专利名称:尖晶石系复合氧化物烧制体及其制造方法 铬酸钠的制造通常是添加铬矿石、苏打灰、石灰及填充剂,在高温下进行氧化焙烧,接着将焙烧物浸于水中提取铬酸钠而进行的,这时产生大量的浸出残渣。因为该浸出残渣中含有有害的六价铬,直接将其废弃会污染土壤或水质,而成为公害的原因,所以要实施无害化处理。例如,有文献提出了下述这些方法,即将相对于残渣量是1~20重量%的还原剂和摩尔比SiO2/CaO为1以上的含有硅酸物质添加到铬酸钠浸出残渣中并进行混合、接着进行烧制该混合物的方法(参照专利文献1);在制造铬酸钠及重铬酸钠的过程中副产的铬酸盐的水提取后的残渣中添加约1~15重量%的含油废硫酸、硫酸沥青、废氯化烃油或废重油并混合的方法(参照专利文献2);将活性碳混合于粉状的铬废渣中、在氧浓度低的环境中400~1000℃、材料温度为700℃以下的温度下焙烧该混合物后再进行急冷的方法(参照专利文献3);将焦碳粉及粉状的粘土与粉状的铬废渣混合、在1000~1300℃温度下焙烧的方法(参照专利文献4);将活性碳材料与粉状的铬矿渣混合、在氧浓度低的环境中400~1000℃温度下焙烧该混合物后再进行急冷的方法(参照专利文献5);将焦碳粉及粉状的粘土与粉状的铬矿渣混合、在1000~1300℃温度下焙烧的方法(参照专利文献6);将粘土类粉末与在重铬酸钠制造过程中产生的矿渣粉末混合或进行表面包覆、在1000~1300℃温度下焙烧的方法(参照专利文献7)等。但是,现状是使用这些方法进行无害化的处理物只是简单地被废弃,并没有被再利用。对该没有被再利用的理由之一,可以举出连再使用时的安全性也不能确保。本申请发明人提出了可以将铬矿渣利用于陶瓷领域,作为铬矿渣再利用之一(参照专利文献8~10)。另外,本申请发明人使用钙含量少的铬矿渣,意在再利用,提出了如下的方案,例如,从基于化学组成及X射线衍射的分析看的话,是至少以Al、Fe及Cr相互固溶的固溶尖晶石和石英为主组成的致密的反应烧制体,该烧制体是热传导率为1.3~2.5kcal/mh℃及电阻率102~107Ωcm范围的尖晶石系复合氧化物烧制体(参照专利文献11);从基于化学组成及X射线衍射的分析看的话,是至少含有Fe及Cr相互固溶的固溶尖晶石作为主矿物组成的含铬铁组成物而且是该组成物的布莱恩比表面积为2000~5000cm2/g微粉末的陶瓷用着色剂(参照专利文献12)(特开昭62-36061号公报);或者,铬矿渣粉末和粘土的致密的反应烧制体,该烧制体从基于化学组成及X射线衍射的分析看的话,是至少以Al、Fe及Cr相互固溶的固溶尖晶石和石英为主组成而且具有热传导率为1.3~2.5kcal/mh℃及电阻率为102~107Ωcm范围的物理性质的尖晶石系复合氧化物烧制体(参照专利文献13)。特开昭48-32767号公报(第1页)[专利文献2]特公昭47-35675号公报(第2页)[专利文献3]特公昭50-25915号公报(第1页)[专利文献4]特开昭47-23390号公报(第1页)[专利文献5]特开昭47-20089号公报(第1页)[专利文献6]特公昭50-25916号公报(第1页)[专利文献7]特公昭47-23319号公报(第1页)[专利文献8]特开昭51-41009号公报(第1页)[专利文献9]特开昭51-81806号公报(第1页)[专利文献10]特开昭59-92968号公报(第1页)[专利文献11]特开昭62-12661号公报(第1页)[专利文献12]特开昭62-36061号公报(第1页) 特开平3-205357号公报(第1页)而且,鉴于这样的现有技术,本申请发明人对于想再利用由铬精炼工序副产的溶渣的无公害型材料进行了研究,结果发现使用具有特定组成、钙含量也比目前增加得少的由铬精炼工序副产的溶渣,该溶渣和还原剂、含有硅酸物质及水构成的各原料被均匀地分散,将微细颗粒的混合物进行造粒或加压成形,在特定温度下烧制所得到的反应性优异的反应前体时,从X射线衍射的分析看的话,至少形成Mg、Al、Cr及Fe的固溶尖晶石相,另一方面,该固溶尖晶石相中被无公害化的铬成分与碱成分进行固溶而成为被稳定化的烧制体,该烧制体具有耐热性,即使在微细化、酸或碱中等的恶劣条件下也不会溶解析出铬成分及碱成分,另外,保水性、排水性优异,至此完成了本发明。
因此,本发明的目的在于提供一种使用由铬精炼工序副产的溶渣为原料、具有耐热性并且即使在微细化、酸或碱中等恶劣的条件下也不会溶解析出铬成分和碱成分的可以再利用的尖晶石系复合氧化物烧制体及其制造方法。
即,本发明的第一发明提供一种尖晶石系复合氧化物烧制体,其特征在于混合由铬精炼工序副产的溶渣和还原剂及含有硅酸物质并进行烧制所得到的主要化学组成为Fe2O329~40重量%Al2O315~20重量%MgO 9~14重量%Na2O 0~4重量%Cr2O39~17重量%SiO2 14~20重量%并且CaO含量为2重量%以下的烧制体,以该烧制体为放射线源并使用Cu-Kα线进行X射线衍射分析时,源自(b)含有硅酸物质的2θ=26.7°附近的衍射峰相对于(a)2θ=36°附近{113面}的衍射峰的强度比(b/a)为0.1以下。
另外,本发明的第二发明提供一种尖晶石系复合氧化物烧制体的制造方法,其特征在于,包括下述第一工序~第三工序第一工序由主要化学组成为Fe2O339~44重量%、Al2O313~19重量%、MgO10~14重量%、Na2O0~4重量%、Cr2O313~20重量%、SiO20~2重量%且CaO含量为2重量%以下的由铬精炼工序副产的溶渣和还原剂、含有硅酸物质及水构成的混合物、调制该混合物中所含有的颗粒平均粒径为100μm以下的微细混合物的工序;第二工序将在所述第一工序中得到的微细混合物进行造粒或加压成形、得到反应前体的工序;第三工序在950℃以上温度下烧制在所述第二工序中得到的反应前体、接着进行冷却得到尖晶石系复合氧化物烧制体的工序。
图1是在实施例1中得到的尖晶石系复合氧化物烧制体的X射线衍射图。
图2是在比较例3中得到的尖晶石系复合氧化物烧制体的X射线衍射图。
以下,详细地说明本发明。
本发明的尖晶石系复合氧化物烧制体是至少混合由铬精炼工序副产的溶渣和还原剂及含有硅酸物质并进行烧制而得到的物质。
在本发明中,所谓由铬精炼工序副产的溶渣是指混合铬矿石和碱并进行氧化焙烧、接着将焙烧物浸渍于水中提取铬酸钠后、大量剩余的残渣。
本发明的尖晶石系复合氧化物烧制体是主要化学组成为Fe2O329~40重量%、优选为30~38重量%Al2O315~20重量%、优选为16~19重量%MgO 9~14重量%、优选为9~13重量%Na2O 0~4重量%、优选为3重量%以下Cr2O39~17重量%、优选为12~15重量%SiO2 14~20重量%、优选为15~18重量%并且CaO含量为2重量%以下、优选为1重量%以下的实质上不含有CaO的烧制体。
在本发明的尖晶石系复合氧化物烧制体中,因为实质上不含有CaO,换言之,因为使用作为原料的由铬精炼工序副产的溶渣中实质上不含有CaO的溶渣,所以本发明的尖晶石系复合氧化物烧制体中没有源自溶渣的铬酸钙或在制造过程中副产的铬酸钙,即使在微细化、高温环境下、酸或碱中等的恶劣条件下也不会溶解析出源自铬酸钙的六价铬成分,再利用时具有安全性。
本发明的尖晶石系复合氧化物烧制体,除上述化学组成以外,以该烧制体为放射线源并使用Cu-Kα线进行X射线衍射分析时,源自(b)含有硅酸物质的2θ=26.7°附近的衍射峰相对于(a)2θ=36°附近{113面}的衍射峰的强度比(b/a)为0.1以下,优选为0.05以下,这是重要的条件。
即,本发明的尖晶石系复合氧化物烧制体,从基于X射线衍射的分析来看,原料的含有硅酸物质实质上不存在。
另外,所谓(a)2θ=36°附近{113面}的衍射峰是指36±0.2°的衍射峰。另外,所谓源自(b)含有硅酸物质的2θ=26.7°附近的衍射峰是指26.7±0.2°的衍射峰。
在本发明中,原料的含有硅酸物质是,赋予尖晶石系复合氧化物烧制体颗粒适当强度的同时、如下述反应式(1)及下述反应式(2)[化学反应式1](1)(1)[化学反应式2](2)(2)所示、将因六价铬还原而副产的Na2O及CaO的碱成分固定化作为硅酸盐、通过碱成分的该固定化、防止在高温下氧和碱共存下的从Cr+3回到Cr+6的原料。
本发明的尖晶石系复合氧化物烧制体是,根据X射线衍射分析发现,所述衍射峰的强度比(b/a)在上述范围内,实质上就不存在源自含有硅酸物质的衍射峰的烧制体,通过该衍射峰的消失而固定碱成分的硅酸盐,还被尖晶石相固溶并稳定化。因此,本发明的尖晶石系复合氧化物烧制体具有适度的强度,具有耐热性,即使在微细化、高温环境下、酸或碱中等的恶劣条件下也不会溶解析出铬成分及碱成分,再利用时具有安全性。
本发明的尖晶石系复合氧化物烧制体是具有上述化学组成的物质,但在以该烧制体为放射线源并使用Cu-Kα线进行X射线衍射分析时,主要的衍射峰存在于2θ=36°附近{113面}、2θ=31°附近{202面}、2θ=58°附近{333面}、2θ=63°附近{404面},因为除该主峰以外的源自(b)含有硅酸物质的2θ=26.7°附近的衍射峰及其它衍射峰实质上不存在,所以由基于X射线衍射的分析发现,实质上表示用下述通式(3)[通式3]Mg(AlxFeyCr1-x-y)2O4(3)(式中,x表示0.267≤x≤0.349、y表示0.322≤y≤0.411、x+y<1。)表示的尖晶石相的单层,可以说在X射线衍射方面来看是高纯度的烧制体。
本发明的尖晶石系复合氧化物烧制体的形状,没有特别限制,该尖晶石系复合氧化物烧制体制造得怎样,是粒状、破碎状还是板状等形状,可以任意设计。根据后述的本发明的优选的实施方式的制造方法,通常得到平均粒径为0.5~25mm的颗粒,但通过对其进行粉碎处理,例如可以任意设计为平均粒径为20μm以下的微细的物质。
另外,本发明的尖晶石系复合氧化物烧制体是具有适度强度的颗粒,由于平均粒径为0.5~25mm的颗粒的单轴压缩强度为1MPa以上,优选为2MPa以上,所以在其使用中形状不用破碎就可以使用。
本发明的尖晶石系复合氧化物烧制体的其它特性在于,是内部含有气泡的多孔体,保水性及排水性优异。即,本发明的尖晶石系复合氧化物烧制体是平均粒径为0.5~25mm的颗粒,吸水量为16~23重量%、优选为18~21重量%,20℃的透水系数为0.001~0.005cm/s、优选为0.002~0.004cm/s。
另外,在本发明中,所谓吸水量是基于JIS A5209的粗骨材的密度及吸水率试验方法、通过下述计算式(1) (式中,W1表示绝对干燥状态的质量、W2表示表面干燥饱水状态的试样的质量)求得的值。
另外,吸水系数是基于JIS A1218的土的透水试验方法、通过下述计算式(2)[计算式2] (式中,A表示试验片的截面(cm3),L表示高度(cm),h表示水头的高度(cm)、t2-t1表示透水时间(sec),Q表示由排水口流出的量(cm2)。)求出的值,是20℃时的值。
而且,本发明的尖晶石系复合氧化物烧制体是平均粒径为0.5~25mm的颗粒,表观比重为1.4~1.8g/cm3、优选为1.5~1.7g/cm3时,可以用作填充性优异的人造骨材等材料。
另外,本发明的所谓表观比重是指基于JIS A1104的骨材的单位容积重量试验方法,通过下述计算式(3)[计算式3] 求得的值。
下面,说明本发明的尖晶石系复合氧化物烧制体的制造方法。
本发明的尖晶石系复合氧化物烧制体的制造方法,包括下述的从第一工序到第三工序。
第一工序由主要化学组成为Fe2O339~44重量%、Al2O313~19重量%、MgO10~14重量%、Na2O0~4重量%、Cr2O313~20重量%且CaO含量为2重量%以下的由铬精炼工序副产的溶渣和还原剂、含有硅酸物质及水构成的混合物、调制该混合物中的颗粒的平均粒径为100μm以下的微细混合物的工序。
第二工序将在所述第一工序中得到的微细混合物进行造粒或加压成形、得到反应前体的工序。
第三工序在950℃以上条件下烧制在所述第二工序中得到的反应前体、接着进行冷却得到尖晶石氧化物烧制体的工序。
第一工序中可以使用的作为第一原料的由铬精炼工序副产的溶渣是混合铬矿石和碱后进行氧化焙烧、接着将焙烧物浸到水中提取铬酸钠后、大量剩余的残渣,使用主要的化学组成为Fe2O339~44重量%、优选为41~44重量%,Al2O313~19重量%、优选为15~19重量%,MgO10~14重量%、优选为11~14重量%,Na2O0~4重量%、优选为0~3重量%,Cr2O313~20重量%、优选为13~17重量%且CaO含量为2重量%以下、优选为1重量%以下、实质上不含有CaO的烧制体成为重要条件。
在本发明中,由铬精炼工序副产的溶渣是,在调制混合铬矿石和碱后进行氧化焙烧、接着将焙烧物浸到水中提取铬酸钠后、大量剩余的残渣的方法中,作为所述碱,不使用消石灰等钙盐,而只使用苛性钠或苏打灰等钠化合物,根据下述反应式(4)[化学反应式4](4)放冷所得到的焙烧物之后、提取铬酸钠后残存的残渣,不需要进行降低溶渣自身的CaO等烦杂的精制操作,所以特别优选,并且,所述铬矿石使用主要化学组成为Fe2O325~34重量%、Al2O313~20重量%、MgO7~11重量%、Cr2O344~48重量%且CaO含量为2重量%以下的物质时,即使不使用消石灰等钙化合物作为碱源而只使用钠化合物,也可以以高收率制造铬酸钠,并且,在提取了铬酸钠的残渣中,CaO自身为2重量%以下,优选为1重量%以下,不调制组成就可以直接使用,所以特别优选。作为这样的铬矿石来说,例如可以列举出南非产的铬矿石。
第二原料的还原剂是,至少包括具有还原作用的C元素为85重量%、优选为88重量%以上的物质,所以是将所述铬中的六价铬完全还原为三价铬所需的原料。可以使用的还原剂,只要是对溶渣中的难溶性铬发挥还原能力就没有特别限制,利用重油、废酸沥青、焦油沥青、沥青、各种合成树脂粉末、焦炭、石碳、フミル酸、来自纸浆废液的木质磺酸盐、锯屑、废糖蜜、淀粉、纤维素、稻草屑等各种产业的副产物或废物或它们的加热分解生成物等是实用的,这些还原剂可以使用一种或两种以上。
这些还原剂的添加量,相对于由铬精炼工序副产的溶渣100重量份,按还原剂中的C元素计,是4~13重量份,优选为7~11重量份。其理由是还原剂的添加量按C元素计不足4重量份时,存在不能充分还原六价铬的倾向,另一方面,还原剂的添加量超过13重量份时,存在残存未反应的还原剂的倾向,这不实用。
第三原料的含有硅酸物质是,至少含有SiO2为60重量%以上、优选为63重量%以上的物质,该含有硅酸物质如上述那样,是通过碱成分的固定化防止在反应中的高温下的碱共存下的Cr+3回到Cr+6并且赋予所得到的尖晶石系复合氧化物烧制体适度强度的原料。可以使用的第三原料的含有硅酸物质,可以举出硅砂、无定形硅、粘土、真珠岩、页岩、硅华、抗火石、尾矿、砂岩、白色沙质沉积石、软硅石、烟尘、黄铁矿溶渣、土硫磺烧渣、铁钢、黄磷、制造其它各种合金等时电炉、溶矿炉等副产的各种含有硅酸溶渣、从铸造工厂排出的旧砂等产业废弃物等,这些可以使用一种或两种以上。其中,使用在水存在下显示出强粘性的粘土矿物时,不仅可以有效地提高各原料的接触面积而且可以调制后述的反应前体,所以是优选的。
这些含有硅酸物质的添加量,相对于由铬精炼工序副产的溶渣100重量份,含有硅酸物质中的SiO2为15~21重量份,优选为17~20重量份。其理由是含有硅酸物质的添加量按SiO2计不足15重量份时,所得到的尖晶石系复合氧化物烧制体的强度不足和碱成分的固定化能不足,而且在反应中存在容易发生从Cr+3回到Cr+6的倾向,另一方面,即使含有硅酸物质的添加量超过21重量份,反应也进行,但残存有未反应原料,而且存在得不到尖晶石单层的倾向,所以不可取。
第四原料的水,是制造使各原料坚固地附着、有效地提高其接触面积的造粒物或加压成形品所需的原料,作为可以使用的水来说,既可以是通常使用的工业用水,也可以用制造各种合金等时电炉、溶矿炉等副产的泥浆液来代替。
水的添加量,相对于由铬精炼工序副产的溶渣100重量份,为11~17重量份、优选为11~15重量份时,可以制造各原料坚固地附着、有效地提高其接触面积的造粒物或加压成形品,所以优选。
第一工序是调制含有混合所述的第一~三原料及第四原料的水所得到的混合物中的颗粒的平均粒径为100μm以下、优选为20~50μm的微细颗粒的混合物。另外,第四原料的水,在使用水溶液或悬浊液作为还原剂的情况下,可以使用它们中所含有的水代替作为第四原料的水。
在本发明中,所谓所述混合物中的颗粒是指不溶于水、即使添加水也以维持特定形状的颗粒存在的物质。在本发明的第一工序中,规定该混合物中的颗粒的平均粒径为上述范围的理由是因为平均粒径超过100μm时,即使对该混合物进行造粒或加压成形也得不到后述的反应性良好的反应前体,所以不能完全地进行对碱成分、铬成分的尖晶石相的稳定化,因为源自含有硅酸物质的2θ=26.7°附近的衍射峰及其它衍射峰存在,所以没有显示出尖晶石的单相,在微细化、高温环境下、酸或碱中等恶劣的条件下,容易溶解析出碱成分、铬成分。
所述第一~三原料优选使用粉末状的物质,但第二原料的还原剂也可以是溶液或悬浊液的状态的物质。因此,第一~第三原料是粉末状或者第一原料和第三原料是粉末状、而第二原料是悬浊液时,在使用不溶于水的物质的情况下,所述混合物中的颗粒的平均粒径表示混合物中的第一~第三原料颗粒的平均粒径,第一原料和第三原料是粉末、而第二原料是溶液时,在第三原料不溶于水的情况下,表示混合物中的第一原料颗粒和第三原料颗粒的平均粒径。
另外,就所述第一~四原料来说,当然使用第一原料的由铬精炼工序副产的溶渣自身的钙含量在上述范围的物质,但优选为即使在第二~第四原料中、使用CaO含量少的物质,当微细的混合物中的CaO含量为2重量%以下、优选为1重量%以下时,在制造过程中没有副产的铬酸钙,即使在微细化、高温环境下、酸或碱中等恶劣条件下也不会溶解析出源自铬酸钙的六价铬成分,再利用时具有安全性,从以上观点考虑而特别优选。
就本发明的第一工序的操作来说,只要是最终混合物中的颗粒的平均粒径在上述范围内而且各原料均匀地分散,就可以使用任何方法,以下示出其一例①按规定量混合预先将第一~第三原料等各原料粉末进行粉碎处理而得到的物质、并调制出上述范围的平均粒径的混合物、再向其中添加规定量的第四原料的水、调制出各原料均匀地分散的混合物的方法。
②按规定量混合第一~第三原料粉末、粉碎处理该混合物并调制出上述范围的平均粒径的混合物、再向其中添加规定量的第四原料的水、调制出各原料均匀地分散的混合物的方法。
③按规定量混合预先将第一原料和第三原料等各原料粉末进行粉碎处理而得到的物质、调制出上述范围的平均粒径的混合物、再向该混合物中添加第二原料的溶液、根据需要添加不足部分的水、调制出各原料均匀地分散的混合物的方法。
④按规定量混合第一原料粉末和第三原料粉末、将该混合物进行粉碎处理、并调制出上述范围的平均粒径的混合物、再向该混合物中添加第二原料的溶液、根据需要添加不足部分的水、调制出各原料均匀地分散的混合物的方法。
上述①~④的粉碎处理,由于原料自身存在水溶剂而显现出粘性,所以优选以干式方式进行,作为可以使用的干式粉碎机来说,例如可以使用干式的珠磨机装置、喷射式磨机装置,但并不限定于此。
另外,得到各原料被均匀地分散的混合物的手段是,利用强大的剪断力作用的机械手段来调制。作为可以使用的混合装置来说,例如可以使用高速混合机、超级混合机、涡轮式混合机、亨舍尔混合机、诺塔混合机、螺旋混合机、浆式混合机等装置。另外,这些均匀分散操作并不限定于例示的机械手段。
第二工序是将所述微细的混合物进行造粒或加压成形从而得到反应前体的工序。
在本发明中,所谓所述反应前体是指利用水溶剂使含有第一~第三原料的由铬精炼工序副产的溶渣和还原剂及含有硅酸物质的混合物在后面进行的烧制之前使得反应性提高、通过缩短各原料间的颗粒间距离并提高各原料的接触面积从而提高反应性的物质。
对于将在第二工序中使用的微细的混合物进行造粒的方法来说,当所得到的造粒物的平均粒径为0.5~25mm、优选为5~20mm时,干燥时及烧制时,造粒物也不会崩坏,所以为优选,另外,由于小的造物颗粒的反应性差,并且,熔粘在烧制炉上,成为给炉子带来麻烦的原因,所以优选粒径为5mm以下的造粒物颗粒含量为25重量%以下、特别优选为15重量%以下。
另外,在该第二工序中,为了有效地进行造粒,在进行造粒之前,预先将成为造粒的核颗粒的制品的尖晶石系复合氧化物烧制体均匀地分散到第一工序的微细的混合物中,可以在这样的状态下使用。这时,所含有的尖晶石系复合氧化物烧制体,其粒径为5mm以下,优选为0.3~3mm,其含量相对于第一原料的由铬精炼工序副产的溶渣,优选为18~35重量%、更优选为20~22重量%。
如此的造粒操作,可以通过例如利用盘型造粒机的方法、利用皿型造粒机的方法、挤出成形机的方法等来实施,但并不特别限制于这些方法。
另一方面,将微细的混合物进行加压成形的方法,是将在第一工序中得到的微细的混合物进行加压成形处理、提高各原料的接触面积的方法。
这时,成形压随着压制机、装入量等不同而不同,没有特别限定,但通常为5~200MPa、优选为10~150MPa。就压制成形机来说,可适当地使用打锭机、团块机、辊式压实机等,只要是可以进行压制,就没有特别限制。
在本发明中,第二工序的反应前体的调制方法,由于在加压成形时生产性差,所以优选通过造粒来进行。
再者,当所得到的造粒物或加压成形品的水分多时,因接着进行的第三工序的烧制而容易崩坏,所以在该造粒物或加压成形品的水分含量超过15重量%的情况下,优选为,在30~350℃、优选为50~200℃下进行干燥,使造粒物或加压成形品的水分含量为15重量%以下之后,实施下面的第三工序。
第三工序是烧制在第二工序中得到的反应前体、接着进行冷却从而得到作为目的物的尖晶石系复合氧化物烧制体的工序。
为了充分进行六价铬的还原反应,烧制温度需要在950℃以上、优选为1000℃以上,烧制温度不足950℃时,从六价铬到三价铬的还原反应不充分,另外,由于溶渣中的碱成分和含有硅酸物质的反应进行得不充分,因此得不到以该烧制体为放射线源并使用Cu-Kα线进行X射线衍射分析时源自(b)含有硅酸物质的2θ=26.7°附近的衍射峰相对于(a)2θ=36°附近的衍射峰{113面}的强度比(b/a)为0.1以下的尖晶石系复合氧化物,所以不可取。另外,在超过1200℃的温度下,由于难以形成还原环境,还原反应有可能不充分,所以烧制优选在1000~1200℃的温度下进行。
就烧制时间来说,需要花费充分时间来进行烧制,直到所得到的尖晶石系复合氧化物烧制体的源自含有硅酸物质的2θ=26.7°附近的衍射峰不存在,通常需要花费0.2小时以上、优选为0.25~1小时来进行烧制。
作为可以使用的烧制炉来说,没有特别限制,例如可以举出隧道式炉、辊式炉(ロ一ラ一ハ一ス炉)、旋转炉及马弗炉。
另外,特别是由于在第二工序中得到的反应前体含有若干水分,所以当烧制温度急剧上升时,造粒物颗粒容易破碎,因该破碎而产生的小的造粒颗粒如上述那样反应性差,还原不充分,并且,熔粘在烧制炉上,成为给炉子带来麻烦的原因,所以优选在投入烧制炉时的烧制炉的温度为400℃以下,将反应前体投入到烧制炉内。
烧制后进行适当冷却,根据需要进行粒度调制,得到作为目的物的尖晶石系复合氧化物烧制体。
另外,就该第三工序中的冷却来说,由于在200℃以上的氧化环境中,三价铬容易变成六价铬,所以需要至少到200℃以下并在还原环境中进行冷却,通常为了避免生成物和空气的接触,优选在还原环境中放冷或者通过水等冷却介质将烧制容器的外壁冷却到200℃以下之后、再通过生成物与水接触的手段等而冷却到室温。
通过如此设计而得到的尖晶石系复合氧化物烧制体,主要化学组成为Fe2O329~40重量%、优选为30~33重量%、Al2O315~20重量%、优选为16~19重量%、MgO9~14重量%、优选为9~11重量%、Na2O0~4重量%、优选为2重量%以下、Cr2O39~17重量%、优选为12~15重量%、SiO214~20重量%、优选为15~18重量%、CaO含量为2重量%以下、优选为1重量%以下,并且,在以该烧制体为放射线源并使用Cu-Kα线进行X射线衍射分析时,源自(b)含有硅酸物质的2θ=26.7°附近的衍射峰相对于(a)2θ=36°附近的衍射峰{113面}的强度比(b/a)为0.1以下,优选为0.05以下。
本发明的尖晶石系复合氧化物烧制体,由于具有上述特性,所以即使长时间浸渍放置于水中也不会溶解析出碱或铬离子,pH也几乎保持中性。而且,本发明的尖晶石系复合氧化物烧制体具有400℃以上的耐热性,另外,对酸或碱的耐药品性优异,粒径也可以微细化为10μm以下,另外,即使在这样恶劣条件下也不会溶解析出铬成分或碱成分,再利用时具有安全性。因此,由于本发明的尖晶石系复合氧化物烧制体即使在恶劣条件下也不会溶解析出铬成分或碱成分,所以当然可以安全、无害地废弃,也不用担心处理或贮藏时变质,另外,即使在其使用中、使用后也不会溶解析出铬成分或碱成分。而且,从再利用的观点来考虑,因为保水性及排水性也优异,所以可以有效地利用于人造骨材例如砂浆用砂、轻质骨材、路壤用骨材、宅地或海岸等填筑用材、其它各种土木、建筑用材料或其原料。
以下,通过实施例详细地说明本发明,但本发明并不限定于此。
<溶渣的调制>
溶渣粉末试样A将98%苏打灰72.9g添加到表1的化学组成的铬矿石(南非产)100g中,用电炉在1000℃下焙烧0.5小时后,将所得到的烧制物放冷之后,通过用水进行提取而得到铬矿渣。
相对于铬矿石100重量份,混合所得到的铬矿渣160重量份,与上述同样,向其中添加苏打灰,反复进行提取操作,得到具有表2所示的化学组成的溶渣粉末试样A。
再者,该溶渣粉末试样A,通过筛分试验求得的平均粒径为0.1mm。
表1
表2
溶渣粉末试样B将98%苏打灰68重量份和消石灰60重量份添加到表3的化学组成的铬矿石(印度产)100重量份中,用电炉在1000℃下焙烧0.5小时后,将所得到的烧制物放冷之后,通过用水进行提取而得到铬矿渣。
相对于铬矿石100重量份,混合所得到的铬矿渣170重量份,与上述同样,向其中添加苏打灰和消石灰,反复进行提取操作,得到具有表4所示的化学组成的溶渣粉末试样B。
再者,该溶渣粉末试样B,通过筛分试验求得的平均粒径为2mm。
表3
表4
<还原剂>
还原剂是通过筛分试验求得的平均粒径为6mm的石油焦炭,使用了下述表5的组成的物质。
表5
<含有硅酸物质>
含有硅酸物质是通过激光衍射法求得的平均粒径为10μm的粘土(笠冈粘土),使用下述表6的组成的物质。
表6
实施例1<第一工序>
将所述粘土30重量份及所述焦炭10重量份添加到100重量份的所述溶渣粉末试样A中,使用粒径为20mm的钢制球并使用球磨机,得到通过激光衍射法求得的平均粒径为20μm的混合物。
接着,将水20重量份添加到所得到的混合物100重量份中,用浆式混合机充分混合0.5小时,得到各原料均匀分散的混合物。再者,该均匀分散的混合物中的CaO含量为0.7重量%。
<第二工序>
使用皿型造粒机,倾斜50度,以旋转数为10rpm,对在第一工序中所得到的均匀分散的混合物进行造粒,得到造粒物。
接着,在100℃下,干燥该造粒物2小时,得到具有下述表7的各物理性质的球状的反应前体。
另外,粒度特性的测定是根据JIS A1102的骨材筛分试验方法进行的。
表7
<第三工序>
在25℃下,将在第二工序中得到的反应前体100重量份投入到电炉内,在1000℃下烧制0.5小时。接着,保持原有的还原环境,自然冷却到25℃,得到烧制体89重量份。
所得到的烧制体,通过骨材筛分试验方法求得的平均粒径为14mm,0.5mm以下的颗粒的含量为5重量%。
所得到的烧制体的各物理性质如表11及表12所示。
实施例2<第一工序>
将所述粘土30重量份及所述焦炭8重量份添加到100重量份的所述溶渣粉末试样A中,使用粒径为20mm的钢制球并使用球磨机,得到通过激光衍射法求得的平均粒径为20μm的混合物。
接着,将在实施例1中所得到的粒径为1mm以下的烧制体5重量份和水20重量份添加到所得到的混合物100重量份中,用浆式混合机充分混合0.5小时,得到各原料均匀分散的混合物。再者,该均匀分散的混合物中的CaO含量为0.7重量%。
<第二工序>
使用皿型造粒机,倾斜50度,以旋转数为10rpm,对在第一工序中所得到的均匀分散的混合物进行造粒,得到造粒物。
接着,在100℃下,干燥该造粒物2小时,得到具有下述表8的各物理性质的球状的反应前体。
另外,粒度特性的测定是根据JIS A1102的骨材筛分试验方法进行的。
表8
<第三工序>
在25℃下,将在第二工序中得到的反应前体投入到电炉内,在1000℃下烧制0.5小时。接着,保持原有的还原环境,自然冷却到25℃,得到烧制体90重量份。
所得到的烧制体,通过骨材筛分方法试验求得的平均粒径为15mm,1mm以下的颗粒的含量为3重量%。
另外,所得到的烧制体的各物理性质如表11及表12所示。
实施例3除了在实施例2的第一工序中使用将由下述表9的化学组成的提取液的精制工序产生的泥浆进行固液分离所得到的泥浆液代替水以外,其它用与实施例2同样的方法,得到了烧制体。
所得到的烧制体,通过骨材筛分试验方法求得的平均粒径为16mm,0.5mm以下的颗粒的含量为6重量%。
另外,所得到的烧制体的各物理性质如表11及表12所示。
表9
比较例1除了在第一工序中进行粉碎、调制均匀分散的混合物的平均粒径为180μm的物质以外,其它用与实施例1同样的操作,得到了烧制体。
所得到的烧制体,通过骨材筛分试验方法求得的平均粒径为10mm,0.5mm以下的颗粒的含量为23重量%。
所得到的烧制体的各物理性质如表11及表12所示。
比较例2用与实施例1同样的方法,实施例第一工序,得到了均匀分散的混合物。在25℃下,将该混合物100重量份直接投入到电炉内,在1000℃下烧制0.5小时。接着,保持原有的还原环境,自然冷却到25℃,得到了烧制体90重量份。接着,进行粗碎,得到了通过骨材筛分试验方法求得的平均粒径为2mm、并且0.5mm以下的颗粒的含量为20重量%的烧制体。
所得到的烧制体的各物理性质如表11及表12所示。
比较例3<第一工序>
将所述粘土30重量份及所述焦炭10重量份添加到100重量份的所述溶渣粉末试样B中,使用粒径为20mm的钢制球并使用球磨机,得到了通过骨材筛分试验方法求得的平均粒径为22μm的混合物。
接着,将水20重量份添加到所得到的混合物100重量份中,用浆式混合机充分混合0.5小时,得到了各原料均匀分散的混合物。再者,该均匀分散的混合物中的CaO含量为25.1重量%。
<第二工序>
使用皿型造粒机,倾斜50度,以旋转数为10rpm,对在第一工序中所得到的均匀分散的混合物进行造粒,得到了造粒物。
接着,在100℃下,干燥该造粒物2小时,得到了具有下述表10的各物理性质的球状的反应前体。
另外,粒度特性的测定是根据JIS A1102的骨材筛分试验方法进行的。
表10
<第三工序>
在25℃下,将在第二工序中得到的反应前体100重量份投入到电炉内,在1000℃下烧制0.5小时。接着,保持原有的还原环境,自然冷却到25℃,得到了烧制体88重量份。
所得到的烧制体,通过骨材筛分方法试验求得的平均粒径为14mm,0.5mm以下的颗粒的含量为2重量%。
所得到的烧制体的各物理性质如表11及表12所示。
<烧制体的评价>
(化学组成的评价)利用ICP发光分析法测定在实施例1~3及比较例1~3中得到的各烧制体试样的化学组成,其结果如表11所示。
(粒径的评价)根据JIS A1102的骨材筛分试验方法分析在实施例1~3及比较例1~3中得到的各烧制体试样的粒度特性,其结果如表12所示。
(利用X射线衍射法的评价)对于在实施例1~3及比较例1~3中得到的各烧制体试样,以其为放射线源并使用Cu-K线进行X射线衍射分析,求得源自(b)含有硅酸物质的2θ=26.7°附近的衍射峰相对于(a)2θ=36°附近的衍射峰{113面}的强度比(b/a),其结果如表12所示。
另外,图1及图2分别表示在实施例1和比较例3中得到的烧制体的X射线衍射图。
(吸水量、吸水系数的评价)根据JIS A5209的粗骨材的密度及吸水率实验方法评价在实施例1~3及比较例1~3中得到的各烧制体的吸水量,并且,根据JIS A1218的土的透水试验方法测定吸水系数。其结果如表12所示。
(单轴压缩强度的评价)在实施例1~3及比较例1~3中得到的各烧制体中,提取粒径为15mm的颗粒5个,根据JIS A5002测定该颗粒的一个单轴压缩强度,其平均值如表12所示。
(表观比重的评价)根据JIS A1104测定在实施例1~3及比较例1~3中得到的各烧制体的表观比重,其结果如表12所示。
表11
注)混合相表示以含有硅酸物质和Mg、Al、Cr及Fe的尖晶石为主的混合相。
表12
<铬的溶解析出试验>
(溶解析出试验1)将在实施例1~3中得到的烧制体50g和水450ml装入到聚乙烯容器内,在20℃下,测定摇振提取6小时后的铬量和pH。其结果如表13所示。
(溶解析出试验2)将在实施例1~3中得到的烧制体50g和水450ml装入到玻璃烧杯内并对其照射紫外线。其结果如表14所示。
(溶解析出试验3)将在实施例1~3中得到的烧制体50g进行粉碎处理,调制了平均粒径为2mm的烧制体试样。装入该粉碎品50g和水450ml,作为酸,使用盐酸、硫酸、硝酸、羧酸,作为碱,使用氢氧化钠、铵,调整pH,测定20℃下6小时后和80℃下6小时后的滤液中的溶解析出铬量和pH。其结果如表15及表16所示。
(溶解析出试验4)将在实施例1~3中得到的烧制体50g进行粉碎处理,调制了平均粒径为2mm的烧制体试样。在80℃、120℃、200℃、300℃、400℃下加热处理该试样后进行冷却,将加热处理后的烧制体50g和水450ml装入到聚乙烯容器内,在20℃下,测定摇振提取6小时后的铬量和pH。其结果如表17所示。
(溶解析出试验5)使用振动磨机将在实施例1~3中得到的烧制体进行粉碎处理,调制了平均粒径不同的各烧制体试样。将该粉碎品50g和水450ml装入到玻璃烧杯内,在20℃下,测定放置6小时后的滤液中的溶解析出铬量和pH。其结果如表18所示。
表13溶解析出试验1的结果
注)表13中的N.D.表示检测界限0.02ppm以下。
表14溶解析出试验2的结果
注)表14中的N.D.表示检测界限0.02ppm以下。
表15溶解析出试验3的结果(20℃)
注)表15中的N.D.表示检测界限0.02ppm以下。
表16溶解析出试验3的结果(80℃)
注)表16中的N.D.表示检测界限0.002ppm以下。
表17溶解析出试验4的结果
注)表17中的N.D.表示检测界限0.02ppm以下。
表18溶解析出试验5的结果(微细化)
注)表18中的N.D.表示检测界限0.02ppm以下。
发明效果如上述的那样,本发明的尖晶石系复合氧化物烧制体是具有400℃以上的耐热性、即使在微细化、高温环境下、酸或碱中等恶劣的条件下也不会溶解析出铬成分及碱成分的可以再利用的安全材料,从有效利用的观点来考虑,该烧制体因为保水性及排水性优异,所以可以有效地利用于例如砂浆用砂、轻质骨材、路壤用骨材、宅地或海岸等填筑用材、其它各种土木、建筑用材料或其原料等。
本发明提供一种不会溶解析出铬成分及碱成分的可以再利用的尖晶石系复合氧化物烧制体。该尖晶石系复合氧化物烧制体是混合由铬精炼工序副产的溶渣和还原剂及含有硅酸物质并进行烧制得到的主要化学组成为Fe
尖晶石系复合氧化物烧制体及其制造方法
- 专利详情
- 全文pdf
- 权力要求
- 说明书
- 法律状态
查看更多专利详情
下载专利文献
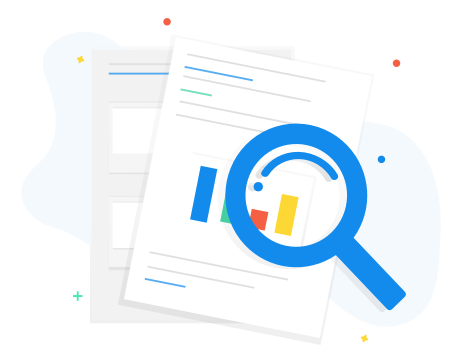
下载专利
同类推荐
-
魏家浩吕志伟吕志伟吕志伟
您可能感兴趣的专利
-
P·莫拉佐尼P·莫拉佐尼P·莫拉佐尼李会郎, 李承元芮秀明, 张秉文
专利相关信息
-
芮秀明K·罗杰斯, G·迪泽瑞嘉李贺军