0.30 0.40的范围。此外,关注合成非晶态二氧化硅粉末的I个粒子时,优选在粒子内不存在空穴或闭塞的裂痕等内部空间。即这是因为,在合成非晶态二氧化硅粉末的内部存在空间时,会成为合成二氧化硅玻璃产品中的气泡的产生或膨胀的原因。因此,真密度为2.10g/cm3以上,优选为2.15 2.20g/cm3。真密度是指按照JIS R7212碳块的测定方法(d)真比重测定,进行真密度测定3次的平均值。此外,粒子内孔隙率为0.05以下,优选为0.01以下。粒子内孔隙率是对50个粉末粒子,测定通过SEM(扫描型电子显微镜)观察截面时的粒子的截面面积,并且在粒子内存在空间时测定该空间的面积,由下式(4)计算出的值的平均值。粒子内孔隙率=粒子内空间总面积/粒子截面总面积(4)
此外,合成非晶态二氧化硅粉末的平均粒径D5tl为10 2000 iim,优选在50 1000 i! m的范围内。这是因为,小于下限值时,粉末粒子间的空间小,在该空间存在的气体会难以脱出,因此容易残留小气泡,另一方面,超过上限值时,粉末粒子间的空间过大,容易残留大气泡。其中,平均粒径D5tl特别优选在80 600 iim的范围内。另外,本说明书中,平均粒径D5tl是指对体积基准的粒子分布的中位值测定3次的平均值。合成非晶态二氧化硅粉末的堆密度,优选为l.0Og/cm3以上。这是因为,小于下限值时,粉末粒子间的空间过大,容易残留大气泡,另一方面,超过上限值时,粉末粒子间的空间小,因此在该空间存在的气体难以脱出,容易残留小气泡。其中,堆密度特别优选在1.20 1.50g/cm3范围内。为了使粉末的熔融性均匀,优选为在使用CuKa射线、利用粉末X射线衍射法测定的情况下,衍射峰宽的、不能确认晶态二氧化硅粉末的粉末。在非晶态和晶态的二氧化硅在熔融中的特性不同,存在晶态的二氧化硅的熔融延迟开始的趋势。因此,使用非晶态和晶态的二氧化硅混合存在的合成非晶态二氧化硅粉末,进行合成二氧化硅玻璃产品等的制造时,在合成二氧化硅玻璃产品中,容易残留气泡。为了合成二氧化硅玻璃产品的杂质混入的降低或高性能化,合成非晶态二氧化硅粉末的杂质浓度,优选除了氢原子以外的IA族、2A 8族、IB 3B族、除了碳和硅以外的4B族、5B族、除了氧以外的6B族、除了氯以外的7B族的浓度小于lppm。其中,特别优选这些杂质浓度小于0.05ppm。此外,为了抑制在高温和减压下的合成二氧化硅玻璃产品中的气泡的产生或膨胀,优选可成为气体成分的羟基为60ppm以下,氯浓度为5ppm以下,碳浓度为5ppm以下。特别是,在本发明第2实施方式的合成非晶态二氧化硅粉末中,在实施球化处理之前进行烧结,由此使表面所吸附的气体成分、粉末内部的气体成分变得极少,可以更加提高合成二氧化硅玻璃产品中的气泡的产生或膨胀的降低效果。S卩,对造粒的二氧化硅粉末,以预定的条件进行烧结,由此可以实现氯浓度小于2ppm或碳浓度小于2ppm的任意一者或两者。并且,造粒的二氧化硅粉末,即原料粉末是通过使四氯化硅水解而生成二氧化硅质的凝胶,干燥该二氧化硅质的凝胶而成为干燥粉,粉碎该干燥粉后,进行分级而得到的二氧化硅粉末时,在球化处理前以预定的条件进行烧结,由此碳浓度小于2ppm。这是由于上述二氧化硅粉末与使用四甲氧基硅烷等有机系硅化合物而得到的二氧化硅粉末相比碳浓度低,因此在将它用作原料粉末而得到的合成非晶态二氧化硅粉末中,残留的碳浓度相比较降低。此外,造粒的二氧化硅粉末是通过使有机系硅化合物水解而生成二氧化硅质的凝胶,干燥该二氧化硅质的凝胶而成为干燥粉,粉碎该干燥粉后,进行分级而得到的二氧化硅粉末时,在球化处理前以预定的条件进行烧结,由此氯浓度小于2ppm。上述二氧化硅粉末与使氯系硅化合物在溶液中反应而得到的二氧化硅粉末相比氯浓度低,因此在将它用作原料粉末而得到的合成非晶态二氧化硅粉末中,残留的氯浓度相比较降低。此外,造粒的二氧化硅粉末是通过使用气相二氧化硅生成二氧化硅质的凝胶,干燥该二氧化硅质的凝胶而成为干燥粉,粉碎该干燥粉后,进行分级而得到的二氧化硅粉末时,在球化处理前以预定的条件进行烧结,由此实现碳浓度小于2ppm、氯浓度小于2ppm。在将使氯系硅化合物在溶液中反应而得到的二氧化硅粉末用作原料粉末而得到的合成非晶态二氧化硅粉末中,残留的氯浓度较为容易变高。此外,在将有机系硅化合物用作原料粉末而得到的合成非晶态二氧化硅粉末中,残留的碳浓度较为容易变高。另一方面,气相二氧化硅与上述两个二氧化硅粉末相比氯浓度、碳浓度都低,因此在将气相二氧化硅用作原料粉末而得到的合成非晶态二氧化硅粉末中,氯浓度、碳浓度这两者极低。从而,还可以进一步提高合成二氧化硅玻璃产品中的气泡的产生或膨胀的降低效果。
本发明的合成非晶态二氧化硅粉末通过实施球化处理后,清洗并干燥,如图1或图2所示较多含有熔融并球化的粒子聚集多个的粒子。这样,本发明的合成非晶态二氧化硅粉末含有较多聚集的粒子,因此粉末的圆形度、未熔解率显示出上述范围,不一定含有较多接近圆球的粒子,但通过熔融而使粉末表面变得平滑,由此不可避免的气体吸附量会降低。另外,对于熔融并球化的粒子聚集多个的粒子,在本说明书中,聚集的一个粒子构成一个粒子。接着,对本发明的合成非晶态二氧化硅粉末的制造方法进行说明。本发明第I实施方式的合成非晶态二氧化硅粉末的制造方法是如图3所示通过对成为原料的二氧化硅粉末实施球化处理后,清洗并干燥而得到的。此外,本发明第2实施方式的合成非晶态二氧化硅粉末的制造方法是如图4所示通过对成为原料的二氧化硅粉末进行烧结,对进行该烧结的二氧化硅粉末实施球化处理后,清洗并干燥而得到的。下面,对各工序进行详细说明。成为本发明的合成非晶态二氧化硅粉末的原料的二氧化硅粉末例如通过如下方法得到。作为第I种方法,首先相对于四氯化硅lmol,准备相当于45 SOmol的量的超纯水。在容器内加入准备的超纯水,在氮气、氩气等气氛中,将温度保持在20 45°C并进行搅拌的同时,添加四氯化硅并使其水解。添加四氯化硅后继续搅拌0.5 6小时,生成二氧化娃质的凝胶。此时,搅拌速度优选设为100 300rpm的范围。接着,将上述二氧化娃质的凝胶移至干燥用容器并将其放入到干燥机,在干燥机内优选以10 20L/min的流量使氮气、氩气等流通的同时,在200°C 300°C的温度干燥12 48小时而得到干燥粉。接着,从干燥机取出该干燥粉,使用辊式粉碎机等粉碎机进行粉碎。使用辊式粉碎机的情况下,适当调整为辊间隙0.2 2.0mm、辊转速3 200rpm来进行。最后,对粉碎的干燥粉,使用振动筛等进行分级,由此得到平均粒径D5tl为10 3000 u m、优选为70 1300 u m的二氧化硅粉末。作为第2种方法,相对于作为有机系硅化合物的四甲氧基硅烷lmol,准备超纯水0.5 3mol、乙醇0.5 3mol。在容器内加入准备的超纯水、乙醇,在氮气、氩气等气氛中,将温度保持在60 0C并进行搅拌的同时,添加四甲氧基硅烷并使其水解。添加四甲氧基硅烷后搅拌5 120分钟,之后相对于四甲氧基硅烷lmol,进一步添加I 50mol的超纯水,继续搅拌I 12小时,生成二氧化硅质的凝胶。此时,优选搅拌速度设为100 300rpm的范围。接着,将上述二氧化硅质的凝胶移至干燥用容器并将其放入到干燥机,在干燥机内优选以10 20L/min的流量使氮气、氩气等流通的同时,在200°C 300°C的温度干燥6 48小时而得到干燥粉。接着,从干燥机取出该干燥粉,使用辊式粉碎机等粉碎机进行粉碎。使用棍式粉 碎机的情况下,适当调整为棍间隙0.2 2.0mm、棍转速3 200rpm来进行。最后,对粉碎的干燥粉,使用振动筛等进行分级,由此得到平均粒径D5tl为10 3000 u m、优选为70 1300 ii m的二氧化硅粉末。作为第3种方法,首先,相对于平均粒径D5tl为0.007 0.030 U m、比表面积为50 380m2/g的气相二氧化娃lmol,准备超纯水3.0 35.0mol0在容器内加入准备的超纯水,在氮气、氩气等气氛中,将温度保持在10 30°C并进行搅拌的同时,添加气相二氧化硅。添加气相二氧化硅后继续搅拌0.5 6小时,生成二氧化硅质的凝胶。此时,搅拌速度优选设为10 50rpm的范围。接着,将上述二氧化硅质的凝胶移至干燥用容器并将其放入到干燥机,在干燥机内优选以I 20L/min的流量使氮气、氩气等流通的同时,在200°C 300°C的温度干燥12 48小时而得到干燥粉。接着,从干燥机取出该干燥粉,使用辊式粉碎机等粉碎机进行粉碎。使用辊式粉碎机的情况下,适当调整为辊间隙0.5 2.0mm、辊转速3 200rpm来进行。最后,对粉碎的干燥粉,使用振动筛等进行分级,由此得到平均粒径D5tl为10 3000 u m、优选为70 1300 u m的二氧化硅粉末。对如此造粒而得到的二氧化硅粉末,以后述的条件进行球化处理,但在本发明第2实施方式的合成非晶态二氧化硅粉末的制造方法中,在该球化处理之前,如图4所示以预定的条件进行烧结。该烧结是在耐热性玻璃或石英制的容器中,在大气或氮气气氛中、在800 1450°C的温度进行的。通过在球化处理工序之前设置烧结工序,可以使表面所吸附的气体成分、粉末内部的气体成分变得极少。此外,由气相二氧化硅造粒的粉末具有纳米尺寸的封闭孔(々口一 X F 7 ),因此对该粉末实施球化处理时,在粒子内残留空穴。因此,通过对由球化处理前的气相二氧化硅造粒的粉末进行烧结,可以使上述纳米尺寸的封闭孔消失。烧结温度低于下限值时,不能充分得到烧结所带来的杂质的降低效果或使气相二氧化硅中的封闭孔消失的效果。另一方面,烧结温度超过上限值时,发生粉体间固结的不利情况。对通过上述第I种 第3种方法得到的二氧化硅粉末或该粉末以上述条件进行烧结的二氧化硅粉末的球化是通过利用热等离子体的球化处理进行的。在利用热等离子体的球化处理中,例如,可以使用图5所示的装置。该装置30具备有:等离子体炬31,产生等离子体;腔室32,是设置在该等离子体炬31的下部的反应筒;和回收部33,设置在该腔室32的下部并回收处理后的粉末。等离子体炬31具有:石英管34,与腔室32连通的顶部被封闭;和高频感应线圈36,卷绕该石英管34。在石英管34的上部贯穿设置有原料供给管37且连接有气体导入管38。在腔室32的侧方,设有气体排出口 39。在等离子体炬31中,在高频感应线圈36通电时,产生等离子体40,由气体导入管38向石英管34中供给氩气、氧等气体。原料粉末通过原料供给管37供给到等离子体40中。此外,腔室32内的气体是由设于腔室32侧方的气体排出口 39排出气体。首先,由装置30的气体导入管38以50L/min以上、优选为65 110L/min的流量导入工作气体的氩气,使频率2 3MHz、输出功率90 180kW的高频施加到等离子体炬31,产生等离子体。等离子体稳定后,以35 130L/min的流量慢慢地导入氧,产生氩气-氧等离子体。接着,将利用上述第I种 第3种方法得到的二氧化硅粉末,由原料供给管37以供给速度9.0 53.0kg/hr投入到氩气-氧等离子体中,使二氧化硅粉末熔融,使成为熔体的粒子降落,利用回收部33回收降落的粒子,由此可以得到球化的二氧化硅粉末41。合成非晶态二氧化硅粉末中的圆形度或未熔解率等的调整可以通过调整氩气的流量或高频输出功率、二氧化硅粉末的供给速度等来进行。例如,通过将氩气的流量调整为50L/min以上,且在上述范围中当高频输出功率(W)设为A、二氧化硅粉末的供给速度(kg/hr)设为B时,以A/B(W.hr/kg)的值在3.0X IO3以上且小于1.0X104的范围的方式调整高频输出功率A和二氧化硅粉末的供给速度B,由此可以得到所期望的圆形度、未熔解率。球化处理后的二氧化硅粉末由于在其表面附着有蒸发到氩气-氧等离子体中的二氧化硅粉末的微粉,因此在清洗容器中加入球状工序后的球化二氧化硅粉末和超纯水,进行超声波清洗。超声波清洗后,该二氧化硅粉末的微粉移动至超纯水中,因此利用网眼大的过滤器进行过滤。反复进行该操作直到二氧化硅粉末的微粉消失。清洗工序后的二氧化硅粉末的干燥优选通过如下进行:首先,在干燥用容器中加入粉末,将该干燥用容器放入到干燥机。然后,在干燥机内使氮气、氩气等以I 20L/min的流量流通的同时,在100°C 400°C的温度保持3 48小时。通过以上的工 序,可以得到本发明的合成非晶态二氧化硅粉末。该合成非晶态二氧化硅粉末的不可避免的气体吸附量少,可以适合用作合成二氧化硅玻璃产品的原料。特别是,在本发明第2实施方式的制造方法中,在球化处理工序之前设置利用预定条件进行的烧结工序,由此可以使表面所吸附的气体成分、粉末内部的气体成分变得极少。实施例接着,对本发明的实施例,与比较例一同进行详细说明。〈实施例1>首先,相对于四氯化硅lmol,准备相当于55.6mol的量的超纯水。在容器内加入该超纯水,在氮气气氛中,将温度保持在25°C并进行搅拌的同时,添加四氯化硅并使其水解。添加四氯化硅后继续搅拌3小时,生成二氧化硅质的凝胶。此时,搅拌速度设为150rpm。接着,将上述二氧化硅质的凝胶移至干燥用容器并将其放入到干燥机,在干燥机内以15L/min的流量使氮气流通的同时,在250°C的温度干燥18小时而得到干燥粉。从干燥机取出该干燥粉,使用辊式粉碎机进行粉碎。此时,辊间隙调整为0.2mm、辊转速调整为50rpm来进行。对粉碎的干燥粉,使用网眼100 μ m和网眼150 μ m的振动筛进行分级,得到平均粒径D5tl为127 μ m的二氧化硅粉末。
接着,使用图5所示的装置30,以下表I所示的条件,对上述得到的二氧化硅粉末实施球化处理而不进行烧结。具体地说,首先,由装置30的气体导入管38导入工作气体的氩气,使高频施加到等离子体炬31,产生等离子体。等离子体稳定后,慢慢地导入氧,产生氩气-氧等离子体。将上述得到的二氧化硅粉末,由原料供给管37投入到氩气-氧等离子体中,使二氧化硅粉末熔融,使成为熔体的粒子降落,利用回收部33回收降落的粒子,由此得到球化的二氧化硅粉末41。球化处理后,在清洗容器中加入上述粉末和超纯水,进行超声波清洗。进行超声波清洗后,利用网眼50 的过滤器进行过滤。反复进行该操作直到附着于二氧化硅粉末的粒子表面上的微粉末消失。最后,在干燥用容器中加入清洗的粉末,在干燥机内使氮气以10L/min的流量流通的同时,在200°C的温度保持48小时,由此得到合成非晶态二氧化硅粉末。〈实施例2>首先,相对于四甲氧基硅烷lmol,准备超纯水lmol、乙醇lmol。在容器内加入准备的超纯水、乙醇,在氮气气氛中,将温度保持在60°C并进行搅拌的同时,添加四甲氧基硅烷并使其水解。添加四甲氧基硅烷后搅拌60分钟,之后相对于四甲氧基硅烷lmol,进一步添加25mol的超纯水,继续搅拌6小时,生成二氧化娃质的凝胶。此时,搅拌速度设为lOOrprn。接着,将上述二氧化硅质的凝胶移至干燥用容器并将其放入到干燥机,在干燥机内以20L/min的流量使氮气流通的同时,在200°C的温度干燥24小时而得到干燥粉。从干燥机取出该干燥粉,使用辊式粉碎机进行粉碎。此时,辊间隙调整为0.2_、辊转速调整为55rpm来进行。对粉碎的干燥粉,使用网眼100 y m和网眼175 y m的振动筛进行分级,得到平均粒径D50为135 ii m的二氧化硅粉末。接着,使用图5所示的装置30,以下表I所示的条件,对上述得到的二氧化硅粉末实施球化处理而不进行烧结。具体地说,首先,由装置30的气体导入管38导入工作气体的氩气,使高频施加到等离子体炬31,产生等离子体。等离子体稳定后,慢慢地导入氧,产生氩气-氧等离子体。将上述得到的二氧化硅粉末,由原料供给管37投入到氩气-氧等离子体中,使二氧化硅粉末熔融,使成为熔体的粒子降落,利用回收部33回收降落的粒子,由此得到球化的二氧化硅粉末41。球化处理后,在清洗容器中加入上述粉末和超纯水,进行超声波清洗。进行超声波清洗后,利用网眼50 的过滤器进行过滤。反复进行该操作直到附着于二氧化硅粉末的粒子表面上的微粉末消失。最后,在干燥用容器中加入清洗后的粉末,在干燥机内使氩气以10L/min的流量流通的同时,在300°C的温度保持12小时,由此得到合成非晶态二氧化硅粉末。〈实施例3>首先,相对于平均粒径D5tl为0.020 U m、比表面积为90m2/g的气相二氧化硅Imol,准备超纯水13mol。在容器内加入准备的超纯水,在氮气气氛中,将温度保持在25°C并进行搅拌的同时,添加气相二氧化硅。添加气相二氧化硅后继续搅拌3小时,生成二氧化硅质的凝胶。此时,搅拌速度设为30rpm。接着,将上述二氧化硅质的凝胶移至干燥用容器并将其放入到干燥机,在干燥机内以10L/min的 流量使氮气流通的同时,在300°C的温度干燥12小时而得到干燥粉。从干燥机取出该干燥粉,使用辊式粉碎机进行粉碎。此时,辊间隙调整为0.5mm、辊转速调整为30rpm来进行。对粉碎的干燥粉,使用网眼400 μ m和网眼550 μ m的振动筛进行分级,得到平均粒径D5tl为484 μ m的二氧化硅粉末。接着,使用图5所示的装置30,以下表I所示的条件,对上述得到的二氧化硅粉末实施球化处理而不进行烧结。具体地说,首先,由装置30的气体导入管38导入工作气体的氩气,使高频施加到等离子体炬31,产生等离子体。等离子体稳定后,慢慢地导入氧,产生氩气-氧等离子体。将上述得到的二氧化硅粉末,由原料供给管37投入到氩气-氧等离子体中,使二氧化硅粉末熔融,使成为熔体的粒子降落,利用回收部33回收降落的粒子,由此得到球化的二氧化硅粉末41。球化处理后,在清洗容器中加入上述粉末和超纯水,进行超声波清洗。进行超声波清洗后,利用网眼200 μ m的过滤器进行过滤。反复进行该操作直到附着于二氧化硅粉末的粒子表面上的微粉末消失。最后,在干燥用容器中加入清洗后的粉末,在干燥机内使氮气以20L/min的流量流通的同时,在200°C的温度保持36小时,由此得到合成非晶态二氧化硅粉末。〈实施例4>首先,相对于四氯化硅lmol,准备相当于70.5mol的量的超纯水。在容器内加入该超纯水,在氩气气氛中,将温度保持在35°C并进行搅拌的同时,添加四氯化硅并使其水解。添加四氯化硅后继续搅拌3小时,生成二氧化硅质的凝胶。此时,搅拌速度设为150rpm。接着,将上述二氧化硅质的凝胶移至干燥用容器并将其放入到干燥机,在干燥机内以10L/min的流量使氮气流通的同时,在300°C的温度干燥24小时而得到干燥粉。从干燥机取出该干燥粉,使用辊式粉碎机进行粉碎。此时,辊间隙调整为0.9mm、辊转速调整为20rpm来进行。对粉碎的干燥粉,使用网眼800 μ m和网眼1000 μ m的振动筛进行分级,得到平均粒径D5tl为927 μ m的二氧化硅粉末。接着,使用图5所示的装置30,以下表I所示的条件,通过与实施例1同样的工序,对上述得到的二氧化硅粉末实施球化处理而不进行烧结,得到球化的二氧化硅粉末41。球化处理后,在清洗容器中加入上述粉末和超纯水,进行超声波清洗。进行超声波清洗后,利用网眼600 μ m的过滤器进行过滤。反复进行该操作直到附着于二氧化硅粉末的粒子表面上的微粉末消失。最后,在干燥用容器中加入清洗的粉末,在干燥机内使氩气以10L/min的流量流通的同时,在300°C的温度保持24小时,由此得到合成非晶态二氧化硅粉末。<比较例I >首先,相对于四氯化硅lmol,准备相当于55.6mol的量的超纯水。在容器内加入该超纯水,在氮气气氛中,将温度保持在25°C并进行搅拌的同时,添加四氯化硅并使其水解。添加四氯化硅后继续搅拌3小时,生成二氧化硅质的凝胶。此时,搅拌速度设为150rpm。接着,将上述二氧化硅质的凝胶移至干燥用容器并将其放入到干燥机,在干燥机内以15L/min的流量使氮气流通的同时,在250°C的温度干燥18小时而得到干燥粉。从干燥机取出该干燥粉,使用辊式粉碎机进行粉碎。此时,辊间隙调整为0.2mm、辊转速调整为50rpm来进行。对粉碎的干燥粉, 使用网眼100 μ m和网眼175 μ m的振动筛进行分级,得到平均粒径D5tl为136 μ m的二氧化硅粉末。接着,使用图5所示的装置30,以下表I所示的条件,通过与实施例1同样的工序,对上述得到的二氧化硅粉末实施球化处理,得到球化的二氧化硅粉末41。球化处理后,在清洗容器中加入上述粉末和超纯水,进行超声波清洗。进行超声波清洗后,利用网眼50 的过滤器进行过滤。反复进行该操作直到附着于二氧化硅粉末的粒子表面上的微粉末消失。最后,在干燥用容器中加入清洗的粉末,在干燥机内使氮气以10L/min的流量流通的同时,在200°C的温度保持48小时,由此得到合成非晶态二氧化硅粉末。<比较例2>首先,相对于四氯化硅lmol,准备相当于55.6mol的量的超纯水。在容器内加入该超纯水,在氮气气氛中,将温度保持在25°C并进行搅拌的同时,添加四氯化硅并使其水解。添加四氯化硅后继续搅拌3小时,生成二氧化硅质的凝胶。此时,搅拌速度设为150rpm。接着,将上述二氧化硅质的凝胶移至干燥用容器并将其放入到干燥机,在干燥机内以15L/min的流量使氮气流通的同时,在250°C的温度干燥18小时而得到干燥粉。从干燥机取出该干燥粉,使用辊式粉碎机进行粉碎。此时,辊间隙调整为0.2mm、辊转速调整为50rpm来进行。对粉碎的干燥粉,使用网眼50 y m和网眼150 u m的振动筛进行分级,得到平均粒径D5tl为113 iim的二氧化硅粉末。接着,使用图5所示的装置30,以下表I所示的条件,通过实施例1同样的工序,对上述得到的二氧化硅粉末实施球化处理,得到球化的二氧化硅粉末41。球化处理后,在清洗容器中加入上述粉末和超纯水,进行超声波清洗。进行超声波清洗后,利用网眼35 的过滤器进行过滤。反复进行该操作直到附着于二氧化硅粉末的粒子表面上的微粉末消失。最后,在干燥用容器中加入清洗的粉末,在干燥机内使氮气以10L/min的流量流通的同时,在200°C的温度保持48小时,由此得到合成非晶态二氧化硅粉末。
<比较例3>首先,相对于四甲氧基硅烷lmol,准备超纯水lmol、乙醇lmol。在容器内加入准备的超纯水、乙醇,在氮气气氛中,将温度保持在60°C并进行搅拌的同时,添加四甲氧基硅烷并使其水解。添加四甲氧基硅烷后搅拌60分钟,之后相对于四甲氧基硅烷lmol,进一步添加25mol的超纯水,继续搅拌6小时,生成二氧化娃质的凝胶。此时,搅拌速度设为lOOrprn。接着,将上述二氧化硅质的凝胶移至干燥用容器并将其放入到干燥机,在干燥机内以20L/min的流量使氮气流通的同时,在200°C的温度干燥24小时而得到干燥粉。从干燥机取出该干燥粉,使用辊式粉碎机进行粉碎。此时,辊间隙调整为0.2mm、辊转速调整为55rpm来进行。对粉碎的干燥粉,使用网眼75 pm和网眼150 的振动筛进行分级,得到平均粒径D5q为126 ii m的二氧化硅粉末。接着,使用图5所示的装置30,以下表I所示的条件,通过实施例1同样的工序,对上述得到的二氧化硅粉末实施球化处理,得到球化的二氧化硅粉末41。球化处理后,在清洗容器中加入上述粉末和超纯水,进行超声波清洗。进行超声波清洗后,利用网眼50 的过滤器进行过滤。反复进行该操作直到附着于二氧化硅粉末的粒子表面上的微粉末消失。最后,在干燥用容器中加入清洗的粉末,在干燥机内使氩气以10L/min的流量流通的同时,在300°C的温度保持12小时,由此得到合成非晶态二氧化硅粉末。
<比较例4>首先,相对于平均粒径D5tl为0.020 μ m、比表面积为90m2/g的气相二氧化硅Imol,准备超纯水13mol。在容器内加入准备的超纯水,在氮气气氛中,将温度保持在25°C并进行搅拌的同时,添加气相二氧化硅。添加气相二氧化硅后继续搅拌3小时,生成二氧化硅质的凝胶。此时,搅拌速度设为30rpm。接着,将上述二氧化硅质的凝胶移至干燥用容器并将其放入到干燥机,在干燥机内以10L/min的流量使氮气流通的同时,在300°C的温度干燥12小时而得到干燥粉。从干燥机取出该干燥粉,使用辊式粉碎机进行粉碎。此时,辊间隙调整为0.5mm、辊转速调整为30rpm来进行。对粉碎的干燥粉,使用网眼350 μ m和网眼550 μ m的振动筛进行分级,得到平均粒径D5tl为440 μ m的二氧化硅粉末。接着,使用图5所示的装置30,以下表I所示的条件,通过与实施例1同样的工序,对上述得到的二氧化硅粉末实施球化处理,得到球化的二氧化硅粉末41。球化处理后,在清洗容器中加入上述粉末和超纯水,进行超声波清洗。进行超声波清洗后,利用网眼250 μ m的过滤器进行过滤。反复进行该操作直到附着于二氧化硅粉末的粒子表面上的微粉末消失。最后,在干燥用容器中加入清洗的粉末,在干燥机内使氮气以20L/min的流量流通的同时,在200°C的温 度保持36小时,由此得到合成非晶态二氧化硅粉末。<比较例5>首先,相对于平均粒径D5tl为0.020 μ m、比表面积为90m2/g的气相二氧化硅Imol,准备超纯水13mol。在容器内加入准备的超纯水,在氮气气氛中,将温度保持在25°C并进行搅拌的同时,添加气相二氧化硅。添加气相二氧化硅后继续搅拌3小时,生成二氧化硅质的凝胶。此时,搅拌速度设为30rpm。接着,将上述二氧化硅质的凝胶移至干燥用容器并将其放入到干燥机,在干燥机内以10L/min的流量使氮气流通的同时,在300°C的温度干燥12小时而得到干燥粉。从干燥机取出该干燥粉,使用辊式粉碎机进行粉碎。此时,辊间隙调整为0.5_、辊转速调整为30rpm来进行。对粉碎的干燥粉,使用网眼400 μ m和网眼600 μ m的振动筛进行分级,得到平均粒径D5tl为480 μ m的二氧化硅粉末。接着,使用图5所示的装置30,以下表I所示的条件,通过实施例1同样的工序,对上述得到的二氧化硅粉末实施球化处理,得到球化的二氧化硅粉末41。球化处理后,在清洗容器中加入上述粉末和超纯水,进行超声波清洗。进行超声波清洗后,利用网眼200 μ m的过滤器进行过滤。反复进行该操作直到附着于二氧化硅粉末的粒子表面上的微粉末消失。最后,在干燥用容器中加入清洗的粉末,在干燥机内使氮气以20L/min的流量流通的同时,在200°C的温度保持36小时,由此得到合成非晶态二氧化硅粉末。<比较例6>首先,相对于平均粒径D5tl为0.020 μ m、比表面积为90m2/g的气相二氧化硅Imol,准备超纯水13mol。在容器内加入准备的超纯水,在氮气气氛中,将温度保持在25°C并进行搅拌的同时,添加气相二氧化硅。添加气相二氧化硅后继续搅拌3小时,生成二氧化硅质的凝胶。此时,搅拌速度设为30rpm。接着,将上述二氧化硅质的凝胶移至干燥用容器并将其放入到干燥机,在干燥机内以10L/min的流量使氮气流通的同时,在250°C的温度干燥24小时而得到干燥粉。从干燥机取出该干燥粉,使用辊式粉碎机进行粉碎。此时,辊间隙调整为0.5mm、辊转速调整为40rpm来进行。对粉碎的干燥粉,使用网眼400 y m和网眼625 y m的振动筛进行分级,得到平均粒径D5tl为492 ii m的二氧化硅粉末。接着,使用图5所示的装置30,以下表I所示的条件,通过实施例1同样的工序,对上述得到的二氧化硅粉末实施球化处理,得到球化的二氧化硅粉末41。球化处理后,在清洗容器中加入上述粉末和超纯水,进行超声波清洗。进行超声波清洗后,利用网眼200 u m的过滤器进行过滤。反复进行该操作直到附着于二氧化硅粉末的粒子表面上的微粉末消失。最后,在干燥用容器中加入清洗的粉末,在干燥机内使氩气以20L/min的流量流通的同时,在250°C的温度保持36小时,由此得到合成非晶态二氧化硅粉末。<比较例7>首先,相对于四氯化硅lmol,准备相当于55.6mol的量的超纯水。在容器内加入该超纯水,在氮气气氛中,将温度保持在25°C并进行搅拌的同时,添加四氯化硅并使其水解。添加四氯化硅后继续搅拌3小时,生成二氧化硅质的凝胶。此时,搅拌速度设为150rpm。接着,将上述二氧化硅质的凝胶移至干燥用容器并将其放入到干燥机,在干燥机内以15L/min的流量使氮气流通的同时,在250°C的温度干燥18小时而得到干燥粉。从干燥机取出该干燥粉,使用辊式粉碎机进行粉碎。此时,辊间隙调整为1.0臟、辊转速调整75印!11来进行。对粉碎的干燥粉,使用网眼800 y m和网眼1200 u m的振动筛进行分级,得到平均粒径D5tl为937 iim的二氧化硅粉 末。接着,使用图5所示的装置30,以下表I所示的条件,通过实施例1同样的工序,对上述得到的二氧化硅粉末实施球化处理,得到球化的二氧化硅粉末41。球化处理后,在清洗容器中加入上述粉末和超纯水,进行超声波清洗。进行超声波清洗后,利用网眼700 u m的过滤器进行过滤。反复进行该操作直到附着于二氧化硅粉末的粒子表面上的微粉末消失。最后,在干燥用容器中加入清洗的粉末,在干燥机内使氩气以10L/min的流量流通的同时,在250°C的温度保持36小时,由此得到合成非晶态二氧化硅粉末。<比较例8>首先,相对于四氯化硅lmol,准备相当于55.6mol的量的超纯水。在容器内加入该超纯水,在氮气气氛中,将温度保持在25°C并进行搅拌的同时,添加四氯化硅并使其水解。添加四氯化硅后继续搅拌3小时,生成二氧化硅质的凝胶。此时,搅拌速度设为150rpm。接着,将上述二氧化硅质的凝胶移至干燥用容器并将其放入到干燥机,在干燥机内以15L/min的流量使氩气流通的同时,在200°C的温度干燥48小时而得到干燥粉。从干燥机取出该干燥粉,使用辊式粉碎机进行粉碎。此时,辊间隙调整为0.8mm、辊转速调整为50rpm来进行。对粉碎的干燥粉,使用网眼700 y m和网眼1000 u m的振动筛进行分级,得到平均粒径D5tl为855 u m的二氧化硅粉末。接着,使用图5所示的装置30,以下表I所示的条件,通过与实施例1同样的工序,对上述得到的二氧化硅粉末实施球化处理,得到球化的二氧化硅粉末41。球化处理后,在清洗容器中加入上述粉末和超纯水,进行超声波清洗。进行超声波清洗后,利用网眼600 u m的过滤器进行过滤。反复进行该操作直到附着于二氧化硅粉末的粒子表面上的微粉末消失。
最后,在干燥用容器中加入清洗的粉末,在干燥机内使氮气以10L/min的流量流通的同时,在200°C的温度保持48小时,由此得到合成非晶态二氧化硅粉末。<比较例9>首先,相对于四氯化硅lmol,准备相当于55.6mol的量的超纯水。在容器内加入该超纯水,在氮气气氛中,将温度保持在25°C并进行搅拌的同时,添加四氯化硅并使其水解。添加四氯化硅后继续搅拌3小时,生成二氧化硅质的凝胶。此时,搅拌速度设为150rpm。接着,将上述二氧化硅质的凝胶移至干燥用容器并将其放入到干燥机,在干燥机内以15L/min的流量使氮气流通的同时,在250°C的温度干燥18小时而得到干燥粉。从干燥机取出该干燥粉,使用辊式粉碎机进行粉碎。此时,辊间隙调整为0.2mm、辊转速调整为50rpm来进行。对粉碎的干燥粉,使用网眼50 y m和网眼150 u m的振动筛进行分级,得到平均粒径D5tl为IOOum的二氧化硅粉末。最后,在烧结用容器中加入粉碎的粉末,将该烧结用容器投入到烧结炉,在烧结炉内使氮气以10L/min的流量流通的同时,在1200°C的温度保持48小时,由此得到合成非晶态二氧化硅粉末。将未实施该球化处理的二氧化硅粉末设为比较例9。< 比较例 10>首先,相对于四甲氧基硅烷lmol,准备超纯水lmol、乙醇lmol。在容器内加入准备的超纯水、乙醇,在氮气气氛中,将温度保持60°C并进行搅拌的同时,添加四甲氧基硅烷并使其水解。添加四甲氧基硅烷后搅拌60分钟后,相对于四甲氧基硅烷lmol,进一步添加25mol的超纯水,继续搅拌6小时,生成二氧化娃质的凝胶。此时,搅拌速度设为lOOrprn。接着,将上述二氧化硅质的凝胶移至干燥用容器并将其放入到干燥机,在干燥机内以20L/min的流量使氮气流通的同时,在200°C的温度干燥24小时而得到干燥粉。从干燥机取出该干燥粉,使用辊式粉碎机进行粉碎。此时,辊间隙调整为0.6mm、辊转速调整为IOOrpm来进行。对粉碎的干燥粉,使用网眼550 y m和剛艮650 y m的振动筛进行分级,得到平均粒径D5tl为590 u m的二氧化硅粉末。 最后,在烧结用容器中加入粉碎的粉末,将该烧结用容器投入到烧结炉,在烧结炉内使氩气以10L/min的流量流通的同时,在1200°C的温度保持48小时,由此得到合成非晶态二氧化硅粉末。将未实施该球化处理的二氧化硅粉末设为比较例10。< 比较例 11>首先,相对于平均粒径D5tl为0.020 U m、比表面积为90m2/g的气相二氧化硅lmol,准备超纯水13mol。在容器内加入准备的超纯水,在氮气气氛中,将温度保持在25°C并进行搅拌的同时,添加气相二氧化硅。添加气相二氧化硅后继续搅拌3小时,生成二氧化硅质的凝胶。此时,搅拌速度设为30rpm。接着,将上述二氧化硅质的凝胶移至干燥用容器并将其放入到干燥机,在干燥机内以10L/min的流量使氮气流通的同时,在300°C的温度干燥12小时而得到干燥粉。从干燥机取出该干燥粉,使用辊式粉碎机进行粉碎。此时,辊间隙调整为0.9mm、辊转速调整为150rpm来进行。对粉碎的干燥粉,使用网眼850 y m和网眼950 y m的振动筛进行分级,得到平均粒径D5tl为895 ii m的二氧化硅粉末。最后,在烧结用容器中加入粉碎的粉末,将该烧结用容器投入到烧结炉,在烧结炉内使氩气以10L/min的流量流通的同时,在1200°C的温度保持48小时,由此得到合成非晶态二氧化硅粉末。将未实施该球化处理的二氧化硅粉末设为比较例11。
1.一种合成非晶态二氧化硅粉末,是对造粒的二氧化硅粉末实施球化处理后,清洗并干燥而得到的平均粒径D5tl为10 2000 u m的合成非晶态二氧化硅粉末, BET比表面积除以由平均粒径D5tl计算出的理论比表面积得到的值超过1.35且1.75以下,真密度为2.10 2.20g/cm3,粒子内孔隙率为0 0.05,圆形度为0.50以上0.75以下以及和未熔解率大于0.25且0.60以下。
2.根据权利要求1所述的合成非晶态二氧化硅粉末,是对所述造粒的二氧化硅粉末进行烧结后,实施所述球化处理的合成非晶态二氧化硅粉末, 满足碳浓度小于2ppm或氯浓度小于2ppm中的任意一者或该两者。
3.根据权利要求2所述的合成非晶态二氧化硅粉末,所述造粒的二氧化硅粉末是通过使四氯化硅水解而生成二氧化硅质的凝胶,干燥该二氧化硅质的凝胶而成为干燥粉,粉碎该干燥粉后,进行分级而得到的二氧化硅粉末, 碳浓度小于2ppm。
4.根据权利要求2所述的合成非晶态二氧化硅粉末,所述造粒的二氧化硅粉末是通过使有机系硅化合物水解而生成二氧化硅质的凝胶,干燥该二氧化硅质的凝胶而成为干燥粉,粉碎该干燥粉后,进行分级而得到的二氧化硅粉末, 氯浓度小于2ppm。
5.根据权利要求2所述的合成非晶态二氧化硅粉末,所述造粒的二氧化硅粉末是通过使用气相二氧化硅生成二氧化硅质的凝胶,干燥二氧化硅质的凝胶而成为干燥粉,粉碎该干燥粉后,进行分级而得到的二氧化硅粉末, 碳浓度小于2ppm,氯浓度 小于2ppm。
6.一种合成非晶态二氧化硅粉末的制造方法,其特征在于,按顺序包括: 造粒工序,生成二氧化硅质的凝胶,干燥该二氧化硅质的凝胶而成为干燥粉,粉碎该干燥粉后,进行分级,由此得到二氧化硅粉末; 利用热等离子体的球化工序,在以预定的流量导入氩气并以预定的高频输出功率产生等离子体的等离子体炬内,以预定的供给速度投入所述造粒工序中所得到的二氧化硅粉末,在从2000°C至二氧化硅的沸点的温度加热并熔融; 清洗工序,去除附着于所述球化工序后的球化二氧化硅粉末表面上的微粉;和 干燥工序,干燥所述清洗工序后的二氧化硅粉末, 将所述球化工序中的氩气的流量调整为50L/min以上、且在高频输出功率设为A、二氧化硅粉末的供给速度设为B时,以A/B的值为3.0X IO3以上且小于1.0X IO4的方式调整后进行,其中,高频输出功率的单位为W,二氧化硅粉末的供给速度的单位为kg/hr,A/B的单位为 W kg/hr, 得到平均粒径D5tl为10 2000 u m、BET比表面积除以由平均粒径D5tl计算出的理论比表面积得到的值超过1.35且1.75以下、真密度为2.10 2.20g/cm3、粒子内孔隙率为0 0.05、圆形度为0.50以上0.75以下以及未熔解率大于0.25且0.60以下的合成非晶态二氧化硅粉末。
7.根据权利要求6所述的合成非晶态二氧化硅粉末的制造方法,所述造粒工序为使四氯化硅水解而生成二氧化硅质的凝胶,干燥该二氧化硅质的凝胶而成为干燥粉,粉碎该干燥粉后,进行分级,由此得到平均粒径D5tl为10 3000 u m的二氧化硅粉末的工序。
8.根据权利要求6所述的合成非晶态二氧化硅粉末的制造方法,所述造粒工序为使有机系硅化合物水解而生成二氧化硅质的凝胶,干燥该二氧化硅质的凝胶而成为干燥粉,粉碎该干燥粉后,进行分级,由此得到平均粒径D5tl为10 3000 μ m的二氧化硅粉末的工序。
9.根据权利要求6所述的合成非晶态二氧化硅粉末的制造方法,所述造粒工序为使用气相二氧化硅生成二氧化硅质的凝胶,干燥该二氧化硅质的凝胶而成为干燥粉,粉碎该干燥粉后,进行分级,由此得到平均粒径D5tl为10 3000 μ m的二氧化硅粉末的工序。
10.一种合成非晶态二氧化硅粉末的制造方法,其特征在于,按顺序包括: 造粒工序,生成二氧化硅质的凝胶,干燥该二氧化硅质的凝胶而成为干燥粉,粉碎该干燥粉后,进行分级,由此得到二氧化硅粉末; 烧结工序,对所述造粒工序中所得到的二氧化硅粉末在800 1450°C的温度进行烧结; 利用热等离子体的球化工序,在以预定的流量导入氩气并以预定的高频输出功率产生等离子体的等离子体炬内,以预定的供给速度投入所述烧结工序中所得到的二氧化硅粉末,在从2000°C至二氧化硅的沸点的温度加热并熔融; 清洗工序,去除附着于所述球化工序后的球化二氧化硅粉末表面上的微粉;和 干燥工序,干燥所述清洗工序后的二氧化硅粉末, 将所述球化工序中氩气的流量调整为50L/min以上且在高频输出功率设为A、二氧化硅粉末的供给速度设为B时,以A/B的值为3.0X IO3以上且小于1.0X IO4的方式调整后进行,其中,高频输出功率的单位为W,二氧化硅粉末的供给速度的单位为kg/hr,A
合成非晶态二氧化硅粉末及其制造方法
- 专利详情
- 全文pdf
- 权力要求
- 说明书
- 法律状态
查看更多专利详情
下载专利文献
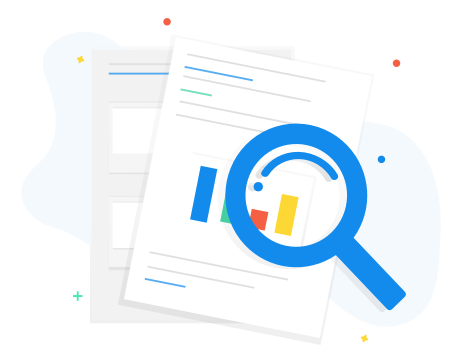
下载专利
同类推荐
-
许浮萍王新, 王桂英
您可能感兴趣的专利
-
A.L.邦奇, P.G.哈里斯J·H·阿伦斯J·H·阿伦斯孙义兴孙义兴关野雅人, 草野正嗣
专利相关信息
-
蒂莫·皮沃斯基, 贝恩德·威尔维斯克里斯托弗·罗斯克里斯托弗·罗斯丘云灵, 熊玉李宗武吴健, 徐刘彬阿德里亚那·布里西奥, 阿德里亚那 布里西奥