专利名称:一种复合耐火窑具的制备方法在电子陶瓷烧成过程中,为使制品获得良好的外观,防止烧结变形,避免高温烧结 时电子陶瓷与所用窑具发生不良反应,一般在电子陶瓷与窑具接触部位使用耐高温、低挥 发、惰性强的氧化锆耐火材料,氧化锆耐火材料的使用方式通常包括以下几种(1)整体做 成纯氧化锆质窑具;⑵以刚玉-莫来石、莫来石-堇青石、刚玉-堇青石等为窑具主体,然 后在其表面喷射或涂抹氧化锆涂层;(3)以刚玉、刚玉_莫来石、刚玉-堇青石等为窑具主 体,在其上铺垫氧化锆隔离砂或氧化锆隔离粉。在使用过程中发现以上三种氧化锆耐火材料的使用方式都存在一定的缺陷,方式 (1)纯氧化锆质窑具存在自重大、蓄热大、原料成本高、烧结困难等问题;方式(2)存在氧 化锆涂层的均勻性差,涂层与窑具主体的结合性差,使用过程中氧化锆涂层容易粉化、分层 起皮和脱落等问题,进而造成电子陶瓷制品的局部污染;方式(3)氧化锆隔离砂或氧化锆 隔离粉不易撒均,使用过程容易因隔离砂和隔离粉的自身烧结问题出现错位和移动,导致 电子陶瓷产品的烧结变形,而且氧化锆隔离砂或氧化锆隔离粉多次使用容易受到污染,进 而影响电子陶瓷产品的质量和性能。
为克服现有电子陶瓷烧成用耐火窑具制备技术方面的不足,本发明提供了一种生 产具有成本低、涂层均勻、整体性好、不易变形、挥发度低等特点的复合耐火窑具的制备方 法;同时该制备方法科学合理、简单易行。为完成上述发明目的所采用的技术方案是首先,选择一种烧制好的窑具主体,通 过对窑具主体进行表面打磨和采用表面活性剂进行活性预处理,使窑具主体的薄厚均勻和 使其表面具有一定的吸附活性;然后,采用负压浸渍方法把预先制备好的高分散、高稳定性 氧化锆料浆均勻吸附到窑具主体的表面,并充分填充到窑具主体的气孔或微裂纹中;最后, 经干燥和高温烧成即得本发明所述的复合耐火窑具。本发明所述的一种复合耐火窑具的制备方法,所述制备方法包括如下步骤(1)窑具主体的选择根据电子陶瓷的种类和烧成条件选择一种和其性能相匹配 的窑具主体;当电子陶瓷的烧成温度较高时,选择一种高熔点的窑具主体,当电子陶瓷的烧成 温度较低时,选择一种低熔点的窑具主体;选择依据是所选的窑具主体要满足在电子陶 瓷多次烧成过程中不易变形、低挥发和低污染;(2)窑具主体的预处理对选择的窑具主体进行表面打磨,打磨平整后放入到表 面活性剂熔液中浸泡1 2小时,干燥后备用;4(3)氧化锆料浆的制备把电熔氧化锆微粉和水溶液按一定比例调和,再加入分 散剂和防沉剂,并用氨水调节溶液PH值后,在搅拌机上搅拌制成高分散、高稳定性的氧化 锆料浆;(4)负压浸渍将处理过的窑具主体放入到容器中,利用抽真空设备抽取真空,待 窑具主体中的气体充分排出后,在真空状态下加入氧化锆料浆充分饱和窑具主体,使料浆 充分填充气孔或微裂纹,并附着在窑具主体的表面;(5)复合窑具的干燥将复合窑具从容器中取出,自然干燥36 72小时,待其表 面的氧化锆料浆涂层凝固后,再将其放入干燥箱中于110 130°C干燥24 48小时,使窑 具充分干燥;(6)复合窑具的烧成将干燥后的复合窑具胚体放入高温窑中烧成,烧后的制品 经拣选和包装后即可投入使用。上述一种复合耐火窑具的制备方法中,所述的窑具主体可以是烧制好的刚玉-莫 来石质、莫来石_堇青石质、刚玉_堇青石质或红柱石质氧化物窑具中任何一种;上述一种复合耐火窑具的制备方法中,所述的活性预处理所用的表面活性剂可以 为草酸或柠檬酸中的一种;上述一种复合耐火窑具的制备方法中,所述的电熔氧化锆微粉是指以CaO 作稳定剂的电熔氧化锆微粉;电熔氧化锆微粉原料的化学组成为CaO 3. 8-4.8%, Zr0294-95 . 8%, Al2O3 < 0. 4%, SiO2 < 0. 3% ;粒度 < 3ym ;上述一种复合耐火窑具的制备方法中,电熔氧化锆微粉与水熔液的质量比为 1 05 1 0. 25。上述一种复合耐火窑具的制备方法中,所述的分散剂为聚丙烯酸胺或聚乙二醇中 的一种,分散剂的含量为电熔氧化锆微粉和水溶液总重量的0.5 1.5% (外加);上述一种复合耐火窑具的制备方法中,所述的防沉剂为CMC,防沉剂的含量为电熔 氧化锆微粉和水溶液总重量的0. 3 0. 5% (外加);上述一种复合耐火窑具的制备方法中,所述的高分散、高稳定性的氧化锆料浆的 PH值为9 10 ;上述一种复合耐火窑具的制备方法中,所述的复合窑具的烧成温度为1450°C 1640 0C ο本发明具有以下优异的性能和特点(1)根据电子陶瓷的种类和烧成条件选择一种和其性能相匹配的窑具主体,可以 降低生产成本,同时可以减轻窑具自重和减少蓄热;(2)通过窑具主体的预处理,使窑具主体的薄厚更加均勻和氧化锆料浆在窑具主 体表面得到更充分粘附,保证了高温烧成过程中涂层与窑具主体更好的烧结在一起;(3)通过制备高分散、高稳定性氧化锆料浆,保证了涂层的均勻性,解决了传统复 合窑具存在的涂层均勻性差的问题;(4)负压浸渍方法的使用,使得窑具主体孔径或裂纹内的料浆与其表面粘附的料 浆形成了一个交错相连的整体,避免了分层起皮和脱落现象的发生;同时,料浆的充分填充 和充分包裹,在窑具主体表面形成了严密的保护层,减少或避免了窑具主体中的低融物在 使用过程中的挥发对电子陶瓷产品的污染。
本发明公开了一种复合耐火窑具的制备方法。该制备方法是首先选择一种窑具主体;通过对窑具主体进行表面预处理,使其表面具有一定的吸附活性;并采用负压浸渍方法把预先制备好的稳定氧化锆料浆均匀吸附到窑具主体的表面和填充到窑具主体的气孔或微裂纹中;经干燥和高温烧成即得本发明所述的复合耐火窑具。采用该发明生产的复合窑具具有成本低、涂层均匀、整体性好、不易变形和挥发度低等优点,该制造方法还具有科学合理、易于推广与应用等优点。
一种复合耐火窑具的制备方法
- 专利详情
- 全文pdf
- 权力要求
- 说明书
- 法律状态
查看更多专利详情
下载专利文献
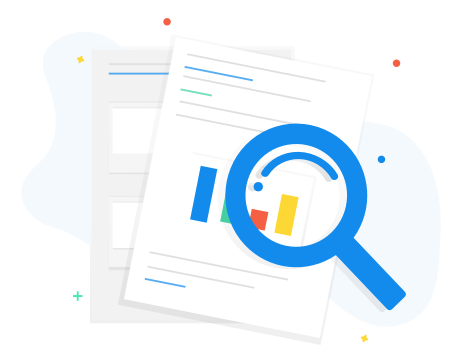
下载专利
同类推荐
-
魏家浩吕志伟吕志伟吕志伟
您可能感兴趣的专利
-
P·莫拉佐尼P·莫拉佐尼李会郎, 李承元芮秀明, 张秉文
专利相关信息
-
芮秀明K·罗杰斯, G·迪泽瑞嘉