专利名称::一种锦棉织物染色工艺的制作方法:近年来,锦棉织物系列产品在国际、国内市场越来越流行。锦纶纤维具有弹性好、强度高、耐磨、耐用、比重小、不易发霉或生蛀虫等特点;其耐穿、耐用及耐磨性约为羊毛的4-5倍,深受人们的喜爱;但锦纶纤维又是一种疏水性纤维,使用时会感到不透湿、不透气,而棉纤维是亲水性纤维,具有透气、透湿等优点,但是又不具备锦纶纤维弹性好等优点,易起皱、不挺括;将锦纶与棉纤维混纺成锦棉织物,使其优势互补,既具有优良的透湿性和透气性,又具有优良的耐磨性和挺括性,大大提升了其使用性能。然而,锦棉织物的染色是一个复杂的过程。目前,国内生产厂家多采用如图1所示的工艺方法对锦棉织物采用酸性染料、活性染料、分散染料和活性染料分浴法对锦棉织物进行染色,其工艺路线为未染色锦棉织物一酸性染料染锦纶纤维(高温高压溢流机染色)一活性染料染棉纤维一汽蒸(固色)一水洗一皂洗一水洗一烘干,完成锦棉染色布;或采用未染色锦棉织物一分散染料染锦一焙烘固色一活性染料染棉一汽蒸(固色)一水洗一皂洗一水洗一烘干,完成锦棉染色布。上述染色工艺对锦棉织物进行染色,发挥了一定的积极作用,但在上述染色工艺技术中存在以下问题1.工艺复杂。必须先染锦纶纤维,清洗后再染棉纤维,生产中不可控制的工艺波动因素多,色相难以把握,酸性染料染色采用的是高温高压溢流染色,生产是间歇式,产量低,缸差大;2.对染料的选择性范围小。有些活性染料,如二氯均三嗪类活性染料易造成锦沾色,染色牢度降低;3.酸性染料牢度差,活性染料的日晒牢度也不稳定。
本发明的目的是针对现有技术中工艺复杂、对染料的选择性范围小、酸性染料牢度差、活性染料的日晒牢度不稳定等问题,提供一种简单、高效、色牢度好,又便于操作和控制的锦棉织物染色新工艺方法。本发明的技术方案是一种锦棉织物染色工艺,主要包括对未染色锦棉织物进行同浴染色一还原汽蒸一氧化一水洗一皂洗一水洗一烘干锦棉染色布步骤,其特征在于将锦棉织物先浸入染料液中进行轧染,然后烘干;再第二次将织物浸入轧染还原料液中,再通过汽蒸还原、水洗、氧化、皂洗,使染料充分发色,然后烘干,完成所需染色全过程。采用还原染料进行染色,织物先浸轧还原染料液,染料液按不同的色相要求来配制。在汽蒸还原工艺中,采用Na0H(100%)、Na2S204(85%)作为还原剂,Na0H(100%)用量控制在20_25g/L,Na2S204(85%)用量控制在22-27g/L,织物在汽蒸箱内汽蒸,汽蒸箱内的蒸汽为饱和蒸汽,汽蒸箱温度为102-105t:,压力为0.15Mpa,时间为60-80秒,具体由车速来决定。在氧化工艺中,采用H202进行氧化,H202有效氧浓度控制在l-2g/L,用NaOH(100%)调节ffl值8_9;在水洗工艺中,织物经过50-6(TC水洗后,进入皂洗箱。在皂洗工艺中,温度为90-95t:,皂洗剂5g/L以上,肥皂液5g/L以上;在水洗工艺中,织物在3格平洗槽内、温度为75t:以上的热水中水洗,平洗槽内的水要倒流。所用还原染料(如还原绿B、还原橄榄T、还原黄G、还原蓝VB、还原棕BR、还原大红R等)、助剂GnH202、NaOH(100%)、Na2S204(85%)、皂洗齐U、液体肥皂等)等均为外购的通用产品。本发明与现有锦棉混纺织物的染色工艺相比,具有以下优点1、染色工艺从两浴两步法改为一浴两步法,工艺简捷,又方便操作,不需要考虑两种纤维染色时的两色效应,布面匀染性好;2、染色牢度高;以橄榄色为例见下表(一)<table>tableseeoriginaldocumentpage4</column></row><table>从表一可看出还原染料染色的各项色牢度指标均高于现有生产技术的染色牢度。3、采用还原染料染色工艺省略了酸性染料的高温高压溢流染色和分散染料的高温焙烘工艺,在水洗时,水的用量也比现有技术少,水洗采用逐格倒流,产生的污水也减少了,在降低环境污染的同时,也大幅度降低了能源消耗,节约了生产成本,提高了生产效率。具体实施例方式下面结合附图和实施例对本发明作进一步描述图1是现有锦棉织物的染色工艺流程示意图;图2是本发明锦棉织物的染色工艺流程示意图。实施例1:以20X12锦50棉50混纺橄榄绿直贡缎为例具体工艺步骤如下①.小样仿色通过实验室小样仿色,选取还原橄榄录B、还原咔叽2G、还原橄榄T三只染料拼色;②.按染料浓度确定还原剂用量如20X12锦50棉50混纺橄榄绿直贡缎染料浓度为8%时NaOH(100%)用量为:20-25g/L;Na2S204(85%)用量为:22-27g/L;③.同浴染色织物浸轧染料溶液(染料溶液按不同颜色的织物要求来配制)一烘干落布;④汽蒸还原织物浸轧以NaOH(100%):20-25g/L,Na2S204(85%):22-27g/L用量配制的还原液中,在还原汽蒸箱内以102-105t:的饱和蒸汽中汽蒸60-80秒,NaOH、化25204用量可根据染料用量的高低来配制;染料用量《4g/L时,NaOH(100X)用量一般控制在10-15g/L、Na2S204(85%)用量控制在12_17g/L;染料用量^4g/L时,NaOH浓度一般控制在20-25g/L、Na2S204(85%)用量控制在22_27g/L;⑤.氧化织物通过两格氧化槽,H202有效氧的浓度为1.5-1.6g/L,ffl值8_9(可用NaOH(100X)来调节);.水洗织物在平洗槽内用50-6(TC水洗一进入皂洗箱皂洗;⑦.皂洗织物在皂洗箱内皂洗,皂洗剂5g/L以上、肥皂液5g/L以上,温度为90-95°C;⑧.水洗织物在3格平洗槽内、温度为75t:以上的热水中水洗,平洗槽内的水要倒流;⑨.烘干将织物烘干为止。实施例2以20X16锦50棉50混纺米色格子布为例具体工艺步骤如下(1).小样仿色通过实验室小样仿色,选取还原灰M、还原咔叽2G、还原棕服三只染料拼色;(2).按染料浓度确定还原剂浓度经复样后,该产品染料液浓度为2.1%,故NaOH(100%)用量为10-12g/L;Na2S204(85%)用量为ll-13g/L;(3).同浴染色织物浸轧以还原灰M、还原咔叽2G、还原棕BR三只染料按不同比例混合而成的染料溶液一烘干落布;(4).汽蒸还原织物浸轧以NaOH(100X):10-12g/L、Na2S204(85%):ll-13g/L用量配制的还原液中,在还原汽蒸箱内以102-105t:的饱和蒸汽中汽蒸60-80秒;(5).氧化织物通过两格氧化槽,H202有效氧的浓度为1.5-1.6g/L,ffl值8_9(可用NaOH(100X)来调节);(6).水洗织物在平洗槽内用50-6(TC水洗一进入皂洗箱皂洗;(7).皂洗织物在皂洗箱内皂洗,皂洗剂5g/L以上、肥皂液5g/L以上,温度为90-95°C;(8).水洗织物在3格平洗槽内、温度为75t:以上的热水中水洗,平洗槽内的水要倒流;(9).烘干将织物烘干为止。本发明所述工艺中用的还原染料及助剂均为外购的通用产品。权利要求一种锦棉织物染色工艺,主要包括对未染色锦棉织物进行同浴染色、汽蒸还原、氧化、水洗、皂洗、水洗、烘干锦棉染色布步骤,其特征在于将锦棉织物先浸入染料液中进行轧染,然后烘干;再第二次将织物浸入轧染还原料液中,再通过汽蒸还原、水洗、氧化、皂洗,使染料充分发色,然后烘干;完成所需染色全过程。2.根据权利要求书1所述的一种锦棉织物染色工艺,其特征在于对锦棉织物采用还原染料进行染色,织物先浸轧还原染料料液,染料料液按不同的色相要求来配制。3.根据权利要求书l所述的一种锦棉织物染色工艺,其特征在于采用化011、化25204作为还原剂,NaOH浓度控制在20-25g/L,Na2S204浓度控制在22_27g/L,锦棉织物在还原汽蒸箱内汽蒸还原,汽蒸箱内的蒸汽为饱和蒸汽,时间为60-80秒,具体由车速来决定。4.根据权利要求书l所述的一种锦棉织物染色工艺,其特征在于采用!1202进行氧化,H202有效氧浓度控制在l-2g/L,用NaOH调节ffl值8-9对锦棉织物进行氧化。5.根据权利要求书l所述的一种锦棉织物染色工艺,其特征在于锦棉织物经过50-60°C水洗后,进入皂洗箱。6.根据权利要求书l所述的一种锦棉织物染色工艺,其特征在于在皂洗工艺中,温度为90-95。C,皂洗剂5g/L以上,肥皂液5g/L以上对锦棉织物进行皂洗。7.根据权利要求书1所述的一种锦棉织物染色工艺,其特征在于在3格平洗槽内,温度在75°C以上的倒流水中,对锦棉织物进行水洗。全文摘要本发明公开了一种锦棉织物染色工艺,其特征在于将锦棉织物先浸入染料液中进行轧染,然后烘干;再第二次将织物浸入轧染还原料液中,再通过汽蒸还原、水洗、氧化、皂洗,使染料充分发色,然后烘干,完成所需染色全过程。染色工艺从两浴两步法改为一浴两步法、染色牢度高、不需要考虑两种纤维染色时的两色效应,布面匀染性好;省略了酸性染料的高温高压溢流染色和分散染料的高温焙烘,用水量少,降低环境污染,大幅度降低了能源消耗,节约了生产成本,提高了生产效率。文档编号D06P3/82GK101768882SQ20081024634公开日2010年7月7日申请日期2008年12月27日优先权日2008年12月27日发明者刘勇,刘显红,张彬,石建峰,邱双林申请人:襄樊新四五印染有限责任公司
一种锦棉织物染色工艺制作方法
- 专利详情
- 全文pdf
- 权力要求
- 说明书
- 法律状态
查看更多专利详情
下载专利文献
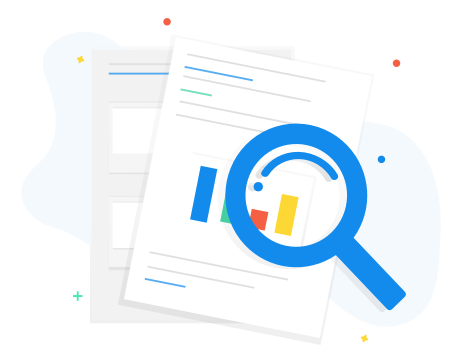
下载专利
同类推荐
-
吴大发吴大发吴大发吴大发
您可能感兴趣的专利
-
吴大发佘志清佘志清付正苟颜钢锋
专利相关信息
-
颜钢锋O·阿克塞尔松O·阿克塞尔松O·阿克塞尔松O·阿克塞尔松