碳化硅晶须增强陶瓷复合材料及其制造方法
- 专利详情
- 全文pdf
- 权力要求
- 说明书
- 法律状态
专利名称::碳化硅晶须增强陶瓷复合材料及其制造方法::本发明一般地说是关于用碳化硅晶须增强的陶瓷复合材料。该复合材料在一些需要高温物理和化学稳定性、耐磨损及抗脆性损坏的应用中,具有应用性。这些应用之一就是金属的切削或者机加工。金属的切削或机加工广泛地用于机械制造领域中。典型的机加工操作包括修刨、刨削、铣削、刮削、拉削、磨削、锯、车削、镗孔、钻孔和铰孔。有些操作,如锯,同时作用在内、外表面上,而其它操作仅作用在内表面(铰孔)、或者外表面(铣削)。机加工操作中常用的生产率测量方法是单位时间内从工件上去除的金属的总量。切削刀具性能的具体参数包括被切削材料、切削速度、切削深度,进刀速度和刀具寿命。Tipnis在“CuttingToolWear”,“WearControlHandbook,P891-893”中指出,磨损是切削刀具的主要损坏方式。其它损坏方式如断裂、剥落、软化或热破裂,将导至灾难性的和无规律的损坏。Tipnis指出,尽管磨损是主要的损坏方式,但却没有一个能预侧刀具磨损的理论。因此,实际采用的方法是将刀具磨损数据与工件材料的去除量和刀具寿命相平衡来使用和加工。Tipnis概括了对切削刀具的基本要求,这些要求如下“(a)它必须比所切削的材料更坚硬以便能够承受切削时产生的应力;(b)它必须具有一定韧性使其不至于在该力作用下断裂;(c)它必须能够承受在刀具切削界面产生的高温而不变形;及(d)磨损不能太快。”Tipnis认为“切削刀具最重要的性能是热硬度(即,在刀具刃口产生高温时抗软化),韧性(即在冲击下耐破损),化学稳定性和反应性(即,在刃口所产生的温度和压力下抗分解和转化),和元素扩散趋势(即在高切削温度下抗磨顶槽能力)”。本文中所说的术语“韧性”是指抗过早损坏能力,特别是碳化硅晶须增强陶瓷刀具在切削开始时的抗过早损坏能力。该“韧性”未必等于按韧性的断裂力学定义在室温测定的KIC。切削性能与说明这些定义的数据并没有相对应的关系。M.C.Shaw,在MetalCuttingPrinciples,P334(Oxford,1984)中强调了在选择切削刀具材料的三个指标。这些指标是(a)在使用温度下的物理和化学稳定性;(b)耐磨损性和(c)耐脆性损坏能力。例如在使用温度下化学性质不稳定会发生如熔化、过量扩散、或熔焊和切削的结合,使刀具材料过快损坏。Shaw在P353-357建议,在选择切削刀具材料时要考虑三个关键的物理性能指标。一个指标是四点抗折试验(军方标准1942b)的抗折强度;第二个指标是用维克斯压头(Vickersindentor)测得的硬度;第三个指标是抗断裂性能。通常用断裂韧性作为耐脆性损坏的指标,采用单槽光束技术(SingleNotchBeamTechnique)或者山形缺口技术(ChevronNotchTechnique)测试断裂韧性。抗裂纹扩展性或帕姆奎斯特韧性(PalmqvistToughness)的测定与硬度试验一同进行。耐磨性(w)是硬度和韧性的函数。E.D.Whitney在《国际粉末冶金》(PowderMelallurgyInternational)Vol.15,No.4,P201-205(1983)中一篇题为“现代陶瓷切削刀具材料”的文章中指出,刀具材料应足够坚硬以抵抗切削中的材料磨损。作为良好的切削刀具,硬度是必须的条件,但并不充分。令人满意的切削刀具材料必须具有足够的韧性和强度以承受切削过程中产生的机械冲击或类似情况。Wei在U.S.Re.32843中公开了以增加韧性和抗断裂性为特征的陶瓷复合材料,并公开了这种复合材料的制造方法。该复合材料中含有5-60%(体积)的碳化硅晶须,它们均匀地分布在陶瓷材料基体中。这种晶须为单晶结构,直径约0.6微米,长度10~80微米。该陶瓷材料可以是氧化铝、莫来石或碳化硼。Wei指出,含有单晶晶须的陶瓷复合材料比不含单晶晶须的陶瓷材料的断裂韧性有明显的改善。他认为晶须可以吸收裂化能量。Rhodes等人在美国专利4,789,277中公开了一种用烧结的复合材料作切削刀具切削金属的方法。该复合材料的基体中主要有氧化铝和在其基体中均匀分布的2-40%(体积)的碳化硅晶须。这种晶须为单晶结构,平均直径约0.6微米,长径比为15至150。本发明的目的是提供一种含有陶瓷晶须的陶瓷复合材料,当其用作,例如,切削刀具时其耐磨性能得到提高。另外,还希望这种改进比简单地依靠改进机械性能,如韧性的先有技术更为可行。本发明是一种含有陶瓷材料基体的致密的晶须增强陶瓷复合材料,该陶瓷材料基体中均匀分布着5-40%(体积),双峰分布、化学兼容的单晶晶须。晶须可以是碳化硅、氮化硅、碳化钛、莫来石、二硼化钛、氧化铝、氧化镁或氮化硼,但是要求这些所选用的晶须与陶瓷基体材料不同,其双峰分布以晶须宽度对应的晶须体积为基础,并且包含的粗单晶晶须与细单晶晶须的体积比为0.1至1。致密前,粗晶须的平均直径大于或等于0.5微米,小于1.0微米,直径范围约为0.1~3微米。致密前,细晶须的平均直径大于或等于0.1微米小于0.5微米,直径范围为0.01~1.3微米。和等量的粗晶须或细晶须相比,这种双峰分布的晶须提高了刀具的切削性能。所希望的晶须是单晶碳化硅晶须。本发明使用的碳化硅晶须为单晶,其中含有β相和α与β混合相碳化硅。这些晶须从两种平均直径范围不同的晶须中选出,形成以体积为基的双峰尺寸分布。称为“粗晶须”的晶须的平均直径范围为0.5微米至小于1.0微米,其直径范围为0.1-3微米。称为“细晶须”的晶须的平均直径范围为0.1微米至小于0.5微米,其直径范围为0.01~1.3微米。粉末状陶瓷基体材料和晶须转变成致密的晶须增强陶瓷复合材料之前,以体积为基准的明显的晶须双峰分布,在形成的致密复合材料中变化很小。对应的晶须体积百分比与晶须宽度相比较而作出的曲线为两条高斯曲线,从而证实了双峰分布的存在。该曲线图用五点平滑连接法绘制(通道宽度0.1和0.2微米)。为得到该图的数据,把用标准金相方法制备的致密的复合材料的磨光截面在扫描电子显微镜(SEM)下放大5000倍。扫描电子显微镜的图象被传到Zeiss-Kontron图象处理系统。用标准颗粒分析参数(Standardsizingparameters)测量DMIN(纤维宽度)和DMAX(纤维长度)。每个晶须或微粒的体积V用V=DMIN2DMAX计算。用五点平滑连接方法将数据连接并用带两条特定高斯曲线的适当函数RS/1处理。“A”形的数据曲线表明了典型的双峰分布。由于粗晶须的体积大,少量粗晶须就可与大量细晶须占据相等的体积。实例表明,用氧化铝和34%(体积)的碳化硅晶须(14%粗晶须,20%细晶须)的混合物制备致密复合材料的磨光截面的扫描电子显微图象中所统计的2356条晶须中只有77条的宽度大于1.4微米,这77条晶须只占统计数量的3%,但其占据的体积大约是统计晶须体积的68%。因此,与仅用晶须数相比,对应的粗晶须占据的体积与细晶须占据的体积相比较提供了一幅更清楚的晶须分布图。使用亚微米双峰分布的单晶碳化硅晶须比只从一种分布方式选用同样数量的晶须在切削性能方面有所提高。实例表明10%(体积)双峰分布的晶须与25%(体积)只含粗或细单晶碳化硅晶须相比,所得到的切削性能至少是一样好。双峰分布的单晶碳化硅晶须的体积范围以占复合材料总体积的5-40%较为合适,最好是10-34%(体积)。晶须含量低于5%则达不到所要求的韧性,晶须含量超过40%(体积)会造成加工困难,特别是在热压处理过程中。如能解决这些加工难题可以使用超过40%(体积)的晶须。双峰分布中粗晶须与细晶须的合适比例为0.3至1.0,最好是0.4至0.8。碳化硅晶须长径的合适比例为10或更小,最好是10。如该比例大于15,增强复合材料中沿晶须横向产生裂纹的可能超过沿其长度方向产生的可能。因此,较大的长径比不会带来特殊的好处,但也不会产生不利的效果。长径比小于2.5不会产生有利效果,实际上还可能会产生一严重的问题,即增加了形成的复合材料脆性。单晶碳化硅晶须通常是以晶须与少量碳化硅颗粒的混合物的形式获得。实际上很难做到从晶须中分离出颗粒而不造成晶须的大量损失。幸好,少量碳化硅颗粒的存在不会对形成的复合材料的性能造成不利影响。但必须小心,应避免碳化硅颗粒的过量,因为脆性和偶然发生断裂的可能随颗粒量的增加而增加。碳化硅晶须特别适合于本发明的目的。然而使用其他晶须,例如从氮化硅、碳化钛、莫来石、二硼化钛、氧化铝、氧化镁或氮化硼这些材料制成的晶须也可以获得满意的结果。该晶须应选自一种具有化学兼容性的材料并与基体材料不同。这里所说的“化学兼容性”是指晶须与基体材料不反应生成新相。本发明的陶瓷复合材料适合在足够的压力和温度条件下热压陶瓷材料颗粒和两种不同尺寸的碳化硅晶须的均匀混合物制备形成密度大于约99%理论密度的陶瓷材料。如果需要,可以用高温等静压或烧结法制备陶瓷复合材料。在热压前需要将双峰分布的碳化硅晶须与陶瓷粉末混合均匀。可以用任何适合的方法混合该混合物以使晶须在粉末中均匀分布,并使陶瓷粉末结块、晶须结团和晶须断裂最少。当陶瓷材料是氧化铝时,特别适合用带有3/16英吋(0.48cm)或更小氧化铝球的磨碎搅拌机混合。搅拌过程中必须小心,即使不能避免也要尽量减少晶须的损坏或断裂。将pH值大约10.5的含水、分散剂和充足氢氧化铵的溶液与氧化铝粉以每分钟330转混合大约30分钟以形成均匀分散体。将用水浸湿的大碳化硅晶须、分散剂和极少量的氢氧化铵加入该均匀的分散体中并且同时进行混合。在大碳化硅晶须全部加入后10分钟,将用水浸湿的小碳化硅晶须加到该分散体中,同时继续混合。小晶须全部加入后两分钟停止混磨,把里面的东西倒在30号筛网(550微米)上分离出磨球。对磨球进行洗涤并配入去离子水,得到的东西转变成加有去离子水的稀释浆。在pH值为7.2时用50%的硝酸对该稀释浆进行絮凝。将絮凝物放在100℃的空气循环炉中干燥。干燥物用60号(250微米)筛网筛选,得到最大凝结块约为100微米的粉末状混合物。将该粉末状混合物成型,得到适当的外形并热压成密度大于约99%理论密度的陶瓷材料。热压可以在带有冲头或冲压元件的感应炉或电阻加热炉中完成,冲头或冲压元件由能够承受所需压力和温度而不与复合材料的成分发生有害反应的石墨或其它合适的材料构成。以一个适当的方法为例,将粉末状混合物注入一个长3英吋(7.6cm)、宽2.5英吋(6.4cm)、深0.5英吋(1.3cm)的石墨冲模中。向冲模施加1000Psig(大约70kg/cm2)的起始压力,同时用约30分钟将温度从室温升到约1200℃,然后将压力增到5000Psig(约350kg/cm2)并保持在这一水平,同时用约30分钟使温度升到1725℃。把冲模在此压力和温度下再保持45分钟。然后,用两小时使冲模冷却到100℃,并从1500℃开始逐渐减压。上面所述的热压操作及下面的实施例是单方向或单轴向热压粉末状混合物,以使复合材料中的晶须优选成直线并无规则地分布在一平面上或其轴与热压轴垂直。用其他处理方法,如高温等静压和快速全向压缩也可得到满意的效果。下面的实施例仅仅是对本发明进行说明而不应把它看作是对本发明范围的限制。除非另有说明,所有成分和百分比都以重量为基准。阿拉伯数字表示本发明范围内的实施例,字母表示对比例。实施例1用66%(体积)的氧化铝粉末(Al2O3,颗粒尺寸0.8μm)和34%(体积)的碳化硅晶须的混合物制备一组热压材料。将该混合物用上文提到的混合和热压步骤进行制备及热压。氧化铝粉末选用Reynolds金属公司RC-HP级产品。碳化硅晶须是所说的粗晶须、细晶须或它们的混合物。粗晶须的平均直径为0.94μm,平均长径比约10.7(范围从1.1至77)从AmericanMetrix商购。细晶须的平均直径为0.22至0.26μm,平均长径比约10.6,从TatehoChemicalIndustriesCo.,Ltd商购。晶须的体积百分比及大小晶须之间的比例(包括两种晶须的尺寸)连同形成的复合材料的切削性能都在表Ⅰ中列出。粗晶须和细晶须在表Ⅰ中分别用字母“C”和“F”表示。将热压材料按美国国家标准局(A.N.S.I)标准用金刚石磨成KNG45型切削刀具镶块。刃口倒角成20度角,宽0.003英吋(0.008cm)。用装有可变速(DC)设备的30马力LeBlond1610重型车床对镶块进行单刃车削试验。切削刀具安装在钨钛钴类硬质合金(Kennametal)座上。在一直径4英吋(10.2cm)、长12英吋(30.5cm)、硬度为241布氏硬度系数的铬镍铁合金(Inconel)718工件上对刀具进行试验。用5号组合钻及锥口钻给工件钻一中心孔,用一个12英吋(30.5cm)、自动定心的三爪卡盘将工件夹住3英吋(7.6cm)长,并用4号莫氏锥度Nirol活顶针(livecenter)将工件固定在车床上。将刀座和带有活顶针的尾架主轴的悬垂部分调到最小以保障最大的稳定性。机器以每分钟750英尺的切削速度旋转,每转的进刀速度0.007英吋,切削深度0.100英吋。不使用切削润滑液。刀具连续走过并检验其刃口的侧面磨损和剥落。切削一分钟后停止试验,按均匀磨损量测量其切削性能并在表Ⅰ中例出。表*非常脆,试验时有断裂的趋势表Ⅰ中的数据表明,至少从均匀磨损这方面讲,用粗、细晶须混合物的刀具的切削性能比只用粗晶须或细晶须的刀具的切削性能有了明显的改善。晶须混合物比单一尺寸的粗或细晶须提供了更为一致的结果。用本发明的其他复合材料也可以得到同样的结果。实施例2用不同的粗晶须重复实施例1的步骤。这种晶须的平均直径为0.67微米,平均长径比为11.0,从AmericanMatrix商购。切削刀具镶块的制备步骤如实施例1,其切削性能列在表Ⅱ中。实施例3用1-3号复合材料的样品重复实施例1的步骤制成热压材料。按前面所述的步骤用接有Zeiss-Kontron图象处理系统的扫描电子显微镜(SEM)对形成的材料进行检验。在对热压材料样品的检验过程中,从11个区域统计出2356个晶须。由下面的等式计算出碳化硅晶须的附加值,以相对体积百分数表示,其中X是DMIN(纤维宽度)相对体积百分比=5.475e-(x-1.004)2/1.56+7.47e-(x-2.401)2/0.416相对体积百分比表示以晶须总体积为基准的给定的体积百分比。最平滑的数据连接曲线图是两条高斯曲线分布。曲线下的面积给出的体积百分比如下大约56%的细晶须及44%的粗晶须。细和粗晶须各自对应的最大分布尺寸为1.0μm和2.4μm。粗、细晶须的体积比是0.8。1-3号复合材料的样品中含有14%(体积)的粗晶须、20%(体积)的细晶须。将这些数据转换成相对体积百分比得出下例数值粗晶须约41%,细晶须约59%。该数据表明碳化硅晶须最初的双峰分布在热压后仍然保留着。用本发明所述的其他复合材料也可获得同样的结果。实施例4改变碳化硅晶须的体积百分比重复实施例1的步骤。所有样品中都保持1-3号样品中粗、细晶须的比例。按实施例1的步骤制造切削刀具并试验其均匀磨损。试验结果与碳化硅晶须的体积百分比一起在表Ⅲ中列出。表Ⅲ</tables>表Ⅲ的数据表明了两个结论。第一,百分之四十和更高体积的晶须填料造成的加工困难无疑会降低切削性能。当晶须填料超过45%(体积)时切削性能进一步变坏。第二,10%(体积)的晶须混合物比34%(体积)的单种晶须提供更好的切削性能。即使是晶须混合物,当其体积低于10%时,切削性能也会降低。这一结论不用过多的试验就容易证实。本发明的其他复合材料具有同样的结果。实施例5和对比例A-C用不同的陶瓷材料重复实施例1的热压步骤。陶瓷材料为一种混合物,其中含有92%UBE工业公司商业标号UBE-SN-10的氮化硅,6%的氧化钇和2%实施例1中用的氧化铝。所有的百分比都以混合物的重量为基准。晶须的数量在表Ⅳ中列出。用金刚石将形成的热压材料磨成切削刀具镶块以便与普通切削刀具作比较。按美国国家标准局(A.N.S.I)标准SNG434型制造镶块,刃口倒角30度,0.006英吋(0.015cm)宽的倒角。用带有5马力可变速度工作台的40马力辛辛那提#5单主轴、升降台和座架的立式铣床的中央铣面试验该镶块。工件是4英吋宽(10.2cm)、12英吋(30.5cm)长、硬度为170布氏硬度系数的30级灰铸铁。所用铣刀是直径12英吋(30.5cm)、轴向前角-5°、径向前角-5°及15°导角的单齿铣刀。机器以每分钟3000表面英尺(公制的)的切削速度旋转,切削深度0.60英吋(0.152cm),每转的进刀速度0.013英吋(0.033cm)。铣刀的中心线与工件的中心线同轴。不使用切削润滑液。铣刀在铸铁工件上连续走过。每次走过后检验刃口的侧面磨损和剥落。用30倍的显微镜测到侧面磨损或剥落的深度超过0.010英吋(0.025cm)时停止试验。表Ⅳ中用去掉的材料的立方英吋(立方厘米)表示铣刀的切削性能。对比例C是Boride产品公司商业标号U.S.-20的非增强氮化硅切削刀具。表Ⅳ表Ⅳ中的数据表明使用粗和细晶须混合物比只用粗或细晶须的优越性存在于陶瓷复合材料中,但氧化铝除外,这些数据连同表Ⅰ中的数据证实双峰分布晶须增强的切削刀具适用于不同的切削应用。用本发明所述的其他复合材料也可以得到同样的结果。权利要求1.一种致密的、晶须增强陶瓷复合材料,它包括一种陶瓷材料基体,该基体含有5-40%(体积)的均匀分布在陶瓷基体材料中的双峰分布、化学兼容的碳化硅、氮化硅、碳化钛、莫来石、二硼化钛、氧化铝、氧化镁或氮化硼的单晶晶须,而且所提供的晶须与陶瓷基体材料不同,其双峰分布是以不同晶须宽度对应的晶须体积为基础的,实质上包含的粗单晶晶须与细单晶晶须的体积比为0.1至1,在致密化前粗晶须的平均直径大于或等于0.5微米但小于1.0微米,其直径范围从0.1微米至3微米,在致密化前,细晶须的平均直径大于或等于0.1微米但小于0.5微米,其直径范围从0.01微米至1.3微米,这种双峰分布与等量的粗晶须或细晶须相比在切削性能方面有所提高。2.根据权利要求1的复合材料,其中碳化硅晶须的体积百分比为10%至34%。3.根据权利要求1的复合材料,其中体积比为0.3至1.0。4.根据权利要求1的复合材料,其中陶瓷材料是氧化铝、氮化硅、莫来石、二氧化硅、AlN及其混合物。5.根据权利要求1的复合材料,其中晶须的长径比约大于3。6.一种用权利要求1的复合材料制造的切削刀具。7.一种致密的、晶须增强陶瓷复合材料其特征在于,一种陶瓷材料基体,其中均匀分布着5-40%(体积)的双峰分布的单晶碳化硅晶须,其双峰分布以不同晶须宽度对应的晶须体积为基础,包含的粗单晶碳化硅晶须与细单晶碳化硅晶须的体积比为0.1至1,在致密化前,粗晶须的平均直径大于或等于0.5微米但小于1.0微米,直径范围从0.1微米至3微米,在致密化前,细晶须的平均直径大于或等于0.1微米但小于0.5微米,直径范围从0.01微米至1.3微米,这种双峰分布与等量的粗晶须或细晶须相比在切削性能方面有所提高。全文摘要使用双峰分布的“粗”和“细”的亚微米级、单晶碳化硅晶须增强陶瓷材料与使用相等数量的粗或细晶须相比在切削性能方面有所提高。粗晶须的平均直径范围从0.5到小于1.0微米,细晶须的平均直径范围从0.1到小于0.5微米。这种双峰分布的晶须在所形成的晶须增强陶瓷复合材料中占体积的5-40%。所形成的材料用作切削刀具。文档编号C04B35/80GK1053603SQ9011042公开日1991年8月7日申请日期1990年12月12日优先权日1989年12月13日发明者阿历山大·J·派齐克申请人:唐化学原料公司
查看更多专利详情
下载专利文献
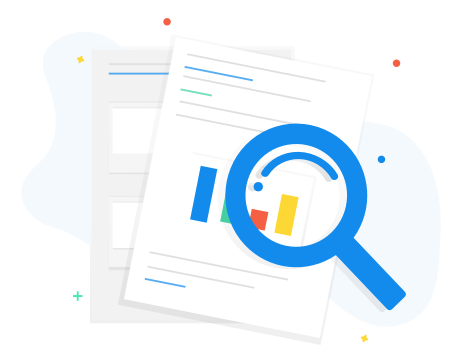
下载专利
同类推荐
-
名取荣治名取荣治汤玉斐杨建
您可能感兴趣的专利
-
杨建郑木莲, 李欣陈秀丽李贺军
专利相关信息
-
李贺军王红云王红云