利用发泡水泥废料制备的免烧砖及其制备方法[0002]现有技术中常见有利用粉煤灰、建筑垃圾生产建筑用免烧砖的报道,公知的制砖技术中,免烧砖是指利用粉煤灰、煤渣、煤矸石、尾矿渣、化工渣或者天然砂、海涂泥等(以上原料的一种或数种)作为主要原料,按一定比例添加外加剂,不经高温煅烧而制造的一种新型墙体砖。如中国专利CN100488911C公开了一种“采用建筑垃圾制备的免烧砖”他的原料按重量份取建筑垃圾65-70份,混合料30-35份,其余为外加剂。尽管它利用工业废渣,实现了废物再利用,但仍然属于添加外加剂制砖的范围,生产成本高还存有污染环境的隐患。[0003]发泡水泥废料是在发泡水泥板的生产过程中原材料的波动及生产环境温度的变化,难免有塌模及发气高度不够的现象,导致产品废弃;在脱模前切割模具上多余的部分;在施工时切割产生的边角料;由于保存及施工方式不当造成发泡水泥板的损毁,成为废料。目前这些废料没有很好的处理方法,只能大量堆积,不仅造成材料的浪费,还占用大量的土地资源,因此对这些废料的再利用不仅可以解决以上问题,还具有重大的经济价值。
[0004]本发明 的发明目的在于针对现有技术的诸多不足,为了最大限度利用发泡水泥废料,一是提供一种利用发泡水泥废料制备的免烧砖,二是提供一种利用发泡水泥废料制备免烧砖的方法。[0005]实现上述目的采用以下技术方案: 一种利用发泡水泥废料制备的免烧砖,所述免烧砖由下述重量配比的原料制成:发泡水泥废料40~90份,粉煤灰O~50份,铁尾矿砂8~12份,水10~20份。[0006]进一步,粉煤灰的粒径< 0.075mm。
[0007]进一步,铁尾矿砂的粒径< 1.5mm。
[0008]进一步,所述的粉煤灰用矿渣或钢渣与石粉和(或)脱硫石膏或铁尾矿粉渣、水泥的混合物替代。
[0009]进一步,所述的替代粉煤灰的混合物按照重量份数计,包含粒径< 0.075mm的矿洛或钢洛10~20份,粒径≤0.15mm的石粉和(或)脱硫石膏或铁尾矿粉洛5~10份,粒径≤0.075mm的水泥2~4份。
[0010]一种利用发泡水泥废料制备免烧砖的方法,其特征在于,包括下述步骤:
a.制备坯料:按照重量份数取发泡水泥废料40~90份,粉煤灰O~50份,铁尾矿砂8~12份,将物料混合加水10~20份搅拌均匀,经4小时困料后获得可供压力成型的坯料;
b.坯体成型:将上述混合均匀并经困料的坯料用液压机成型为坯体,坯体的成型压强为20MPa~30MPa,加压速率为O~5KN/s ;
c.养护:将成型后坯体在温度20±1°C,湿度90±1%的养护室中养护28天取出,再在常温下自然干燥得到成品砖。
[0011]进一步,所述的粉煤灰用混合物替代,所述的混合物按照重量份数计,包含粒径≤0.075mm的矿渣或钢渣10~20份,粒径≤0.15mm的石粉和(或)脱硫石膏或铁尾矿粉渣5~10份,粒径≤0.075mm的水泥2~4份。
[0012]进一步,当粉煤灰用混合物替代时,制备免烧砖的方法是:
a.制备坯料:按照重量份数取发泡水泥废料40~90份,粒径≤0.075mm的粉煤灰O~50份,混合物15~35份,铁尾矿砂8~12份,将物料混合加水10~20份搅拌均匀,经4小时困料后获得可供压力成型的坯料;
b.坯体成型:将上述混合均匀并经困料的坯料用液压机成型为坯体,坯体的成型压强为20~30MPa,加压速率为O~5KN/s ;
c.养护:将成型后坯体在温度20±1°C,湿度90±1%的养护室中养护28天取出,再在常温下自然干燥得到抗压强度为7.5~29.6MPa成品免烧砖;
采用上述技术方案,与现有技术相比,本发明利用发泡水泥废料加压制备免烧砖,将发泡水泥废料变废为宝,减少了对土地的占用及对环境的污染,其显著的效果在于,用发泡水泥废料加压制备免烧砖不用添加任何外加剂,利用发泡水泥废料体系中水化产物为结晶中心促进未水化水泥颗粒继续发生水化反应以及物料水化反应之间的协同作用就可以满足生产要求,降低了生产成本,提高了经济效益。本发明的生产方法操作方便,所生产的免烧砖抗压强度高达30MPa,实现了最大程度利用废料,生产出符合国家标准的建筑砖的目的。
具体实施例
[0013]下面结合具体实施例对本发明做进一步的描述。
[0014]本发明公开的是一种利用发泡水泥废料制备的免烧砖及其制备方法,其发明思想是:以在发泡水泥板的生产过程中由于原材料的波动及生产环境温度的变化,产生的废弃的发泡水泥废料为主要原料,配以粉煤灰及铁尾矿砂利用专门的工艺来生产免烧砖。具体实施例如下:
实施例1
按照重量份数:取发泡水泥板废料40份,粒径≤ 0.075mm粉煤灰50份,粒径≤ 1.5mm铁尾矿砂10份,加水15份,按配比计量后搅拌均匀,经4小时困料后获得可供压力成型的坯料。将上述混合均匀并经困料的坯料采用液压机成型为坯体,坯体的成型压强为20MPa,加压速率为O~5KN/s。将成型后坯体在温度20± 1°C,湿度90 ± 1%的养护室中养护28天,再在常温下自然干燥得到成品免烧砖。
[0015]经检测,按照重量份数取发泡水泥废料为40份、粉煤灰50份、铁尾矿砂10份、加水15份,免烧砖的抗压强度为12.7MPa。
[0016]实施例2
按重量份取发泡水泥废料重量40份,粒径≤ 0.075mm的粉煤灰50份,粒径≤ 1.5mm的铁尾矿砂12份,加水10份,按配比计量后搅拌均匀,经4小时困料后获得可供压力成型的坯料。将上述混合均匀并经困料的坯料采用液压机成型为坯体,坯体的成型压强为20MPa,加压速率为O~5KN/S。将成型后坯体在温度20± 1°C,湿度90 ± 1%的养护室中养护28天,再在常温下自然干燥得到成品免烧砖。
[0017]经检测,按重量份取水泥废料40份、粉煤灰50份、铁尾矿砂12份、水10份时,免烧砖的抗压强度为7.5MPa。
[0018]实施例3
按重量份取发泡水泥废料重量70份,粒径< 0.075mm的粉煤灰20份,粒径< 1.5mm的铁尾矿砂10份,加水20份,按配比计量后搅拌均匀,经4小时困料后获得可供压力成型的坯料。将上述混合均匀并经困料的坯料采用液压机成型为坯体,坯体的成型压强为20MPa,加压速率为O~5KN/s。将成型后坯体在温度20± 1°C,湿度90 ± 1%的养护室中养护28天,再在常温下自然干燥得到成品免烧砖。
[0019]经检测,按重量份取水泥废料70份、粉煤灰20份、铁尾矿砂10份、加水20份,免烧砖的抗压强度为22.4MPa。
[0020]实施例4
按重量份取发泡水泥废料90份,粒径< 0.075mm的粉煤灰10份,粒径< 1.5mm的铁尾矿砂10份,加水15份,按配比计量后搅拌均匀,经4小时困料后获得可供压力成型的坯料。将上述混合均匀并经困料的坯料采用液压机成型为坯体,坯体的成型压强为30MPa,加压速率为O~5KN/s。将成型后坯体在温度20±1°C,湿度90±1%的养护室中养护28天,再在常温下自然干燥得到成品免烧砖。
[0021]经检测,按重量份数取水泥废料90份、粉煤灰10份、铁尾矿砂10份、加水15份,免烧砖抗压强度高达29.6MPa。
[0022]实施例5
按重量份数取发泡水泥废料52份,粒径≤0.075mm的粉煤灰20份,粒径≤1.5mm的铁尾矿砂10份,部分替代粉煤灰混合物中按重量份数取粒径< 0.075mm的钢渣10份、粒径(0.15mm的石粉5份、粒径≤0.075mm的水泥3份,加水15份,按配比计量后搅拌均匀,经4小时困料后获得可供压力成型的坯料;将上述混合均匀并经困料的坯料采用液压机成型为坯体,坯体的成型压强为20MPa,加压速率为O~5KN/s。将成型后坯体在温度20±1°C,湿度90±1%的养护室中养护28天,再在常温下自然干燥得到成品免烧砖。
[0023]经检测,按重量份数取,发泡水泥废料52份、粉煤灰20份、钢渣10份、石粉5份、水泥3份、铁尾矿砂10份、加水15份,免烧砖的抗压强度为16.6MPa。
[0024]实施例6
按重量份数取发泡水泥废料52份,粒径≤0.075mm的粉煤灰20份,粒径≤1.5mm的铁尾矿砂10份、部分替代粉煤灰混合物中按重量份数取粒径< 0.075mm的矿渣10份、粒径≤0.15mm的脱硫石膏5份、粒径≤0.075mm的水泥3份、加水15份,按配比计量后搅拌均匀,经4小时困料后获得可供压力成型的坯料;将上述混合均匀并经困料的坯料采用液压机成型为坯体,坯体的成型压强为20MPa,加压速率为O~5KN/s。将成型后坯体在温度20±1°C,湿度90±1%的养护室中养护28天,再在常温下自然干燥得到成品免烧砖。
[0025]经检测,按重量份数取,发泡水泥废料52份、粉煤灰20份、矿渣10份、脱硫石膏5份、水泥3份、加水15份,免烧砖的抗压强度为18.3MPa。
[0026]上述实施例仅表达了本发明的一种实施方式,但并不能因此而理解为对本发明范围的限制。应当指出,对于本领域的普通技术人员来说,在不脱离本发明构思的前提下,还可以做出若干变形和改进,这些都属于本发明的`保护范围。
利用发泡水泥废料制备的免烧砖及其制备方法
- 专利详情
- 全文pdf
- 权力要求
- 说明书
- 法律状态
查看更多专利详情
下载专利文献
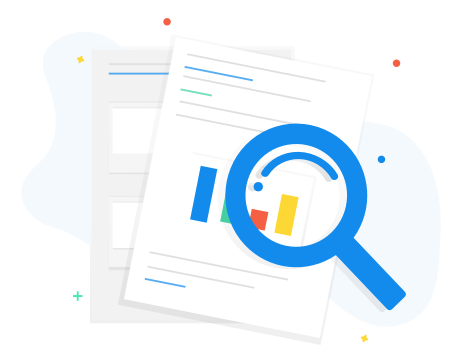
下载专利
同类推荐
-
张声军李鹏程
您可能感兴趣的专利
-
王善祝, 王明
专利相关信息
-
刘杰, 吕春叶强田福祯田福祯陈凯, 陈树德