专利名称:分体式导丝槽辊的制作方法目前,在高性能纤维(如碳纤维、芳纶纤维等)生产过程中,必须将几 十甚至上百根丝束在较长的辊体上均匀铺开,使丝束之间的间距基本相等。 在现有技术中,通常采用整体式槽辊,即在辊体上车制很多凹槽,每根丝束 放置于凹槽中。凹槽侧面及底面电镀铬,然后再抛光处理。 一般纤维制造工 艺上要求凹槽底径尺寸公差高于6级,表面粗糙度Ra值不大于0.2,因此, 这样的槽辊存在以下缺点 一是由于凹槽数量很多,磨削凹槽底部直径时需 反复进刀,其尺寸很难保证一致,尺寸精度低于7级,导致丝束的线速度不 等,使丝的条干不匀率上升,对于伸长率很小的丝束则极易拉断;二是凹槽 侧面和底面之间存在过渡圆角,该圆角在纤维制造工艺上要求越小越好,而 在机械制造和电镀处理工艺上要求越大越好。三是凹槽侧面及底面的粗糙度 和镀层厚度达不到工艺要求。四是槽辊的制造成本很高。 发明内容本实用新型提供一种分体式导丝槽辊,该槽辊凹槽底部直径尺寸精度可 达到5级,凹槽侧面和底面之间没有圆角,凹槽侧面及底面的粗糙度Ra值小 于O.l,镀层厚度均匀,槽辊的制造成本较低。本实用新型是这样实现的分体式槽辊由辊体和多个挡圈及紧定螺钉组成。 挡圈安装在辊体上,间距相等,两挡圈之间辊体外圆构成凹槽的底面,挡圈 的侧面构成凹槽的侧面。紧定螺钉将挡圈固定在辊体上,使挡圈随辊体一起 旋转。在每个挡圈和辊体的结合面处,辊体上都设有一直径略小于凹槽底径的台阶,防止挡圈轴向移动。由于凹槽是由两个零件组装后形成的,因此凹 槽侧面和底面之间没有圆角,而单独加工这两个零件的难度比车制凹槽的难 度又小得多。新型槽辊辊体的外圆采用普通车床车制,经磨床磨削后直径尺 寸精度可达到5级,磨削时只需一次进刀,而整体式凹槽必须采用专用砂 轮,反复进刀,且砂轮无法磨削凹槽根部的圆角。电镀时,新型槽辊的两个 零件只需要采用普通的电镀工艺既可达到镀层均匀,而整体式槽辊的凹槽部 分必需制作专用电镀工装。当凹槽圆角小于0.7mm时,专用电镀工装都无法 保证圆角处的镀层厚度均匀,而纤维制造工艺却要求圆角必须小于0. 5mm。抛 光时,新型槽辊的两个零件可采用超生波抛光、研磨等方法,因此其表面粗 糙度可以达到0. 1以上;而整体式槽辊因零件结构原因无法使用这些方法, 只能采用砂带抛光。本实用新型具有凹槽底部直径尺寸精度高,凹槽侧面和底面之间没 有过渡圆角,凹槽侧面及底面的粗糙度Ra值小,镀层厚度均匀,槽辊的制造 成本较低的优点。下面结合本实用新型的附图及实施例来进一步说明。 图1是本实用新型的纵剖面构造图。 图中1.辊体,2.挡圈,3.紧定螺钉。如图1所示,本实用新型由辊体(1)和挡圈(2)及紧定螺钉(3)组成。辊 体(l)由无缝钢管车成后精磨,再表面电镀铬,镀层厚度0. 05 0. 08ran,镀后 采用超声波抛光。辊体(1)直径为》60 mm <i)400 mrn。挡圈(2)安装在辊体(l) 上,间距约为3 30 mm,厚度5 20 mm,高度3 10 mm。挡圈(2)由无 缝钢管车成后精磨两端面,再表面电镀铬,镀层厚度0. 05 0. 08mm,镀后抛 光,再研磨两端面。辊体(l)和挡圈(2)之间采用松配合,配合间隙应大于 0.3mm,以防安装时擦伤辊体(l)的表面。紧定螺钉(3)将挡圈固定在辊体(1)上,使挡圈(2)随辊体(1)一起旋转。在每个挡圈(2)和辊体(1)的结合面处, 辊体(l)上都设有一直径略小于凹槽底径的台阶,台阶高度一般为lmm。紧定 螺钉(3)的头部卡在该台阶中,防止挡圈(2)轴向移动。组装后,两挡圈(2)之 间辊体(l)外圆形成凹槽的底面,挡圈(2)的侧面形成凹槽的侧面。由于凹槽 是由两个零件组装后形成的,因此凹槽侧面和底面之间没有过渡圆角。以直 径d) 240±0.03 mm、长度850mm的72槽槽辊为例,当槽间距为5mra,挡圈厚 度为5mra,高度为5 mm时,分体式槽辊的制造成本约为整体式槽辊的二分之
分体式导丝槽辊制作方法
- 专利详情
- 全文pdf
- 权力要求
- 说明书
- 法律状态
查看更多专利详情
下载专利文献
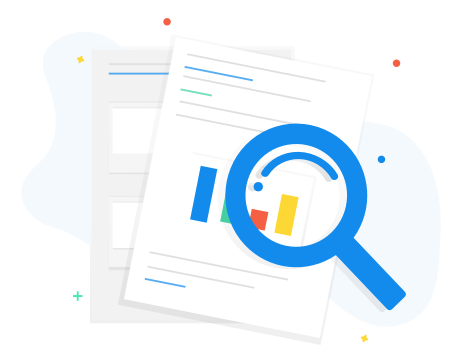
下载专利
同类推荐
-
李平贵李平贵李平贵赵均
您可能感兴趣的专利
-
赵均赵均施玛瑜·M·施瓦特斯曼施玛瑜·M·施瓦特斯曼
专利相关信息
-
田殿志, 井中平刘升, 娄金培刘升, 娄金培李小金, 邝坚李小金, 邝坚李小金, 邝坚