硅酸盐熟料和水泥的制备方法及制备硅酸盐熟料的回转窑的制作方法【技术领域】[0001]本发明涉及建材【技术领域】,尤其涉及一种硅酸盐熟料和水泥的制备方法及制备硅酸盐熟料的回转窑。[0002]目前,随着我国《粉煤灰综合利用管理办法》的修订及鼓励支持政策的实施,粉煤灰综合利用产业得到快速发展,粉煤灰提取氧化铝生产技术得到了大力推广。在利用粉煤灰提取氧化铝生产过程中,粉煤灰熟料经溶出氧化铝后产生的固体废弃物赤泥(硅钙渣),其产量较大,每生产I吨氧化铝约产出8~10吨赤泥(硅钙渣)。该物质主要矿物组成为Y-硅酸二钙,可用作硅酸盐熟料煅烧用原料,代替部分石灰石及硅质、铝质原料。我国硅酸盐熟料生产以石灰石 为主要原材料,占配料比例70%以上,随着建材产业的发展,资源紧张、成本增高的问题也将日益突出,积极寻找石灰石的替代品或部分替代品已成为趋势。[0003]赤泥(硅钙渣)是在氧化铝熟料煅烧过程中由Y-硅酸二钙自粉化而成,其矿物组成与硅酸盐熟料相接近,除Y-硅酸二钙外,还有部分游离的氧化钙和少量的方解石、莫来石等矿物质,具有氧化钙含量高、碱含量低、活性好的特性,同时含有15%~20%的氧化硅成份及3%~6%的氧化铝成份。可替代硅酸盐熟料煅烧中的石灰石及部分硅质原料、铝质原料。如何有效合理的处理、开发和利用,实现变废为宝,具有现实意义,对推进我国粉煤灰综合利用的实施,起到积极的作用。
[0004]针对上述技术问题,本发明设计开发了硅酸盐熟料和水泥的制备方法及制备硅酸盐熟料的回转窑,目的在于更好的利用工业固体废弃物赤泥(硅钙渣),实现资源再利用,同时改善硅酸盐熟料煅烧的易烧性,降低硅酸盐熟料的能耗;提高回转窑的加热效率和硅酸盐水泥的抗压性能。[0005]本发明提供的技术方案为:[0006]一种硅酸盐熟料的制备方法,包括:
[0007]步骤一、将原料赤泥(硅钙渣)、石灰石、铁质原料、硅质原料和铝质原料以质量百分比分别为30%~83%、10%~75%、0~5%、0~10%和O~5%混合,经粉磨后制得生料;
[0008]步骤二、将上述生料输送至回转窑的预热器中预热,继而进入预分解炉进行初次分解,初次分解后的生料进入回转窑内煅烧,煅烧温度1200°C~1400°C,煅烧时间5~45min ;
[0009]步骤三、煅烧结束冷却后形成硅酸盐熟料。
[0010]优选的是,所述的硅酸盐熟料的制备方法中,所述步骤一中,所述赤泥(硅钙渣)、石灰石、铁质原料、硅质原料和铝质原料以质量百分比分别为50%、2~3%、3~5%和O~2%混合。[0011]一种硅酸盐水泥的制备方法,包括:将硅酸盐熟料、赤泥(硅钙渣)、石膏和炉渣以质量百分比分别为45 %~85 %、O %~40 %、2~10 %和4~13 %混合,经粉磨后制得硅酸盐水泥。
[0012]优选的是,所述的硅酸盐水泥的制备方法中,所述硅酸盐熟料、赤泥(硅钙渣)、石膏和炉渣的质量百分比分别为55%~75%、10%~30%、5%和10%。
[0013]一种制备硅酸盐熟料的回转窑,包括:
[0014]预热器,其包括η个旋风筒、η-1个风管、一个下料管、一个分解炉和一个窑尾烟室,各个旋风筒通过所述风管依次连接,最后一个旋风筒通过下料管与所述分解炉连通,所述分解炉连接所述窑尾烟室,原料赤泥、石灰石、铁质原料、硅质原料和铝质原料配制为生料,与进入分解炉的燃料混合、预热,生料被高速气流携带,悬浮于分解炉内,燃料随气流一面旋流向上运转,一面进行燃烧、分解,燃料的燃烧放热过程与生料的吸热分解过程同时在悬浮状态下迅速进行,生料在进入煅烧炉前完成物料初步分解;
[0015]煅烧炉,其与分解炉连通,初步分解后的物料在所述煅烧炉中进行高温煅烧,高温煅烧分两个阶段进行,第一阶段为在1200~1300°C煅烧5~15min,第二阶段为在1300~1400。。煅烧 10 ~30min ;
[0016]冷却机,煅烧后的物料在冷却机中冷却后得到硅酸盐熟料;
[0017]其中,所述旋风筒均呈倒置的圆锥形,且η个旋风筒自上而下锥角从80°依次减小至50°,相邻两个旋风筒的出料口与进料口密封连通,即位于下方的旋风筒的进料口上设置有一挡板,所述挡板上开设有进料口,所述进料口与位于上方的相邻旋风筒的出料口配合设置。
[0018]优选的是,所述的制备硅酸盐熟料的回转窑中,所述旋风筒内设置有向上运行的高温烟气换热管道,所述高温烟气换热管道设置为螺旋形,
[0019]其中,经过相邻两个旋风筒的出料口和进料口处的高温烟气换热管道设置为圆柱形。
[0020]优选的是,所述的制备硅酸盐熟料的回转窑中,η值设置在2~6之间。
[0021]本发明所述的硅酸盐熟料和水泥的制备方法及制备硅酸盐熟料的回转窑中,采用新型干法窑外分解窑煅烧硅酸盐生料,通过控制赤泥(硅钙渣)与石灰石的配比以及煅烧过程中的煅烧温度、煅烧时间等条件,实现对硅酸盐熟料的物相控制。由于赤泥(硅钙渣)的加入,物料易烧性好,物料煅烧温度较传统配料煅烧温度低、煅烧时间短,从而降低煅烧熟料能耗。经试验,熟料能耗降低30%,台时产量可提高10%。同时回转窑的旋风筒设置为锥角由上到下逐渐减小的多个倒置圆锥形结构,更有利于物料的输送,且高温烟气换热管道设置为螺旋形,增大了物料与高温烟气的换热面积,燃料的燃烧放热过程与生料的吸热分解过程同时在悬浮状态下迅速进行,有利于物料的分解,充分利用了燃料燃烧的热量。
[0022]图1是本发明所述的硅酸盐熟料的制备方法的流程示意图。
[0023]下面结合附图对本发明做进一步的详细说明,以令本领域技术人员参照说明书文字能够据以实施。
[0024]对比例
[0025]一种硅酸盐熟料的制备方法,包括:
[0026]按熟料的石灰饱和系数0.667、硅率3.5、铝率2.2配制生料,于1230°C下煅烧I小时,冷却至室温,制得硅酸盐熟料。
[0027]一种硅酸盐水泥的制备方法,包括:
[0028]将矿渣、天然硬石膏和硅酸盐熟料以质量百分比分别为86%、13%和1%混合、粉磨,制成硅酸盐水泥。按照GB17671-1999《水泥胶纱强度检验方法》测定试验的3天、7天、28天的抗压强度分别为16.4MPa、18.lMPa、22.6MPa。
[0029]实施例1
[0030]本发明提供一种硅酸盐熟料的制备方法,包括:
[0031]步骤一、将原料赤泥(硅钙渣)、石灰石、铁质原料、硅质原料和铝质原料以质量百分比分别为和2%混合,经粉磨后制得生料;
[0032]步骤二、将上述生料输送至回转窑的预热器中预热,继而进入预分解炉进行初次分解,初次分解后的生料进入回转窑内煅烧,煅烧温度1200°C~1400°C,煅烧时间5~45min ; [0033]步骤三、煅烧结束冷却后形成硅酸盐熟料。
[0034]一种硅酸盐水泥的制备方法,包括:将硅酸盐熟料、石膏和炉渣以质量百分比分别为85%、2%和4%混合,经粉磨后制得硅酸盐水泥,测得3天后抗压强度为27.5MPa,7天后抗压强度为38.5MPa,28天后抗压强度为59.1MPa0
[0035]一种制备硅酸盐熟料的回转窑,包括:
[0036]预热器,其包括2个旋风筒、I个风管、一个下料管、一个分解炉和一个窑尾烟室,各个旋风筒通过所述风管依次连接,最后一个旋风筒通过下料管与所述分解炉连通,所述分解炉连接所述窑尾烟室,原料赤泥、石灰石、铁质原料、硅质原料和铝质原料配制为生料,与进入分解炉的燃料混合、预热,生料被高速气流携带,悬浮于分解炉内,燃料随气流一面旋流向上运转,一面进行燃烧、分解,燃料的燃烧放热过程与生料的吸热分解过程同时在悬浮状态下迅速进行,生料在进入煅烧炉前完成物料初步分解;
[0037]煅烧炉,其与分解炉连通,初步分解后的物料在所述煅烧炉中进行高温煅烧,高温煅烧分两个阶段进行,第一阶段为在1200°C煅烧5min,第二阶段为在1300°C煅烧IOmin
[0038]冷却机,煅烧后的物料在冷却机中冷却后得到硅酸盐熟料;
[0039]其中,所述旋风筒均呈倒置的圆锥形,且2个旋风筒自上而下锥角从80°减小至70°,相邻两个旋风筒的出料口与进料口密封连通,即位于下方的旋风筒的进料口上设置有一挡板,所述挡板上开设有进料口,所述进料口与位于上方的相邻旋风筒的出料口配合设置。
[0040]所述的制备硅酸盐熟料的回转窑中,所述旋风筒内设置有向上运行的高温烟气换热管道,所述高温烟气换热管道设置为螺旋形,
[0041]其中,经过相邻两个旋风筒的出料口和进料口处的高温烟气换热管道设置为圆柱形。
[0042]实施例2[0043]本发明提供一种硅酸盐熟料的制备方法,包括:
[0044]步骤一、将原料赤泥(硅钙渣)、石灰石、铁质原料、硅质原料和铝质原料以质量百分比分别为和2%混合,经粉磨后制得生料;
[0045]步骤二、将上述生料输送至回转窑的预热器中预热,继而进入预分解炉进行初次分解,初次分解后的生料进入回转窑内煅烧,煅烧温度1200°C~1400°C,煅烧时间5~45min ;
[0046]步骤三、煅烧结束冷却后形成硅酸盐熟料。
[0047]一种硅酸盐水泥的制备方法,包括:将硅酸盐熟料、赤泥(硅钙渣)、石膏和炉渣以质量百分比分别为和7%混合,经粉磨后制得硅酸盐水泥,测得3天后抗压强度为30.8MPa,7天后抗压强度为39.2MPa,28天后抗压强度为60.1MPa0
[0048]一种制备硅酸盐熟料的回转窑,包括:
[0049]预热器,其包括3个旋风筒、2个风管、一个下料管、一个分解炉和一个窑尾烟室,各个旋风筒通过所述风管依次连接,最后一个旋风筒通过下料管与所述分解炉连通,所述分解炉连接所述窑尾烟室,原料赤泥、石灰石、铁质原料、硅质原料和铝质原料配制为生料,与进入分解炉的燃料混合、预热,生料被高速气流携带,悬浮于分解炉内,燃料随气流一面旋流向上运转,一面进行燃烧、分解,燃料的燃烧放热过程与生料的吸热分解过程同时在悬浮状态下迅速进行,生料在进入煅烧炉前完成物料初步分解;
[0050]煅烧炉,其与分解炉连通,初步分解后的物料在所述煅烧炉中进行高温煅烧,高温煅烧分两个阶段进行,第一阶段为在1250°C煅烧8min,第二阶段为在1330°C煅烧15min ;
[0051]冷却机,煅烧后的物料在冷却机中冷却后得到硅酸盐熟料;
[0052]其中,所述旋风筒均呈倒置的圆锥形,且3个旋风筒自上而下锥角从80°依次减小至60°,即分别为80°、70°、60°,相邻两个旋风筒的出料口与进料口密封连通,即位于下方的旋风筒的进料口上设置有一挡板,所述挡板上开设有进料口,所述进料口与位于上方的相邻旋风筒的出料口配合设置。
[0053]所述的制备硅酸盐熟料的回转窑中,所述旋风筒内设置有向上运行的高温烟气换热管道,所述高温烟气换热管道设置为螺旋形,
[0054]其中,经过相邻两个旋风筒的出料口和进料口处的高温烟气换热管道设置为圆柱形。
[0055]实施例3
[0056]本发明提供一种硅酸盐熟料的制备方法,包括:
[0057]步骤一、将原料赤泥(硅钙渣)、石灰石、铁质原料和硅质原料以质量百分比分别为65%、33%、2%和3%混合,经粉磨后制得生料;
[0058]步骤二、将上述生料输送至回转窑的预热器中预热,继而进入预分解炉进行初次分解,初次分解后的生料进入回转窑内煅烧,煅烧温度1200°C~1400°C,煅烧时间5~45min ;
[0059]步骤三、煅烧结束冷却后形成硅酸盐熟料。
[0060]一种硅酸盐水泥的制备方法,包括:将硅酸盐熟料、赤泥(硅钙渣)、石膏和炉渣以质量百分比分别为和10%混合,经粉磨后制得硅酸盐水泥,测得3天后抗压强度为31.1MPa, 7天后抗压强度为40.3MPa,28天后抗压强度为60.6MPa。[0061]一种制备硅酸盐熟料的回转窑,包括:
[0062]预热器,其包括4个旋风筒、3个风管、一个下料管、一个分解炉和一个窑尾烟室,各个旋风筒通过所述风管依次连接,最后一个旋风筒通过下料管与所述分解炉连通,所述分解炉连接所述窑尾烟室,原料赤泥、石灰石、铁质原料、硅质原料和铝质原料配制为生料,与进入分解炉的燃料混合、预热,生料被高速气流携带,悬浮于分解炉内,燃料随气流一面旋流向上运转,一面进行燃烧、分解,燃料的燃烧放热过程与生料的吸热分解过程同时在悬浮状态下迅速进行,生料在进入煅烧炉前完成物料初步分解;
[0063]煅烧炉,其与分解炉连通,初步分解后的物料在所述煅烧炉中进行高温煅烧,高温煅烧分两个阶段进行,第一阶段为在1280°C煅烧12min,第二阶段为在1370°C煅烧20min ;
[0064]冷却机,煅烧后的物料在冷却机中冷却后得到硅酸盐熟料;
[0065]其中,所述旋风筒均呈倒置的圆锥形,且4个旋风筒自上而下锥角从80°减小至50°,即分别为80°、70°、60°、50°,相邻两个旋风筒的出料口与进料口密封连通,即位于下方的旋风筒的进料口上设置有一挡板,所述挡板上开设有进料口,所述进料口与位于上方的相邻旋风筒的出料口配合设置。
[0066]所述的制备硅酸盐熟料的回转窑中,所述旋风筒内设置有向上运行的高温烟气换热管道,所述高温烟气换热管道设置为螺旋形,
[0067]其中,经过 相邻两个旋风筒的出料口和进料口处的高温烟气换热管道设置为圆柱形。
[0068]实施例4
[0069]本发明提供一种硅酸盐熟料的制备方法,包括:
[0070]步骤一、将原料赤泥(硅钙渣)、石灰石、铁质原料、硅质原料和铝质原料以质量百分比分别为83 %、10 %、2 %、I %和4 %混合,经粉磨后制得生料;
[0071]步骤二、将上述生料输送至回转窑的预热器中预热,继而进入预分解炉进行初次分解,初次分解后的生料进入回转窑内煅烧,煅烧温度1200°C~1400°C,煅烧时间5~45min ;
[0072]步骤三、煅烧结束冷却后形成硅酸盐熟料。
[0073]一种硅酸盐水泥的制备方法,包括:将硅酸盐熟料、赤泥(硅钙渣)、石膏和炉渣以质量百分比分别为45140^5%和13%混合,经粉磨后制得硅酸盐水泥,测得3天后抗压强度为31.9MPa,7天后抗压强度为41.6MPa,28天后抗压强度为62.3MPa。
[0074]一种制备硅酸盐熟料的回转窑,包括:
[0075]预热器,其包括6个旋风筒、5个风管、一个下料管、一个分解炉和一个窑尾烟室,各个旋风筒通过所述风管依次连接,最后一个旋风筒通过下料管与所述分解炉连通,所述分解炉连接所述窑尾烟室,原料赤泥、石灰石、铁质原料、硅质原料和铝质原料配制为生料,与进入分解炉的燃料混合、预热,生料被高速气流携带,悬浮于分解炉内,燃料随气流一面旋流向上运转,一面进行燃烧、分解,燃料的燃烧放热过程与生料的吸热分解过程同时在悬浮状态下迅速进行,生料在进入煅烧炉前完成物料初步分解;
[0076]煅烧炉,其与分解炉连通,初步分解后的物料在所述煅烧炉中进行高温煅烧,高温煅烧分两个阶段进行,第一阶段为在1300°C煅烧15min,第二阶段为在1400°C煅烧30min ;
[0077]冷却机,煅烧后的物料在冷却机中冷却后得到硅酸盐熟料;[0078]其中,所述旋风筒均呈倒置的圆锥形,且6个旋风筒自上而下锥角从80°减小至50°,即分别为80°、75°、70°、60°、55°、50°,相邻两个旋风筒的出料口与进料口密封连通,即位于下方的旋风筒的进料口上设置有一挡板,所述挡板上开设有进料口,所述进料口与位于上方的相邻旋风筒的出料口配合设置。
[0079]所述的制备硅酸盐熟料的回转窑中,所述旋风筒内设置有向上运行的高温烟气换热管道,所述高温烟气换热管道设置为螺旋形,
[0080]其中,经过相邻两个旋风筒的出料口和进料口处的高温烟气换热管道设置为圆柱形。
[0081]由此可知,利用本发明所述的方法制备的硅酸盐水泥的抗压性能得到了显著提高。四个实施例中,硅酸盐熟料中各个组分的平均含量SiO2为21.75%, Al2O3为5.44%,Fe2O3 ^ 3.62%, CaO为65.52%, MgO为2.03%,石灰饱和系数为0.908,硅率为2.4,铝率为 1.50。
[0082]尽管本发明的实施方案已公开如上,但其并不仅仅限于说明书和实施方式中所列运用,它完全可以被适用于各种适合本发明的领域,对于熟悉本领域的人员而言,可容易地实现另外的修改,因 此在不背离权利要求及等同范围所限定的一般概念下,本发明并不限于特定的细节和这里示出与描述的图例。
硅酸盐熟料和水泥的制备方法及制备硅酸盐熟料的回转窑制作方法
- 专利详情
- 全文pdf
- 权力要求
- 说明书
- 法律状态
查看更多专利详情
下载专利文献
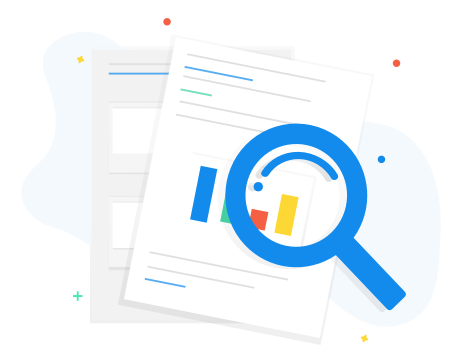
下载专利
同类推荐
-
张声军M·J·德内卡, S·戈麦斯M·J·德内卡, S·戈麦斯
您可能感兴趣的专利
-
王善祝, 王明刘杰, 吕春叶强
专利相关信息
-
叶强陈凯, 陈树德张雷谭纪林李明照