专利名称:玻璃粒子、玻璃粒子集合体及玻璃粒子的制造方法 一直以来,玻璃材料被用于形成陶瓷电子部件方面、陶瓷的低温烧结用助剂或基板材料、电极的接合材料、绝缘处理用保护膜材料等多种领域中。例如,在叠层陶瓷电容器中,将添加了玻璃粒子的材料作为烧结助剂使用,或在外部电极内作为玻璃料(glass frit)混合使用。另外,在电阻材料中,被用于形成绝缘电阻部分。虽然玻璃材料当像这样与陶瓷或金属等混合使用或利用其绝缘特性单独使用时,可以用于很多领域中,但是,以往的玻璃材料多为对用熔融急冷法制作的大块玻璃进行机械粉碎处理而得的材料。所以,有如下的特征,即,所能达到的微小化的粒径有限,并且粒度分布较宽,其形状也不均一,形成许多凝聚体等。当将该玻璃材料用于所述用途时,与陶瓷或金属材料、有机物等物质机械混合而使用。在像这样将熔融急冷法的玻璃材料与其他物质混合而使用的应用中,会由于其形状不均一,凝聚体较多而产生难以获得高密度的均一分散状态的问题。针对这些问题,已经提出有在玻璃粒子的内部封入了氧化物粒子的玻璃微粒(例如参照专利文献1)和在金属粉末的至少一部分上形成了玻璃薄膜的金属粉末的技术方案(例如参照专利文献2)。特开2001-302282号公报[专利文献2]特开平10-330802号公报但是,专利文献1中,由于需要准备玻璃粉末作为原料粉的工序,因此工序数量增多。另外,由于经过利用等离子体形成的气相状态来形成氧化物封入玻璃,因此无法使用能够在玻璃中固溶的金属晶种,或者无法内包金属粒子,因而有必要限定玻璃的组成。另外,专利文献2中,对利用喷雾热分解法制作由玻璃层覆盖的金属粉末进行了公布。具体来说,将含有1种或2种以上的热分解性金属化合物的溶液进行喷雾,形成微小的液滴,通过在比金属化合物的分解温度更高的温度下对该液滴加热而进行热分解,析出金属粉末。此时,通过在金属化合物溶液中预先添加氧化物前驱体等,就可以在生成金属粉末的同时,进行玻璃包覆。但是,在喷雾热分解法中所使用的原料溶液中,使用无机化合物(硝酸盐、氯化物等)或有机化合物(烷氧基金属醇盐等)、凝胶(氧化硅凝胶或氧化铝凝胶等)等的混合溶液或混合凝胶。一般来说,考虑到原料成本和生产效率的因素,玻璃构成元素的至少一部分元素要使用将硝酸盐或硫酸盐、醋酸盐、氯化物等可溶性盐溶解于溶剂中的物质。所以,考虑到溶液稳定性,有必要将溶液的pH调整为酸性,因而要使用硝酸或硫酸等强酸。当在该原料溶液中添加要内包的金属粒子时,金属会溶解在溶液中,从而导致内包金属的组成或玻璃的组成与设计组成不同。另外,当在大气中对该原料溶液进行喷雾热分解时,还会有金属粒子暴露在高温的大气中而氧化的问题。
鉴于以上问题,本发明的目的在于,在将玻璃粉末和金属粉末混合使用的应用中,取消玻璃粉末和金属粉末的混合工序。
另外的目的在于,提供在玻璃粒子中内包的金属的种类或玻璃的组成方面没有限定的、内包了更宽组成范围的金属的玻璃粒子、玻璃粒子集合体及玻璃粒子的制造方法。
而且,本发明的目的还在于,提供如下的玻璃粒子、玻璃粒子集合体及玻璃粒子的制造方法,即,即使使用硝酸或硫酸等强酸作为喷雾热分解法的原料溶液,金属粒子也不会被溶解,即使在喷雾热分解时与大气接触,也可以防止被氧化。
本发明为了达成所述目的,采用如下的构成。
即,本发明的玻璃粒子的特征是,是内包了金属粒子的玻璃粒子,所述金属粒子的表面被氧化物膜覆盖。
所述氧化物膜最好含有所述玻璃粒子的构成元素。
所述氧化物膜最好含有氧化硅、氧化硼及氧化磷当中至少任意1种。
所述玻璃粒子的粒径最好为被内包的所述金属粒子的粒径的2倍以上20万倍以下。
另外,本发明的玻璃粒子的特征是,多个所述金属粒子在被分散的状态下被内包。
另外,本发明的玻璃粒子的特征是,具有从所述玻璃粒子的中心向外侧层叠了由不同玻璃成分构成的多个玻璃层而形成的多层构造。
另外,本发明的玻璃粒子集合体是所述玻璃粒子集合而成的玻璃粒子集合体,其特征是,平均粒径在0.01μm以上10μm以下。
另外,本发明的玻璃粒子的制造方法的特征是,是内包了金属粒子的玻璃粒子的制造方法,该制造方法包括用氧化物膜覆盖被内包的所述金属粒子的表面的工序、在含有玻璃的构成元素的溶液中混合由氧化物膜覆盖了表面的所述金属粒子而制作原料料浆的工序、将所述原料料浆形成液滴而导入高温的炉体内部进行热分解的工序。
所述热分解的温度最好高于所述玻璃的玻璃化温度。
另外,本发明的玻璃粒子的制造方法的特征是,还包括将所得的玻璃粒子混合在含有与所述玻璃粒子不同的玻璃成分的溶液中而制作原料料浆的工序、将所制作的所述原料料浆形成液滴而导入高温的炉体内部进行热分解的工序。
如果使用本发明的玻璃粒子,由于当使玻璃粒子分散在溶剂中时,玻璃粒子抑制了金属粒子的移动,因而可以防止金属粒子的凝聚,从而可以制作出玻璃粒子和金属粒子均一地分散的料浆。
另外,如果采用本发明的玻璃粒子的制造方法,就不需要准备玻璃粉末和金属粉末的各自的原料粉末、混合、熔融、粉碎之类的较多的工序,因而能够以较少的工序高效率并且低成本地提供预先内包了金属粒子的玻璃粒子。而且,还可以提供在金属粒子的种类和玻璃粒子的组成上没有限制的富于变化的玻璃粒子或玻璃粒子集合体。
图1是表示本发明的内包金属玻璃粒子的制造方法的一个例子的制造工序的方框图。
图2是进行了氧化硅涂覆处理的镍粒子。
图3是本发明中使用的喷雾热分析装置。
图4是实施例1的条件下制作的本发明的内包金属玻璃粒子集合体的XRD图。
图5是以往的玻璃粒子集合体的XRD图。
图6是实施例2~4的条件下制作的本发明的内包金属玻璃粒子集合体的XRD图。
图7是实施例1的条件下制作的本发明的内包金属玻璃粒子集合体的TG-DTA图。
图8是以往的玻璃粒子集合体的TG-DTA图。
图9是表示实施例1的条件下制作的本发明的内包金属玻璃粒子的SEM照片的2次电子图像和反射电子图像。
图10是表示以往的玻璃粒子的SEM照片的2次电子图像和反射电子图像。
图11是表示实施例2的条件下制作的本发明的内包金属玻璃粒子的SEM照片的2次电子图像和反射电子图像。
图12是表示实施例2的条件下制作的本发明的内包金属玻璃粒子的TEM照片和EDX观测点。
图13是图12所示的TEM照片整体的EDX图。
图14是图12中的EDX测定点1的EDX图。
图15是图12中的EDX测定点2的EDX图。
图中,1—金属粒子的制作工序,2—涂覆氧化物膜的工序,3—制作喷雾溶液的工序,4—溶液的混合分散处理工序,6—喷雾热分解工序
下面对本发明的实施方式进行详细的说明。
本发明的玻璃粒子是内包金属粒子的玻璃粒子(以下称为「内包金属玻璃粒子」)。另外,本发明的所谓玻璃粒子集合体是指多个所述内包金属玻璃粒子集合而成的物质,具体来说,表示玻璃粉末。
作为玻璃粒子的玻璃的构成元素,可以包括Si、B、P、Li、Na、K、Mg、Ca、Ti、Cu、Al、Ba、Zn、Ga、Ge、Pb、Bi的至少任意一个元素。具体来说,最好包括作为网络形成氧化物的氧化硅、氧化硼及氧化磷中的至少任意1种。玻璃粒子只要是具有玻璃化温度及玻璃软化温度的材料,既可以仅由非晶体玻璃构成,也可以包含晶体玻璃。另外,也可以包含在对玻璃粒子进行加热时结晶化的结晶化玻璃。
玻璃粒子的粒径虽然只要内包金属粒子,就没有特别的限制,但是在实用上优选0.1μm~1000μm。当玻璃粒子的粒径过小时,例如在利用后述的喷雾热分解法制作玻璃粒子时,就有必要减缓原料料浆的供给速度等,因而会造成生产效率降低。另一方面,当玻璃粒子的粒径过大时,在玻璃粒子的形成中会花费较多时间,或者需要大型的装置。
另外,玻璃粒子的粒径最好为金属粒子的粒径的2倍以上20万倍以下。当玻璃粒子的粒径在金属粒子的粒径的2倍以上时,就很容易内包金属粒子。另外,由于玻璃粒子的量相对于金属粒子相对变多,因此玻璃粒子作为结合剂、接合剂的作用得到加强。因此,如果像这样使用玻璃量相对较多的内包金属玻璃粒子,则不需要另外添加玻璃料等结合剂、接合剂。而且,20万倍以下的上限是从已经说明了的玻璃粒子的粒径的实用范围和后述的金属粒子的粒径的实用范围导出的。
另外,虽然玻璃粒子的形状最好为球状,但是也可以是近似球状,只要是对作为目的的用途不造成妨碍的形状即可。
另外,玻璃粒子也可以具有从所述玻璃粒子的中心向外侧层叠了由不同玻璃成分构成的多个玻璃层的多层构造。这里所说的「不同玻璃成分」不仅意味着构成玻璃的元素不同。「不同玻璃成分」是指,即使构成玻璃的元素相同,玻璃化温度、玻璃软化温度或熔融温度等作为玻璃的特性也不同。所以,当将具有该多层构造的玻璃粒子切成圆片时,切口就会像树的年轮那样,像所谓的Baumkuhen那样,从中心向外侧形成多个特性不同的层。
通过采用此种多层构造,例如就可以在玻璃粒子的外侧和中心部使特性梯度变化,因此就可以获得如下的特性,即,外侧的玻璃成分在低温下软化,而中心部的玻璃成分不会达到高温。
通过形成此种具有多层构造的内包金属玻璃粒子,例如就可以使具有不同热特性的玻璃成分作为一个粒子而存在,通过在玻璃成分中选择适当的物质,就可以任意地设计玻璃化温度或结晶化温度、熔融温度等各种特性。
玻璃层的层数要根据目的来适当地选择。另外,各玻璃层的玻璃组成要根据烧结助剂或糊状物等所使用的用途来适当地选择符合其特性的组成,因而并不是被特别限定的。
作为金属粒子,只要在Cu、Ni、Ag、Pt、Au、Pd、Al等金属当中含有1种以上即可。另外,还可以使用单金属成分或含有多金属成分的合金、单金属成分之间的混合物、单金属和合金的混合物或合金之间的混合物。在叠层陶瓷电容器等陶瓷电子部件中,由于多使用单金属的镍或铜作为电极材料,因此金属粒子最好为镍、铜或镍合金、铜合金。
虽然金属粒子最好被完全地包含在玻璃粒子的内部,但是其一部分也可以从玻璃粒子的表面显露出来。在本说明书中,「内包」的含意也包括像这样金属粒子的一部分从玻璃粒子的表面显露出来的情况。
金属粒子在表面具有氧化物膜。这样,例如即使当将玻璃粒子混合在强酸的溶剂中时,金属粒子也不会溶解,而可以稳定地存在。氧化物膜也可以含有氮化物或碳化物。另外,氧化物膜最好由与玻璃粒子的玻璃成分具有相溶性的物质构成,更优选含有玻璃粒子的构成元素。通过形成此种氧化物膜,就可以获得与金属的种类或玻璃组成无关的富于变化的内包金属玻璃粒子。
金属粒子的粒径在实用上优选5nm~100μm。当金属粒子的粒径过小时,金属粒子的制造在技术上就会变得很困难。另一方面,当金属粒子的粒径过大时,内包金属玻璃粒子的重量增大,在混合到溶剂中时很容易沉降,因而分散性降低。
另外,也可以在使多个金属粒子分散后的状态下将其内包于玻璃粒子中。此种构造例如在使很多金属粒子分散在溶剂中时十分有效。
另外,内包金属玻璃粒子可以作为集合体使用。具体来说,各个粒子表示由本发明的内包金属玻璃粒子形成的玻璃粉末等。
虽然该内包金属玻璃粒子被单独使用也会具有相同的特性,但是也可以与具有不同特性的内包金属玻璃粒子混合而作为玻璃粒子的集合体使用。
该内包金属玻璃粒子集合体能够以各种各样的形态使用。例如,能够以薄膜、块状成形体、薄片、糊状物等形态使用。
另外,内包金属玻璃粒子集合体的平均粒径最好在0.01μm以上10μm以下的范围内。为了获得具有平均粒径小于0.01μm的粒径的内包金属玻璃粒子集合体,需要降低溶液浓度,采用静电喷雾或超声波喷雾法等可以形成微小的液滴的雾化方法,因此,有粒子的生成效率变差,对生产效率产生不良影响的情况。另一方面,当平均粒径超过10μm时,就会对与陶瓷的混合或作为糊状物使用时的印刷性或表面平滑性产生不良影响。
所以,在对内包金属玻璃粒子的生产效率或印刷性、表面平滑性不产生影响的应用中,也可以在该平均粒径范围之外。这里所说的平均粒径是由利用扫描电子显微镜等可以观察粒子形状的观察工具获得的粒子图像求得的粒子直径的平均值。
下面将对作为本发明的一个实施方式的内包金属玻璃粒子的制造方法进行叙述,同时对本发明的内包玻璃金属粒子进行更详细的说明。
图1是表示本发明的一个实施方式的内包金属玻璃粒子的制造方法的工序的方框图。
该实施方式的内包金属玻璃粒子的制造方法具有制作内包于玻璃粒子中的金属粒子的工序1、用氧化物膜涂覆金属的表面的工序2、制作含有玻璃的构成元素的喷雾溶液的工序3、在该喷雾溶液中对涂覆了氧化物膜的金属粒子进行混合分散处理而制作原料料浆的工序4、将该原料料浆制成微小的液滴形状导入已经加热的炉体内,通过利用来自炉体的辐射热将原料料浆热分解,然后急冷,获得内包金属玻璃粒子5的喷雾热分解工序6。
喷雾热分解法是适于制得球状的玻璃粒子的方法,是可以通过将含有玻璃的构成元素的溶液制成微小的液滴形状而导入已经加热的炉体内,利用来自炉体的辐射热将原料溶液热分解,然后急冷,获得作为目的物的玻璃粒子的方法。
但是,作为喷雾热分解法的原料溶液,一般使用将硝酸盐或硫酸盐、醋酸盐、氯化物等的可溶性盐作为玻璃构成元素的至少一部分的元素溶解于溶剂中的溶液,因此,考虑到溶液稳定性,有必要将溶液的pH值调整为酸性,因而需要使用硝酸或硫酸等强酸。
所以,当在该原料溶液中添加混合要内包于玻璃粒子中的金属粒子时,金属就会溶解,因而产生金属的表面及玻璃的接触部分的组成发生变化的问题。另外,当在大气中对该原料溶液进行喷雾热分解时,金属的粒子暴露在高温的大气中,因而还会产生氧化的问题。
考虑到这个问题,最好像该实施方式那样,设置对内包于玻璃粒子中的金属粒子的表面进行改性的工序。即,最好用具有对酸的耐溶解性和/或耐氧化性的氧化物膜对金属粒子的表面进行改性。
本发明的实施方式中使用的制作装置,即喷雾热分解装置可以使用公知的装置,炉体的加热温度或粒子输送速度、喷雾方法或喷雾条件可以根据喷雾原料溶液的种类、玻璃的组成或特性进行适当地选择。通过像这样使用喷雾热分解法,就可以不用经过像以往技术那样的使用玻璃粉末单体和金属粉末单体作为原料,进行原料的粉碎或混合之类的工序,而可以从在玻璃溶液中分散了金属粒子的原料料浆直接形成内包金属玻璃粒子,因此就能够以低成本短时间地获得内包金属玻璃粒子。
另外,由于以料浆状态使内包金属玻璃粒子的构成元素混合,因此还具有玻璃粒子的组成更加均一的特征。在此种喷雾热分解法中,只要可以供给使料浆热分解并产生粒子的热量,不仅可以利用来自炉体的辐射热加热,还可以采用利用火焰的直接加热的方法等公知的加热方法。
该喷雾热分解法中的原料料浆的加热温度至少需要比作为目的的玻璃化温度更高,更优选的是,通过设定为玻璃的熔融温度以上的温度,就可以容易地制成玻璃粒子。
另外,一般在玻璃的制作中,进行熔融玻璃的急冷,利用使用了热等离子体的高温气相场来进行玻璃粒子的合成,还要进行玻璃粒子的急冷用气体的供给等,但是利用本发明的方法中,由于从进行热分解的炉体到回收装置的输送路径的温度梯度很陡,因此没有必要特别进行急冷用气体的供给,而可以通过调节玻璃粒子的输送速度来容易地合成。当然,根据玻璃组成,有时需要比设计温度梯度更陡的梯度,因而就需要冷却气体的供给等冷却手段,但是使用该冷却手段也是可以的。
原料料浆的雾化方法虽然可以使用双流体喷嘴喷雾法或超声波喷雾法、静电喷雾法等公知的方法,但是考虑到生产效率和使喷雾溶液与悬浮的金属粒子均一地雾化,最好使用双流体喷嘴喷雾法作为进行雾化的方法。
要制作的内包金属玻璃粒子的粒径可以通过调整原料料浆的浓度、雾化条件来获得作为目的的粒径。即,当使用双流体喷嘴喷雾法时,如果要缩小内包金属玻璃粒子的粒径,只要降低原料料浆的浓度,并减缓向喷嘴供给的原料料浆的供给速度,增多喷雾用气体的流量即可。另外,相反,当要增大内包金属玻璃粒子的粒径时,只要增大原料料浆的浓度,并加快向喷嘴供给的原料料浆的供给速度,减少喷雾用气体的流量即可。
不管怎样,只要使该液滴状的原料料浆的大小达到使金属粒子被内包于玻璃粒子的内部的状态的大小即可,为此,使液滴状的原料料浆的大小达到例如添加到原料料浆中的被内包的金属粒子的粒径的2倍以上即可,金属粒子即成为内包于玻璃粒子的内部的状态。
由于可以像这样在使原料料浆形成雾滴的阶段中,对用喷雾热分解法制作的内包金属玻璃粒子的粒径进行调整,因此就不需要为了控制内包金属玻璃粒子的粒径而在合成后进行粉碎或筛分等后处理。因而就可以利用较少的工序以高效率获得内包金属玻璃粒子。当然,这要根据目的,并不是要限制进行粉碎或筛分等处理。
另外,利用喷雾热分解法合成的内包金属玻璃粒子由过滤器等回收装置回收。对于该回收方法也没有限制。
另外,本发明的特征是,使用在含有玻璃粒子的构成元素的溶液中混合了内包的金属的粒子的原料料浆,并且其特征在于,通过将该原料料浆形成液滴的状态后的物质导入高温的炉体内部并使之热分解来制造。
所以,在利用所述方法形成雾状的液滴的内部,已经被内包的金属粒子以分散的状态存在,因而,如果预先将原料料浆中所内包的金属粒子调整至所需的粒径及浓度,则不需要实施退火等热处理来使金属析出,就可以获得内包金属玻璃粒子。另外,即使在因原料料浆的热分解而造成的体积收缩等反应中,由于被内包的金属粒子的粒径及浓度不发生变化,因此就可以实现在玻璃粒子的内部的内包,使之达到所需的粒径及浓度。
这里,所谓被内包的金属粒子的浓度是指体积浓度。
本发明中,对所述原料料浆中悬浮的内包用的金属粒子如所述那样,进行了对其表面用含有玻璃的构成元素的氧化物膜覆盖的表面改性。通过进行该耐溶解性的表面改性,即使要内包的金属的粒子悬浮于原料料浆中,也不会溶解于强酸溶剂中,因而可以使之稳定地存在。
另外,最好像这样,在本发明的内包金属玻璃粒子的制造方法中,利用在要内包的金属的表面形成氧化物膜的工序来赋与耐溶解性,这样,在本质上就不会对要内包的金属的种类或形状、粒径等金属的特性造成限制,还可以内包玻璃的构成元素的金属。
作为含有玻璃粒子的玻璃的构成元素的氧化物膜,虽然可以合适地使用作为玻璃的网络构造构成元素的氧化硅,但是,只要是具有对酸性溶液的耐溶解性的物质,就没有特别的限制,也可以含有氮化物、碳化物等。含有该玻璃的构成元素的氧化物的形成方法可以利用烷氧基金属醇盐的水解而容易地获得。下面将叙述具体的表面改性氧化物的形成方法的一个例子。
首先,准确地称量出所需量的要内包的金属粒子,使之分散在乙醇等非水溶剂中。准确地称量出达到所需涂覆厚度的量的作为表面改性物质的原料的原硅酸四乙酯等烷氧基金属醇盐,并添加到该分散了金属粒子的非水溶剂中,进行分散处理。
然后,在乙醇等非水溶剂中添加能够将原硅酸四乙酯充分水解的量的水。继而,向分散了金属和烷氧基金属醇盐的溶液中,一边进行分散处理,一边滴下添加了水的水解用溶液,使烷氧基金属醇盐水解,在金属粒子的表面形成表面改性氧化物。
此种方法是表面改性氧化物的形成方法的一个例子,当然,也可以使用其他的在金属粒子的表面形成表面改性氧化物的方法。该表面改性氧化物的形成方法也可以使用作为气相中的涂覆法的CVD法或溅射法、其他的液相法。
该方法的特征是,通过像这样对要内包的金属粒子的表面进行改性,形成氧化物膜,就可以抑制在原料料浆热分解时产生的内包金属的氧化反应,因此就可以采用大气气氛作为喷雾热分解时的气氛,不需要为了抑制金属的氧化而进行使用还原性气氛等特殊的调整。所以,即使在原料料浆中不使用酸性溶液,而使用有机金属化合物的混合物或凝胶混合物的情况下,最好也进行该表面改性。
而且,虽然使用酸性溶液及有机金属化合物等作为本发明的原料料浆而制得的内包金属玻璃粒子的酸性溶液及有机金属化合物等的构成元素,例如氮或碳有可能有从几个ppm到1.0wt%以下程度的残留,但是,可以根据使用本发明的玻璃粒子的用途,对残留量进行适当调整。
通过使如所述那样制作的内包金属玻璃粒子悬浮于含有具有不同特性的玻璃成分的原料料浆中,利用所需的喷雾方式形成微小的液滴,并使之热分解,使原料料浆的玻璃成分形成于悬浮的内包金属玻璃粒子的表面,就可以获得具有以内包金属玻璃粒子为核、用其他的玻璃成分覆盖了其表面的构造的玻璃粒子。
另外,通过反复进行具有该构造的内包金属玻璃粒子的制造工序,就可以制成至少2层以上的多层构造,从而可以更精密地控制各个特性。例如,使用含有具有比该玻璃组成的熔点更低的熔点的玻璃成分的原料料浆,与制作内包金属玻璃粒子时相同,利用喷雾热分解法,就可以制作内包金属玻璃粒子。
下面将基于实施例对本发明的详细内容进行说明。
(实施例1)内包金属的制作利用在气体中的蒸发法制作了作为要内包的金属粒子的镍粒子。在将氦气氛气压调整至6.65kPa的反应器内,向氧化镁坩锅内加入镍锭80g,利用施加了54A的感应电流的感应线圈的感应加热,加热至大约1800℃,使之蒸发。在以每分钟4升的速度供给的氦气流中将蒸发的镍冷却,利用过滤器回收。制作的镍粒子集合体的比表面积直径为30nm。
在用于使内包金属具有耐溶解性的氧化物涂覆物乙醇溶液中,加入利用所述方法制作的镍粒子集合体,并加入可以在镍粒子集合体的表面形成厚2nm、6nm、8nm的氧化硅膜的量的原硅酸四乙酯(TEOS),利用超声波分散机进行30分钟的分散处理。然后,向乙醇中加入TEOS的5倍的量的氨和10倍的量的水,进行了充分的搅拌处理。继而,以每秒1cc的速度,向添加了镍粒子集合体和TEOS的乙醇溶液中,滴下混合了氨和水的乙醇溶液,进行TEOS的水解反应。在该水解后,利用过滤将形成了氧化硅膜的镍粒子集合体与溶剂分离,进而添加乙醇,通过进行超声波清洗,除去了未反应的TEOS、氨。其后,进行真空干燥,得到分别形成了2nm、6nm、8nm的氧化硅膜的镍粒子集合体。
图2表示用透射电子显微镜(TEM)观察到的利用该水解处理制作的镍粒子集合体的结果。
表面的氧化硅膜的膜厚为与设计相同的2nm、6nm、8nm,图2(a)所示的形成了2nm的氧化硅膜的镍粒子集合体中,氧化硅膜的表面的凹凸较大,未形成均一厚度,但是图2(b)、(c)中分别所示的形成了6nm、8nm的氧化硅膜的镍粒子集合体中,其表面没有凹凸,在粒子全部表面上具有均一的厚度。
然后,将该形成了氧化硅膜的镍粒子集合体加入调整至pH2的硝酸类喷雾原料溶液中,利用镍离子检测器确认了溶解状态,结果发现,氧化硅膜厚为2nm的镍粒子集合体在投入后30分钟后,检测出了镍离子。但是,氧化硅膜厚为6nm及8nm的各个镍粒子集合体即使在投入16小时后,也未检测出镍离子,显示出足够的赋与对酸性溶液的耐溶解性的功能。其结果显示,镍粒子集合体上所形成的氧化硅膜的厚度最好在5nm以上,在进行长时间的合成时,附加在镍粒子表面的耐溶解性物质必须在粒子全部表面形成氧化硅膜。
而且,作为比较例,将未在表面形成氧化物膜的镍粒子集合体加入调整至pH2的硝酸类喷雾原料溶液中,利用镍粒子检测器确认了溶解状态,结果发现,在投入5分钟后产生气泡,溶解出25ppm的镍离子。另外,在投入后经过16小时的状态下,镍粒子集合体完全溶解。
原料料浆的制作作为酸性溶液中的起始原料,分别准确地称量氧化硅凝胶(粒径<5nm)、硼酸、碳酸钡、碳酸锂,使它们按氧化物换算达到28∶21∶43∶8的比例,加入烧杯中,向其中添加水,使氧化物浓度达到4wt%,将各构成元素溶解,得到了喷雾原料溶液A。
然后,称量按照8nm的厚度形成了氧化硅膜的镍粒子集合体,使得以金属镍换算达到1.2vol%的浓度,并在水中进行了30分钟的超声波分散,将其加入喷雾原料溶液A中,按照使整体的浓度以氧化物换算达到2.5wt%的方式进行调整,并进行充分地搅拌,得到了分散有镍粒子集合体的原料料浆B。将该原料料浆B搅拌2小时,测定了溶液中的镍离子浓度,但是未检测出镍离子。
此时,金属镍的浓度1.2vol%是在预想粒径1μm的玻璃粒子的情况下,大约分散了100个粒径30m的镍粒子的浓度。另外,作为原料料浆B的浓度的2.5wt%是在使原料料浆B形成雾状后液滴的粒径为5μm的情况下,得到1μm的玻璃粒子的浓度。
利用喷雾热分解法进行的内包金属玻璃粒子的制作图3表示本发明的内包金属玻璃粒子的制造方法中使用的喷雾热分解装置。该喷雾热分解装置为如上所示的公知的装置。
在利用电加热器将炉体部的温度调整至900℃的辐射热加热方式的直立型喷雾热分解炉中,将所述的原料料浆B利用原料泵以10mL/分的速度、将2kgf/cm2的压力的空气以20L/分的流量分别向双流体喷嘴供给,将制成的液滴导入炉体内,使之发生热分解反应。而且,在内径200mm、长1000mm、加热长度1000mm的炉芯管中,以输送气体流量35L/min、雾化量100mL/h进行,在滞留时间8.6秒内使之发生热分解反应。此时的喷雾气氛为空气。而且,这里,未进行退火等热处理。利用该热分解反应制作的内包金属玻璃粒子集合体被气流导入具有袋式滤器的产品收集器的回收部中而被回收。
(实施例2~4)使用实施例1中所示的内包金属的制作方法及顺序,在将制作气氛压力调整至1.13kPa的反应器内,使镍锭蒸发,得到了比表面积直径15nm的镍粒子集合体。在该镍粒子集合体上,使用实施例1中所示的氧化物涂覆法,得到了在镍粒子表面形成了8nm的氧化硅膜的镍粒子集合体。
称量形成了该氧化硅膜的镍粒子集合体,使之以金属镍换算在实施例1中所示的喷雾原料溶液A中达到1.2、2.4、3.6vol%的浓度,将其在水中超声波分散30分钟后,加入喷雾原料溶液A中,按照使整体的浓度以氧化物换算达到2.5wt%的方式进行调整,进行充分的搅拌,得到了使金属镍粒子集合体分散而成的原料料浆。
对该含有金属镍粒子的原料料浆在与实施例1相同的条件下进行喷雾热分解,得到了实施例2~4的内包金属玻璃粒子。
(比较例1)为了与内包金属玻璃粒子的特性进行比较,按照与所述相同的条件、顺序制作了使用不含镍的喷雾原料溶液A的玻璃粒子集合体。
使用X射线衍射(XRD)对实施例1中制作的内包金属玻璃粒子集合体及比较例1的玻璃粒子集合体的晶形进行了测定,结果发现,在内包金属玻璃粒子集合体中,如图4所示,观察到了因金属镍产生的峰,还有图5所示的不含镍的玻璃粒子集合体中看到的20°~40°附近的宽峰,说明内包的镍以金属状态存在,而玻璃成分形成玻璃粒子。
另外,根据图6所示的改变了金属镍浓度的实施例2~4中制作的内包金属玻璃粒子集合体的XRD图,随着原料料浆中的金属镍浓度逐渐变高,XRD图上的因金属镍而产生的峰也逐渐变大,说明可以利用混合在原料料浆中的金属粒子的量来控制内包金属玻璃粒子集合体中的金属量。而且,图6中,也同时显示有比较例1。
表1中表示实施例1~4及比较例1的各特性的一览情况。
表1
另外,利用差热分析天平(TG-DTA)对实施例1及比较例1中制作的玻璃粒子集合体的玻璃特性进行了评价。其结果分别如图7及图8所示,对于两试样,都在相同温度下确认了伴随玻璃态化、玻璃化、熔化而产生的峰,即使内包镍,也显示出与不含有镍的玻璃粒子集合体同等的特性。
另外,从所述表1可以发现,改变原料料浆中的金属镍浓度而制作的内包金属玻璃粒子集合体与比较例1的玻璃粒子集合体具有同等的玻璃特性,即使增大原料料浆中的金属镍浓度,在玻璃粒子集合体中也未显示出明显的影响。这样就说明,可以利用原料料浆的玻璃组成对作为按照本发明的方法制作的玻璃粒子的效果之一的玻璃粒子的特性进行控制。
利用扫描型电子显微镜,对实施例1、比较例1及实施例2的玻璃粒子进行了观察。将其结果分别表示在图9、图10、图11中。而且,在各图中,(a)表示二次电子图像,(b)表示反射电子图像的SEM照片。
利用该扫描型电子显微镜对粒子形状和平均粒径进行评价的结果为,如图9所示,内包了镍的玻璃粒子具有与图10所示的未内包的玻璃粒子相同的球状外形。另外,其平均粒径为,内包金属玻璃粒子为0.48μm,未内包的玻璃粒子为0.44μm,二者处于同等水平。另外,作为内包金属的镍的平均粒径为15nm。
另外,从表1可以看到,改变原料料浆中的金属镍浓度而制作的内包金属玻璃粒子的粒径与比较例1的玻璃粒子为同等大小,即使增大原料料浆中的金属镍的浓度,对于玻璃粒子的粒径也未显示出明显的影响,说明可以利用原料料浆的玻璃成分浓度对作为按照本发明的方法制作的玻璃粒子的效果之一的玻璃粒子的粒径进行控制。
另外,在用扫描型电子显微镜的观察中,当对图9及图10进行比较时,如图10所示,未内包镍的样品在2次电子图像和反射电子图像中未看到明显的反差,而与此相反,如图9所示,实施例1中制作的内包镍的玻璃粒子在反射电子图像中可以观察到表示金属的存在的明显的反差,说明在玻璃粒子内镍以金属状态存在。
另外,如图11所示,根据以相同浓度在原料溶液A中混合了比实施例1粒径更小的镍粒子而得到的实施例2的状态下制作的试样的2次电子图像,与图9相比,表示金属的存在的明显的反差的大小较小,表明内包粒径较小的镍粒子,说明可以利用原料料浆中混合的镍粒子的粒径,对作为按照本发明的方法制作的玻璃粒子的效果之一的内包于玻璃粒子中的镍的粒径进行控制。
使用透射型电子显微镜(TEM)和能量分散型X射线微分析仪(EDX),对内包金属玻璃粒子集合体的粒子内的组成进行了评价。图12表示实施例3的条件下制作的试样的TEM图像和EDX的测定点。另外,图13表示全部观察视野的EDX图。
如图13所示,在所观察的内包金属玻璃粒子集合体中,检测出由作为玻璃的主要构成元素的硅、钡产生的峰和作为内包金属的镍的峰,说明玻璃粒子中含有金属成分。另外,图13中的铜的峰是TEM观察网的峰。
图14和图15分别表示在测定点1及测定点2的各位置处,对该内包金属玻璃粒子的粒子内部的详细组成分析的结果。在测定点1,如图14所示,可以确认含有镍和作为玻璃粒子的主要成分的硅和钡的峰,在测定点2,如图15所示,可以确认不含有镍,而有作为玻璃粒子的主要成分的硅和钡的峰。根据该结果,所制作的内包金属玻璃粒子在一个粒子内,玻璃以与金属镍分离的状态存在于粒子内。即,说明是金属镍被内包于玻璃粒子内的玻璃粒子。
本发明作为电子部件的制造等中使用的玻璃材料是十分有用的。
本发明提供一种玻璃粒子的制造方法,包括用氧化物膜覆盖被内包的金属粒子的表面的工序、在含有所述玻璃的构成元素的原料溶液中混合由氧化物膜覆盖了表面的所述金属粒子而制作原料料浆的工序、将所述原料料浆形成液滴而导入高温的炉体内部进行热分解的工序。利用本发明可以取消将玻璃粉末和金属粉末等混合而使用的用途中的混合工序,可以获得预先在玻璃粒子中内包了金属粒子的玻璃粒子。
玻璃粒子、玻璃粒子集合体及玻璃粒子的制造方法
- 专利详情
- 全文pdf
- 权力要求
- 说明书
- 法律状态
查看更多专利详情
下载专利文献
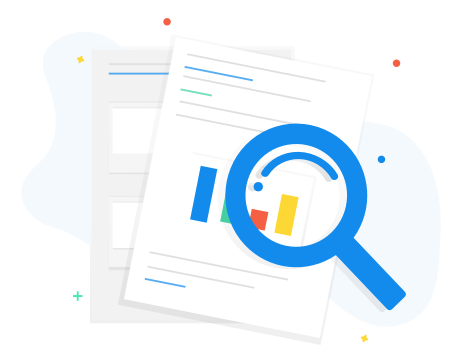
下载专利
同类推荐
-
G.克拉夫特岸本正一高伯菘, 王坤池王坤池, 王清华王坤池, 王清华方晨航
您可能感兴趣的专利
-
苅谷浩幸, 前田伸广苅谷浩幸, 前田伸广苅谷浩幸, 前田伸广吕文慧, 尹计深吕文慧, 尹计深肖湘东张艺龄
专利相关信息
-
丁体英李延祚赵修建, 李新菊赵修建, 李新菊李坤泉