专利名称::一种纺织用复合酶制剂及其应用的制作方法:在传统的棉纺织物前处理工艺中,一般多采用烧碱高温精练法,使用氢氧化钠的强碱溶液,在高温下,甚至有时在超过水沸点的情况下处理退浆后的棉织物,以除去表面的非纤维素成份。在此过程中,必须加以仔细控制,否则棉纤维会形成氧化纤维素而损伤;另外一方面,棉纤维表面因去除了大量起润滑作用的蜡质而失去应有的手感。此外,碱煮练的方法还存在水耗和能耗大,产生大量碱性强、色度深、COD高的废水,以及中和碱形成的盐会对织物的色泽产生影响等问题,这一工艺已不能适应国际上绿色纺织品的发展趋势。生物酶替代烧碱的棉织物酶精练工艺近些年来一直是国内外研究的热点。生物酶处理方法可大大改善棉纺织预处理工艺对产品成本及环境的影响,可节约大量工艺用水、生产时间、能耗、原料及对废水的处理费用,减少对环境排放水中的盐含量及COD等等,同时还提高了产品品质。其中尤为引人瞩目的便是碱性果胶酶。在碱性条件下,作为棉纤维主体的纤维素有润胀的趋向,而果胶酶降解果胶,分散纤维,又可极大限度地防止纤维的降解,同时体系具有天然的抗杂菌污染的能力(因为大多数细菌或酶的最适pH在中性或酸性范围内)。与传统工艺相比,生物法处理后的棉织物更柔软,其原因是处理后的织物表面能保留有一定数量有益的蜡质,而又不影响织物良好的吸水性能。经实验证明,果胶酶与纤维素酶复配对棉织物精练有很好的协同作用,果胶酶使棉纤维中的果胶分解,纤维素酶使纤维素大分子分解,有效地去除棉纤维表面的各类疏水性杂质,提高棉织物的润湿性,能达到传统碱精练棉织物的水平。复合酶适应了棉纤维杂质多样性的特点,利用各种酶对杂质的专一性和协同性可以取得更好的结果;同时,复合酶可以縮短处理时间,就可以使织物达到良好的吸湿性。酶精练不仅能达到碱精练的同样效果,并且具有手感蓬松、柔软、色泽鲜艳、节能、设备简单、工艺流程短、无污水处理等优点。多种酶制剂的复配已成为酶制剂的发展方向。(三)
本发明的目的是提供一种可用于纺织物尤其是棉织物和纱布前处理工艺的高效复合生物酶制剂及其应用,从而改良传统的纺织物精炼处理工艺,提高产品品质,减少环境污染。本发明采用的技术方案是—种复合酶制剂,主要含有终浓度如下的组分聚硅氧烷50100g/L脂肪醇聚氧乙烯醚50100g/L吐温80150g/L司盘80150g/L山梨醇3080g/L氯化钙310g/L苯甲酸钠515g/L碱性果胶酶8001000U/mL纤维素酶10001200U/mL溶剂为水。所述吐温为Tween(2080)系列,包括Tween20、Tween40、Tween60、Tween80等,可为上述之一或其中两种以上的混合;司盘为Span(2080)系列,包括Span20、Span40、Span60、Span80等,可为上述之一或其中两种以上的混合。上述组分为所述复合酶制剂的有效成分,不包括其中可能含有的少量杂质。本发明还涉及一种所述的复合酶制剂的制备方法,所述方法包括以饲料类芽孢杆菌(Paenibacilluspabuli)CCTCCNo:M207183为出发菌株,在适用于饲料类芽孢杆菌的液体发酵培养基中进行发酵培养,获得的发酵液经分离纯化制得液体酶或固体酶,将液体酶或固体酶与助剂溶于水中,配制成有效成分终浓度如下的复合酶制剂聚硅氧烷50100g/L脂肪醇聚氧乙烯醚50100g/LTween208080150g/LSpan208080150g/L山梨醇3080g/L氯化钙310g/L苯甲酸钠515g/L碱性果胶酶8001000U/mL纤维素酶10001200U/mL本申请发明人经自行筛选得到一株饲料类芽孢杆菌(Paenibaci1luspabuli)WZ008,现已保藏于中国典型培养物保藏中心,地址中国武汉武汉大学,430072,保藏编号CCTCCNo:M207183,保藏日期2007年11月22日。通过液体深层发酵可获得高活性的碱性果胶酶和纤维素酶。发酵液经超滤浓縮后可制得液体酶制剂,其中碱性果胶酶活力20002200U/mL,纤维素酶活力25002800U/mL;发酵液经硫酸铵分段盐析及真空冷冻干燥,或直接经喷雾干燥后可制得固体粉剂,其中碱性果胶酶活力50005400U/g,纤维素酶活力52005600U/g。本发明还涉及所述的复合酶制剂在纺织物前处理中的应用。具体的,所述复合酶制剂可用于纺织物尤其是棉织物或纱布的精炼前处理,可代替传统的碱煮练处理工艺。所述复合酶制剂用量以碱性果胶酶计为100250U/g纺织物,处理温度4060°C,处理pH7.011.0,浴比1:101:20,处理时间30150min。本发明的有益效果主要体现在使用本发明复合酶制剂应用于纺织物前处理代替传统碱煮炼,在生产方面,可节约大量的水耗、能耗、原料碱、生产时间,以及对废水的处理费用等,有效降低生产成本,减轻劳动强度;在产品方面,可减少对纺织物纤维的损伤,增加白度和毛效,有利于后续的染色工艺,同时柔软度和悬垂度更好,手感更佳,产品品质得到明显提升;在环境方面,可减少对环境排放水中的盐含量及BOD、COD等,显著降低对环境的污染,是一条符合可持续发展的绿色工艺路线。(四)图1为饲料类芽孢杆菌CCTCCNo:M207183发酵过程中的各项参数图。(五)具体实施例方式下面结合具体实施例对本发明进行进一步描述,但本发明的保护范围并不仅限于此实施例1:以饲料类芽孢杆菌(Paenibacilluspabuli)WZ008作为出发菌株,该菌株是本申请发明人从腐败的苹果表皮中筛选而得,现已保藏于中国典型培养物保藏中心,保藏号为CCTCCNo:M207183。采用液体深层发酵方法生产碱性果胶酶和纤维素酶。其中发酵培养基终浓度组成为果胶6g/L,麸皮4g/L,酵母膏5g/L,蛋白胨1.5g/L,CaC035g/L,(NH4)2S0420g/L,NaCl0.3g/L,KH2P040.5g/L,K2HP042g/L,MgS047H202g/L,FeS040.01g/L,pH8.59.0,溶剂为水。发酵条件为在15L自控式机械搅拌发酵罐中,将制备好的种子液按10%(v/v)的接种量移入9L发酵培养基中,使装液量为10L,控制罐压0.03Mpa,通入空气压力0.12Mpa,空气流速25NL/min,温度30°C,转速300rmp,发酵60h。其间每4h取样分析发酵过程中的各项参数,包括碱性果胶酶活力、生物量(菌体浓度)、总糖浓度和发酵液的pH值结果见图1。实施例2:分别用碱精练工艺与酶精练工艺处理棉布。碱精练工艺流程沸水预处理30min—碱精练一热水洗一冷水洗一烘干(105°C,lh)。其中碱精炼处理条件NaOH40%(o.w.f,NaOH质量占织物质量百分比),肥皂2g/L,温度IO(TC,浴比1:15(棉布与处理液质量比),处理时间150min。酶精练工艺流程沸水预处理30min—酶精练一热水洗一冷水洗一烘干(105°C,lh)。其中酶精炼处理条件复合酶100250U/g织物(以碱性果胶酶计),温度55°C,pH9.6,浴比1:15(棉布与处理液质量比),处理时间150min。其中复合酶配制方法将经喷雾干燥后的生物酶固体粉剂溶于以下体系聚硅氧烷50g/L,脂肪醇聚氧乙烯醚80g/L,Tween-80120g/L,Span-20120g/L,山梨醇50g/L,氯化钙6g/L,苯甲酸钠8g/L,溶剂为水。复配后的酶制剂中碱性果胶酶活力为1000U/mL,纤维素酶活力为1200U/mL。经不同工艺处理后的棉布各参数对比见下表<table>tableseeoriginaldocumentpage6</column></row><table>注"-"代表无,"+"代表有,"+"越多代表程度越高。实施例3:分别用碱精练工艺与酶精练工艺处理棉布。碱精练工艺流程沸水预处理30min—碱精练一热水洗一冷水洗一烘干(105°C,lh)。其中碱精炼处理条件NaOH40%(o.w.f),肥皂2g/L,温度10(TC,浴比l:15,处理时间150min。酶精练工艺流程沸水预处理30min—酶精练一热水洗一冷水洗一烘干(105°C,lh)。其中酶精炼处理条件复合酶100250U/g织物(以碱性果胶酶计),温度55°C,pH9.6,浴比1:15,处理时间150min。其中复合酶配制方法将经喷雾干燥后的生物酶固体粉剂溶于以下体系聚硅氧烷100g/L,脂肪醇聚氧乙烯醚80g/L,Tween-80120g/L,Span-20120g/L,山梨醇50g/L,氯化钙6g/L,苯甲酸钠8g/L,溶剂为水。复配后的酶制剂中碱性果胶酶活力为1000U/mL,纤维素酶活力为1200U/mL。经不同工艺处理后的棉布各参数对比见下表<table>tableseeoriginaldocumentpage7</column></row><table>注"-"代表无,"+"代表有,"+"越多代表程度越高。实施例4:分别用碱精练工艺与酶精练工艺处理棉布。碱精练工艺流程沸水预处理30min—碱精练一热水洗一冷水洗一烘干(105°C,lh)。其中碱精炼处理条件NaOH40%(o.w.f),肥皂2g/L,温度10(TC,浴比l:15,处理时间150min。酶精练工艺流程沸水预处理30min—酶精练一热水洗一冷水洗一烘干(105°C,lh)。其中酶精炼处理条件复合酶100250U/g织物(以碱性果胶酶计),温度55°C,pH9.6,浴比1:15,处理时间150min。其中复合酶配制方法将经喷雾干燥后的生物酶固体粉剂溶于以下体系聚硅氧烷80g/L,脂肪醇聚氧乙烯醚50g/L,Tween-80120g/L,Span-20120g/L,山梨醇50g/L,氯化钙6g/L,苯甲酸钠8g/L,溶剂为水。复配后的酶制剂中碱性果胶酶活力为1000U/mL,纤维素酶活力为1200U/mL。经不同工艺处理后的棉布各参数对比见下表<table>tableseeoriginaldocumentpage8</column></row><table>注"-"代表无,"+"代表有,"+"越多代表程度越高。实施例5:分别用碱精练工艺与酶精练工艺处理棉布。碱精练工艺流程沸水预处理30min—碱精练一热水洗一冷水洗一烘干(105°C,lh)。其中碱精炼处理条件NaOH40%(o.w.f),肥皂2g/L,温度10(TC,浴比l:15,处理时间150min。酶精练工艺流程沸水预处理30min—酶精练一热水洗一冷水洗一烘干(105°C,lh)。其中酶精炼处理条件复合酶100250U/g织物(以碱性果胶酶计),温度55°C,pH9.6,浴比1:15,处理时间150min。其中复合酶配制方法将经喷雾干燥后的生物酶固体粉剂溶于以下体系聚硅氧烷80g/L,脂肪醇聚氧乙烯醚100g/L,Tween-80120g/L,Span-20120g/L,山梨醇50g/L,氯化钙6g/L,苯甲酸钠8g/L,溶剂为水。复配后的酶制剂中碱性果胶酶活力为1000U/mL,纤维素酶活力为1200U/mL。经不同工艺处理后的棉布各参数对比见下表处理工艺酶活(U/g织物)减重率(%)毛效(cm/30min)白度柔软度织物上裂解的不饱和聚半乳糖醛酸量((xmol/g)未处理003.4——0碱精练03.648.1+++4.221002.278.2+++++4.91酶精练1502.398.6++++++5.762002.619.1+++6.852502.75.9.5++++++7.43注"-"代表无,"+"代表有,"+"越多代表程度越高。实施例6:分别用碱精练工艺与酶精练工艺处理棉布。碱精练工艺流程沸水预处理30min—碱精练一热水洗一冷水洗一烘干(105°C,lh)。其中碱精炼处理条件NaOH40%(o.w.f),肥皂2g/L,温度10(TC,浴比l:15,处理时间150min。酶精练工艺流程沸水预处理30min—酶精练一热水洗一冷水洗一烘干(105°C,lh)。其中酶精炼处理条件复合酶100250U/g织物(以碱性果胶酶计),温度55°C,pH9.6,浴比1:15,处理时间150min。其中复合酶配制方法将经喷雾干燥后的生物酶固体粉剂溶于以下体系聚硅氧烷80g/L,脂肪醇聚氧乙烯醚80g/L,Tween-8080g/L,Span-20120g/L,山梨醇50g/L,氯化钙6g/L,苯甲酸钠8g/L,溶剂为水。复配后的酶制剂中碱性果胶酶活力为1000U/mL,纤维素酶活力为l加OU/mL。经不同工艺处理后的棉布各参数对比见下表<table>tableseeoriginaldocumentpage10</column></row><table>注"-"代表无,"+"代表有,"+"越多代表程度越高。实施例7:分别用碱精练工艺与酶精练工艺处理棉布。碱精练工艺流程沸水预处理30min—碱精练一热水洗一冷水洗一烘干(105°C,lh)。其中碱精炼处理条件NaOH40%(o.w.f),肥皂2g/L,温度10(TC,浴比l:15,处理时间150min。酶精练工艺流程沸水预处理30min—酶精练一热水洗一冷水洗一烘干(105°C,lh)。其中酶精炼处理条件复合酶100250U/g织物(以碱性果胶酶计),温度55°C,pH9.6,浴比1:15,处理时间150min。其中复合酶配制方法将经喷雾干燥后的生物酶固体粉剂溶于以下体系聚硅氧烷80g/L,脂肪醇聚氧乙烯醚80g/L,Tween-80150g/L,Span-20120g/L,山梨醇50g/L,氯化钙6g/L,苯甲酸钠8g/L,溶剂为水。复配后的酶制剂中碱性果胶酶活力为1000U/mL,纤维素酶活力为1200U/mL。经不同工艺处理后的棉布各参数对比见下表<table>tableseeoriginaldocumentpage11</column></row><table>注"-"代表无,"+"代表有,"+"越多代表程度越高。实施例8:分别用碱精练工艺与酶精练工艺处理棉布。碱精练工艺流程沸水预处理30min—碱精练一热水洗一冷水洗一烘干(105°C,lh)。其中碱精炼处理条件NaOH40%(o.w.f),肥皂2g/L,温度10(TC,浴比l:15,处理时间150min。酶精练工艺流程沸水预处理30min—酶精练一热水洗一冷水洗一烘干(105°C,lh)。其中酶精炼处理条件复合酶100250U/g织物(以碱性果胶酶计),温度55°C,pH9.6,浴比1:15,处理时间150min。其中复合酶配制方法将经喷雾干燥后的生物酶固体粉剂溶于以下体系聚硅氧烷80g/L,脂肪醇聚氧乙烯醚80g/L,Tween-80120g/L,Span-2080g/L,山梨醇50g/L,氯化钙6g/L,苯甲酸钠8g/L,溶剂为水。复配后的酶制剂中碱性果胶酶活力为1000U/mL,纤维素酶活力为l加OU/mL。经不同工艺处理后的棉布各参数对比见下表<table>tableseeoriginaldocumentpage12</column></row><table>注"-"代表无,"+"代表有,"+"越多代表程度越高。实施例9:分别用碱精练工艺与酶精练工艺处理棉布。碱精练工艺流程沸水预处理30min—碱精练一热水洗一冷水洗一烘干(105°C,lh)。其中碱精炼处理条件NaOH40%(o.w.f),肥皂2g/L,温度100。C,浴比l:15,处理时间150min。酶精练工艺流程沸水预处理30min—酶精练一热水洗一冷水洗一烘干(105°C,lh)。其中酶精炼处理条件复合酶100250U/g织物(以碱性果胶酶计),温度55°C,pH9.6,浴比1:15,处理时间150min。其中复合酶配制方法将经喷雾干燥后的生物酶固体粉剂溶于以下体系聚硅氧烷80g/L,脂肪醇聚氧乙烯醚80g/L,Tween-80120g/L,Span-20150g/L,山梨醇50g/L,氯化钙6g/L,苯甲酸钠8g/L,溶剂为水。复配后的酶制剂中碱性果胶酶活力为1000U/mL,纤维素酶活力为1200U/mL。经不同工艺处理后的棉布各参数对比见下表<table>tableseeoriginaldocumentpage13</column></row><table>注"-"代表无,"+"代表有,"+"越多代表程度越高。权利要求一种纺织用复合酶制剂,主要含有终浓度如下的组分聚硅氧烷50~100g/L脂肪醇聚氧乙烯醚50~100g/L吐温80~150g/L司盘80~150g/L山梨醇30~80氯化钙3~10g/L苯甲酸钠5~15g/L碱性果胶酶800~1000U/mL纤维素酶1000~1200U/mL溶剂为水。2.—种如权利要求l所述的复合酶制剂的生产菌株饲料类芽孢杆菌(Paenibacilluspabuli)WZ008,保藏于中国典型培养物保藏中心,地址中国武汉武汉大学,430072,保藏日期2007年11月22日,保藏编号CCTCCNo:M207183。3.—种如权利要求1所述的复合酶制剂的制备方法,所述方法包括以饲料类芽孢杆菌(Paenibacilluspabuli)CCTCCNo:M206105为出发菌株,在适用于饲料类芽孢杆菌的液体发酵培养基中进行发酵培养,获得的发酵液经分离纯化制得液体酶或固体酶,将液体酶或固体酶与助剂溶于水中,配制成有效成分终浓度如下的复合酶制剂50lOOg/LlOOg/L脂肪醇聚氧乙烯醚^808050Tween208080150g/LSpan208080150g/L山梨醇3080g/L氯化钙3lOg/L苯甲酸钠515g/L碱性果胶酶800lOOOU/mL纤维素酶10001200U/mL溶剂为水。4.如权利要求1所述的复合酶制剂在纺织物前处理中的应用。5.如权利要求4所述的应用,其特征在于所述复合酶制剂用于纺织物的精炼前处理,所述复合酶制剂用量以碱性果胶酶计为100250U/g纺织物,处理温度4060°C,处理pH7.011.0,浴比1:101:20,处理时间30150min。全文摘要本发明提供了一种可用于纺织物尤其是棉织物前处理工艺的高效复合生物酶制剂及其应用,所述复合酶制剂,主要含有终浓度如下的组分聚硅氧烷50~100g/L,脂肪醇聚氧乙烯醚50~100g/L,Tween20~80系列80~150g/L,Span20~80系列80~150g/L,山梨醇30~80g/L,氯化钙3~10g/L,苯甲酸钠5~15g/L,碱性果胶酶800~1000U/mL,纤维素酶1000~1200U/mL,溶剂为水。本发明使用复合酶制剂应用于纺织物前处理代替传统碱煮炼,可有效降低生产成本,减轻劳动强度,使产品品质得到明显提升,另外可减少对环境排放水中的盐含量及BOD、COD等,显著降低对环境的污染,是一条符合可持续发展的绿色工艺路线。文档编号D06M13/224GK101713150SQ20091015454公开日2010年5月26日申请日期2009年11月11日优先权日2009年11月11日发明者应向贤,汪钊,沈雪亮,章银军,鄢洪德,魏春申请人:浙江工业大学
一种纺织用复合酶制剂及其应用制作方法
- 专利详情
- 全文pdf
- 权力要求
- 说明书
- 法律状态
查看更多专利详情
下载专利文献
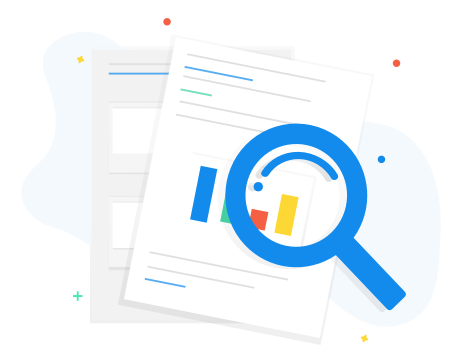
下载专利
同类推荐
-
魏家浩吕志伟吕志伟吕志伟
您可能感兴趣的专利
-
P·莫拉佐尼P·莫拉佐尼李会郎, 李承元芮秀明, 张秉文芮秀明
专利相关信息
-
K·罗杰斯, G·迪泽瑞嘉K·罗杰斯, G·迪泽瑞嘉李贺军