专利名称:由合成树脂整体模制而成的表面紧固件的制作方法 通常,人们使用由合成树脂材料整体模制在板状基体上并可使具有大致相同形状的接合元件通过压力相互接合在一起的模制表面紧固件,是由于模制表面紧固件易于接合,且模制表面紧固件的接合强度较高,因此,模制表面紧固件特别适合于将工业材料和内装饰件等连接在一起。例如,JP2994464A公开的模制表面紧固件包括一个蘑菇状的接合元件,该接合元件具有从板状基体表面上隆起且其截面积从底端到顶端减小的凸起部分和位于该凸起部分顶端并沿水平方向伸出于该顶端周边的接合头部。在具有上述形状的该模制表面紧固件中,在接合时,接合元件与具有相同形状的相配合表面紧固件的接合元件一起工作,使头部部分弹性变形,且接合元件沿水平方向膨胀和收缩。因此,接合元件就可与相配合的表面紧固件的接合元件相接合。另外,US5212853公开的模制表面紧固件具有门形的接合元件,该接合元件包括一对从基体表面凸起的支腿部分和将这些支腿部分的顶端连接在一起并沿垂直于这些支腿部分布置方向的水平方向伸出的接合头部。根据这样一种模制表面紧固件,当接合时,接合元件的头部部分弹性变形,并与具有相同形状的相配合的表面紧固件的接合元件一起工作,且在水平方向上膨胀和收缩,从而使该接合元件与相配合的表面紧固件的接合元件接合在一起。另外,一个柱状凸起在接合头部的顶部或者在基体表面上与相配合的表面紧固件的接合头部相对应的位置上隆起。柱状凸起的高度设定得使该柱状凸起可贴靠在与每个柱状凸起相对的基体表面或接合头部的顶部上。因此,就可避免在垂直于两个接合表面紧固件之间的接合表面的方向发生交错。JP2994464A所公开的模制表面紧固件具有一个蘑菇状的接合元件,该接合元件具有位于凸起部分的顶端并沿水平方向伸出于该顶端周围的接合头部。另外,一个接合元件可在接合头部的所有方向上与相配合的表面紧固件的多个接合元件相接合,从而获得较高的接合率。但是,由于接合元件的凸起部分和接合头部之间的颈部较窄,在接合元件脱离接合状态时,接合头部就相互地被拉向相反方向,从而使其颈部易于断裂。由于反复地进行这种脱离操作,因而使接合力降低,且表面紧固件原来所具有的功能在较短的时间内就会失去。另外,US5212853所公开的模制表面紧固件具有门形接合元件,该接合元件仅在垂直于凸起部分的支腿部分的布置方向的两个水平的相反方向上伸出。因此,当脱离接合时,头部不会象蘑菇状接合元件那样发生断裂,从而保证了凸起部分和接合头部之间的接合力。但是,接合头部仅在伸出的两个相反方向上与相邻的两个接合元件接合,而不是在支腿部分的布置方向上与相配合的表面紧固件接合。因此,如果接合的表面紧固件相互沿接合元件支腿部分的布置方向布置时,接合力就会降低,从而使表面紧固件易于分离。
本发明的目的是为解决上述问题,提供一种模制表面紧固件,该模制表面紧固件在接合的接合元件之间不会产生摆动,并具有较高的接合力,从而极大地避免接合元件脱开。为实现上述发明目的,根据本发明,提供一种合成树脂模制表面紧固件,其中,多个接合元件整体模制在板状基体表面上,并可与具有相同形状的相配合表面紧固件的接合元件接合和脱开。另外,该模制表面紧固件的特征在于接合元件具有凸起部分、接合头部和配合凸起,上述凸起部分从板状基体表面隆起,且一对相反的侧表面形成倾斜表面,上述接合头部连续地形成于所述凸起部分的顶端,并在除倾斜表面以外的其它两个相对的侧表面上沿水平方向伸出,所述配合凸起从板状基体的表面上隆起,当接合元件相互接合在一起时,配合凸起位于相配合的表面紧固件的相邻的一对接合元件的两个相面对的倾斜表面之间,并具有与两个倾斜表面中的至少一个相配合并贴靠在一起的倾斜表面。
在这种模制表面紧固件中,接合元件的接合头部仅在除凸起部分的倾斜表面以外的其它侧表面上沿水平方向伸出。且伸出的侧部边缘在接合头部的伸出的侧部边缘处与相配合的表面紧固件的接合元件的接合头部的侧部边缘相接合。通过使仅在其它侧表面上具有伸出的接合头部的接合元件具有这种结构,就可保证其与US5212853所公开的模制表面紧固件具有相同的足够的接合力。
另外,模制表面紧固件具有配合凸起,在接合元件相互接合时,配合凸起位于相配合的表面紧固件的一对相邻接合元件的两个相面对的倾斜表面之间,配合凸起具有可与接合元件的两个倾斜表面中的至少一个相配合并贴靠在一起的倾斜表面,从而可有效地避免接合的表面紧固件沿水平方向移动,并保持稳定地接合。同时,根据本发明,相配合和贴靠在一起表明接合元件的倾斜表面和配合凸起的倾斜表面相互接触,且这些倾斜表面以很窄的间隙相互贴靠在一起。
另外,根据该模制表面紧固件,最好,配合凸起设置在可与相配合的表面紧固件的一对相邻的接合元件的两个相面对的倾斜表面相配合并贴靠在一起的位置上。这样,如果配合凸起与其它表面紧固件的一对相邻接合元件的两个相面对的倾斜表面相配合并贴靠在一起时,可完全避免在接合的表面紧固件之间发生沿水平方向的位移。
另外,一个接合元件的一对相反的倾斜表面从其底端向前端逐渐相互靠近。这样,如果凸起部分的横截面面积从前端向作为具有基体表面的连接部分的底端逐渐增大,凸起部分的强度就得到增强。另外,即使在接合头部在伸出侧的侧表面相对于基体表面形成于竖直方向的情况下,由于存在相邻的配合凸起,因此,即使在按压紧固件使它们向竖直表面弯曲时,配合凸起也支承着表面紧固件,从而限制了凸起部分弯曲和倒下,并保证了所需的接合率。
另外,同一接合元件的一对相反的倾斜表面从底端向前端相互大致平行地倾斜。在这种接合元件中,最好,相邻的两个接合元件基本上呈V形,且其凸起部分的底端相连。
这样,如果相邻的两个接合元件在其凸起部分的底端相连并具有部分共同的凸起部分时,就可增强凸起部分的强度。另外,相邻的两个接合元件基本上呈V形,当接合时,在按压表面紧固件的压力作用下,其接合头部向相反的方向弯曲,从而使它们相互分开,这样就便于将配合凸起插入到两个接合元件之间。
同时,最好,配合凸起的形状基本上与相配合的表面紧固件的一对相邻接合元件的两个相面对的倾斜表面之间所限定的空间的形状相同。例如,配合凸起的整个横截面形状大致为梯形,或者大致为三角形。
另外,整体模制表面紧固件具有这样的结构,使配合凸起可与接合元件牢固地弹性接触。因此,通过使配合凸起和接合元件的倾斜表面弹性接触,配合凸起就牢固地插入配合在接合元件之间,从而可有效地避免两个接合的表面紧固件之间发生移动。
为使配合凸起和接合元件的倾斜表面之间弹性接触,配合凸起或接合元件可制成中空形状和门形形状,配合凸起可设有一对沿倾斜表面的布置方向具有特定距离的弹性凸起。
另外,配合凸起的凸起高度不超过接合元件的高度。如果配合凸起的凸起高度高于接合元件的高度,接合元件的顶部和相配合的表面紧固件的基体表面之间就会形成间隙。而这种状态是不希望出现的。在此情况下,为避免沿垂直于接合面的方向发生摆动,最好,配合凸起的凸起高度与接合元件的高度相等。
另外,配合凸起设置在相邻的两个接合元件的中间。例如,在接合元件的倾斜表面沿模制方向布置的情况下,配合凸起设置在沿表面紧固件宽度方向相邻的两个接合元件的中间。在此情况下,一个接合元件位于相配合的表面紧固件的沿前后方向和左右方向相邻的四个接合元件之间,并与这四个接合元件相接合。
另外,配合凸起可设置在沿前后方向和左右方向相邻的四个接合元件的中间。在此情况下,一个接合元件位于沿相配合的表面紧固件宽度方向相邻的两个接合元件之间,并在该接合元件的接合头部的两个伸出的侧部边缘处与相配合的表面紧固件的两个接合元件的伸出的侧部边缘相接合。
图1是本发明第一实施例的模制表面紧固件的布置图。
图2是图1所示模制表面紧固件的侧视图。
图3是图1所示模制表面紧固件的正视图。
图4是模制表面紧固件和与其相配合的模制表面紧固件处于相互接合状态的侧视图。
图5是模制表面紧固件和与其相配合的模制表面紧固件处于相互接合状态的正视图。
图6是用于说明模制表面紧固件和与其相配合的模制表面紧固件处于相互接合状态的图4沿VI-VI的截面图。
图7是模制表面紧固件和与其相配合的本发明第一实施例的一种改进形式的模制表面紧固件处于相互接合状态的侧视图。
图8是用于说明模制表面紧固件和与其相配合的图7所示模制表面紧固件处于相互接合状态的图7沿VIII-VIII的截面图。
图9是本发明第二实施例的模制表面紧固件的侧视图。
图10是图9所示模制表面紧固件处于接合状态的侧视图。
图11是配合凸起的一种改进形式的侧视图。
图12是接合元件的一种改进形式的侧视图。
图13是本发明第三实施例的模制表面紧固件的侧视图。
图14是图13所示模制表面紧固件的侧视图。
图15是模制表面紧固件和与其相配合的模制表面紧固件处于接合状态的示意图。
图16是本发明第四实施例的模制表面紧固件的布置图。
图17是图16所示模制表面紧固件的侧视图。
图18是模制表面紧固件和与其相配合的模制表面紧固件处于接合状态的侧视图。
图19是用于说明图18所示接合状态的图18沿XIX-XIX的截面图。
图20是本发明第四实施例的一种改进的模制表面紧固件的布置图。
图21是用于制造上述模制表面紧固件的制造设备的结构示意图。
图22是图21所示制造设备的模制部分的示意图。
图23是由本发明第一实施例的模制表面紧固件材料构成的一维形式的一维紧固件元件的顶视图和侧视图。
图24是由制造设备的加热和加压装置来加工接合头部的示意图。
下面将结合附图对本发明的典型实施例进行描述。图1是本发明第一实施例的模制表面紧固件的布置图。图2是模制表面紧固件的侧视图,图3是模制表面紧固件的正视图。另外,图4是模制表面紧固件和与其相配合的模制表面紧固件处于相互接合状态的侧视图。图5是模制表面紧固件和与其相配合的模制表面紧固件处于相互接合状态的正视图。图6是用于说明模制表面紧固件接合状态的图4沿VI-VI的截面图。
在这些图中,标号1表示模制表面紧固件。该模制表面紧固件由热塑性合成树脂材料制成。作为热塑性合成树脂材料,可单独使用聚酰胺树脂、聚酯类树脂、聚丙烯树脂、聚乙烯树脂、聚苯乙烯树脂和聚氨基甲酸酯树脂或使用其结合物。另外,为保证可简便地进行模制,最好本发明的模制表面紧固件1具有合理的形状。
模制表面紧固件1完全由同种合成树脂材料组成。在该模制表面紧固件1中,多个接合元件3在板状基体2的表面上隆起,接合元件3沿模制方向两排一块地进行布置,且每块沿紧固件的宽度方向具有均匀的间隔。另外,同一块的排间距小于各个块之间的距离。
另外,相邻的接合元件3沿模制方向以均匀间隔布置。而且,配合凸起4分别在相同块的两排相邻接合元件3的中间和相邻接合元件3的两块中间设置在基体2的相同表面上。
如图1-3所示,该实施例的各个接合元件3的构造是具有从板状基体2表面凸起的凸起部分3a和连续地形成于凸起部分3a顶端的接合头部3b。凸起部分3a呈矩形形状,其水平横截面在模制方向较长,沿模制方向的一对相对表面包括倾斜表面3c、3c,这些倾斜表面3c、3c从其底端向其顶端倾斜而相互靠近。
除了倾斜表面3c、3c以外的其它的两个相对侧表面3d、3d是垂直于板状基体2的表面的竖直表面3d、3d。具有这些倾斜表面3c、3c和竖直表面3d、3d的凸起部分3a具有一个整体形状大致为梯形的竖直部分。
接合头部3b仅在竖直表面3d、3d的侧面沿水平方向伸出,并几乎在倾斜表面3c、3c的侧面不伸出。
另外,根据该实施例,配合凸起4沿宽度方向布置在相邻接合元件3的中间并从基体2的表面凸起。配合凸起4具有一对沿模制方向相对的倾斜表面4a、4a,其整体形状基本上呈梯形。另外,倾斜表面4a与接合元件3的倾斜表面3c具有相同的倾斜角,其形状可使其插入并配合在沿模制方向相互配合的相邻表面紧固件的接合元件3之间所形成的倒置梯形空间中。
根据该实施例,配合凸起4的凸起高度h大致是接合元件3的凸起高度H的0.6倍。另外,该配合凸起4的凸起高度h可设定为任意的高度,只要其不超过接合元件3的凸起高度H即可。另外,为了在表面紧固件相互接合时避免沿垂直于基体2表面的方向交错排列,最好,配合凸起4的凸起高度H大致与接合元件3的凸起高度H相等。
其次,下面将结合附图4-6对具有上述结构的本发明第一实施例的模制表面紧固件的压缩和连接状态进行描述。
当两个模制表面紧固件1重合并从基体2的后表面对其进行按压时,相对的两个模制表面紧固件1的接合元件3就相互插接在一起,并使接合头部3b沿纵向(模制方向)和各相互配合的表面紧固件的宽度方向弹性变形,也就是,插入到在前后方向和左右方向相邻的四个接合元件3的中间位置。根据该实施例,当发生弹性变形时,由于接合元件3是如上所述的两排一块地进行布置,而且每块之间的距离大于同一块中排与排之间的间距,因此,接合元件3和配合凸起4之间的距离在靠近接合元件3宽度方向的一侧较大。因此,接合元件3可充分地弹性变形,从而顺滑地插入到相互配合的表面紧固件的接合元件3中。
然后,在表面紧固件的接合元件3越过与其相配合的表面紧固件的接合元件3之后,它们就弹性地恢复到其原始状态。如图4和5所示,各个接合头部3b的顶表面在此状态下牢牢地与相配合的表面紧固件的基体2的表面相接触。另外,即使沿使两者相互分离的方向拉动接合的模制表面紧固件1,各个接合头部3b的倾斜部分也与相配合的表面紧固件的在前后方向和左右方向相邻的四个接合元件3相接合在一起。因此,表面紧固件1不会轻易分离,从而可获得所需的接合力。
在表面紧固件1处于接合状态时,配合凸起4位于沿模制方向相邻的相配合表面紧固件的一对接合元件3、3的两个相面对的倾斜表面3c、3c之间。而且,同一配合凸起4的两个倾斜表面4a、4a与相邻的这对接合元件3、3的两个相面对的倾斜表面3c、3c相配合并贴靠在一起。
因此,在这种接合的表面紧固件1中,配合凸起4与一对在模制方向相邻的接合元件3、3相配合,一个配合凸起4的倾斜表面4a、4a与一对接合元件3、3的两个相面对的倾斜表面3c、3c相配合并相互贴靠在一起,因此,接合的表面紧固件1不会在水平方向摆动,并保持稳定的接合状态。
另外,接合元件3的凸起部分3a整体上基本呈梯形形状。特别是,该凸起部分3a不易向其倾斜表面3c的侧面倾斜。另外,配合凸起4在垂直于模制方向的表面紧固件的宽度方向上毗邻设置,因此,沿宽度方向的倾斜受到限制,从而可保证其处于稳定的接合状态。
同时,根据该实施例,如图1所示,多个接合元件3两排一组地布置成一块,且每块之间具有均匀的间距。而且,排与排之间的距离也可布置成均匀一致的。
另外,根据该实施例,所有的配合凸起4都与一对在相配合的表面紧固件的模制方向相邻的接合元件3、3的两个相面对的倾斜表面3c、3c相配合并相互贴靠在一起,且该相配合的表面紧固件在模制方向上,其每个接合元件3都具有均匀的间距。但也可使在模制方向上每个接合元件3的间距不一致。在此情况下,如图7和8所示,在大间距部分形成的配合凸起5中,其一侧的倾斜表面5a仅与位于同一侧的接合元件3的倾斜表面3c相配合并相互贴靠在一起。另外,位于大间距部分的接合元件3也仅在模制方向同一侧的两个倾斜部分处与相配合的表面紧固件的接合元件3相接合,因此,与上述实施例相比,接合力和分离阻力都变小了。在此情况下,如果调整接合元件3沿模制方向的间距,就可将表面紧固件的接合力和分离阻力调整到所需的数值。
另外,根据上述实施例,配合凸起4具有整体上大致为梯形的竖直截面。但该竖直截面也可以是大致为三角形的形状。
图9和10示出了本发明第二实施例的模制表面紧固件11。图9是该模制表面紧固件11的侧视图,图10是模制表面紧固件11处于接合状态时的侧视图。另外,根据该第二实施例,接合元件3的形状及其布置方式与第一实施例的相同,因此,这里就不再详细进行描述了。
该实施例的模制表面紧固件11的结构特征在于其具有配合凸起6。与第一实施例一样,该实施例的配合凸起6也设置在沿宽度方向相邻的两个接合元件3的中间位置上。该配合凸起6包括一对在模制方向上以特定间距凸出的弹性凸起6a、6a,这两个弹性凸起6a、6a在模制方向上的外表面是与接合元件3的倾斜表面3c基本上具有相同倾角的倾斜表面6b。
另外,弹性凸起6a、6a的外表面(倾斜表面6b、6b)之间的距离与位于其底端部沿模制方向相邻的接合元件3、3的接合头部3b、3b之间的间隙基本上相等。另外,弹性凸起6a、6a的外表面之间的距离略大于位于前端部的接合元件3、3的相应配合位置的距离。因此,如图10所示,当表面紧固件11、11接合在一起时,弹性凸起6a、6a的倾斜表面6b、6b就与一对相邻的接合元件3、3的两个相面对的倾斜表面3c、3c弹性地接触。
因此,在配合凸起6中,其倾斜表面6b、6b与一对接合元件3、3的两个相面对的倾斜表面3c、3c牢牢地弹性接触,从而可更有效地避免表面紧固件11、11接合时在水平方向产生摆动。
同时,根据本发明,以特定间距布置的一对弹性凸起6a、6a可用作配合凸起6,因此,使配合凸起6与接合元件3牢牢地弹性接触。但是,该实施例并不局限于这种结构。例如,图11所示的配合凸起7,这种门形结构的配合凸起7包括一对沿模制方向布置的支腿部分7a、7a和一个与这些支腿部分7a、7a的顶端相连接的连接部分7b,这样,配合凸起7就可与接合元件3牢固地弹性接触。另外,也可采用内部是中空的且侧表面形状基本上是梯形或三角形的配合凸起结构。
另外,为了使配合凸起与接合元件弹性地接触,如图12所示,接合元件8的凸起部分包括一对支腿部分8a、8a和一个将支腿部分8a、8a的顶端连接在一起的连接部分8b。而且,也可采用连接部分8b的顶表面是接合头部8c的门形结构的接合元件。而且在这种门形接合元件8的情况下,支腿部分8a、8a在模制方向上的外表面是倾斜表面8d、8d,且接合头部8c在倾斜表面8d、8d之外的两个侧表面处伸出。另外,也可采用凸起部分是中空的接合元件结构。
图13-15示出了本发明第三实施例的模制表面紧固件12。图13是该模制表面紧固件12的布置示意图,图14是该模制表面紧固件12的侧视图,而图15是模制表面紧固件12处于接合状态的示意图。同时,第三实施例的模制表面紧固件12的特征在于其接合元件3和配合凸起4的布置位置,而接合元件3和配合凸起4的结构与第一实施例的相同,这里就不再详细进行描述了。
根据本发明第三实施例的模制表面紧固件12,其与第一和第二实施例相同,接合元件3以两排为一块地进行布置,每块之间的间距均匀一致。另外,在模制方向上,接合元件3以均匀的间距进行布置。且从基体2的相同表面凸出的配合凸起4设置在沿前后方向和左右方向相邻的四个接合元件3的中间。
按照这种结构的模制表面紧固件12,如图15所示,当表面紧固件与具有相同形状的相配合的表面紧固件12接合在一起时,接合元件3就插入到在相配合的表面紧固件宽度方向上相邻的两个接合元件3的中间位置处,并使接合头部3b弹性地变形。如果接合元件3的接合头部越过相配合的表面紧固件的接合元件3的接合头部3b时,它们就可弹性地恢复到其原始形状。另外,各个接合头部3b的两个伸出的边缘与相配合的表面紧固件的两个接合元件3的各接合头部3b的伸出边缘相接合。
在此情况下,配合凸起4沿模制方向位于相配合的表面紧固件的一对接合元件3、3的两个相面对的倾斜表面3c、3c之间。另外,一个配合凸起4的两个倾斜表面4a、4a与一对相邻的接合元件3、3的两个相面对的倾斜表面3c、3c相配合并相互贴靠在一起。
因此,在相接合的表面紧固件12中,配合凸起4与在模制方向相邻的接合元件3相配合,且配合凸起4的倾斜表面4a与接合元件3的倾斜表面3c相配合并相互贴靠在一起,因此,接合在一起的表面紧固件12在水平方向不会彼此产生摆动,并可保持稳定的接合状态。
图16-19示出了本发明第四实施例的模制表面紧固件13。图16是该模制表面紧固件13的布置示意图,图17是该模制表面紧固件13的侧视图,图18是该模制表面紧固件13与相配合的模制表面紧固件处于接合状态的侧视图,图19是图18沿XIX-XIX的截面图,用于解释该接合状态。
在第四实施例的模制表面紧固件13中,多个接合元件9和多个配合凸起10从基体2的表面上凸起。如图16和17所示,接合元件9包括从板状基体2的表面上隆起的凸起部分9a和连续地形成于该凸起部分9a顶端上的接合头部9b。
在凸起部分9a中,沿模制方向位于相反侧的一对侧面形成倾斜表面9c、9c,这些倾斜表面9c从其底端到顶端相互平行地倾斜。另外,在沿模制方向相邻的两个接合元件9、9中,彼此的凸起部分9a、9a的底端部分地连接在一起,彼此的倾斜表面9c、9c在与模制方向相反的方向倾斜。这两个相对的倾斜表面9c、9c基本上形成V形形状。另外,接合头部9b仅在除了一对倾斜表面9c、9c以外的相对的两个竖直表面9d、9d侧沿大致水平的方向伸出。
配合凸起10位于沿宽度方向相邻的接合元件9、9的中间,配合凸起10具有一对沿模制方向相反的倾斜表面10a、10a,且配合凸起10整体上基本呈三角形形状。另外,倾斜表面10a与接合元件9的倾斜表面9c具有相同的倾角,且配合凸起10的高度h基本上与从沿模制方向相邻的两个接合元件9的V形分叉部到接合头部9b的高度相等。换句话说,配合凸起10的形状可与具有共同底端的两个相邻接合元件9之间所形成的倒三角空间相匹配。
如果具有这种结构的两个第四实施例的模制表面紧固件13相互接合在一起,如图18和19所示,各接合元件9就插入到在相配合的表面紧固件的前后方向和左右方向相邻的四个接合元件9的中间位置处,并使接合头部9b弹性地变形。如果一个表面紧固件的接合元件9的接合头部9b越过相配合的表面紧固件的接合元件9的接合头部9b,其就可弹性地恢复到其原始形状。另外,各个接合头部9b的四个倾斜部分与相配合的表面紧固件的四个接合元件9的各接合头部9b的倾斜部分相接合在一起。
配合凸起10插入到沿相配合的表面紧固件的模制方向相邻的并具有共同底端的一对接合元件9、9之间。在此情况下,如上所述,由于具有共同底端的一对接合元件9、9大致呈V形,因此,在接合时,按压表面紧固件易于使接合头部9b、9b沿使其相互分离的方向弯曲,从而使配合凸起10、10方便地插入到两个接合元件9、9之间。
插入到接合元件9、9之间的配合凸起10位于接合元件9、9的两个面对的倾斜表面9c、9c之间,且同一配合凸起10的两个倾斜表面10a、10a与一对相邻的接合元件9、9的两个面对的倾斜表面9c、9c相配合并相互贴靠在一起。另外,根据该实施例,沿模制方向布置的配合凸起10、10交替地与相配合的表面紧固件的接合元件9、9的倾斜表面9c、9c相配合,并与两个倾斜表面9c、9c相配合并相互贴靠在一起。
在按这种方式相接合的表面紧固件13中,配合凸起10装配在沿制模方向相邻的接合元件9、9的倾斜表面9c、9c之间,且配合凸起10的倾斜表面10a、10a与接合元件9、9的两个倾斜表面9c、9c相配合并相互贴靠在一起,从而使接合的表面紧固件13不会彼此在水平方向上产生摆动,并保持稳定的接合状态。
另外,在具有上述结构的接合元件9和配合凸起10中,如图20所示,可采用将配合凸起10形成在沿前后方向和左右方向相邻的四个接合元件9的中间位置的结构。在这种结构的情况下,处于接合状态的接合元件9位于沿宽度方向相邻的相配合表面紧固件的两个接合元件之间。另外,在同一接合元件9中,接合头部9b的两个侧边缘与沿相配合的表面紧固件的宽度方向相邻的两个接合元件9的侧边缘相接合。
下面将描述一种制造上述模制表面紧固件的方法。在以下的描述中,以制造第一实施例的模制表面紧固件的方法为例进行描述,但是,第二到第四实施例的模制表面紧固件也可按同样的方法来制造。
图21是用于连续地模压模制表面紧固件1的制造设备的结构示意图,图22是模压部分的放大图。
在这些图中,标号21表示挤出喷嘴,该喷嘴21的前端弯曲表面具有与后面将描述的模具轮22大致相同曲率的弧形面21a。另外,该挤出喷嘴21具有与所要模制于模具轮22的弯曲表面上的板状基体2的壁厚相适应的间隙。熔融树脂以特定的树脂压力和特定的树脂量从该挤出喷嘴21的前端弧形面21a中部形成的树脂挤出口21b以板状形式连续地挤出。根据该实施例,挤出喷嘴21在其中部具有一个熔融树脂通道21c。
模具轮22呈中空滚筒状,并具有水冷套来作为其内部冷却装置。另外,其周边表面可起模制表面紧固件1的部分模制表面的作用。如上所述,挤出喷嘴21的前端弧形面21a具有间隙,而且,模具轮22的轴线平行于挤出口21b。
根据该实施例,在模具轮22的周边表面上,按照上述模制表面紧固件的布置方式形成用于模压接合元件的多个腔和用于模压配合凸起的多个腔。具有这种结构的模具轮22通过一个已知的驱动装置(未示出)沿图21箭头所示方向转动。
用于模压配合凸起的腔的内部形状与配合凸起4的外部形状基本相同。另外,如图23(a)所示,其顶表面的内部形状与元件3’的外部形状基本相同,也就是,沿模压方向较长的矩形形状。另外,用于模压接合元件的腔22b具有图23所示的元件3’的外部形状,也就是,如图23(b)所示,其侧部形状是这样的,可使其矩形部分3b’在梯形部分3a’的顶表面上凸起。
另外,根据该实施例,冷却水箱23设置在模具轮22的下方,模具轮22的下半部基本上浸在冷却水箱23之内。在该冷却水箱23前部的向上方向和倾斜方向上设置一个卷取辊24。同时,该卷取辊24的前方设有一对上辊和下辊25a、25b,如图24所示,上辊和下辊构成加热和加压装置25。
上辊25a在其内部具有加热源(未示出),其表面温度设定为可使树脂材料软化的温度。另外,如放大的图24所示,上辊25a的周边表面的下端略低于所运载的一维紧固件的元件3’的项部所处的平面,并将其设定为模制接合元件3的接合头部3b的高度。另外,位于上辊25a下方并与上辊相面对的下辊25b的顶表面设置得使其位于移动的一维紧固件的板状基体的下表面所处的平面上。
为了利用上述结构的模制表面紧固件制造设备制造出本发明的表面紧固件1,以特定树脂压力从挤出喷嘴21连续挤出的熔融树脂连续地进入与转动模具轮22所形成的间隙内,部分熔融树脂充满间隙以模制板状基体2。同时,部分熔融树脂连续地充入到形成于模具轮22的周边表面上的用于模制接合元件的腔22a和用于模制配合凸起的腔中,从而连续地模制出一维模制表面紧固件1’,并随着模具轮22的转动,多个元件3’和多个配合凸起4就整体地模制在基体2的表面上。
位于模具轮22周边表面上的包括本发明表面紧固件1原料的一维形状的一维模制表面紧固件1’围绕模具轮22的半个周边表面通过。在此过程中,一维模制表面紧固件1’由模具轮22内部的冷却水套冷却,同时,一维模制表面紧固件1’从低温冷却水循环流动的冷却水箱23内通过并快速地冷却,从而使一维模制表面紧固件1’易于固化。
完全固化的基体2由卷取辊24卷取。模制的一维表面紧固件1’在作为加热和加压装置25的上辊和下辊25a、25b之间通过。如图24所示,当其在上辊和下辊25a、25b之间通过时,上加热辊25a对元件3’的梯形部分3a’的顶表面上凸起的矩形部分3b’的顶部进行加热和加压,从而使矩形部分3b’软化时从其顶部发生变形,且其顶表面基本上变成平面。同时,形成沿模制表面紧固件的宽度方向增大的接合头部3b,由此而获得本发明的接合元件3的形状。
在解除了不采用特定冷却装置的常温冷却之后,卷取经上辊和下辊25a、25b输送的本发明模制表面紧固件1,并完成整个制造过程。
根据上述利用所述制造设备的制造方法,就可连续地制造出本发明的模制表面紧固件。当然,本发明的模制表面紧固件也可利用上述设备以外的其它适当设备来连续地进行制造,或者,利用普通喷射模设备来成批地进行模制。
本发明提供一种由合成树脂整体模制而成的表面紧固件,其具有位于板状基体的表面上的接合元件和配合凸起。接合元件具有凸起部分和接合头部,凸起部分从板状基体的表面上隆起,并具有一对相反的倾斜表面,接合头部连续地形成于凸起部分的顶端,并在除倾斜表面以外的其它两个相对的竖直表面侧部沿水平方向伸出。当接合元件相互接合在一起时,配合凸起位于相配合的表面紧固件的一对相邻接合元件的两个相面对的倾斜表面之间,并具有与两个倾斜表面相配合并贴靠在一起的倾斜表面,从而可避免接合时产生摆动,并具有较高的接合力以避免接合元件脱开,从而可将合成树脂模制表面紧固件平稳地按压和相互连接在一起。
由合成树脂整体模制而成的表面紧固件制作方法
- 专利详情
- 全文pdf
- 权力要求
- 说明书
- 法律状态
查看更多专利详情
下载专利文献
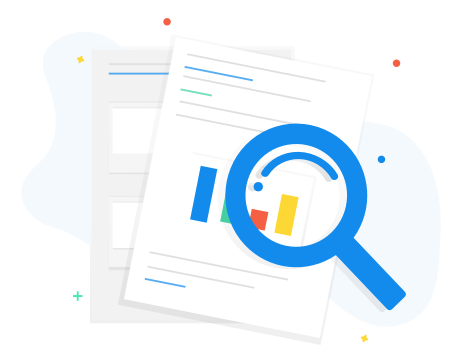
下载专利
同类推荐
-
T.F.奥斯曼R.J.V.艾弗里欧希舜, S·S·拉姆博兹刘升逑利·博尔达克, 胡安·帕罗蒂利·博尔达克, 胡安·帕罗蒂雅内尔·比尔克
您可能感兴趣的专利
-
松永怜姜雯雯, 闫佳莹赵亮
专利相关信息
-
H·A·M·哈维里, K·勒佩拉B·贾拉德, S·博尔查德特沈进焕, 杜春梅