专利名称:碳纤维束及其制造方法作为碳纤维束的制造方法,已知有使用聚丙烯腈(PAN)等原料纤维(前驱体纤 维),对其进行氧化处理及碳化处理而得到碳纤维的方法。如此得到的碳纤维具有高强度、 高弹性率等良好的特性。近年来,利用碳纤维制造的复合材料(例如,碳纤维强化塑料(CFRP)等)的用途 不断发展。例如,在运动休闲领域、航空宇宙领域、机动车领域中,不断要求复合材料的(1) 更高性能化(高强度化、高弹性化)、(2)更轻量化(纤维的轻量化及纤维含有量的减少 化)。为了满足所述要求,在对碳纤维与树脂(基质材料)进行复合化时,要求获得的复合 材料能够呈现更高物性的碳纤维。为了得到高性能的复合材料,基质材料具有的物性很重要。而且,碳纤维的表面特 性的改良、及碳纤维的强度和弹性率的提高也很重要。通常来说,对具有相对于基质材料的 粘结性高的碳纤维表面的碳纤维和基质材料进行复合化、及使碳纤维充分均勻地分散在基 质材料中很重要。其结果,能得到更高性能的复合材料。关于碳纤维的表面褶皱、表面特性、强度及弹性率,一直以来都在进行研究(例 如,参照专利文献1 4)。在碳纤维的结构中,一个喷丝头所具有的纺纱孔越多越适合于大量生产。然而,从 具有20000以上的纺纱孔的喷丝头纺纱而制造的前驱体纤维束原本的开纤性高,因此,在 以该前驱体纤维束为原料制造碳纤维束时,在下述的氧化工序或碳化工序中会被过开纤而 制造出物性不均勻的碳纤维束。在为了控制开纤的程度而大量地添加浆液时,尤其是在碳化工序中,会大量产生 由浆液产生的不纯物,其结果,得到的碳纤维束的不均勻变大,难以得到高强度、高弹性率 的碳纤维束。为了避免上述问题,有使用具有较少的纺纱孔的喷丝头进行纺纱制成前驱体纤维 束,将多根前驱体纤维束进行集束而制造由20000根以上的单纤维构成的前驱体纤维束的方法。例如,考虑制造集束24000根单纤维而成的碳纤维束的情况。通常,使用一个喷丝 头,得到由3000 12000根单纤维构成的前驱体纤维束。具有如下的得到碳纤维束的方 法,即,捆扎2 8根该前驱体纤维束而集束成由24000根单纤维构成的前驱体纤维束,然 后,进行氧化处理、碳化处理,得到由24000根单纤维构成的碳纤维束。或者,具有如下的 得到碳纤维束的方法,即,原封不动地对所述各前驱体纤维束进行氧化处理,之后在碳化处 理中,对各纤维束进行集束,得到由24000根单纤维构成的碳纤维束。再者,具有如下的得 到碳纤维束的方法,即,原封不动地对所述各前驱体纤维束进行氧化处理,之后在碳化处理后,对各纤维束进行集束,得到由24000根单纤维构成的碳纤维束。然而,在使用由所述方法制造的碳纤维束而制造复合材料的情况下,在为了浸渍树脂而对所述集束的碳纤维束进行开纤时,容易产生与原来的各纤维束分离的所谓断束。另外,由于构成集束的纤维束的各碳纤维不是使用单一喷丝头制造的纤维束,因 此强度等的偏差容易变大。如此,集束多根纤维束而制造的由20000根以上的单纤维构成的碳纤维束在开纤 时容易产生断束,而且构成纤维束的各碳纤维的物性不均。再有,由于构成纤维束的各碳纤 维的物性不均,因此碳纤维的束拉伸强度、束拉伸弹性率通常也低。通常,在制造复合材料时,使碳纤维束充分开纤,使基质树脂均勻地浸渍在其中。 在碳纤维束的开纤时,若产生断束,则树脂的浸渍变得不均,得到的复合材料的物性变差。 因此,作为适用于复合材料的制造的碳纤维束所要求的特性,列举有不产生断束而能够充 分地开纤的特性。专利文献1 日本特开平10-25627号公报(权利要求书)专利文献2 日本特开2006-183173号公报(权利要求书)专利文献3 日本特开2005-133274号公报(权利要求书)专利文献4 日本特开2002-327339号公报(权利要求书)
本发明的发明者为了解决上述问题而进行了反复研究。其结果,发现了 将使用一 个喷丝头具有20000以上的纺纱孔的喷丝头而制造的前驱体纤维束在规定条件下进行交 织处理,然后,通过进行规定的氧化处理、碳化处理、表面氧化处理,能够制造容易开纤且难 以引起断束的碳纤维束。基于上述研究的结果,完成了本发明。本发明的目的在于,提供一种解决了上述问题的碳纤维束及其制造方法。实现上述目的的本发明如下所述。(1) 一种碳纤维束,集束20000 30000根碳纤维而形成,所述碳纤维使用扫描型 探测显微镜测定的碳纤维的表面的褶皱的间隔为100 119nm、表面的褶皱的深度为23 30nm,且平均纤维直径为4. 5 6. 5 μ m、比表面积为0. 6 0. 8m2/g、密度为1. 76g/cm3以 上,其中,束拉伸强度为5650MPa以上,束拉伸弹性率为300GPa以上,以规定张力卷绕的束 的束宽度为5. 5mm以上,在对移动中的碳纤维束施加规定张力的断束评价方法中未观察到 断束。(2) (1)所述的碳纤维束的制造方法,使使用具有20000 30000的纺纱孔的喷丝 头对纺纱原液进行纺纱而得到的凝固纱束,通过加压空气的吹出压为表压20 60kPa的交 织喷嘴中,得到前驱体纤维束,接下来,在加热空气中以200 280°C对所述前驱体纤维束 进行氧化处理,得到氧化纤维束,对该氧化纤维束进行第一碳化处理,然后,在惰性气体环 境中,以温度1360 2100°C进行第二碳化处理,之后,将通过所述碳化处理而得到的碳纤 维束在无机酸盐水溶液中以每Ig碳纤维的电量为20 100库仑的方式通过电解氧化法进 行表面氧化处理,该第一碳化处理是在惰性气体环境中,以温度300 900°C、1. 03 1. 06 的延伸倍率对所述氧化纤维束进行一次延伸处理,之后以0. 9 1. 01的延伸倍率进行二次 延伸处理。(3)根据(2)所述的碳纤维束的制造方法,纺纱原液是将丙烯酸系聚合体溶解在氯化锌水溶液或有机溶剂中的溶液。发明效果本发明的碳纤维束使用由单一的喷丝头形成的前驱体纤维束进行制造,因此并不 局限于由20000根以上的单纤维构成,在开纤时难以产生断束。因此,在制造复合材料时, 能够使束较大地开纤而均勻地浸渍树脂。其结果,能够制造物性优良的复合材料。进而,碳 纤维束中的各单纤维能够使用单一的喷丝头进行制造,因此各单纤维间的物性的偏差小。 其结果,与以往的集合多个束而制造的由20000根以上的单纤维构成的碳纤维束相比,本 碳纤维束的束拉伸强度、束拉伸弹性率高。构成碳纤维束的碳纤维由于具有规定的表面褶皱的间隔、深度及比表面积,因此 与基质树脂的粘结性良好。根据本发明的碳纤维束的制造方法,由于能够使用具有20000以上的纺纱孔的喷 丝头来制造前驱体纤维,因此适合于大量生产。图1是示出构成本发明的碳纤维束的碳纤维的一例的简要局部剖面图。图2是示出在本发明的碳纤维束的制造方法中使用的交织喷嘴的一例的概念图。图3是示出相对于第一碳化工序中的一次延伸时的温度上升的PAN系氧化纤维的 弹性率的推移的图表。图4是示出相对于第一碳化工序中的一次延伸时的温度上升的PAN系氧化纤维的 微晶尺寸的推移的图表。图5是示出相对于第一碳化工序中的二次延伸时的温度上升的一次延伸处理纤 维的密度的推移的图表。图6是示出相对于第二碳化工序中的一次处理时的温度上升的第一碳化处理纤 维的密度的推移的图表。图7是示出相对于第二碳化工序中的一次处理时的温度上升的第一碳化处理纤 维的微晶尺寸的推移的图表。图8是示出相对于第二碳化工序中的二次处理时的温度上升的一次处理纤维的 密度的推移的图表。符号说明2 碳纤维4 波状形状的峰状部分6 波状形状的谷状部分a 峰状部分的间隔(褶皱的间隔)b 峰状部分与谷状部分的高低差(褶皱的深度)12 交织喷嘴14 前驱体纤维16 加压空气供给口18 加压空气20 空气流
纤维)而成的。该碳纤维的束拉伸强度为5650MPa以上,优选为5680MPa以上。没有优选的上限,但是通常为5700MPa左右。该碳纤维的束拉伸弹性率为300GPa以上,优选为308 370GPa。 此外,在本说明书中,有时将碳纤维的束拉伸强度简称为强度,将碳纤维的束拉伸弹性率简 称为弹性率。该碳纤维束在下述的束宽度测定法中测定的束宽度为5. 5mm以上,优选为6 10mm,更优选为6 8mm。再有,该碳纤维束在下述的断束评价方法中未观察到断束。在构成本发明的碳纤维束的碳纤维(单纤维)的表面上,具有形成在与纤维轴的 方向同方向上的多个褶皱。通过下述的测定方法求出的碳纤维的比表面积为0. 6 0. 8m2/g。碳纤维的密度为1. 76g/cm3以上,优选为1. 76 1. 80g/cm3。碳纤维的平均直径为4. 5 6. 5 μ m,优选为5. 0 6. 0 μ m。图1是示出构成本发明的碳纤维束的碳纤维的一例的简要局部剖面图。图1是通 过与碳纤维轴正交的面剖开的碳纤维的剖面图。本例的碳纤维2在表面上具有碳纤维的直 径沿纤维的周向增减而形成的褶皱。在图1中,4表示直径大的峰状部分。6表示直径小的 谷状部分。a表示峰状部分的间隔(褶皱的间隔)。b表示峰状部分与谷状部分的高低差(褶 皱的深度)。褶皱的间隔a及褶皱的深度b使用扫描型探测显微镜来测定。在使用扫描型 探测显微镜观察碳纤维的表面时,褶皱的间隔a = 100 119nm,表面褶皱的深度b = 23 30nmo本发明的碳纤维束例如能够通过以下的方法制造。(纺纱原液)制造本发明的碳纤维束时的初始原料是前驱体纤维制造用的纺纱原液。作为纺纱 原液,只要是碳纤维制造用的纺纱原液,就可以不受限制地使用现有公知的纺纱原液。其 中,优选丙烯酸系碳纤维制造用的纺纱原液。具体来说,优选对含有90质量%以上、优选95 质量%以上的丙烯腈的单体进行单独聚合或与其它的单体共聚合而形成的纺纱原液。作为 与丙烯腈共聚合的其它的单体,例示有丙烯酸、丙烯酸甲酯、衣康酸、甲基丙烯酸甲酯、丙烯 酰胺等。作为纺纱原液,优选在氯化锌水溶液或二甲基甲酰胺(DMF)、N, N- 二甲基乙酰胺 (DMAc)等有机溶剂中溶解5 20质量%的上述丙烯腈系聚合体而形成的物质。(纺纱)使用一个喷丝头具有20000 30000、优选20000 26000个纺纱孔的喷丝头,从
该喷丝头喷出纺纱原液。作为使从纺纱孔喷出的纺纱原液凝固的方法,有湿式纺纱法、干湿 式纺纱法、干式纺纱法。湿式纺纱法是向充满冷却到低温的凝固液(在纺纱原液制造中使用的溶剂-水的混合液)的凝固浴中直接供给从喷丝头喷出的纺纱原液的方法。干湿式纺 纱方法首先从喷丝头向空气中喷出纺纱原液,然后,在通过3 5mm左右的空间后,向凝固 浴供给的方法。根据湿式纺纱方法,在最终得到的碳纤维的表面自然形成微细的褶皱。对于该褶皱的大小,所述褶皱的间隔a = 100 119nm,表面褶皱的深度b = 23 30nm左右。在制 造复合材料时,该褶皱的存在能够期待碳纤维与树脂的粘结性的提高。因此,作为纺纱方 法,优选湿式纺纱法。此外,纺纱孔的形状通常为正圆。在干式纺纱法等中,褶皱的形成能 够通过对纺纱孔的形状下工夫和调节纺纱条件等来实现。凝固的丙烯酸系纤维等接下来适当地被实施水洗、干燥、延伸等的通常进行的处理。在上述纺纱工序中,以耐热性的提高或纺纱作业的稳定性为目的,优选将油剂附 加给丙烯酸系纤维等。作为油剂,优选组合具有亲水基的浸透性油剂和硅系油剂而形成的 公知的油剂。(交织处理)在纺纱工序中,在构成前驱体纤维束的多个前驱体纤维之间产生缠绕(交络)或 由油形成的伪粘结。再者,具有过度开纤的情况。它们成为产生细毛、前驱体断裂的原因。 为了避免所述问题,进行交织处理。通过交织处理,解除纤维束内的局部的交络而施加适当 的交络,并进行适度的开纤处理。交织处理例如在图2所示的交织喷嘴中通过使前驱体纤维束通过而进行。在图2中,12是交织喷嘴。前驱体纤维束14通过构成该交织喷嘴12的圆筒状主 体12a的内部。在交织喷嘴12上贯通圆筒状主体12a设有多个(在本图中为三个)加压 空气供给口 16。加压空气18通过加压空气供给口 16供给到圆筒状主体12a内。在供给 的加压空气的作用下,在圆筒状主体12a内产生空气流20。加压空气的吹出压保持为表压 20 60kPa。当加压空气的吹出压小于20kPa时,解除纺纱工序中发生的前驱体纤维束内的前 驱体纤维相互的缠绕,进行前驱体纤维束的开纤。在内部压力为20 60kPa时,开纤和交络适度地发生,提高前驱体纤维束的收束性。当加压空气的吹出压超过60kPa时,前驱体纤维束内的交络过度进行,从而前驱 体纤维损伤,最终纤维束强度下降。在该交织处理工序中,通过形成为上述适当的加压空气 的吹出压(表压20 60kPa),使纤维不损伤地对纤维束施加适当的开纤和交络。(氧化处理)进行了交织处理的前驱体纤维接下来在200 280°C的加热空气中进行氧化处 理。在前驱体纤维为丙烯酸系纤维时,通过进行氧化处理,在丙烯酸系纤维中在分子内发生 环化反应,使氧结合量增加。其结果,前驱体纤维被形成为不熔化、难燃化,添加丙烯酸系氧 化纤维(OPF)。氧化处理通常在延伸倍率0. 85 1. 30的范围内延伸。为了得到高强度、高弹性 率的碳纤维,延伸倍率优选为0. 95以上。通过上述氧化处理,得到密度为1. 3 1. 5g/cm3 的氧化纤维。
(第一碳化处理)在本碳纤维的制造方法中,在第一碳化处理工序中,在非活性环境中,在300 900°C的温度范围内,以1. 03 1. 06的延伸倍率对上述氧化纤维进行一次延伸处理。接下 来,在非活性环境中,在300 900°C的温度范围内,以0. 9 1. 01的延伸倍率对上述进行 了一次延伸处理的氧化纤维进行二次延伸处理,得到纤维密度为1. 50 1. 70g/cm3的第一 碳化处理纤维。(第一碳化处理·一次延伸处理)在第一碳化处理工序中,氧化纤维在上述温度范围内从低温的300°C慢慢地向高温(900°C )升温。在该工序中,下述(1) (3)所记载的弹性率、密度、微晶尺寸等发生变 化。在上述第一碳化处理工序的一次延伸处理中,在氧化纤维升温、处于下述范围中 的情况下,以总计1. 03 1. 06的延伸倍率进行延伸处理。(1)从氧化纤维的弹性率下降到极小值的时刻开始到增加到9. SGPa为止的范围;(2)该纤维的密度到达1. 5g/cm3为止的范围;(3)该纤维的广角X射线测定(衍射角26° )的微晶尺寸到达1. 45nm为止的范 围,从上述的氧化纤维的弹性率下降到极小值的时刻开始到增加到9. SGPa为止的范 围为图3所示的β的范围。通过在从氧化纤维的弹性率下降到极小值的时刻开始到增加到9. SGPa为止的范 围内进行延伸(1. 03 1. 06倍),抑制断纱,使氧化纤维的低弹性率部高效延伸而进行高配 向化,从而得到致密的一次延伸处理纤维。另一方面,在氧化纤维的弹性率下降到极小值之前(α的范围)延伸1.03倍以上 时,断纱增加,导致得到的一次延伸处理纤维的显著的强度降低,因此不优选。另外,在弹性率下降到极小值且接下来增加到9. SGPa后的范围(Y的范围)内延 伸1.03倍以上时,纤维的弹性率变高,因此强制进行不合理的延伸。其结果,纤维缺陷或空 隙增加,延伸的效果受损。由此,在上述弹性率的范围内进行一次延伸处理。通过在氧化纤维的密度到达1. 5g/cm3为止的范围内进行延伸(1. 03 1. 06倍), 能够抑制空隙的生成,并提高配向度,从而得到高品质的一次延伸处理纤维。与此相对,在密度高于1. 5g/cm3的范围内进行1. 03倍以上的一次延伸时,不合理 的延伸引起的空隙的生成增加,导致最终的碳纤维的结构缺陷、密度下降,因此不优选。由 此,在上述密度范围内进行一次延伸处理。此外,在一次延伸的延伸倍率小于1.03倍时,延伸的效果小,无法得到高强度的 碳纤维。在延伸倍率高于1. 06倍时,导致断纱,无法得到高品质及高强度的碳纤维。(第一碳化处理·二次延伸处理)在第一碳化处理工序的二次延伸处理中,在升温中,在(1) 一次延伸处理后的纤 维的密度在二次延伸处理中持续上升的范围,以及(2)如图4所示在一次延伸处理后的纤 维的广角X射线测定(衍射角26° )中观测的微晶尺寸不大于1.45nm的范围内,以0.9 1.01倍的延伸倍率进行延伸处理。在第一碳化处理工序的二次延伸处理中,如图5所示,随着碳化温度的上升,纤维的密度具有不增加的条件、继续增加的条件、增加后减少的条件。在所述条件中,进行了一次延伸处理的纤维的密度在二次延伸处理中在持续上升的条件下以0. 9 1. 01倍的延伸倍率进行延伸处理,由此,抑制空隙生成,最终能够得到致 密的碳纤维。连续上升的条件能够通过控制碳化处理温度条件来实现。与此相对,在纤维密度下降期间进行二次延伸处理时,碳纤维中的空隙的生成增 力口,无法得到致密的碳纤维。而且,在二次延伸处理中包含纤维密度不变化的期间时,无法 期待二次延伸处理产生的致密性的提高,最终无法得到高强度的碳纤维。由此,二次延伸处 理在纤维密度持续增加的范围内进行。再有,在通过一次延伸处理后的纤维的广角X射线测定(衍射角26° )测定的微 晶尺寸为1. 45nm以下的范围内以0. 9 1. 01倍的延伸倍率进行延伸处理。通过该延伸处 理,不使结晶生长而形成致密化,抑制空隙的生成,最终可得到具有高致密性的碳纤维。在微晶尺寸大于1. 45nm的范围内进行二次延伸处理时,得到的碳纤维的空隙增 力口。再有,由于断纱而导致品质下降,无法得到高强度的碳纤维。由此,二次延伸处理在上 述微晶尺寸的范围内实施。此外,在二次延伸处理中,在延伸倍率小于0. 9倍时,由广角X射线测定(衍射角 26° )所测定的第一碳化处理纤维的配向度显著下降,无法得到高强度的碳纤维。在延伸 倍率高于1. 01倍时,导致断纱,无法得到高品质及高强度的碳纤维。由此,二次延伸处理中 的延伸倍率优选为0. 9 1. 01倍的范围内。为了得到高强度的碳纤维,由广角X射线测定(衍射角26° )所测定的第一碳化 处理纤维的配向度优选为76.0%以上。在配向度小于76. 0%时,无法得到高强度的碳纤维。作为将配向度形成为76. 0% 以上的方法,必须将耐燃化处理中的延伸倍率形成为0. 95以上,进而如上所述,必须将第 一碳化工序形成为上述规定的条件。在第一碳化处理工序中,在上述的条件下进行氧化纤维的一次延伸处理、二次延 伸处理,得到第一碳化处理纤维。上述第一碳化处理工序使用一个炉或两个以上的炉,连续 或分别处理都可以。(第二碳化处理)在第二碳化工序中,在非活性环境中、在超过900°C的温度 2100°C、优选在 1360 2100°C的温度范围内对上述第一碳化处理纤维进行延伸处理而得到第二碳化处理 纤维。根据需要,该工序也可以分为一次延伸处理和二次延伸处理。此外,为了使制造的碳纤维具有必要的弹性率,作为第二碳化处理·二次延伸处理 的后工序,根据需要,也可以设置第三碳化工序而进行碳纤维的热处理。再有,第二碳化处 理及后工序的热处理也可以使用一个炉连续进行。或者也可以使用两个或三个炉分别进行 各处理。(第二碳化处理·一次处理)在第二碳化处理的一次处理中,使如上所述得到的第一碳化处理纤维从炉的入口 侧的1360°C慢慢地向出口侧的2100°C升温。在该工序中,在上述升温中,在满足下述条件的范围内,使该纤维延伸。延伸倍率 在满足下述条件的范围内适当决定。通常,延伸倍率为0. 95 1. 05倍的范围内。
(1)该纤维的密度持续上升的范围;(2)该纤维的含氮率维持在10质量%以上的范围;(3)广角X射线测定(衍射角26°)的微晶尺寸不大于1·47ηπι的范围,在第二碳化工序一次处理中,处理的第一碳化处理纤维的密度、微晶尺寸的变化 的一例,如图6及图7所示。也一起示出处理条件范围。此外,在第二碳化工序一次处理中,纤维张力(F MPa)依赖于通过第一碳化工序后 的碳纤维截面积(S mm2),因此在本发明中,使用纤维应力(B mN)作为张力因数。在本发明中,纤维应力的范围为满足下式的范围。1. 24 > B > 0. 46(其中,B = FXSS = 3iD2/4D为第一碳化处理纤维的直径(mm))在此,纤维截面积通过以下的方法算出。首先,如JIS-R-7601规定那样,使用测微 显微镜,反复η = 20次测定纤维直径。接下来,求出测定的纤维直径的平均值。使用该纤 维直径的平均值,算出正圆的面积。将算出的正圆的面积值作为纤维截面积值。(第二碳化处理·二次处理)对通过上述方法得到的一次处理纤维实施以下的二次处理。在该二次处理中,在升温中,在一次处理纤维的密度未变化的范围内或密度下降 的范围内对该纤维进行延伸处理。延伸倍率通常为0. 98 1. 02倍的范围。上述一次处理纤维的二次处理中的密度的变化及处理条件范围的一例如图8所
7J ο此外,第二碳化工序的二次延伸处理中的纤维张力(H MPa)也与一次延伸处理时 相同地,依赖于第一碳化工序后的纤维截面积(Smm2)。在本发明中,使用纤维应力(E mN) 作为张力因数。该纤维应力的范围为满足下式的范围。2. 80 > E > 0. 23(其中,E = HXSS= 3iD2/4D为第一碳化处理纤维的直径(mm))此外,第二碳化处理纤维的直径优选为4 7 μ m,更优选为4. 5 6. 5 μ m。(表面氧化处理)上述第二碳化处理纤维实施表面氧化处理。在表面氧化处理中进行气相或液相。 从工序管理的简便度方面和提高生产性的方面出发,优选液相处理。在液相处理中,从液体 的安全性、液体的稳定性的方面出发,优选使用电解液的电解处理。作为电解液中使用的电 解质,优选硫酸铵、硝酸铵等的无机酸盐。电解处理所需的电量优选每Ig碳纤维20 100 库仑。在小于20库仑/g时,表面处理不充分。在这种情况下,表面褶皱的深度小于23nm, 比表面积也小于0. 6m2/g,无法得到本发明中规定的表面形态。而且,在超过100库仑/g时, 会导致纤维强度的下降。(上浆处理)根据需要,实施了上述表面氧化处理的碳纤维接下来进行上浆处理。上浆处理能够以公知的方法进行。上浆剂能够根据用途适当使用公知的上浆剂。优选在使上浆剂均勻 附着后,进行干燥。作为上浆剂,例示有环氧系、氨基甲酸乙酯系等公知的上浆剂。(卷绕处理)上述根据需要进行了上浆处理后的碳纤维通常进行卷绕。卷绕通过现有的公知的方法进行。通常,碳纤维在9. 8 29. 4N的张力下卷绕在绕线管等上后,进行包装。由于通过上述方法制造的碳纤维在纤维表面具有褶皱,因此在与基质材料进行复 合化而制造复合材料时,表现出与基质材料的良好的粘结性,作为良好的复合材料的加强 件起作用。该碳纤维的树脂浸渍束强度、树脂浸渍束弹性率及密度高,而且细毛或断纱少。实施例以下,通过实施例及比较例更具体地说明本发明。各实施例、比较例中的处理条 件,及前驱体纤维、氧化纤维、碳纤维的物性的评价方法如下所述。(密度)各纤维的密度通过阿基米德法测定。在丙酮中对试料纤维进行了脱气处理后,测 定笛、度。(广角X射线测定(衍射角17°或26°)的微晶尺寸、配向度)使用X射线衍射装置(理学电机制RINT1200L)、计算机(日立2050/32)得到衍射 图案。从衍射图案中求出衍射角17°或26°的微晶尺寸。配向度使用半幅值求出。(束的交络度)准备测定交络度的束,切断成长度lm、制造5根束试料。固定试料的一端而使另 一端垂下。将安装了挂钩的由20g的砝码构成的夹具的挂钩挂在试料上,使砝码自然落下。 将挂钩挂在试料上的位置是距垂下的试料的上端5cm的下部,是试料宽度方向的中央。求 出砝码的落下距离(Acm),使用下式,算出各试料的交络度。各试料的交络度=100cm/Acm使测定次数η为5次而求出各试料的交络度,将它们的平均值作为该纤维束的交络度。(第一碳化工序一次延伸处理纤维的单纤维弹性率)利用JIS R 7606(2000)所规定的方法测定第一碳化工序一次延伸处理纤维的单
纤维弹性率。(碳纤维的束拉伸强度、束拉伸弹性率)通过JIS R 7601规定的方法测定第二碳化处理纤维的束强度、束弹性率。(碳纤维的形状的测定方法)碳纤维表面的褶皱的深度(峰状部分与谷状部分的高低差)作为平方平均面粗糙 度而求出。将测定用的碳纤维放置在测定用不锈钢圆盘上,并将样品的两端固定在圆盘上, 由此调制测定用试料。使用扫描型探测显微镜(DI社制SPM NanoscopeIII),以Tapping Mode测定试料。使用带有得到的数据的软件进行二次曲线修正,从修正了的数据求出碳纤 维的平方平均面粗糙度。碳纤维表面的褶皱的间隔(峰状部分的间隔)使用该扫描型探测显微镜进行测 定。利用该显微镜测定碳纤维试料的表面的2 μ m见方的范围,从得到的形状图像测量褶皱 的数目。反复进行5次同样的测定,求出褶皱的数目,再求出其平均值。根据求出的褶皱的数量的平均值,算出褶皱的间隔。(碳纤维比表面积)使用比表面积测定装置(- 7·寸7· 4才二夕7株式会社制全自动气体吸附量测 定装置AUT0S0RB-1)测定碳纤维的比表面积。提取Ig碳纤维,插入到测定装置。使用氪气, 通过规定的方法进行测定,得到比表面积的测定值。(碳纤维束的断束评价方法)使三根直径15mm的不锈钢制棒(表面粗糙度150号)(第一棒 第三棒)以各5cm的间隔相互隔离,平行固定。将碳纤维束锯齿状地缠绕在这三根棒上。在将9.8N的张 力施加在碳纤维束上的状态下,以5m/分的速度使碳纤维束从第一棒向第三棒滑动。在5 分钟的时间内观察在第三棒上滑动的纤维束,评价将纤维束分割成多个束的断束状况。(碳纤维束宽度的评价方法)利用以下的方法评价碳纤维束的宽度。以9. 8N的张力将碳纤维束卷绕在绕线管 上。测定绕线管上的纤维束宽度。沿卷绕的纤维束的长度方向,每隔Im测定5次(η = 5) 纤维束宽度,将其平均值作为纤维束宽度。(树脂浸渍后的干纤维的评价方法)利用JIS R 7601所规定的方法测定纤维束拉伸强度、纤维束拉伸弹性率,然后,使 用SEM(扫描型电子显微镜)来观察向上述试验供给的试料的断裂面。在观察树脂未附着 在纤维表面上的状态时,判断干纤维。(氧化处理工序的稳定性的评价方法)对于氧化处理工序的稳定性,将氧化处理工序中的纤维束切断发生件数为1次 /24小时以上的情况判定为工序稳定性差。将发生件数小于1次/24小时的情况判定为工 序稳定性良好。实施例1通过一个喷丝头具有24000个孔的喷丝头将纺纱原液排出到氯化锌的25质量% 的水溶液(凝固液)中,由此,连续地得到凝固线。纺纱原液是将由95质量%的丙烯腈、4 质量%的丙烯酸甲酯、1质量%的衣康酸构成的共聚体以7质量%溶解在氯化锌水溶液中 而形成的液体。在通过规定的方法对该凝固线进行水洗、涂油、干燥、延伸后,以加压空气的吹出 压为表压50kPa通过交织喷嘴。由此,得到由24000根纤维直径为9. Ομπι的丙烯系前驱体 纤维构成的交络度为3. 5的前驱体纤维束。将该纤维束向入口温度(最低温度)为230°C、出口温度(最高温度)为250°C的 热风循环式氧化炉供给,在加热空气中以1. 05的延伸倍率进行氧化处理。该氧化炉具有从 入口向出口慢慢变成高温的温度梯度。其结果,得到了纤维密度为1.36g/cm3、交络度为5 的丙烯系氧化纤维束。该氧化处理工序的工序稳定性良好,没有产生细毛、纤维向辊卷绕等 的麻烦。接下来,将该氧化纤维束向第一碳化炉供给,进行第一碳化处理,该第一碳化炉从 入口温度(最低温度)300°C朝向出口温度(最高温度)800°C慢慢升温。碳化处理包括非 活性环境中的一次延伸及二次延伸处理。一次延伸处理在图3所示的纤维弹性率持续上升的β的范围内以延伸倍率1. 05倍延伸。该一次延伸处理后的一次延伸处理纤维的单纤维弹性率为8. 8GPa、密度为1. 40g/ cm3、微晶尺寸为1. 20nm,没有发现断纱。之后,在第一碳化工序中,对该一次延伸处理纤维进行二次延伸。二次延伸是在密度持续上升的范围内且微晶尺寸不大于1.45nm的范围(图4、图5)内进行的。延伸倍率 为1. 00倍。通过该二次延伸处理,得到了密度为1. 53g/cm3、配向度为77. 1%、纤维直径为 6. 8 μ m、纤维截面积为3. 63 X IO-W的第一碳化处理纤维。第一碳化处理纤维未发现断纱。接下来,使用第二碳化炉在以下所示的条件下对该第一碳化处理纤维实施一次处 理、二次处理。第二碳化炉的内部为非活性环境,入口温度(最低温度)为800°C,出口温度 (最高温度)为1500°C。该碳化炉内部的温度具有从入口侧向出口侧慢慢变成高温的温度 梯度。首先,在密度及微晶尺寸处于如图6及图7所示的一次延伸处理条件的范围内期 间,以纤维张力28. IMPa、纤维应力1. 020mN对上述第一碳化处理纤维进行延伸处理,得到 了一次处理纤维。即,如图7所示,密度随着温度上升而增加,在达到最大值1. 9g/cm3为止 的期间内延伸。并且,如图6所示,微晶尺寸随着温度上升而暂时减少,之后开始增加,然后 在到成为1.47nm为止的期间内延伸。之后,在第二碳化工序中,继续对该一次处理纤维进行二次处理。延伸处理在图8 所示的二次处理条件的范围的密度的范围内,以纤维张力33. 7MPa、纤维应力1. 223mN进行 延伸处理,得到了第二碳化处理纤维。接下来,使用硫酸铵水溶液作为电解液,以每Ig碳纤维30库仑的电量对该第二碳 化处理纤维实施表面处理。接下来以公知的方法,将上浆剂(环氧树脂)换算成固体成分,添加1.0质量%、 进行干燥。其结果,获得密度为1. 77g/cm3、纤维直径为5. 1 μ m、束拉伸强度为5780MPa、束 拉伸弹性率为319GPa的碳纤维。在纤维表面上观察褶皱,褶皱的间隔为115nm、褶皱的深度为24nm、比表面积为 0. 65m2/g,得到了具有良好的物性的碳纤维束。该纤维束用于纤维束宽度的评价、断束的评 价。以上的结果如表1 3所示。比较例1将一个喷丝头具有12000个孔的喷丝头并列排列两个。将实施例1所使用的纺纱 原液向所述两个喷丝头供给,使纺纱液排出到凝固液(氯化锌水溶液)中而使其凝固。由 此,得到各由12000根丝构成的两束的凝固纱束。接下来,与实施例1相同地,对所述凝固 纱束实施水洗以后的处理,得到两束丙烯系前驱体纤维束。所述两束纤维束除了在第二碳 化处理时收束而形成为一束的纤维束之外,与实施例1进行同样的处理。其结果如表1所示。得到的碳纤维束的断束评价的结果是观察了断束的结果。比较例2除了将两束丙烯酸系前驱体纤维束在第一碳化处理前收束成1束纤维束之外,进 行与比较例1相同的处理,得到了碳纤维束。其结果如表1所示。得到的碳纤维束的断束 评价的结果是观察了断束的结果。比较例3
将一个喷丝头具有3000个孔的喷丝头排列8个。向所述8个喷丝头供给由实施 例1得到的纺纱原液,喷出并凝固在凝固液(氯化锌水溶液)中而凝固。由此,得到了由 3000根丝构成的8束凝固纱束。接下来,与实施例1相同地,对该凝固纱束实施水洗以后的 处理,得到了 8束丙烯酸系前驱体纤维束。所述8束纤维束除了在第二碳化处理时收束成 为一束的纤维束之外,与实施例1进行同样的处理。其结果如表1所示。得到的碳纤维束的断束评价的结果是观察了断束的结果。实施例2在交织施加处理中,除了将交织喷嘴的加压空气的吹出压形成为表压30kPa之外,与实施例1同样地进行处理。其结果如表2所示,前驱体纤维束的交络度、氧化纤维束的交络度、氧化处理工序 的稳定性都良好。得到的碳纤维如表3所示,密度为1. 77g/cm3、纤维直径为5. 1 μ m、束拉伸强度为 5795MPa、束拉伸弹性率为319GPa。在纤维表面上观察褶皱,褶皱的间隔为114nm、褶皱的深 度为24nm、比表面积为0. 64m2/g,得到了具有良好的物性的碳纤维束。该碳纤维束未发现 断束。比较例4除了未对前驱体纤维束实施交织施加处理之外,与实施例1进行了相同的处理。如表2所示,前驱体纤维束的交络度是2,氧化纤维束的交络度为4,氧化处理工序 的稳定性变差。比较例5在实施例1得到的前驱体纤维束的交织施加处理中,除了将交织喷嘴的加压空气 的吹出压形成为表压IOkPa之外,与实施例1进行同样的处理。如表2所示,前驱体纤维束 的交络度为2,氧化纤维束的交络度为4。在氧化处理工序中,存在纤维束过度开纤、氧化处 理工序的稳定性变差的问题。比较例6在实施例1得到的前驱体纤维束的交织施加处理中,除了将交织喷嘴的加压空气 的吹出压形成为表压70kPa之外,与实施例1进行同样的处理。如表2所示,前驱体纤维束 的交络度为5,氧化纤维束的交络度为10,得到的碳纤维强度低。实施例3除了将由实施例1得到的第一碳化纤维的第二碳化处理中的炉的最高温度形成 为1700°C、将第二碳化纤维的表面氧化处理中的每Ig碳纤维的电量形成为80库仑之外,与 实施例1进行同样的处理。其结果如表3所示。实施例4除了将由实施例1得到的第一碳化纤维的第二碳化处理中的炉的最高温度形成 为1400°C、将第二碳化纤维的表面氧化处理中的每Ig碳纤维的电量形成为25库仑之外,与 实施例1进行同样的处理。其结果如表3所示。比较例7除了将由实施例1得到的第二碳化纤维的表面氧化处理中的每Ig碳纤维的电量形成为15库仑之外,与实施例1进行同样的处理。结果如表3所示。碳纤维(CF)强度、碳纤维表面的褶皱的深度、比表面积都不足,无法得到具有良好的物性的碳纤维束。比较例8除了将由实施例1得到的第一碳化纤维的第二碳化处理中的炉的最高温度形成 为1350°C、将第二碳化纤维的表面氧化处理中的每Ig碳纤维的电量形成为25库仑之外,与 实施例1进行同样的处理。结果如表3所示。CF弹性率、碳纤维表面的褶皱的间隔、表面的褶皱的深度都不 足,无法得到具有良好的物性的碳纤维束。比较例9除了第一碳化处理中的延伸处理只是一次延伸处理之外,与实施例1进行了同样 的处理。结果如表3所示。CF强度不足,无法得到具有良好的物性的碳纤维束。比较例10除了第一碳化工序中的延伸处理只是二次延伸处理之外,与实施例1进行了同样 的处理。结果如表3所示。CF强度不足,无法得到具有良好的物性的碳纤维束。(表1) (表2) (表 3)
在本发明中,公开了一种碳纤维束,该碳纤维束的束拉伸强度为5650MPa以上,束拉伸弹性率为300GPa以上,束宽度为5.5mm以上,在断束评价方法中未观察到断束,该碳纤维束通过如下方法进行制造,即,使使用具有20000~30000的纺纱孔的喷丝头进行纺纱而得到的凝固纱束,通过空气的吹出压为20~60kPa的交织喷嘴中,得到前驱体纤维,然后,在加热空气中以200~280℃对所述前驱体纤维进行氧化处理,得到氧化纤维,对该氧化纤维进行第一碳化处理,然后,在惰性气体环境中,以温度1360~2100℃进行第二碳化处理,之后,在无机酸盐水溶液中以每1g碳纤维的电量为20~100库仑的方式进行表面氧化处理,所述第一碳化处理是在惰性气体环境中,以温度300~900℃、1.03~1.06的延伸倍率对所述氧化纤维进行一次延伸,之后以0.9~1.01的延伸倍率进行二次延伸。
碳纤维束及其制造方法
- 专利详情
- 全文pdf
- 权力要求
- 说明书
- 法律状态
查看更多专利详情
下载专利文献
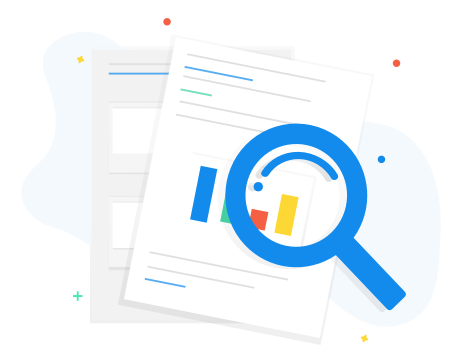
下载专利
同类推荐
-
孙德林, 余先纯孙德林, 余先纯焦万丽, 张磊焦万丽, 张磊焦万丽, 张磊曾燮榕王新, 王桂英
您可能感兴趣的专利
-
J·H·阿伦斯J·H·阿伦斯宋淑群宋淑群吉川秀和
专利相关信息
-
蒂莫·皮沃斯基, 贝恩德·威尔维斯蒂莫·皮沃斯基, 贝恩德·威尔维斯丘云灵, 熊玉李宗武吴健, 徐刘彬阿德里亚那·布里西奥, 阿德里亚那 布里西奥